Chemical composition specifications determine the performance, quality, and suitability of zircon powder across industrial applications. Procurement professionals face the challenge of selecting zircon powder materials that meet stringent technical requirements while managing costs and ensuring consistent supply. Understanding chemical specifications enables informed purchasing decisions. This comprehensive analysis examines the critical chemical parameters that define premium zircon powder, providing practical guidance for evaluating zircon powder suppliers, interpreting certificates of analysis, and selecting zircon powder grades that optimize performance in demanding applications. Leading manufacturers rely on precise chemical control to deliver consistent zircon powder quality that meets the most demanding industrial standards.
What Primary Chemical Components Determine Zircon Quality?
Zirconium dioxide content represents the most critical specification in premium zircon powder, directly influencing thermal properties, chemical resistance, and overall performance. High ZrO₂ content drives superior performance. Premium grades typically contain 65-67% zirconium dioxide, with the highest quality materials reaching 66-67%. This high concentration provides exceptional refractoriness, enabling applications in extreme temperature environments where conventional materials fail.
Silicon dioxide levels complement zirconium dioxide content, typically ranging from 32-34% in premium grades. The ZrO₂ to SiO₂ ratio affects thermal expansion characteristics, chemical stability, and processing behavior. Materials with optimal ratios demonstrate superior dimensional stability during thermal cycling and reduced interaction with molten metals in foundry applications.
Hafnium oxide presence, while naturally occurring in zircon, requires careful monitoring for nuclear applications. Premium grades maintain hafnium content below 2%, with nuclear-grade materials requiring even stricter limits. The hafnium content affects neutron absorption properties and must be controlled for reactor applications where neutron transparency is required.
Component | Premium Grade (%) | Standard Grade (%) | Nuclear Grade (%) |
---|---|---|---|
ZrO₂ | 65-67 | 63-65 | 65-67 |
SiO₂ | 32-34 | 33-35 | 32-34 |
HfO₂ | <2.0 | <2.5 | <0.5 |
Fe₂O₃ | <0.1 | <0.15 | <0.05 |
TiO₂ | <0.2 | <0.3 | <0.1 |
Iron oxide content significantly impacts color, magnetic properties, and surface quality in casting applications. Premium grades maintain iron levels below 0.1%, preventing discoloration and magnetic contamination that can affect processing equipment. Low iron content becomes particularly important in investment casting where surface finish quality directly impacts final component performance.
Titanium dioxide levels influence opacity and thermal behavior, with premium grades limiting TiO₂ content to below 0.2%. Excessive titanium can affect sintering characteristics in ceramic applications and alter thermal expansion properties. Controlled titanium content ensures predictable processing behavior and consistent material properties across production batches.
How Do Trace Element Limits Affect Performance?
Radioactive element content requires strict control for safety compliance and application suitability. Radiation limits ensure safe handling and use. Natural zircon contains uranium and thorium, typically totaling 50-500 ppm in standard grades. Premium materials maintain combined radioactive content below 200 ppm, with some applications requiring even lower levels for export compliance and workplace safety.
Heavy metal impurities affect chemical purity and can introduce contamination in sensitive applications. Lead content must remain below 10 ppm in premium grades, while cadmium levels require control below 5 ppm. These limits become critical in applications where material purity affects final product performance or regulatory compliance.
Alkali metal content influences processing behavior and thermal properties. Sodium and potassium levels typically remain below 0.1% combined in premium grades. Excessive alkali content can cause flux action during high-temperature processing, leading to dimensional instability and altered sintering behavior in ceramic applications.
Trace Element | Premium Limit | Standard Limit | Detection Method |
---|---|---|---|
U + Th | <200 ppm | <500 ppm | Gamma spectroscopy |
Pb | <10 ppm | <20 ppm | ICP-MS |
Cd | <5 ppm | <10 ppm | ICP-MS |
Na₂O + K₂O | <0.1% | <0.2% | XRF/ICP |
P₂O₅ | <0.05% | <0.1% | XRF |
Rare earth element presence can affect material properties and processing characteristics. Cerium, lanthanum, and yttrium content typically remains below 100 ppm combined in premium grades. While these elements occur naturally in zircon deposits, excessive levels can alter thermal expansion and chemical resistance properties.
