Are you struggling to find a material that maintains its shape and integrity under extreme temperatures? In precision industries, even tiny changes caused by heat can lead to component failure and costly errors. The challenge is finding a reliable material with very low thermal expansion. Zircon powder offers a powerful answer to this problem. Its unique thermal properties provide exceptional stability, making it a go-to choice for applications where precision is everything. With a proven track record in demanding fields like ceramics and refractories, zircon powder stands as a trusted material for engineers and manufacturers who cannot afford to compromise on quality and performance.
What is Zircon Powder?
Zircon powder is a finely milled substance derived from the mineral zircon, a zirconium silicate (ZrSiO4). It is known for its exceptional hardness, opacity, and, most critically, its resistance to high temperatures. This material is not just another industrial powder; it is a highly specialized agent of stability. Its composition is primarily zirconium silicate, but its value comes from the unique combination of physical and chemical properties it possesses. Here’s the deal: these properties make it indispensable in a variety of high-stakes industrial settings.
The key characteristics of zircon powder include:
- A very high melting point
- Low thermal conductivity
- Excellent chemical inertness
This means it doesn’t easily melt, transfer heat, or react with other chemicals, even under harsh conditions. It is typically available in several grades, with variations in particle size and purity. For instance, finer powders might be used for creating smooth glazes in ceramics, while coarser grades could be used in refractory bricks. The choice of grade depends entirely on the specific demands of the application, from casting and foundry work to producing advanced ceramic components. Understanding these fundamental traits is the first step in appreciating its role in modern manufacturing.
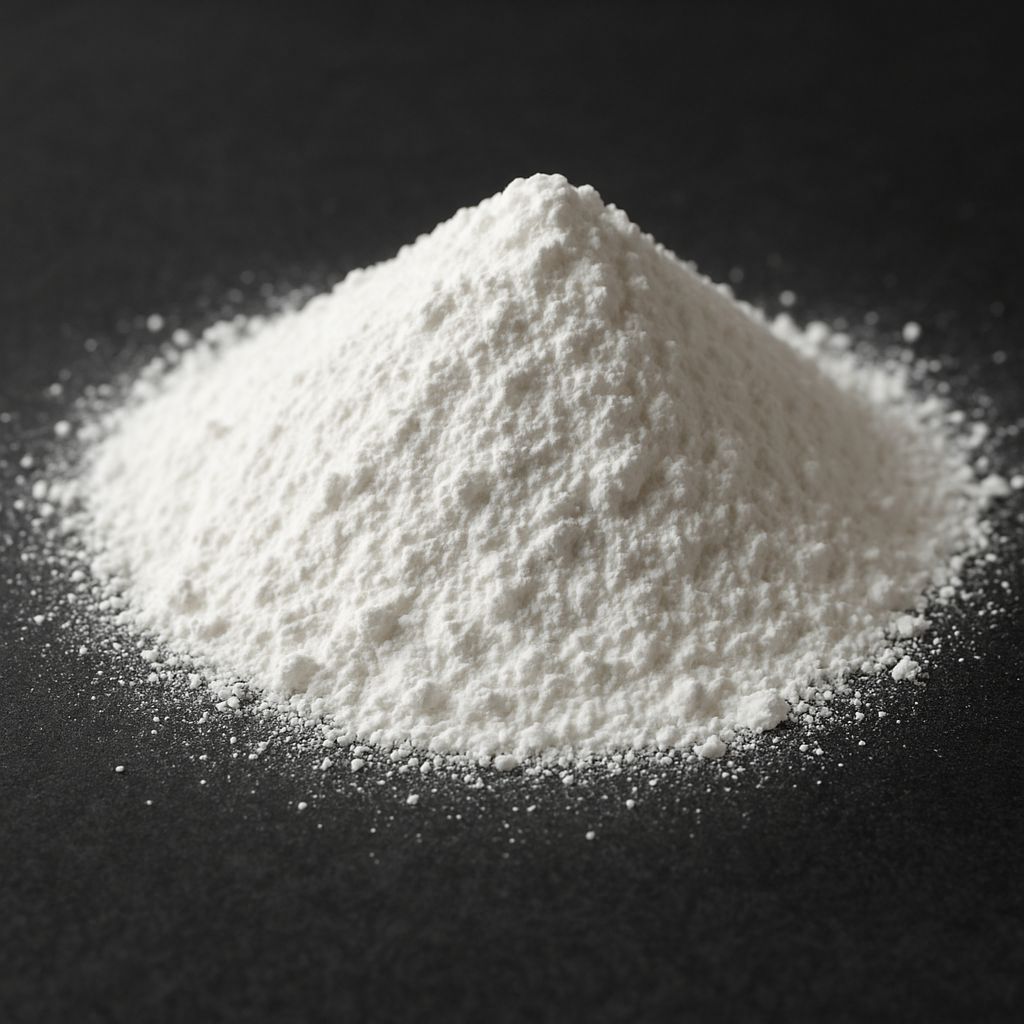
A mound of pure, white zircon powder, ready for industrial use.
