Zircon sand has become a dependable choice for industrial casting applications, especially in foundries and refractory environments. But many purchasing managers still wonder what sets it apart from other materials in real-world usage. This article addresses that concern by showing exactly how zircon sand supports efficient, high-quality performance in tough industrial settings. It explains why technical professionals consistently rely on zircon for thermal stability, purity, and casting accuracy. If you’re sourcing for manufacturing, procurement, or engineering roles, this guide will clarify why zircon sand remains a smart, technically sound option. Global Industry’s long-standing track record with refractory materials adds credibility to the insights shared below.
Why do foundries rely on zircon sand?
Foundries need consistency. Molten metals behave unpredictably, and surface defects can turn a quality casting into scrap. Here’s where zircon sand earns its value.
Zircon sand brings thermal stability. It holds up well against the extreme heat that casting environments throw at it. Melting points over 2,200°C make it ideal for both ferrous and non-ferrous metal casting. This means fewer thermal failures, fewer mold defects, and a lower rejection rate.
Casting defects often result from materials expanding under heat. Zircon has very low thermal expansion. That helps maintain dimensional accuracy in molds and cores. It supports high-tolerance parts that don’t require excessive post-processing.
It also bonds well with binders, especially in resin-coated sand systems. This makes it easier to work with and improves surface finishes on final castings.
Finally, its chemical inertness means zircon resists reaction with molten metals. This limits penetration and sand fusion — common issues in silica-based mold systems.
Here’s a quick breakdown:
Property | Impact on Foundry Use |
---|---|
High melting point | Withstands heat without breaking down |
Low thermal expansion | Maintains mold shape, fewer casting flaws |
Chemical inertness | Reduces metal-mold reactions |
Good binder adhesion | Supports stronger, smoother molds |
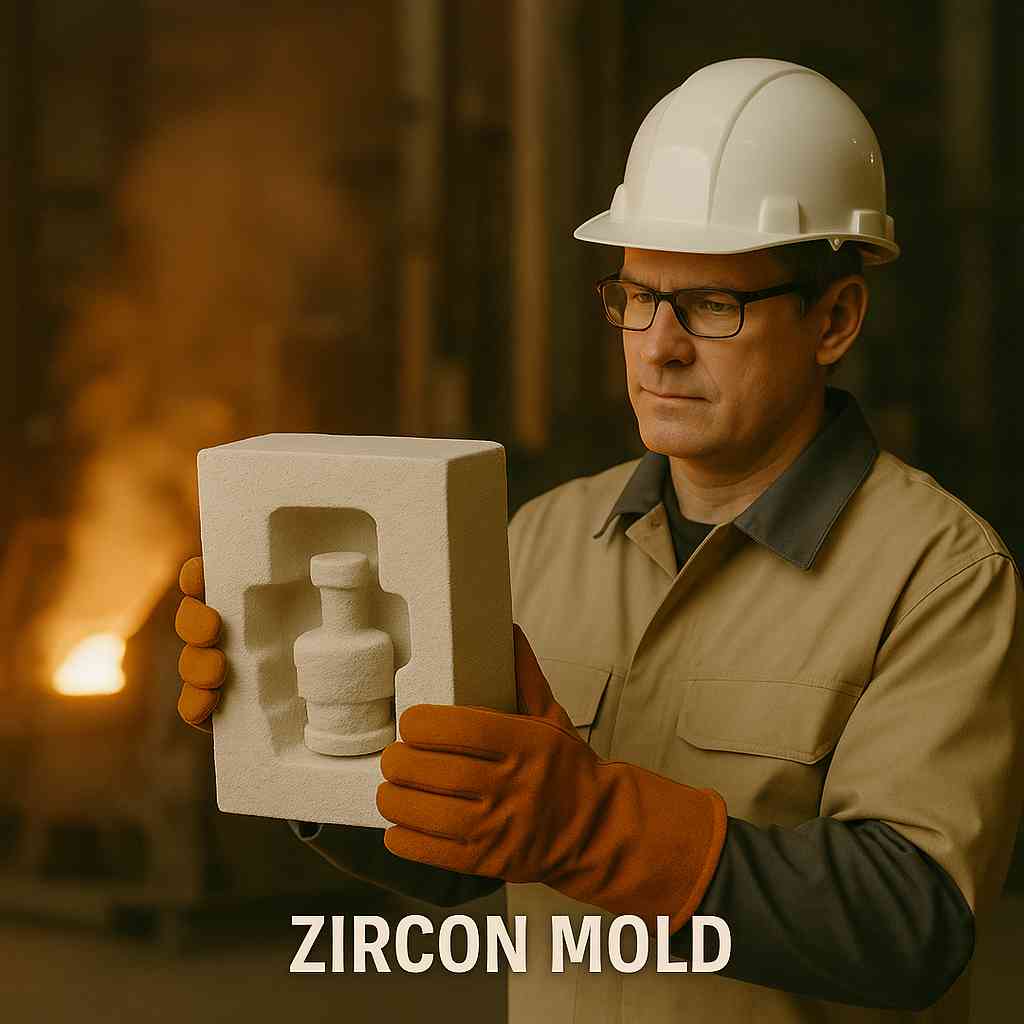
This image shows a technician checking casting molds formed using zircon, illustrating its practical use in real facilities.
What makes zircon suitable for refractory bricks?
Refractories face similar challenges. High temperatures, corrosive slag, and mechanical wear define kiln and furnace environments. So why do engineers pick zircon for bricks and linings?
