Zircon sand buyers often wonder about the best grain size for smooth production and consistent results. Choosing the wrong grade wastes time, creates rejects, and costs money. This article gives clear answers for purchasing managers and production heads who need reliable data before buying. It shows how to measure grain size, why it affects product quality, and how suppliers maintain stable batches. With this, any procurement or technical team gains strong confidence to select zircon sand grades wisely and avoid surprises during casting, glazing, or refractory work. Trust this clear guide for facts that matter on the shop floor.
What Defines Zircon Sand Grain Size?
Here’s the thing: grain size means the actual diameter range of each tiny sand piece. For zircon sand, this directly affects its behavior in kilns, molds, or glaze mixes. Buyers want uniform grains to get predictable melting points and smooth surfaces. Too coarse, and casting gets rough. Too fine, and flow or heat handling suffers.
Most buyers deal with three broad grades:
● Coarse grade – grains over 100 microns. Good for foundry molds where air escape is critical.
● Medium grade – 50–100 microns. This is a balanced option for many ceramic bodies.
● Fine grade – below 50 microns. Best for high-gloss glazes or fine-cast jewelry molds.
Good suppliers specify exact ranges, not just vague labels. They also provide a particle size distribution (PSD) chart for proof.
Grade | Micron Range | Typical Use |
---|---|---|
Coarse | >100 µm | Foundry molds |
Medium | 50–100 µm | General ceramics |
Fine | <50 µm | Glazes, precision casting |
Check this table when reviewing a vendor’s datasheet to match it with your application specs.
How Is Grain Size Measured in Zircon Sand?
Let’s clear this up: nobody guesses grain size by eye. Labs use certified tools. Two main methods rule this field: sieve analysis and laser diffraction.
Sieve analysis uses stacked metal screens. Sand is shaken through, and retained amounts on each sieve tell how much is coarse or fine. This method works well for larger grains but struggles below 50 microns.
Laser diffraction fires a laser beam through sand suspended in liquid. The light pattern reveals exact size distribution for each particle cluster. This method works well for powders too fine for sieves.
Every big zircon sand producer runs these tests regularly. Reports usually show D10, D50, and D90 values. D50 means half the particles are smaller than that size — a quick guide for consistency.
Method | Best For | Accuracy |
---|---|---|
Sieve Analysis | Coarse to medium grains | Good |
Laser Diffraction | Fine powders | Very high |
Always request test reports before signing supply contracts.
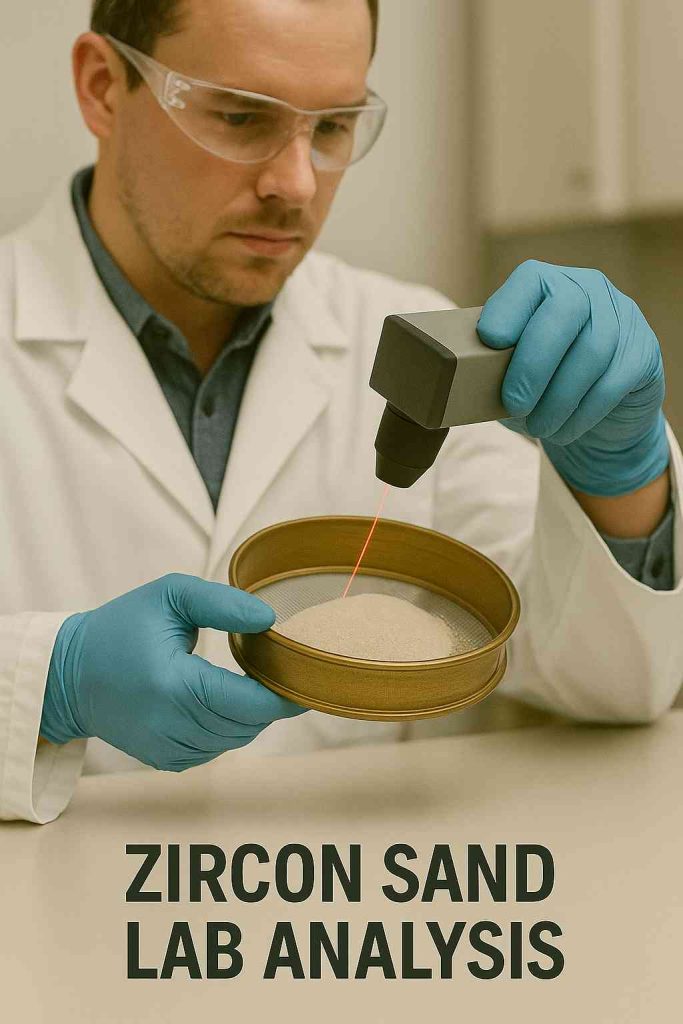
This image shows lab technicians testing zircon sand grain size with laser tools and sieves.
