You’re probably dealing with the challenge of sourcing zircon sand while managing quality and costs. Zircon sand plays a crucial role in several industries—ceramics, foundries, and refractories. Yet understanding how this mineral moves from the mine to the final product can be difficult. This article aims to give you a clear, practical view of each step in zircon sand’s journey, so you can make smart, informed decisions for your business. My years of experience helping procurement teams with raw materials and market trends have taught me what works and what to watch for. Let’s start at the beginning.
What is Zircon Sand and Its Role?
Zircon sand is a naturally occurring mineral composed primarily of zirconium silicate (ZrSiO₄). This mineral is particularly valued across various industries due to its unique properties, including exceptional hardness, high melting point, and remarkable heat resistance. It plays a critical role in the manufacturing of various products that require durability and resilience under temperature extremes.
Zircon sand serves as a key raw material in several sectors. For example, in the ceramics industry, it is used to create glazes that not only enhance aesthetic appeal but also improve the overall strength and resistance to thermal shock of ceramic products. In foundries, zircon sand is integral in the production of molds and cores, providing the necessary precision and heat resistance needed to shape molten metals without degrading. Additionally, in the refractory industry, zircon sand is blended with other materials to produce bricks and linings that can withstand extreme temperatures and corrosive environments, making it ideal for applications in furnaces and kilns.
Here’s the deal—if you’re considering buying zircon sand, it’s essential to be aware of the following key facts:
- Composition: Zircon sand contains approximately 65–85% zirconium silicate, which indicates its high purity level. Higher zircon content translates to better performance and durability in end products.
- Grain Sizes: Zircon sand is available in various grain sizes, ranging from fine to coarse. Finer grains yield smoother ceramic finishes, while coarser grains may be better suited for other applications, such as mold-making in foundries.
- Thermal Stability: With an impressive melting point of around 2,540°C, zircon sand stands up to extreme temperatures. This characteristic is crucial for applications that involve high thermal stress, ensuring that products maintain their integrity and functionality.
