Zircon sand’s natural radioactivity raises questions for managers and health and safety teams across industrial sectors. From foundries to ceramics plants, firms use zircon sand in high-temperature processes and precision casting. Yet, there’s concern about health risks from radioactive particles in zircon sand. Here’s what matters most: this article gives you clear answers and practical guidance on how to handle zircon sand safely while keeping in line with international standards. At Global Industry, we draw on real-world experience in industrial minerals and radiation safety to offer insights that go beyond theory. As demand for zircon grows in many industries, understanding the best ways to protect workers and the environment is more vital than ever.
What is Zircon Sand Used For?
Zircon sand has a long history in manufacturing. It’s known for its thermal stability and ability to stand up to intense heat. This makes it a favorite in ceramics production, where it strengthens glazes and improves the final product’s lifespan. In foundries, zircon sand helps create precise molds that stand up to the demands of molten metal casting. Its use in refractories also brings better performance under heat stress.
Let’s break this down a bit more: the sand’s natural properties, including a high melting point and low expansion rate, make it ideal for these applications.
● Ceramic manufacturing in Europe, North America, and Asia often depends on zircon sand to create high-quality tiles and sanitary ware.
● Foundries in regions like Germany and China value zircon’s performance in precision casting.
● Refractory brick makers worldwide depend on zircon’s resilience against cracking and thermal shock.
Here’s a quick look at its most common uses and benefits:
Industry | Application | Benefit |
---|---|---|
Ceramics | Toughen glazes, reduce porosity | Longer-lasting tiles, better finish |
Refractories | Refractory shapes, high-heat bricks | Greater resistance to heat cycles |
Foundries | Mold and core production | Cleaner, more accurate castings |
Chemical industries | Raw material for zirconium chemicals | Consistent quality, low impurity levels |
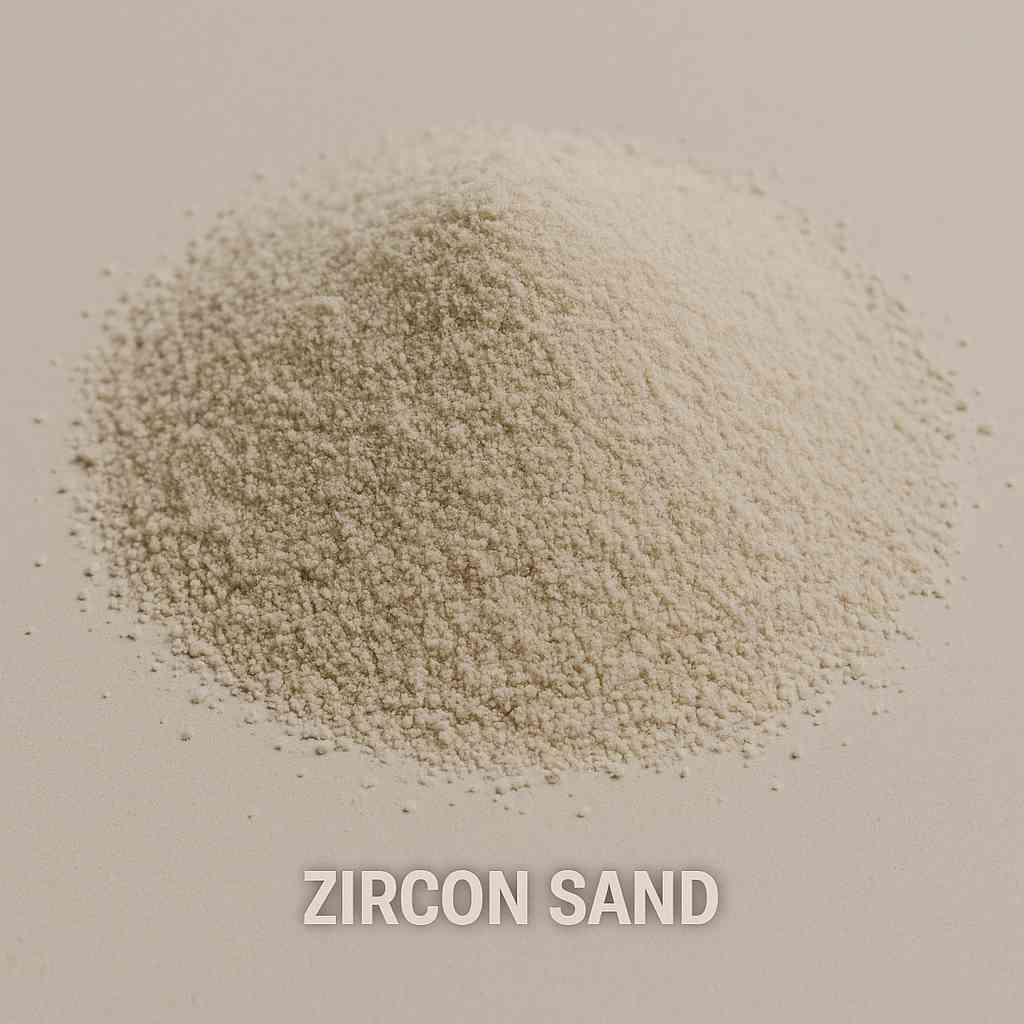
This image shows zircon sand prepared for use in various industrial processes.
