Modern glass and glazing formulations demand superior performance. Manufacturers constantly seek materials that enhance strength, clarity, and durability. Without the right additives, products often fall short of expectations.
This presents a challenge for purchasing managers and technical teams. They need materials that offer consistent quality and tangible value. Our advanced material science offers a clear path forward. We understand the needs of contemporary industries.
This article will explain how zircon powder can help. It can significantly improve your glass and glazing products. You will learn about its unique properties and applications. This knowledge will empower you to make informed decisions. It ensures your products meet high standards. Our goal is to provide actionable insights. This will help you stay competitive.
Zircon Powder: What Is It?
Zircon powder is a finely ground mineral, zirconium silicate (ZrSiO4). It comes from zircon sand, a natural material found in many places. Zircon sand undergoes a strict processing procedure to ensure purity and the right particle size.
Key Features:
- Composition: Zircon powder mainly contains high amounts of zirconium dioxide (ZrO2) and silicon dioxide (SiO2).
- Special Properties: These components give it strong characteristics. These include a high refractive index, excellent thermal stability, and strong chemical resistance.
These properties offer practical benefits in many industrial processes. For example, its high melting point, about 2550°C (4622°F), makes it perfect for high-temperature applications. It does not easily react with other substances, which is a huge advantage where stability is important.
How It’s Made:
Making zircon powder involves several steps:
- Mining: It starts with extracting raw zircon sand.
- Concentration: The raw sand is then cleaned using physical methods like gravity and magnetic separation to remove impurities.
- Grinding: After cleaning, the sand is ground into very small particles. The particle size is precisely controlled to suit different uses.
Different types of zircon powder exist, varying in purity and particle size. These differences allow for specific applications across many industries.
Common Uses:
Zircon powder is widely used in many areas:
- Ceramics: It makes glazes and tiles opaque, giving them a bright white look. It also makes them stronger and more resistant to heat changes.
- Refractories: Zircon powder can withstand extreme heat, making it a key part of heat-resistant products like bricks, crucibles, and furnace linings.
