Zircon powder is a vital material in many industries. Its use spans from ceramics to advanced electronics. Yet, many businesses, especially purchasing managers, face a challenge. They need to understand how new research and development (R&D) can impact their supply chains and product innovation. Staying ahead means knowing where this material is going. This article will explore the latest R&D breakthroughs. It will show how these advancements are expanding zircon powder’s commercial uses. This knowledge will help you make smarter purchasing decisions. It will also help you identify new opportunities for your products. We aim to provide clear, actionable insights. This ensures you remain competitive in a fast-changing market.
What is Zircon Powder and Its Importance?
Zircon powder is a finely ground mineral, zirconium silicate (ZrSiO4). It comes from zircon sand, a natural material. This material is found in various parts of the world. Zircon sand undergoes a strict processing procedure. This ensures its purity and the right particle size for industrial use.
Key Features:
- Composition: Zircon powder primarily contains high amounts of zirconium dioxide (ZrO2) and silicon dioxide (SiO2).
- Special Properties: These components give it unique characteristics. These include a high refractive index, excellent thermal stability, and strong chemical resistance.
These properties offer practical benefits across many industrial processes. For example, its high melting point, around 2550°C (4622°F), makes it ideal for high-temperature applications. It does not easily react with other substances. Why does this matter? This stability is a huge advantage where material integrity is critical.
Current Commercial Applications:
Zircon powder is already widely used in several key sectors:
- Ceramics: It serves as an opacifier in glazes and tiles. It provides a bright white finish and improves strength and thermal shock resistance.
- Refractories: Its ability to withstand extreme heat makes it a core component in heat-resistant products. These include bricks, crucibles, and furnace linings.
- Foundries: Zircon sand and powder are used for metal casting molds. They handle high temperatures and show minimal expansion. This helps produce high-quality metal parts.
Why R&D is Crucial for Growth:
While current uses are significant, the future of zircon powder lies in continuous research and development. R&D drives innovation. It uncovers new properties and applications. It also refines existing production methods. This leads to higher purity, better performance, and lower costs. For businesses, investing in R&D or partnering with suppliers who do is vital. It ensures access to cutting-edge materials. It also helps maintain a competitive edge. What does this mean for your business? It means staying relevant and profitable in a rapidly evolving market.
Property | Typical Value |
---|---|
Chemical Formula | ZrSiO4 |
Mohs Hardness | 7.5 |
Melting Point | ~2550°C (4622°F) |
Density | 4.6 – 4.7 g/cm³ |
Refractive Index | 1.93 – 2.01 |
