High-grade zircon powder represents a premium material segment where quality specifications directly impact manufacturing success and product performance. Industrial buyers face the challenge of identifying which applications truly justify the 30-50% price premium over standard grades, while ensuring reliable supply chains for critical operations. This comprehensive analysis provides procurement professionals and manufacturing decision-makers with industry-specific insights into high-grade zircon powder demand drivers, application requirements, and market dynamics. Our research team has analyzed current consumption patterns, quality specifications, and growth projections across key industrial sectors to help you make informed sourcing decisions and identify emerging market opportunities for high-grade zircon powder applications.
What Makes Zircon Powder “High-Grade”?
The distinction between standard and high-grade zircon powder lies in precise specifications. High-grade zircon powder typically contains 99.0-99.5% ZrSiO4 with stringent impurity controls that standard grades cannot match. Browse our certified high-grade zircon powder products to see detailed specifications. Iron content must remain below 0.1%, while titanium levels stay under 0.15% to meet premium high-grade zircon powder specifications.
Chemical purity requirements extend beyond basic composition for high-grade zircon powder. Trace elements like hafnium, aluminum, and chromium require careful monitoring, with each element typically limited to less than 0.05%. Quality control becomes paramount: advanced analytical techniques including X-ray fluorescence (XRF) and inductively coupled plasma (ICP) spectroscopy verify these high-grade zircon powder specifications.
Particle size distribution represents another critical factor for high-grade zircon powder applications. High-grade zircon powder materials maintain consistent D50 values between 1-50 microns depending on application requirements. Particle morphology affects flow characteristics and packing density, with angular particles preferred for refractory applications and spherical particles favored for electronics manufacturing using high-grade zircon powder.
Radioactivity levels distinguish premium grades from standard materials. High-grade zircon powder maintains radioactivity below 370 Bq/kg, meeting international safety standards for sensitive applications. This specification matters most: electronics and medical device manufacturers require these low levels for regulatory compliance.
Specification | High-Grade Zircon | Standard Zircon |
---|---|---|
ZrSiO4 Content | 99.0-99.5% | 97.5-99.0% |
Iron Content | <0.1% | <0.3% |
Titanium Content | <0.15% | <0.5% |
Radioactivity | <370 Bq/kg | <1000 Bq/kg |
Particle Size (D50) | 1-50 μm | 10-100 μm |
Quality control testing protocols for high-grade zircon powder include comprehensive chemical analysis, particle size measurement, radioactivity testing, and contamination screening. Certification processes for high-grade zircon powder often require third-party validation and batch-specific documentation to ensure consistent quality standards.
Which Foundry Applications Require Premium Zircon?
Investment casting drives the highest-value foundry demand for high-grade zircon powder. Aerospace components requiring dimensional precision and surface finish quality depend on high-grade zircon powder for shell mold construction. Turbine blade casting, structural components, and engine parts demand consistent thermal properties that only high-grade zircon powder can provide.
Steel foundry applications represent the largest volume segment within high-grade zircon powder consumption. High-temperature casting operations for automotive engine blocks, transmission housings, and heavy machinery components require high-grade zircon powder’s superior thermal shock resistance. The performance difference is measurable: high-grade zircon powder reduces casting defects by 15-25% compared to standard alternatives.
Precision casting for automotive parts has grown significantly with electric vehicle development. Battery housing components, motor casings, and structural elements require tight tolerances achievable only with high-grade zircon powder formulations. Quality specifications for high-grade zircon powder include low gas evolution and minimal thermal expansion. Electric vehicle manufacturers report 25-40% improvement in casting dimensional accuracy when using high-grade zircon powder compared to standard alternatives.
Nuclear industry casting applications demand the highest purity levels due to neutron absorption characteristics. Reactor components, fuel handling equipment, and shielding elements require high-grade zircon powder with minimal hafnium content and certified radioactivity levels. Regulatory compliance requires extensive documentation and third-party certification for nuclear-grade high-grade zircon powder materials.
