Zircon sand plays a central role in tile fabrication, acting as a key ingredient that contributes to both the aesthetic and functional quality of ceramic tiles. As the demand for tiles that are durable, visually appealing, and cost-efficient continues to rise, manufacturers increasingly turn to zircon for practical solutions. Its versatility and unique properties allow it to meet the stringent requirements of modern production techniques.
In this article, we will delve into how zircon sand functions in the ceramic tile production process. We will explore the numerous benefits it provides, both during manufacturing and in the finished product. Furthermore, we will offer insights into how your sourcing strategy can be enhanced by understanding the industrial relevance of zircon.
Backed by comprehensive technical properties and real-world applications, this guide aims to equip purchasing managers, engineers, and ceramic production planners with the clarity and confidence needed to make informed decisions. By understanding the value of zircon sand, industry professionals can optimize production processes and improve the quality of ceramic tiles.
WHAT IS ZIRCON SAND?
Zircon sand, also known as zirconium silicate (ZrSiO₄), is a mineral extracted from heavy mineral sands, predominantly found in countries like Australia, South Africa, and the United States. The extraction process involves separating zircon from other minerals, such as ilmenite and rutile, using methods like gravity separation and magnetic filtration. This meticulous refinement prepares zircon for various industrial applications, including ceramics.
One of the most remarkable characteristics of zircon is its durability and chemical stability. Compared to many other naturally occurring silicates, zircon stands out due to its ability to remain inert even at extreme temperatures, often exceeding 1,000°C. This property is essential for the ceramic tile industry, where firing processes demand resilience against high heat.
Geologically, zircon has a fascinating origin; it typically forms in igneous rocks and becomes redistributed through natural processes such as erosion and sedimentation. Its unique formation leads to mineral sand deposits that are rich in zircon, making it a highly sought-after resource. The refinement process is intricate and includes steps like electrostatic separation, which leverages differences in electrical conductivity to extract zircon grains effectively.
Key Properties of Zircon Sand
Excellent Chemical Resistance: Zircon maintains integrity when exposed to corrosive environments, enhancing the longevity of the final ceramic product.
High Melting Point: Zircon exhibits a melting point greater than 2,700°C, making it ideal for high-temperature applications.
Low Thermal Expansion: This characteristic helps minimize distortion during thermal processing.
Property | Typical Value |
---|---|
ZrO₂ + HfO₂ | ~66% |
SiO₂ | ~33% |
Moh’s Hardness | 7.5 |
Specific Gravity | 4.5–4.7 |
Melting Point | >2,700°C |
These properties make zircon particularly compatible with the high demands of tile firing processes, where maintaining mechanical integrity and aesthetic quality is paramount. Additionally, a visual inspection of processed zircon sand at ceramic-grade mineral facilities reveals its fine quality, underscoring its importance in tile production.
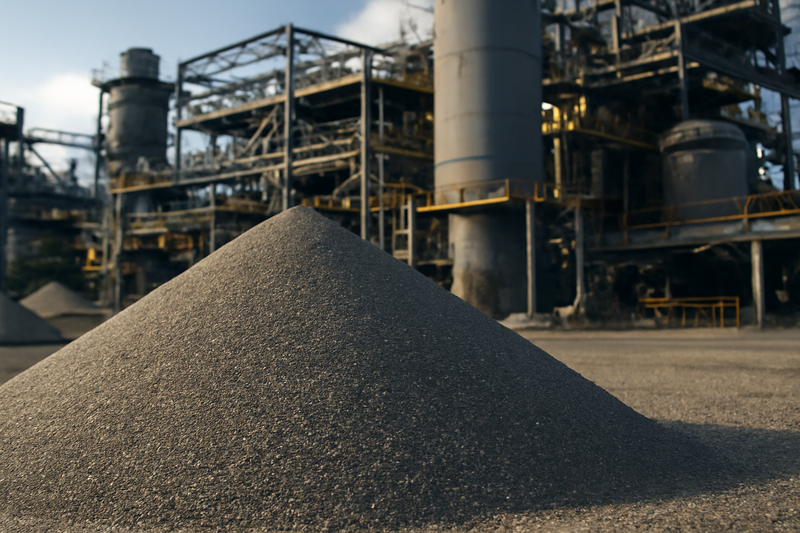
A close-up of processed zircon sand stored at a ceramic-grade mineral facility.
