In the competitive landscape of zircon powder production, businesses must often grapple with the challenges of efficiency and cost-effectiveness. Many decision-makers find it difficult to navigate the complexities of extraction methods that impact their bottom line. This article aims to provide clear insights into the extraction techniques transforming zircon powder production. By understanding these innovations, companies can improve their processes and gain a competitive edge. Trust in the depth of this article to equip you with the knowledge required to streamline your operations and enhance product quality.
What Are the Key Extraction Techniques for Zircon Powder?
Extraction techniques are at the heart of zircon powder production. Understanding these methods is crucial to improving efficiency and quality.
Zircon, a valuable mineral used in ceramics, refractories, and foundries, is primarily extracted from zircon sand. The extraction process begins with gravity separation, which takes advantage of the differences in density between zircon and other minerals. Following gravity separation, techniques like magnetic separation are used to remove iron-bearing minerals, ensuring high purity levels.
Historically, zircon extraction methods have evolved from simple hand-panning techniques to more complex mechanical processes. Today, advanced flotation methods involve the use of chemicals to enhance the recovery rate. These modern techniques offer significant advantages over traditional methods, including:
- Higher yields
- Reduced operational costs
- Improved purity of extracted zircon
Adopting these methods not only serves to optimize production but also contributes to environmental sustainability. As the world focuses more on efficient resource use, understanding these extraction techniques will position companies advantageously in the market.
Extraction Method | Key Advantages | Challenges |
---|---|---|
Gravity Separation | Low cost, simple process | Less effective for fine particles |
Magnetic Separation | Effective for mixed mineral sands | Requires careful calibration |
Flotation | High recovery rate | More complex and chemical-intensive |
How Do Modern Techniques Improve Extraction Efficiency?
Modern extraction techniques are revolutionizing the zircon industry by significantly enhancing extraction efficiency.
Recent advancements in hydraulic separation technology allow for the efficient classification of particles, minimizing waste and maximizing yield. This method uses high-pressure water jets to separate zircon from impurities based on size and density.
Additionally, automated systems have streamlined the extraction process. Process control technologies, using sensors and real-time data monitoring, can optimize parameters such as:
- Flow rates
- Chemical additions
- Energy consumption levels
This not only improves the efficiency of extraction but also ensures consistent product quality.
Another factor leading to improved efficiency is the introduction of advanced reagents in flotation processes. Newer chemicals are designed to selectively bind to zircon, increasing recovery rates while reducing the amount of overall reagent required.
For instance, bio-based collectors are gaining attention for their effectiveness and lower environmental impact. By adopting these technologies, companies can significantly reduce both operational costs and their environmental footprint.
These modern efficiencies translate into cost savings and higher profitability for businesses in the zircon powder production sector. Therefore, adopting these technologies becomes essential for staying competitive and meeting market demands.
Modern Technique | Description | Benefits |
---|---|---|
Hydraulic Separation | Uses high-pressure water jets | Increases yield, minimizes waste |
Automated Process Control | Real-time monitoring and adjustments | Ensures quality consistency |
Advanced Reagents | Eco-friendly chemicals | Higher recovery, lower costs |
What Roles Do Chemical Reagents Play in Extraction?
Chemical reagents are critical components in the extraction process of zircon. They play several roles that can directly influence efficiency and quality.
In flotation, reagents are used to separate zircon from other minerals. Common reagents include collectors, which enhance the hydrophobic properties of zircon, making it easier to separate from other materials. Additionally, frothers are added to stabilize the froth and improve mineral recovery.
There are many types of reagents used in zircon processing, including:
- Collectors: Enhance separation of zircon from other minerals.
- Frothers: Control froth formation in flotation processes.
- Modifying Agents: Alter the surface properties of minerals.
However, not all reagents are created equal. The choice of reagents can greatly impact yield, quality, and environmental compliance. Companies must weigh the benefits of different reagents, balancing performance with environmental and safety considerations.
There are ongoing developments in green chemistry aimed at reducing the environmental impact of reagents. New, eco-friendly reagents are being introduced that not only achieve high recovery rates but also minimize harmful residues.
