The milling process of zircon sand is a critical step in its transformation from raw material to usable product. For businesses in industries like ceramics, glass manufacturing, and refractories, understanding how this process works is essential. The milling process not only impacts the particle size and consistency of zircon sand but also affects its application in various products. If you’re involved in purchasing zircon sand for industrial use, you need to understand these processes to ensure quality, cost-effectiveness, and efficiency.
In this article, we will break down how the milling process works, why it’s important, and how you can make informed decisions about your zircon sand sourcing. Let’s explore the core aspects of zircon sand milling and provide valuable insights for your business needs.
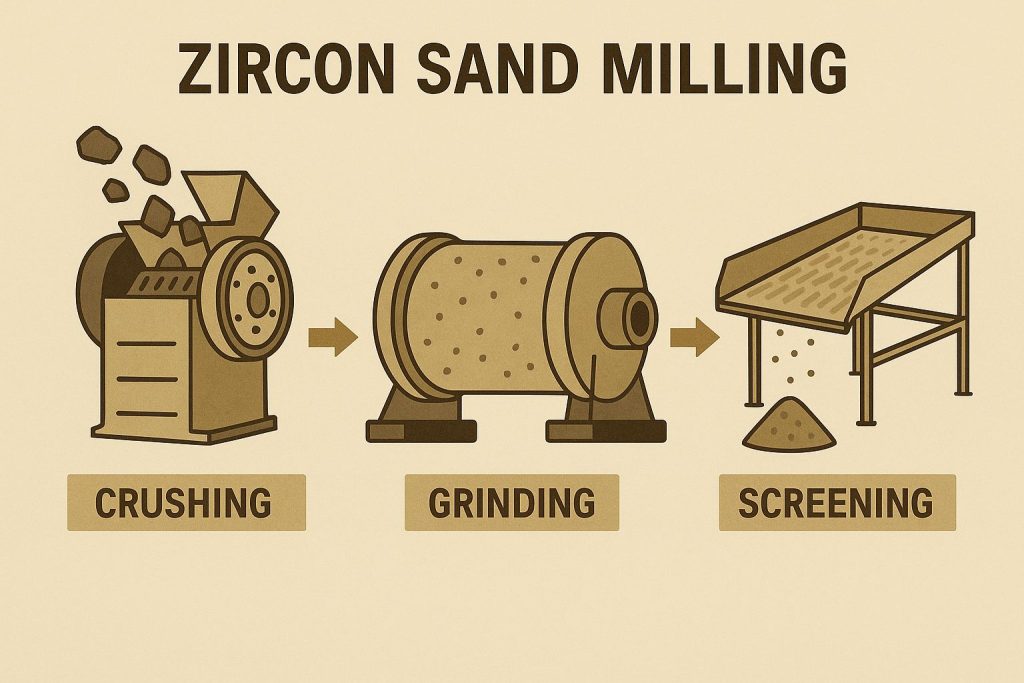
This image shows the zircon sand milling process with detailed stages like crushing, grinding, and screening.
What Is the Milling Process of Zircon Sand?
The milling process of zircon sand refers to the mechanical process of reducing the particle size of the sand, which enhances its usability in industrial applications. Essentially, this process involves grinding, crushing, and sometimes blending the raw material to achieve the desired consistency.
● Overview of zircon sand and its industrial importance
Zircon sand is primarily made up of zirconium silicate (ZrSiO₄), and it is a key raw material in the production of various products, including ceramics, glass, and refractory materials. It is highly valued due to its thermal stability and chemical resistance.
● Introduction to the milling process
Milling zircon sand usually begins with raw zircon being processed in specialized mills that use grinding media to reduce its particle size. The objective is to produce a fine powder that can be easily used in other manufacturing processes. This finely milled material ensures consistency in product performance across industries.
● Key stages of milling zircon sand
- Initial crushing: The raw zircon is first crushed into smaller fragments.
- Grinding: These fragments are then ground using mills, such as ball mills or roller mills, to further reduce their size.
- Screening and sorting: The milled sand is sorted according to particle size to ensure uniformity.