- Foundries: Zircon sand and powder are used for metal casting molds because they can handle high temperatures and do not expand much, helping make high-quality metal parts.
- Advanced Applications: Zircon compounds are also used in special ways, including nuclear fuel rods and as a source for zirconium metal.
The unique properties of zircon powder make it vital in these fields. Understanding what it is helps you see how it can improve glass and glazing.
Property | Typical Value |
---|---|
Chemical Formula | ZrSiO4 |
Mohs Hardness | 7.5 |
Melting Point | ~2550°C (4622°F) |
Density | 4.6 – 4.7 g/cm³ |
Refractive Index | 1.93 – 2.01 |
Thermal Conductivity | Low (2.5 – 5.0 W/m·K) |
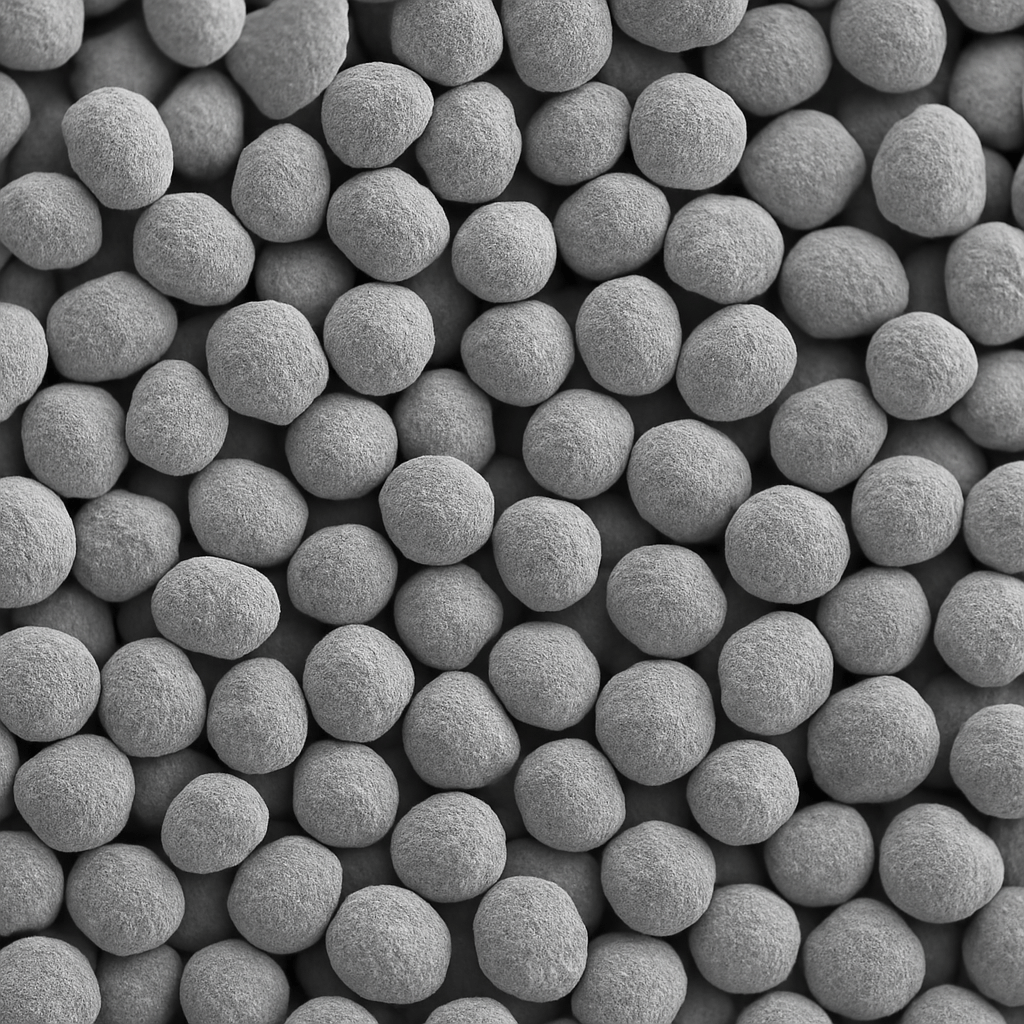
Why Use Zircon in Glass?
Adding zircon powder to glass offers many benefits. Its role in glass making is complex, extending beyond mere aesthetics. It provides tangible improvements in product performance.
Key Benefits in Glass Manufacturing:
- Opacifier: Zircon powder makes glass opaque, giving it a milky or white appearance. This is useful for applications where transparency is not desired, such as architectural or decorative glass.
- Mechanical Strength: Zircon powder makes glass stronger, reducing its likelihood of breaking and scratching. This directly translates to fewer defects for manufacturers.
- Thermal Shock Resistance: Glass with zircon powder can better handle rapid temperature changes. This is vital for products exposed to hot and cold shifts, helping to extend their lifespan.
- Chemical Durability: Glass containing zircon powder resists acids, alkalis, and water. This enhances product longevity, especially in harsh chemical environments.
How It Compares:
While other materials can also make glass opaque, zircon powder stands out due to its excellent combination of properties. It simultaneously improves opacity, strength, and chemical resistance.
- Titanium Dioxide: This can also make glass opaque, but it often does not provide the same level of mechanical strength as zircon powder.
- Older Opacifiers: Some older materials might introduce unwanted colors. Zircon powder maintains a pure white or neutral color, making it a top choice for high-quality glass.
Cost Implications:
Although zircon powder might have a higher initial cost, its benefits often lead to long-term savings. Improved product quality, fewer breakages, and an extended product life result in overall cost reductions. For example, making stronger glass means less waste and fewer customer complaints, leading to a more efficient production process. Enhanced performance also adds value for the end-user, potentially allowing for higher pricing of the final product.