Understanding the roles and implications of these reagents is vital for businesses striving for both efficiency and sustainability in zircon extraction.
Type of Reagent | Function | Environmental Impact |
---|---|---|
Collectors | Improve separation efficiency | Varies by type; newer options are eco-friendly |
Frothers | Stabilize froth during flotation | Generally low, but still requires monitoring |
Modifying Agents | Change surface characteristics of minerals | Eco-friendly options are emerging |
How Does Ultra-Fine Grinding Affect Zircon Powder Quality?
Ultra-fine grinding is a crucial process in the production of zircon powder, significantly impacting its final quality and application.
The term “ultra-fine” refers to particle sizes that are significantly reduced, often to less than 10 micrometers. This process is vital for certain applications, such as ceramics and refractories, where particle size affects the physical properties of the final product.
As zircon is ground to ultra-fine sizes, its surface area increases, enhancing its reactivity and performance in various applications. For instance, in the ceramic industry, finer particles lead to better dispersion in binders, improving overall strength and durability of the final products.
However, ultra-fine grinding comes with its challenges. It can be energy-intensive, and producers must balance the benefits of finer particles against the costs involved. Here are some considerations for effective ultra-fine grinding:
- Energy Efficiency: Seek technologies that minimize energy use.
- Quality Control: Regularly monitor particle sizes to ensure quality.
- Equipment Selection: Choose equipment suited for ultra-fine processing.
Companies can achieve a more energy-efficient grinding process by using modern milling technologies, such as jet mills or ultra-fine grinding systems. These innovations not only enhance quality but also reduce overall production costs.
Table: Impact of Particle Size on Zircon Applications
Particle Size (Microns) | Application | Characteristics |
---|---|---|
< 10 | Ceramics | Improved strength and durability |
10 – 25 | Refractories | Enhanced thermal stability |
25 – 100 | Castings | Better flow properties |
What Environmental Considerations Are Involved?
Environmental considerations are paramount in zircon powder production. The extraction process can have significant ecological effects, including habitat disruption and pollution.
To mitigate these impacts, many companies are adopting sustainable practices. This includes using biodegradable chemicals and optimizing water usage to minimize discharge into the environment.
Additionally, companies are increasingly focused on reclamation efforts. After extraction, restoring the land to its natural state is essential. This helps preserve local ecosystems and demonstrates a commitment to responsible mining practices.
Regulatory compliance is another critical aspect. Different regions have varying environmental regulations, and companies must ensure they meet these standards to avoid legal complications. By investing in compliance, companies not only protect the environment but also enhance their brand reputation among stakeholders.
Here are some key sustainable practices:
- Water Management: Implement processes that recycle water.
- Waste Reduction: Minimize waste through efficient operations.
- Product Stewardship: Ensure products are responsibly sourced and processed.
For many businesses, adopting these sustainable practices is no longer an option but a necessity for long-term success in the zircon industry.
