High-purity zircon sand extraction plays a vital role in industries that demand consistent material performance. From ceramic manufacturers to electronics suppliers, precision in raw materials is non-negotiable. However, many industrial buyers struggle with inconsistencies in sand purity, leading to flaws in production or unexpected rework costs. This article offers a clear, reliable answer. We’ll break down each stage of the extraction process, show how to maintain purity, and explain quality assurance techniques that meet strict buyer expectations. Here’s why this matters—getting this process right means fewer defects, lower processing waste, and better supplier reliability. Our company, a trusted name in materials sourcing, provides this detailed overview for technical professionals and procurement teams seeking clarity and performance.
What is high-purity zircon sand used for?
High-purity zircon sand extraction isn’t just a raw material process—it’s foundational to several sectors that depend on stable mineral inputs. Zircon sand with a high degree of purity is often used in ceramic tiles, sanitaryware, and structural ceramics. The reason? Its excellent refractive index and thermal stability.
In casting industries, particularly investment casting, consistent zircon purity helps create precision molds. Even trace impurities can weaken thermal resistance and dimensional accuracy. This is why sand quality matters from the very beginning.
In electronics, zircon compounds are used in capacitor coatings and piezoelectric components. Purity here is not optional—it determines the performance and durability of components.
Chemical industries use zirconium derivatives sourced from purified sand for catalyst supports and corrosion-resistant linings. So what does this tell us? High-purity zircon sand extraction directly influences product performance, making it a strategic concern for B2B buyers.
Industry Application | Reason for Purity Requirement |
---|---|
Ceramics | Appearance and strength |
Foundries | Dimensional accuracy |
Electronics | Electrical reliability |
Chemical Processing | Reaction stability |
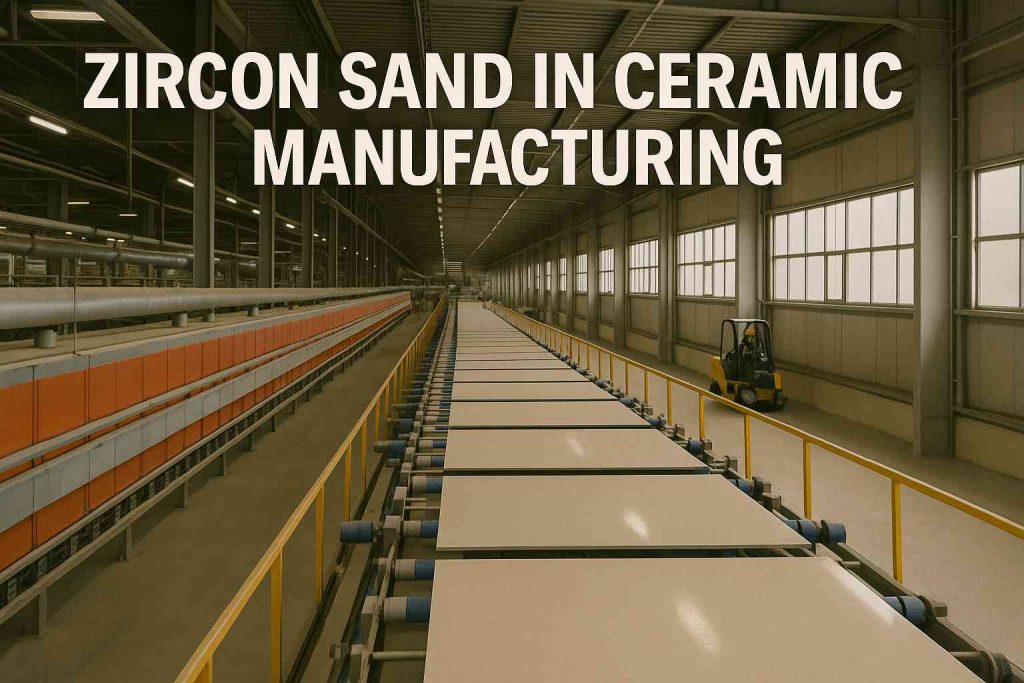
This image shows zircon sand being used in large-scale ceramic tile production.
How is zircon sand typically sourced?
Zircon sand is mined from heavy mineral sand deposits, often located along coastlines or old riverbeds. The sourcing phase determines both volume availability and baseline impurity levels. Deposits rich in monazite, ilmenite, or rutile often coexist with zircon and must be separated early.
