Zircon sand supports top-quality glass production for industries that can’t afford flaws. Many purchasing managers worry about impurities, poor clarity, and unstable batches. This piece explains how zircon sand solves these headaches. You’ll see clear facts, practical methods, and industry-backed insights that prove its real value in glass factories. Read on and feel confident about sourcing the right zircon sand for your next procurement plan.
How Does Zircon Sand Impact Glass Quality?
Glass quality makes or breaks customer trust. Using zircon sand protects clear finishes, fewer flaws, and predictable strength batch after batch. So, why do top producers insist on it?
One key advantage is how zircon sand purifies molten glass. During high heat, particles or leftover dust can float up, creating bubbles, streaks, or haze. Zircon acts like a filter—its chemistry grabs those bits and traps them in the slag instead of letting them ruin a clean pane.
Another big plus is controlling expansion and contraction. Glass plants hate surprise cracks. When heat cycles repeat fast, unstable batches may warp or split. Consistent zircon content smooths this stress, which means windows, bottles, and containers survive sudden changes in temperature.
Scratch resistance gets a quiet boost too. Small scratches lower product grade and hurt sales. Zircon-rich batches resist tiny surface damage during handling, shipping, or installation.
In practical terms, it saves on scrap and cuts returns from buyers who spot flaws. This means tighter profit margins and smoother supply to end users. Even small defect drops add up when you ship millions of square feet of glass every month.
Here’s an updated snapshot:
Quality Factor | How Zircon Sand Supports It |
---|---|
Clarity | Filters out micro particles |
Color | Keeps tone neutral and bright |
Strength | Reduces stress cracks |
Surface | Harder to scratch, easier to clean |
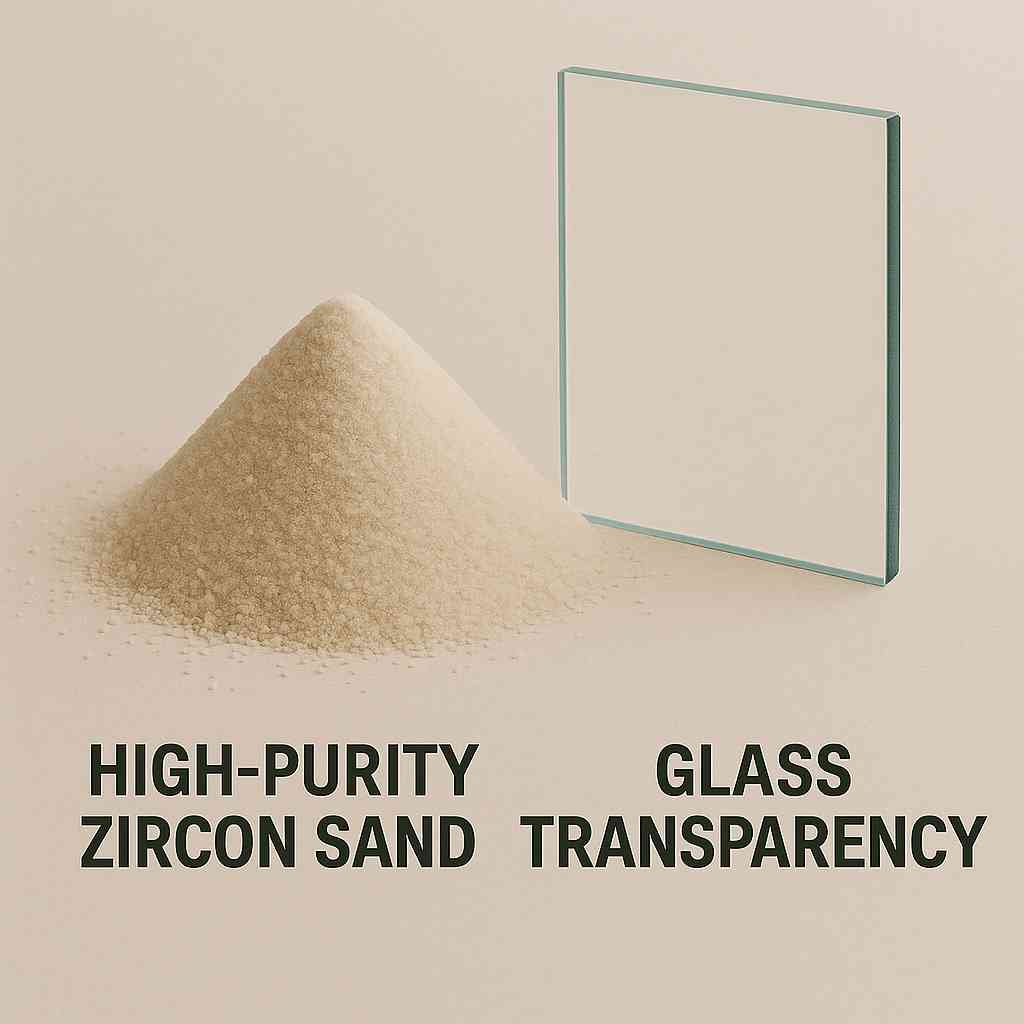
Image shows raw zircon sand next to clear glass sheets to highlight its purifying role
Buyers and plant managers often say: investing in clean zircon upfront costs less than fixing flaws after production. Consistent quality feeds into repeat contracts, satisfied builders, and fewer warranty claims.
Why Is Zircon Sand Preferred in Glass Production?
Factories pick zircon sand because it performs better than other minerals. Here’s why it stands out.
This sand brings a rare mix of high melting point, chemical stability, and low cost. That combo means fewer furnace issues and better control over melting.
Competing minerals like quartz or feldspar can’t match its uniform grain size. This uniformity means no hot spots in the furnace and steady melting rates.
