Casting buyers and production managers often face the same headache: how to pick the right sand that keeps molds stable, costs reasonable, and output quality consistent. Choosing a filler that underperforms costs money, time, and reputation. Here’s good news — using zircon sand fixes many headaches. It’s stable, precise, and helps factories keep parts within tight tolerances. This guide shows how zircon sand works in real-world casting, why it’s trusted by pros, and how it fits budgets without cutting corners. Stick around and see why foundries pick it year after year.
Why Do Foundries Prefer Zircon Sand?
Here’s why this matters: production managers and buyers hate wasted time and money. Poor mold materials crack under heat, distort shapes, and create bad parts that need fixing or scrapping. That’s costly. Zircon sand helps stop these problems before they start — That’s why many foundries pick zircon sand as a smarter choice compared to ordinary silica or olivine sand.
Zircon sand stands out for three big reasons: high heat resistance, stable shape under stress, and clean surface finish. These features keep molds strong, even when pouring very hot metals like steel or nickel. Fewer cracks or sudden breaks mean better part quality. For managers, that means fewer rejects and less rework, which saves labor and energy costs fast.
Another plus is how smooth parts come out. Zircon grains have a round, even shape that packs tightly. This makes cleaner mold walls, which means less grinding or polishing later. Some plants have seen a 20% drop in finishing costs after switching to zircon. Smooth surfaces also cut down on tool wear during machining, so shops keep their cutting edges longer.
Let’s talk money: at first glance, zircon sand costs more per ton than basic silica sand. But smart buyers know that what really counts is cost per usable mold. Zircon molds last longer and can handle more casting cycles. They fail less often and cause fewer emergency stops. That saves big money over time and keeps delivery schedules on track.
Reliable supply is another reason buyers trust zircon. Good suppliers clean, grade, and test the sand before shipping. This means each batch performs the same. Consistent molds mean steady output and fewer last-minute surprises for planners.
Here’s a quick comparison to see how zircon stacks up:
Feature | Zircon Sand | Silica Sand | Olivine Sand |
---|---|---|---|
Max Service Temp (°C) | 1650 | 1100 | 1400 |
Thermal Shock Resistance | Excellent | Low | Medium |
Mold Reuse Cycles | 3–5 | 1 | 2–3 |
Grain Shape | Rounded | Angular | Rounded |
Surface Finish | Smooth | Rough | Average |
As you can see, the big picture is not just the price per ton — it’s the total cost per good part. When molds last longer and castings need less fixing, the savings add up quickly.
One real story shows this well. A mid-sized auto parts factory moved from silica to zircon for gearbox housings. Six months later, defects dropped 17%, mold changes fell by half, and machine downtime shrank by 12%. Better molds meant smoother shifts and on-time deliveries.
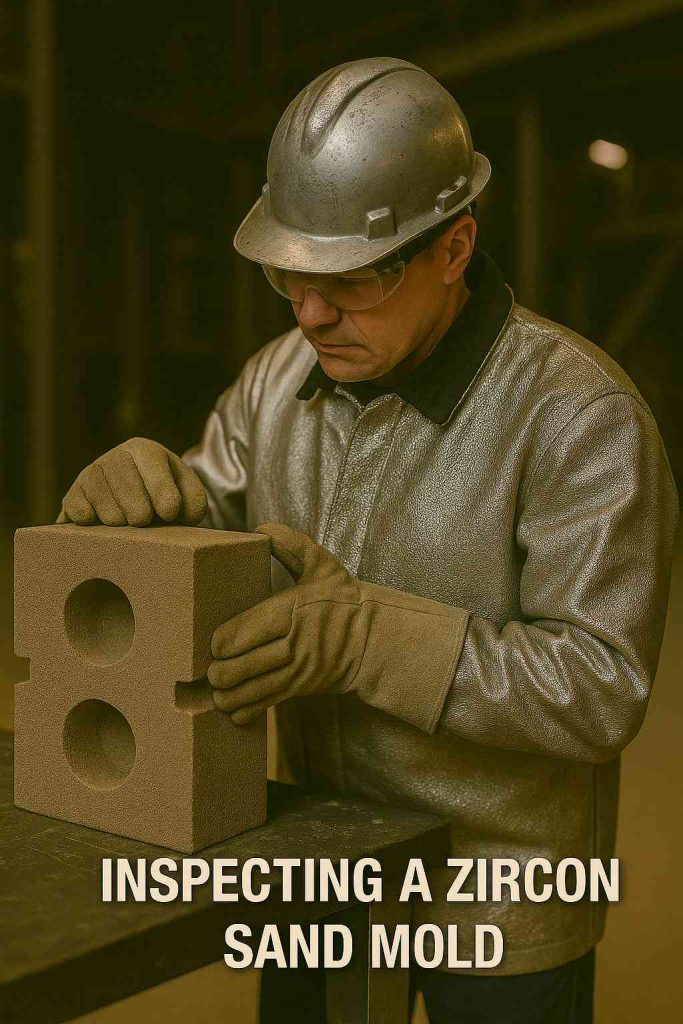
A technician checks mold strength, showing how zircon keeps walls firm when pouring hot metal
In short: foundries trust zircon sand because it works. It cuts hidden costs, keeps lines running, and protects product quality. For managers, it’s a small switch that pays back in stronger production and steady profits. in cost control, part precision, and production reliability. It’s a small material decision that safeguards big investments in machinery, staff hours, and client trust..