There are two main geographic sources: coastal and inland. Coastal sands, like those in Australia or South Africa, are dredged. Inland deposits, like those in India or China, require open-pit or strip mining.
Here’s what most people miss—raw zircon from different locations has varying impurity profiles. For example, zircon from India may contain more iron oxides, while African sources may carry more radioactive minerals.
Once mined, the sand is stockpiled and transported for primary separation. Environmental concerns are real here. Water usage, land disruption, and tailing storage are major regulatory hurdles. Responsible suppliers use closed-loop water systems and land reclamation methods to reduce impact.
Source Type | Common Region | Mining Method | Notable Contaminants |
---|---|---|---|
Coastal Deposits | South Africa | Dredging | Rutile, monazite |
Inland Deposits | India, China | Strip Mining | Iron oxides, clay minerals |
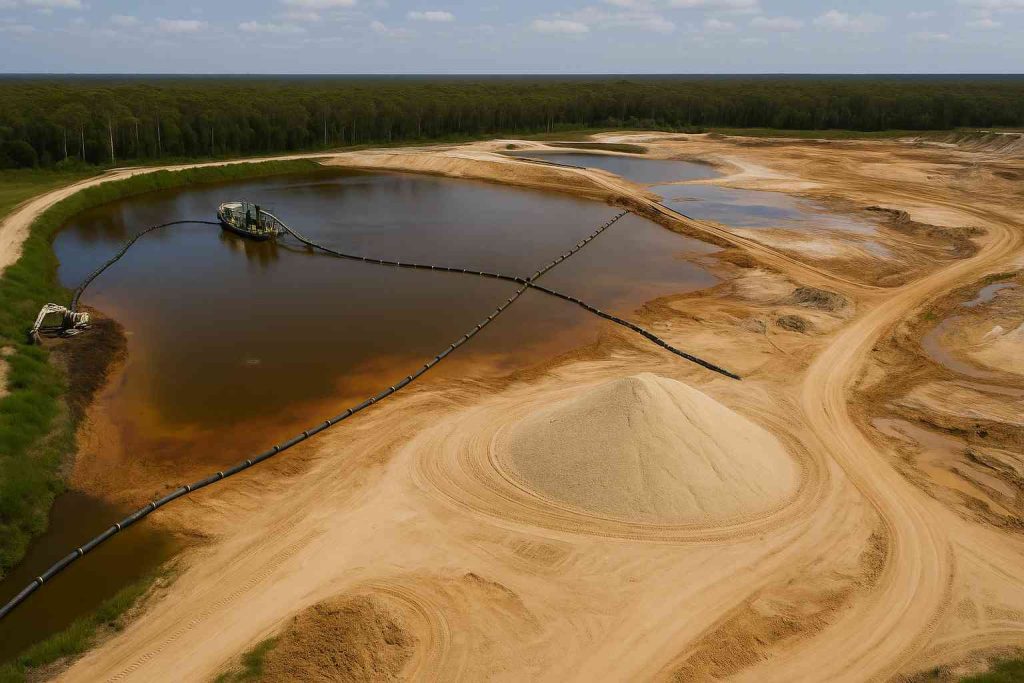
An aerial shot of a zircon sand mining operation using dredging equipment.
What are the stages of zircon ore preparation?
Zircon sand doesn’t arrive pure. Ore must be processed in several steps to reach high-purity status. It begins with mechanical reduction—usually jaw crushers followed by roll crushers. This breaks large clumps into manageable particles.
Next, the material is screened using vibratory classifiers. Particles that fall outside the target range are cycled back through. This step also removes oversize rock and clay fragments.
Washing is next. Water jets clean surface dirt and clay fines that may interfere with later processes. This step also separates lighter materials, like mica or organic debris.
Want to know what’s next? Some operations use spirals and cyclones to create a sand concentrate with higher zircon content. At this point, purity has improved—but only marginally. It’s the next steps that matter more.
Preparation Step | Purpose |
---|---|
Crushing | Reduce ore to workable size |
Screening | Remove oversize and undersize |
Washing | Eliminate fines and surface dust |
Spiral Separation | Pre-concentrate zircon fraction |
Which purification techniques remove impurities?
Mechanical sorting gets us partway there, but high-purity zircon sand extraction depends on refining techniques. These fall into three categories: magnetic, electrostatic, and chemical.
