In today’s competitive manufacturing landscape, businesses face the pressing challenge of staying ahead in technological advancements. Zirconia powder processing has emerged as a critical area where innovation can greatly impact efficiency and product quality. Companies must understand the latest trends and technologies to optimize their processes effectively. This article will address the innovations transforming zirconia powder processing, focusing on real-world applications and solutions that can provide tangible benefits. By exploring these advancements, readers can trust that they will gain insights that can lead to improved operational performance and competitive advantage.
What Are the Current Trends in Zirconia Powder Processing?
The demand for zirconia powder is surging across various industries, including dental, medical, and electronics. This growth is driven by its unique properties, such as high strength, low thermal conductivity, and biocompatibility.
Key developments in processing techniques are shifting how manufacturers approach zirconia powder production. For example, the integration of high-efficiency milling techniques and advanced sintering technologies enhances the powder’s final properties. These advanced techniques enable better control over grain size and distribution, which directly affects performance.
Furthermore, customized processing methods are gaining popularity. Manufacturers can now tailor zirconia powder to meet specific application needs, which is especially important in sectors like dental crowns and industrial ceramics. Tailored powders help enhance product performance, leading to better outcomes for end-users.
Manufacturers are also focusing on optimizing their supply chains to respond more quickly to market demands. Streamlined operations not only reduce costs but also increase production output. Companies are increasingly investing in real-time data monitoring systems. These systems track production metrics and help identify areas for improvement. This real-time information allows manufacturers to make informed decisions, enhancing responsiveness to market changes.
In addition, there is a growing emphasis on sustainability. Many manufacturers are looking for ways to minimize waste and reduce their carbon footprint. This trend includes adopting practices that either recycle waste materials or utilize more environmentally friendly processes. Such initiatives not only benefit the environment but also appeal to consumers who prioritize sustainability.
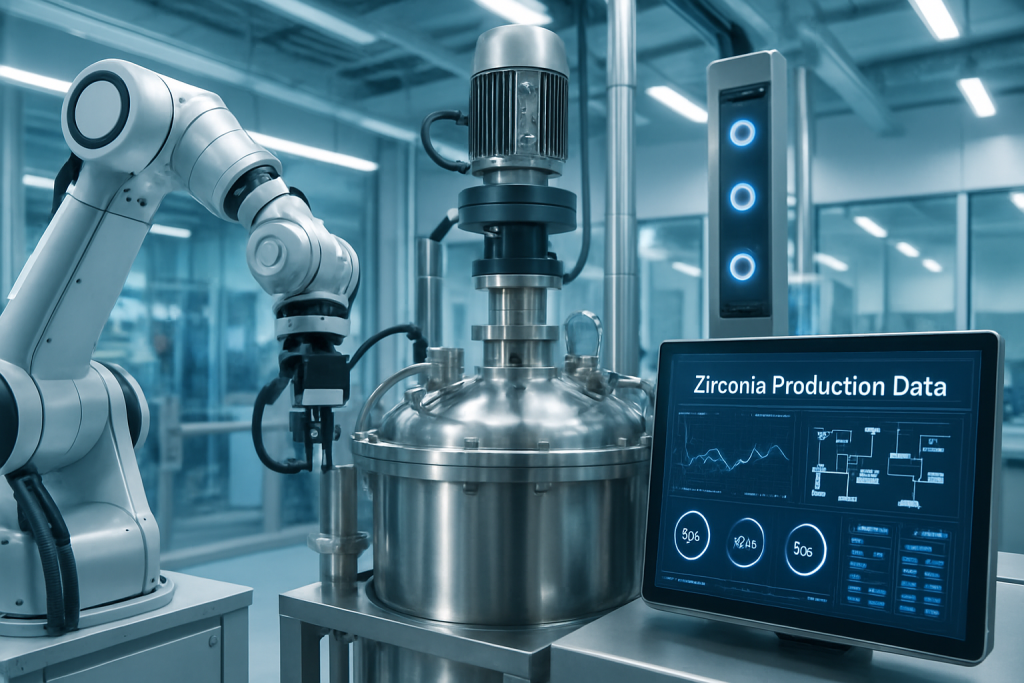
This image illustrates the advanced technology used in zirconia powder production, highlighting efficiency and innovation.