How Does Zircon Sand Support Precision Casting?
Let’s unpack this: every casting buyer and plant engineer wants perfect parts on the first run. Any surface flaw, dimension shift, or hidden cavity means scrap or costly rework. This is where zircon sand proves its real value — it holds the mold’s exact shape and handles molten metal without surprise problems.
One key benefit is how tight zircon grains pack. These grains are round, fine, and highly uniform. This means fewer gaps in the mold walls. When metal pours in, heat flows through the mold evenly instead of gathering in one spot. Even heat means less cracking and fewer surface defects. Buyers producing turbine blades, pump housings, or engine blocks depend on this level of accuracy to meet strict specs.
Smooth mold walls also lead to smoother final parts. With fewer rough spots, less finishing is needed. Workers spend less time sanding, grinding, or polishing cast parts before shipping. This lowers labor costs and shortens delivery times — two big wins for any production line trying to stay on schedule.
Think about gas build-up: in some castings, trapped gases create bubbles or blowholes. This ruins part strength. Zircon’s tight packing reduces gas channels. Less trapped gas means denser, stronger metal parts. Plus, cleaner molds mean less slag or leftover debris inside cast cavities. Shops that cast stainless steel or high-nickel alloys see the difference right away.
A quick look at these technical perks shows why buyers trust zircon for tight-tolerance work:
Precision Factor | Result with Zircon Sand |
---|---|
Mold Wall Smoothness | Excellent |
Gas Porosity Risk | Low |
Thermal Crack Risk | Low |
Edge Detail Clarity | Very High |
Let’s bring in a real example: a valve manufacturer used cheaper sand for years. They fought constant leaks from tiny cracks and hidden blowholes. Switching to high-grade zircon fixed the issue. Leak failures dropped by nearly 30% in six months. Their clients noticed fewer warranty claims — and the procurement team proved their spend paid off.