Thermal Conductivity | Low (2.5 – 5.0 W/m·K) |
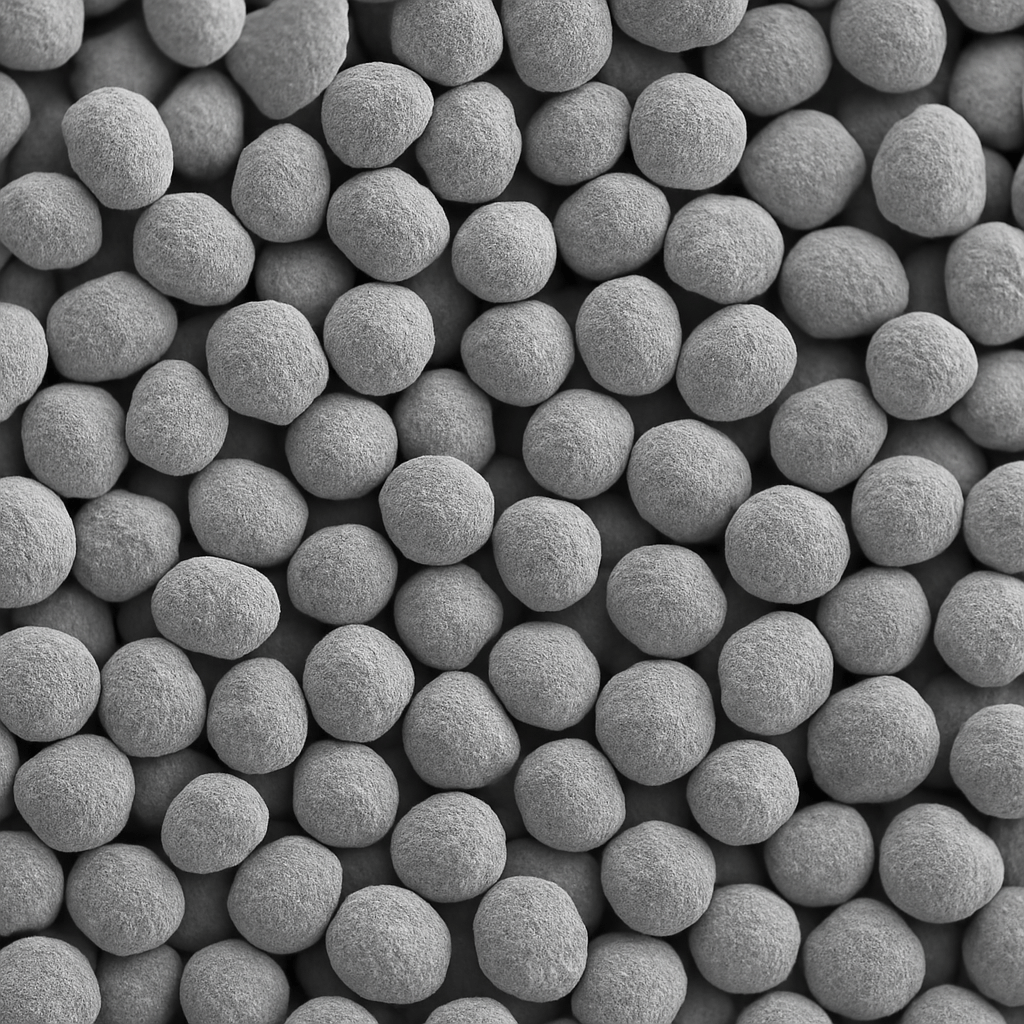
A microscopic view of zircon powder particles, highlighting their fine and uniform structure.
How Are New Synthesis Methods Evolving?
New synthesis methods are changing how zircon powder is produced. These advancements focus on achieving higher purity, finer particle sizes, and more uniform distributions. This leads to superior material performance. Traditional methods often involve mechanical grinding. But what’s new? Modern techniques offer more precise control over the material’s properties.
Advanced Manufacturing Techniques:
- Sol-Gel Method: This technique involves creating a colloidal suspension (sol) that gradually forms a gel. The gel is then dried and heated to produce fine, pure zircon powder. This method allows for excellent control over particle size and morphology. It results in highly homogeneous materials.
- Hydrothermal Synthesis: This process uses high-temperature aqueous solutions under pressure. It creates crystalline materials directly from precursors. Hydrothermal synthesis can produce very pure and uniform zircon particles. It often requires lower processing temperatures than traditional methods.
- Co-precipitation: This method involves simultaneously precipitating two or more ions from a solution. It forms a mixed compound. For zircon, this can lead to highly uniform precursor materials. These then convert into fine zircon powder upon heating.
Impact on Purity and Particle Size Control:
These new methods significantly improve material purity. They reduce impurities that can affect performance. They also allow for precise control over particle size. This is crucial for advanced applications. For example, smaller, more uniform particles can lead to stronger ceramics or more transparent optical components. Why is this important for you? It means materials can be tailored for specific, high-performance needs.
Benefits for Specific Applications:
- Electronics: In electronic components, smaller and purer zircon particles mean better dielectric properties. This leads to more efficient capacitors and sensors.
- Biomedical: For medical implants, high purity and controlled particle size reduce the risk of adverse reactions. It also improves the integration of the implant with biological tissues.
- Coatings: In advanced coatings, uniform fine particles ensure a smoother, more durable finish. This enhances the protective qualities of the coating.
These evolving synthesis methods are not just academic exercises. They directly translate into tangible benefits for industrial applications. They enable the creation of next-generation products with enhanced performance and reliability. This makes them a key area of R&D for any business looking to innovate.
Synthesis Method | Key Advantage | Typical Particle Size (nm) |
---|---|---|
Sol-Gel | High Purity, Uniformity | 10-100 |
Hydrothermal | Controlled Morphology | 50-500 |
Co-precipitation | Homogeneous Precursors | 20-200 |
What Innovations Exist in Surface Modification?