Key Trends Summary
Trend | Description |
---|---|
Increase in demand | Rising use in various industries |
High-efficiency milling | Enhanced processing techniques |
Customized processing | Tailor powder characteristics to specific needs |
Streamlined supply chains | Improved responsiveness and reduced costs |
This holistic understanding of current trends allows manufacturers to adapt their strategies effectively, solidifying their position in the market.
How Are Manufacturing Innovations Impacting Zirconia Processing?
Recent advancements in manufacturing technologies are profoundly influencing how zirconia powder is processed. For instance, modern techniques such as laser processing and additive manufacturing offer new possibilities. These technologies allow for more precise shaping and better control over material properties.
One significant innovation is the development of advanced tools and machinery designed specifically for zirconia. These specialized tools improve cutting speeds and operational efficiency, which is vital for maintaining product quality. For example, high-precision CNC machines equipped with diamond tooling can offer unparalleled accuracy during component manufacturing.
Moreover, automation plays a critical role in reducing human error and increasing repeatability in processes. Companies that implement robotic systems for handling zirconia powder have reported substantial gains in production consistency and quality control. Automated production lines facilitate better integration of different processing stages, leading to enhanced overall performance.
Innovations Summary
Innovation | Impact |
---|---|
Laser processing | Improved precision and control |
Advanced tools | Enhanced cutting speeds and efficiency |
Automation systems | Reduced human error and increased consistency |
Robotic handling | Better integration of processing stages |
Ultimately, these manufacturing innovations transform zirconia processing into a more efficient, reliable, and precise operation.
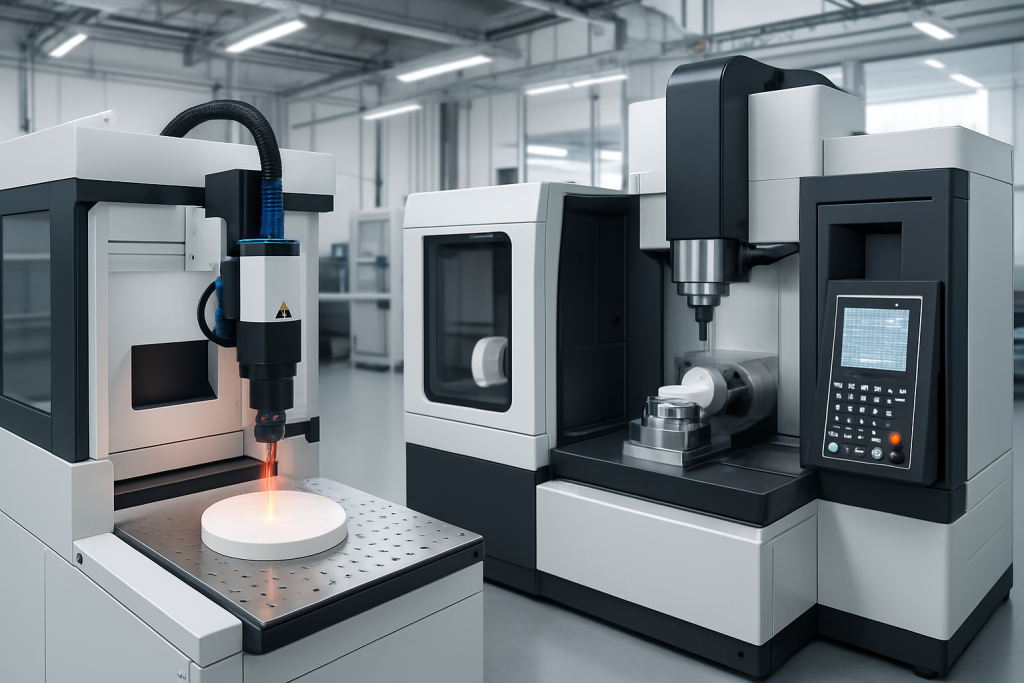
This image represents the state-of-the-art machinery used in zirconia processing, showcasing advanced manufacturing capabilities.