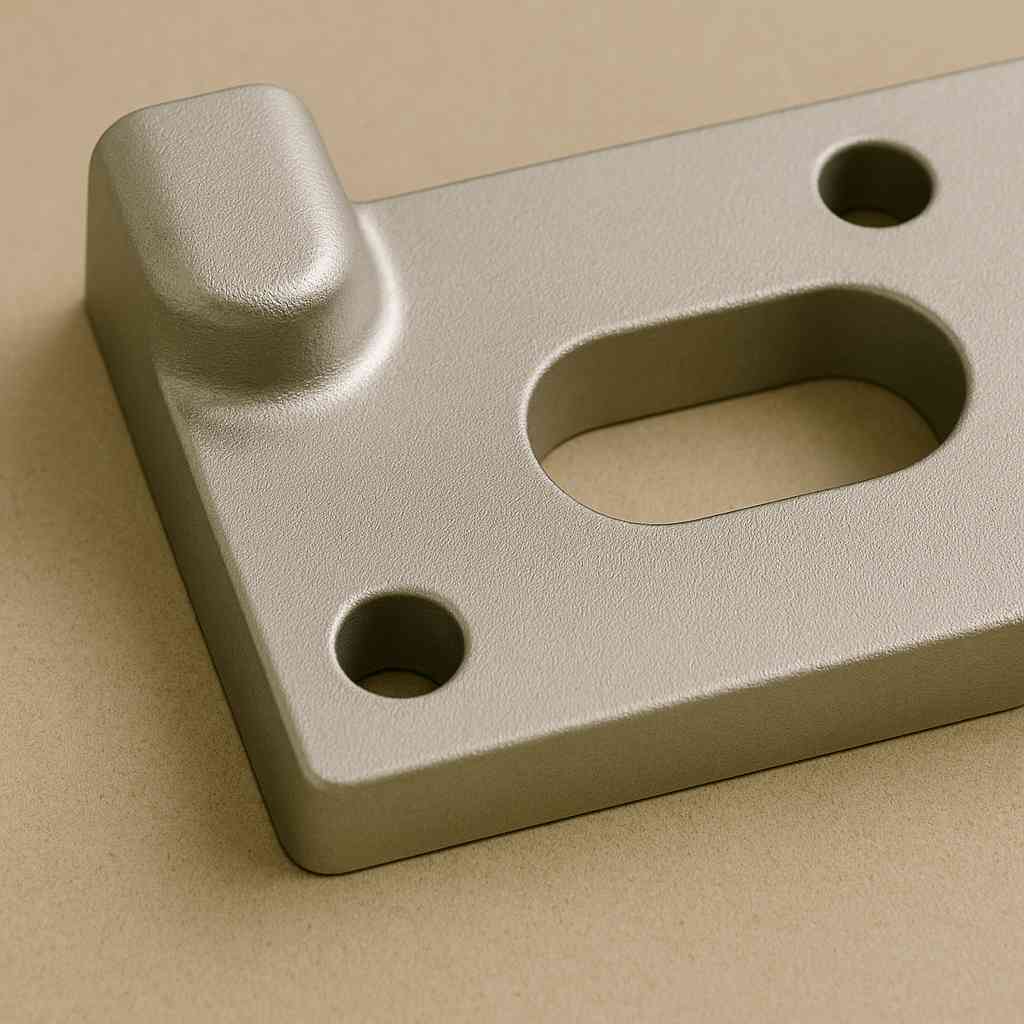
A clean metal casting shows how zircon molds produce sharp edges and smooth surfaces
Precision casting isn’t just for high-tech jets or medical tools. Even medium-grade pumps, gears, and frames benefit when molds hold shape and metal cools evenly. Consistency reduces inspection rejects, re-casting, and customer complaints.
Bottom line: zircon sand doesn’t just fill a mold — it locks in detail and controls heat so each part comes out right the first time. For purchasing managers, this means predictable quality, fewer production delays, and smoother customer deliveries. And that makes zircon an investment, not just a raw material.
Microscope view showing uniform grains that improve mold surface finish
What Role Does Purity Play in Casting Quality?
Here’s the thing: purity isn’t just a number — it keeps molds strong and parts clean. Impurities in sand can react during pouring, weaken mold walls, or cause tiny flaws inside cast parts. That’s trouble for any shop making high-precision components.
Good zircon sand comes cleaned and graded to tight standards. Reputable suppliers remove excess iron, clay, and organic bits so the sand stays stable at high heat. This chemical stability means fewer surprises once metal hits the mold.
Smart buyers always ask for a lab report showing ZrO₂, SiO₂, and iron levels. Checking these helps avoid bad batches and keeps casting quality steady.
Component | Typical High-Grade Value |
---|---|
ZrO₂ + HfO₂ | 65–66% |
SiO₂ | 32–33% |
Fe₂O₃ | Below 0.15% |
Quick tip: the cleaner the sand, the safer the mold. For tight-tolerance work — think aerospace or medical parts — pure sand protects quality and cuts hidden risks. It’s a simple safeguard that keeps production smooth and rework costs low.
How Does Zircon Sand Handle Extreme Heat?
Now, think about this: high pouring temperatures break weak molds. Zircon’s thermal conductivity helps heat spread evenly. This cuts hot spots that can crack mold walls.
Unlike silica that expands suddenly at 573°C, zircon shows stable expansion. This means molds keep shape even with metal at 1400–1600°C.
Repeated heating? No problem. Zircon handles multiple cycles before breakdown. This extends mold life and reduces sand replacement cost.