Another reason is global supply stability. Top producers lock in contracts to avoid raw material gaps. Zircon mines, especially in Australia and South Africa, deliver trusted grades for glass buyers worldwide.
Producers get more value since less sand does more work. It’s cost-effective long-term because it reduces waste and energy spending.
Below is a comparison:
Property | Zircon Sand | Quartz | Feldspar |
---|---|---|---|
Melting Point | Very High | High | Medium |
Chemical Stability | Excellent | Good | Fair |
Cost | Medium | Low | Low |
Consistency | High | Medium | Low |
Using zircon sand cuts hidden costs tied to rework or defect handling. Clear panels, sturdy containers, and glossy finishes show its power in daily production.
What Is the Chemical Composition of Zircon Sand?
Understanding what sits inside zircon sand explains why it does such a solid job in modern glass works. Let’s see what’s really in it.
At its core, zircon sand mostly contains zirconium silicate, which chemists write as ZrSiO4. This single mineral carries heavy heat resistance and barely reacts with other furnace materials. Because it stays stable while other batch parts melt and bubble, it protects glass from unwanted surprises.
Alongside zirconium silicate, tiny bits of alumina, iron oxide, and titanium dioxide may appear. These stay low in volume. High-quality sand always shows less than 0.2% iron oxide. That’s critical—excess iron can tint clear glass green or brown, ruining large flat sheets that architects rely on.
Suppliers test each mine run to verify purity. They grade the sand, bag or bulk it, and issue a chemical analysis certificate. Buyers read these reports carefully before signing big volume contracts.
Here’s a standard composition snapshot for premium batches:
Element | Average Percentage (%) |
---|---|
ZrO₂ | 65–66 |
SiO₂ | 32–34 |
Fe₂O₃ | <0.15 |
TiO₂ | <0.2 |
Here’s something practical: if a furnace handles glass for optical lenses, iron must stay near zero. That’s why top lens plants pay extra for near-zero impurity sand. It’s cheaper than fixing color flaws later.
This clean mineral mix also means the sand melts consistently every time. No sudden lumps. No fizzing reactions. Just smooth, clean flow into high-grade glass panels, lab tubes, or durable bottles.
So, while sand may look plain on the surface, its tight chemical specs drive quality from batch one to batch thousand. curves and no surprise reactions. Managers like that because it stops quality issues before they reach customers.
How Is Zircon Sand Added to Glass Batches?
Batching steps must be precise to avoid waste. So, how do plants handle it?
