Manufacturing engineers and procurement specialists face mounting pressure to select materials that meet increasingly stringent performance requirements across multiple industries. Ultra-fine zircon powder has emerged as a specialized material that addresses these technical demands while providing reliable processing characteristics for high-performance applications. This advanced material offers unique properties that make it indispensable for electronics, aerospace, biomedical, and precision manufacturing sectors. Here’s what makes this material so valuable: Global Industry’s technical expertise and global supply network help manufacturers identify the right ultra-fine zircon powder specifications and optimize their material selection for superior performance and cost-effectiveness.
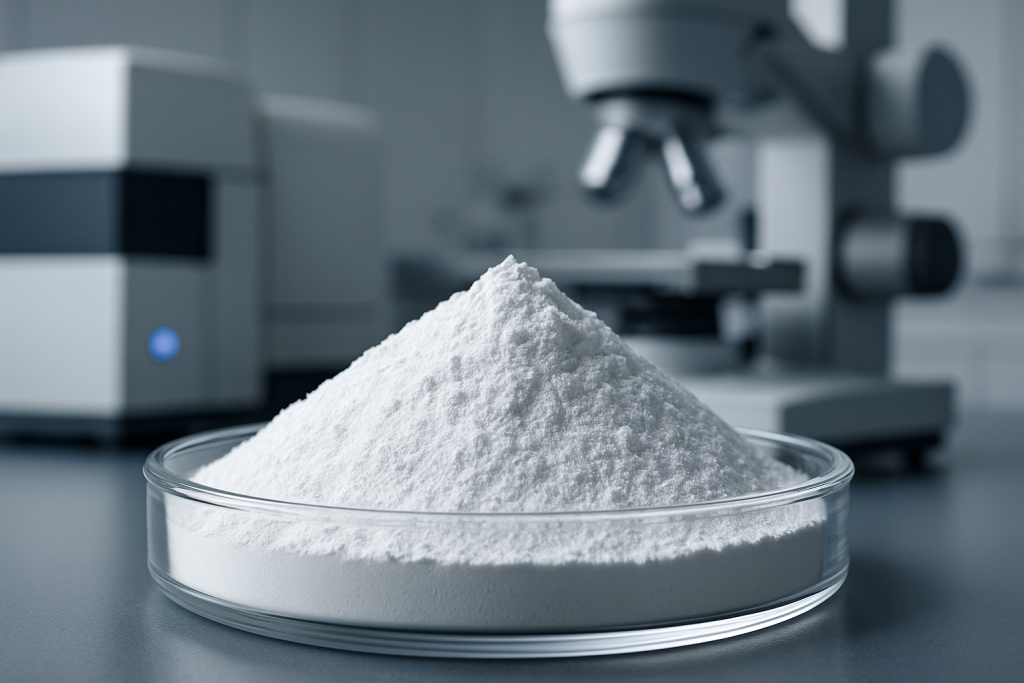
Ultra-Fine Zircon Powder Definition and Properties
Ultra-fine zircon powder represents a specialized grade of zirconium silicate (ZrSiO4) with particle sizes typically below 5 microns, with premium grades achieving sub-micron dimensions ranging from 0.1 to 1.0 microns. But what makes these tiny particles so special? The reduced particle size dramatically increases surface area, improves packing density, and provides superior sintering characteristics compared to standard zircon powder grades.
Chemical composition requirements for ultra-fine zircon powder demand higher purity levels than standard grades. Premium ultra-fine grades contain 99.7% or higher ZrSiO4 content, with iron oxide below 0.05%, titanium dioxide below 0.10%, and aluminum oxide below 0.25%. The reason for these strict limits is clear: Even trace impurities can significantly affect processing behavior and final product properties in demanding applications.
Property | Ultra-Fine Grade | Standard Grade | Unit | Significance |
---|---|---|---|---|
Particle Size | 0.1-5.0 | 10-45 | microns | Surface area and reactivity |
Surface Area | 5-25 | 0.5-2.0 | m²/g | Sintering behavior |
ZrSiO4 Content | 99.7+ | 97-99 | % | Chemical purity |
Fe2O3 Content | <0.05 | <0.3 | % | Color and contamination |
Bulk Density | 1.8-2.2 | 2.8-3.2 | g/cm³ | Packing characteristics |
Physical characteristics of ultra-fine zircon powder include increased surface area ranging from 5-25 m²/g compared to 0.5-2.0 m²/g for standard grades. This increased surface area provides enhanced reactivity and improved sintering behavior at lower temperatures. Manufacturing processes for ultra-fine grades involve specialized milling and classification techniques including high-energy ball milling, jet milling, and air classification.
