Steel makers everywhere face the same headache. Refractory linings inside their furnaces break down too fast, leak heat, and force costly shutdowns. When a lining fails, production stops and profits slip away. Many cheap materials can’t handle the intense heat and constant chemical attack that steel plants throw at them daily. Here’s the good news — zircon sand changes the game. With its high heat resistance and tough structure, zircon sand keeps furnace linings strong and stable much longer than traditional options. This means less downtime, safer operations, and real savings over time.
In this guide, I’ll show you exactly why zircon sand remains a trusted choice for steel linings, how it delivers clear value for plant managers, and what you need to know to make the best use of it in your own steel production.
Why Do Steel Linings Need Zircon Sand?
A furnace works under brutal conditions every single day. Inside, molten metal flows and temperatures soar above 1,500°C. The lining must hold firm to protect the furnace walls and keep workers safe. You might wonder, why do so many plants now rely on zircon sand?
The answer is simple: reliability. Many old linings made of standard clay or silica cannot take repeated heating and cooling. They crack, crumble, and let heat escape. Each repair means lost production time and higher labor costs. When a plant uses zircon, these problems shrink fast.
Zircon forms a dense shield that blocks heat loss and reduces thermal stress. It’s not just about surviving heat — it’s about staying solid while handling molten slag and chemical attack. Operators notice fewer breakdowns and smoother output. Some large steel mills report doubling their lining lifespan after switching to high-grade zircon.
Maintenance teams back this up with real numbers. They spend less time patching walls and more time running batches. That reliability keeps orders on track and clients happy.
Take a look at this comparison to see why zircon stands out.
Refractory Material | Max Service Temp (°C) | Typical Lifespan (Months) |
---|---|---|
Zircon Sand | 1,750 | 12–24 |
Silica | 1,600 | 6–12 |
Alumina | 1,700 | 8–14 |
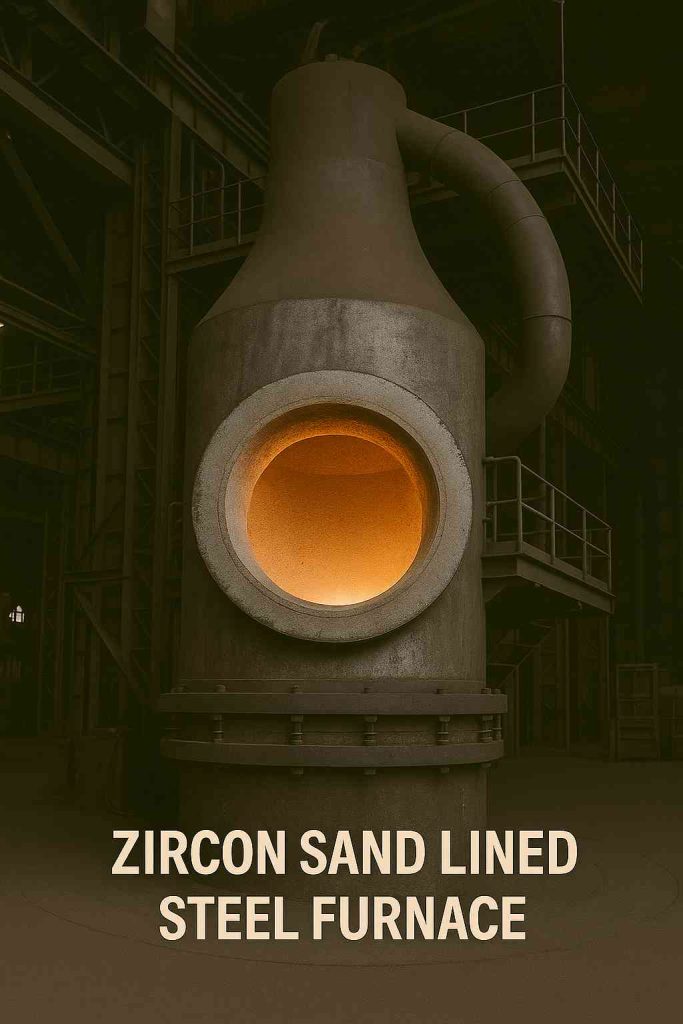
This image shows a blast furnace lined with high-purity zircon sand to withstand intense heat cycles.