By the end of the process, the zircon sand is finely ground and ready for various industrial applications.
How Does Milling Affect Zircon Sand’s Properties?
Milling zircon sand alters its physical and chemical properties, making it more suitable for different applications. This section highlights the key impacts of milling on zircon sand.
● Impact on grain size
Milling significantly reduces the size of zircon grains, which is crucial for industries that require high precision, such as ceramics and glass production. The smaller the grain size, the better the material can be processed for these specialized products.
● Changes in chemical properties during milling
The grinding process can sometimes alter the chemical makeup of the zircon sand. The increased surface area resulting from smaller particle sizes may lead to increased reactivity, which can be advantageous in specific applications, such as in the production of certain types of glass or in chemical processes requiring high purity.
● Physical property alterations
The reduction in particle size also affects the hardness, density, and porosity of the zircon sand. These changes can improve its thermal stability, which is particularly valuable in industries like refractories, where high resistance to heat is necessary.
Bolded Phrase: Here’s the deal—milling is not just about making the material smaller; it’s about ensuring that it meets the specific requirements of various industries.
Table 1: Impact of Milling on Zircon Sand’s Properties
Property | Before Milling | After Milling |
---|---|---|
Particle Size | Coarse grains | Fine powder |
Chemical Reactivity | Low | Increased surface area |
Thermal Stability | Moderate | Improved |
What Equipment Is Used in Zircon Sand Milling?
The milling process of zircon sand involves a variety of machines, each with its unique role in achieving the desired material properties.
● Common milling machinery and their functions
The most common equipment used for milling zircon sand includes ball mills, vertical mills, and jet mills. These machines utilize different grinding techniques to achieve fine particle sizes.
● Role of ball mills in zircon sand milling
Ball mills are often the go-to option for zircon milling. They consist of rotating cylindrical drums filled with grinding media, such as steel balls, which help break down the zircon sand through impact and friction.
● Advanced milling technologies
Some modern facilities use more advanced milling techniques like jet milling. Jet mills use high-velocity air streams to grind materials without the need for grinding media, offering advantages in terms of fine control over particle size.
Bolded Phrase: You might be wondering, what makes these mills so effective for zircon sand processing? It’s the controlled energy that allows for precise size reduction.
Table 2: Comparison of Milling Equipment
Milling Equipment | Primary Function | Advantages | Common Applications |
---|---|---|---|
Ball Mill | Grinding raw zircon sand | High capacity, simple operation | General purpose milling |
Vertical Mill | Reduces particle size using grinding discs | Higher efficiency, less wear | Fine grinding of zircon sand |
Jet Mill | Uses air streams to grind | Produces very fine particles | Specialized high-purity applications |
Why Is Milling Important for Zircon Sand Processing?
Milling plays a pivotal role in optimizing zircon sand for various industrial uses. The main reason for milling is to adjust the particle size and consistency, which directly affects the quality and performance of the final product.
● Milling’s role in increasing efficiency in downstream processes
Smaller and more uniform particle sizes lead to more efficient processing in subsequent stages, such as blending, firing, or molding. This reduces waste and enhances the overall yield in manufacturing processes.
● Importance of consistent particle size for quality control
In industries like ceramics and glass, even minor variations in particle size can affect the final product. Milling ensures that zircon sand is of uniform quality, minimizing defects in finished goods.
● Applications that benefit from properly milled zircon sand
Industries such as refractory manufacturing, ceramics, and glass production rely heavily on properly milled zircon sand to ensure high-quality, durable, and consistent products.
Bolded Phrase: Here’s the deal—without efficient milling, the entire production process may be compromised, leading to inconsistencies and higher costs.
Table 3: Applications of Milled Zircon Sand
Industry | Application | Role of Milled Zircon Sand |
---|---|---|
Ceramics | Production of tiles, porcelain | Improved particle size and surface finish |
Glass Manufacturing | High-performance glass | Enhanced strength and clarity |
Refractories | Heat-resistant materials | Better thermal stability and durability |
How Are Different Milling Techniques Applied to Zircon Sand?
Different milling techniques can be applied depending on the required particle size and the specific application for the zircon sand.