Phosphorus content requires control below 0.05% in premium applications due to its effect on high-temperature stability. Phosphorus can form low-melting compounds that compromise refractory performance and create processing difficulties in demanding thermal environments.
Sulfur content limitations prevent corrosion issues and maintain chemical stability. Premium grades maintain sulfur below 0.02%, preventing the formation of sulfide compounds that can cause material degradation and affect performance in oxidizing environments.
Which Analytical Methods Verify Chemical Specifications?
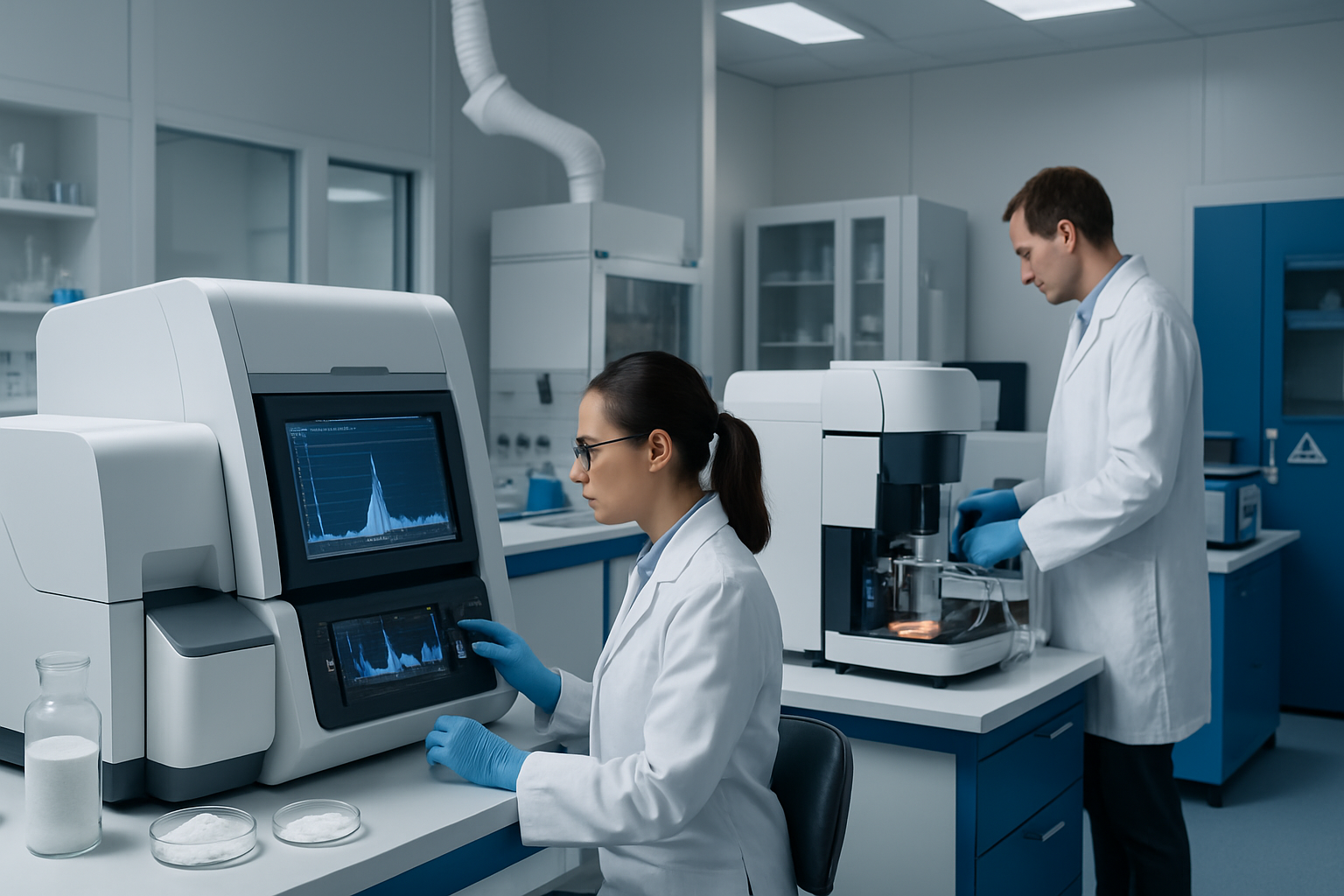
X-ray fluorescence spectroscopy provides rapid, accurate analysis of major elements in zircon powder. XRF delivers reliable composition data quickly. Modern XRF systems achieve ±0.2% accuracy for major components like ZrO₂ and SiO₂, making them ideal for quality control and incoming zircon powder verification. The non-destructive nature of XRF analysis allows testing without sample consumption, enabling complete zircon powder batch verification.