Zircon not only endures heat but also cuts unexpected repair costs. Plant managers love this because fewer stops mean more steel and stronger profits. When considering new lining material, this mineral often sits at the top of the shortlist for serious producers who need consistency and safety day in and day out.
This image shows a blast furnace lined with high-purity zircon sand to withstand intense heat cycles.
How Does Zircon Sand Improve Thermal Performance?
High heat is the biggest test for any furnace lining. Every steel batch pushes the inner walls to their limits. Cheap linings struggle here. They crack when heat jumps quickly or when cool air hits during shutdowns. Let’s break this down — zircon sand handles thermal stress better than most alternatives.
The secret lies in its high melting point, close to 2,550°C. This means it stays rock solid even when steel melts and slag splashes against the lining. Where other materials weaken and allow heat to leak, zircon holds firm. This stops energy loss, which helps keep fuel costs in check.
A good lining must do more than just survive extreme heat. It must expand and contract without cracking apart. Zircon sand’s unique structure allows smooth thermal expansion. Fewer cracks mean fewer emergency fixes and a safer work environment for the crew.
A medium-sized mill in Southeast Asia tested zircon-based linings in their ladle furnaces. After 12 months, thermal loss dropped by 15%. This meant the plant saved on fuel and kept a more stable production schedule, even during peak demand.
Let’s compare how zircon stacks up next to other materials that plants often use:
Property | Zircon Sand | Alumina | Silica |
---|---|---|---|
Melting Point (°C) | 2,550 | 2,072 | 1,710 |
Thermal Conductivity (W/mK) | 2.5 | 30 | 1.4 |
Thermal Expansion (x10⁻⁶/K) | 4.5 | 8.1 | 0.55 |
Low thermal conductivity is also helpful. It means heat stays inside the furnace instead of leaking out through the walls. With more heat where it’s needed, melting and processing become faster and more efficient. Plants see this on their energy bills month after month.
Here’s what it means for your operations — stronger linings hold steady through countless heat cycles. Production keeps running without surprise halts for patching cracks or replacing bricks. Over time, this reliability turns into real money saved and less stress for maintenance teams.
For any steel manager aiming to run lean and steady, zircon sand is a trusted guard against thermal stress. It helps every furnace keep its heat where it belongs: inside melting steel, not escaping into the air.
What Are the Chemical Stability Advantages?
Steel production tests linings in two tough ways — extreme heat and harsh chemical attack. Molten steel and aggressive slags wear down weaker materials fast, leading to leaks and costly downtime. Let’s get clear on this — zircon sand stands firm where others fail.
This mineral has a tight crystal structure that resists acids, alkalis, and metal oxides. Compared to basic fireclay or magnesite, zircon sand shows far less erosion when exposed to corrosive slags. This extra stability means fewer breakdowns, less surprise maintenance, and more reliable production runs.
A steel plant in Eastern Europe made a smart switch to zircon-based linings for their ladles and tundishes. Before, chemical erosion forced them to replace linings twice a year. After using zircon sand, replacement dropped to once every 18 months, saving labor and keeping hot metal flowing without long stoppages.
Cleaner walls are another plus. With zircon, slag buildup drops sharply. Less slag means smoother heat flow and quicker clean-outs. Workers spend fewer hours scraping off hardened slag, which means faster turnarounds after scheduled maintenance.
Check this data — it shows how zircon sand stays strong against chemical wear.