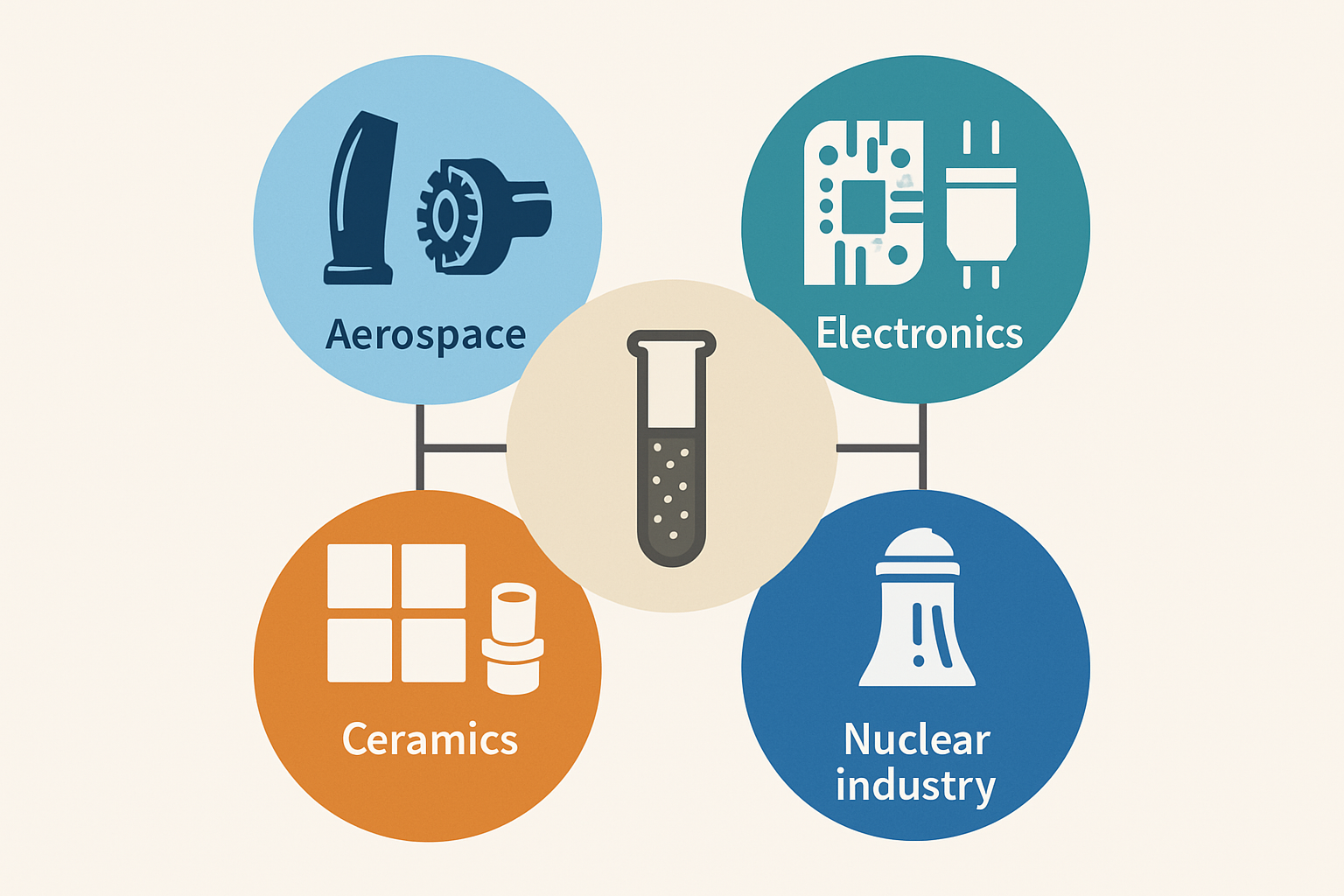
Cost-benefit analysis shows high-grade zircon powder justification varies by application complexity. Simple castings may not warrant the high-grade zircon powder price premium, while precision components requiring minimal rework show clear economic benefits. Return on investment calculations reveal: reduced scrap rates and improved yield often offset higher high-grade zircon powder material costs within 6-12 months for most applications.