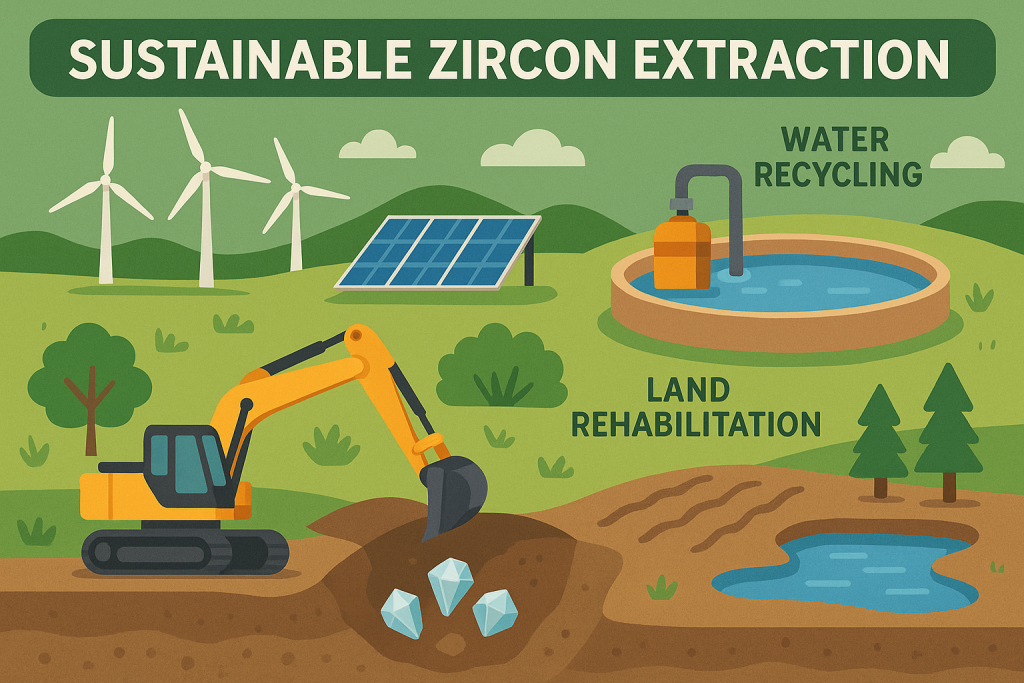
An illustration depicting methods used in zircon extraction, highlighting sustainable practices.
How Does Particle Size Distribution Impact Application?
The distribution of particle sizes in zircon powder significantly affects its performance in various applications. A well-considered particle size distribution can optimize functionality and reduce production issues.
In industries like ceramics, a specific distribution of particle sizes leads to better properties in the finished product. For example, a mix of fine particles contributes to compactness, while coarser particles can provide strength.
Measuring particle size distribution is typically done through laser diffraction or sieve analysis methods. These techniques provide insight into how the particles will perform across different applications.
To maximize the effectiveness of zircon powder, companies must focus on achieving the ideal distribution for their specific use cases. This is increasingly important, especially as applications in high-tech industries call for precise specifications.
Application | Ideal Particle Size Range (Microns) | Required Properties |
---|---|---|
Ceramics | 1 – 10 | High compactness, durability |
Coatings | 5 – 50 | Smooth application, consistency |
Foundry | 25 – 100 | Flow properties, strength |
What Innovations Are Emerging in Zircon Extraction?
Innovation is vital to maintaining competitiveness in zircon extraction. Recent technological advances are reshaping the landscape of zircon powder production.
One significant innovation is the development of bioleaching techniques. This process uses naturally occurring microbes to extract minerals, offering a more environmentally friendly option compared to traditional chemical methods.
Another promising advancement involves automation in extraction setups. Automated systems track and manage extraction processes, allowing for improved precision and efficiency. This can reduce human error and operational costs.
As the industry evolves, data analytics is becoming increasingly critical. Companies leverage data to analyze production variables, optimize operations, and improve decision-making. Here are some cutting-edge technologies influencing the extraction process:
- Machine Learning: Enhances predictive maintenance of extraction equipment.
- Remote Sensors: Monitor environmental impact and operational efficiency.
- Blockchain Technology: Enhances traceability in zircon sourcing.
Staying updated on these innovations allows businesses to identify potential investments and adopt technologies that align with their strategic goals.
Table: Emerging Technologies in Zircon Extraction
Technology | Description | Potential Benefits |
---|---|---|
Bioleaching | Uses microbes for mineral extraction | Eco-friendly and cost-effective |
Automation | Tracks and optimizes extraction processes | Reduces human error and cost |
Data Analytics | Utilizes data to improve decision-making | Enhances operational efficiency |
How Do Market Trends Affect Zircon Production Techniques?
Market trends play a crucial role in shaping extraction techniques for zircon powder. Demand fluctuations often drive innovation, leading to changes in how companies approach production.
As industries evolve and the need for high-quality zircon increases, producers must adapt quickly. For instance, the rise of green technologies has led to a demand for zircon powder that is sustainably sourced and processed. Companies that respond to this demand can differentiate themselves in the marketplace.
