In the production of electronic components, the choice of materials plays a pivotal role. One such material, zirconia powder, has gained significant attention for its unique properties. Professionals seeking to optimize their manufacturing processes often grapple with understanding its impact. This article addresses that concern by exploring the role of zirconia powder in electronics. With its resistance to wear, high thermal stability, and excellent insulating properties, zirconia powder can enhance the quality and performance of various electronic components. By delving into its applications and benefits, this piece aims to provide valuable insights for decision-makers in the industry.
What Are the Characteristics of Zirconia Powder?
Zirconia powder boasts several distinctive characteristics that make it suitable for electronic applications. Firstly, it is known for its exceptional strength and toughness. This durability allows components made from zirconia to withstand significant mechanical stress without failing.
Moreover, zirconia powder has a high melting point, which is advantageous in applications that involve extreme temperatures. It can maintain its structural integrity under conditions that might compromise other materials.
Additionally, zirconia powder possesses excellent insulating properties. This characteristic is essential for electronic components like capacitors and insulators, as it prevents unwanted electrical conduction.
To summarize the qualities of zirconia powder effectively, here is a quick comparison with other materials often used in electronics:
Property | Zirconia Powder | Alumina | Silica |
---|---|---|---|
Strength | High | Medium | Low |
Melting Point | 2680°C | 2050°C | 1710°C |
Insulating Properties | Excellent | Good | Fair |
Cost | Moderate | Low | Low |
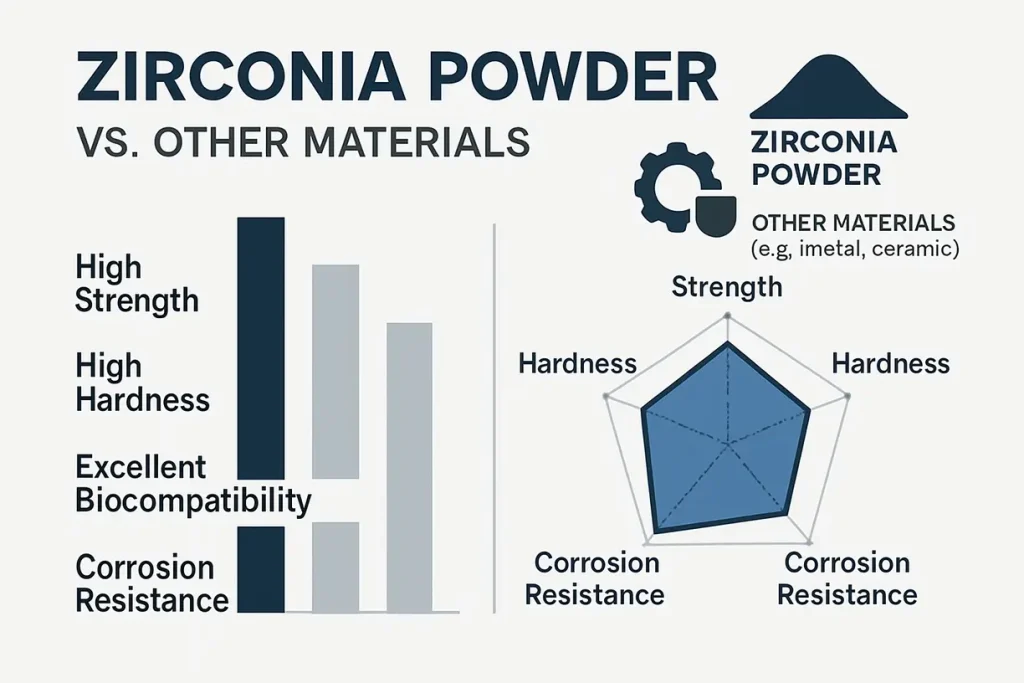
This image illustrates the various characteristics of zirconia powder compared to other materials, highlighting its advantages.
How Is Zirconia Powder Used in Electronics?
Zirconia powder is employed in numerous applications within the electronics sector. One of the most common uses is in ceramic capacitors. These capacitors benefit from zirconia’s insulating properties, which enhance their efficiency and reliability.
Another area where zirconia powder shines is in piezoelectric devices. Here, its mechanical properties allow for accurate transformation between mechanical and electrical energy, which is crucial in sensors and actuators.
Moreover, insulating components, such as substrates for electronic circuits, utilize zirconia powder due to its high dielectric strength. This strength helps in maintaining signal integrity in complex electronic systems.
To further illustrate these applications, consider the following examples:
- Automotive Sensors: Used extensively in vehicle monitoring systems, zirconia-enhanced components increase reliability.