What Role Does Automation Play in Zirconia Processing?
Automation is revolutionizing the manufacturing industry, and zirconia powder processing is no exception. Integrating automated systems can dramatically enhance efficiency and reliability in production.
Automation reduces the risk of human error, which is especially crucial in environments where precision is key. By employing robotics and automated machinery, manufacturers can ensure consistent quality in every batch of zirconia powder produced. For instance, automated mixing and blending systems can achieve uniformity that manual processes may struggle to replicate.
Additionally, the implementation of automated monitoring systems allows for real-time data analysis. These systems track metrics such as temperature, humidity, and pressure in production environments. Timely data can trigger adjustments before issues arise, thus maintaining optimal processing conditions.
Companies also benefit from the ability to operate with fewer staff. Less dependency on human labor for repetitive tasks allows skilled workers to engage in more complex problem-solving activities, optimizing resource utilization.
Automation Benefits Summary
Benefit | Description |
---|---|
Reduced human error | Enhances precision in production |
Real-time monitoring | Allows quick adjustments to processing conditions |
Operating efficiency | Fewer staff required for repetitive tasks |
Enhanced productivity | Allows skilled labor to focus on value-added tasks |
As automation continues to develop, its role in zirconia processing will only become more vital.
How Do Green Technologies Influence Zirconia Powder Processing?
Sustainability is a growing concern for manufacturers worldwide. Incorporating green technologies into zirconia Sustainability is a growing concern for manufacturers worldwide. Incorporating green technologies into zirconia powder processing is becoming increasingly popular. Companies recognize that adopting eco-friendly practices not only helps the environment but can also enhance their market appeal and meet regulatory requirements.
Innovative techniques, such as waste recycling and energy-efficient processes, are being implemented to reduce the environmental impact of zirconia production. For example, companies are investing in systems that capture and recycle waste materials, minimizing waste disposal while saving costs. This can include reprocessing scrap zirconia back into the production cycle, which effectively lowers material costs and reduces overall waste.
Furthermore, the adoption of energy-efficient machinery helps reduce electricity consumption, resulting in lower operational costs. Energy-efficient designs, such as LED lighting and optimized kilns, can significantly decrease the carbon footprint of zirconia processing facilities. These innovations not only benefit the environment but also contribute to a company’s bottom line.
Green chemistry methods are also emerging in zirconia production. These methods involve using non-toxic solvents and materials to minimize environmental hazards. By employing greener alternatives, manufacturers can ensure compliance with increasingly stringent environmental regulations.
Green Technology Impact Summary
Technology | Influence |
---|---|
Waste recycling | Minimizes disposal costs and environmental impact |
Energy-efficient machinery | Reduces operational costs and energy consumption |
Green chemistry methods | Lessens environmental hazards |
The shift toward green technologies reflects manufacturers’ commitment to sustainable practices while maintaining quality and efficiency. By prioritizing these innovations, companies can not only comply with regulations but also appeal to environmentally conscious consumers.
What Specific Techniques Are Enhancing Zirconia Processing Quality?
Quality control is essential in zirconia powder processing. Implementing specific techniques can significantly enhance the characteristics of zirconia products.
One notable technique is advanced purification processes. These methods ensure that impurities are minimized, leading to superior final products. For example, ultrafiltration can be adopted to achieve extremely high levels of purity in zirconia powder.
Another key technique involves controlling particle size distribution. Different applications of zirconia may require varied particle sizes. Using specialized milling processes allows manufacturers to achieve the desired particle size tailored to specific applications, such as in dental implants or industrial ceramics.