Why Does Thermal Expansion Matter?
Thermal expansion is a fundamental property of matter. It describes the tendency of a material to change its shape, area, and volume in response to a change in temperature. In most materials, atoms and molecules vibrate more vigorously when heated, pushing each other apart and causing the material to expand. You might be wondering: why is this a big deal? In precision applications, this expansion can be a massive problem. Imagine a ceramic component in an engine or a mold for casting molten metal. If it expands too much, it can crack, warp, or cause the final product to be out of specification. This can lead to part failure, production downtime, and significant financial losses.
The impact on material performance is direct and often critical. Materials with high thermal expansion are unsuitable for environments with fluctuating temperatures. They lack dimensional stability, meaning their size changes unpredictably with heat. This is where materials like zircon powder become so valuable. Its low coefficient of thermal expansion (CTE) means it expands and contracts very little when heated and cooled. This stability is paramount in precision applications where tight tolerances must be maintained. Whether in aerospace, automotive, or electronics manufacturing, controlling thermal expansion is key to creating reliable, long-lasting products.
Property | Zircon Powder | Alumina | Silica |
---|---|---|---|
CTE (x10⁻⁶/°C) | 4.5 | 8.1 | 0.54 |
Melting Point (°C) | 2190 | 2072 | 1713 |
Hardness (Mohs) | 7.5 | 9 | 7 |
How Does Zircon Powder Resist Heat?
Zircon powder’s remarkable ability to withstand high temperatures stems directly from its atomic structure. Its low coefficient of thermal expansion is its most celebrated feature in this regard. Unlike many metals and ceramics that expand significantly when heated, zircon maintains its dimensions. The bottom line is this: this property prevents stress buildup and cracking during thermal cycling, which is common in many industrial processes. This inherent stability is a direct result of the strong chemical bonds within its zirconium silicate crystal lattice, which resist the increased atomic vibration that comes with heat.
The crystalline structure of zircon powder is incredibly stable. It remains in its tetragonal crystal form up to very high temperatures, without undergoing phase transitions that could cause abrupt changes in volume and compromise structural integrity. This contrasts with other materials that may change their crystal structure at certain temperatures, leading to internal stresses. The stability of zircon powder means it performs predictably and reliably, time after time. When compared to other refractory materials like alumina or magnesia, zircon often provides a better balance of:
- Thermal stability
- Chemical inertness
- Mechanical strength
This makes it a preferred choice for some of the most demanding applications.
Where Does Zircon Powder Excel?
Zircon powder finds its home in applications where heat and precision are primary concerns. In high-temperature industrial processes, it is a star performer. For example, in the foundry and investment casting industries, it is used to create molds and cores for casting high-temperature alloys. What does this mean for you? It means you can produce intricate metal parts with high accuracy, as the zircon mold won’t deform when filled with molten metal. Its non-wetting properties also ensure a smooth surface finish on the final cast part, reducing the need for extensive post-processing.
Another key area is in the manufacturing of advanced ceramics. Precision ceramic components used in everything from electronics to aerospace benefit from zircon powder’s properties. It acts as an opacifier, giving ceramics a brilliant white and opaque finish, and as a refractory component, allowing them to withstand high service temperatures. In the steel industry, it is used in refractory linings for ladles and furnaces that hold molten steel. Its ability to resist corrosion from molten metal and slag makes it an ideal protective barrier. These applications all share a common need: a material that can take the heat without losing its shape or strength. Zircon powder consistently delivers.