Most producers weigh zircon sand alongside soda ash, limestone, and cullet (recycled glass). They store it dry to prevent clumping. Automatic feeders then drop it into mixers.
Dosage matters. Too much sand raises cost with little gain. Too little weakens clarity and raises defect risk. Best practice ranges from 2% to 5% by batch weight.
Pro tip: keep sand dry. Wet sand can clump, causing poor mixing and uneven melting.
Batching Step | Key Action |
---|---|
Storage | Keep dry, sealed bins |
Weighing | Use calibrated scales |
Feeding | Automate for accuracy |
Mixing | Blend evenly with other materials |
Modern batch houses use sensors to adjust feeding rates in real time. This tech cuts human error and improves furnace feed consistency.
What Types of Glass Use Zircon Sand?
Not every glass plant needs zircon sand, but the ones that do swear by it. Here’s where it fits best in the glass world.
Large flat glass sheets—think skyscraper windows and high-end storefront panels—must be spotless and color-stable. Builders and architects demand glass that stays clear for decades under harsh sunlight. Adding zircon sand during batch melting filters out tiny impurities that cause haze or streaks.
Container glass—bottles and jars for food or cosmetics—uses zircon sand too. A tiny bit added to the mix boosts wall strength. Stronger walls mean bottles resist breakage during filling, capping, transport, and store shelving. Less breakage cuts insurance costs and keeps product loss low.
Then there’s specialty glass: lab tubes, fiber optics, glass used in chemical plants. These all need raw materials with extreme purity. Any iron or titanium can disrupt how light passes or how chemicals react inside the glassware. Zircon sand, properly graded, ensures this special glass stays chemically neutral and visually flawless.
Below is a quick rundown of common matches:
Glass Type | Why Use Zircon Sand |
---|---|
Flat Glass | Better clarity, less weather stain |
Container Glass | Tougher walls, fewer breaks |
Specialty Glass | Ultra-high purity, precise melting |
Many big plants keep several zircon sand grades on hand. Bulk grade handles flat glass. Higher purity grades feed small-batch specialty glass lines.
Smart procurement means matching the right grade to the right line. Overpaying for ultra-pure sand in low-end containers wastes budget. Underpaying for bulk sand in high-end glass risks customer complaints and lost orders.
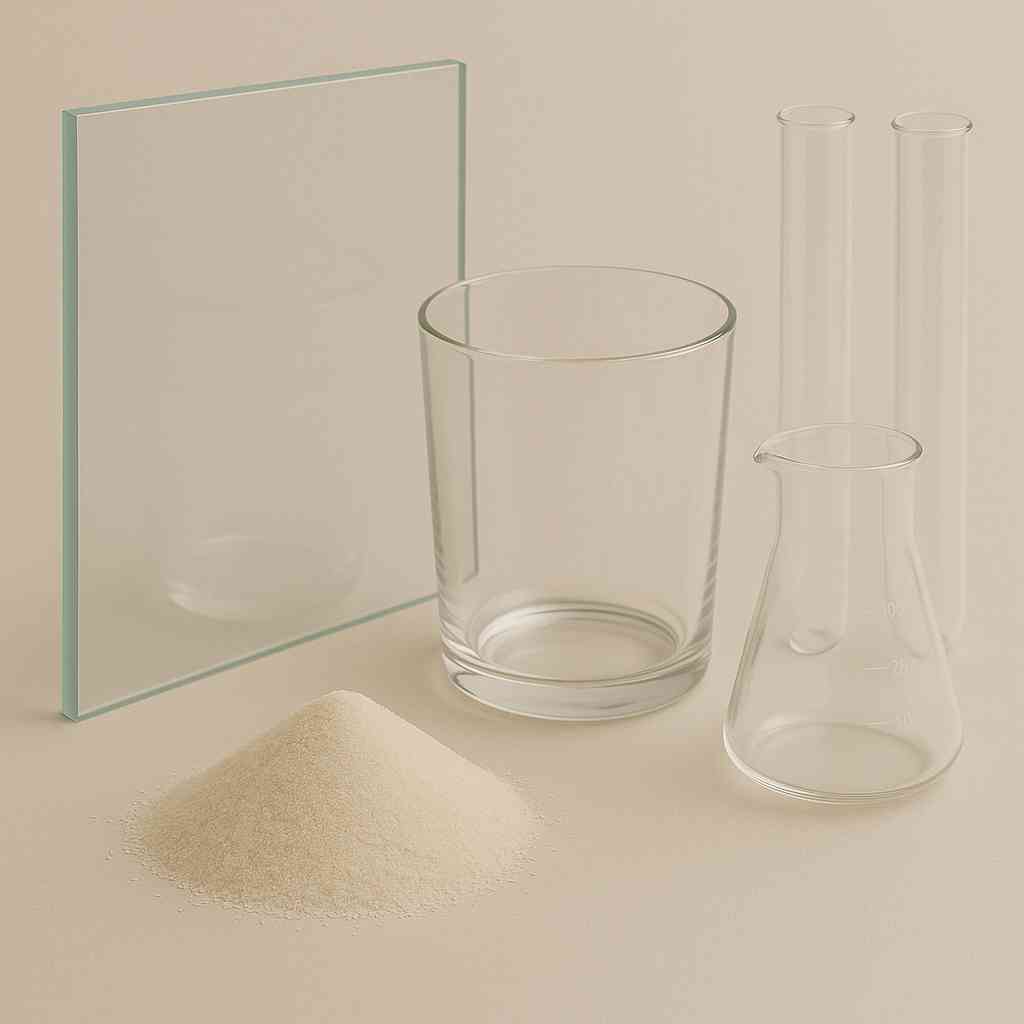
Image shows flat glass sheets, strong containers, and clear lab tubes produced using proper zircon sand grades