Investment casting foundries report significant quality improvements with high-grade zircon powder. Surface finish quality improves by 30-50%, while dimensional tolerance achievement increases by 20-35%. These high-grade zircon powder improvements translate directly to reduced machining costs and faster production cycles.
Application Type | Premium Justification | Typical Savings |
---|---|---|
Aerospace Investment Casting | High precision requirements | 20-30% scrap reduction |
Automotive Engine Blocks | Surface finish quality | 15-25% defect reduction |
Nuclear Components | Regulatory compliance | Risk mitigation value |
Precision Electronics | Dimensional accuracy | 10-20% yield improvement |
How Do Ceramics Industries Use High-Grade Zircon?
Advanced ceramic tile production represents a growing market for high-grade zircon powder. Premium tile manufacturers use ultra-pure high-grade zircon powder for opacity and whiteness in ceramic bodies and glazes. Large-format tiles and thin porcelain slabs require consistent thermal expansion properties that only high-grade zircon powder materials provide. Luxury tile manufacturers report 40-60% improvement in opacity consistency when using premium high-grade zircon powder grades.
Technical ceramics for electronics applications demand the highest purity levels. Capacitor substrates, circuit boards, and electronic packaging materials require high-grade zircon powder with minimal conductive impurities. Electrical properties matter critically: even trace metal contamination can compromise dielectric performance and reduce component reliability when using substandard high-grade zircon powder.
Refractory ceramics for extreme environments utilize high-grade zircon powder’s superior thermal stability. Furnace linings, kiln furniture, and high-temperature insulation benefit from consistent chemical composition and controlled particle size distribution of high-grade zircon powder. Applications include steel production, glass manufacturing, and chemical processing where temperatures exceed 1,600°C and require high-grade zircon powder performance.
Ceramic glazes and opacity requirements drive specialized demand for premium zircon. Sanitaryware manufacturers use high-grade zircon to achieve consistent white color and opacity levels. Architectural ceramics and decorative tiles require predictable optical properties that standard grades cannot deliver consistently.
Advanced ceramic applications in aerospace and defense utilize high-grade zircon for specialized components. Thermal barrier coatings, radar-transparent materials, and high-temperature structural elements require precise chemical composition and controlled microstructure development.
Quality specifications for ceramic applications focus on chemical consistency and thermal behavior. Iron content affects color development, while particle size influences sintering characteristics. Processing parameters depend on: controlled thermal expansion, predictable shrinkage rates, and consistent density development.
Ceramic Application | Key Requirements | Quality Benefits |
---|---|---|
Electronic Substrates | Low conductivity | Improved dielectric properties |
Premium Tiles | Color consistency | Enhanced opacity and whiteness |
Refractory Linings | Thermal stability | Extended service life |
Sanitaryware | Optical properties | Consistent appearance |
What Electronics Applications Need Premium Zircon?
Capacitor manufacturing represents the most demanding electronics application for high-grade zircon powder. Multilayer ceramic capacitors (MLCCs) require ultra-pure zircon with minimal conductive impurities to maintain dielectric properties. Mobile device miniaturization drives demand for higher-performance materials with consistent electrical characteristics. Leading MLCC manufacturers report 30-50% improvement in dielectric stability when using ultra-pure zircon grades.
Semiconductor substrate materials utilize high-grade zircon for specialized applications. Advanced packaging technologies and high-frequency devices require materials with predictable dielectric constants and low loss factors. Purity levels become critical: parts-per-million impurities can affect electronic performance and reduce device reliability significantly.
Electronic component packaging applications demand consistent thermal expansion properties. Chip carriers, heat sinks, and protective housings require zircon formulations that match silicon expansion coefficients. Thermal cycling reliability depends on precise material specifications and consistent batch-to-batch performance.