Why Does Grain Size Matter for Industrial Use?
Here’s why you should care: grain size controls flow, packing, and heat transfer. For foundries, coarse sand lets gases escape and stops casting defects. For tiles or sanitary ceramics, medium grains balance slip flow and surface finish. Fine grains in glazes make brilliant shine but need careful handling to avoid lumps.
Consider these real shop-floor examples:
● A sanitaryware factory shifted from coarse to medium grade to cut pinholes in glossy surfaces.
● An aerospace parts foundry switched to fine grain for better mold detail but had to upgrade its vacuum system to handle tighter packing.
Bigger grains usually mean higher permeability. Finer grains mean higher surface area — so more binder or water may be needed.
Application | Preferred Grain Size |
---|---|
Foundry molds | Coarse |
Floor tiles | Medium |
Glossy glazes | Fine |
Match your grain size to the end-product demands for smoother production and fewer rejects.
What Factors Influence Zircon Sand Grain Size?
You might wonder: why do two mines produce sand with different grain sizes? Nature sets the baseline — each deposit forms under different temperature and pressure. Some regions produce naturally coarse zircon, others yield fine grains needing minimal grinding.
Processing also matters. After mining, raw sand goes through washing, magnetic separation, and sometimes milling. Each stage tweaks the final size. Aggressive milling can break grains too much, creating dust that hurts performance.
Transport and storage can affect size, too. Poor handling lumps fine sand or mixes grades.
Stage | Impact on Grain Size |
---|---|
Mining site | Natural formation defines initial size |
Washing & separation | Removes unwanted minerals |
Milling | Adjusts grain to target range |
Packing & transport | Risk of clumping or segregation |
Always confirm processing steps with your supplier to check they follow strict quality controls.
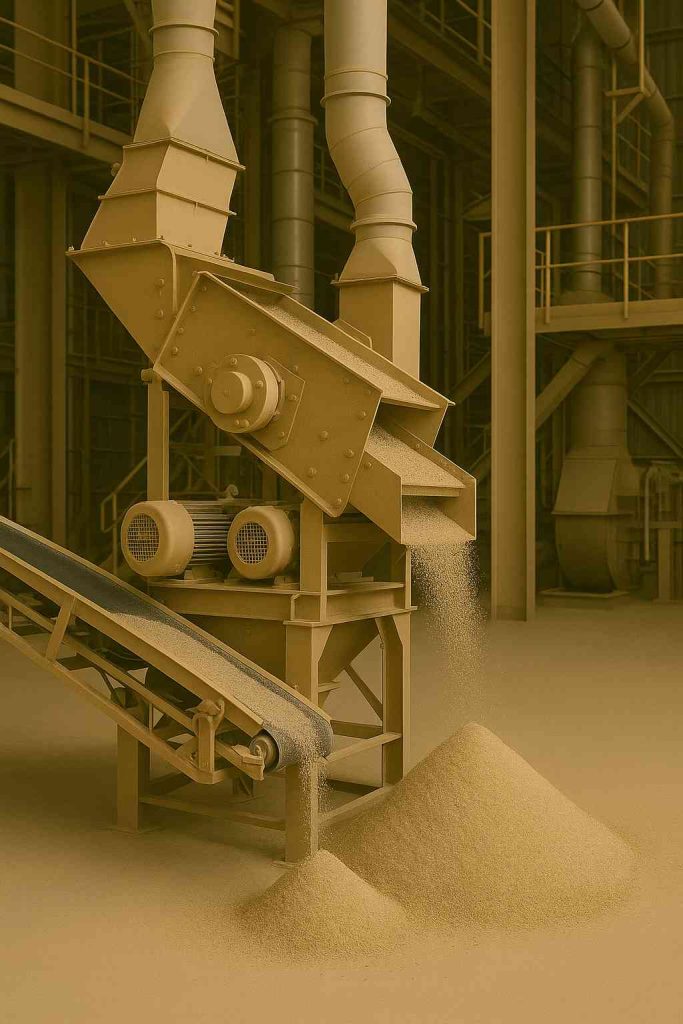
This image shows machinery at a zircon sand plant separating and refining grains for commercial use.