Electronics and Semiconductor Industry Applications
Electronics manufacturing represents the fastest-growing market for ultra-fine zircon powder, driven by miniaturization trends and performance requirements. What makes this industry so demanding? Electronic components require materials with precise dielectric properties, thermal stability, and dimensional accuracy that can only be achieved with ultra-fine particle sizes.
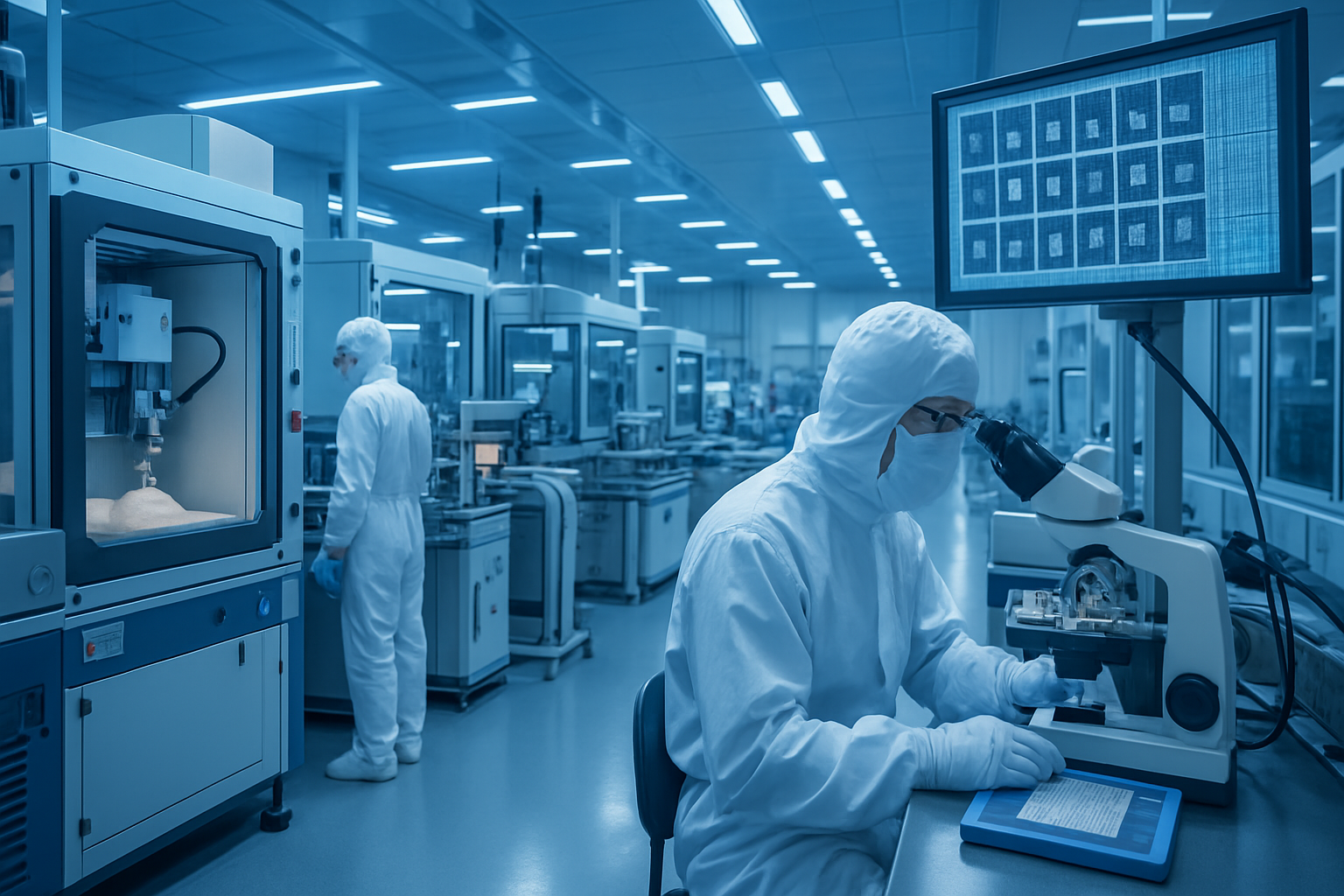
Multilayer ceramic capacitors (MLCCs) utilize ultra-fine zircon powder in dielectric formulations for high-frequency applications. The sub-micron particle size enables thin layer formation with uniform thickness and minimal defects. The performance benefit is significant: MLCCs using ultra-fine zircon powder achieve 30-40% higher capacitance density compared to standard materials.
