Industrial-grade zircon powder is a critical material across numerous high-performance applications, from refractories and ceramics to investment casting and specialized coatings. Its unique properties, particularly its high density and exceptional hardness, make it indispensable in environments demanding extreme durability and thermal stability. However, for purchasing managers and technical buyers, simply knowing that zircon is dense and hard isn’t enough. Understanding the precise density and hardness specifications is paramount to ensuring the material meets specific application requirements, optimizes performance, and ultimately, delivers cost-effectiveness.
This article delves into the essential density and hardness metrics that define industrial-grade zircon powder. We will explain their significance, measurement methods, and how they influence material selection for diverse industrial uses. Our aim is to equip B2B buyers with a clear, practical guide, enabling them to make informed procurement decisions and acquire the exact zircon powder suited for their operational needs.
What is industrial-grade zircon powder?
Industrial-grade zircon powder, derived from zirconium silicate (ZrSiO4), is a highly refined material crucial for various high-temperature and abrasive applications. Unlike raw zircon sand, this powder undergoes rigorous processing. This includes milling, purification, and classification to achieve specific particle size distributions, chemical purity, and physical properties.
But what truly sets it apart? Its exceptional refractory properties, chemical inertness, and high melting point (approximately 2550°C or 4622°F) make it an invaluable component in industries where extreme conditions are commonplace. This refined form is specifically engineered to meet the stringent demands of industrial processes, offering superior performance compared to less processed alternatives.
For instance, in the foundry industry, its low thermal expansion and high refractoriness prevent mold distortion and ensure dimensional accuracy of castings. In ceramics, it contributes to the strength, whiteness, and thermal shock resistance of products.
The distinction between industrial-grade and ordinary zircon powder lies in the consistency of its properties. These are critical for predictable performance in manufacturing. Ordinary zircon, often used as a raw material, may contain impurities or have a broader particle size distribution. This makes it unsuitable for precision applications where consistent performance is paramount.
Industrial-grade zircon powder, on the other hand, is meticulously controlled to ensure uniformity. This is a key factor for B2B buyers seeking reliable and high-quality materials for their production lines. This level of refinement ensures that the zircon powder performs consistently, reducing defects and improving efficiency in demanding industrial environments. The purity levels, often exceeding 99% ZrSiO4, are carefully monitored, as even trace impurities can significantly impact the material’s performance at elevated temperatures or in corrosive chemical environments. Therefore, understanding the specific grade and its intended application is vital for procurement professionals.
Why are density and hardness critical?