Property | Typical Range | Importance for Buyers |
---|---|---|
Zircon content | 65–85% | Higher content leads to better performance |
Grain size | 30–200 µm | Different sizes cater to various uses |
Melting point | ~2,540 °C | Excellent for high-temperature applications |
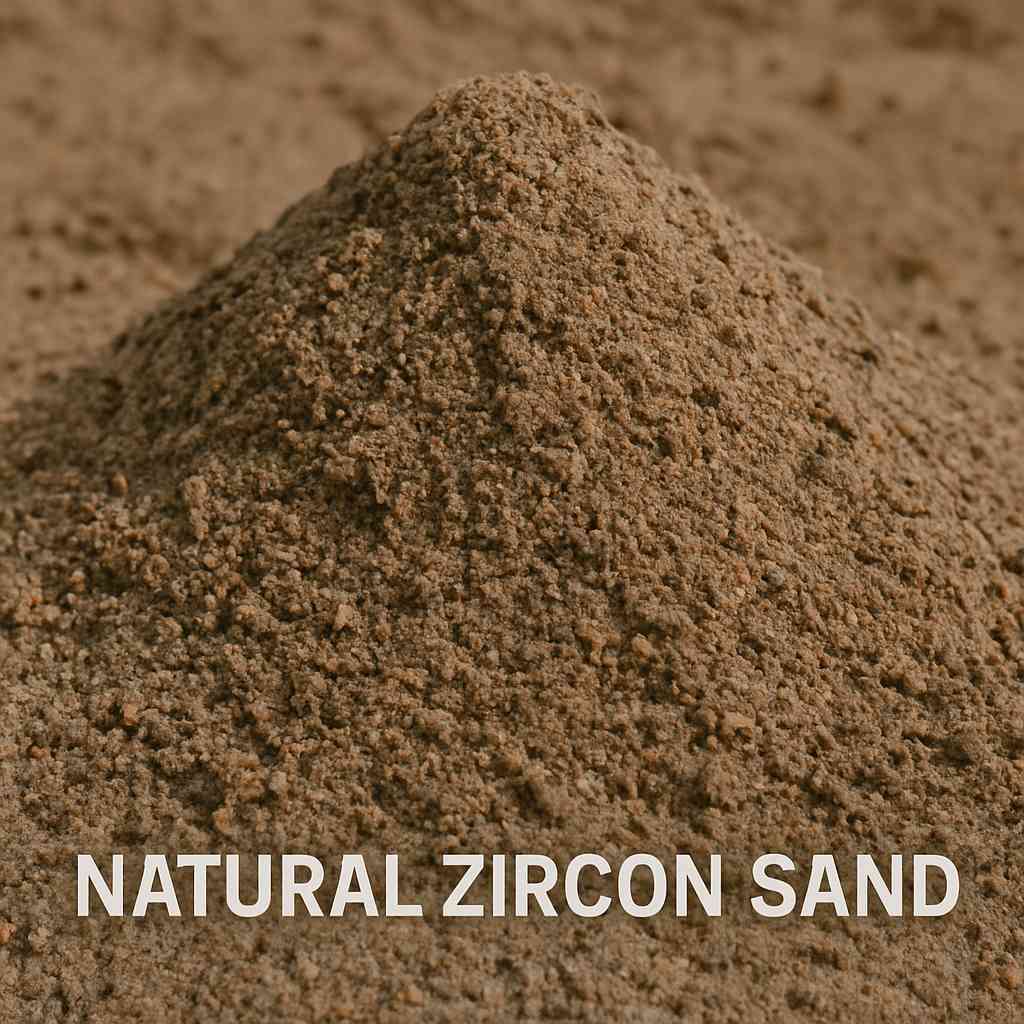
Manufacturers consistently choose zircon sand for its reliability and resistance to breakdown under harsh conditions. From vibrant, glossy tiles to precision metal molds used in intricate engineering, zircon sand is instrumental in achieving the desired quality and performance across a wide range of applications.
How is Zircon Sand Mined?
Zircon sand is usually found in beach and river deposits, where natural weathering processes concentrate this valuable mineral among other sediments. The mining method used can vary widely based on the geographical location and the specific characteristics of the deposit.
You might be wondering—what’s the best way to get this mineral? Here are the primary methods employed in different regions:
● Dredging (Australia)
In Australia, which is a leading producer of zircon, miners commonly use dredging techniques. Large, specialized machines are deployed to extract sand from shallow water bodies. This method allows for efficient extraction and immediate separation of zircon from other minerals right at the source. Dredging can be environmentally invasive, as it may alter local aquatic ecosystems, but it is also highly effective for maintaining consistent production levels.
● Dry Mining (South Africa)
In South Africa, miners utilize dry mining techniques. This involves heavy machinery digging up sand from land-based deposits. Once extracted, the sand is transported to processing plants for cleaning. Although this method is less intrusive to water habitats, it can lead to dust generation and soil disturbance issues, which necessitate careful management to minimize environmental impact.
● River Mining (Indonesia)
In Indonesia, river mining presents a smaller-scale but significant source of zircon sand. This technique often relies on manual labor or lighter machinery to extract sand from riverbanks. While it contributes to local economies, river mining can cause noticeable changes to the river’s flow and sediment dynamics, which may affect both ecosystems and local communities.