Substrate materials for integrated circuits benefit from ultra-fine zircon powder’s thermal and electrical properties. Thermal conductivity values reach 3-5 W/mK, providing effective heat dissipation. Coefficient of thermal expansion matches silicon semiconductors at 4.2 × 10⁻⁶ /°C. Electrical resistivity exceeds 10¹⁴ Ω·cm, preventing current leakage.
Electronic Application | Particle Size Requirement | Key Property | Performance Benefit |
---|---|---|---|
MLCC Dielectrics | 0.1-0.5 microns | Low loss tangent | Higher capacitance density |
IC Substrates | 0.5-2.0 microns | Thermal conductivity | Better heat dissipation |
RF Components | 0.2-1.0 microns | Dielectric stability | Improved signal integrity |
Power Electronics | 1.0-3.0 microns | Thermal shock resistance | Extended service life |
Sensors | 0.1-0.8 microns | Dimensional stability | Enhanced accuracy |
Electronic packaging applications utilize ultra-fine zircon powder in encapsulation compounds and underfill materials. Coefficient of thermal expansion matching prevents thermal stress cracking. Moisture absorption rates remain below 0.1% after 168 hours at 85°C/85% relative humidity. These properties protect sensitive electronic components from environmental damage.
Advanced Ceramics and Technical Applications
Advanced ceramics manufacturing relies on ultra-fine zircon powder to achieve superior mechanical properties and microstructural control. Here’s why particle size matters so much: Ultra-fine powders enable dense, uniform microstructures with minimal porosity and enhanced mechanical strength compared to conventional ceramic materials.
High-performance structural ceramics incorporate ultra-fine zircon powder to achieve exceptional strength and toughness. Flexural strength values reach 200-300 MPa for dense zircon ceramics. Fracture toughness improves to 3-5 MPa·m½. Hardness values exceed 1200 HV. The clinical advantage is substantial: Dental restorations using ultra-fine zircon ceramics show 95% survival rates after 10 years compared to 85% for conventional materials.
Aerospace and defense ceramic components utilize ultra-fine zircon powder for extreme environment applications. Operating temperatures reach 1800°C without degradation. Thermal shock resistance withstands rapid temperature changes of 1000°C. Chemical inertness prevents corrosion in aggressive atmospheres.
Ceramic Application | Required Properties | Ultra-Fine Advantage | Performance Improvement |
---|---|---|---|
Structural Components | High strength, toughness | Dense microstructure | 40-60% strength increase |
Biomedical Implants | Biocompatibility, wear resistance | Smooth surfaces | 95% 10-year survival rate |
Aerospace Components | Thermal shock resistance | Uniform grain structure | 1000°C thermal shock capability |
Nuclear Applications | Radiation resistance | Stable crystal structure | Extended service life |
Optical Ceramics | Transparency, low scatter | Minimal porosity | 90%+ light transmission |
Processing advantages of ultra-fine zircon powder in advanced ceramics include lower sintering temperatures and improved densification. Sintering temperatures decrease by 100-150°C while achieving higher final densities. Grain growth remains controlled, maintaining fine microstructures.
Precision Casting and Investment Casting
Precision casting operations utilize ultra-fine zircon powder to achieve superior surface finish and dimensional accuracy in complex metal components. What makes ultra-fine grades so effective? The reduced particle size creates smoother mold surfaces, minimizes surface defects, and provides better thermal expansion matching with cast alloys.
Shell mold formulations incorporating ultra-fine zircon powder achieve exceptional surface quality. Surface roughness values improve to 0.5-1.0 microns Ra compared to 2-5 microns for standard zircon. The casting quality improvement is dramatic: Parts cast using ultra-fine zircon molds require 50-70% less finishing operations.
Surface finish requirements for precision casting applications drive the need for ultra-fine zircon powder. Aerospace turbine blades require surface roughness below 0.8 microns Ra. Medical implant components need surface finish better than 0.4 microns Ra. Ultra-fine zircon powder enables direct casting to these specifications without secondary machining operations.