Density and hardness are not merely technical specifications; they are fundamental properties that dictate the performance, durability, and suitability of industrial-grade zircon powder in its diverse applications. Why should these metrics be at the forefront of a purchasing manager’s mind? The answer lies in their direct correlation with the material’s functional attributes.
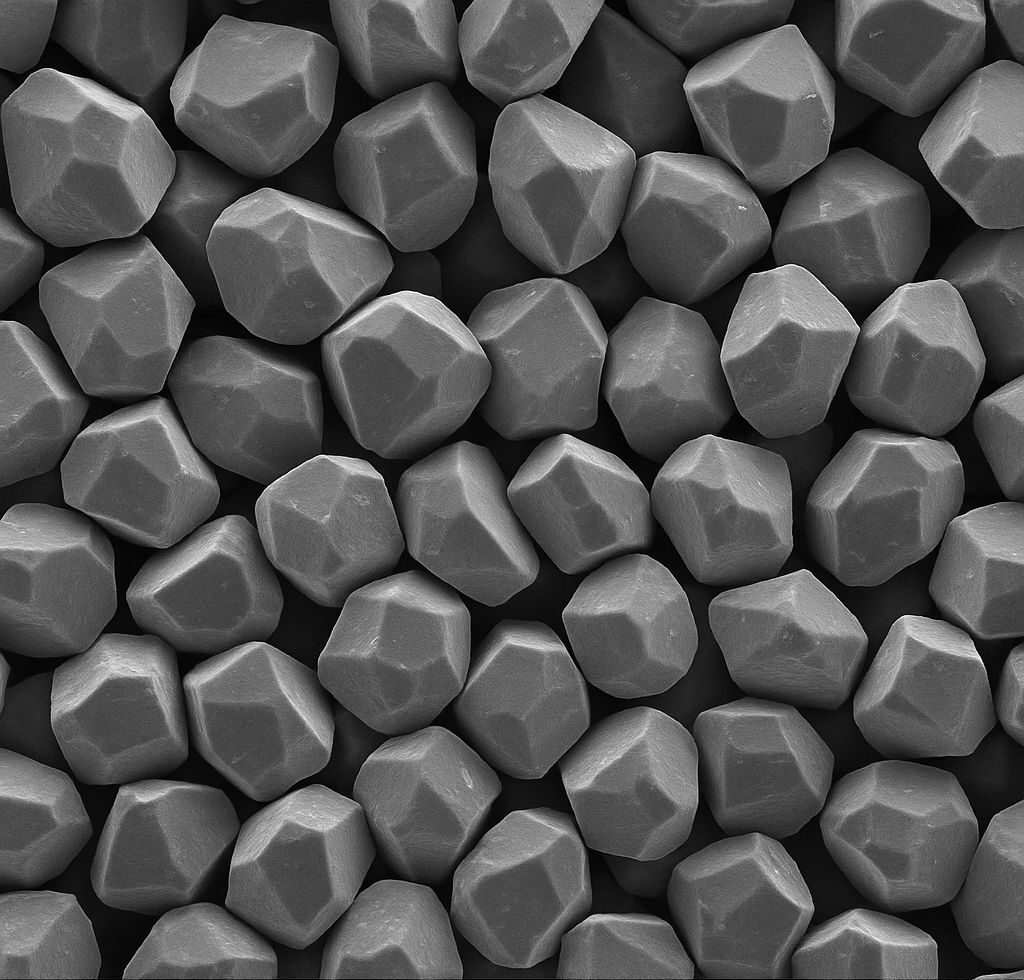
Density’s Role: True density (the density of the solid material itself, excluding pores) is crucial for applications requiring high mass per unit volume, such as heavy refractories or radiation shielding. A higher true density generally indicates a more compact and less porous material. This translates to superior thermal stability and resistance to chemical attack. For instance, in refractory linings, a dense zircon powder contributes to a longer service life by resisting penetration from molten metals and slags. It also influences the thermal conductivity and heat capacity of the final product, vital for energy efficiency in high-temperature furnaces.
Hardness’s Role: Hardness, on the other hand, measures a material’s resistance to scratching, abrasion, and indentation. For applications like grinding media, abrasive blasting, or wear-resistant coatings, the hardness of zircon powder directly determines its effectiveness and longevity. A harder zircon powder will maintain its sharp edges longer, providing superior cutting or grinding efficiency. It will also resist wear more effectively, extending the lifespan of components.
Conversely, a zircon powder with insufficient hardness for a given application will quickly degrade. This leads to increased material consumption, frequent replacements, and higher operational costs. Therefore, understanding and specifying the correct density and hardness values is not just about meeting a technical requirement. It’s about optimizing performance, reducing downtime, and ensuring the economic viability of the end product. These properties are particularly important when considering the material’s behavior under stress, whether mechanical stress from abrasion or thermal stress from extreme temperatures. They are the bedrock upon which the reliability and efficiency of zircon-based products are built.
How is zircon powder density measured?
Measuring the density of zircon powder is not a straightforward task, as different types of density are relevant for various applications. So, what are these different densities, and how are they determined?
There are primarily three types of density pertinent to powders:
● True Density: This refers to the density of the solid material itself, excluding any pores or voids within the particles or between them. It is an intrinsic property of the material. For zircon powder, the theoretical true density is approximately 4.65 g/cm³. This is typically measured using gas pycnometry (e.g., helium pycnometer). This method is highly accurate and is crucial for applications where the material’s inherent density is critical, such as in high-density ceramics or refractories.
● Bulk Density: This is the mass of the powder divided by the total volume it occupies, including the voids between particles. It’s a more practical measurement for handling, storage, and transportation, as it reflects how much material can fit into a given container. Bulk density is influenced by particle size, shape, and distribution, as well as the degree of compaction. It is usually measured by simply weighing a known volume of loosely packed powder.