Zircon-based bricks offer excellent resistance to acidic and basic slags. In metallurgy and glass melting, slag corrosion can damage standard alumina or silica-based refractories. But zircon holds up well, keeping the lining structure intact longer.
Heat cycling — rapid changes between high and low temperatures — causes many materials to crack. Zircon handles thermal shock better than many alternatives. That translates to longer life cycles and lower maintenance costs.
Zircon’s density also works in its favor. The higher the bulk density, the less porous the brick, which helps in applications requiring gas-tight or liquid-tight linings.
Its stability under stress gives engineers the confidence to specify zircon linings in high-performance or continuous-run operations.
Refractory Advantage | Benefit in Application |
---|---|
Slag resistance | Longevity in smelting, metallurgy |
Thermal shock resistance | Reduced cracking, better safety |
Structural integrity | Withstands mechanical loads |
Low porosity | Better containment, less seepage |
How does zircon sand compare with other materials?
Zircon isn’t the only sand used in casting. Chromite, olivine, and silica all compete for market share. But not all sands perform equally in foundry environments.
Silica is cheap and abundant, but it suffers from high thermal expansion. That causes cracking in molds and dimensional distortion in castings. Chromite has better heat resistance, yet it’s heavier and less chemically stable under certain conditions.
Olivine offers a middle ground but lacks the purity and consistency zircon delivers. In high-precision applications, zircon’s performance still outweighs its cost.
When weighing procurement decisions, it’s not just about price per ton. You need to account for rework costs, mold reliability, and quality control headaches.
Let’s compare side-by-side:
Material | Melting Point | Expansion Rate | Chemical Stability | Cost | Reusability |
---|---|---|---|---|---|
Zircon | ~2,200°C | Very Low | High | Medium-High | High |
Silica | ~1,700°C | High | Low | Low | Low |
Chromite | ~2,000°C | Medium | Medium | Medium | Medium |
Olivine | ~1,800°C | Low | Medium | Low-Medium | Low |
Bottom line? Zircon reduces defect rates, improves part consistency, and extends tool life — benefits that can far outweigh upfront material costs.
What are the technical properties of zircon sand?
Technical buyers often ask for specs before making a decision. Let’s break down the core characteristics that define zircon’s industrial value.