Mining Method | Country | Environmental Considerations |
---|---|---|
Dredging | Australia | Water usage, impact on local habitats and fauna |
Dry mining | South Africa | Dust generation, soil disturbance, possible degradation of land |
River mining | Indonesia | Alterations to water flows, potential impact on surrounding ecosystems |
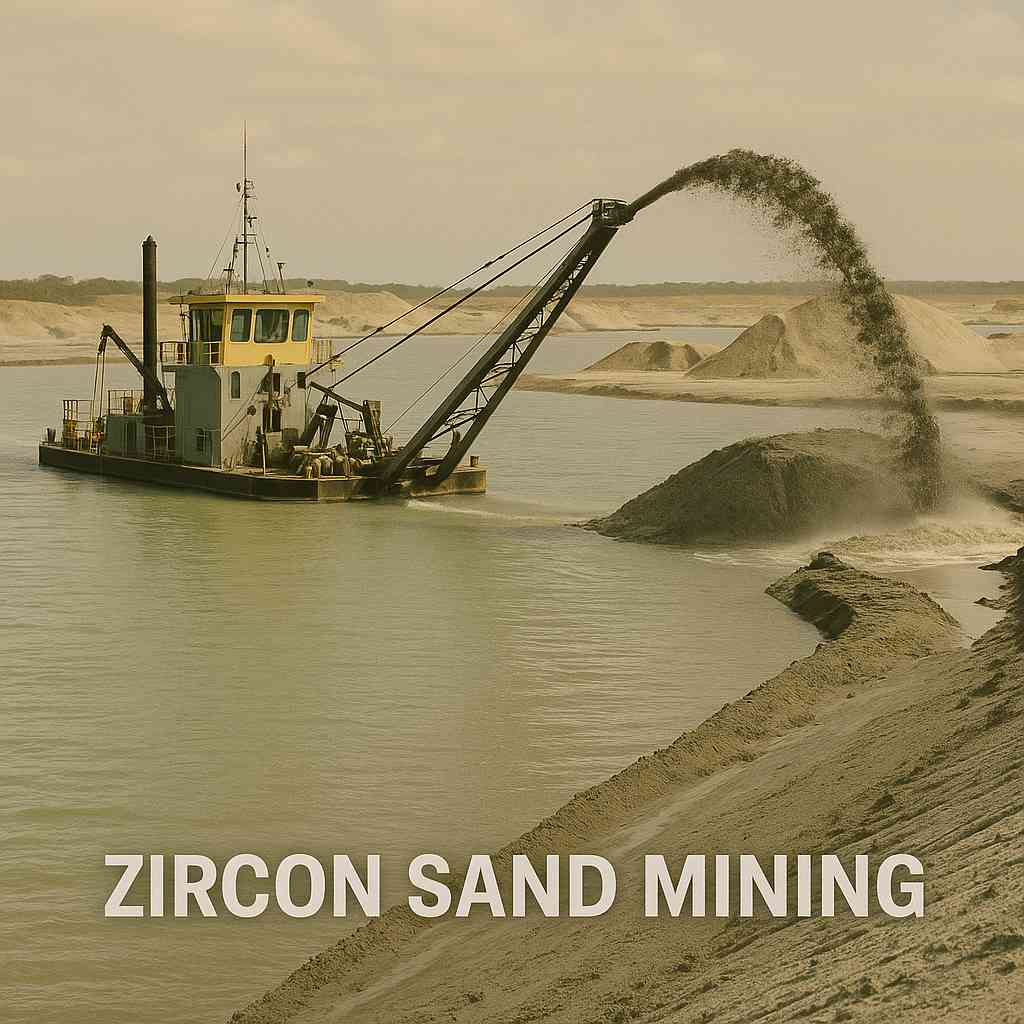
Good practices and adherence to environmental regulations are critical to reducing the negative impacts of mining activities. This may include conducting environmental impact assessments, minimizing habitat disruption, and restoring mined areas post-extraction. Moreover, responsible mining companies often engage with local communities to address their concerns and ensure fair benefit-sharing from mineral resources.
Through sustainable mining practices, the extraction of zircon sand not only meets industry needs but also supports ecological balance and community welfare.
What Happens During the Processing Stage?
Mining is just the first step in the journey of zircon sand. Once it is extracted from the ground, it undergoes a meticulous processing stage designed to purify the mineral and eliminate any unwanted materials. This step is pivotal; it ensures that the zircon sand meets high-quality standards, which is essential for its performance in various applications.