- Mobile Phones: Many smartphones utilize capacitors made from zirconia powder, optimizing performance while preserving space.
- Medical Devices: In devices requiring precise measurements, zirconia powder enhances the accuracy and reliability of sensors.
Tables showcasing various applications can help in understanding how zirconia enhances electronic components:
Application | Type of Component | Benefit |
---|---|---|
Automotive Sensors | Sensors | Improved reliability |
Mobile Phones | Capacitors | Enhanced performance |
Medical Devices | Sensors | Greater accuracy and reliability |
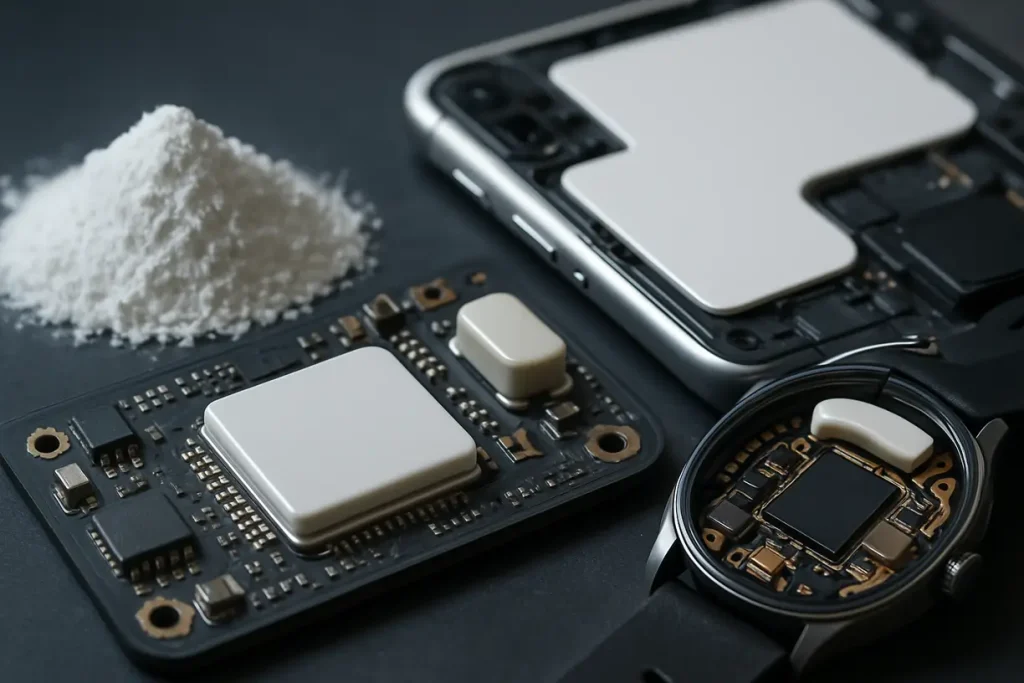
This image depicts the applications of zirconia powder in electronics, providing visual insight into its usage.
Why Is Zirconia Powder Preferred in Electronic Manufacturing?
The preference for zirconia powder in electronic manufacturing stems from its numerous advantages. Firstly, its durability ensures that components created from zirconia can withstand extreme wear and tear—this is crucial in applications that demand long-lasting performance. For example, electronic devices often face mechanical stress and exposure to varying temperatures. Zirconia’s robust characteristics mean that it can endure these challenges without compromising functionality, which translates into lower replacement costs and higher customer satisfaction over time.
Additionally, zirconia powder offers thermal stability. When electronic components operate, they can generate significant heat, especially during high-demand tasks. Zirconia remains stable even at elevated temperatures, which helps prevent failures that might occur with materials that cannot handle heat fluctuations. Such stability is particularly valuable in industries like telecommunications, automotive electronics, and aerospace, where reliability in high-heat environments is critical.
Another key factor is the ease of processing associated with zirconia powder. This material can be easily shaped, molded, and processed into intricate designs without significant difficulty. This flexibility in manufacturing permits a diverse range of applications, from simple insulators to complex electronic components. The ability to create precise shapes reduces waste and lowers production costs, enhancing overall efficiency in manufacturing processes.
Furthermore, zirconia powder offers excellent insulating properties, making it a preferred choice for components such as capacitors and insulators. In situations where electrical conductivity must be minimized, zirconia effectively prevents unwanted electrical transmission. This characteristic is essential in maintaining the performance of sensitive electronic equipment, thereby ensuring that devices operate efficiently and safely.