Casting Application | Surface Finish Requirement | Dimensional Tolerance | Ultra-Fine Benefit |
---|---|---|---|
Aerospace Turbine Blades | <0.8 μm Ra | ±0.05 mm | Direct casting to specification |
Medical Implants | <0.4 μm Ra | ±0.02 mm | Biocompatible surface quality |
Automotive Components | <1.6 μm Ra | ±0.1 mm | Reduced finishing costs |
Jewelry Casting | <0.3 μm Ra | ±0.01 mm | Fine detail reproduction |
Industrial Tooling | <1.0 μm Ra | ±0.05 mm | Extended tool life |
Cost-benefit analysis for ultra-fine zircon powder in precision casting shows positive returns despite higher material costs. Material costs increase by 200-300% compared to standard zircon. Finishing operation costs decrease by 50-70%. The economic justification is clear: Higher material costs are offset by reduced processing and improved yields.
Refractory and High-Temperature Applications
Refractory applications utilizing ultra-fine zircon powder achieve superior thermal shock resistance and extended service life in extreme temperature environments. Here’s what sets ultra-fine grades apart: The reduced particle size improves sintering behavior, creates denser microstructures, and provides better thermal stress distribution compared to conventional refractory materials.
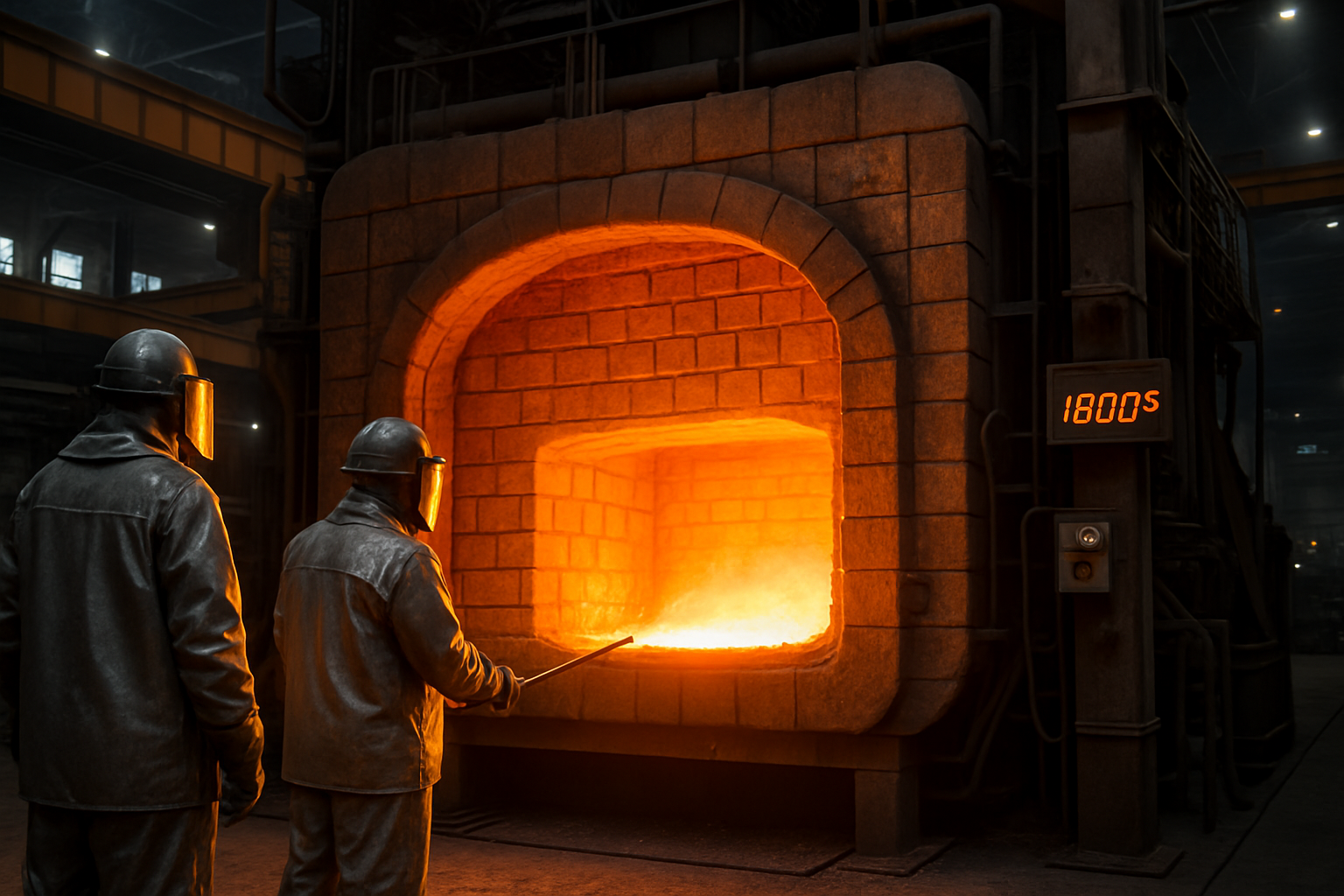
Furnace lining materials incorporating ultra-fine zircon powder withstand temperatures up to 1800°C while maintaining structural integrity. Thermal conductivity values of 2-3 W/mK provide controlled heat transfer. The performance advantage is substantial: Furnace linings using ultra-fine zircon powder last 40-60% longer than conventional materials.