Zircon Sand Processing: The Steps Involved
The processing of zircon sand involves several key steps, each aimed at enhancing the purity and quality of the final product. It is important to note that the methods and technologies employed in this stage can greatly influence the properties of zircon sand.
- Gravity Separation: This initial step utilizes the difference in density between zircon and other minerals. Heavy minerals like zircon are separated from lighter ones through equipment such as spirals and shaking tables. The effectiveness of this method depends on the right adjustments regarding water flow and sand feed rate. Highly efficient gravity separation can yield 70-80% of the zircon content, making it an essential step in the process.
- Magnetic Separation: Following gravity separation, the next phase involves magnetic separators to remove iron-based minerals. Zircon is non-magnetic, which means that magnetic separation effectively extracts iron impurities that may negatively affect the quality of the zircon sand. This step typically results in an impressive recovery rate of 85-90% of the zircon sand, significantly purifying the material.
- Electrostatic Separation: The final cleanup involves electrostatic separation, a highly effective method for achieving optimal purity. This process utilizes electrical charges to separate lighter minerals and any remaining contaminants from the zircon. The expected yield in this stage can reach as high as 90-95%, ensuring that the zircon sand is of the highest possible quality before it is packaged and shipped.
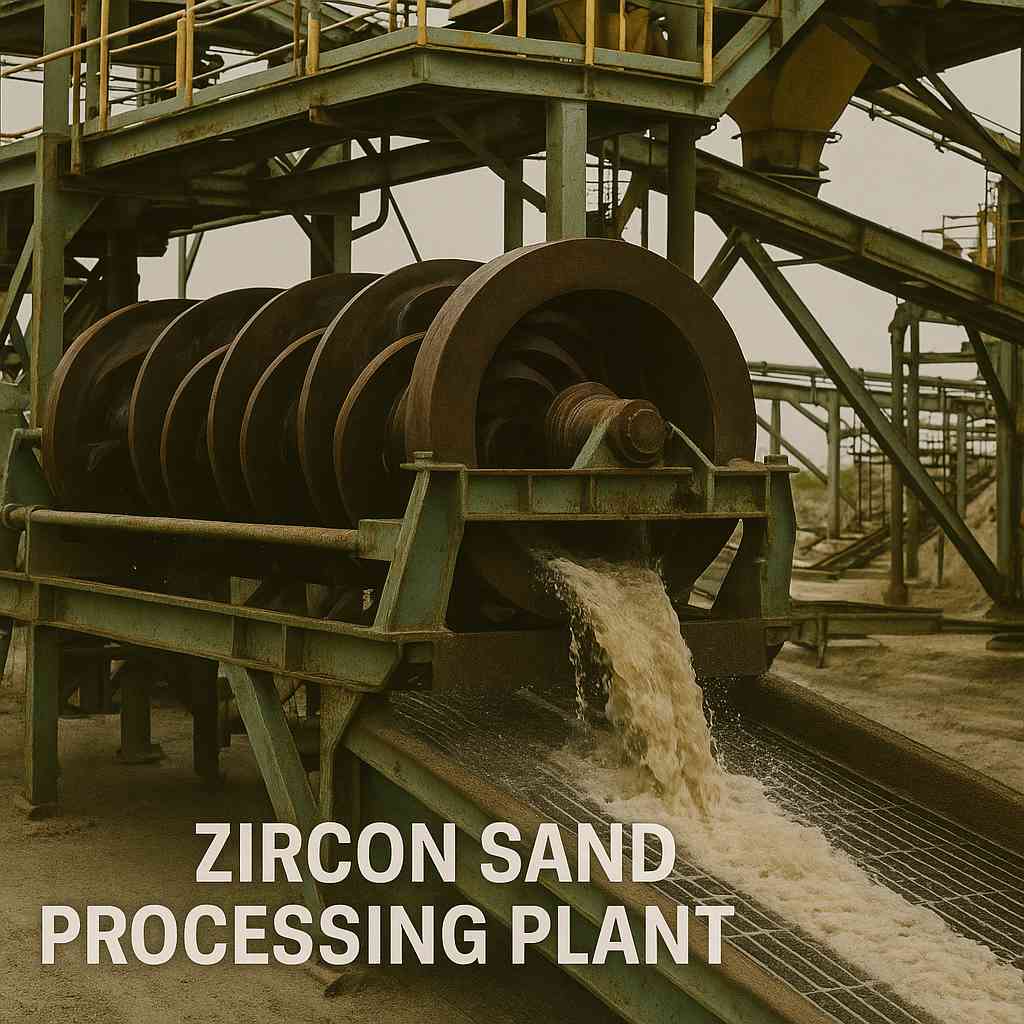
The Importance of Quality Control
Throughout these processing stages, rigorous quality control measures are implemented to monitor the purity and consistency of the zircon sand. This includes laboratory testing for zircon content, grain size distribution, and the presence of impurities. High-quality zircon sand not only improves the performance of end products but also boosts the reputation of manufacturers relying on this crucial material.