Application | Industry | Key Benefit |
---|---|---|
Investment Casting Molds | Foundry | High dimensional accuracy |
Ceramic Glazes | Ceramics | Opacity and brightness |
Refractory Bricks | Steel | High-temperature stability |
Foundry Coatings | Automotive | Smooth surface finish |
Zirconia Production | Advanced Materials | High-purity raw material |
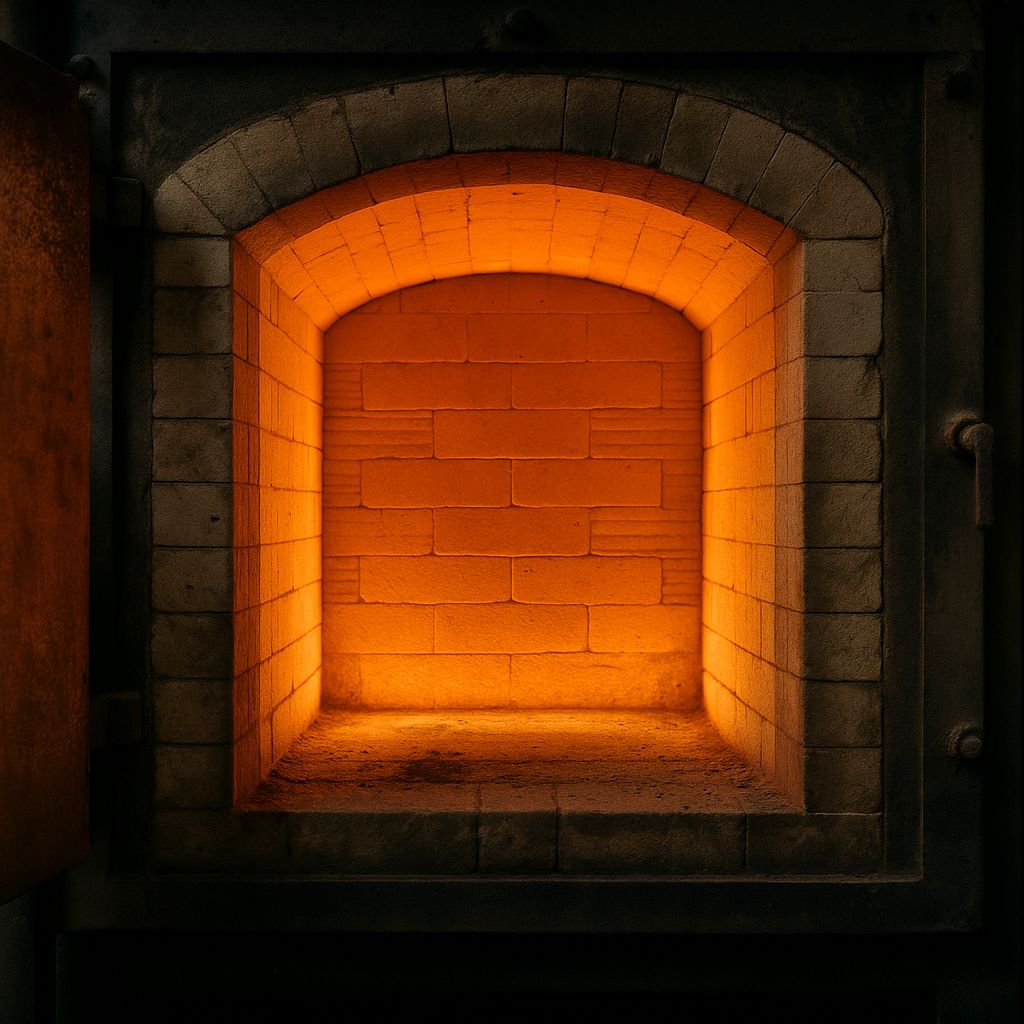
A view inside a high-temperature furnace, protected by a durable refractory lining.
What Are Its Application Benefits?
The use of zircon powder translates into several tangible benefits for manufacturers. The most significant is enhanced dimensional stability. Products made with or coated with zircon powder hold their intended shape and size even when subjected to extreme heat. This is crucial for precision components where even microscopic deviations can be detrimental. Think about it: for a B2B buyer, this means:
- Fewer product rejections
- Less material waste
- A more efficient production line
This stability directly contributes to a higher quality final product and a stronger bottom line.
Furthermore, zircon powder significantly improves the thermal shock resistance of materials. Thermal shock occurs when a material is subjected to a rapid temperature change, causing it to crack. Because zircon powder expands and contracts so little, it mitigates the internal stresses that lead to such failures. This results in an extended product lifespan for components like refractory bricks or ceramic parts, reducing maintenance costs and downtime. The overall effect is a more robust and reliable end product, which enhances the manufacturer’s reputation and provides greater value to the end-user. These benefits make zircon powder not just a material, but a strategic asset.