Additionally, market trends impact the geographical focus of zircon production. Regions with rich zircon deposits might experience increased investment as companies seek to capitalize on their resources.
Another trend is the growing interest in high-tech applications for zircon powder. Industries such as electronics and renewable energy are driving demand for high-quality zircon products.
Being aware of these trends helps businesses strategize and align their operations with current market needs. Adaptability is crucial in maintaining relevance in the zircon industry.
Market Trend | Impact on Production | Implications for Companies |
---|---|---|
Increased Demand for Quality | Drives innovation in extraction methods | Need for investment in technology |
Focus on Sustainability | Requires eco-friendly practices | Enhances brand reputation |
High-Tech Applications | Demand for pure, high-quality zircon | Necessitates advanced processing |
What Are the Challenges Facing Zircon Powder Producers?
Zircon powder producers face several challenges that can hinder their ability to operate efficiently.
One prominent challenge is the volatility of raw material costs. Fluctuating prices for zircon sand can impact overall production costs, making it difficult to maintain profitability.
Another issue is strict regulatory compliance. As environmental regulations tighten, producers must adapt their operations accordingly, often requiring significant investments in new technologies or processes.
Labor shortages can also pose a challenge. The industry requires skilled workers to operate advanced machinery effectively. Investing in workforce development is key to addressing these gaps.
Despite these challenges, companies can implement strategies to mitigate risks and ensure consistent production levels. This may include:
- Diversifying Supply Chains: Reducing dependency on single sources.
- Investing in Technology: Streamlining operations to improve efficiency.
- Training Programs: Enhancing employee skills and retention.
By identifying and addressing these challenges proactively, zircon powder producers can position themselves for sustained growth and success.
How Can Companies Optimize Their Zircon Powder Production?
Optimization is critical for maximizing efficiency in zircon powder production.
Companies can start by assessing their current extraction processes. Conducting a process audit identifies areas for improvement. This could involve upgrading equipment, refining extraction methods, or revisiting supplier agreements to ensure competitive pricing.
Additionally, implementing lean manufacturing principles can minimize waste and streamline operations. Techniques such as Just-In-Time (JIT) production help reduce inventory costs while maintaining flexibility.
Moreover, fostering a culture of continuous improvement can encourage innovation among employees. Engaging staff in the optimization process can lead to fresh ideas and solutions that enhance productivity.
Consider the following strategies:
- Regular Training: Invest in training employees on new technologies.
- Benchmarking: Compare production practices against industry leaders.
- Feedback Mechanisms: Establish channels for employees to share insights.
By taking these steps, businesses can create a more efficient production cycle, leading to enhanced quality and increased profit margins.
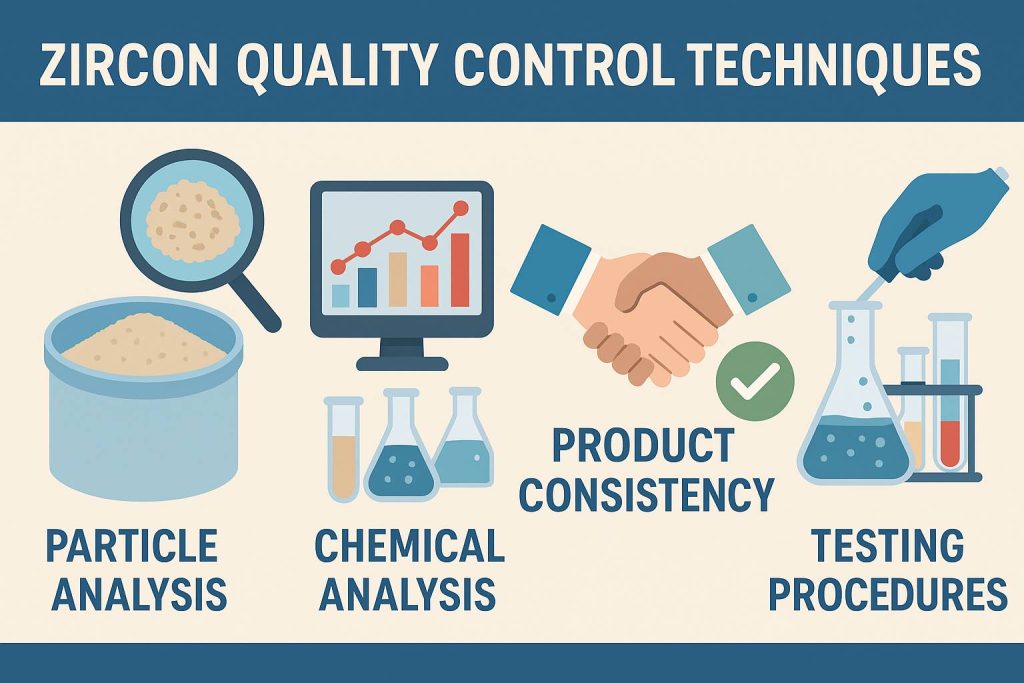
An infographic showcasing effective quality control methods in zircon powder production.