Grain size matters in mold performance. Zircon sand typically has a subangular grain structure. This supports tight packing in molds and better flow of molten metal around details.
Chemical purity is another key factor. High-quality zircon has over 66% ZrO₂ + SiO₂ and minimal contaminants like iron or titanium. That purity translates into better resistance under heat and pressure.
Thermal conductivity is moderate, which helps control solidification rates in casting. Refractoriness, or the temperature at which the material begins to soften, exceeds 1,800°C — often outperforming alumina-based materials.
Property | Typical Value |
---|---|
Grain shape | Subangular |
ZrSiO₄ content | >98% |
Refractoriness | >1,800°C |
Specific gravity | ~4.6 g/cm³ |
Bulk density | ~2.6 g/cm³ |
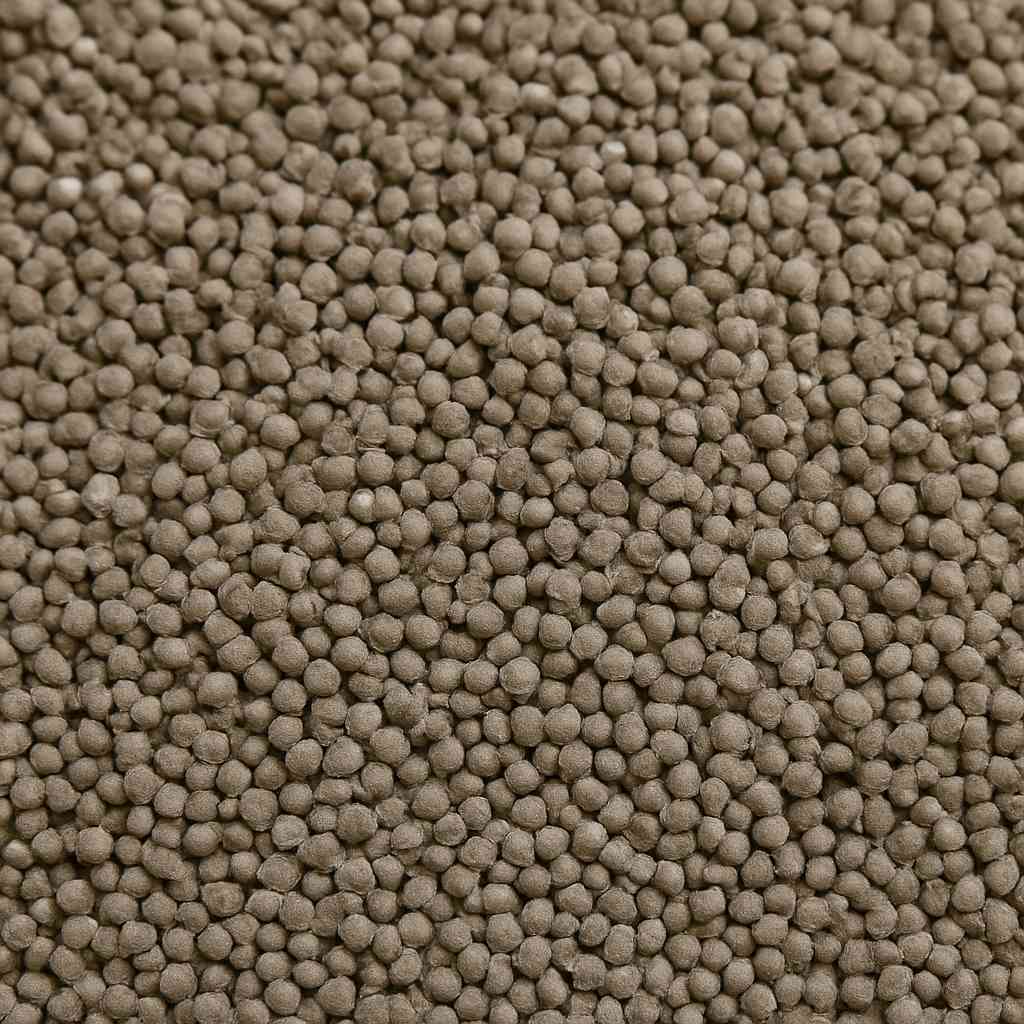
This image shows high-purity zircon grains, emphasizing uniform shape and clean composition for casting reliability.