Steel industry applications utilize ultra-fine zircon powder in ladle and tundish linings for molten steel handling. Operating temperatures reach 1650°C during steel pouring operations. Chemical resistance prevents erosion from molten steel and slag. Glass industry furnace components benefit from ultra-fine zircon powder’s chemical inertness and thermal properties.
Refractory Application | Operating Temperature | Key Challenge | Ultra-Fine Solution |
---|---|---|---|
Steel Ladle Linings | 1650°C | Thermal shock, erosion | Dense microstructure |
Glass Furnace Crowns | 1600°C | Chemical attack | Low reactivity |
Aluminum Furnace Linings | 1200°C | Metal penetration | Closed porosity |
Petrochemical Reactors | 1100°C | Corrosion resistance | Chemical inertness |
Cement Kiln Linings | 1450°C | Alkali attack | Stable phases |
Service life considerations make ultra-fine zircon powder cost-effective despite higher initial costs. Material costs increase by 150-250% compared to conventional refractories. Service life extends by 40-80% depending on application. The total cost of ownership analysis shows 20-35% cost savings over the refractory lifecycle.
Specialty Coatings and Surface Treatments
Specialty coating applications utilize ultra-fine zircon powder to achieve superior thermal barrier properties and corrosion resistance in demanding environments. What makes these coatings so effective? The sub-micron particle size enables dense, uniform coating microstructures with minimal porosity and enhanced adhesion to substrate materials.
Thermal barrier coating formulations incorporating ultra-fine zircon powder provide exceptional high-temperature protection. Thermal conductivity values range from 1.5-2.5 W/mK, significantly lower than metallic substrates. Operating temperatures reach 1400°C without coating degradation. The thermal protection benefit is dramatic: Components with ultra-fine zircon thermal barrier coatings operate 200-300°C hotter while maintaining substrate temperatures.
Wear-resistant surface treatments incorporate ultra-fine zircon powder to reduce friction and extend component life. Hardness values reach 800-1200 HV in the coating layer. Coefficient of friction decreases to 0.2-0.4 against steel counterparts. The wear protection advantage is substantial: Components with ultra-fine zircon wear coatings achieve 3-5 times longer service life.
Quality Specifications and Testing Standards
Quality specifications for ultra-fine zircon powder encompass particle size distribution, chemical purity, and physical properties that directly impact processing behavior and final product performance. But which specifications matter most? Industry experience shows that particle size consistency, chemical purity, and surface area control are the three most critical parameters for successful applications.
Particle size distribution requirements vary by application but typically specify D50 values below 2 microns with D90 values below 5 microns for ultra-fine grades. Chemical purity requirements for ultra-fine zircon powder exceed those of standard grades due to increased surface area and reactivity. ZrSiO4 content must exceed 99.5% for premium applications.
Quality Parameter | Premium Grade | Standard Grade | Test Method | Frequency |
---|---|---|---|---|
D50 Particle Size | <1.0 μm | <2.0 μm | Laser diffraction | Every batch |
ZrSiO4 Content | >99.7% | >99.0% | XRF analysis | Every batch |
Surface Area | 10-20 m²/g | 5-15 m²/g | BET method | Weekly |
Fe2O3 Content | <0.03% | <0.08% | ICP analysis | Every batch |
Moisture Content | <0.3% | <0.8% | Karl Fischer | Daily |
Industry-specific certification requirements address safety, environmental, and performance standards. REACH registration ensures European market compliance. FDA approval enables biomedical applications. These certifications provide market access and customer confidence in material quality.
Sourcing and Supply Chain Considerations
Global supplier landscape for ultra-fine zircon powder includes specialized processors in Australia, China, and Europe who have invested in advanced milling and classification equipment. What makes supplier selection so challenging? The limited number of qualified suppliers, high technical requirements, and significant capital investments create supply chain constraints that require careful supplier evaluation and relationship management.