Inductively coupled plasma analysis offers superior precision for trace element determination. ICP-OES and ICP-MS techniques provide detection limits in the ppm range, essential for verifying radioactive element content and heavy metal impurities. These methods require sample dissolution but deliver unmatched accuracy for elements requiring strict control.
Wet chemical analysis methods remain important for specific determinations and referee analysis. Classical gravimetric and volumetric techniques provide absolute accuracy for major components and serve as calibration standards for instrumental methods. These methods require skilled technicians but offer independence from instrumental drift and matrix effects.
Analysis Method | Elements Covered | Accuracy | Analysis Time |
---|---|---|---|
XRF | Major elements | ±0.2-0.5% | 5-10 minutes |
ICP-OES | Trace elements | ±5-10% | 30-60 minutes |
ICP-MS | Ultra-trace | ±10-20% | 45-90 minutes |
Wet Chemistry | Major elements | ±0.1-0.2% | 2-4 hours |
Gamma Spec | Radioactive | ±15-25% | 4-24 hours |
Mass spectrometry techniques enable precise isotopic analysis for specialized applications. Thermal ionization mass spectrometry (TIMS) and secondary ion mass spectrometry (SIMS) provide isotopic ratios required for nuclear applications and research purposes. These advanced techniques require specialized equipment and expertise but deliver unmatched precision for critical applications.
Quality control sampling protocols ensure representative analysis results. Proper sampling techniques, including increment collection, sample reduction, and homogenization, prevent bias and ensure analytical results reflect bulk material composition. Statistical sampling plans based on lot size and variability requirements guide sampling frequency and locations.
Certification and documentation requirements vary by application and customer specifications. Certificates of analysis must include analytical methods, detection limits, and uncertainty estimates. Traceability to certified reference materials ensures accuracy, while chain of custody documentation maintains sample integrity throughout the analytical process.
What Industry Standards Govern Chemical Composition?
ASTM standards provide comprehensive specifications for zircon powder chemical composition across multiple applications. Industry standards ensure consistent quality expectations. ASTM C545 covers zircon refractories, specifying chemical requirements for different service conditions. ASTM C577 addresses zircon for investment casting, with specific limits for elements affecting casting quality and surface finish.
ISO requirements establish international standards for chemical analysis and reporting. ISO 12677 specifies methods for chemical analysis of zircon-containing refractories, while ISO 17892 covers sampling and testing procedures. These standards ensure global consistency in testing methods and result interpretation.
Industry-specific standards address unique application requirements. The foundry industry follows AFS (American Foundry Society) guidelines for casting sand specifications, including chemical purity requirements. The ceramics industry relies on standards from organizations like the American Ceramic Society for technical ceramics applications.
Standard | Application | Key Requirements |
---|---|---|
ASTM C545 | Refractories | ZrO₂ >65%, Fe₂O₃ <0.15% |
ASTM C577 | Investment casting | ZrO₂ >66%, Fe₂O₃ <0.1% |
ISO 12677 | Analysis methods | Precision requirements |
AFS 5094 | Foundry sand | Acid demand <5 mL |
JIS R2001 | Japanese ceramics | Specific purity grades |
Regional regulatory requirements affect chemical specifications for international trade. European REACH regulations require registration and safety data for chemical substances, including detailed composition information. US EPA regulations govern radioactive material content and handling requirements for materials containing natural radioactivity.