In conclusion, the processing stage is where most of the value is created. Clean, consistent zircon sand translates into superior products, ensuring that industries can rely on the material for demanding applications. A thorough understanding of these steps empowers buyers and manufacturers alike to make informed decisions about sourcing and quality assurance.
This stage is where most of the value is created. Clean, consistent zircon sand means better products down the line.
How Does Transportation Affect Zircon Sand Quality?
Clean zircon sand still needs to be transported efficiently to factories and buyers around the globe. The handling and conditions during shipping and storage play a crucial role in determining whether the sand maintains its quality when it reaches its destination.
Here’s the thing—poor handling can quickly turn a valuable commodity into a costly waste.
● Moisture Exposure: If zircon sand becomes wet during transportation, it can clump together, creating hard aggregates that are difficult to work with. Clumped sand can lead to inconsistent product qualities and trouble during processing in factories. To counter this problem, using sealed bags or containers that are water-resistant can significantly reduce the risk of moisture infiltration. Additionally, monitoring the storage conditions, particularly during transit, is vital to ensure that the environment remains dry.
● Dust Loss: Dust is another significant concern. If packaging is not adequately sealed, fine particles of zircon sand can escape into the air during transportation. This not only represents a loss of material but also poses a challenge to maintaining quality, as the remaining sand may become enriched with larger, less desirable grains. To mitigate dust loss, companies should utilize containers specifically designed to keep fine materials contained and minimize the risk of spillage.
● Long Shipping Times: Prolonged shipping times can lead to variations in moisture levels within the sand, especially if the product is stored in less-than-ideal conditions. Fluctuations in humidity can cause fines to clump together or can even lead to chemical changes that affect the sand’s properties. Planning logistics effectively, such as scheduling tighter shipping windows and using climate-controlled transportation when necessary, helps in maintaining the integrity of the material throughout its journey.