Chemical Resistance | Zircon Sand | Magnesite | Fireclay |
---|---|---|---|
Acid Resistance | High | Medium | Low |
Alkaline Resistance | High | High | Medium |
Erosion Rate (mm/year) | 0.5 | 1.2 | 2.0 |
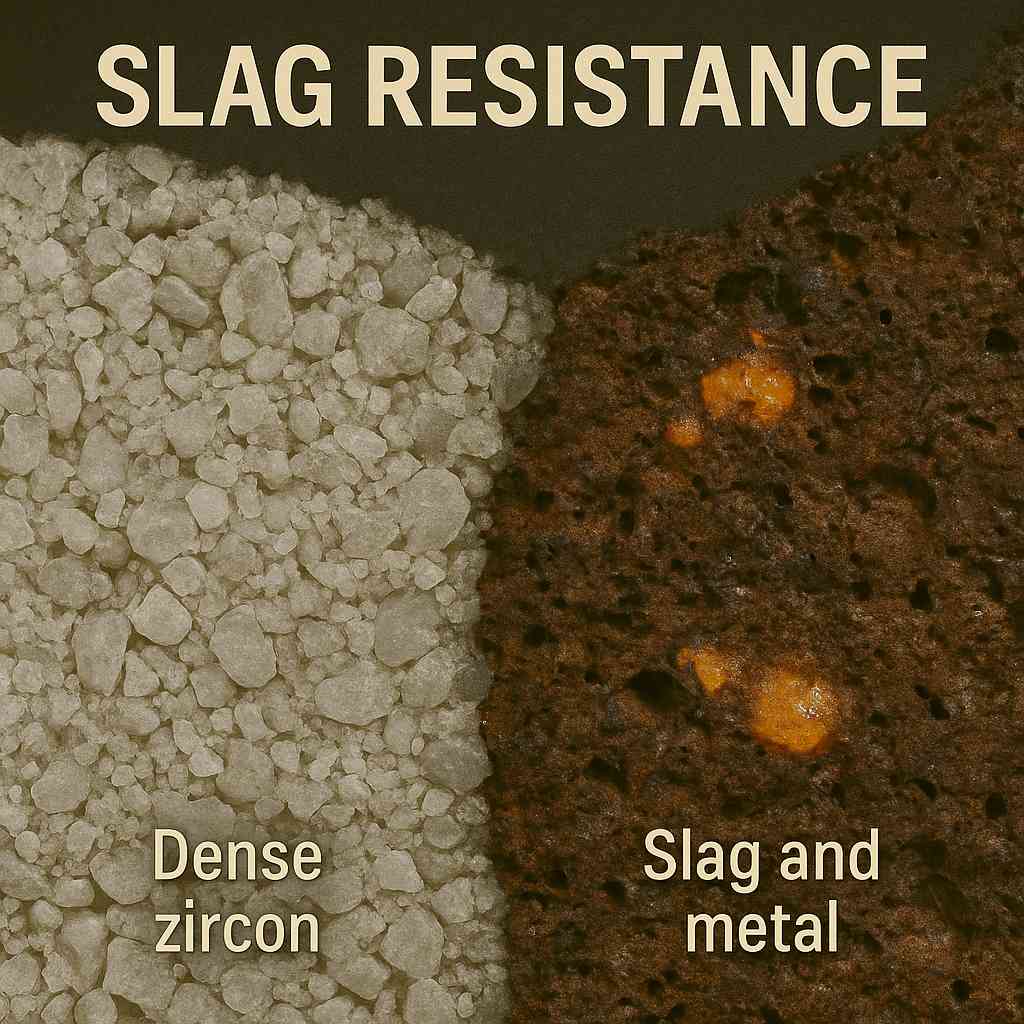
This image shows how zircon’s tight crystal bonds protect furnace linings from harsh slags and molten metal.
All this adds up to real money saved. Less erosion means longer service life and smoother steel output. Plant managers see fewer headaches and steadier profits — all thanks to zircon’s unmatched chemical durability inside every furnace wall.ical attack from molten slag.
How Does Zircon Sand Strengthen Mechanical Durability?
A lining must handle more than heat and chemicals. It needs the muscle to stay strong while the furnace roars and cools day after day. Weak linings buckle under the constant push and pull of thermal expansion. They form cracks, break into chunks, and tumble into molten steel. Here’s where zircon makes a difference — it stands tough even in punishing conditions.
Zircon sand particles pack tightly together. This tight packing creates a dense structure that resists breaking under weight and sudden shifts in temperature. The result? A lining that stays solid longer, even when the furnace runs non-stop.
Think about a basic fireclay lining. It handles moderate heat but loses strength quickly if temperature changes too fast. Plant teams often see chunks break away during tapping or slag cleaning. That means sudden downtime, patch jobs, and sometimes accidents if hot metal hits a weak spot.
In a well-known case study, a foundry in India replaced its old clay-based ladle linings with a zircon mix. After six months, operators reported 60% fewer cracks and almost no falling debris during tap-out. They needed fewer patch jobs, which freed workers to focus on production, not repairs.
The secret is zircon’s low thermal expansion rate and good shock resistance. Even if the furnace cools and heats up dozens of times, the lining stays bonded tight to the wall. This helps prevent gas leaks and keeps the furnace safe for longer production runs.