Additionally, rigorous quality assurance protocols are crucial. Companies are employing comprehensive testing methods, including x-ray diffraction and scanning electron microscopy, to analyze and confirm the properties of zirconia consistently.
Quality Techniques Summary
Technique | Benefit |
---|---|
Advanced purification | Ensures high levels of purity |
Particle size control | Tailors products to specific applications |
Rigorous quality assurance | Maintains consistent properties |
Focusing on these techniques not only elevates product quality but also ensures compliance with industry standards.
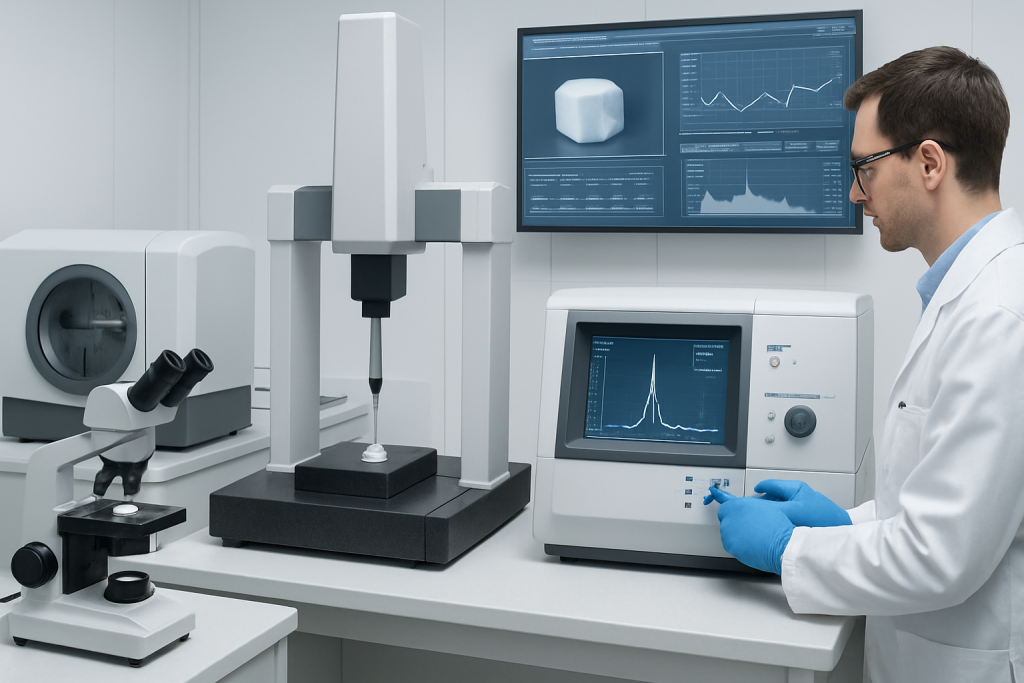
This image depicts advanced quality assurance techniques used in zirconia processing, ensuring optimal product standards.
How Are Digital Technologies Transforming Zirconia Powder Production?
Digital technologies are playing a transformative role in zirconia powder processing. Industry 4.0 concepts are at theTo succeed in the zirconia processing industry, companies need to focus on innovation and continuous improvement. Staying competitive requires constant adaptation to market changes and technological advancements.
One effective strategy is investing in research and development. By exploring new applications and processing techniques, businesses can create unique offerings that meet specific market demands. This proactive approach not only enhances product quality but also opens the door to new revenue streams.
Additionally, enhancing workforce skills through training programs can boost productivity. Employees equipped with the latest industry knowledge can drive innovation and efficiency within the company. Investing in continuous education, like workshops and certifications, can elevate team performance and engagement.
Collaboration is also vital. Partnering with research institutions or technology providers can provide valuable insights and resources needed for innovation. This collaborative approach can foster a culture of continuous improvement, encouraging the sharing of best practices and cutting-edge techniques.