How Do Suppliers Guarantee Consistent Grain Size?
Let’s face it: no buyer wants surprises in a shipment. Reliable suppliers use strict quality control (QC) to guarantee consistent grains. QC teams test samples from each production lot, check them against the lab standard, and adjust processes if needed.
Big exporters often hold certifications like ISO 9001. This shows they follow repeatable processes and maintain detailed records.
For extra safety, buyers should:
● Ask for batch-wise test reports
● Check for third-party lab certificates
● Verify if the supplier uses automatic screening machines
QC Practice | Buyer Benefit |
---|---|
Batch sampling | Reduces risk of bad batches |
Lab certification | Confirms accuracy |
Automated screening | Higher consistency |
Stick with certified suppliers for smoother procurement and fewer production headaches.
How Should Buyers Choose the Right Grain Size?
Here’s what smart buyers do: pick grain size based on what your factory really needs. Over-specifying wastes money; under-specifying risks rejects.
For example:
● Casting foundries needing strong molds favor coarser sand.
● Ceramic tile plants want medium grains for slip flow and surface smoothness.
● High-end porcelain glazes need ultra-fine grains for a glossy, scratch-free finish.
Discuss with your production team first. Then share clear specs with your supplier. It helps to request a small sample batch for trials.
Factory Type | Best Grain Size |
---|---|
Metal casting | Coarse |
General ceramics | Medium |
Porcelain glazing | Fine |
Align grain size with product goals to balance cost and quality.
What Are Common Grain Size Ranges in the Market?
Here’s a quick look: different regions offer slightly different grades. Australian zircon sands usually come medium to coarse. African deposits often run finer but need extra cleaning. Some Asian suppliers provide custom-milled grades tailored to unique specs.
Buyers often see ranges like:
● Coarse: 100–150 microns
● Medium: 50–100 microns
● Fine: below 50 microns
Most vendor datasheets list D50 values plus a full PSD chart.
Region | Typical Grain Size |
---|---|
Australia | Medium to coarse |
Africa | Fine to medium |
Asia | Custom milled |
Check these charts to compare global options when planning bulk orders.
How to Handle Grain Size Variations in Production?
Here’s what can happen: even trusted suppliers might ship slightly off-grade sand sometimes. Good plants have ways to handle this without costly downtime.
Common fixes include:
● Blending: mix batches with different sizes to meet target specs.
● Adjusting process settings: tweak water content or binder ratios.
● Filtration: use fine screens to catch lumps before use.
Some large factories hold backup stock of finer or coarser sand for quick adjustments.
Fix | When to Use |
---|---|
Blending | Minor grain mismatch |
Process tweaks | Small flow or mix changes |
Filtration | Lump removal |
Train your team on these quick fixes to keep production stable.