Surface modification is another critical area of R&D for zircon powder. It involves altering the outer layer of the particles. This changes how they interact with other materials. It can significantly enhance performance in various applications. What’s the big deal? It allows zircon powder to be used in ways previously not possible.
Coating Technologies:
- Polymer Coatings: Applying a thin layer of polymer to zircon particles can improve their dispersion in organic matrices. This is vital for composite materials and paints. It prevents particle clumping and ensures a uniform mix.
- Ceramic Coatings: Coating zircon powder with other ceramic materials can enhance its high-temperature stability or chemical resistance. This is useful in refractory applications or harsh chemical environments.
- Metal Oxide Coatings: Layers of metal oxides, like alumina or silica, can improve the surface reactivity or optical properties of zircon particles. This opens doors for new catalytic or optical applications.
Surface Functionalization for Enhanced Compatibility:
Surface functionalization involves attaching specific chemical groups to the zircon particle surface. These groups can then bond with other materials. This improves compatibility and performance. For example, silane coupling agents are often used. They create a chemical bridge between the inorganic zircon and organic polymers. How does this help? It leads to stronger, more durable composite materials.
Role in Composite Materials:
In composite materials, zircon powder acts as a filler or reinforcement. Surface modification ensures that the zircon particles bond effectively with the matrix material. This prevents delamination and improves overall mechanical properties. For instance, in dental composites, surface-modified zircon powder can enhance strength and wear resistance. This leads to longer-lasting dental restorations. In aerospace composites, it can improve thermal stability and reduce weight.
Case Study: Enhanced Polymer Composites
A leading manufacturer of high-performance polymer composites faced challenges. They needed to improve the mechanical strength and thermal stability of their products. Traditional fillers did not provide the desired level of enhancement. They began using zircon powder with a specialized polymer coating. This coating allowed the zircon particles to disperse uniformly within the polymer matrix. It also created strong interfacial bonds. The result was a 25% increase in tensile strength and a 15% improvement in heat deflection temperature. This breakthrough allowed them to develop lighter, stronger components for the automotive industry. What was the key takeaway? Surface modification unlocked new performance levels.
These innovations in surface modification are expanding the utility of zircon powder. They are making it a more versatile material for advanced engineering applications. This is a crucial area for businesses seeking to develop next-generation materials.
Coating Type | Primary Benefit | Example Application |
---|---|---|
Polymer Coating | Improved Dispersion | Polymer Composites |
Ceramic Coating | Enhanced Thermal Stability | High-Temperature Refractories |
Metal Oxide Coating | Modified Reactivity/Optics | Catalysts, Optical Filters |
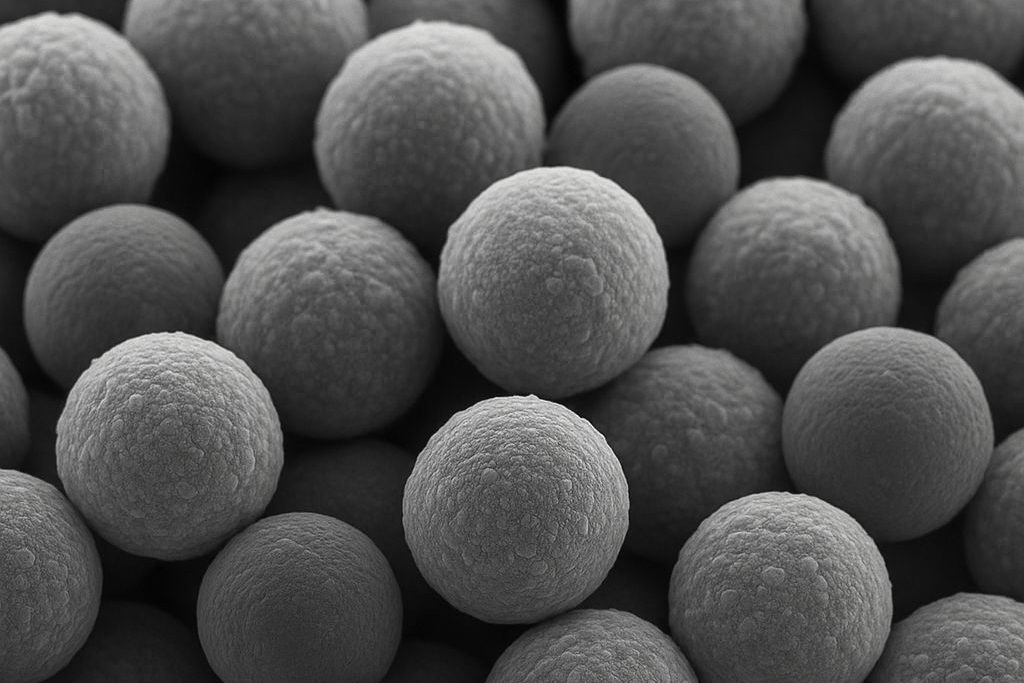
An illustration showing zircon powder particles with a thin, uniform surface coating.