Summary Table
Issue | Possible Effect | How to Handle It |
---|---|---|
Moisture exposure | Clumping, waste | Use sealed bags, covered storage |
Dust loss | Less material, poor quality | Use containers that keep dust in |
Long shipping times | Moisture swings, fines loss | Tight scheduling, good storage |
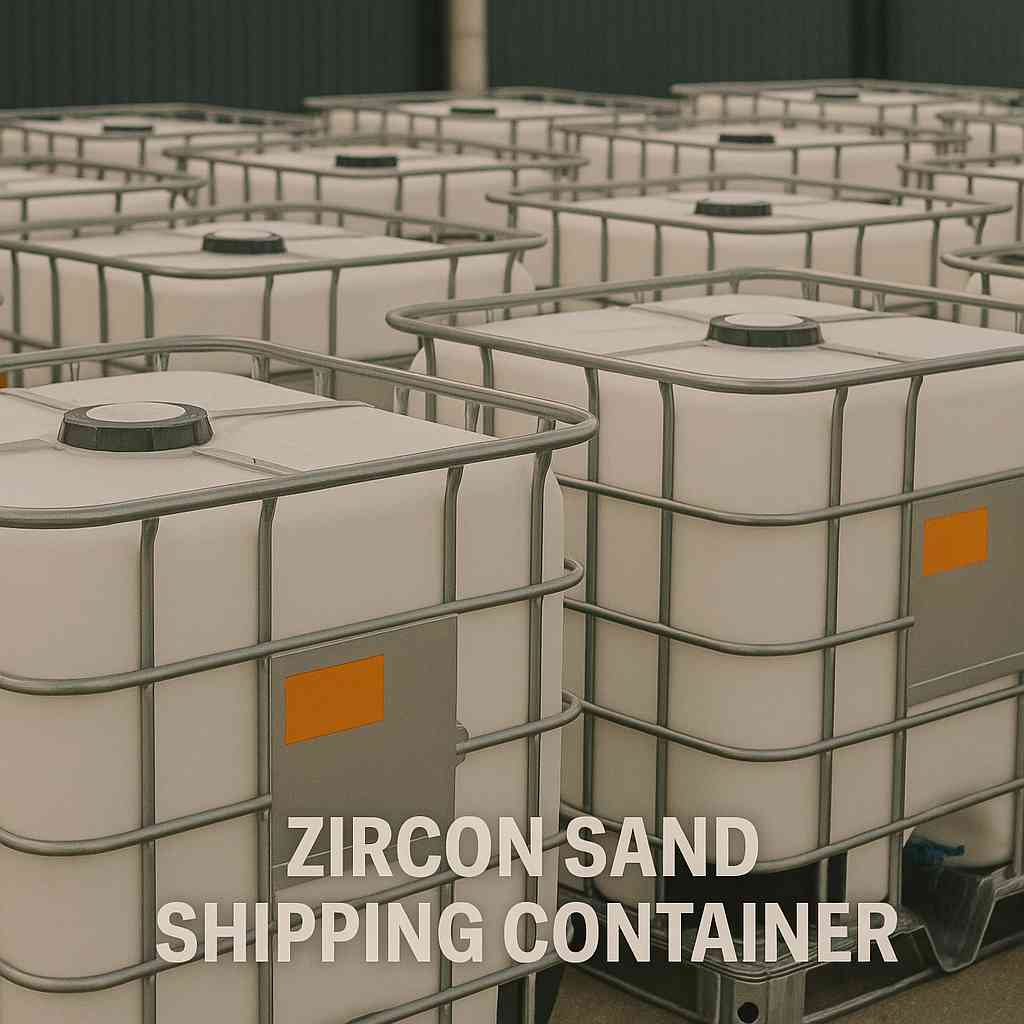
By prioritizing good transportation practices, companies can significantly reduce waste and maintain high-quality standards. This attention to detail not only leads to fewer complaints from end users but also contributes to overall cost-effectiveness in the supply chain. Ultimately, ensuring that zircon sand arrives in optimal condition enhances production efficiency and supports the reputation of manufacturers who rely on this essential raw material.
How is Zircon Sand Used in Manufacturing?
When zircon sand finally gets to the factory, it’s put to work in many ways. In ceramics, it’s used to make bright, smooth glazes. In foundries, it’s part of the molds that shape hot metal. And in refractories, it’s blended into bricks that can handle extreme heat.
Here’s what you should know—each use has its own needs.
● Ceramic makers want fine grains and low iron for smooth finishes.
● Foundries need controlled sizes so the mold shapes stay precise.
● Refractories mix zircon with other minerals to keep bricks from breaking.