HOW IS ZIRCON SAND USED IN CERAMIC TILE MANUFACTURING?
In tile manufacturing, zircon sand is primarily used as an opacifier in glazes and as an additive in body formIn tile manufacturing, zircon sand serves multiple critical purposes. Primarily, it acts as an opacifier in glazes and a key additive in body formulations.
Opacifier Function
As an opacifier, zircon sand contributes to producing a bright, white, and uniform finish on ceramic tiles. This is essential for achieving the aesthetic qualities that consumers desire. Glazes enhanced with zircon exhibit increased opacity, leading to visually appealing surfaces.
Body Formulations
In the body of the tile, zircon improves thermal resistance. Its unique properties help stabilize the tile structure during the firing process, reducing the risk of shrinkage. This quality is crucial since consistent sizing is essential for ensuring tiles fit together correctly during installation.
Stabilizing Agent
During high-temperature firing, zircon acts as a stabilizing agent. Tiles infused with zircon maintain their shape and surface texture during the sintering process, which minimizes issues like cracking and warping. This reliability translates to fewer rejects and higher productivity, significantly impacting profitability in large-scale operations.
Benefits Summary:
- Predictable Quality: Zircon enables manufacturers to achieve predictable, high-quality finishes even under fast-firing production cycles, which is essential in modern production environments.
- Less Equipment Downtime: Its consistency reduces the need for frequent recalibration or tooling adjustments, streamlining workflows and enhancing operational efficiency.
In conclusion, zircon enhances product quality while optimizing the manufacturing process, making it an indispensable component in ceramic tile production.
WHY IS ZIRCON SAND IMPORTANT FOR TILE DURABILITY?
Tile durability is crucial in both residential and commercial applications, and zircon sand plays a significant role in enhancing this quality.
- Hardness: Zircon has a high Mohs hardness of 7.5, which means the tiles produced are less prone to scratches and wear. This hardness translates into longer-lasting surfaces that maintain their pristine appearance even under heavy foot traffic, making zircon-infused tiles especially appealing for high-use areas.
- Low Porosity: The addition of zircon contributes to denser tile bodies, which significantly reduces water absorption rates. Tiles with lower porosity are less vulnerable to moisture ingress, thereby minimizing the risks of mold growth and staining. This characteristic is vital for maintaining hygiene, particularly in areas like kitchens and bathrooms.
- Thermal Resilience: Zircon’s properties allow tiles to withstand high temperatures without deformation. In industries where tiles are subjected to rapid temperature changes, such as in kilns during firing, zircon helps maintain the structural integrity of the tile, reducing the chance of warping or cracking.
- Dimensional Stability: Maintaining shape and size after cooling is crucial for proper installation and fitting. Zircon enhances the dimensional stability of tiles, ensuring they remain flat and well-aligned, which contributes to a smoother overall aesthetic and functionality in flooring and wall installations.
Metric Comparison:
Metric | Without Zircon | With Zircon |
---|---|---|
Scratch Resistance | Moderate | High |
Water Absorption | ~3% | <0.5% |
Surface Strength | Low | High |
Breakage during firing | 5–7% | <1.5% |
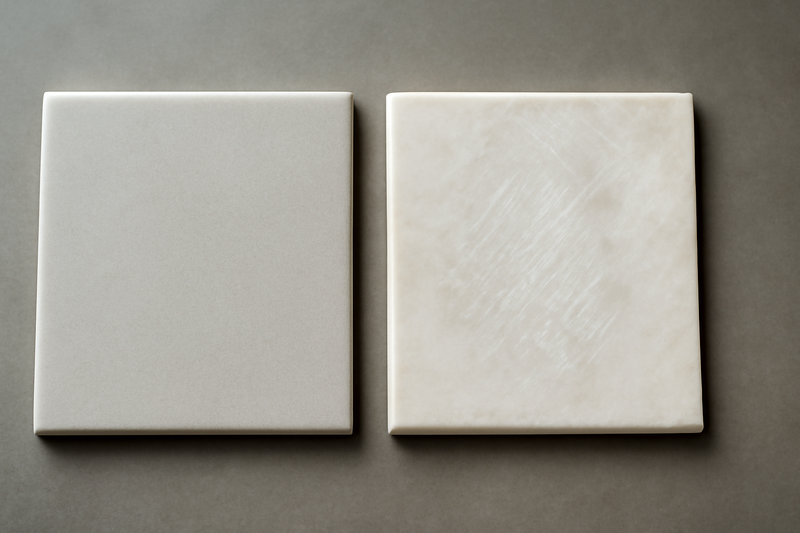
Two tiles after identical wear testing; left with zircon, right without—note the difference in surface quality.