Property | Value |
---|---|
Thermal Conductivity (W/mK) | 2.5 |
Expansion Coefficient (10⁻⁶/°C) | 4.5 |
Max Service Temp (°C) | 1650 |
Key takeaway: better heat handling equals fewer scrap parts.
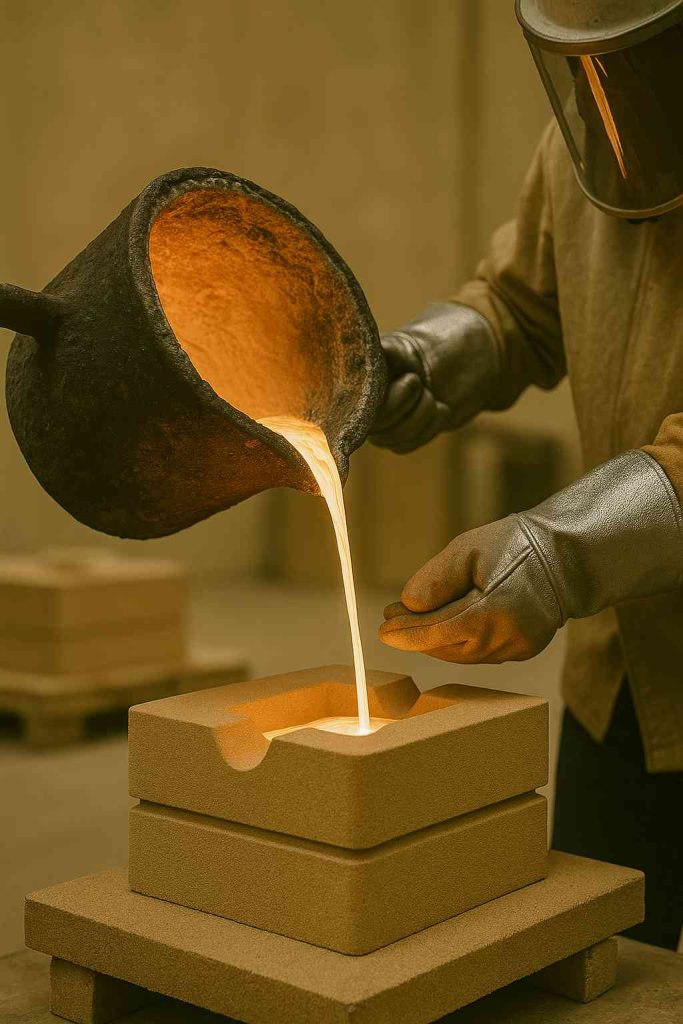
Molten metal being poured safely into a stable zircon sand mold
Where Is Zircon Sand Sourced and Processed?
Here’s what matters: knowing where zircon comes from helps buyers judge supply risks and quality. Major reserves lie in Australia, South Africa, and parts of China. These regions have stable mining operations and well-developed export routes.
After mining, raw zircon goes through washing and grading. This removes dirt, fine clay, and other unwanted bits. Better cleaning means more consistent grain size and fewer unexpected mold failures.
Smart procurement teams check a supplier’s track record. Good suppliers back up their batches with quality reports and clear shipping schedules. This reduces delays and last-minute sourcing headaches.
Major Region | Known Producers | Usual Purity |
---|---|---|
Australia | Iluka Resources | Very High |
South Africa | Richards Bay | High |
China | Various Local Mines | Medium to High |
One takeaway: strong sourcing and good processing mean fewer mold surprises and smoother planning for buyers who need steady casting runs.
What Are the Cost Benefits for Foundries?
Let’s break it down: zircon sand costs more up front than basic sand — but it often saves more than it costs. Molds last longer, hold shape better, and handle more pours before wearing out. That means fewer replacements and less downtime for changing molds mid-shift.
Fewer casting defects save time and money on repairs. When molds fail less often, production lines run smoother, keeping delivery dates safe and overtime costs down.
Cost Factor | Benefit with Zircon |
---|---|
Mold Life | Extended |
Defect Rate | Lower |
Scrap Waste | Reduced |
Downtime | Less Frequent |
In short: while the price per ton is higher, the total cost per usable part usually drops. Finance teams and planners see this payback clearly in budget forecasts. Better molds mean stable production and happier customers.