Look at this simple strength check:
Mechanical Property | Zircon Sand | Standard Fireclay |
---|---|---|
Flexural Strength (MPa) | 15 | 5 |
Thermal Shock Resistance | High | Medium |
Compressive Strength (MPa) | 70 | 40 |
Numbers alone don’t tell the whole story. Maintenance crews often say they trust zircon because it “just stays put.” This confidence lowers stress for both supervisors and floor teams. A stronger lining means fewer unplanned repairs, better worker safety, and more steel poured without fear of failure.
Here’s the takeaway — using zircon sand is like reinforcing your furnace with a hidden armor. It holds firm under high loads and harsh cycles, keeping operations smooth and giving plant managers more sleep at night.
What Is the Impact on Operational Costs?
Every plant manager knows that saving money doesn’t always mean buying the cheapest material upfront. Sometimes, spending more at the start cuts hidden costs later. This is exactly the story with zircon sand in steel linings. Let’s unpack this carefully — what looks pricey at first often proves to be a smart cost reducer when you run the numbers year after year.
Basic linings like fireclay cost less per ton, sure. But they break down sooner, let heat escape, and need constant patching. Each patch means downtime, labor costs, and energy loss. Frequent shutdowns also throw off production schedules and force extra overtime pay to catch up on lost output.
Zircon sand changes this budget equation. It holds up longer, so the furnace keeps running with fewer interruptions. Plants that switch to zircon often report needing half as many full relinings each year. That alone saves thousands in material costs and labor hours. Plus, less downtime means more steel made on time and happier customers who stick around.
One mid-sized mill in South America shared data showing how lining costs shifted. Their annual spend on standard bricks and emergency fixes used to reach $150,000 per furnace. After switching to zircon linings, they paid around $60,000 more upfront but cut unplanned shutdowns by 40%. The result? Total yearly lining-related costs dropped by 27% once lost production and overtime were factored in.
See how these numbers stack up in a simple table:
Cost Element | Without Zircon | With Zircon |
---|---|---|
Average Annual Lining Cost | $50,000 | $60,000 |
Downtime Losses | $100,000 | $50,000 |
Total Annual Cost | $150,000 | $110,000 |
Here’s another hidden saving — energy bills shrink too. Since zircon sand blocks heat loss better, less fuel burns to keep the steel at the right melt point. Over months, this lower fuel usage becomes real money back in the budget.
There’s also a workforce benefit. Maintenance crews spend fewer nights patching walls and more time on preventive tasks that extend equipment life elsewhere in the plant.
So when the finance team asks why the budget includes premium zircon sand, smart plant managers point to the bigger picture: more uptime, steady production, and a safer, more reliable operation. And in the steel business, that edge makes all the difference between profit and loss in tough markets.
How Is Zircon Sand Applied in Linings?
Choosing zircon sand is only half the plan. How you use it decides how much value you really get. Let’s get into the details — proper application ensures you squeeze every bit of performance from this mineral.
Steel plants can’t just pour zircon sand into a furnace wall and expect miracles. It comes in different forms, each tailored for a specific need. The three most common are pre-shaped bricks, castable mixes, and spray coatings.
Bricks are ready-made blocks. Workers stack and mortar them inside the furnace walls. They are thick and tough, built to handle areas where molten metal hits hardest. For spots under constant mechanical wear, bricks hold shape the best.
Castables are more flexible. Think of them like a high-performance concrete. Workers mix zircon sand with binders and pour or pack it into custom shapes. They use castables to line curved spaces, odd corners, or repair large patches without needing whole new bricks.
Spray coatings come into play when time is tight. Teams mix zircon slurry and spray it over worn spots. It dries fast and forms a fresh protective barrier. This patch method keeps production rolling without needing a long shutdown for major repairs.
Getting the mix right is key. Too much binder or water makes castables weak and prone to cracks. Too little binder leaves gaps where heat can slip through. Many steel plants follow strict recipes — often guided by refractory suppliers — to make sure every batch sets with uniform strength.
Take a look at this snapshot of typical uses:
Application Method | Use Area | Key Benefit |
---|---|---|
Bricks | Furnace walls | High wear resistance |
Castables | Custom shapes | Flexibility |
Spray Coatings | Quick repairs | Fast turnaround |
One large foundry in Turkey improved furnace life by switching from clay bricks to a combination of zircon bricks for the high-wear belly zone and castables for the dome. This hybrid approach matched each zone with the right material and cut lining maintenance costs by 30% over two years.