Zircon not only prevents common issues such as dimensional changes and surface deterioration but also contributes to the overall longevity of tiles, making them an excellent investment. With these advantages, including enhanced durability qualities, zircon plays a central role in ensuring tiles perform well over time.
WHAT ARE THE BENEFITS OF USING ZIRCON SAND IN CERAMIC TILES?
Beyond durability, zircon influences a multitude of production and end-use factors that are essential to B2B buyers in the tile industry.
● Improved Yield: Zircon’s exceptional properties result in fewer rejects due to cracks or imperfections in the glaze. This translates to more efficient production processes and lower costs.
● Energy Savings: Tiles that contain zircon can endure quicker firing cycles without sacrificing quality. Faster cycles mean less energy consumption, ultimately leading to cost savings in kiln operation.
● Consistent Finish: The inclusion of zircon contributes to a higher gloss and uniformity across batches. A consistent finish is vital for manufacturers aiming to meet the aesthetic demands of consumers without compromising on production quality.
● Color Stability: Zircon enhances visual uniformity even under diverse lighting conditions. This characteristic is particularly advantageous for premium tile products which require vibrant and consistent colors.
● Raw Material Efficiency: By reducing shrinkage during the firing process, zircon allows for tighter control over the input materials. This efficiency means that manufacturers can optimize their raw material usage while maintaining product quality.
Benefit | Operational Effect |
---|---|
Fewer Defects | Reduced rework costs |
Better Finish | Enhanced marketability |
Thermal Control | Reduced kiln maintenance |
Yield Control | Higher first-pass quality rates |
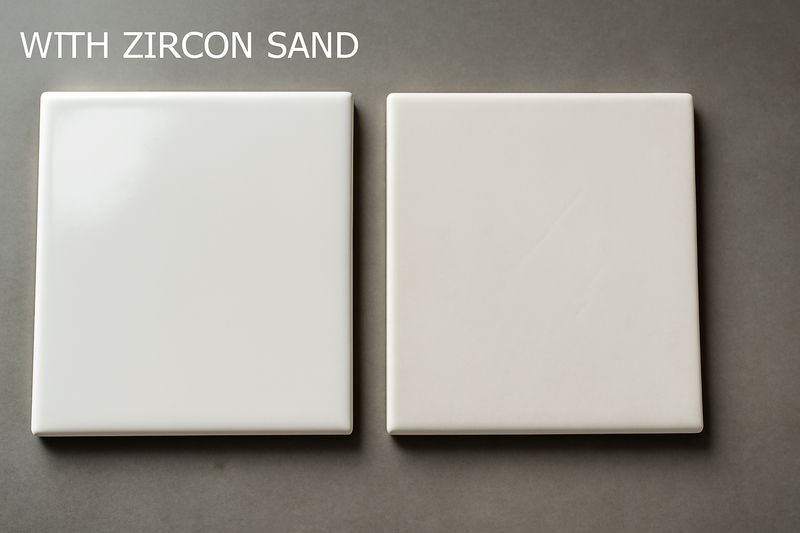
A side-by-side showing whiter, glossier tile produced with zircon compared to one without.
A side-by-side comparison vividly illustrates the aesthetic superiority of tiles produced with zircon, emphasizing whiter and glossier surfaces compared to those made without it. Ultimately, the integration of zircon into tile production processes not only enhances the finished product but also streamlines operational workflows, making it a strategic choice for manufacturers looking to thrive in a competitive marketplace.