To illustrate these points, consider the factors influencing material choice in electronic manufacturing:
Factor | Zirconia Powder | Alternatives |
---|---|---|
Durability | High | Moderate to Low |
Thermal Stability | Excellent | Varies |
Ease of Processing | High | Varies per material |
Cost | Moderate | Lower for some |
This comparison illustrates why manufacturers often select zirconia powder over alternative materials. Its combination of durability, thermal stability, and insulating properties makes it a versatile and reliable choice for the demanding landscape of electronic manufacturing. By choosing zirconia powder, companies can not only enhance product performance but also create a more efficient manufacturing process that responds to modern industry challenges.
What Are the Key Production Processes Involving Zirconia Powder?
The production of zirconia powder involves several key processes that significantly affect its quality. The first step is the extraction of zirconium from zircon ores. This process typically involves chemical treatment and purification to obtain high-purity zirconia.
After purification, the powder undergoes milling and sieving. These steps ensure a uniform particle size, which is crucial for consistency in electronic applications. Ideally, the particle size will fall within specified limits to maintain performance standards.
Following this, the sintering process is applied. During sintering, the powder is heated to just below its melting point. This process compacts the powder particles, enhancing their density and strength.
Understanding these production processes is vital. Consider the following table summarizing the key stages:
Step | Description |
---|---|
Extraction | Zirconium is extracted and purified |
Milling | Powder particles are sized uniformly |
Sintering | Heating compacts and strengthens powder |
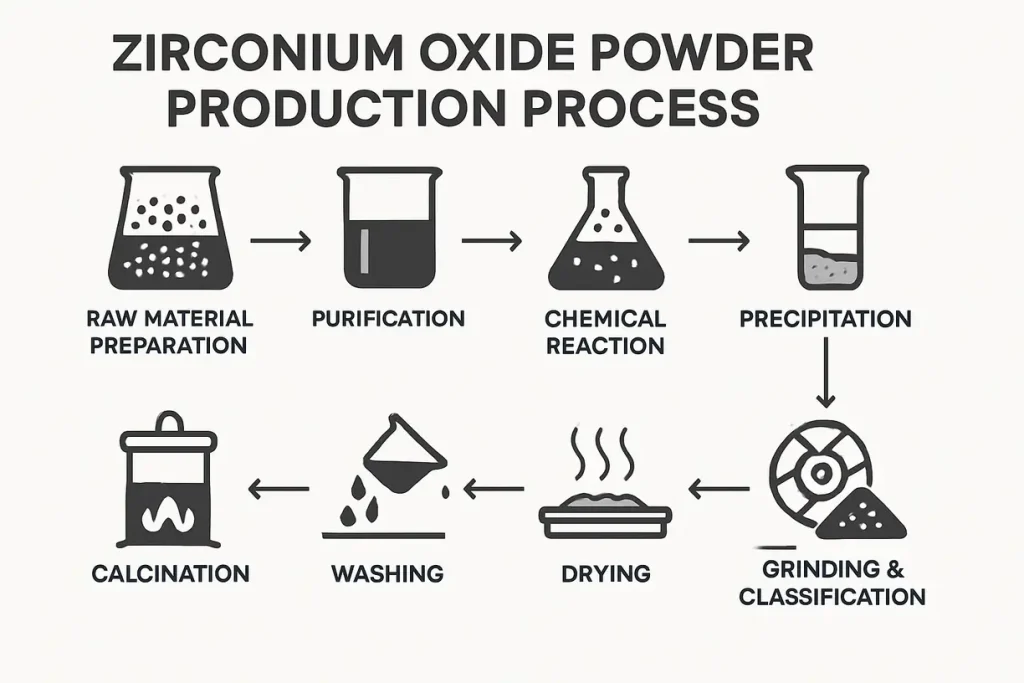
This image visualizes the production processes for zirconia powder, providing clarity on each step involved.
How Does Zirconia Powder Affect Component Performance?
Zirconia powder significantly improves the performance of electronic components in several ways. One of the most notable benefits is its high conductivity for specific applications. While zirconia is generally used where insulation is needed, its ability to conduct ions under certain conditions makes it useful in applications like solid oxide fuel cells.
Moreover, its wear resistance is unmatched. Components made from zirconia can function reliably in abrasive environments, contributing to longer operational lifespans.
Another advantage is its thermal shock resistance. This property enhances component reliability during sudden temperature changes, which is a regular occurrence in many electronic systems.