Remember this point — proper installation training matters too. Skilled workers ensure bricks fit tight, castables cure correctly, and coatings bond well. Even the best zircon sand fails if installed poorly.
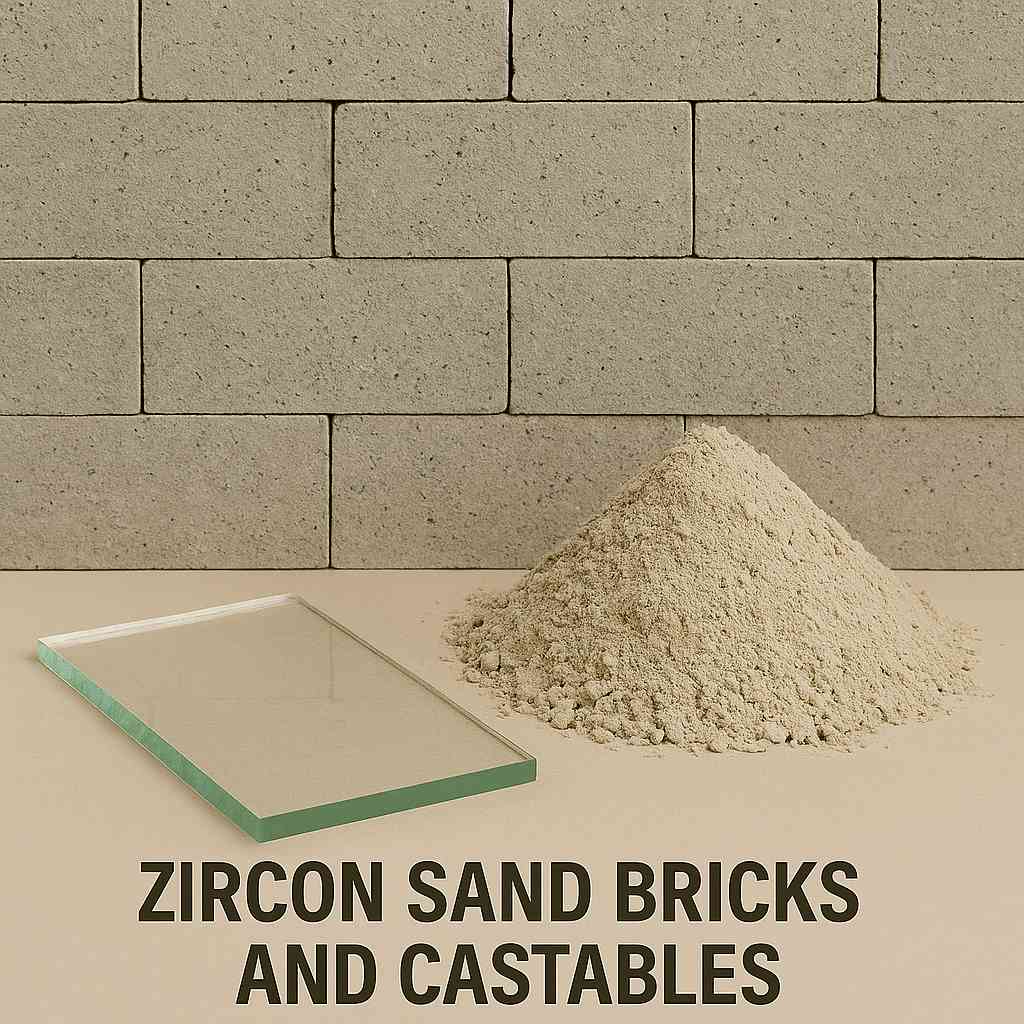
This image shows zircon bricks stacked for furnace walls and castable mixes ready for installation.
In the end, picking the right form and following proven methods guarantees the furnace walls stay tough. This smart use of zircon means fewer shutdowns, safer work conditions, and a longer lining life that keeps steel flowing.urnace walls and castable mixes ready for installation.
How to Source High-Quality Zircon Sand?
Getting the best results from zircon sand starts long before the furnace doors open. It begins with smart Finding premium zircon sand is just as critical as using it right. Poor-quality sand undermines even the best lining plan. So, what do smart managers do? They run strict checks before signing any deal.
Start by asking for detailed lab reports. High-grade zircon should have very low iron and titanium. These metals weaken the lining’s chemical strength. A trusted supplier provides clear chemical breakdowns and physical specs.