Conclusion
In summary, understanding the extraction techniques transforming zircon powder production is essential for any organization in the industry. With advancements in methods, chemical use, and environmental practices, companies can significantly enhance their operational efficiency. By implementing the insights shared in this article, you can achieve measurable improvements in production processes. Global Industry is here to help you along the way. Contact us today to discuss how we can support your zircon extraction needs and foster a successful partnership.
FAQ Section
Q1: What are the primary extraction techniques for zircon powder?
The extraction of zircon powder primarily involves three techniques: gravity separation, flotation, and magnetic separation. Gravity separation utilizes the difference in density to separate zircon from other minerals, while flotation employs chemical reagents to selectively attach to zircon particles, allowing them to float and be collected. Magnetic separation uses magnets to pull zircon from non-magnetic impurities, enhancing the purity of the final product. Each technique has its advantages depending on the mineralogical composition of the ore.
Q2: How do modern techniques increase efficiency in zircon extraction?
Modern extraction techniques have significantly improved the efficiency of zircon extraction by incorporating advanced technologies and equipment. For instance, automated sorting and sensor-based sorting systems enhance the speed and accuracy of separation. Additionally, innovations in processing, such as enhanced flotation methods and advanced gravity separation technologies, maximize yield while minimizing waste and energy consumption. These improvements not only increase output but also help reduce operational costs, making zircon extraction more economically viable.
Q3: What chemicals are typically used in zircon extraction?
The chemical processes involved in zircon extraction commonly utilize reagents such as sodium hydroxide and hydrochloric acid. Sodium hydroxide is often employed in the alkaline digestion process to break down the mineral matrix and release zircon, while hydrochloric acid helps to remove impurities by selectively dissolving non-zircon materials. Other reagents, depending on the specific extraction method and desired purity, may include sulfuric acid and various flotation agents. The choice of chemicals plays a crucial role in the overall efficiency and environmental impact of the extraction process.
Q4: What environmental impacts are associated with zircon powder production?
Zircon extraction can lead to several environmental impacts, including habitat disruption due to mining activities and the potential for chemical pollution from the reagents used in the extraction process. The removal of overburden may destroy local ecosystems, while leachate from tailings can contaminate local water sources. To address these issues, it is essential for zircon producers to adopt sustainable practices such as land rehabilitation, responsible waste management, and the implementation of measures to mitigate chemical runoff. Compliance with environmental regulations is also vital to reduce the ecological footprint of zircon extraction.
Q5: How can zircon powder producers stay competitive?
To maintain competitiveness in the zircon market, producers can adopt innovative extraction methods that enhance efficiency and reduce costs. This includes optimizing existing processes through the integration of new technologies and automation. Additionally, staying responsive to market trends and shifts in demand is crucial for strategic planning. Offering high-quality zircon powder tailored to specific customer requirements, along with transparency in sustainability efforts, can also provide a competitive edge. Finally, investing in research and development can lead to the discovery of more efficient extraction techniques and applications for zircon.