● Tap Density: Similar to bulk density, but measured after the powder has been subjected to a standardized tapping procedure to achieve maximum compaction. This provides an indication of how much the powder can be compacted during processing, important for applications like powder metallurgy or tablet pressing. The difference between bulk and tap density, often expressed as the Carr Index or Hausner Ratio, can indicate the powder’s flowability and compressibility.
For B2B buyers, understanding which density measurement is relevant for their application is key. For example, a purchasing manager for refractory bricks might be more concerned with true density for performance, while a logistics manager might prioritize bulk density for shipping efficiency. Suppliers should provide clear specifications for the type of density measured and the method used. Below is a table summarizing these density types and their typical measurement methods:
Density Type | Definition | Measurement Method | Relevance for Buyers |
---|---|---|---|
True Density | Density of the solid material, excluding voids | Gas Pycnometry (e.g., Helium Pycnometer) | Material performance, intrinsic property |
Bulk Density | Mass of powder divided by total volume (including voids) | Weighing a known volume of loosely packed powder | Handling, storage, transportation efficiency |
Tap Density | Mass of powder divided by volume after tapping | Tapping machine (standardized procedure) | Flowability, compressibility, processing |
What hardness tests apply to zircon powder?
Hardness is a critical property for industrial-grade zircon powder, especially in applications where resistance to wear and abrasion is paramount. But how exactly is the hardness of such a fine powder quantified? Unlike solid materials where hardness can be measured directly on a surface, powders require indirect methods or measurements on compacted forms.
The most common hardness scales applicable to minerals like zircon include:
● Mohs Scale: This is a qualitative ordinal scale, from 1 (talc) to 10 (diamond), characterizing scratch resistance. Zircon typically has a Mohs hardness of 7.5, placing it among very hard minerals. While useful for general classification, the Mohs scale is less precise for industrial specifications.
● Vickers Hardness: For more quantitative measurements, Vickers hardness is often employed. This test involves indenting the material with a diamond indenter under a specific load and measuring the size of the resulting indentation. A smaller indentation indicates a harder material. These tests are typically performed on polished sections of consolidated zircon materials (e.g., sintered zircon ceramics) rather than the loose powder itself.
● Knoop Hardness: Similar to Vickers, Knoop hardness also uses a diamond indenter but with a rhombic-based pyramidal shape. This method is suitable for brittle materials and thin layers, and like Vickers, is applied to consolidated forms of zircon.
For powders, the hardness is often inferred from the hardness of the bulk material or by testing compacted pellets. Another relevant concept for powders is particle hardness, which relates to the individual particle’s resistance to fracture or deformation. This is particularly important for abrasive applications. Suppliers often provide a range for hardness, or refer to the Mohs scale for general guidance.
For B2B buyers, understanding the test method used by the supplier is as important as the hardness value itself, as different methods can yield varying results. It is also important to consider how the hardness of the powder translates to the performance of the final product. For example, a harder zircon powder might lead to a longer-lasting grinding wheel or a more durable refractory lining. Here’s a brief overview of relevant hardness tests:
Hardness Test | Principle | Application to Zircon Powder | Key Insight for Buyers |
---|---|---|---|