Customer-specific chemical specifications often exceed standard requirements for critical applications. Aerospace and nuclear customers frequently specify tighter limits on trace elements and require additional testing for elements not covered in standard specifications. These custom requirements reflect the demanding performance requirements of advanced applications.
International trade and quality certification standards facilitate global commerce in zircon powder. ISO 9001 quality management systems ensure consistent production and testing procedures, while ISO 14001 environmental management addresses sustainability concerns. Third-party certification bodies verify compliance with international standards and customer requirements.
How Does Chemical Composition Impact Applications?
Refractory performance depends directly on chemical composition, particularly ZrO₂ content and impurity levels. Chemical purity determines thermal performance limits. High zirconium dioxide content provides superior refractoriness, enabling service temperatures above 1800°C in demanding applications. Low iron content prevents flux formation that can compromise refractory integrity at high temperatures.
Ceramic applications require precise chemical control for predictable sintering behavior and dimensional stability. Alkali content affects sintering temperature and shrinkage characteristics, while iron content influences color development and magnetic properties. Consistent zircon powder chemical composition ensures reproducible processing conditions and uniform product quality.
Foundry casting quality correlates strongly with zircon powder chemical purity, particularly iron and alkali content. Low iron levels prevent metal penetration and improve surface finish quality in precision casting applications. Controlled alkali content maintains dimensional stability during thermal cycling and prevents mold degradation during metal pouring.
Application | Critical Parameters | Performance Impact |
---|---|---|
Steel refractories | ZrO₂ >66%, Fe₂O₃ <0.1% | Corrosion resistance |
Investment casting | Fe₂O₃ <0.05%, alkalis <0.05% | Surface finish |
Technical ceramics | Consistent composition | Dimensional control |
Nuclear applications | U+Th <100 ppm | Radiation safety |
Glass furnaces | Al₂O₃ <0.5% | Contamination control |
Nuclear industry requirements focus on radioactive element content and neutron absorption properties. Uranium and thorium limits ensure radiation safety during handling and processing, while hafnium content affects neutron transparency in reactor applications. These specifications require specialized analytical capabilities and strict documentation procedures.
Investment casting precision depends on thermal expansion matching and chemical inertness. Low thermal expansion coefficients, achieved through optimal chemical composition, prevent dimensional distortion during casting cycles. Chemical inertness prevents reaction with molten metals, maintaining mold integrity and surface quality.