Using zircon powder wisely is not just about material cost. It improves the entire production process and helps deliver superior products. This makes it a smart choice for businesses focused on quality and long-term value.
Glass Property | Improvement from Zircon Powder |
---|---|
Opacity | Significantly increased |
Mechanical Strength | Enhanced |
Thermal Shock Resistance | Improved |
Chemical Durability | Better resistance to acids/alkalis |
Scratch Resistance | Higher |
How Zircon Enhances Glass Strength?
Zircon powder significantly enhances glass strength through several key mechanisms. Its presence in the glass matrix contributes to a more robust and resilient material.
How It Strengthens:
- Nucleation Sites: When zircon powder particles are added to molten glass, they act as nucleation sites. These points facilitate the formation of a uniform glass structure during cooling.
- Homogeneous Structure: This leads to a more even and consistent internal structure. This reduces internal stress and minimizes the formation of tiny flaws, which are common starting points for cracks.
- Better Fracture Resistance: By reducing these weak spots and promoting a uniform structure, zircon powder makes glass much harder to break. It significantly improves its resistance to fracture.
Improved Mechanical Properties:
Glass incorporating zircon powder exhibits clear improvements in its mechanical properties, particularly in how it handles external forces:
- Higher Flexural Strength: The glass can better withstand bending forces without fracturing.
- Better Impact Resistance: The material becomes tougher and more resilient to sudden impacts.
For example, in safety glass applications, this added strength is vital. It helps prevent dangerous shattering, causing the glass to break into smaller, safer pieces instead. This provides a significant safety boost in various products.
Thermal Shock Resistance:
Thermal shock resistance is another major benefit. Glass products often undergo rapid temperature changes, which can induce significant stress. Zircon powder helps glass handle these stresses by improving its thermal expansion characteristics. This lowers the chance of breakage due to thermal shock, leading to more reliable products, fewer breakages, and ultimately, higher customer satisfaction and fewer warranty claims.
Toughness in Harsh Conditions:
Glass with zircon powder also becomes tougher in harsh environments. It resists wear and tear and can withstand chemical attacks. This makes it suitable for demanding applications such as laboratory glassware or industrial factory equipment. Zircon powder adds a layer of protection, extending product life and reducing the need for frequent replacements, which translates to cost savings for businesses.
Real-World Example:
Consider special factory windows exposed to extreme heat and chemicals. Adding zircon powder keeps them strong and intact, ensuring continuous operations and enhanced worker safety. The result is a better-performing product that lasts longer and provides more value, making zircon powder a smart choice for glass manufacturers seeking top performance.
Strengthening Mechanism | Benefit to Glass Performance |
---|---|
Nucleation Sites | Fine microstructure |
Defect Reduction | Increased fracture resistance |
Improved Thermal Expansion | Enhanced thermal shock resistance |
Chemical Inertness | Better chemical durability |
Hardness Contribution | Higher abrasion resistance |
Zircon’s Role in Glazing Formulations?
Zircon powder is not only crucial for glass but also plays a very important role in glazes, particularly in ceramic glazes. Its unique properties make it indispensable for achieving desired aesthetic and functional qualities.
Benefits in Ceramic Glazes:
Glazes are thin, shiny layers applied to ceramic products. Zircon powder serves as a primary opacifier, making glazes opaque. This gives ceramics a solid, even color, typically white. Without zircon powder, glazes would appear transparent. Zircon powder achieves opacity due to its high refractive index, which causes light to scatter within the glaze, resulting in a bright, smooth surface.
Beyond opacity, zircon powder significantly enhances glaze performance:
- Harder Surface: The glazed surface becomes more resistant to scratches and wear. This is a significant advantage for products like floor tiles or bathroom fixtures, ensuring they maintain their appearance and integrity over time.
- Better Chemical Resistance: Glazes often come into contact with various chemicals. Zircon powder helps the glaze resist these chemicals, preventing stains or damage. This feature is particularly useful for bathroom fixtures, keeping them clean and durable.