How to Choose the Right Zircon Sand?
Here’s a smart move: picking the right zircon sand makes or breaks mold performance. Not every project needs the same grain size or purity level, so buyers should match sand specs to their casting needs.
Fine mesh sizes work best for parts with sharp edges and detailed features. Coarser grains handle larger, thicker molds where ultra-smooth surfaces matter less. Checking mesh size consistency helps avoid mold defects like thin spots or poor flow.
Always ask for supplier certificates. Trusted sellers provide grain size distribution, moisture content, and chemical test results for each batch. Testing a small sample run is a safe way to confirm the sand meets shop standards before placing big orders.
Parameter | Best Practice |
---|---|
Mesh Size | Choose based on part detail |
Moisture | Keep under 0.5% |
Purity | Confirm with lab data |
Supplier Support | Look for quick batch reports |
Many foundries also check if suppliers offer technical support. Good partners help adjust sand specs as part designs evolve, so production stays efficient and costs stay predictable.
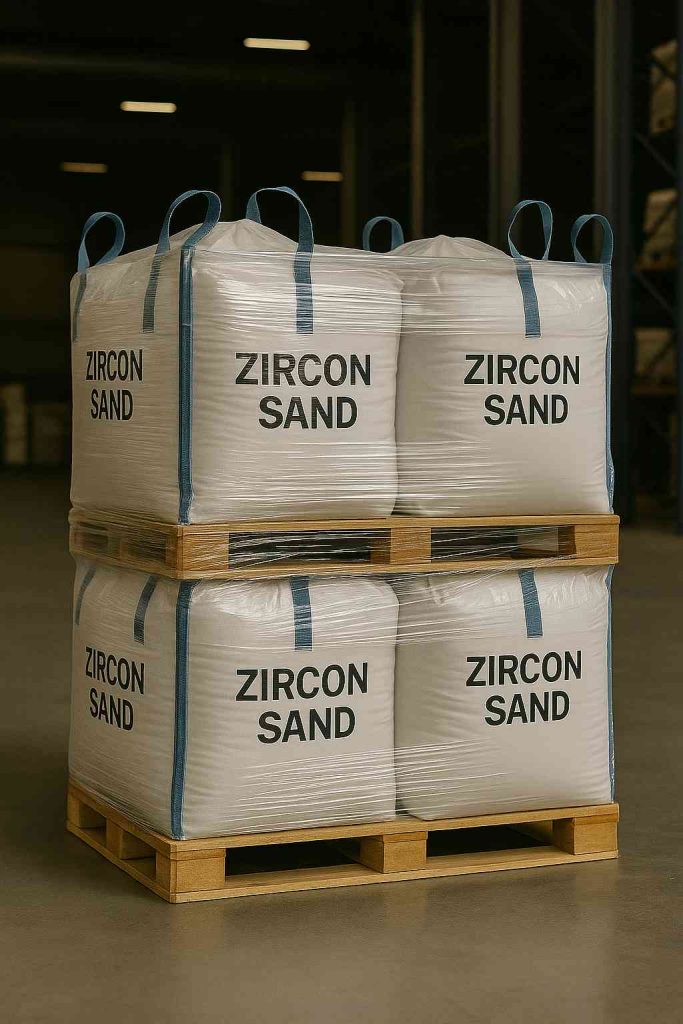
Pallets of bagged zircon sand stored clean and dry, ready for shipment to foundries worldwide
In short: taking time to pick the right sand — and the right supplier — protects quality, keeps costs steady, and avoids surprises once production ramps up. It’s a simple step that helps every batch meet customer expectations.
What Are Common Issues When Using Zircon Sand?
Here’s what shops need to watch: even top-grade zircon sand needs care to work its best. One common problem is moisture. If bags sit on damp floors or in humid storage, sand absorbs water. Wet sand clumps together, causing rough mold walls and bad cast surfaces.
The fix is simple — store bags on raised pallets in a dry, well-ventilated space. Rotate stock so older bags get used first, keeping sand fresh and free-flowing.
Another challenge is breakdown from repeated use. After several casting cycles, grains can crack or become too fine. This clogs filters and affects mold strength. Foundries should check reclaimed sand for excessive fines and add fresh sand if needed.