Keeping the product line clear of flaws or unexpected color shifts keeps buyers loyal and factories running at top profit.sand grades to glass type. It avoids overspending on purity that some products don’t need.
How Does Zircon Sand Improve Furnace Efficiency?
Running a glass furnace eats up huge energy bills. Any edge in efficiency saves thousands of dollars daily. So, how does zircon sand help trim costs?
Zircon sand melts at high temperatures and holds heat well. When mixed into the batch, it spreads thermal load more evenly. This reduces hot spots that wear out furnace bricks and cause cold spots that mess up the melt.
Because heat distribution stays smooth, operators can lower peak firing temperatures slightly without hurting throughput. Over a year, even a 1% drop in peak heat cuts fuel costs by a big chunk, especially for natural gas-fired furnaces.
Longer brick life is another plus. Bricks face repeated expansions and contractions. Stable melting means fewer harsh swings in furnace walls. Maintenance shutdowns get pushed back, raising uptime and plant productivity.
Let’s compare clear benefits:
Benefit | Result |
---|---|
Stable heat spread | Even melt, less energy waste |
Lower hot spots | Longer furnace lining life |
Controlled expansion | Fewer cracks, smoother runs |
Small energy savings | Big cost drops over time |
One European float glass maker reported a 5% drop in total fuel spend after upgrading batch zircon quality. They also stretched furnace relining cycles by an extra year—huge savings in labor and downtime.
Modern plants pair zircon-rich batches with real-time sensors that tweak burner output minute by minute. This pairing keeps temperatures steady no matter what mix changes come down the line.
Furnace crews love it. Fewer repairs, fewer emergency shutdowns, and a melt zone that behaves predictably every shift.
Are There Environmental Benefits of Using Zircon Sand?
Sustainability rules push glass plants to cut waste and emissions. Smart raw materials help meet these targets faster. Here’s how zircon sand supports greener operations.
Zircon’s chemical stability means fewer rejected loads. Clean melts equal clear panes and stronger containers on the first pass. Less scrap means less energy used to remelt bad batches.
Many glass factories recycle leftover fines from grinding or handling. These tiny particles often go back into the next batch instead of hitting the landfill. Closed-loop reuse cuts fresh sand demand, which eases mining pressure and cuts carbon footprint.
Responsible mining practices matter too. Major zircon miners follow strict land recovery programs. After mining, they restore ground cover, plant native species, and monitor soil health to protect local communities and ecosystems.