Which industries benefit most from zircon applications?
Zircon isn’t limited to one segment. It’s used across several manufacturing and high-heat industries. Here’s a look at where it really matters.
Steel and iron foundries rely on zircon for core and mold creation, especially for critical engine components or heavy machine parts. The reduced risk of defects supports consistent production.
In the glass industry, zircon stabilizes refractories that contact molten glass. It prevents surface corrosion and product discoloration, maintaining optical clarity.
Ceramic manufacturing uses zircon in glazes and tile bodies. It helps control shrinkage and boosts surface durability.
Aerospace and petrochemical industries turn to zircon for high-precision castings and linings in pressure-sensitive systems.
Summary table by industry:
Industry | Use Case |
---|---|
Metal Casting | Engine blocks, structural parts |
Glass Production | Furnace linings, clarity protection |
Ceramics | Glazes, abrasion resistance |
Aerospace | Precision molds and coatings |
Petrochemical | Lining for reactors, thermal shields |
How does zircon affect casting surface quality?
Casting quality isn’t just about metal — the mold material plays a huge part. So how does zircon impact the end result?
Low expansion means tighter dimensional control. Patterns hold their shape, and metal flows more predictably. That’s good news for anyone producing aerospace or automotive parts where precision matters.
Zircon’s stability helps minimize veining and penetration defects. These flaws, often caused by sand movement or gas formation, are costly and time-consuming to repair.
Surface finish also benefits from the finer grain size of zircon. Castings come out smoother, often needing less grinding or machining.
And because zircon molds last longer, foundries spend less time on maintenance or mold remakes.
Performance metrics at a glance:
Defect Type | Impact with Zircon Sand |
---|---|
Veining | Drastically reduced |
Metal penetration | Greatly minimized |
Surface roughness | Smoother finish |
Dimensional error | Lower tolerance variance |
What handling and processing methods are used?
Working with zircon sand requires standard practices to get the most out of it. So, what’s involved in daily operations?
Sand preparation is key. Whether used as-is or resin-coated, consistent moisture and binder ratios help ensure mold performance.
Recycling plays a big role. Zircon can be reclaimed through thermal or mechanical systems. This reduces waste and helps control costs. Many facilities report 4-5 reuse cycles before breakdown.
Safety is also critical. While zircon is stable, it may contain trace radioactive elements. Good ventilation, dust collection, and PPE use are best practices.