Mohs Scale | Scratch resistance | General classification (Zircon: 7.5) | Quick comparative understanding |
Vickers Hardness | Indentation with diamond indenter | On consolidated zircon materials | Quantitative measure of resistance to plastic deformation |
Knoop Hardness | Indentation with rhombic-based pyramidal diamond indenter | On consolidated zircon materials | Suitable for brittle materials and thin layers |
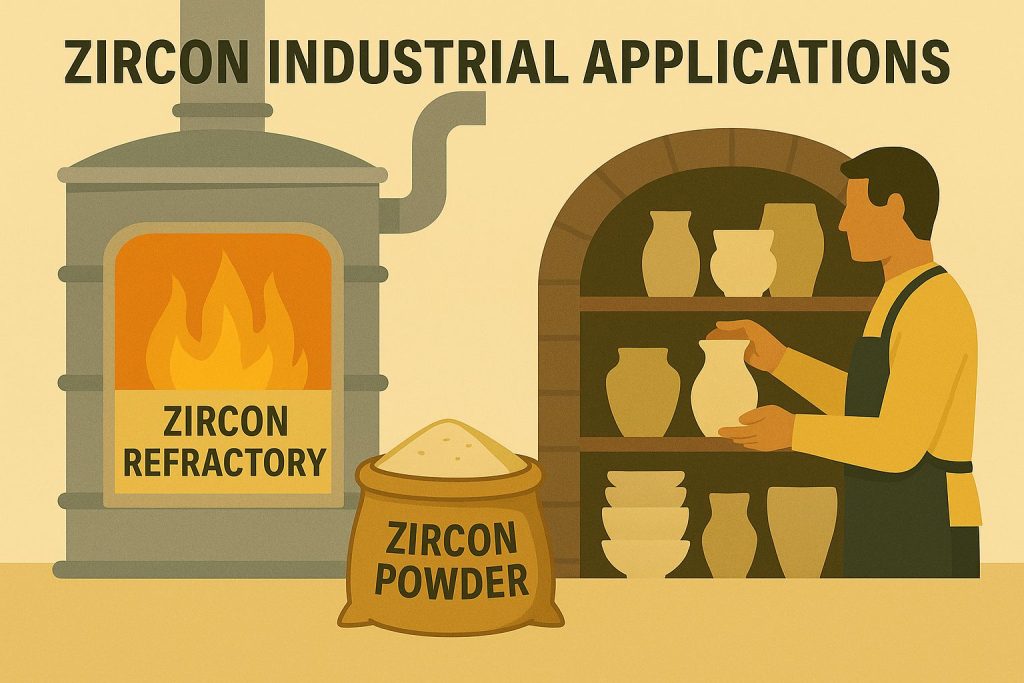
How do specs impact zircon powder uses?
The specific density and hardness specifications of industrial-grade zircon powder profoundly influence its suitability and performance across a wide array of applications. How do these technical details translate into real-world performance?
Impact on Refractories: In the refractory industry, high true density is critical for manufacturing dense, high-performance refractory bricks and castables used in furnaces and kilns. A denser material offers superior resistance to slag penetration and chemical attack, extending the lifespan of the refractory lining and reducing maintenance costs. For example, in glass furnaces, zircon refractories with optimized density contribute to improved thermal efficiency and reduced glass defects.
Impact on Ceramics: In the ceramic industry, both density and hardness play a role. For technical ceramics requiring high strength and wear resistance, a zircon powder with precise particle size distribution and high inherent hardness is essential. This ensures the final ceramic product can withstand harsh operating conditions. For example, in the production of ceramic glazes, the fineness and hardness of zircon powder affect the opacity and scratch resistance of the glaze.
Impact on Investment Casting: In the investment casting industry, zircon flour and sand are used to create molds for high-precision metal parts. Here, the density and particle shape influence the mold’s permeability and surface finish, while the refractoriness (linked to density) prevents mold degradation at high temperatures. A consistent density ensures uniform mold properties, which is vital for producing defect-free castings.
Impact on Abrasives: For abrasive applications, such as grinding wheels, sandpaper, or blasting media, the hardness of the zircon powder is the primary determinant of its effectiveness. A harder zircon particle will cut and abrade more efficiently and will resist breakdown longer, leading to superior performance and reduced consumption of abrasive materials.
Other Applications: Conversely, in some specialized applications like thermal insulation, a lower bulk density might be preferred to achieve better insulating properties, though this is less common for primary zircon powder applications. For pigments and opacifiers, consistent particle density is crucial for opacity and color consistency.
The table below illustrates how different applications prioritize specific density and hardness characteristics:
Application | Key Density Requirement | Key Hardness Requirement | Impact on Performance |
---|---|---|---|
Refractories | High True Density | Moderate to High | Resistance to slag, thermal stability, extended lifespan |
Technical Ceramics | High True Density | High | Strength, wear resistance, thermal shock resistance |
Investment Casting | Consistent Bulk Density | Moderate | Mold permeability, surface finish, thermal stability |
Abrasives | N/A (Particle Hardness) | High | Cutting efficiency, wear resistance, material consumption |
Pigments/Opacifiers | Consistent Particle Density | N/A | Opacity, color consistency, dispersion |
What industry standards define zircon powder?
To ensure consistency and quality, industrial-grade zircon powder is often produced and traded according to various industry standards. What are these standards, and why are they important for B2B buyers? These standards provide a common language and set of specifications that facilitate trade and ensure product reliability.