Some buyers go further by choosing suppliers with sustainability certifications. This keeps procurement teams aligned with global green building standards and environmental audits.
A quick view:
Environmental Edge | How It Helps |
---|---|
Fewer rejects | Cuts waste and repeat melting |
Fines reuse | Lowers raw input needs |
Mine rehab | Restores natural habitats |
Certifications | Supports green building goals |
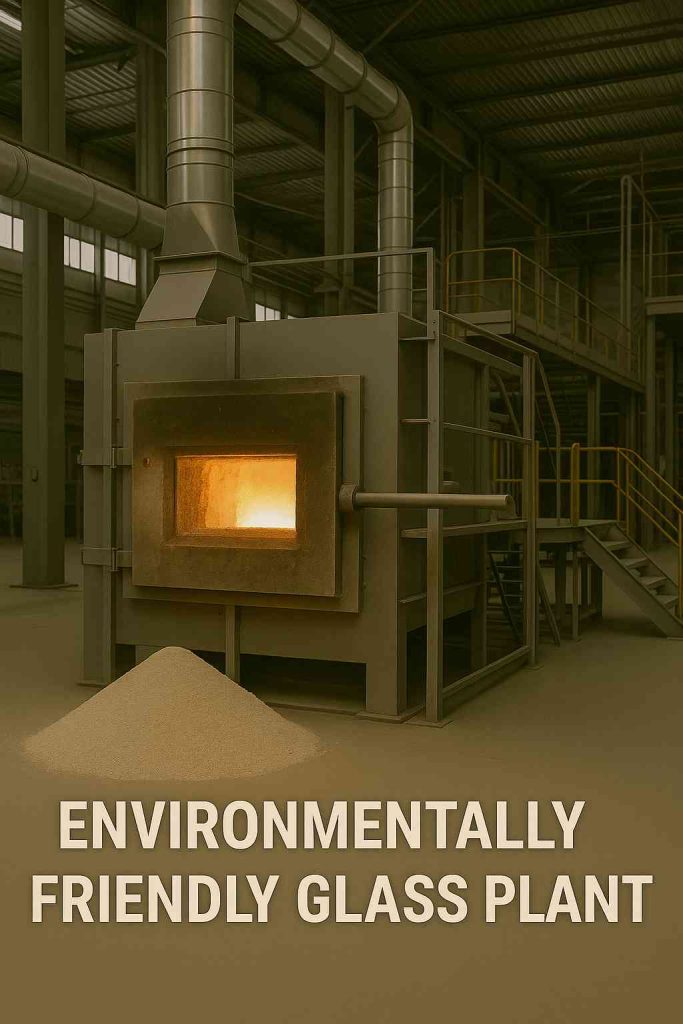
Image shows a modern glass furnace with efficient heat use and green building compliance supported by clean zircon sand
Choosing stable, tested zircon sand helps glass plants show buyers and regulators they run clean, efficient, and responsible lines—winning more contracts and staying ahead of tougher global rules.
What Challenges Come with Zircon Sand in Glass?
No raw input is perfect. Here are common worries.
Supply chains can face hiccups if mines close or export rules change. Buyers often secure multi-year deals to keep stock steady.
Quality can vary by mine. This means testing each shipment and keeping a shortlist of approved suppliers.
Handling calls for dust control. Breathing fine zircon particles may affect worker health. Plants follow strict rules for ventilation and PPE.
Risk | Mitigation |
---|---|
Supply Fluctuations | Long-term contracts |
Quality Shifts | Incoming lot testing |
Dust | PPE and dust collectors |
Smart buyers plan ahead and stay in touch with mines and traders to avoid surprises.
How Do Manufacturers Ensure Zircon Sand Quality?
Maintaining steady quality keeps customers happy and glass lines profitable. How do factories confirm every zircon shipment meets strict specs?
It starts with supplier vetting. Buyers check mining practices, lab equipment, and past shipment records. They demand up-to-date test reports showing composition, moisture, and grain size.
Once a load arrives at the plant, on-site labs run their own tests. Teams check for unwanted iron, water content, and any unusual grains. If samples fail, the batch sits in quarantine until cleared or replaced.