Specialty applications often require custom chemical specifications tailored to specific performance requirements. Electronic ceramics demand ultra-low alkali content to prevent electrical conductivity, while optical applications require minimal iron content to maintain transparency. These specialized requirements drive premium pricing and specialized production techniques.
What Quality Control Measures Ensure Consistency?
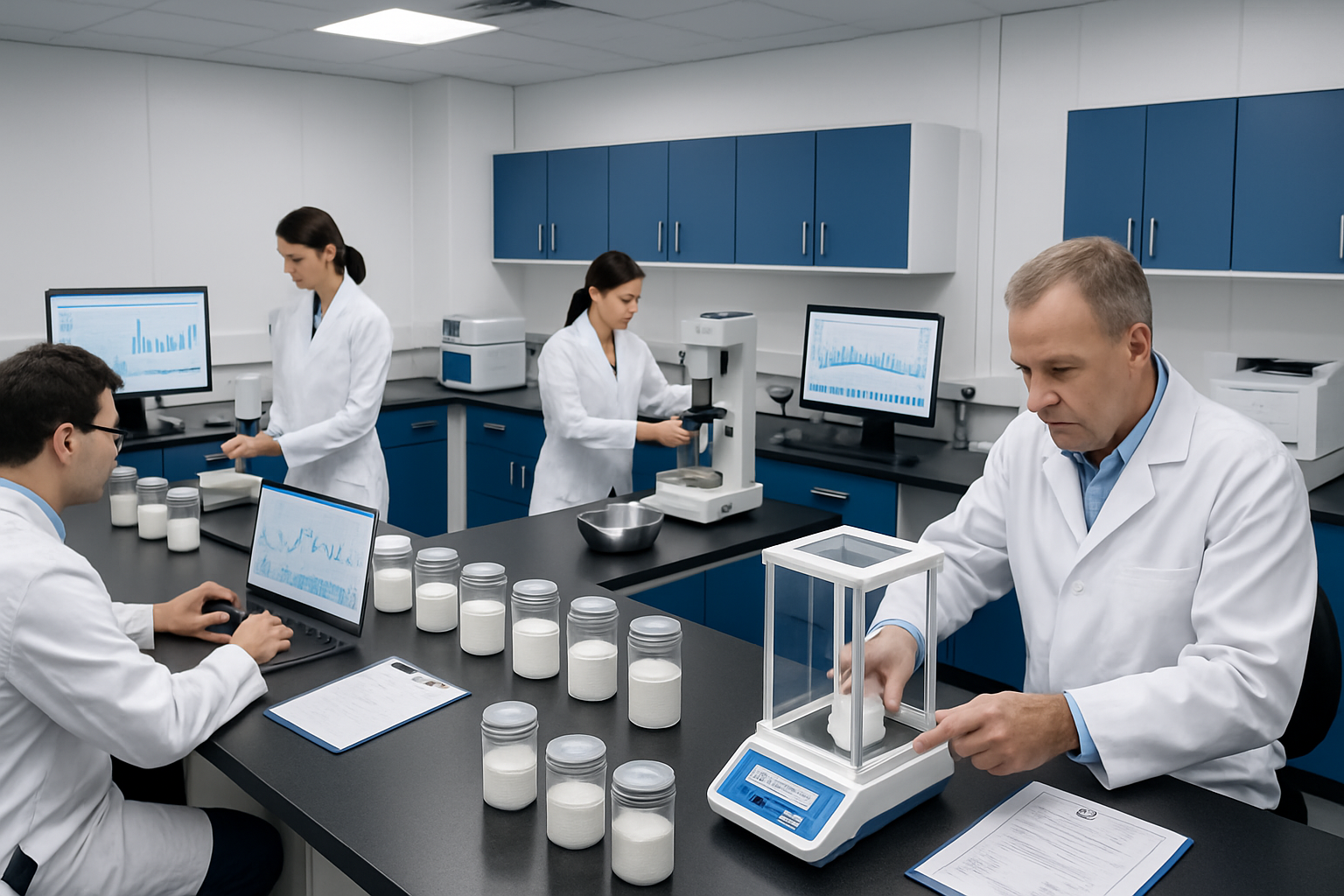
Batch testing protocols establish systematic verification of chemical composition for every zircon powder production lot. Consistent testing prevents quality variations. Statistical sampling plans determine sample size and frequency based on lot size and historical variability data. Multiple samples from different locations within each zircon powder batch ensure representative analysis and detect potential segregation issues.
Statistical process control monitors chemical composition trends and identifies process variations before they affect product quality. Control charts track key parameters like ZrO₂ content and iron levels, triggering investigations when values approach specification limits. Process capability studies quantify the ability to meet customer requirements consistently.
Supplier qualification and audit requirements ensure upstream quality control throughout the supply chain. Raw material suppliers must demonstrate analytical capabilities, quality systems, and traceability procedures. Regular audits verify continued compliance with quality requirements and identify opportunities for improvement.
Quality Control Element | Frequency | Acceptance Criteria |
---|---|---|
Batch analysis | Every lot | Within specification |
Process monitoring | Continuous | Cpk >1.33 |
Supplier audits | Annual | ISO 9001 compliance |
Method validation | Annual | Precision <5% RSD |
Reference standards | Monthly | Certified values ±2% |
Incoming material inspection and verification procedures prevent non-conforming material from entering production. Independent analysis of supplier certificates validates analytical results and identifies potential discrepancies. Quarantine procedures hold material until verification is complete, preventing quality issues in downstream processing.
Certificate of analysis documentation standards ensure complete traceability and regulatory compliance. Certificates must include analytical methods, detection limits, uncertainty estimates, and analyst identification. Electronic data management systems maintain records and enable rapid retrieval for customer inquiries and regulatory inspections.
Traceability and quality assurance systems connect chemical composition data with production records and customer shipments. Lot tracking systems enable rapid identification of affected material in case of quality issues. Quality management systems ensure consistent procedures and continuous improvement in analytical capabilities and quality control processes.