Furthermore, keeping an eye on competitor activities and market trends can help businesses anticipate shifts within the industry. Understanding competitor strengths and weaknesses allows for strategic positioning and can inspire new ideas for innovation.
Staying Competitive Summary
Strategy | Benefits |
---|---|
Investment in R&D | Fuels innovation and unique product offerings |
Workforce training | Boosts productivity and efficiency |
Collaboration | Provides insights for continuous improvement |
Monitoring competitors | Helps in strategic positioning and innovation |
These strategies empower companies to maintain a competitive edge in the rapidly evolving zirconia processing market.
What Challenges Are Faced in Zirconia Powder Processing?
Despite significant advancements, challenges persist in zirconia powder processing. It’s crucial to identify these hurdles in order to develop effective solutions.
One major challenge is the fluctuation of raw material prices. Global economic conditions can impact the costs of zirconium ore, leading to increased production expenses. For manufacturers, this means closely monitoring market trends and exploring alternative sourcing options to mitigate risks. Establishing long-term supplier agreements can also provide price stability.
Another challenge is maintaining stringent quality control amid rising production demand. As production scales up, ensuring that quality does not falter becomes more challenging. Companies may face pressure to increase output while adhering to strict quality standards. Implementing automated quality checks can help alleviate this stress, providing consistent assessments throughout the production process.
Furthermore, meeting regulatory requirements can be complex, especially as these standards evolve. Companies need to be proactive in understanding and complying with environmental regulations and industry-specific guidelines. Staying current with regulations is essential to avoid potential penalties and ensure market access.
Lastly, workforce skill gaps can also pose a challenge. As technology evolves, continuous training and upskilling of staff become necessary to keep pace with advancements. Investing in employee development not only enhances productivity but also boosts morale and retention.
Challenges Summary
Challenge | Solution |
---|---|
Raw material price fluctuations | Long-term supplier agreements |
Quality control | Automated quality checks |
Regulatory compliance | Keeping current with evolving standards |
Workforce skill gaps | Ongoing training and upskilling programs |
Addressing these challenges proactively can significantly enhance operational resilience, positioning manufacturers for long-term success in the zirconia powder processing industry.
How Can Companies Stay Competitive in Zirconia Processing?
To succeed in the zirconia processing industry, companies need to focus on innovation and continuous improvement. Staying competitive requires constant adaptation to market changes and technological advancements.
One effective strategy is investing in research and development. By exploring new applications and processing techniques, businesses can create unique offerings that meet specific market demands. This proactive approach allows companies to anticipate trends and remain ahead of competitors.
Additionally, enhancing workforce skills through training programs can boost productivity. Employees equipped with the latest industry knowledge can drive innovation and efficiency within the company. Cross-training staff in various roles ensures versatility, allowing the workforce to adapt to changing operational needs seamlessly.
Collaboration is also vital. Partnering with research institutions or technology providers can provide valuable insights and resources needed for innovation. This collaborative approach can foster a culture of continuous improvement. By sharing knowledge and experiences with industry partners, companies can develop best practices and tackle challenges more effectively.
Moreover, leveraging digital tools can streamline operations and enhance customer interactions. Utilizing advanced software for project management and customer relationship management ensures timely responses and effective communication. Companies that prioritize customer feedback can adjust their products and services, fostering loyalty and repeat business.
Staying Competitive Summary
Strategy | Benefits |
---|---|
Investment in R&D | Fuels innovation and unique product offerings |
Workforce training | Boosts productivity and efficiency |
Collaboration | Provides insights for continuous improvement |
Leveraging digital tools | Streamlines operations and enhances customer interaction |
These strategies empower companies to maintain a competitive edge while adapting to the evolving landscape of zirconia processing.
What Future Innovations Are Expected in Zirconia Processing?
The future of zirconia powder processing looks promising. Emerging technologies are expected to drive further innovation in the field.