● Overview of dry vs. wet milling
Dry milling involves grinding zircon sand without the use of liquids, while wet milling uses a slurry of water or other liquids. The choice of method affects the final product’s particle size, distribution, and properties.
● Advantages of each method in zircon sand processing
Dry milling is typically faster and easier to control, but wet milling can achieve finer particle sizes. Each method has its benefits, depending on the needs of the specific industry.
● Case studies of zircon sand milling methods used in industry
In glass manufacturing, wet milling is often used to produce ultra-fine zircon sand, while dry milling is favored in refractory applications where larger particles are acceptable.
Bolded Phrase: You might be wondering—which milling method is best? The answer depends on the final product’s requirements.
Table 4: Wet vs Dry Milling of Zircon Sand
Method | Particle Size | Efficiency | Common Uses |
---|---|---|---|
Wet Milling | Finer particles | Higher energy consumption | Glass, ceramics |
Dry Milling | Coarser particles | Lower energy consumption | Refractories, construction |
What Are the Challenges in Zircon Sand Milling?
While milling zircon sand offers many benefits, several challenges arise during the process that can affect efficiency and product quality.
● Common issues faced in the milling process
Milling zircon sand can be challenging due to its hardness, which can cause excessive wear on milling equipment. Furthermore, achieving uniform particle sizes may require fine-tuning of milling parameters.
● Equipment maintenance and wear
The grinding media in ball mills can wear down over time, which can result in inconsistent milling and additional costs. Regular maintenance is crucial to keep equipment running efficiently.
● Overcoming challenges related to particle distribution
Achieving the ideal particle size distribution can be tricky. Overgrinding can lead to excessive fines, while undergrinding results in large, unusable particles.
Bolded Phrase: But here’s the catch—while these challenges are common, they can be mitigated with the right equipment and techniques.
Table 5: Common Milling Challenges and Solutions
Challenge | Impact | Solution |
---|---|---|
Equipment wear | Decreased efficiency and product quality | Regular maintenance and upgrades |
Particle size variation | Inconsistent product quality | Fine-tuning milling parameters |
Overgrinding | Excessive fines, wasted material | Optimizing grinding time and speed |
How Can Milling Efficiency Be Improved in Zircon Sand Processing?
Improving the milling process can significantly enhance efficiency and reduce costs in zircon sand production.
● Best practices for improving milling efficiency
Implementing advanced control systems and regular equipment maintenance can increase milling efficiency. Fine-tuning operating parameters like speed and temperature also helps optimize the process.
● Role of technology in optimizing milling processes
New technologies, such as automation and sensor-based controls, allow for more precise milling operations. This leads to fewer interruptions, reduced waste, and better consistency in the final product.
● Potential innovations in zircon sand milling
Ongoing innovations in milling equipment and processes, such as the development of more energy-efficient mills, promise to further improve zircon sand milling efficiency.
Bolded Phrase: Here’s the deal—small adjustments in the milling process can lead to big improvements in quality and cost.
What Are the Environmental Considerations in Zircon Sand Milling?
The environmental impact of milling zircon sand is an important factor to consider, especially as industries increasingly focus on sustainability.
● Energy consumption during milling
Milling zircon sand is an energy-intensive process. Companies must explore ways to reduce energy use without compromising efficiency, such as investing in energy-efficient equipment.
● Environmental impact of zircon sand milling waste
The waste generated during milling, including dust and by-products, can contribute to environmental pollution. Proper waste management practices, such as recycling and waste reduction, are essential.
● Sustainable milling practices in the zircon industry
Sustainability can be achieved through various practices, such as using renewable energy sources for milling operations or reducing water usage in wet milling processes.
Bolded Phrase: You might be wondering—how can we make milling more eco-friendly? The answer lies in smarter technology and better resource management.
How Does Zircon Sand Milling Affect the Final Product?
Milling is one of the first steps in transforming raw zircon sand into a usable product. The final product’s quality and performance depend heavily on how well the milling process is executed.
● The relationship between milling and end-product quality
Milled zircon sand must meet specific size and purity standards to be suitable for high-performance applications like ceramics and refractories.