Use | Key Specs | Typical Problems |
---|---|---|
Ceramic glazes | Fine grains, low iron | Streaks or cloudy finishes |
Foundry molds | Consistent grains | Bad mold shapes, rough surfaces |
Refractory bricks | Blend with alumina | Cracking under heat |
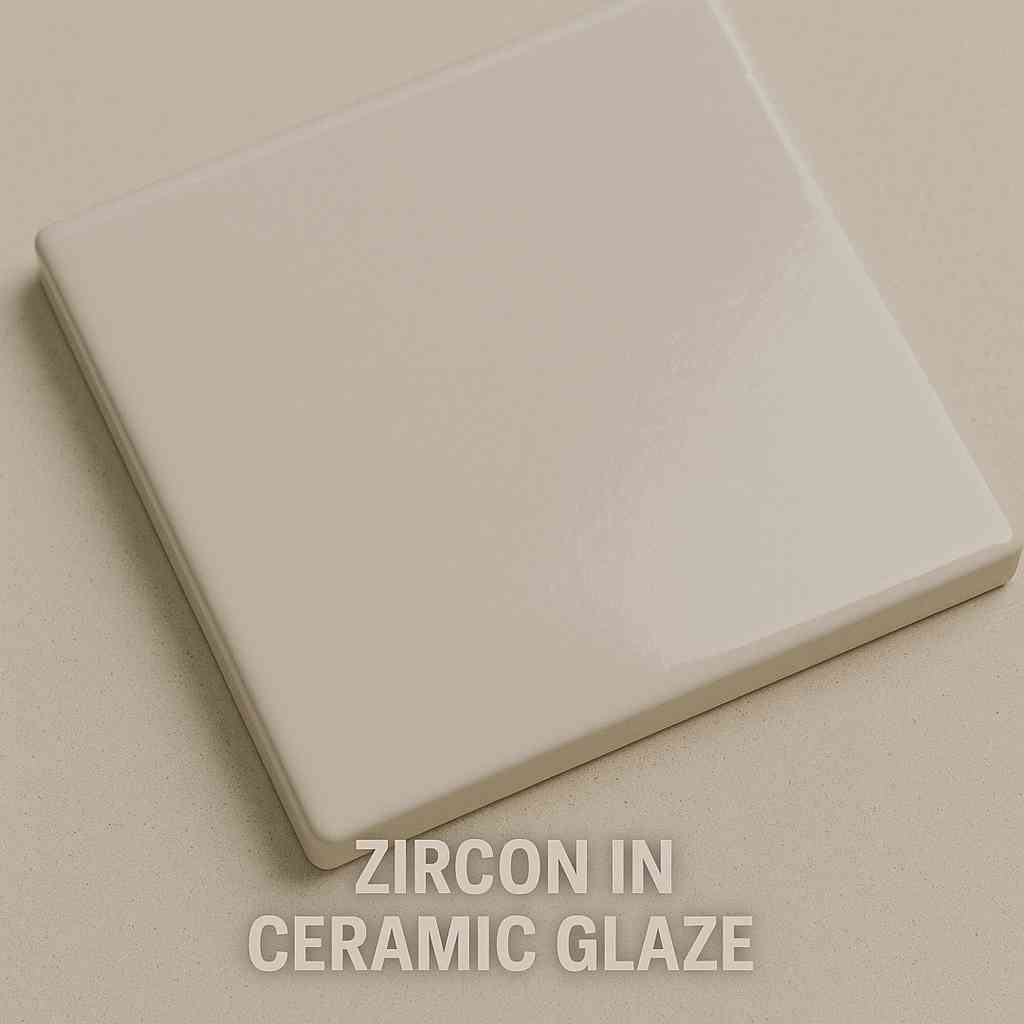
The key is matching the sand you buy to the job you’re doing. Getting it wrong can mean wasted money and more headaches later.
What Are the End-of-Life Considerations for Zircon Sand?
When zircon sand’s job is done, it can either be reused or thrown out. Some industries can reclaim sand by heating it and removing old binders. Others might crush used materials and add them to new bricks or molds.
You might be thinking—can we save money by reusing this sand?
● Foundry sand is often reclaimed by burning off binders and reusing the clean grains.
● Used bricks and refractory parts can be crushed and added back into new products.
● If the sand is contaminated with heavy metals or other junk, it has to be thrown away safely.