Tile Manufacturer Example:
Imagine a tile manufacturer who faced issues with uneven opacity and susceptibility to scratches. After incorporating zircon powder into their glaze formulation, their tiles achieved a uniformly bright white finish, and scratch resistance improved by over 30%. This dramatically reduced customer complaints, demonstrating how selecting the right materials can profoundly impact product quality.
Thermal Expansion Control:
Zircon powder also helps control the thermal expansion of the glaze when heated. This prevents common problems such as crazing (the formation of tiny cracks) or spalling (glaze flaking off). By helping the glaze’s thermal expansion match that of the ceramic body, zircon powder creates a strong bond, maintaining the product’s integrity.
The aesthetic and practical properties of zircon powder make it an essential material in ceramic glaze technology. It enables manufacturers to create high-quality, durable, and attractive ceramic products that meet market demands.
Benefit of Zircon in Glazes | Impact on Product Performance |
---|---|
Opacifying Effect | Uniform, bright white surface |
Surface Hardness | Increased scratch resistance |
Chemical Resistance | Prevents stains/corrosion |
Thermal Expansion Control | Prevents crazing/spalling |
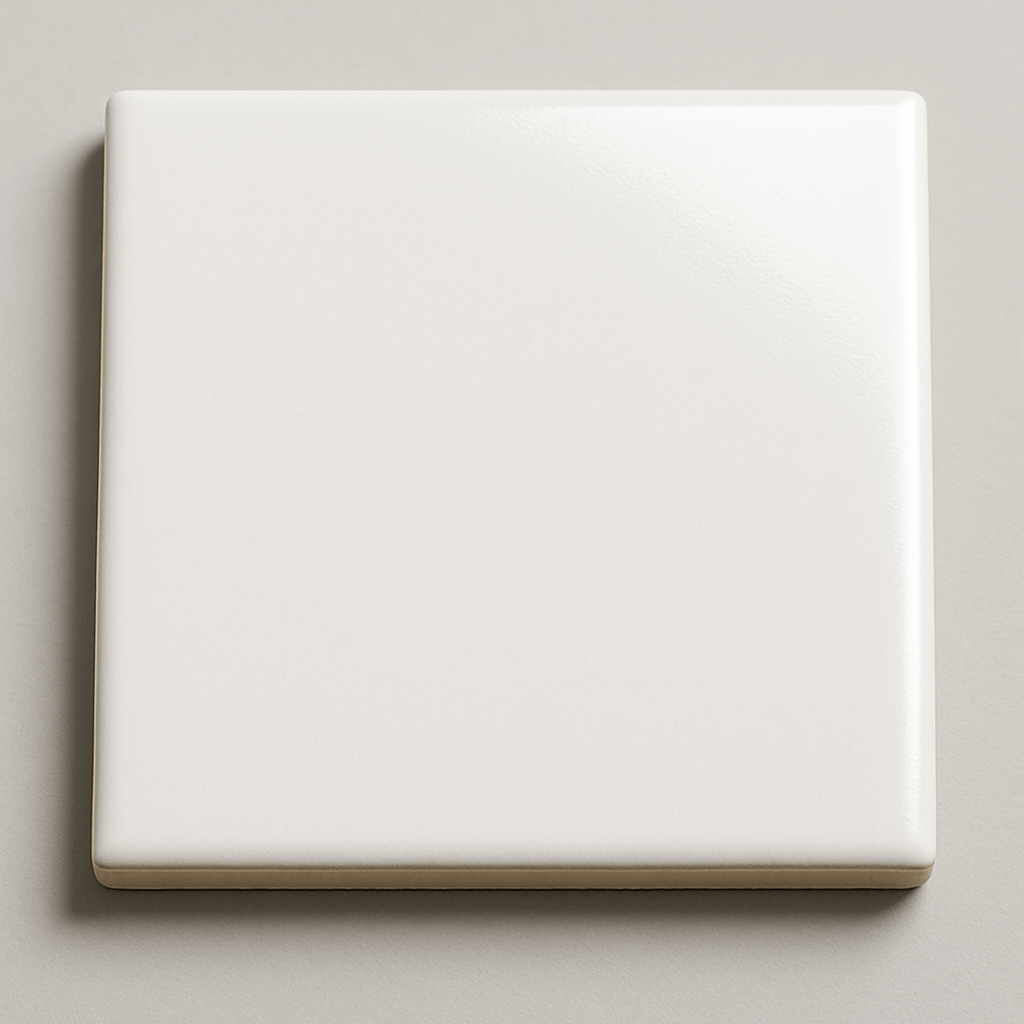
Zircon Powder for Optical Clarity?