Magnetic separation removes minerals with ferrous content, such as ilmenite or magnetite. Even weak magnets can help isolate zircon from these components. But here’s the kicker—zircon itself is not magnetic, making this technique ideal for cleaning up the mix.
Electrostatic separation works on conductivity differences. Minerals like rutile and leucoxene conduct electricity better than zircon and can be separated on high-voltage plates. Purity levels rise here dramatically.
The final method is chemical. Acid leaching, usually with sulfuric or hydrochloric acid, dissolves remaining surface contaminants like iron, titanium, or organics. This method is costly but effective.
Method | Target Impurities | Pros | Cons |
---|---|---|---|
Magnetic Separation | Ferromagnetic minerals | Simple, low cost | Limited to metal-bearing |
Electrostatic | Conductive minerals | Effective for dry feedstock | Needs dry, fine material |
Acid Leaching | Oxides, carbonates | Highest purity yield | Cost and safety concerns |
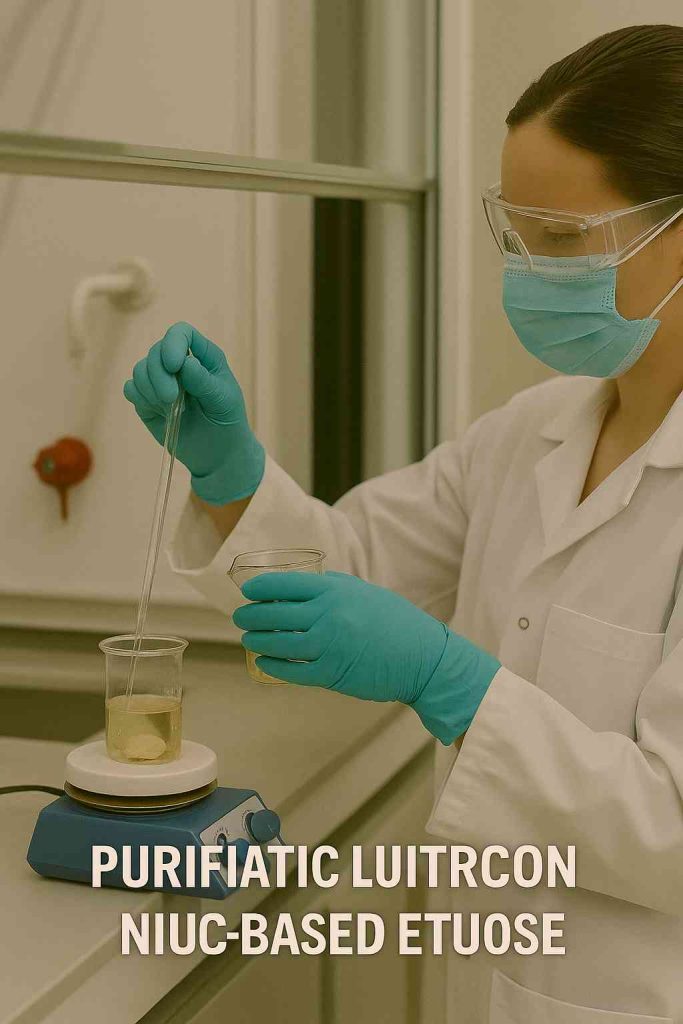
Technicians perform acid-based purification on zircon samples in a controlled lab environment.
How is particle size refined for industrial use?
Zircon sand must meet size specs for different end uses. Granularity affects both performance and process compatibility. High-purity zircon sand extraction isn’t complete without tight control of particle distribution.
The process starts with ball milling or jet milling to reduce size. Then comes classification—dry or wet sieving sorts particles by mesh size. Buyers often specify D50 (median diameter), and meeting this spec is critical.
Need an example? Tile manufacturers often need particles under 44 microns for proper glaze dispersion. Foundries may require 100-200 microns for optimal mold performance.
Application | Preferred Size Range (µm) |
---|---|
Ceramics Glaze | < 44 |
Investment Casting | 100–150 |
Refractory Coatings | 75–125 |
What quality control measures are involved?
Maintaining purity and consistency isn’t optional. High-purity zircon sand extraction must include quality control at each step. This usually begins with sample collection at receiving, processing, and final packaging.