Key organizations and their standards include:
● ASTM International: Formerly American Society for Testing and Materials, ASTM publishes standards for a wide range of materials. While there isn’t one single ASTM standard exclusively for zircon powder, various test methods for particle size analysis, chemical composition, and density are applicable.
● ISO (International Organization for Standardization): ISO develops international standards, and specific ISO standards may apply to the testing and characterization of ceramic raw materials, which would include zircon powder.
Beyond these broad organizations, specific industry associations, such as those in the refractories or ceramics sectors, may develop their own guidelines or recommended practices for zircon powder. For example, the American Ceramic Society or the European Ceramic Society might have publications or technical committees that address the properties and testing of zircon.
Suppliers often adhere to these standards to demonstrate the quality and consistency of their products. For purchasing managers, understanding and verifying adherence to these standards is a crucial step in quality assurance and risk mitigation. It provides confidence that the zircon powder they procure will consistently meet the required performance criteria.
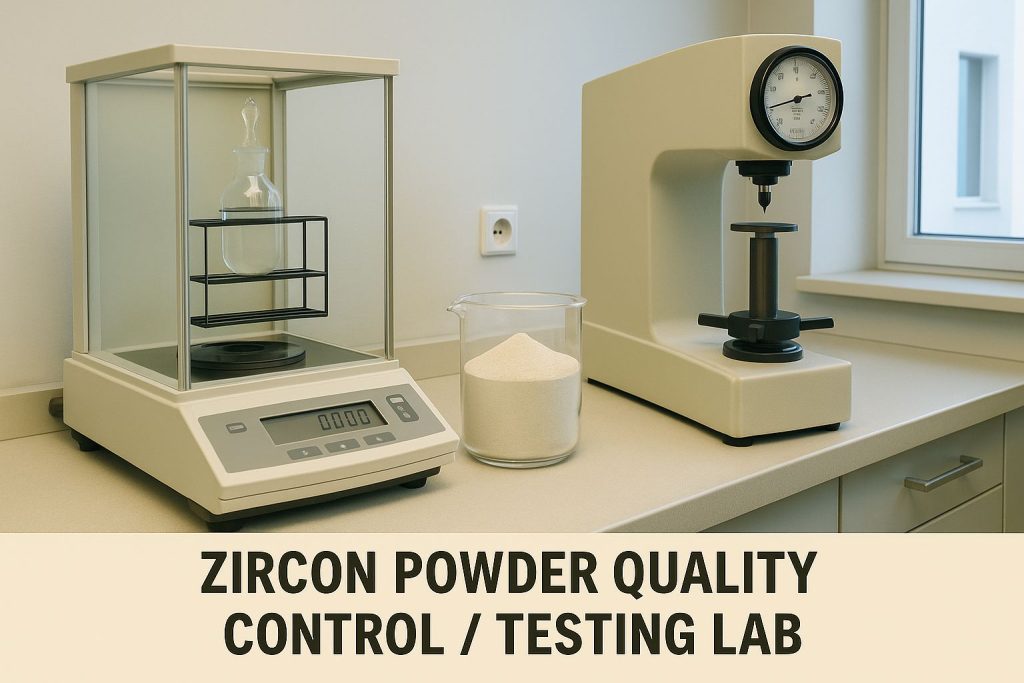
How to choose the right zircon powder?
Selecting the appropriate industrial-grade zircon powder requires a systematic approach that goes beyond simply looking at density and hardness numbers. What factors should purchasing managers consider to make an informed decision?
● Application Requirements: Thoroughly understand the specific demands of your application. Is it high-temperature refractory lining, abrasive blasting, precision casting, or a ceramic glaze? Each application will have unique requirements for density, hardness, particle size distribution, chemical purity, and thermal properties.
● Supplier Specifications: Always request detailed technical data sheets from potential suppliers. These documents should clearly outline the physical and chemical properties of the zircon powder, including measured density (specifying the type, e.g., true, bulk, tap) and hardness (specifying the test method). Compare these specifications against your application’s needs.
● Particle Size Distribution (PSD): While not directly density or hardness, PSD significantly impacts how the powder performs. A narrow PSD might be crucial for precision applications like investment casting or advanced ceramics, ensuring consistent packing density and surface finish.
