Are you facing material limits in your work? Many makers struggle to find materials that can handle tough conditions, last long, or have special features. Old materials often fail. This leads to bad product work and higher costs. What if there was a way to fix this? This article shows a clear answer: changed zircon powder. This new material helps make things work better. It gives you stronger products that handle heat well and have special uses. Our ideas come from deep study and real-world use in material science. We give you facts you can use to make your products better.
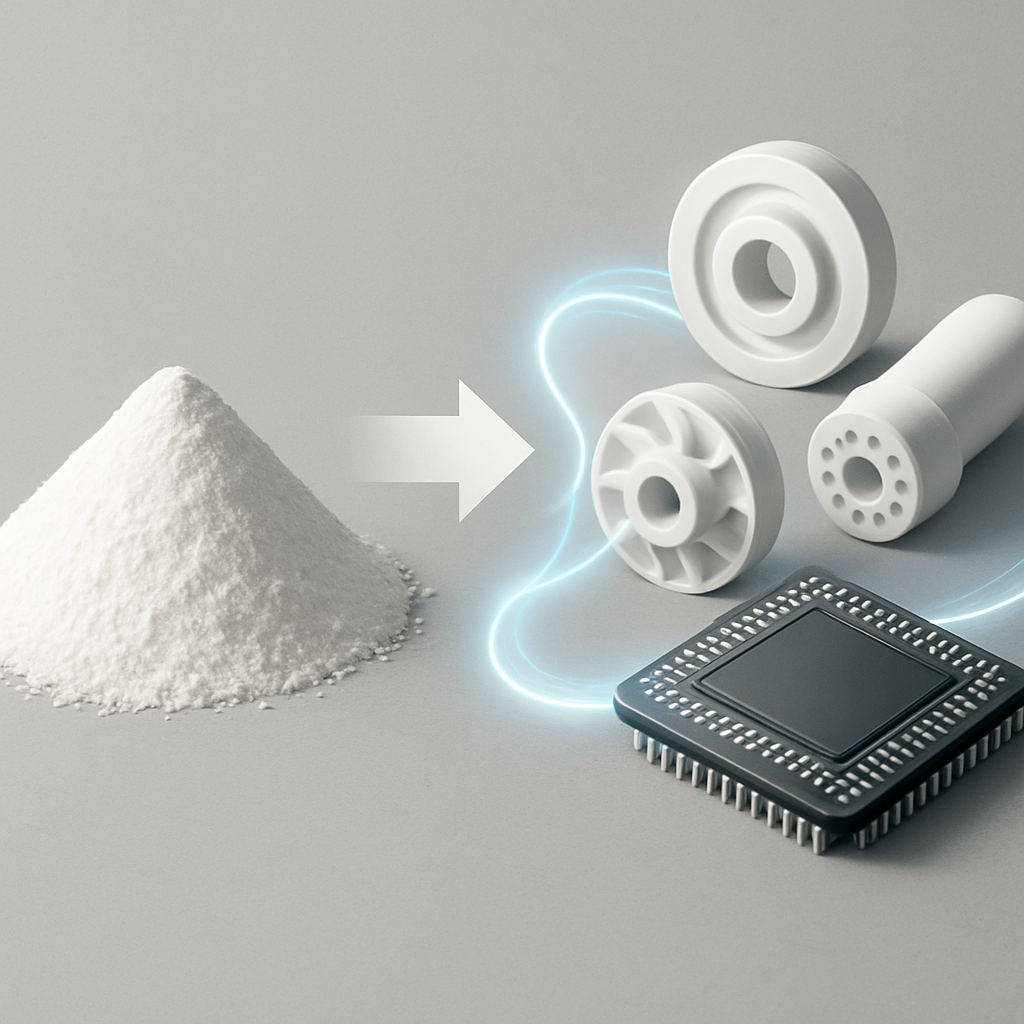
What Is Modified Zircon Powder?