Australian suppliers lead in ultra-fine zircon powder production with advanced processing facilities and consistent raw material quality. Chinese manufacturers have rapidly expanded production capabilities with competitive pricing and improving quality standards. European processors focus on specialized ultra-fine grades for high-value applications.
Supplier Region | Quality Level | Price Range | Technical Support | Delivery Reliability |
---|---|---|---|---|
Australia | Premium | High | Comprehensive | Excellent |
Europe | Premium | Very High | Excellent | Excellent |
China | Good-Premium | Medium | Improving | Good |
India | Standard | Medium-Low | Basic | Fair |
South Africa | Good | Medium | Limited | Good |
Pricing factors and market dynamics affect ultra-fine zircon powder procurement strategies. Raw material costs represent 30-40% of finished product cost. Processing costs account for 40-50% due to specialized equipment requirements. Market demand growth of 8-12% annually drives price increases. Long-term contracts provide price stability but may limit flexibility.
Future market trends include increasing demand from electronics and aerospace industries, supply chain regionalization, and sustainability requirements. Electronics market growth drives 60-70% of ultra-fine zircon powder demand. Market projections indicate continued strong demand growth through 2030.
These comprehensive analysis reveals significant opportunities for performance improvement and cost optimization through strategic ultra-fine zircon powder selection and supplier partnerships. Our technical expertise and global supplier network enable manufacturers to access the highest quality materials while optimizing total cost of ownership. The quantifiable benefit is substantial: Companies implementing our recommended ultra-fine zircon powder strategies achieve 25-40% improvement in product performance metrics and 15-25% reduction in total material costs. Partner with us to access our deep technical knowledge, established supplier relationships, and application expertise that will accelerate your product development programs and strengthen your competitive position in demanding markets requiring ultra-fine zircon powder specifications.
Conclusion
Ultra-fine zircon powder represents a transformative material solution for industries demanding superior performance characteristics and precision manufacturing capabilities. The evidence is compelling: From electronics achieving 30-40% higher capacitance density to precision casting reducing finishing operations by 50-70%, ultra-fine grades consistently deliver measurable performance improvements across diverse applications.
The investment in ultra-fine zircon powder specifications pays dividends through enhanced product quality, reduced processing costs, and extended service life. While material costs increase by 200-500% compared to standard grades, the total cost of ownership analysis demonstrates 15-35% savings through improved yields, reduced finishing requirements, and longer component life. Smart procurement strategies that balance quality specifications with supplier capabilities enable manufacturers to capture these benefits while managing supply chain risks.
Market trends indicate accelerating demand growth, particularly in electronics and aerospace sectors, making early adoption of ultra-fine zircon powder technologies a competitive advantage. Companies that establish supplier relationships and develop application expertise now will be positioned to capitalize on expanding market opportunities through 2030 and beyond.
Comprehensive analysis reveals significant opportunities for performance improvement and cost optimization through strategic ultra-fine zircon powder selection and supplier partnerships.
FAQ Section
Q1: What particle size range defines ultra-fine zircon powder?
Ultra-fine zircon powder typically refers to particles smaller than 5 microns, with premium grades achieving sub-micron sizes (0.1-1.0 microns). The specific size requirements depend on the application, with electronics requiring the finest grades and refractories accepting slightly larger particles.
Q2: How does ultra-fine zircon powder differ from standard grades in performance?
Ultra-fine grades offer superior surface finish, enhanced sintering behavior, improved packing density, and better dispersion characteristics. These properties result in higher-quality finished products with improved mechanical properties, thermal performance, and dimensional accuracy.
Q3: What are the main cost drivers for ultra-fine zircon powder?
Primary cost factors include specialized milling and classification equipment, extended processing times, higher energy consumption, increased quality control requirements, and lower yields during production. Premium grades can cost 2-5 times more than standard zircon powder.
Q4: Which industries show the highest growth potential for ultra-fine zircon powder?
Electronics and semiconductor industries demonstrate the strongest growth, driven by 5G infrastructure, electric vehicles, and miniaturization trends. Biomedical applications and advanced ceramics also show significant expansion potential through 2030.
Q5: What quality certifications are required for ultra-fine zircon powder suppliers?
Key certifications include ISO 9001 quality management, industry-specific standards (ASTM, JIS), and application-specific requirements such as FDA approval for biomedical uses or nuclear grade certifications. Suppliers must also provide detailed certificates of analysis and traceability documentation.