Where Are Emerging Applications for Zircon Powder?
Zircon powder is finding new homes in various cutting-edge industries. These emerging applications are driven by its unique properties. They are also a result of ongoing R&D. Where is it making an impact? It’s expanding beyond traditional uses into high-value sectors.
Biomedical Applications:
- Dental Materials: Zirconia-based ceramics, derived from zircon powder, are increasingly used in dentistry. They make crowns, bridges, and implants. Their high strength, biocompatibility, and aesthetic appeal make them ideal replacements for metal-based restorations.
- Medical Implants: Zirconia is also being explored for orthopedic implants. These include hip and knee replacements. Its wear resistance and inertness are key advantages. This reduces the risk of rejection and extends implant life.
Electronics Applications:
- Capacitors: Zirconia-based materials have high dielectric constants. This makes them suitable for high-performance capacitors. These are used in advanced electronic devices. They allow for smaller, more efficient components.
- Sensors: Zirconia is used in oxygen sensors. These are vital in automotive exhaust systems and industrial processes. They accurately measure oxygen levels. This helps optimize combustion and reduce emissions.
- Solid Oxide Fuel Cells (SOFCs): Yttria-stabilized zirconia (YSZ), a derivative of zircon, is a key electrolyte material in SOFCs. It conducts oxygen ions at high temperatures. This enables efficient energy conversion.
Energy Applications:
- Nuclear Industry: Zirconium alloys, derived from zircon, are used in nuclear fuel rods. They have low neutron absorption cross-sections and good corrosion resistance. This makes them safe and efficient for nuclear reactors.
- Catalysis: Zirconia can act as a catalyst support or a catalyst itself. It promotes various chemical reactions. This is important in chemical manufacturing and environmental protection.
Environmental Applications:
- Water Treatment: Zirconia-based materials are being developed for water purification. They can adsorb heavy metals and other pollutants. This helps clean contaminated water sources.
- Air Purification: In air purification systems, zirconia can help break down harmful volatile organic compounds (VOCs). This improves air quality.
Example: Dental Zirconia
A dental lab recently switched to zirconia-based crowns. They found a significant improvement in patient satisfaction. The crowns were stronger, more natural-looking, and lasted longer. This led to increased referrals and a stronger reputation. What was the driving force? The superior properties of zircon-derived materials.
These emerging applications highlight the versatility and growing importance of zircon powder. They represent significant market opportunities for suppliers and manufacturers alike. Staying informed about these developments is key to future business success.
Emerging Application Sector | Specific Use Case | Key Benefit of Zircon |
---|---|---|
Biomedical | Dental Crowns, Implants | Biocompatibility, Strength |
Electronics | Capacitors, Oxygen Sensors | High Dielectric Constant |
Energy | Nuclear Fuel Rods, SOFCs | Neutron Transparency, Ion Conductivity |
Environmental | Water/Air Purification | Adsorption, Catalysis |
What Role Does Nanotechnology Play?
Nanotechnology is revolutionizing the field of zircon powder. It involves working with materials at the nanoscale, typically 1 to 100 nanometers. At this scale, materials often exhibit unique properties. These differ from their bulk counterparts. Why is this a game-changer? It allows for unprecedented control over material characteristics.