Here’s a little extra: because of these benefits, global demand for zircon sand continues to rise, especially in regions investing in infrastructure and advanced ceramics.
What Are the Health Risks of Radiation in Zircon Sand?
Natural radioactivity in zircon sand comes from trace amounts of uranium and thorium. While these amounts are small, daily exposure in large-scale processing can pose health risks if not managed.
You might be wondering how serious this really is: the radiation exposure from zircon sand is typically low but can add up over time, especially if there’s dust in the air.
Let’s dig into these risks:
● Inhaled dust containing radioactive particles can settle in the lungs and stay there, creating a source of internal radiation.
● Skin contact with high concentrations of zircon sand can lead to surface exposure, though this risk is lower than inhalation.
● Long-term exposure to radioactive dust may increase the risk of lung issues or other health concerns.
To get a sense of scale, here’s how zircon sand’s typical dose rates compare to background levels:
Material | Dose Rate (μSv/h) |
---|---|
Background radiation | 0.1–0.2 |
Zircon sand (industrial grade) | 0.2–0.7 |
These numbers come from global studies, including European and Asian workplaces, and they show why firms need to watch exposure carefully. Companies in the Middle East, Africa, and South America also report similar ranges.
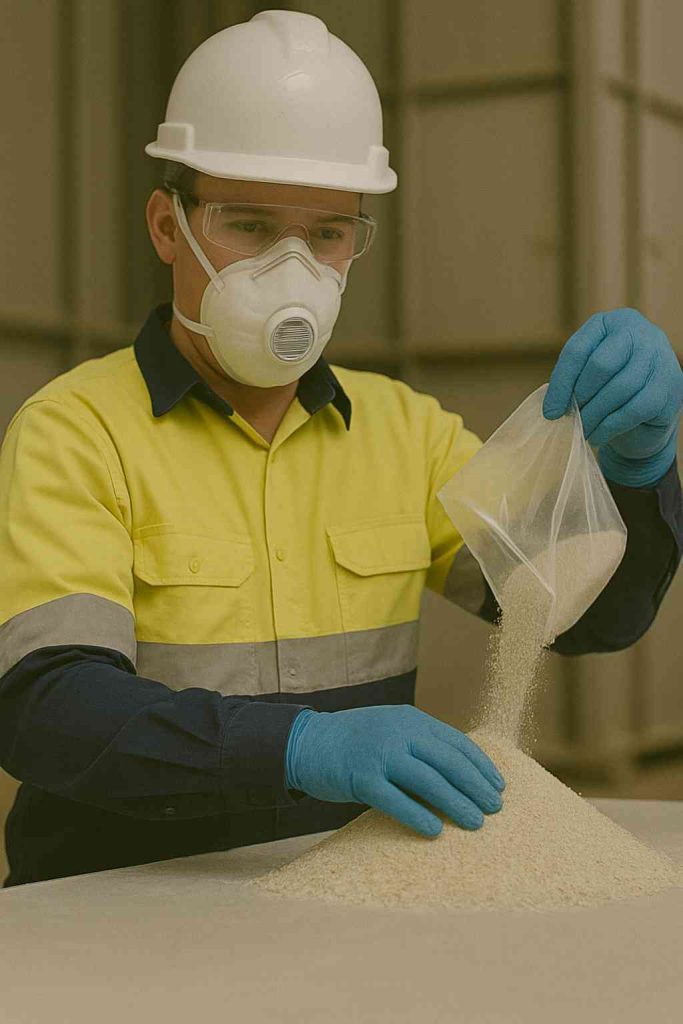
This image shows a worker safely handling zircon sand with protective equipment.