What Cost Factors Relate to Chemical Specifications?
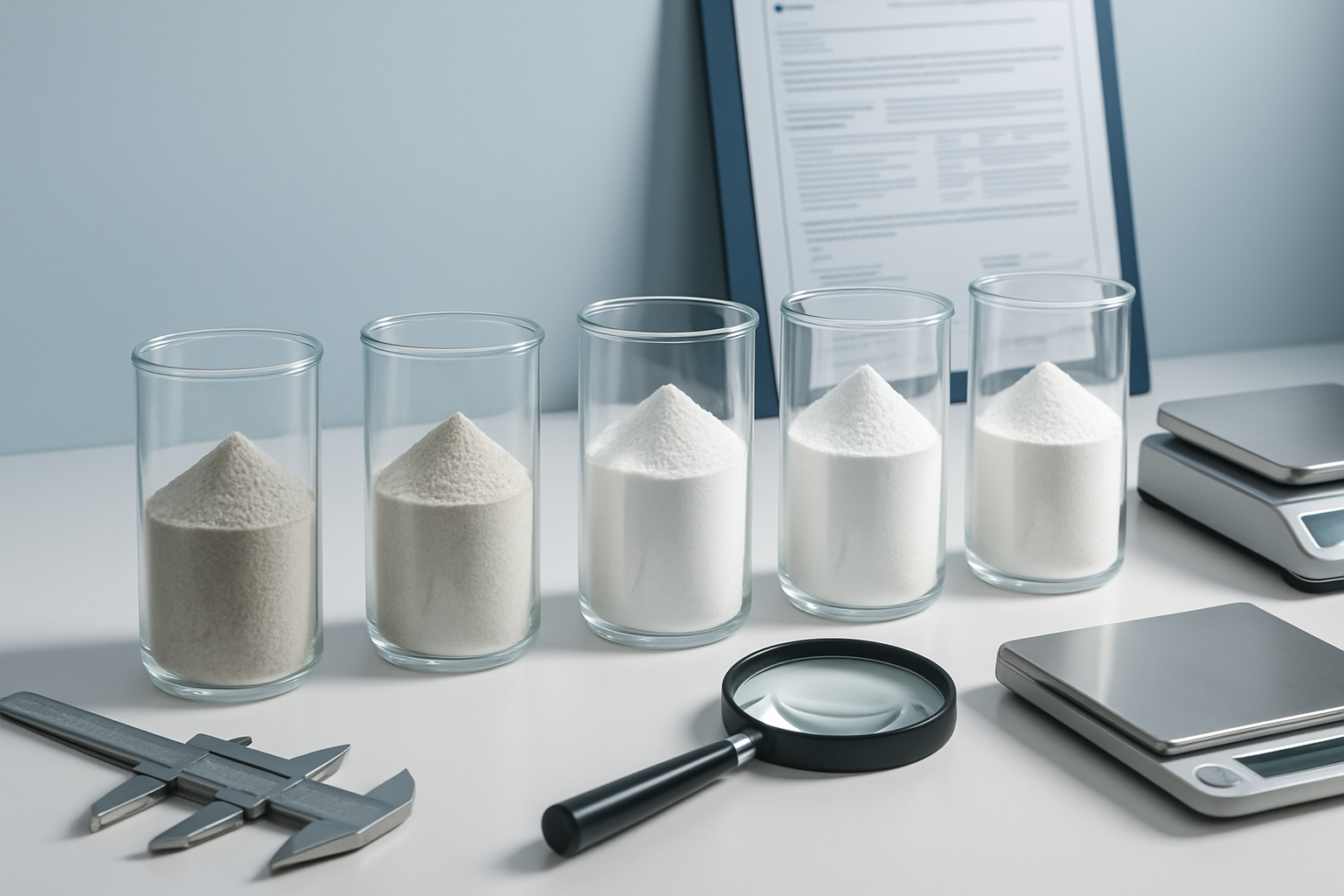
Premium pricing for high-purity grades reflects the additional processing and quality control required to achieve superior chemical specifications. Higher purity commands premium pricing. Ultra-low iron grades can cost 20-30% more than standard materials due to specialized beneficiation techniques and additional quality control testing. Nuclear-grade materials with strict radioactive element limits command even higher premiums due to limited supply sources and extensive documentation requirements.