Benefit | Impact on B2B Buyers |
---|---|
Enhanced Dimensional Stability | Fewer defects, less waste |
Improved Thermal Shock Resistance | Longer product life, lower maintenance |
Increased Refractoriness | Higher operating temperatures possible |
Chemical Inertness | Less corrosion, greater purity |
How Is Zircon Powder Processed?
The journey from raw zircon sand to high-purity zircon powder is a multi-step process designed to refine and control the material’s properties. It begins with the mining of zircon-bearing mineral sands. These sands are then processed through various physical separation techniques, like gravity and magnetic separation, to concentrate the zircon. But it doesn’t stop there. The concentrated zircon sand is then milled into a fine powder. The milling process is critical, as it determines the particle size distribution of the final product, which in turn affects its performance in applications like glazes and refractories.
Quality control is a constant throughout the manufacturing process. Samples are regularly taken and tested for:
- Chemical composition
- Particle size
- Other physical properties
This ensures that each batch of zircon powder meets the strict specifications required by customers. For some advanced applications, the powder may undergo further processing, such as calcination, to enhance its properties. Customization is also a key aspect of production. Suppliers often work closely with B2B buyers to provide a grade of zircon powder tailored to their specific needs, whether it requires a particular particle size for a casting slurry or exceptional purity for an electronic component. This rigorous processing and quality control are what make zircon powder a reliable and consistent industrial material.
Processing Step | Purpose |
---|---|
Mining & Concentration | Isolate raw zircon sand |
Milling | Reduce particle size |
Classification | Control particle size distribution |
Quality Control Testing | Ensure product specifications are met |
Customization | Tailor product to customer needs |
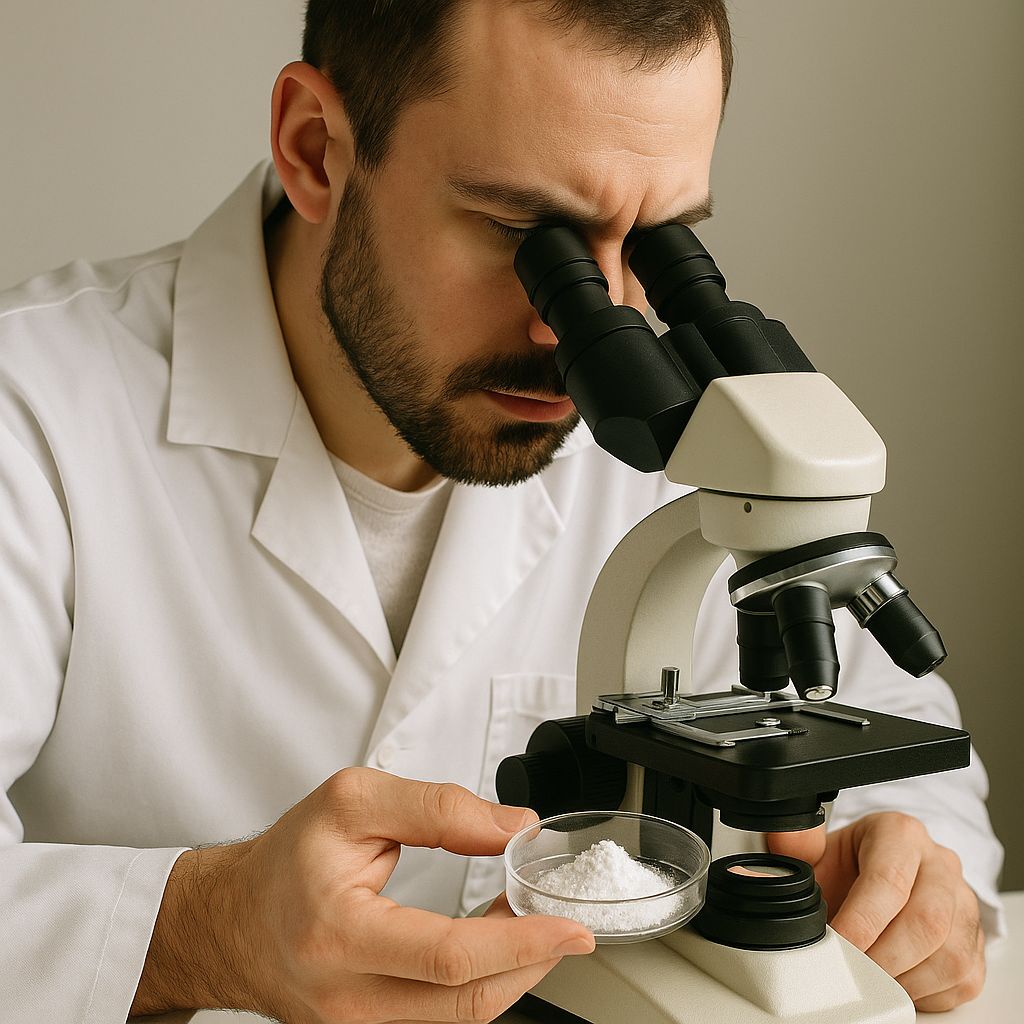
A technician performs quality control on zircon powder to ensure purity and consistency.