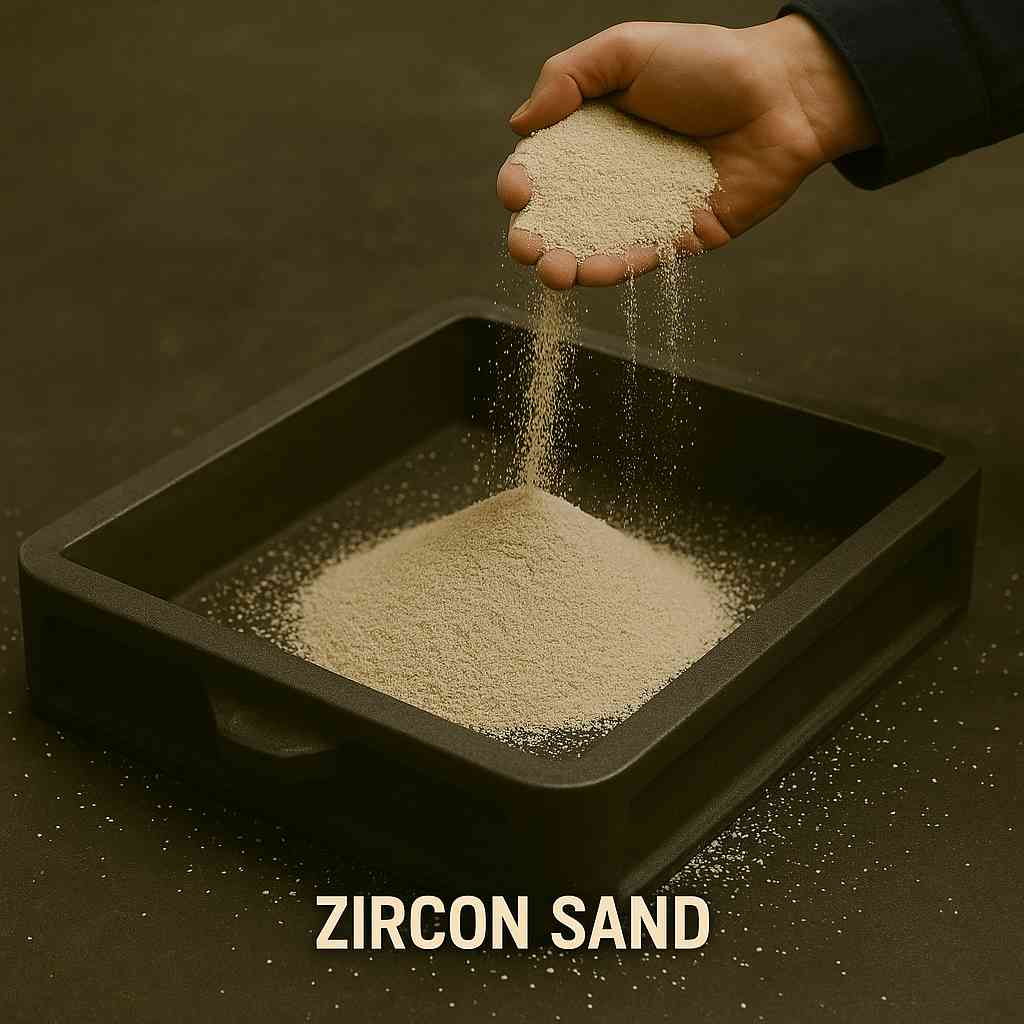
This image shows zircon sand being poured into a foundry mold, highlighting its use in metal casting.
Where Can Buyers Get Reliable Zircon Sand?
Let’s wrap this up: picking a trusted source saves endless headaches. Look for suppliers with proven track records, robust testing, and clear documents. Global exporters from Australia, South Africa, and Indonesia dominate this field.
Before signing a long-term deal, always:
● Request product samples
● Demand batch-wise lab reports
● Inspect storage and packing standards
Many top buyers sign supply agreements that include penalty clauses for bad batches. This protects your operation.
Supplier Tip | Why It Matters |
---|---|
Sample first | Avoids surprises |
Lab report | Confirms specs |
Contract terms | Protects buyer |
Conclusion
Choose reliable partners to secure smooth production year-round.
Picking the right grain size keeps production smooth, cuts waste, and ensures top product quality. Buyers who check specs, verify labs, and demand steady QC rarely face nasty surprises. For solid technical help or bulk orders, contact Global Industry today. We deliver proven zircon sand grades with lab certificates to match. Talk to our team now and keep your production line running clean and stable.
FAQ Section
Q1: What size range is best for ceramic tiles?
For ceramic tiles, most plants choose medium to fine zircon sand. This keeps slip flow stable and makes glazing smoother. Fine grains help create a bright, even finish without pinholes or rough spots. Always test a small batch to confirm your glaze formula works well with the sand grade.
Q2: How do I test zircon sand grain size myself?
Use a set of certified lab sieves if you have grains larger than 50 microns. For finer powders, send a sample to a trusted lab with laser particle size equipment. Many suppliers offer lab test services and provide a full particle size distribution report so you can cross-check each shipment.
Q3: Can different batches vary in grain size?
Yes, slight variations can happen between mining lots or after storage. Reliable suppliers reduce this risk by sampling each production batch, using automatic sieves, and adjusting milling as needed. Always request batch-specific lab results to confirm the sand stays within your required range.
Q4: Does finer zircon sand cost more?
Generally, yes. Producing finer grades needs extra milling and careful screening to remove dust and keep grains uniform. This adds labor and machine costs. However, paying a bit more for the right grain size often saves money later by reducing defects or rework in glazing and casting.
Q5: What paperwork should suppliers provide?
Ask for a detailed Certificate of Analysis (COA) with every shipment. This should include the grain size distribution, chemical purity, moisture content, and any test results done by third-party labs. A good supplier will also share process flow charts or quality certifications to show their production standards meet industry norms.