Zircon powder is often associated with opacity, yet it also plays a role in enhancing the clarity of specialized glass. This might seem counterintuitive, but its influence is subtle and significant.
Subtle Influence on Light:
Its effect on light is precise and important. In precision optics, perfect transparency is not always the sole objective. Sometimes, the goal is to control light scattering or achieve specific light-bending properties. Zircon powder, with its high refractive index, can precisely guide light, allowing for glass with tailored optical properties.
Reducing Optical Defects:
Zircon powder helps reduce common optical flaws like streaks or bubbles. While zircon powder itself is opaque, its precise incorporation helps make the molten glass more uniform. This uniformity minimizes defects in the glass, resulting in a material optimally suited for its optical purpose.
Applications in Precision Optics:
Glass containing zircon powder is utilized in various precision optical products:
- Special Lenses and Prisms: Used for high-performance optical components requiring precise light manipulation.
- Optical Fibers: Controlled addition of zircon powder helps guide light efficiently, reducing signal loss.
- Scientific Instruments: Zircon powder can create glass that filters specific light wavelengths, enhancing the performance of light sensors.
Camera Lens Example:
Consider a camera lens manufacturer who requires glass with specific light dispersion properties. Using zircon powder allows them to achieve the exact optical characteristics needed, leading to sharper images and better color reproduction.
Future of Optical Glass:
Trends in optical glass indicate a move towards more customized solutions. There is a growing need for engineered materials that offer novel ways to control light. Zircon powder, with its fine particles and controllable properties, is well-suited for these demands. Researchers are exploring new methods to integrate zircon powder into advanced optical materials, including metamaterials and photonic crystals. These innovations promise significant advancements in data transfer, imaging, and energy efficiency.
The role of zircon powder in these developments underscores its versatility. It is more than just an additive; it is a material poised for future optical innovation, making it highly valuable for companies pushing technological boundaries.
Optical Property | Zircon Powder Contribution |
---|---|
Refractive Index | High, for light manipulation |
Uniformity | Reduces optical defects |
Light Filtering | Custom wavelength control |
Signal Guiding (Fibers) | Improves efficiency |
Zircon in Specialty Glass Products?
Zircon powder finds extensive use in a variety of specialty glass products. Its versatility makes it suitable for demanding applications where standard glass might not suffice.
Key Uses in Specialty Glass:
- Heat-Resistant Glass: This type of glass must withstand extreme temperatures without deforming. Zircon powder enhances glass stability at high temperatures and reduces its thermal expansion and contraction. This is vital for laboratory glassware, oven doors, and industrial furnace windows. For instance, a manufacturer of furnace windows found that incorporating zircon powder significantly extended the lifespan of their products, leading to cost savings for their customers.
- Radiation Shielding Glass: Glass designed to block radiation needs to be dense and capable of absorbing harmful rays. Zircon powder, with its high atomic number, increases glass density, enabling it to attenuate X-rays and gamma rays effectively. This makes it invaluable in medical and nuclear applications, such as X-ray room windows.
- Technical Glass Fibers: Glass fibers are fundamental in telecommunications and composite materials. Zircon powder can modify the refractive index of these fibers, allowing for precise control of light propagation in optical fibers. It also enhances the fibers’ strength and chemical resistance, making them robust even in harsh environments.