HOW DOES ZIRCON SAND AFFECT TILE PERFORMANCE?
Zircon doesn’t just survive the kiln—it significantly enhances your product across multiple performance categories. Its contributions extend beyond mere survival during firing; they fundamentally improve the robustness and usability of the tiles in various settings.
- Chemical Resistance: Zircon’s inherent properties enhance the tiles’ resistance to acids and common household cleaning agents. This is particularly beneficial in environments such as kitchens and bathrooms, where tiles are frequently exposed to harsh substances.
- Aesthetic Consistency: Tiles infused with zircon maintain a high level of visual quality. This is critical for design-focused applications where aesthetics are paramount, helping manufacturers meet high customer expectations for appearance without compromising durability.
- Wear Resistance: Zircon-enhanced tiles perform exceptionally well under foot traffic, remaining intact longer over time. This durability not only extends the life of the tile but also improves customer satisfaction as maintenance needs decrease.
- Thermal Stability: Zircon’s ability to withstand high temperatures ensures that the tiles resist deformation, which is particularly important in locations where rapid temperature fluctuations are common. For instance, outdoor patios may see sudden changes in temperature, and zircon helps maintain tile integrity.
- Reduced Internal Stress: By absorbing and distributing heat evenly, zircon minimizes the development of internal stresses within the tile body. This characteristic mitigates one of the leading causes of structural failures in ceramics.
The following table summarizes the performance metrics comparing zircon tiles to standard tiles:
Performance Metric | Zircon Tile | Standard Tile |
---|---|---|
Acid Resistance | High | Moderate |
Gloss Retention | High | Low |
Breaking Strength | High | Standard |
UV Stability | Excellent | Poor |
Ultimately, incorporating zircon into tile formulations translates into higher customer satisfaction, fewer warranty claims, and an overall better return on investment for manufacturers. With these performance benefits, zircon is clearly an indispensable material in modern tile production.her customer satisfaction and fewer warranty claims make zircon tiles a safer long-term investment.
ARE THERE ALTERNATIVES TO ZIRCON SAND IN CERAMIC TILE PRODUCTION?
Alternatives exist, but each has drawbacks:
- Alumina offers high hardness but can discolor under firing.
- Feldspar is cheap but lacks the opacity and density zircon provides.
- Silicon carbide works in industrial ceramics but is too abrasive and expensive for flooring.
Alternative | Pros | Cons |
---|---|---|
Alumina | Durable, hard | High cost, color control issues |
Feldspar | Inexpensive, available | Weak glaze finish |
Zircon | Balanced performance | Regional supply variations |
Although these alternatives can be utilized in developing certain tile formulations, achieving the same level of glaze definition and long-term performance as zircon is challenging. Consequently, many manufacturers integrate a combination of these materials but continue to rely on zircon to ensure product quality and durability.
Overall, understanding the specific needs and performance expectations of the ceramic tiles being produced can help manufacturers make informed decisions about whether to incorporate zircon sand or explore alternative materials.
HOW IS THE SUPPLY OF ZIRCON SAND MANAGED?
Zircon is globally mined and traded as a commodity, with Australia, South Africa, and Indonesia being key suppliers. The extraction and supply management of zircon sand involve several layers of complexity due to varying global demand and environmental regulations.
Mining operations are often subject to rigorous environmental assessments to minimize ecological impact. Consequently, the market experiences periodic shortages, influenced by not only local regulations but also geopolitical factors that can affect export capabilities.
To mitigate these challenges, companies are increasingly adopting sustainability practices. These include:
- Reclamation Protocols: Mining companies are implementing strategies for land rehabilitation post-extraction, aiming to restore sites to their natural state.
- Less Energy-Intensive Refining: Innovations in the refinement process are being explored to reduce the overall energy consumption involved in zircon processing.
- Traceability Reports: Buyers mandate transparency regarding the sourcing of zircon, leading to a higher demand for documented supply chains that adhere to international standards.