XRF (X-ray fluorescence) and ICP (inductively coupled plasma) tests determine elemental composition. Spectroscopy detects titanium, iron, and other common impurities.
Grain size and shape analysis confirm performance in molds or glazes. Flowability and packing density are also tested. Let’s break it down—without these steps, you’re guessing, not assuring quality.
Quality Metric | Common Test Method |
---|---|
Elemental Purity | XRF / ICP |
Particle Size | Laser Diffraction |
Surface Cleanliness | Acid Solubility |
How is high-purity zircon packaged and stored?
Packaging protects against contamination and moisture. After extraction, zircon is dried, sieved, and packed. Most suppliers use double-layer polypropylene bags with moisture barriers.
Export packaging must meet international labeling standards, including hazard markings if applicable (due to trace radioactivity). Pallets are stretch-wrapped and secured for ocean freight.
Storage is equally important. Why does this matter? Improper handling allows airborne dust or oil residues to reduce the purity level post-processing.
Packaging Type | Description |
---|---|
25kg PP Bags | Inner liner, moisture barrier |
1MT Jumbo Bags | Lined, stackable |
Bulk Containers | Used for direct industrial supply |
What challenges impact purity during processing?
Even the best setups face risks. Equipment wear introduces metal fragments into the mix. Poor maintenance or old milling machines increase this threat. Regular inspections and food-grade coatings help reduce it.
Cross-contamination can occur if lines are reused for different minerals. Dedicated lines or intensive cleaning between runs are best practices.
What else can go wrong? Variability in feedstock. Some deposits vary by the truckload. Constant testing and blending help normalize output.
Issue | Source | Mitigation Strategy |
---|---|---|
Metal Leaching | Equipment wear | Coatings, maintenance |
Feedstock Variability | Geological inconsistency | Blending and batch testing |
Residue Contamination | Poor cleaning protocols | Dedicated lines or flushing |
How do industry standards influence processing?
Industry norms define the target. For example, ISO 12677 outlines zircon purity tests. ASTM E2617 sets procedures for detecting trace radioactive elements.
Clients may also have their own technical data sheets requiring ≥99% ZrSiO₄ content, <0.1% TiO₂, and similar targets. Put simply—regulations and buyer specs shape the entire process.
Environmental rules require proper handling of tailings and acids. Failure to comply affects licensing and market access.
Standard | Focus Area |
---|---|
ISO 12677 | Zircon purity verification |
ASTM E2617 | Radioactivity analysis |
Local Environmental Codes | Acid disposal, water recycling |
Conclusion
High-purity zircon sand extraction is not a one-step process. It involves precise sourcing, separation, refining, and quality control. When done correctly, the result is a material that performs consistently across industrial applications. For buyers, this means fewer product defects and smoother downstream operations. Our company helps procurement leaders understand what defines quality in zircon and how to source it confidently. For tailored support or a sample quote, contact our team directly. Let’s work together toward higher material consistency and supply chain clarity.
FAQ Section
Q1: Is high-purity zircon sand different from standard zircon?
Yes. High-purity zircon sand contains fewer impurities like iron, titanium, and silica. It’s refined to meet strict industrial standards, making it suitable for technical ceramics, foundries, and electronics. Standard zircon often has inconsistent quality and is not ideal for precision processes.
Q2: What purity levels do industrial buyers usually require?
Most ceramic and casting applications require ≥98.5% ZrSiO₄ content. Electronics and chemical users often specify ≥99%. Buyers also set strict limits on TiO₂ and Fe₂O₃, sometimes below 0.1%, depending on downstream sensitivity.
Q3: What documents should suppliers provide with each shipment?
Suppliers should include a Certificate of Analysis, recent XRF or ICP test results, moisture level report, packaging specification, and, where needed, a radiation compliance declaration. These confirm product quality and simplify customs clearance.
Q4: Can chemical purification be skipped for some applications?
Only in low-spec or non-technical applications. For high-performance sectors like electronics or pigments, chemical steps such as acid leaching are necessary to meet impurity thresholds. Skipping these stages increases the risk of defects and product rejection.
Q5: How can buyers prevent receiving inconsistent zircon quality?
Work with suppliers who apply batch-level testing and provide third-party lab verification. Specify exact impurity limits in your contract and request samples from each production batch before full shipment. Building a long-term relationship with audited suppliers also reduces variability.