Handling Area | Best Practice |
---|---|
Sand prep | Calibrated binder mix |
Reuse process | Thermal or mechanical reclamation |
Storage | Dry, well-ventilated bins |
Safety | PPE, dust controls |
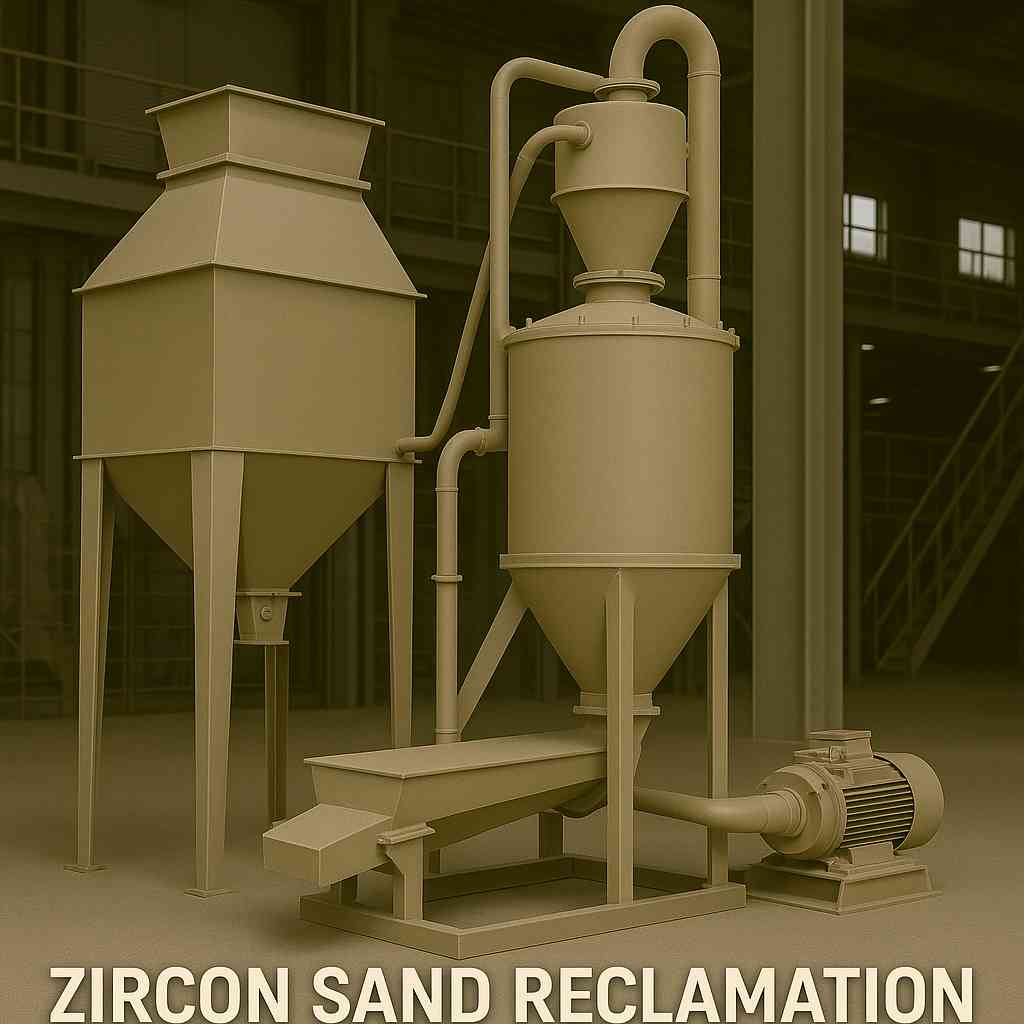
This image shows equipment used to recycle zircon sand in a foundry, supporting efficiency and material savings.
How do buyers evaluate zircon sand quality?
Procurement teams care about more than cost. Let’s look at what separates high-quality zircon from the rest.
Consistent particle size supports mold performance. Suppliers should provide certified grading data for each batch.
Purity levels — specifically the ZrSiO₄ content — directly affect thermal and chemical resistance. Anything below 98% may underperform.
International standards like ASTM or ISO guide these parameters. A supplier offering compliant products adds confidence to your buying decision.
Finally, documentation and support matter. Good suppliers don’t just ship — they help troubleshoot issues, test batches, and align specs with customer needs.
Key quality benchmarks:
Criterion | Why It Matters |
---|---|
Particle distribution | Mold packing consistency |
Chemical purity | Heat resistance, durability |
Supplier certification | Trust, repeatable quality |
Technical support | Issue resolution, alignment |
What market factors influence zircon sand availability?
Supply chains for zircon aren’t immune to global events. So what should buyers watch out for?
Top-producing countries include Australia, South Africa, and Mozambique. Political shifts, export regulations, and environmental reviews in these regions can slow supply.
Prices tend to fluctuate with demand from construction, ceramics, and tech sectors. Bulk buyers often use long-term contracts to hedge against volatility.