Zircon powder comes from zircon sand. It is a basic material in many industries. It is a natural mineral, zirconium silicate (ZrSiO4). It is known for its high melting point, chemical stability, and resistance to wear. But raw zircon powder has limits. These limits stop it from being used in high-performance products. For example, it might not react well with other materials. Or its strength might not be enough for tough places. It also might not mix well with other materials in composite products. So, what makes modified zircon powder different?
Modification means changing the physical or chemical traits of raw zircon powder. This makes it work better. This process turns a basic material into a special part that can meet tough technical needs. The main goal is to make the powder fit specific uses by fixing the weak points of the raw material. For example:
- Surface treatments can help it spread better in plastics.
- Doping can change how it conducts electricity or how it expands with heat.
Each method adds new or better traits, including more strength, better heat stability, or improved catalytic action. Knowing these changes helps you see how useful this material is.
There are several basic ways to modify zircon:
- Surface coating: A thin layer of another material (e.g., silica, alumina, or plastics) is put on the zircon particles. This helps the powder mix better in different materials, improves chemical fit, or adds a protective layer.
- Chemical grafting: Working groups are chemically joined to the zircon surface, creating a special connection that can react with other parts in a mix. This leads to stronger bonds and better material traits.
- Doping: Small amounts of other elements are put into the zircon crystal.
Each method aims to give new or better traits, including more strength, better heat stability, or improved catalytic action. The method chosen depends on what the final product needs and what traits need to be better. Understanding these changes helps you see how useful this material is.
Modified zircon powder is very important in advanced materials. It is a key part of making high-performance ceramics, special heat-resistant materials, and advanced coatings. Its special traits allow for parts that work in extreme heat. They can also resist harsh chemicals. Or they can show exact electrical traits. Without these changes, many modern industrial products would not be possible. This material helps make new things in fields from aerospace to medical devices.
Historically, zircon has been used for hundreds of years. It was mostly used in its natural form. It was used for things like pottery and abrasives. Changing zircon powder in a planned way started in the mid-20th century. This was because there was a growing need for materials that performed better in new technologies. Early changes focused on making it more heat-resistant for furnaces. As material science got better, so did the ways to modify zircon. This led to many different special powders we have today. This shows a constant effort to make materials better.
Property | Unmodified Zircon Powder | Modified Zircon Powder (Example) |
---|---|---|
Melting Point | ~2550 °C | ~2550 °C (retained) |
Chemical Reactivity | Low | Tunable (e.g., increased surface activity) |
Mechanical Strength | Good | Excellent (e.g., improved fracture toughness) |
Thermal Conductivity | Moderate | Variable (can be enhanced or reduced) |
Dispersibility | Poor in some matrices | Good (e.g., in polymers, solvents) |
Surface Area | Low | High (e.g., for catalytic applications) |
Why Modify Zircon Powder?
Modifying zircon powder fixes many limits of its raw form. Natural zircon handles high heat well. But its basic structure often lacks the right traits for new industrial uses. For example, in mixed materials, raw zircon might not stick well to plastic parts. This makes the final product weaker. By changing its surface or inside structure, makers can fix these issues, making zircon much more useful and strong.

Here are the key reasons to modify zircon powder:
● Enhanced Specific Functions: For example, in oven linings, modified zircon can handle heat stress better, preventing cracks from rapid temperature changes. In electronics, specific modifications can fine-tune electrical properties for better signal flow or energy storage.
● Meeting Industry Needs: Modern industries like aerospace and medical tools require materials with improved reliability and longevity. Modified zircon, with its tailored surface, can meet these tough demands, making it suitable for implants or dental components.
● Long-Term Cost-Effectiveness: While initial modification steps might increase cost, the improved performance and longer lifespan of products made with modified zircon often lead to significant savings. For instance, an oven lining lasting twice as long means less downtime and lower repair costs.