What Future Trends Impact Zircon?
The market for zircon powder is not static. Several trends are shaping its future use and development. Here’s a look at what’s next. Emerging applications in advanced technologies are a major driver. For example, research into solid oxide fuel cells and new types of batteries is exploring the use of zirconia, which is derived from zircon, as a key component. The push for greater energy efficiency and smaller electronic devices is also creating new opportunities for materials that offer superior thermal management. As technology advances, the unique properties of zircon powder will likely find their way into even more innovative products.
Sustainability is another important factor. The industry is facing increasing pressure to adopt more environmentally friendly practices. This includes everything from:
- More efficient mining and processing techniques
- Development of recycling programs for zircon-containing products like refractories
B2B buyers are increasingly looking for suppliers who can demonstrate a commitment to sustainability. The market outlook for zircon remains strong, driven by continued growth in the ceramics, foundry, and chemical industries. However, its long-term success will depend on the industry’s ability to innovate and adapt to these new technological and environmental demands.
Trend | Implication for Zircon Powder |
---|---|
Advanced Technologies | New markets in energy and electronics |
Sustainability Demands | Pressure for greener processing |
Circular Economy | Focus on recycling used refractories |
Geopolitical Factors | Shifts in global supply chains |
Conclusion
In summary, zircon powder’s value in high-heat applications is undeniable. Its low thermal expansion and high refractoriness provide the stability that precision industries demand. For your business, this translates directly into a more reliable manufacturing process and a higher-quality final product, giving you a clear competitive advantage. Ready to leverage these benefits? Contact Global Industry today to discuss how our high-purity zircon powder can meet your specific application needs. Let’s build more durable and precise products together.
FAQ Section
Q1: What makes zircon powder unique for high-temperature uses?
Its exceptionally low coefficient of thermal expansion and high melting point make it highly resistant to heat and thermal shock. This combination allows it to maintain structural integrity and dimensional stability even under extreme thermal cycling, which is critical for precision components in demanding environments.
Q2: Can zircon powder be used in extreme thermal cycling?
Yes, absolutely. Zircon powder’s inherent dimensional stability and low thermal expansion coefficient make it an ideal material for applications that experience rapid and repeated temperature changes. This property significantly reduces the risk of thermal stress and cracking, extending the lifespan of components in industries like aerospace and automotive.
Q3: How does particle size affect zircon powder performance?
Particle size is a crucial factor influencing zircon powder’s performance. Finer particles, typically measured in microns, are often preferred for applications requiring smooth surface finishes, such as in ceramic glazes and precision investment casting slurries. Conversely, coarser particles are more suitable for structural applications like refractory bricks and linings, where bulk density and thermal insulation properties are paramount. The specific application dictates the optimal particle size distribution.
Q4: Is zircon powder safe for all industrial applications?
Zircon powder is generally considered very safe and chemically inert for most industrial applications. However, as with any fine particulate material, proper industrial hygiene practices are essential. This includes using appropriate personal protective equipment, such as respirators, to prevent inhalation of airborne particles, especially during handling and processing. Always consult safety data sheets (SDS) for specific handling guidelines.
Q5: Where can I find reliable zircon powder suppliers?
To ensure consistent quality and performance, look for established suppliers with a strong reputation in the industrial materials sector. Reliable suppliers typically have robust quality control systems, offer various grades of zircon powder, and possess a proven track record of serving B2B clients in demanding industries. Companies like Global Industry, for example, specialize in high-purity industrial powders and can provide tailored solutions to meet specific application requirements.