Nanoparticle Synthesis and Characterization:
Researchers are developing new methods to synthesize zircon nanoparticles. These methods ensure precise control over size, shape, and surface chemistry. Techniques like flame spray pyrolysis and chemical vapor deposition are gaining traction. Characterization tools, such as transmission electron microscopy (TEM) and X-ray diffraction (XRD), are vital. They confirm the nanoscale properties.
Enhanced Properties at Nanoscale:
Zircon nanoparticles exhibit enhanced properties compared to conventional zircon powder:
- Increased Strength: Nanocrystalline zirconia can be significantly stronger and tougher. This is due to its fine grain structure. It resists crack propagation more effectively.
- Improved Transparency: While bulk zircon is opaque, carefully synthesized zirconia nanoparticles can be transparent. This is because light scattering is minimized at the nanoscale. This opens doors for transparent ceramics.
- Higher Reactivity: The increased surface area of nanoparticles leads to higher chemical reactivity. This is beneficial for catalytic applications or faster sintering processes.
Challenges and Opportunities in Nano-Zircon:
Working with nanoparticles presents challenges. These include agglomeration (particles clumping together) and safe handling. However, the opportunities are immense. Nano-zircon can lead to:
- Miniaturized Devices: Smaller, more powerful electronic components.
- Advanced Coatings: Ultra-hard, scratch-resistant, and transparent coatings.
- Targeted Drug Delivery: In biomedical applications, nanoparticles can deliver drugs more precisely.
Example: Transparent Zirconia for Optics
A company specializing in high-end optical components sought a material with extreme hardness and transparency. Traditional glass was too brittle. Bulk zirconia was opaque. By using precisely engineered zirconia nanoparticles, they developed a transparent ceramic. This material offered superior scratch resistance and optical clarity. It is now used in specialized camera lenses and protective covers for sensitive equipment. What made this possible? The unique properties unlocked at the nanoscale.
Nanotechnology is pushing the boundaries of what zircon powder can do. It is creating new markets and applications. For businesses, understanding and leveraging nano-zircon technology is key to future innovation and competitive advantage.
Nanoscale Property | Benefit to Application |
---|---|
Increased Strength | Durable Ceramics, Composites |
Improved Transparency | Optical Components, Protective Coatings |
Higher Reactivity | Catalysis, Faster Sintering |
Reduced Agglomeration | Better Dispersion in Matrices |
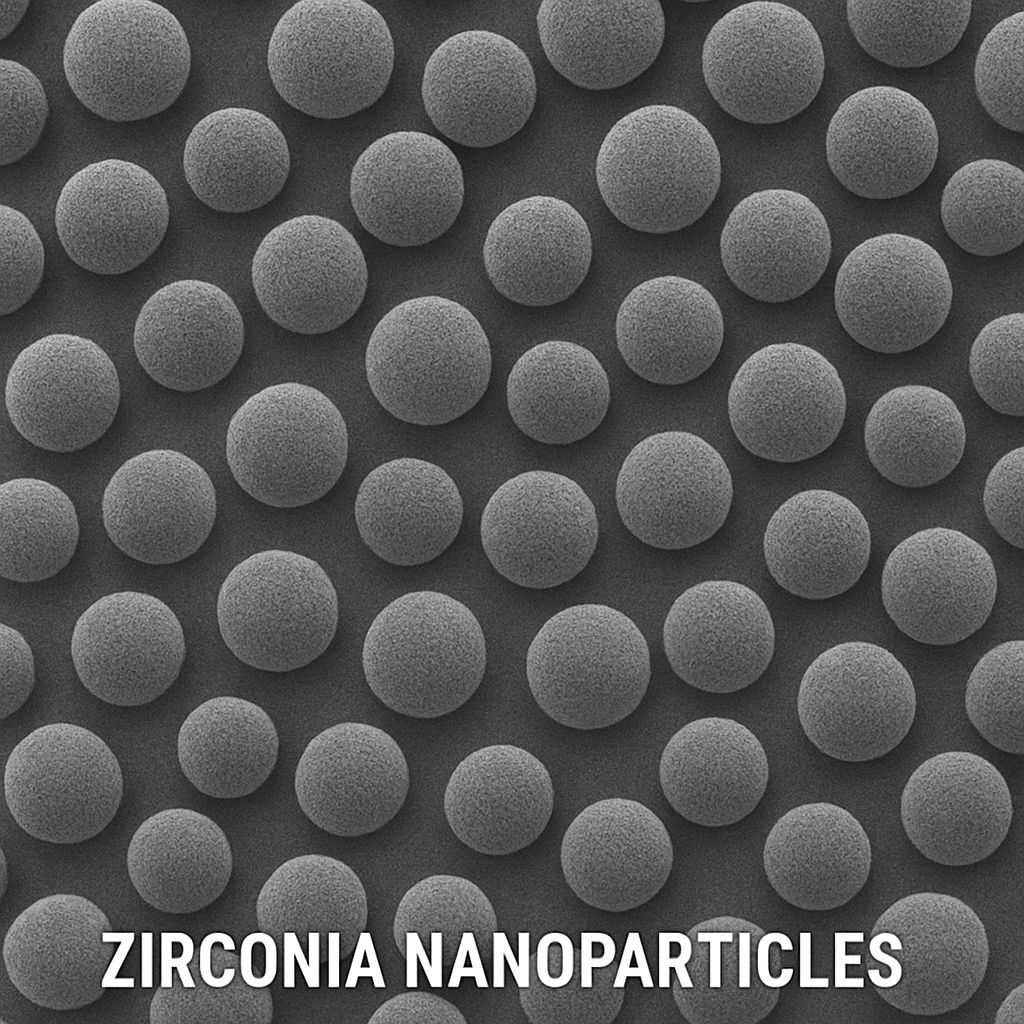
An artistic rendering of zircon nanoparticles, emphasizing their tiny size and uniform distribution.
How is Zircon Powder Used in Advanced Ceramics?