To better visualize these benefits, consider the following table:
Performance Metric | Zirconia Powder | Alternatives |
---|---|---|
Conductivity | Moderate | Low to Moderate |
Wear Resistance | Excellent | Variable |
Thermal Shock Resistance | High | Low to Moderate |
Clearly, zirconia powder plays a crucial role in enhancing the overall efficiency of electronic components.
What Challenges Are Associated with Using Zirconia Powder?
Despite its many advantages, working with zirconia powder comes with challenges. One significant issue is cost. While zirconia is more affordable than some high-performance ceramics, its price can still be a barrier for some manufacturers, especially if cheaper alternatives exist.
Another challenge revolves around processing difficulties. While zirconia is easy to shape, achieving the desired properties requires precise control during sintering and milling. Improper handling can lead to subpar materials and inconsistent performance.
Additionally, there are environmental concerns. The extraction and processing of zirconia have ecological impacts that need consideration. Manufacturers must ensure compliance with environmental standards and regulations to minimize their ecological footprint.
To identify these challenges effectively, check the following table:
Challenge | Description |
---|---|
Cost | Higher than some alternatives |
Processing | Requires precise control |
Environmental Impact | Extraction and processing have ecological consequences |
These challenges highlight the need for careful consideration when choosing zirconia powder for electronic applications.
What Are the Environmental Considerations for Zirconia Powder?
Environmental considerations are increasingly important in today’s manufacturing landscape. The production of zirconia powder can impact the environment, raising concerns for many companies.
One primary issue is related to resource extraction. The mining of zircon ores can disrupt local ecosystems. Companies must implement sustainable practices to mitigate these impacts.
Another concern involves waste generation. Processing zirconia can produce waste materials that require careful management. Adopting cleaner production techniques can help minimize environmental harm.
Additionally, manufacturers should consider the recyclability of zirconia-based components. While zirconia is durable, end-of-life management is essential to reduce waste and promote sustainability.
To summarize the environmental issues, consider the following table:
Consideration | Description |
---|---|
Resource Extraction | Can disrupt local ecosystems |
Waste Generation | Requires management to reduce environmental impact |
Recyclability | End-of-life management is crucial |
These considerations are essential for companies looking to enhance their sustainability efforts.
How Do Manufacturers Ensure Quality with Zirconia Powder?
Ensuring quality in zirconia powder manufacturing involves several critical practices. Quality control begins with selecting high-purity zircon ores. This foundation is crucial for achieving the desired properties in the final product.
Manufacturers often employ rigorous testing of the powder to verify its performance characteristics. These tests can include assessing particle size, purity, and mechanical properties.
Additionally, certification from relevant industry standards adds credibility. Adhering to standards like ISO ensures that the products meet expectations for performance and reliability.
To present an overview of these quality assurance measures, here is a helpful table:
Measure | Description |
---|---|
High-Purity Selection | Starts with quality raw materials |
Rigorous Testing | Confirms performance characteristics |
Certification | Ensures compliance with industry standards |
By implementing these quality measures, manufacturers can provide reliable products that meet the demands of the industry.
What Innovations Are Emerging in Zirconia Powder Applications?
Innovations in the use of zirconia powder are reshaping electronic applications. One exciting development is in the realm of 3D printing. Manufacturers are exploring ways to use zirconia in additive manufacturing processes, allowing for more complex geometries and structures.
Another emerging trend involves smart materials. Researchers are studying how zirconia can be integrated with other materials to create responsive electronic devices. This integration can lead to smarter, more adaptive components in the future.
Furthermore, advancements in nanotechnology are paving the way for enhanced performance from zirconia. By manipulating zirconia at the nanoscale, researchers aim to unlock new properties that could elevate the performance of electronic components.
To summarize these innovations, consider the following table:
Innovation | Description |
---|---|
3D Printing | Enabling complex geometries |
Smart Materials | Integration for adaptive components |
Nanotechnology | Enhancing properties through nanoscale manipulation |
These developments highlight the potential of zirconia powder to evolve within the electronic sector.
How Is Zirconia Powder Pricing Structured in the Market?
The pricing of zirconia powder can vary based on several factors. Raw material costs significantly impact production expenses. When the cost of zirconium rises, it often results in higher prices for zirconia powder.
Another determinant is the purity level. Higher-purity zirconia attracts a premium price due to its superior performance attributes. Manufacturers often weigh the cost versus benefits when selecting the appropriate purity level for their applications.
Additionally, market demand plays a vital role. Fluctuations in the electronics industry can affect the pricing structure. When demand for electronic components rises, it can lead to increased zirconia prices.