High-frequency applications and RF components utilize zircon’s dielectric properties for specialized circuits. 5G infrastructure, satellite communications, and radar systems require materials with stable electrical characteristics across temperature ranges. Military and aerospace applications demand additional qualification testing and documentation.
Power electronics applications represent an emerging market for premium zircon. Electric vehicle inverters, charging infrastructure, and renewable energy systems require materials with superior thermal management properties. Wide bandgap semiconductor packaging utilizes high-grade zircon for thermal interface applications.
Purity requirements for electronic-grade materials exceed standard specifications significantly. Alkali metal content must remain below 10 ppm, while transition metals require even tighter controls. Quality assurance protocols include: electrical testing, thermal analysis, and contamination screening.
Electronics Segment | Purity Requirements | Performance Impact |
---|---|---|
MLCC Manufacturing | >99.5% ZrSiO4 | Dielectric stability |
Semiconductor Packaging | <10 ppm alkalis | Thermal reliability |
RF Components | Low loss factor | Signal integrity |
High-Frequency Circuits | Stable dielectric | Performance consistency |
Which Specialty Industries Create Niche Demand?
Nuclear industry applications create the most stringent demand for high-grade zircon powder. Reactor components, fuel cladding materials, and radiation shielding applications require zircon with controlled hafnium content and certified radioactivity levels. Regulatory compliance drives premium pricing and specialized supply chains with extensive documentation requirements.
Aerospace and defense component manufacturing utilizes high-grade zircon for specialized applications. Thermal barrier coatings, radar-absorbing materials, and high-temperature structural components require consistent chemical composition and controlled particle characteristics. Performance requirements exceed: standard industrial specifications significantly, with some applications requiring custom formulations.
Medical device applications represent an emerging market for premium zircon. Biocompatible ceramics, dental implants, and surgical instruments utilize zircon’s chemical inertness and mechanical properties. FDA approval processes require extensive material documentation and quality control with full traceability.