● Expanded Applications: Modified zircon powder can be used in many different areas beyond its traditional heat-resistant applications. This includes strong ceramics for armor or special coatings for rust protection. This adaptability makes modified zircon a top choice for engineers and product makers.
Limitation of Raw Zircon | How Modification Addresses It |
---|---|
Poor mixing in plastics | Surface changes, coating |
Low heat shock resistance | Adding other elements, particle design |
Bad electrical traits | Careful adding of elements, crystal structure change |
Not very reactive | Chemical bonding, surface activation |
Doesn’t mix well with some materials | Surface treatment for better stickiness |
Key Zircon Powder Modification Methods
SuSurface treatment is a big part of changing zircon powder. These ways change only the outside layer of the zircon particles; they don’t change the main part. Common ways include:
- Coating: A thin, even layer of another material (e.g., silica, alumina, or plastics) is put on the zircon particles. This helps the powder mix better in different materials, improves chemical fit, or adds a protective layer.
- Grafting: Working molecules are chemically joined to the zircon surface. This makes a special connection that can react with other parts in a mix, leading to stronger bonds and better material traits.
Why is this important for your product? It means you can mix zircon better into complex material systems, leading to better performance.
Adding other elements and mixing methods are key to changing zircon powder’s basic traits. These include:
- Doping: Small amounts of foreign elements are put into the zircon crystal. These added elements can change how zircon acts with electricity, heat, or force. For example, adding yttria (Y2O3) is a known way to make zirconia stable, which is key for uses needing high toughness.
- Mixing: Different compounds are put together to make a new material with better traits. These ways let you control the material’s basic behavior exactly, opening doors for special uses.
Controlling particle size and shape is another key way to change zircon. The size, shape, and how zircon particles are spread greatly affect the final material’s traits. For example:
- Nanoscale particles: Making particles very small (nanoscale) can greatly increase their surface area. This leads to better reaction and better sticking together at lower heat.
- Particle shape: Round particles often flow better and pack tighter, which is good for things like molding. Odd shapes might stick together better for some rough uses.
Ways like controlled making, spray drying, and grinding are used to get the right particle traits. Think about how this affects your making process. Good particle shape can lead to more steady product quality and lower making costs.
Chemical making ways offer many paths to make changed zircon powder with special traits. These ways involve making zircon or its starting materials under controlled chemical conditions. This is to get specific mixes, crystal shapes, or particle shapes. Hydrothermal making, sol-gel ways, and co-making are examples of these paths. These ways let you add other elements at the smallest level. This leads to very even materials. They also let you make complex mixed particles. Here, zircon is closely joined with other working materials. This level of control at the making stage is key for making new materials with exact performance traits.
Advanced making ways help the change methods. They make the zircon powder’s traits even better. These include strong grinding, plasma shaping, and different sticking ways. Strong grinding can make particles smaller and add flaws. These flaws make it react better. Plasma shaping turns odd-shaped particles into smooth, round ones. This makes them flow and pack better. Special sticking ways, like spark plasma sticking (SPS), let you make things denser at lower heat and faster. This keeps fine grain shapes and stops bad changes. These ways are key for turning the good points of changed zircon powder into high-performing finished products.
Modification Method | Primary Effect | Example Application |
---|---|---|
Surface Coating | Better mixing, chemical fit | Plastic mixes, paints |
Doping | Changed electrical/heat traits, stable phase | Fuel cells, heat barriers |
Particle Size Control | Better reaction, sticking behavior | Advanced ceramics, catalysts |
Chemical Synthesis | Exact mix, evenness | Pure ceramics, working materials |
High-Energy Milling | Smaller particles, more reaction | Nano mixes, reactive powders |
Enhanced Properties From Zircon Modification
Changed zircon powder shows many better traits. These greatly improve how materials work in different uses. Here are some key enhancements:
● Strength and Hardness: By controlling particle size, shape, and surface chemistry, makers can create zircon powders that lead to ceramics with much better toughness and wear resistance. For example, in tooth ceramics, modified zircon can make dental parts that last longer and chip less, meaning a longer life for patients.