Zircon powder is a cornerstone in the production of advanced ceramics. These materials are designed for extreme conditions. They offer superior mechanical, thermal, and chemical properties. Why is zircon so vital here? It provides the foundational strength and stability needed for high-performance applications.
High-Performance Ceramics:
- Aerospace Components: Zirconia-toughened ceramics are used in jet engine parts and thermal barrier coatings. They withstand high temperatures and extreme stresses.
- Automotive Parts: In automotive applications, zirconia ceramics are found in oxygen sensors and wear-resistant components. They improve fuel efficiency and engine longevity.
- Industrial Tools: Cutting tools, grinding media, and wear parts benefit from zirconia’s hardness and toughness. This extends their lifespan and improves manufacturing efficiency.
Toughening Mechanisms and Crack Resistance:
Zirconia exhibits a unique property called transformation toughening. This is key to its use in advanced ceramics. When a crack starts to form, metastable tetragonal zirconia particles transform into a monoclinic phase. This transformation involves a volume expansion. This expansion puts the crack under compression. What does this achieve? It effectively stops the crack from growing. This makes the ceramic much tougher and more resistant to fracture.
Sintering Advancements and Densification:
Sintering is the process of compacting and forming a solid mass of material by heat or pressure without melting it to the point of liquefaction. Advances in sintering techniques are crucial for zirconia ceramics. Hot isostatic pressing (HIP) and spark plasma sintering (SPS) are examples. These methods achieve high densities and fine grain structures. This further enhances the mechanical properties of the final ceramic product. High densification means fewer pores. Fewer pores mean stronger, more reliable parts.
Example: Ceramic Bearings
A manufacturer of high-speed machinery needed bearings that could operate at extreme temperatures and resist wear. Traditional metal bearings failed quickly. They adopted ceramic bearings made with zirconia-toughened alumina. These new bearings offered superior hardness, wear resistance, and thermal stability. This led to a significant increase in machine uptime and reduced maintenance costs. What was the direct impact? Enhanced operational efficiency and reliability.
Zircon powder’s role in advanced ceramics is expanding. It is enabling the creation of materials that push the boundaries of performance. This makes it an essential material for industries demanding the highest levels of durability and reliability.
Ceramic Application | Key Zirconia Benefit | Performance Improvement |
---|---|---|
Aerospace | High-Temperature Stability | Reduced Wear, Longer Life |
Automotive | Wear Resistance | Improved Fuel Efficiency |
Industrial Tools | Hardness, Toughness | Extended Tool Life |
Medical Devices | Biocompatibility, Strength | Enhanced Durability |
What are the Latest Trends in Zircon Powder Research?