Issue | Solution |
---|---|
Moisture Absorption | Store Dry, Use Pallets |
Grain Breakdown | Screen Regularly |
Waste Handling | Follow Local Disposal Rules |
Environmental rules also apply. Many regions require safe handling and proper disposal of spent sand. Using sand reclamation helps meet rules and saves money. A few checks in storage and handling prevent costly casting headaches later.
How Is Waste Zircon Sand Recycled?
Here’s good practice: instead of dumping used zircon sand, many foundries clean and reuse it. Sand regeneration burns off binders and filters out debris. Thermal and mechanical reclamation methods both work, depending on plant size and local setup.
Recycled sand cuts new purchase needs. It also reduces landfill fees and helps meet environmental targets. Some shops run small reclaim units in-house for quick reuse. Others send used sand to outside recyclers who clean and return it ready for molds.
Reuse Method | Advantage |
---|---|
In-House Reclaim | Quick Turnaround |
Outsourced Reclaim | No Extra Equipment |
Disposal | Higher Cost, Less Eco-Friendly |
Regular testing of recycled sand helps maintain performance. Good practice mixes a portion of fresh sand to keep molds strong and defects low. Over time, recycling becomes a reliable way to balance quality and budget.
How Do Industry Standards Affect Procurement?
One more thing buyers care about: meeting industry standards keeps projects on track and clients satisfied. Standards like ASTM E11 or ISO 11127 define grain sizes, purity levels, and moisture limits. Smart procurement teams make sure every delivery matches these specs.
Contracts should clearly list sand grades, delivery times, testing rules, and penalties for substandard batches. This protects production from delays and costly mold failures.
Standard | Covers |
---|---|
ASTM E11 | Sieve Mesh Sizes |
ISO 11127 | Chemical Purity |
Local Rules | Disposal & Worker Safety |
Many buyers keep backup suppliers in case of sudden demand spikes or port delays. Planning ahead with clear contracts, verified specs, and reliable partners means mold quality stays high — and casting runs stay on schedule. It’s one more way zircon sand supports steady production and keeps customers happy.
Conclusion
Zircon sand keeps molds stable, parts precise, and costs under control. Foundries see fewer defects, smoother finishes, and longer mold life. That means better output and less waste.
With Global Industry, buyers get steady supply, tested quality, and support they can trust. Ready to improve your casting line? Reach out today for samples or pricing and see how stable molds protect your bottom line. We’re here to help your foundry run strong and deliver on time, every time.
FAQ
Q1: What industries use zircon sand for casting?
Many precision casting sectors rely on zircon sand due to its excellent thermal resistance and low expansion characteristics. Key industries include aerospace, automotive, medical equipment manufacturing, and industrial machinery production. These industries value zircon sand for its ability to produce high-quality, intricate castings that meet stringent performance specifications.
Q2: Can zircon sand be reused after casting?
Yes, foundries often reclaim and regenerate used zircon sand to cut costs and reduce waste. The regeneration process involves cleaning the sand to remove impurities and restore its properties, allowing it to be reused in subsequent casting processes. This sustainable practice not only minimizes environmental impact but also maintains casting quality, which is essential for manufacturing precision components.
Q3: Is zircon sand safe for workers?
When handled correctly with appropriate protective measures, zircon sand is generally safe for workers. However, dust control and proper ventilation are critical to prevent inhalation risks. Employers should provide personal protective equipment (PPE) such as masks, goggles, and gloves to ensure safety during handling and processing. Regular training on safe handling practices is also advisable to minimize exposure.
Q4: How does zircon sand affect product turnaround time?
Zircon sand enhances product turnaround time by improving mold durability and reducing defect rates. Its superior thermal stability allows for quicker cooling cycles, enabling foundries to expedite production. Consequently, reduced defects lead to fewer rework processes, resulting in faster delivery of finished parts to customers. This efficiency is crucial in industries with tight production schedules.
Q5: What is the typical price range for zircon sand?
Prices for zircon sand can vary significantly based on grade, purity, and global market conditions. Typically, the cost ranges from 1,000 to 1,000 to 1,000 to 2,000 per metric ton, but fluctuations in demand and supply can impact prices. Buyers should factor in long-term savings from its durability and high performance, as the initial investment in high-quality zircon sand can lead to reduced maintenance and replacement costs over time.