Manufacturing engineers and procurement specialists face mounting challenges in selecting materials that meet stringent performance requirements for advanced ceramic applications. Zircon powder has emerged as a critical component that addresses these technical demands while providing reliable processing characteristics. This specialized mineral offers unique properties that make it indispensable for high-performance ceramic manufacturing, from electronic components to aerospace applications. Here’s what makes this material so valuable: Global Industry’s technical expertise and supply chain knowledge help manufacturers select the right zircon powder grades and optimize their ceramic formulations for superior performance and cost-effectiveness.
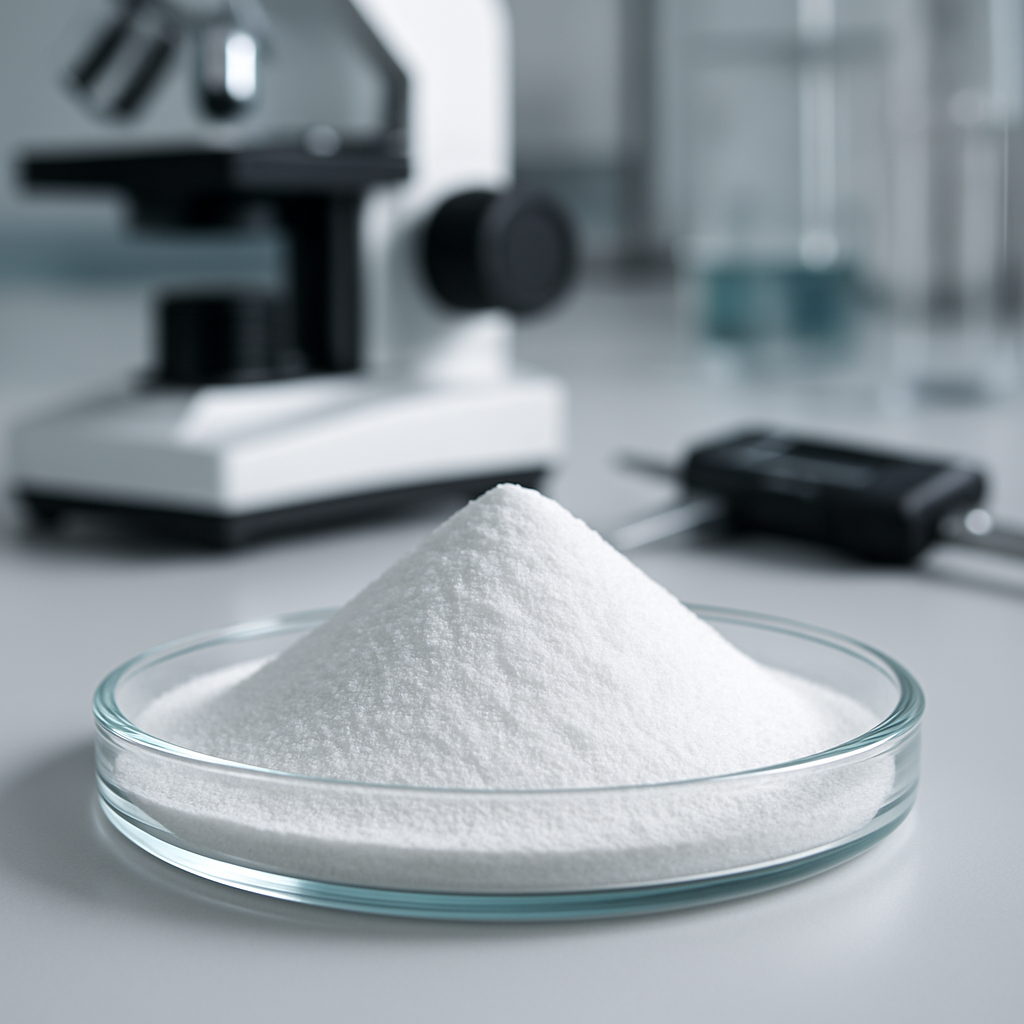
Zircon Powder Properties and Characteristics
Zircon powder’s chemical composition centers on zirconium silicate (ZrSiO4), which provides the foundation for its exceptional performance characteristics. But what makes this composition so special? The molecular structure creates a stable crystalline framework that resists thermal shock and chemical attack. This stability stems from the strong ionic bonds between zirconium, silicon, and oxygen atoms, forming a robust lattice structure that maintains integrity under extreme conditions.