New Ideas and the Future:
Innovation in specialty glass continues to grow. Researchers are constantly seeking new materials to improve glass performance. Zircon powder is at the forefront of these efforts. It is being investigated for its potential in smart glass technologies, including glass that changes color or opacity in response to electrical currents or heat. These applications require specific optical and electrical properties that zircon powder can help achieve. It is also being explored for advanced display technologies.
This signifies a crucial development: creating glass with customized properties opens new markets and differentiates products. For businesses, it means staying competitive and providing solutions for future demands. Zircon powder is more than just an additive; it is a key component that enables the creation of high-performance glass products for critical applications. Ongoing research promises even more novel uses, making the future of zircon powder in specialty glass very bright.
Specialty Glass Application | Zircon Powder Contribution |
---|---|
Heat-Resistant Glass | Thermal stability, low thermal expansion |
Radiation Shielding Glass | Increased density, radiation attenuation |
Technical Glass Fibers | Refractive index control, strength |
Smart Glass Technologies | Custom optical/electrical properties |
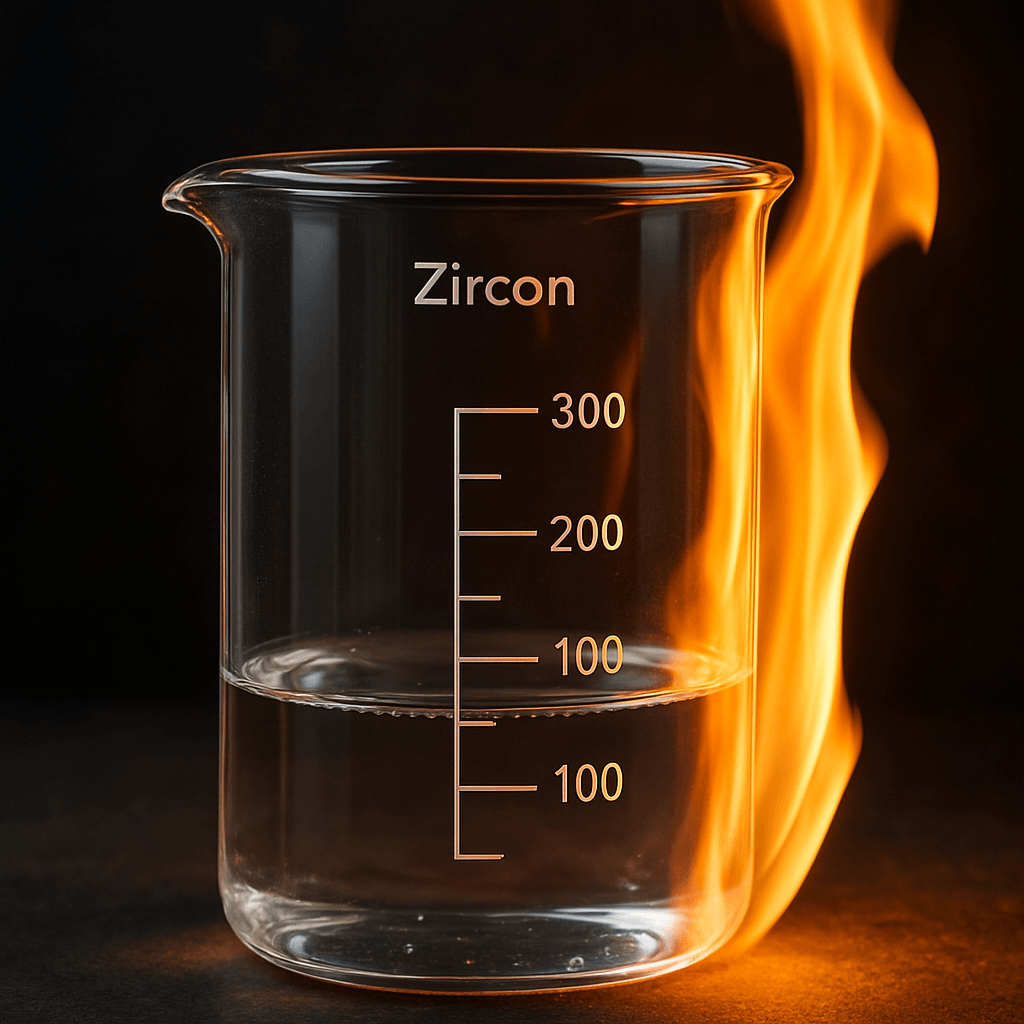
Quality Control for Zircon Powder?