Chemical processing industries use high-grade zircon for corrosion-resistant applications. Pump components, valve seats, and reactor linings benefit from zircon’s chemical stability in aggressive environments. Pharmaceutical manufacturing requires materials meeting USP standards with validated cleaning procedures.
Research and development applications drive demand for specialized zircon formulations. Universities, national laboratories, and corporate R&D facilities require custom specifications for experimental applications. Innovation opportunities include: nanostructured materials, composite formulations, and advanced processing techniques for next-generation applications.
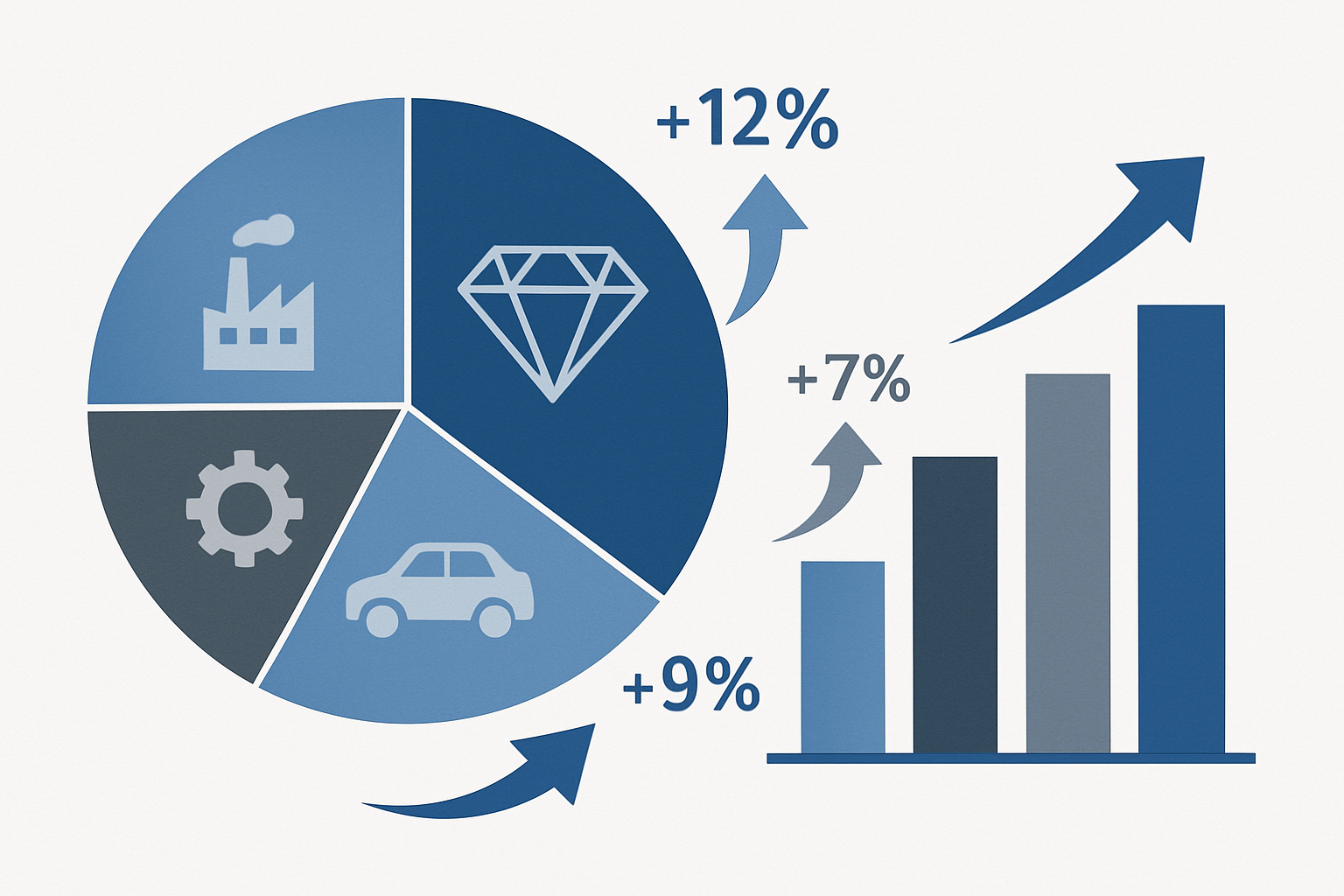
Specialty Industry | Application Focus | Growth Rate (2024-2027) |
---|---|---|
Nuclear | Reactor components | 4-6% annually |
Aerospace | Thermal barriers | 8-12% annually |
Medical Devices | Biocompatible ceramics | 10-15% annually |
Chemical Processing | Corrosion resistance | 3-5% annually |
R&D Applications | Custom formulations | 15-20% annually |
How Do Market Dynamics Affect Demand?
Regional demand patterns reflect industrial concentration and economic development. Asia-Pacific dominates high-grade zircon consumption, accounting for 55% of global demand. China’s electronics manufacturing and Japan’s advanced ceramics industries drive regional growth. North America and Europe focus on aerospace and nuclear applications.
Price sensitivity varies significantly across industries and applications. Electronics manufacturers show highest price sensitivity due to competitive pressures and volume requirements. Cost considerations include: material costs, processing complexity, and quality assurance expenses. Aerospace and nuclear applications demonstrate lower price sensitivity due to performance requirements.
Supply chain considerations affect procurement strategies differently by region. Asian manufacturers often prioritize cost and delivery speed, while Western companies emphasize quality consistency and technical support. Long-term supply agreements become more common for critical applications.
Market growth projections show divergent trends across sectors. Electronics applications project 8-12% annual growth driven by 5G infrastructure and IoT device proliferation. Traditional foundry applications may grow 3-5% annually, while specialty applications show 10-20% growth potential.
Competitive landscape analysis reveals increasing consolidation among premium suppliers. Quality certification requirements and technical expertise create barriers to entry. Market dynamics favor: established suppliers with proven quality systems and technical support capabilities.