For example, advancements in nanotechnology could lead to the development of even finer zirconia powders with enhanced properties. These powders can offer superior performance in high-tech applications, such as electronics and aerospace.
Additionally, the integration of Artificial Intelligence (AI) in process optimization holds great promise. AI can analyze vast amounts of data to predict and improve production efficiencies, leading to significant cost savings and better quality.
Developments in sustainable practices will continue to shape how zirconia powder is produced. Innovations in green chemistry and renewable energy sources will likely gain traction, leading to more eco-friendly production methods.
Future Innovations Summary
Innovation | Potential Impact |
---|---|
Nanotechnology | Development of finer powders |
Artificial Intelligence (AI) | Improved efficiencies and cost savings |
Sustainable practices | More eco-friendly production methods |
These advancements will likely offer long-term benefits for manufacturers.
How Can Businesses Evaluate Zirconia Powder Processing Suppliers?
Choosing the right supplier is crucial for maintaining quality in zirconia powder processing. Businesses should establish clear criteria when evaluating potential suppliers.
First, consider the supplier’s track record. A history of reliable deliveries and quality products can be a good indicator of a supplier’s capability.
Next, assess the supplier’s commitment to innovation. Suppliers that invest in new technologies are often better positioned to meet your changing needs.
Another vital factor is the supplier’s ability to provide customized solutions. Companies often require tailored zirconia powder for specific applications, so a flexible supplier can significantly enhance operational efficiency.
Finally, it’s important to evaluate customer service. Suppliers who prioritize responsive communication and support can ease collaboration and foster strong partnerships.
Evaluation Criteria Summary
Criterion | Description |
---|---|
Track record | History of reliable deliveries and quality |
Commitment to innovation | Investments in technology and processes |
Customized solutions | Ability to meet specific needs |
Customer service | Quality of communication and support |
Carefully considering these criteria will ensure a fruitful supplier relationship.
Conclusion
In conclusion, the landscape of zirconia powder processing is continually evolving with significant innovations and trends shaping its future. From advanced manufacturing techniques to green technologies and automation, each aspect improves efficiency and product quality. Companies that stay informed about these developments can achieve remarkable gains in their operational performance. Partner with Global Industry today to access cutting-edge resources and support that can help you navigate these changes effectively. Together, we can pave the way for future success.
FAQ Section
Q1: What industries use zirconia powder?
Zirconia powder finds applications in various sectors such as dental, ceramics, electronics, and aerospace, due to its exceptional properties like high strength, wear resistance, and biocompatibility. In the dental industry, it’s often used for crowns and bridges, while in electronics, it serves as an insulator in capacitors and batteries.
Q2: How does automation improve zirconia processing?
Automation enhances efficiency by optimizing production speed and reducing labor costs. It minimizes human error, ensuring that each batch meets quality standards. Additionally, automated systems can continuously monitor conditions during processing, allowing for real-time adjustments that enhance product consistency.
Q3: What environmental concerns are associated with zirconia processing?
Zirconia processing can generate waste and emissions, raising environmental concerns, particularly related to the disposal of chemical substances used in manufacturing. However, advancements in green technologies, such as recycling and energy-efficient methods, are helping to mitigate these environmental impacts, leading to more sustainable practices.
Q4: What are the benefits of digital technologies in zirconia production?
Digital technologies improve data management, enabling better tracking of production processes. Real-time monitoring systems allow manufacturers to identify issues promptly and make adjustments, enhancing overall operational efficiency. Additionally, data analytics can uncover insights that drive continuous improvement in production practices.
Q5: How can a company ensure the quality of zirconia powder?
To ensure high quality, companies should implement rigorous quality control measures throughout the production process. This includes using advanced purification techniques to remove impurities, conducting regular testing and inspections, and investing in employee training to maintain high standards in production. Collaborative feedback loops with customers can also help refine quality assurance practices.