● How milling impacts zirconium-based products
Zirconium products, such as zirconia, require finely milled zircon sand to achieve optimal properties. The correct milling process can ensure high-quality zirconium-based materials.
● Performance testing of milled zircon sand in different industries
Milled zircon sand is tested for various properties, such as its ability to withstand high temperatures, which is essential in refractory and ceramics applications.
Bolded Phrase: Here’s the deal—proper milling directly influences product performance across industries.
How Do Milling Parameters Impact Zircon Sand’s Industrial Applications?
Understanding how milling parameters affect zircon sand is crucial for ensuring its suitability for specific applications.
● Influence of milling time on zircon sand properties
Longer milling times can produce finer particle sizes, which are essential for applications like glass production but may not be necessary for refractory uses.
● Temperature and speed control during milling
Controlling milling temperature and speed helps to achieve the desired particle size and consistency.
● Optimizing milling conditions for various applications
The optimal milling conditions depend on the specific requirements of the final product. Adjusting parameters ensures that the zircon sand meets industry standards.
Bolded Phrase: But here’s the catch—finding the right milling parameters can make all the difference in product performance.
What Are the Economic Impacts of Zircon Sand Milling?
Milling zircon sand is not only a technical process but also has economic implications. Understanding these impacts can help businesses make better decisions when investing in zircon sand milling.
● Cost factors involved in zircon sand milling
Milling requires significant capital investment in equipment and energy. However, properly milled zircon sand can reduce waste and improve manufacturing efficiency, offering a return on investment.
● Economic benefits of improved milling techniques
Upgrading milling technology can improve efficiency, reduce energy consumption, and lower costs in the long run, benefiting both manufacturers and end-users.
● The role of milling in the global zircon market
Efficient milling processes can enhance the competitiveness of zircon sand suppliers in the global market, driving down prices and increasing availability.
Bolded Phrase: You might be wondering—how can zircon sand milling affect my bottom line? Efficient milling techniques offer both cost savings and competitive advantages.
What Are the Future Trends in Zircon Sand Milling Technology?
The milling process continues to evolve, and future trends in technology are likely to bring more advancements and efficiency improvements.
● Emerging technologies for improved milling
Automation and AI-driven systems are expected to play a larger role in zircon sand milling, leading to more precise control over particle size and faster processing times.
● The potential of automation in zircon sand milling
Automated systems can help reduce human error, enhance efficiency, and lower costs in the zircon sand milling process.
● How innovations will shape the future of zircon sand processing
New technologies will likely focus on reducing energy consumption, increasing milling precision, and improving overall sustainability.
Bolded Phrase: Here’s the deal—the future of zircon sand milling looks promising, with exciting innovations on the horizon.
Conclusion
In this article, we’ve explored how the milling process of zircon sand works, its impact on properties, and the role it plays in various industries. Understanding these aspects can help you make informed decisions when sourcing zircon sand for your business. By optimizing the milling process, you can ensure consistent product quality, improve efficiency, and lower costs. At Global Industry, we offer high-quality zircon sand and milling solutions tailored to your needs. Contact us today for more information and to discuss how we can support your production process.
FAQ Section
Q1: What is the purpose of milling zircon sand?
Milling zircon sand is done to reduce its particle size, making it suitable for various industrial applications such as ceramics and glass manufacturing.
Q2: How does zircon sand milling affect its chemical properties?
Milling increases the surface area of zircon sand, which can enhance its reactivity and suitability for certain applications, such as glassmaking.
Q3: What types of equipment are used in zircon sand milling?
Ball mills, vertical mills, and jet mills are commonly used to mill zircon sand, each providing different benefits depending on the desired particle size.
Q4: Are there environmental concerns associated with zircon sand milling?
Yes, milling zircon sand consumes a significant amount of energy and generates waste. Sustainable practices can help mitigate these environmental impacts.
Q5: How do milling parameters like time and temperature affect zircon sand?
Milling time and temperature affect the particle size and consistency of zircon sand, which in turn impacts its quality and suitability for various applications.