To better understand these pricing factors, here is a table summarizing key influences:
Pricing Factor | Influence |
---|---|
Raw Material Costs | Directly affects production expenses |
Purity Level | Higher purity means higher prices |
Market Demand | Fluctuations in demand can impact prices |
These considerations can help businesses navigate the zirconia market effectively.
What Future Trends Involve Zirconia Powder in Electronics?
As the electronics sector progresses, zirconia powder remains at the forefront of innovation. One trend is the miniaturization of components. As electronics become smaller, the demand for high-performance materials like zirconia increases.
Another trend involves the integration of advanced technologies. With the rise of the Internet of Things (IoT) and smart devices, zirconia powder’s properties can support new applications in connected technology.
Moreover, sustainable practices continue to evolve. Manufacturers are investing in cleaner processes to minimize environmental impacts. This shift aligns with a growing demand for eco-friendly materials in electronics.
To visualize these future trends, consider the following table:
Trend | Description |
---|---|
Miniaturization | Smaller, high-performance components |
Advanced Technology | Integration with IoT and smart devices |
Sustainable Practices | Investment in cleaner manufacturing processes |
These trends signal an exciting future for zirconia powder in electronics.
Where Can Businesses Source High-Quality Zirconia Powder?
Sourcing quality zirconia powder is crucial for manufacturers. Businesses should prioritize suppliers with a proven track record of providing high-purity zirconia. Reputable manufacturers often possess certifications that validate their compliance with industry standards.
Another approach is to attend industry trade shows and conferences. These events allow manufacturers to connect directly with potential suppliers, facilitating informed decisions.
Finally, establishing long-term relationships with trustworthy suppliers can ensure a consistent supply of quality zirconia powder. Such partnerships can also lead to favorable pricing and improved service.
To facilitate sourcing, consider the following table:
Sourcing Method | Description |
---|---|
Reputable Suppliers | Prioritize high-purity certification |
Industry Events | Connect with suppliers directly |
Long-Term Relationships | Foster reliability and better pricing |
These strategies can help businesses find the right sources for their zirconia powder needs.
Conclusion
In conclusion, understanding how zirconia powder impacts electronic component production highlights its significance in various applications. The material’s durability, thermal stability, and insulating properties present clear advantages for manufacturers. Companies that choose to integrate zirconia powder into their processes can benefit from improved performance and longer-lasting components. For expert insights and sourcing solutions, connect with Global Industry and explore how we can support your production needs. Together, we can achieve excellence in electronics.
FAQ Section
Q1: What advantages does zirconia powder have over other materials?
Zirconia powder offers several distinct advantages over traditional materials like alumina and silica. Its superior thermal stability allows it to maintain integrity under high temperatures, making it ideal for demanding electronic applications. The excellent wear resistance means that components can last longer, reducing the need for replacements. Additionally, zirconia’s superior mechanical strength ensures that even in harsh environments, the components remain intact, minimizing the risk of failure.
Q2: Are there any specific applications where zirconia powder shines?
Yes, zirconia powder excels in various applications within the electronics sector. It is widely used in the manufacturing of ceramic capacitors, which benefit from its excellent dielectric properties. Additionally, zirconia is an ideal material for insulators that need to prevent unwanted current flow. Its applications extend to piezoelectric devices, where it plays a crucial role in sensors and actuators, enabling precise measurement and performance.
Q3: How does the production process for zirconia powder affect its quality?
The quality of zirconia powder is heavily influenced by its production processes, including sourcing, purification, milling, and sintering. High-purity raw materials are critical; impurities can weaken the end product. The milling process must ensure uniform particle size for consistent performance, while sintering conditions must be carefully controlled to achieve the desired strength and density. These factors directly impact the material’s suitability for high-performance electronic applications.
Q4: What environmental impacts are associated with zirconia powder production?
The production of zirconia powder can pose environmental challenges, primarily due to resource extraction and waste generation. Mining zirconium can disrupt local ecosystems, leading to habitat loss. Additionally, the processing stages can generate waste materials that require careful handling to prevent pollution. Manufacturers are increasingly focused on reducing their ecological footprint through sustainable practices, such as recycling and using environmentally friendly processes.
Q5: How can companies ensure they are sourcing quality zirconia powder?
To source high-quality zirconia powder, companies should evaluate suppliers based on their track record and reputation in the industry. They should seek suppliers with certifications that confirm compliance with international quality standards, such as ISO certifications. Additionally, visiting suppliers or industry trade shows can provide firsthand insight into manufacturing practices. Establishing long-term relationships with trusted suppliers can also ensure a steady supply of high-quality material tailored to specific application needs.