Sustainability efforts are also gaining momentum. Pressure to reduce environmental impact may shape how zircon is mined, processed, and shipped.
Market overview:
Factor | Influence on Supply |
---|---|
Geopolitical events | Risk of disruption |
Industry demand | Price volatility |
Regulation trends | Licensing, ESG shifts |
Transport logistics | Delivery delays |
Are there alternatives or enhancements to zircon?
Some applications can tolerate substitutes. But not all can match zircon’s balance of cost and performance. Here’s what buyers should consider.
Synthetic sands are being tested in R&D, but high cost and inconsistent results limit adoption in most industrial foundries.
Blended sands — mixing zircon with cheaper fillers — can work for non-critical parts. But the trade-offs include higher defect rates and lower reusability.
In coatings, some companies add additives to improve surface finish. These may help, but don’t fully replace zircon’s natural properties.
Ultimately, for precision work or thermal stress environments, zircon remains the preferred option — especially when reusability and surface quality are priorities.
Substitute Type | Use Case | Trade-Offs |
---|---|---|
Chromite, olivine | Low-cost applications | Reduced consistency |
Synthetic sand | R&D trials | Higher price, variable results |
Coated fillers | Surface finish tweaks | Limited improvement |
Conclusion
Zircon sand plays a practical role in industrial casting and refractory applications due to its stability, consistency, and purity. It supports defect reduction, improves part accuracy, and helps reduce waste through reuse. Global Industry provides consistent, industrial-grade zircon solutions that meet strict foundry and refractory needs. If you’re sourcing materials for high-performance environments, contact our technical team for sample data, sourcing support, or specifications tailored to your operation. Let’s work together to keep your casting line efficient and your products precise.
FAQ
Q1: What is zircon sand made of?
Zircon sand is primarily composed of zirconium silicate (ZrSiO₄), a naturally occurring mineral found in heavy mineral sand deposits. These deposits often contain a variety of minerals, including ilmenite and rutile, and are typically sourced from beach, river, or lake sediments. Zircon is highly valued not only for its zirconium content but also for its durability and resistance to thermal and chemical degradation.
Q2: Can zircon sand be reused in foundry applications?
Yes, zircon sand can be reclaimed and reused multiple times in foundry applications, provided that appropriate thermal or mechanical reclamation processes are applied. This not only reduces material costs but also minimizes waste, promoting a more environmentally sustainable practice. Effective reclamation can help maintain the quality of mold surfaces and casting precision, making zircon sand a preferred choice for many foundries.
Q3: What is the difference between foundry-grade and refractory-grade zircon?
Foundry-grade zircon is optimized for casting molds and is typically processed to enhance its flowability and adhesion properties, ensuring superior mold performance during casting. In contrast, refractory-grade zircon is specially processed to withstand extreme temperatures and harsh environments found in applications such as kiln linings and furnaces. This grade of zircon often showcases superior structural integrity and thermal stability, making it critical in various high-temperature industrial processes.
Q4: Does zircon sand pose any safety risks?
While zircon sand is generally stable and non-toxic, it may contain trace amounts of naturally occurring radioactive elements, such as uranium and thorium, depending on its geological source. Handling zircon sand requires implementing proper ventilation and safety measures to minimize exposure to any potential health risks. It’s advisable for workers to wear appropriate personal protective equipment (PPE) and to adhere to safety protocols to ensure a safe working environment.
Q5: How do I choose a reliable zircon supplier?
When selecting a zircon supplier, consider companies that have reputable ISO certifications, consistent quality records, and a history of reliability in product delivery. It’s important to evaluate potential suppliers based on their technical support offerings, responsiveness to customer inquiries, and transparency in sourcing practices. Additionally, seeking references or testimonials from current customers can provide insights into the supplier’s reliability and service quality. Being informed about industry standards can further aid in making a wise choice.