Waste Type | Can Be Reused? | Disposal Rules |
---|---|---|
Spent foundry sand | Up to 95 % reusable | Reclaim or landfill |
Old bricks | Crushed, reused | Often reused locally |
Contaminated sand | Hard to reuse | Must follow disposal codes |
Recycling helps reduce costs and keeps waste out of landfills. But it’s only possible if you handle the sand the right way from the start.
How Do Market Trends Influence the Zircon Sand Life Cycle?
You can’t forget that zircon sand is a global product. Prices and supply chains change fast. If you’re not watching the market, you might get caught paying more or not having enough.
Here’s what to watch—markets move fast.
● Demand from China and Europe can cause prices to jump.
● New mining projects can push prices down.
● Shipping costs and currency changes can affect what you pay.
Market Driver | Effect on Buyers | Smart Strategy |
---|---|---|
High demand in Asia | Price rises | Build relationships with miners |
New mines in Africa | Possible price drops | Monitor new projects |
Currency changes | Cost changes | Hedge currency or diversify sourcing |
Smart buyers don’t just watch prices—they build relationships with good suppliers and stay ahead of these shifts.
Conclusion
This article has provided a comprehensive overview of the life cycle of zircon sand, highlighting the intricate journey it takes from extraction to its final applications. Each step in this process, from mining and processing to transportation and usage, plays a critical role in determining the quality and effectiveness of the final product. Understanding these stages not only helps businesses streamline their operations but also empowers them to make more informed purchasing decisions that can significantly impact their bottom line.
At Global Industry, we recognize the complexities involved in sourcing zircon sand, and we are dedicated to offering our expertise to help you navigate these challenges. By staying informed about market trends and maintaining strong relationships with reliable suppliers, you can secure the best quality zircon sand for your production needs while minimizing costs.
As you consider your sourcing strategies, remember that a deep understanding of the zircon sand life cycle will enable you to mitigate risks, optimize efficiency, and ultimately enhance the performance of your products. For trusted sourcing and a steady supply of high-quality zircon sand, reach out to us today and let us support your business in achieving its goals.
FAQ
Q1: Where is most zircon sand sourced from?
Most zircon sand comes from Australia, South Africa, and Indonesia. These countries have extensive mineral-rich deposits and well-developed mining operations. Australia is the top global producer, known for its high-quality zircon sand. South Africa also has large reserves and significant export capabilities. Indonesia’s deposits support smaller-scale mining with steady production for Asian markets.
Q2: Is zircon sand safe to handle?
Yes, zircon sand is generally safe to handle if you manage dust and keep it dry. In factories and warehouses, the main risk comes from inhaling fine dust, so proper ventilation and sealed storage containers are key. Workers should wear masks in dusty areas to avoid inhalation. When stored and transported in sealed bulk bags, zircon sand poses minimal health or safety risks for your team.
Q3: How does zircon sand affect the environment?
Mining zircon sand can change the environment by disturbing land and water systems. However, today’s regulations and responsible mining practices help limit damage. Companies are required to monitor water use and manage dust to protect local ecosystems. Many mines also invest in land rehabilitation projects that restore habitats once mining ends. For buyers, working with responsible suppliers means supporting these efforts and meeting compliance rules.
Q4: Can zircon sand be recycled?
Yes, zircon sand can be recycled in many industrial processes. In foundries, old sand from metal casting can be reclaimed by heating it to remove binders, letting you reuse most of it. In ceramics and refractories, some used material can be crushed and added to new bricks or glazes. Recycling cuts down on waste and can save money over time. But it requires careful handling and cleaning to ensure the recycled sand meets product standards.
Q5: What industries mainly use zircon sand?
Zircon sand is widely used in industries that need materials to stand up to high temperatures and wear. Ceramic tile makers use it to create bright, durable glazes. Foundries rely on it to make precise molds that shape molten metal. The refractory industry uses it in bricks and linings that can handle intense heat in kilns and furnaces. Across these sectors, zircon sand provides consistent performance and long-lasting results.