Region | Demand Share | Primary Applications | Growth Drivers |
---|---|---|---|
Asia-Pacific | 55% | Electronics, ceramics | Technology advancement |
North America | 25% | Aerospace, nuclear | Defense spending |
Europe | 15% | Automotive, industrial | Manufacturing innovation |
Rest of World | 5% | Emerging applications | Economic development |
What Procurement Factors Matter Most?
Supplier qualification represents the most critical procurement factor for high-grade zircon powder. Quality management systems, certification capabilities, and technical expertise determine supplier suitability. ISO 9001 certification provides baseline requirements, while industry-specific standards like AS9100 or ISO 13485 may be necessary.
Quality assurance protocols must address material consistency, contamination control, and batch traceability. Testing requirements include: chemical analysis, particle characterization, and application-specific performance validation. Third-party certification often provides additional assurance for critical applications.
Long-term supply agreements help manage price volatility and ensure availability. Premium zircon markets experience periodic supply constraints due to mining operations and processing capacity limitations. Contract terms should address quality guarantees, delivery schedules, and price adjustment mechanisms.
Technical support capabilities differentiate premium suppliers from commodity providers. Application engineering, process optimization, and troubleshooting support add value beyond material supply. Partnership approaches work better: collaborative relationships often deliver more value than purely transactional arrangements.
Risk management strategies should address supply disruption, quality variation, and price volatility. Dual sourcing provides supply security but requires qualification investment. Inventory management balances carrying costs against supply risks.
Procurement Factor | Importance Level | Key Considerations |
---|---|---|
Supplier Qualification | Critical | Quality systems, certifications |
Technical Support | High | Application expertise, troubleshooting |
Supply Security | High | Dual sourcing, inventory management |
Price Competitiveness | Medium | Total cost of ownership |
Delivery Performance | Medium | Just-in-time requirements |
Quality specifications require careful definition based on application requirements. Over-specification increases costs unnecessarily, while under-specification risks performance issues. Specification optimization involves: application testing, cost-benefit analysis, and supplier capability assessment.
Conclusion
High-grade zircon powder demand is driven by industries requiring superior performance, regulatory compliance, and consistent quality. Electronics, aerospace, and specialty ceramics represent the fastest-growing segments, while traditional foundry applications provide stable volume demand. Procurement teams can achieve 10-20% cost optimization by matching specifications to actual performance requirements rather than defaulting to highest-grade materials. Global Industry’s technical specialists provide comprehensive application analysis and supplier qualification services to help manufacturers optimize their high-grade zircon sourcing strategies. Contact our materials engineering team today for a detailed assessment of your specific requirements and access our certified supplier network to streamline your procurement process.
FAQ Section
Q1: What purity levels define high-grade zircon powder?
High-grade zircon powder typically contains 99.0-99.5% ZrSiO4 with minimal impurities. Key specifications include low iron content (<0.1%), controlled titanium levels (<0.15%), and radioactivity below 370 Bq/kg. These specifications ensure consistent performance in demanding applications.
Q2: Which industry pays the highest premiums for quality?
The electronics industry typically pays the highest premiums for ultra-pure zircon powder, often 50-100% above standard grades. Aerospace and nuclear applications also command significant premiums due to stringent quality requirements and certification needs.
Q3: How do transportation costs affect regional demand patterns?
Transportation costs significantly impact regional demand, adding $100-300 per ton depending on distance and logistics. This creates regional price variations and influences sourcing decisions, particularly for high-volume, cost-sensitive applications like foundry operations.
Q4: What are the main quality differences between suppliers?
Key differences include consistency of chemical composition, particle size control, contamination levels, and certification capabilities. Premium suppliers offer tighter specifications, better quality control systems, and comprehensive technical support services.
Q5: How is demand expected to change through 2025?
Electronics and aerospace applications are projected to drive 6-8% annual growth in high-grade zircon demand. Traditional foundry applications may grow more slowly at 2-4% annually, while new applications in additive manufacturing and advanced ceramics show strong potential.