How is Radiation Exposure from Zircon Sand Measured?
Here’s a fact worth knowing: measuring radiation in the workplace is essential for staying safe and staying legal. Radiation exposure monitoring begins with personal dosimeters. These track how much exposure a worker receives in real time. Workplaces also measure airborne dust, since inhalation is the biggest risk.
Here’s a quick list of common monitoring methods:
● Personal dosimetry: Workers wear small devices that measure the dose they get each day.
● Air sampling: Air pumps pull in dust samples so labs can test for radioactive particles.
● Surface contamination checks: Swabs and gamma probes help find radioactive dust on surfaces.
Table: Workplace Radiation Monitoring
Monitoring Type | What It Measures | Tool Used |
---|---|---|
Personal exposure | Total dose received | Dosimeters, badges |
Airborne particles | Dust and fine particle content | Air samplers, filters |
Surface radioactivity | Contamination on equipment and floors | Wipe tests, handheld meters |
Interpreting these numbers is just as vital. For instance, if air sampling shows higher than normal levels, companies must act fast. They might adjust ventilation or limit work times in those areas.
Some firms have shared case studies where monthly testing caught unexpected spikes in airborne dust. These audits showed the need to upgrade ventilation systems. Such real-world examples help others see why proactive monitoring matters.
How Can Companies Manage Radiation Risks?
Here’s the deal: firms can cut risks with a mix of smart equipment and good practices. Engineering controls like dust collectors and wet cutting systems keep radioactive particles from getting airborne. These are some of the most effective tools in reducing inhalation risks.
● Engineering controls: Local exhaust fans, dust extraction systems, and wet cutting reduce dust in the air.
● PPE: Respirators and protective suits stop workers from inhaling or contacting dust.
● Work practices: Rotating workers, limiting time spent in dusty zones, and using enclosed systems help too.
Table: Key Risk Management Practices
Control Type | Example Solutions | Impact |
---|---|---|
Engineering | Dust collectors, water suppression | Keeps dust out of the air |
PPE | Half-mask respirators, full suits | Personal protection |
Administrative practices | Rotation schedules, restricted areas | Lower exposure for workers |
Real-world examples show the value of these controls. For example, a ceramics plant in Italy saw dust levels drop by 60% after adding water-based cleaning systems. In foundries in India, using local exhausts in high-dust areas helped meet exposure limits.
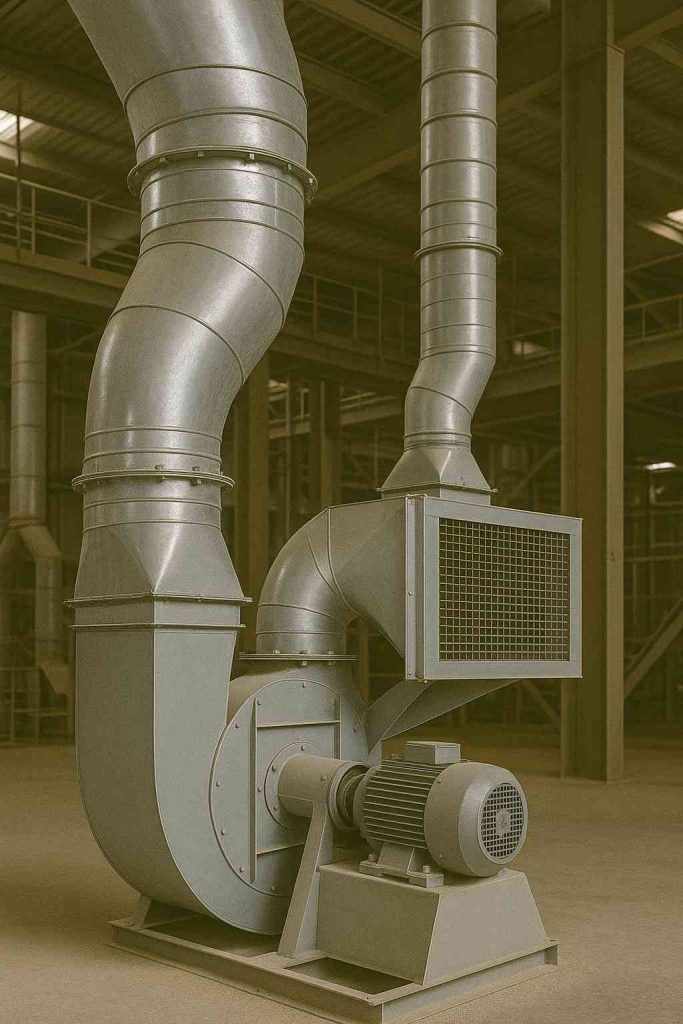
This image shows an industrial ventilation system used to reduce airborne dust.