● Chemical Purity: Impurities can significantly affect the performance of zircon powder, especially at high temperatures. Look for specifications on ZrSiO4 content and levels of impurities like TiO2, Fe2O3, and Al2O3. Higher purity often translates to better performance and stability.
● Consistency and Quality Control: Inquire about the supplier’s quality control processes. Consistent quality from batch to batch is paramount for maintaining stable production processes and product performance. Certifications (e.g., ISO 9001) can provide assurance of robust quality management systems.
● Technical Support and Expertise: A reputable supplier should offer technical support and be able to advise on the best zircon powder grade for your specific needs. Their expertise can be invaluable in troubleshooting and optimizing your processes.
● Cost-Benefit Analysis: While cost is always a factor, it should not be the sole determinant. A cheaper zircon powder that fails to meet performance requirements can lead to higher overall costs due to rework, material waste, and production downtime. Focus on the total cost of ownership and the value proposition.
By meticulously evaluating these factors, B2B buyers can confidently select the zircon powder that not only meets their technical specifications but also contributes to the efficiency and profitability of their operations.
Conclusion
In conclusion, understanding the precise density and hardness specifications of industrial-grade zircon powder is not merely a technical exercise but a strategic imperative for B2B buyers. These properties are fundamental to the material’s performance, durability, and suitability across a vast spectrum of high-demand industrial applications. From ensuring the longevity of refractory linings to optimizing the efficiency of abrasive media, the right specifications directly translate into enhanced product quality, reduced operational costs, and improved competitive advantage. By delving into the nuances of true, bulk, and tap densities, and appreciating the various hardness testing methodologies, purchasing managers can move beyond generic descriptions to make truly informed procurement decisions.
Furthermore, recognizing the impact of these specifications on specific applications and adhering to established industry standards are crucial steps in securing reliable and high-performing zircon powder. Ultimately, a comprehensive approach to material selection, one that meticulously considers application requirements, supplier specifications, particle characteristics, and quality control, empowers B2B buyers to acquire the exact zircon powder needed to drive innovation and achieve operational excellence. This detailed understanding ensures that every investment in zircon powder yields maximum value, reinforcing its role as an indispensable material in modern industrial processes.
FAQ
Q1: What is the primary difference between true density and bulk density for zircon powder?
True density refers to the density of the solid zircon material itself, excluding any pores or voids within or between particles. It’s an intrinsic property. Bulk density, conversely, includes the volume of voids between particles, reflecting how much powder fits into a given space. True density is key for material performance, while bulk density is important for handling and storage.
Q2: Why is Mohs hardness less precise for industrial zircon powder specifications compared to Vickers or Knoop?
Mohs hardness is a qualitative scratch resistance scale, useful for general mineral classification. Vickers and Knoop are quantitative indentation hardness tests, providing more precise numerical values. For powders, Vickers and Knoop are typically applied to consolidated forms (e.g., sintered ceramics) to give a more accurate measure of the material’s resistance to deformation under load, which is more relevant for industrial performance.
Q3: How does particle size distribution (PSD) relate to density and hardness in zircon powder applications?
While not a direct measure of density or hardness, PSD significantly influences how the powder packs (affecting bulk and tap density) and how individual particles interact in abrasive or ceramic applications. A precise PSD can optimize packing density, improve flowability, and ensure consistent performance in processes like investment casting or ceramic manufacturing, indirectly impacting the effectiveness of the material’s inherent density and hardness.
Q4: What role do industry standards play in procuring zircon powder?
Industry standards (e.g., from ASTM, ISO) provide a common framework for specifying and testing zircon powder properties. Adhering to these standards ensures consistency, quality, and reliability across different suppliers and batches. For B2B buyers, relying on standardized specifications simplifies procurement, reduces risks, and provides assurance that the material meets defined performance benchmarks.
Q5: Can a zircon powder be too hard for certain applications?
While hardness is generally desirable for wear resistance, in some niche applications, excessive hardness combined with brittleness might be a concern, leading to particle fracture rather than effective abrasion or polishing. However, for most industrial applications of zircon powder, higher hardness (within the material’s inherent limits) is beneficial for durability and performance, especially in abrasive or high-wear environments. The key is to match the hardness to the specific demands of the application to optimize performance without introducing other issues.