Some large glass groups even run pilot melts. They use a small furnace to melt test batches before pushing sand to full-scale production. This extra step catches flaws early and saves on wasted mainline runs.
Key checkpoints include:
Checkpoint | Why It Matters |
---|---|
Chemical purity | Stops tint or streaks |
Grain uniformity | Keeps melting even |
Moisture level | Prevents feeder blockages |
Contaminant scan | Avoids defects, furnace damage |
Leading suppliers back up each load with full certificates and test logs. Plants store these for audit trails, proof of due diligence, and insurance reasons.
Consistent checks mean fewer last-minute production stops. It also reassures builders, architects, and bottling clients that every glass pane or jar meets specs without surprise color shifts or bubbles.
How to Choose Reliable Zircon Sand Suppliers?
Finding and keeping a strong supply partner shields plants from price spikes and product risk. So, what do top procurement teams look for when picking zircon sand vendors?
First, proof of track record. Trusted vendors provide shipment histories, lab certificates, and client references. They respond fast to questions and offer technical help if a furnace needs tuning for sand grades.
Next, clear contract terms protect both sides. These set specs for grain size, moisture, and chemical limits. Volume guarantees and clear delivery schedules keep production steady even if mines slow output.
Added value includes on-call technical advice. Some vendors send field engineers to help with batching tweaks or furnace tests, solving flow or melt problems on site.
Below is a checklist to guide smart supplier choices:
What To Check | Benefit |
---|---|
Past performance | Confidence in quality |
Detailed contract | Clear specs, stable supply |
Tech support | Smooth furnace operation |
Long-term vendor ties build mutual trust. Many plants sign multi-year supply deals that lock in prices, protect from sudden export shifts, and keep glass output stable 365 days a year.
Choosing the right partner turns raw sand into reliable profit—clear glass, solid bottles, and no late-night calls to fix flaws that never should happen in the first place.y.
Conclusion
Zircon sand does more than fill a batch list. It protects clarity, raises strength, and helps glass lines run with fewer stops and less waste. Buyers see lower defect rates, smoother furnace cycles, and happier clients down the chain. Partner with Global Industry to secure steady supply, tight specs, and proven support you can trust shift after shift. Reach out today and keep your glass production stable, clear, and profitable.
FAQ Section
Q1: Is zircon sand used in all types of glass?
No, zircon sand is not universally used in all glass types. It is particularly effective in applications such as clear flat glass, sturdy containers, and high-purity laboratory glassware, where the presence of even the tiniest flaws can significantly impact quality and functionality. Its unique properties help ensure superior optical clarity and mechanical strength, making it a preferred choice in these specialized applications.
Q2: How much zircon sand is added per ton of glass?
Most glass manufacturers typically mix in 2% to 5% zircon sand by weight per ton of glass, though the exact percentage can vary based on the desired clarity, strength, and specific glass formulation. Factors such as the type of glass being produced and its intended use play a crucial role in determining the optimal zircon sand content to achieve the required balance of performance characteristics.
Q3: Can zircon sand be replaced by other materials?
While alternative materials—like feldspar and various aluminosilicates—do exist, they often fail to match the high melting stability and impurity control offered by zircon sand. The unique crystalline structure of zircon contributes to superior thermal resistance and minimizes the risk of contamination, making it a preferred material in high-performance glass applications where quality cannot be compromised.
Q4: Does zircon sand affect glass color?
Yes, zircon sand plays a crucial role in influencing the color of the finished glass. Pure zircon sand helps to prevent the presence of iron and other impurities that can cause clear glass to take on undesirable green or brown tints. By maintaining a high level of purity, zircon ensures that glass sheets remain crystal clear, which is essential for applications requiring high optical standards.
Q5: Where do most manufacturers source zircon sand?
The majority of zircon sand used in glass manufacturing is sourced from major mines located in Australia, South Africa, and certain regions of Asia, including India and Sri Lanka. These geographical regions are known for their rich deposits of high-grade zircon. To ensure a reliable and consistent supply, many manufacturing plants establish long-term contracts with suppliers, securing the necessary materials for uninterrupted production.