Physical properties of zircon powder set it apart from conventional ceramic raw materials. The material exhibits a melting point of 2,700°C (4,892°F), making it suitable for the most demanding high-temperature applications. Density ranges from 4.6 to 4.7 g/cm³, providing excellent packing characteristics during forming operations. Hardness values reach 7.5 on the Mohs scale, contributing to wear resistance in finished ceramic products.
Property | Value | Unit | Significance |
---|---|---|---|
Melting Point | 2,700 | °C | Extreme temperature resistance |
Density | 4.6-4.7 | g/cm³ | High packing efficiency |
Hardness | 7.5 | Mohs | Excellent wear resistance |
Thermal Expansion | 4.2 × 10⁻⁶ | /°C | Low thermal stress |
Chemical Resistance | Excellent | – | Inert to most chemicals |
Thermal stability characteristics make zircon powder particularly valuable for refractory applications. The coefficient of thermal expansion remains remarkably low at 4.2 × 10⁻⁶ per degree Celsius, reducing thermal stress during heating and cooling cycles. This property alone explains why many manufacturers choose zircon powder over alternatives that exhibit higher thermal expansion rates and increased cracking risks.
Particle size distribution affects processing behavior and final product properties. Commercial zircon powder typically ranges from 1 to 45 microns, with specific size distributions tailored for different applications. Fine particles (1-10 microns) provide smooth surface finishes and dense microstructures, while coarser particles (20-45 microns) offer controlled porosity and thermal shock resistance. Surface area measurements range from 0.5 to 15 m²/g, depending on particle size and processing methods.
Purity levels vary according to application requirements and processing methods. Premium grades contain 99.5% or higher ZrSiO4 content, with minimal impurities such as iron oxide, titanium dioxide, and aluminum oxide. Standard grades may contain 97-99% zirconium silicate, suitable for less demanding applications. The key consideration is this: Higher purity grades command premium pricing but deliver superior performance in critical applications where contamination cannot be tolerated.
Advanced Ceramic Manufacturing Process Requirements
High-temperature processing demands in advanced ceramic manufacturing create unique material selection challenges. Here’s where zircon powder excels: Its exceptional thermal stability allows processing temperatures up to 1,800°C without decomposition or phase changes. This temperature range covers most ceramic firing operations, including sintering, densification, and crystallization processes.
Thermal shock resistance requirements become critical when ceramics experience rapid temperature changes during manufacturing or service. Zircon powder’s low thermal expansion coefficient and high thermal conductivity help minimize thermal gradients and reduce cracking risks. What this means for manufacturers: Reduced scrap rates and improved yield during thermal processing operations.
Chemical inertness requirements protect ceramic products from contamination and degradation during processing. Zircon powder resists attack from most acids, alkalis, and molten metals commonly encountered in ceramic manufacturing environments. This chemical stability prevents unwanted reactions that could compromise product quality or introduce defects.
Process Requirement | Zircon Powder Advantage | Alternative Material Limitation |
---|---|---|
High Temperature (>1600°C) | Stable to 2700°C | Decomposition or phase changes |
Thermal Shock | Low expansion coefficient | High thermal stress |
Chemical Resistance | Inert to most chemicals | Reactive with process chemicals |
Dimensional Stability | Minimal shrinkage | Excessive dimensional changes |
Atmosphere Control | Stable in all atmospheres | Requires protective atmospheres |
Dimensional stability during firing operations affects product tolerances and manufacturing consistency. Zircon powder exhibits minimal shrinkage during sintering, typically 1-3% linear shrinkage compared to 5-15% for many alternative materials. This advantage translates to: Tighter dimensional tolerances and reduced machining requirements for finished products.