● Heat Stability and Conductivity: Zircon naturally handles heat well, but modifications can fine-tune this. For hot uses like oven linings or heat barrier coatings, modified zircon can handle even hotter cycles without breaking down. Some changes can also make it conduct heat better (for electronics) or less (for insulation), allowing for exact heat control solutions.
● Chemical Resistance: Modified zircon powder can fight off acids, bases, and harmful gases much better, which is very important in chemical manufacturing tools. Surface changes can create a protective layer that stops chemical attacks, ensuring parts last long and stay whole.
● Electrical and Light Traits: In electronics, specific doping or surface treatments can change zircon’s electrical constant, making it good for capacitors, insulators, or circuit bases. Its light traits can also be modified for use in special glass, optical fibers, or bright colors.
● Dispersibility and Mixing: Raw zircon can often clump together, leading to uneven spread and poor material traits. Modifications like surface coatings or chemical joining can greatly help the powder spread evenly, ensuring the final product is mixed well and works best.
Industrial Applications of Modified Zircon Powder
Modified zircon powder is used a lot in ceramics and heat-resistant materials. Here’s how:
- Advanced Ceramics: It is a key part of tooth replacements, valued for its added strength and body-friendliness.
- Industrial Ovens and Kilns: Modified zircon-based heat-resistant parts last longer and handle high heat better, meaning they work longer and need less fixing. It can handle tough conditions, making it a must-have for uses needing high performance and long life.
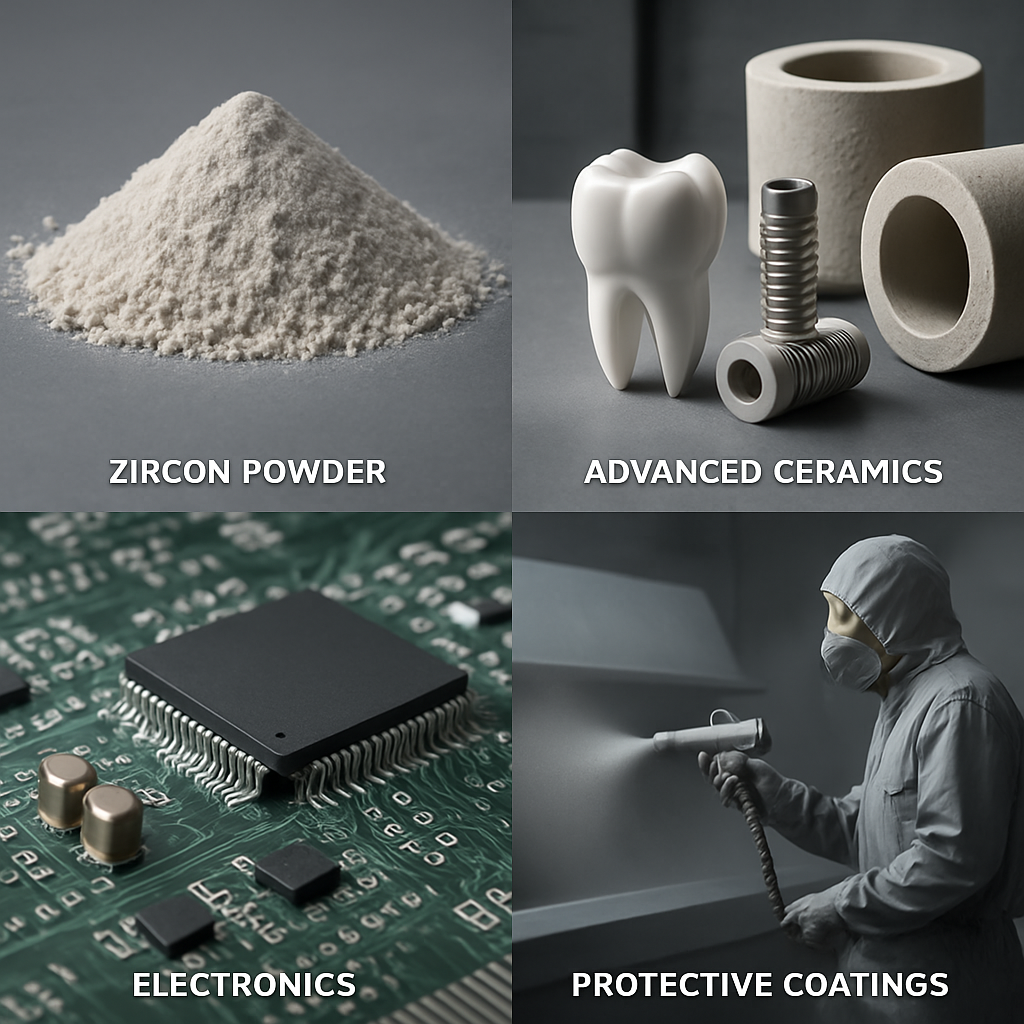
In coatings and paints, changed zircon powder has many uses. It can be used as a color, giving great cover and whiteness. This is true especially in hot uses where other colors might break down. Beyond looks, changed zircon makes coatings stronger and more protective. It gives better wear resistance, chemical stability, and UV protection. This makes it great for protective coatings in harsh places. It makes coated surfaces last longer. It also means less need for often re-coating.
Changed zircon is also key in electronics and electrical parts. Its special electrical traits make it good for capacitors, insulators, and bases for circuits. It helps make smaller, more powerful electronic parts. This is because it can handle high heat and keep its electrical traits. In photonics, changed zircon is used in special glass and optical fibers. This allows for better light control and signal sending. These uses show how important changed zircon is for making new electronic and light-based tools.