Testing and analysis costs represent a significant component of quality control expenses. Comprehensive chemical analysis including trace elements and radioactive content can cost $200-500 per sample. High-frequency testing for critical applications increases these costs but provides essential quality assurance for demanding applications.
Specification tolerance effects on pricing reflect the difficulty of achieving tight compositional control. Materials with ±0.1% tolerance on major elements cost more than those with ±0.5% tolerance due to increased rejection rates and additional processing steps. Customers must balance specification requirements with cost considerations based on application criticality.
Grade Category | Price Premium | Key Specifications |
---|---|---|
Standard | Baseline | ZrO₂ 63-65%, Fe₂O₃ <0.15% |
Premium | +15-25% | ZrO₂ 65-67%, Fe₂O₃ <0.1% |
Ultra-pure | +25-40% | ZrO₂ >66%, Fe₂O₃ <0.05% |
Nuclear | +50-100% | U+Th <100 ppm |
Custom | Variable | Customer-specific limits |
Supply chain considerations for premium grades include limited source availability and longer lead times. High-purity zircon deposits are geographically concentrated, creating supply chain risks and price volatility. Long-term supply agreements help manage these risks but may require volume commitments and price premiums.
Long-term cost benefits of consistent quality include reduced processing costs, improved yield, and enhanced product performance. Premium materials with tight compositional control reduce variability in downstream processing, leading to higher yields and lower rejection rates. Improved performance in end applications can justify higher material costs through extended service life and reduced maintenance requirements.
Total cost of ownership analysis considers material cost, processing efficiency, and performance benefits. While premium grades cost more initially, their superior performance can reduce total costs through improved processing yields, extended service life, and reduced maintenance requirements. This analysis helps justify premium material selection for critical applications where performance outweighs initial cost considerations.
Conclusion
Chemical composition specifications define the quality, performance, and suitability of zircon powder across demanding industrial applications. Understanding these parameters enables procurement professionals to make informed decisions that balance performance requirements with cost considerations. Premium zircon powder grades with superior chemical purity deliver enhanced performance in critical applications, justifying their higher costs through improved processing efficiency and extended service life. Global Industry’s technical expertise and quality control capabilities ensure consistent delivery of zircon powder materials that meet the most stringent chemical specifications, supporting customer success in demanding applications.
FAQ Section
Q1: What is the typical ZrO₂ content in premium zircon powder?
Premium zircon powder typically contains 65-67% ZrO₂ content, with the highest grades reaching 66-67%. This high zirconium dioxide content directly correlates with superior refractory properties, thermal stability, and performance in demanding applications such as investment casting and high-temperature ceramics.
Q2: How do radioactive element limits affect zircon powder selection?
Natural zircon contains trace amounts of uranium and thorium, typically 50-500 ppm combined. Premium grades maintain lower levels (under 200 ppm) to meet safety regulations and customer requirements. These limits are particularly important for nuclear applications and export compliance with international radiation safety standards.
Q3: Which trace elements most significantly impact zircon powder performance?
Iron oxide content (typically <0.1% in premium grades) most significantly affects color and magnetic properties. Titanium dioxide levels (<0.2%) influence opacity and thermal behavior. Alkali metal content affects sintering behavior and must be controlled for consistent processing characteristics in ceramic and refractory applications.
Q4: What analytical accuracy is required for chemical composition testing?
Major elements (ZrO₂, SiO₂) require ±0.5% accuracy, while trace elements need ±10-20% relative accuracy depending on concentration levels. Premium applications often demand tighter tolerances, with some specifications requiring ±0.2% accuracy for major components and certified reference materials for calibration.
Q5: How do chemical specifications vary between different zircon powder applications?
Foundry applications prioritize low iron content (<0.05%) for surface quality, while refractory applications focus on high ZrO₂ content (>66%) for thermal performance. Nuclear applications require strict radioactive element limits, and ceramic applications emphasize consistent alkali metal content for predictable sintering behavior and dimensional control.