What Are the Best Practices for Safe Handling?
Safe handling of zircon sand calls for careful methods. You might be asking: what exactly does that look like? Best practices start with how zircon is stored and handled. Sealed bags and dedicated storage zones stop dust from spreading. Wetting the material also cuts airborne particles.
● Use sealed, labeled bags for storage to limit spills.
● Keep work areas clean with wet mopping instead of sweeping.
● Train workers on the proper way to open and empty bags to cut down dust clouds.
● Create clear waste disposal steps to avoid accidental spread.
Table: Proven Safe Handling Methods
Step | Best Practice | Outcome |
---|---|---|
Storage | Sealed bags, dedicated rooms | Less chance of dust escaping |
Handling | Wetting down material, slow pouring | Cuts down dust in air |
Cleanup | Wet cleaning, industrial vacuums | Cleaner work zones |
Disposal | Marked containers, sealed bins | Safer waste removal |
Common mistakes include dry sweeping dusty floors or using compressed air for cleaning, both of which make things worse. Training programs help workers understand these risks and avoid them.
Firms also track near-misses or minor spills as part of a broader safety plan. This data shows managers where they can improve processes to keep everyone safe.
What Are the Regulatory Requirements?
Across countries, regulatory agencies set strict rules for handling zircon sand. Here’s the key point: firms must follow these rules to stay safe and stay in business.
● Agencies like OSHA (US) and ICRP (international) create exposure standards.
● In the EU, the Basic Safety Standards Directive requires companies to manage exposure and report on safety programs.
● Asian and South American regulations are often similar, though with country-specific updates.
Some regions also require licenses for handling large volumes of zircon sand. This can include environmental permits and worker health reports. Firms in Africa and the Middle East often find licensing straightforward but must stay current with updates.
Table: Key Regulatory Frameworks
Region | Main Regulatory Agency | Key Requirement |
---|---|---|
US | OSHA | Exposure limits, training, records |
Europe | Basic Safety Standards (EU) | Monitoring, reporting, licensing |
Asia-Pacific | National health agencies | Regional exposure limits, reporting |
South America | Varies by country | Regional exposure limits, licenses |
Regional differences can create challenges. For example, a manufacturer in Brazil may face different reporting forms than one in China. That’s why many firms work with local experts to stay compliant.
What Are the Environmental Considerations?
Handling zircon sand isn’t just about worker safety. It’s about taking care of the environment too. Here’s what’s worth knowing: poor handling can harm ecosystems through dust and waste run-off.
Mining itself can damage habitats, so responsible firms plan site restoration early. Dust emissions from handling zircon can also settle in local soil and water, which can affect plants and animals.
To reduce these risks, companies:
● Use dust suppression systems at mining and processing sites.
● Treat wastewater to remove fine particles before release.
● Recycle zircon sand where possible instead of sending it to waste.
Table: Environmental Protections
Challenge | Key Practice |
---|---|
Dust impact | Wetting, dust collectors |
Water run-off | Closed-loop water systems |
Habitat disruption | Post-mining land reclamation |
Examples include mining firms in Australia replanting native species and using treated wastewater for dust control. In Europe, companies monitor soil health around their plants to protect local farming.