Ensuring the quality of zircon powder is paramount for product performance. Purity standards are critical, as impurities can compromise the final glass or glaze, leading to flaws, reduced performance, or even product failure.
Key Quality Checks:
- Particle Size: This is crucial as it directly affects how the powder disperses in the melt and impacts the final product’s properties. Consistent particle size ensures uniform results.
- Chemical Purity: Strict control over chemical composition prevents unwanted reactions or discoloration in glass. Manufacturers often set stringent limits for impurities like iron or titanium.
- Moisture Content: Moisture must be kept low to prevent issues during high-temperature processing, such as bubbling or cracking.
- Surface Area: This property influences the powder’s reactivity and its bonding efficiency with other components in the mixture.
Testing and Approval:
Reputable suppliers adhere to rigorous testing protocols and provide a Certificate of Analysis (COA) for each batch. These certificates detail the powder’s physical and chemical properties, offering transparency and helping buyers verify that the material meets their specific requirements. Regular audits of a supplier’s quality management system are also common to ensure consistent adherence to standards and reliability.
Impact on Manufacturing Process:
High-quality zircon powder contributes to more stable and predictable manufacturing processes. It minimizes batch-to-batch variations, reducing waste and rework. Ultimately, this leads to higher yields and lower production costs. For buyers, sourcing materials from a reliable supplier with robust quality control is not just about cost; it is about mitigating risks and ensuring the consistent quality of their own products.
Conclusion
Zircon powder is a vital additive for advanced glass and glazing. Its unique properties lead to enhanced performance in terms of strength, heat resistance, chemical resistance, and optical characteristics. From architectural glass to specialized optical components, zircon powder offers tangible benefits that address the demands of modern industries. By understanding its applications and ensuring its quality, businesses can effectively leverage zircon powder to create superior products, optimize processes, and maintain a competitive edge. Global Industry provides advanced material solutions, and we are committed to helping you achieve your product goals. Contact us to discuss your needs.
FAQ Section
Q1: What is zircon powder mainly used for in glass and glazing?
Zircon powder is primarily used to opacify glass and glazes, providing a bright, uniform white appearance. It also significantly improves strength, thermal shock resistance, and chemical resistance.
Q2: How does zircon powder make glass stronger?
Zircon powder strengthens glass by acting as nucleation sites in molten glass, promoting a more uniform structure with fewer microscopic flaws. This results in glass that is much harder to break, more flexible, and more resistant to impacts.
Q3: Can zircon powder be used in clear glass?
While often used in opaque materials, zircon powder can also be employed in specialized clear glass applications, particularly in precision optics. Its high refractive index helps guide light and reduce optical flaws, allowing for glass with tailored optical properties.
Q4: What are the important quality checks for zircon powder?
Important quality checks for zircon powder include assessing particle size, ensuring high chemical purity (low impurity content), maintaining low moisture content, and controlling its surface area. Reputable suppliers provide a Certificate of Analysis (COA) to verify these properties.
Q5: What are the benefits of using zircon powder in ceramic glazes?
In ceramic glazes, zircon powder provides excellent opacity, resulting in a uniform, bright white surface. It also enhances surface hardness, improves chemical resistance, and helps control thermal expansion, preventing issues like crazing or spalling.