Next, think about supply security. Reliable plants can’t afford sudden material shortages. Many firms pick suppliers with multiple mines or regional storage hubs. This cuts delivery risks when local mining issues pop up.
Certificates add peace of mind too. Global standards push suppliers to follow clean mining and stable sorting processes. Don’t shy away from requesting audit results or customer testimonials.
Large buyers often trial a small shipment before a bulk order. Running a test batch checks how well the sand works with existing mixes and application tools.
Here’s a snapshot for your checklist:
Supplier Check | Why It Matters |
---|---|
Lab Reports | Verify purity and grain size |
Multiple Mines | Reduce supply risks |
Certifications | Assure global quality |
Trial Batches | Confirm real-world fit |
References | Learn from other buyers |
One final thought — keep close contact with suppliers. Good communication means updates about new grades, early notice about price shifts, and better contract terms for loyal clients.
What Safety Measures Apply During Use?
Handling zircon needs care. Fine dust can irritate lungs. Heads up, always wear a mask and gloves when mixing or cutting bricks.
Workers must keep storage dry. Wet sand clumps and weakens performance. Many shops store bags on pallets, away from walls.
Teams should train new hires on proper tools and protective gear. Following rules cuts injuries and meets local workplace standards.
Safety Tip | Reason |
---|---|
Wear Dust Mask | Prevent lung irritation |
Store on Pallets | Keep sand dry |
Train Workers | Reduce accidents |
How Are Performance Benefits Measured?
Plants need proof zircon works. So, what’s the process? Inspect linings every month for cracks or thin spots.
Measure wall temperature to spot heat leaks early. Many plants use infrared scans. Lab tests check samples for strength after service.
Keeping data helps plan better maintenance. Good records show real cost savings year over year.
KPI | Typical Target |
---|---|
Lining Thickness | ≥90% of original |
Wall Temp | Within safe limit |
Crack Length | <10 cm |
What Trends Influence Zircon Sand Demand?
Steel firms now push for cleaner production. This drives demand for linings that last longer and waste less energy. Interesting fact, some mills test hybrid linings—zircon plus recycled material—to cut raw material use.
Global markets also affect supply. Events in mining regions can shift prices fast. Buyers watch trends and stock up during low-price periods.
Factor | Effect on Demand |
---|---|
New Furnace Tech | Needs better linings |
Sustainability Push | Longer-lasting linings |
Global Supply | Price shifts |
Conclusion
In short, using zircon sand means stronger steel linings, lower fuel costs, and fewer shutdowns. Steel makers gain stable output and predictable budgets year-round. For tailored advice or bulk orders, reach out to Global Industry today. Let’s build reliable steel plants together and keep operations running strong.
FAQ Section
Q1: Is zircon sand suitable for all steel types?
Zircon sand works well for most common steel grades, including carbon and stainless steels, due to its excellent thermal stability and resistance to chemical attack. However, for specialized or high-alloy steels, it’s crucial to consult with material experts or metallurgists to ensure compatibility and performance, as unique compositions or production processes may require tailored solutions.
Q2: How long do zircon-based linings usually last?
The service life of zircon-based linings can vary significantly based on operating conditions, including temperature, type of application, and the frequency of use. Generally, zircon linings often exceed the lifespan of traditional refractory materials by 30% to 50%. Users can expect longer maintenance intervals and reduced downtime, making them a cost-effective choice in the long term.
Q3: Can zircon sand be reused or recycled?
Yes, some spent zircon material can be recycled or reused depending on the level of contamination and local recycling practices. The feasibility and efficiency of recycling depend on factors such as the type of contaminants present and the specific applications. It is advisable to evaluate the quality of the used zircon and consult specialized recycling facilities for optimal results.
Q4: What is the average cost difference compared to alternatives?
Although the initial cost of zircon products may be higher than some alternative materials, the overall total operational savings often justify the investment. Factors such as reduced replacement costs, extended service life, lower maintenance requirements, and increased production uptime contribute to a more favorable cost-benefit scenario over time. Users typically find that the enhanced performance leads to significant long-term financial benefits.
Q5: Who should I contact for technical support on zircon linings?
For technical support regarding zircon linings, it is advisable to reach out to reputable refractory suppliers who specialize in zircon products. These suppliers often have dedicated technical teams available to provide insights and recommendations. Additionally, certified installation contractors familiar with zircon applications can offer practical guidance and support during installation and maintenance processes, ensuring optimal performance.