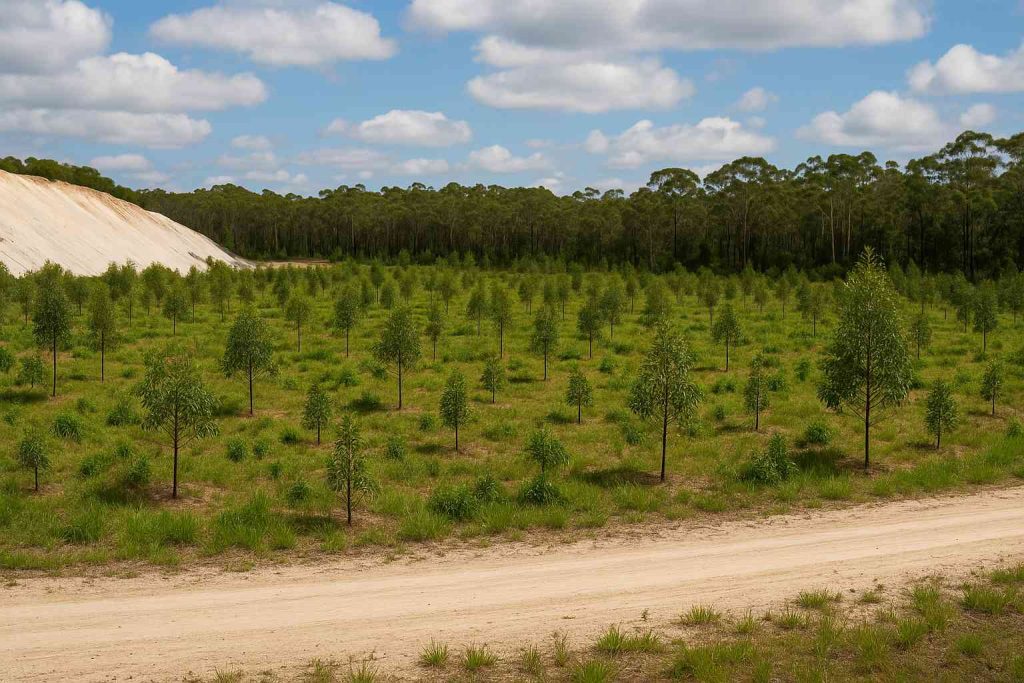
This image shows how some mining firms restore land after zircon extraction to help local habitats.
Caring for the environment also supports relationships with regulators and local communities. It’s part of how modern firms build trust and keep doing business in competitive markets.
Conclusion
To bring it all together, this article provided a clear view of the radiological risks linked to zircon sand and practical steps for managing them. It covered how zircon sand is used, where radiation comes from, how firms can control exposure, and what global regulations say. At Global Industry, we help teams turn knowledge into action with practical support and technical expertise. Ready to strengthen your safety program? Contact us today for tailored advice and regulatory compliance assistance. Let’s work together to build safer, more reliable workplaces for everyone.
FAQ Section
Q1: How dangerous is the radiation in zircon sand?
Radiation levels in zircon sand can vary, and while they may be low in many cases, improper handling can pose health risks for workers. Prolonged exposure to elevated radiation levels can lead to serious health concerns, which is why it’s essential to implement proper safety practices and monitoring protocols in every workplace that handles zircon sand.
Q2: Can workers handle zircon sand safely?
Yes, workers can handle zircon sand safely by adhering to established safety protocols. Using appropriate personal protective equipment (PPE) such as respirators, protective suits, and gloves significantly reduces exposure risks. Additionally, employing effective ventilation systems, conducting regular clean-up procedures, and providing training on safe handling practices can all contribute to maintaining low worker exposure.
Q3: Are there any legal exposure limits for zircon sand?
Yes, regulatory agencies worldwide have established clear legal exposure limits for zircon sand. These limits are based on potential health risks and serve to ensure worker safety. It is crucial for firms to monitor and document their exposure levels diligently to comply with these regulations, thereby ensuring the protection of their employees and remaining within legal boundaries.
Q4: How is zircon sand different from other industrial minerals?
Zircon sand is unique compared to most other industrial minerals due to its higher natural radioactivity levels. This inherent radioactivity is primarily due to the presence of uranium and thorium within the zircon mineral structure. As a result, zircon sand requires more stringent handling rules, regular safety testing, and monitoring to mitigate potential health risks associated with radiation exposure.
Q5: What should companies do to stay compliant with safety regulations?
To ensure compliance with safety regulations regarding zircon sand, companies should conduct regular reviews of applicable safety standards and guidelines. Training employees on safe handling techniques is essential to raise awareness and minimize risks. Additionally, implementing routine monitoring of air and dust levels demonstrates a commitment to maintaining a safe work environment. Regular safety audits and assessments will further enhance workplace safety and help firms adhere to legal requirements.