Modified zircon powder is also used in the biomedical field. Its high strength, biocompatibility, and resistance to wear make it good for dental implants and other medical devices. It can be used in joint replacements and surgical tools. This shows its value in critical health uses. The ability to tailor its surface for better integration with biological systems makes it a preferred material for long-term implantable devices.
Conclusion
Modified zircon powder is a game-changer in material science. It transforms a basic material into a high-performance solution. This helps meet the tough demands of modern industries. By changing its traits, modified zircon offers better strength, heat stability, chemical resistance, and electrical properties. This makes it useful in many areas, from advanced ceramics to biomedical devices. For makers and procurement pros, understanding these changes is key. It helps you make smart choices. It also helps you find new chances to innovate.
Investing in modified zircon powder means investing in better product work, longer life, and new ideas. This helps you stay ahead in a fast-moving market. Consider how modified zircon powder can elevate your next project. It can help you achieve new levels of performance and reliability.
FAQ
Q1: What is the primary purpose of modifying zircon powder?
The primary purpose of modifying zircon powder is to enhance its physical, chemical, and functional properties, making it suitable for high-performance applications where raw zircon powder has limitations.
Q2: How does surface treatment improve zircon powder?
Surface treatment, such as coating or grafting, improves zircon powder by enhancing its dispersibility in various matrices, improving chemical compatibility, and adding protective layers, leading to better material integration and performance.
Q3: In which industries is modified zircon powder most commonly used?
Modified zircon powder is most commonly used in advanced ceramics, electronics, heat-resistant materials, coatings, paints, and biomedical applications due to its enhanced properties.
Q4: Can modified zircon powder reduce overall production costs?
Yes, while initial modification steps might add cost, the enhanced performance, longer lifespan, and reduced need for replacements in products made with modified zircon powder often lead to significant long-term cost savings and a higher return on investment.
Q5: What are some emerging applications for modified zircon powder?
Emerging applications for modified zircon powder include advanced sensors, next-generation communication tools, high-quality screens, and specialized catalytic applications for environmental remediation, driven by its tunable electrical, optical, and surface properties.