Country | Market Share (%) |
---|---|
Australia | 37 |
South Africa | 30 |
China | 10 |
Others | 23 |
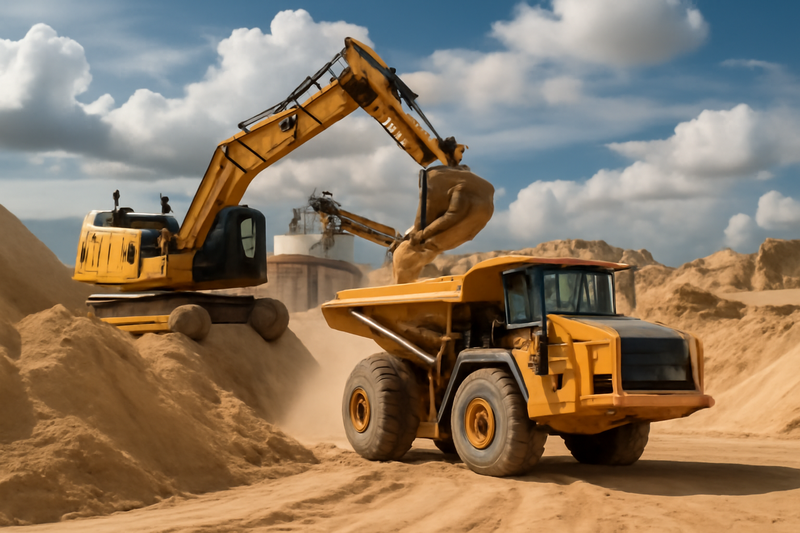
Large-scale zircon sand extraction operation with machinery loading refined sand into trucks.
In addition, long-term contracts and verified suppliers have become standard in procurement workflows. Manufacturers often utilize raw material forecasting models to better anticipate market needs, ensuring that supply aligns with production schedules. This level of planning is essential for maintaining operational continuity and product quality in the face of market fluctuations.
CONCLUSION
Zircon sand isn’t just another raw material—it fundamentally defines the quality of ceramic tiles. Its unique properties—such as high melting point, low expansion, and exceptional chemical stability—make it indispensable in modern tile manufacturing. From enhancing surface appearance and durability to optimizing production processes, zircon significantly influences the overall performance of tile products.
Moreover, understanding the sourcing and supply chain complexities of zircon can empower manufacturers to make informed decisions that align with sustainability goals. With increasing demand for eco-friendly materials, utilizing responsibly sourced zircon not only meets market expectations but also reinforces a company’s commitment to environmental stewardship.
At Global Industry, we recognize the critical role zircon plays in tile production. We provide reliable sourcing, technical expertise, and material traceability to help manufacturers enhance their operations. By prioritizing zircon in your production strategy, you can elevate tile quality, improve profitability, and ensure customer satisfaction. Contact us today to explore how zircon can redefine your tile offerings.
FAQ
Q1: What makes Zircon Sand a preferred material for tile manufacturers?
Zircon enhances durability, controls glaze brightness, and significantly reduces product defects in high-volume tile manufacturing. Its unique thermal and chemical stability helps maintain quality during fast-firing cycles, which is critical for modern, high-efficiency production lines.
Q2: How does Zircon Sand affect tile appearance?
It increases whiteness, opacity, and gloss uniformity—especially in glazed tiles—resulting in a cleaner, brighter surface. Zircon also ensures visual consistency between batches, a key factor for premium tile producers targeting architectural or design-driven markets.
Q3: Can ceramic tiles be made without Zircon Sand?
Yes, but they often fail to meet commercial quality benchmarks in gloss, strength, and resistance. Alternative materials like feldspar or kaolin may be cheaper but don’t offer the same level of finish or wear performance, leading to higher defect rates and shorter product lifespans.
Q4: How is Zircon Sand sourced for use in ceramics?
Zircon is extracted from coastal or alluvial mineral sand deposits using gravity and magnetic separation. It is then purified to ceramic-grade specifications, typically exceeding 98% ZrSiO₄ content, ensuring reliable performance during glaze and body formulation.
Q5: What environmental impact does Zircon Sand extraction have?
Mining involves land use and water consumption, but leading suppliers adopt responsible practices like land rehabilitation, dust control, and ISO-certified sustainability systems. The ceramic industry increasingly prefers zircon from traceable, low-impact sources.