The field of zircon powder research is dynamic. It is constantly evolving. Several key trends are shaping its future. These trends promise to unlock even more commercial applications. What should you be watching? These areas represent the next wave of innovation.
AI and Machine Learning in Material Design:
Artificial intelligence (AI) and machine learning (ML) are transforming material science. They are used to predict material properties. They also optimize synthesis routes. For zircon powder, AI can accelerate the discovery of new formulations. It can also fine-tune processing parameters. This reduces trial-and-error. It speeds up the development of new products. How does this benefit you? Faster innovation cycles and more efficient R&D.
Sustainable Production Methods:
There is a growing focus on sustainability. Researchers are developing greener ways to produce zircon powder. This includes reducing energy consumption. It also involves minimizing waste. Efforts are being made to use recycled materials. They are also exploring more environmentally friendly chemical processes. This aligns with global environmental goals. It also meets consumer demand for sustainable products.
Interdisciplinary Collaborations:
Zircon powder research is increasingly interdisciplinary. It brings together experts from different fields. These include material science, chemistry, physics, and engineering. This collaborative approach fosters new ideas. It also accelerates breakthroughs. For example, combining nanotechnology with biomedical engineering is leading to new medical devices. What’s the takeaway? Complex problems require diverse expertise.
Example: AI-Driven Material Discovery
A research consortium used AI to screen thousands of potential zircon-based compounds. Their goal was to find a material with specific catalytic properties. AI algorithms identified several promising candidates in a fraction of the time. This would have taken years using traditional lab methods. One candidate showed exceptional performance in a new industrial process. This led to a more efficient and environmentally friendly production route. What was the impact? A significant leap in material discovery efficiency.
These trends show a future where zircon powder is even more versatile and impactful. They highlight a commitment to innovation and sustainability. For businesses, understanding these trends is key to identifying future market opportunities and staying competitive.
Research Trend | Impact on Zircon Powder Development |
---|---|
AI/Machine Learning | Faster material discovery, optimized synthesis |
Sustainable Production | Reduced environmental footprint, resource efficiency |
Interdisciplinary Collaboration | Accelerated innovation, novel applications |
Conclusion
In conclusion, zircon powder is a dynamic and evolving enabler for future technologies across diverse sectors. From advanced medical solutions and next-generation electronics to sustainable energy systems and environmental remediation, its potential continues to expand. Partnering with innovative suppliers and research institutions ensures access to cutting-edge materials needed to succeed and lead in tomorrow’s rapidly advancing technological landscape.
FAQ Section
Q1: What is the primary benefit of R&D in zircon powder?
The primary benefit of R&D in zircon powder is the expansion of its commercial applications. It leads to improved material properties, new synthesis methods, and enhanced performance in various industries. This allows businesses to create more advanced and competitive products.
Q2: How do new synthesis methods improve zircon powder?
New synthesis methods, such as sol-gel and hydrothermal synthesis, improve zircon powder by allowing for precise control over particle size, morphology, and purity. This results in materials with tailored properties, leading to better performance in specific applications like electronics and biomedical devices.
Q3: What are some surprising new uses for zircon powder?
Some surprising new uses for zircon powder include biomedical applications like dental and orthopedic implants, advanced electronic components such as high-performance capacitors and oxygen sensors, and environmental applications in water and air purification systems. Its versatility is continuously being discovered.
Q4: Is nanotechnology making zircon powder more versatile?
Yes, nanotechnology significantly enhances zircon powder’s versatility. By working at the nanoscale, researchers can create zircon nanoparticles with increased strength, improved transparency, and higher reactivity. This opens up new possibilities for miniaturized devices, advanced coatings, and targeted drug delivery systems.
Q5: How does zircon powder contribute to sustainable technologies?
Zircon powder contributes to sustainable technologies in several ways. It is used in solid oxide fuel cells for efficient energy conversion and in catalysis for cleaner chemical processes. Ongoing R&D also focuses on developing more sustainable production methods for zircon powder itself, reducing its environmental footprint.