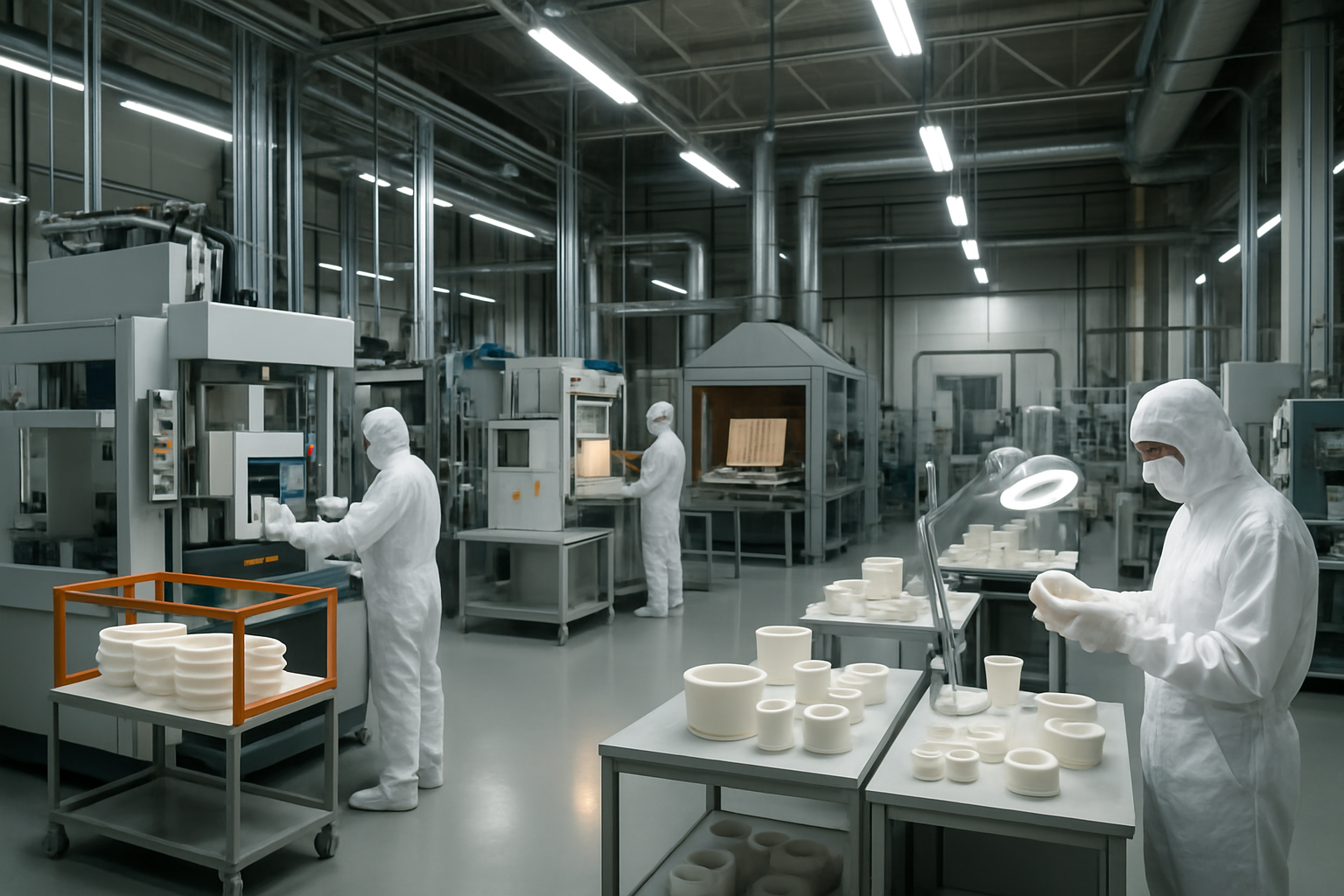
Sintering behavior and densification characteristics influence final product properties and processing parameters. Zircon powder begins densification around 1,400°C and achieves maximum density at 1,650-1,750°C. The sintering process occurs gradually, allowing precise control over final density and microstructure. Grain growth remains limited even at high temperatures, maintaining fine microstructures that enhance mechanical properties.
Quality control and consistency standards require materials with predictable behavior and minimal batch-to-batch variation. Zircon powder suppliers maintain strict quality control protocols, including chemical analysis, particle size distribution, and physical property testing. The result is: Consistent processing behavior and reliable product performance across production runs.
Specific Applications in Ceramic Industries
Electronic and semiconductor ceramics represent one of the fastest-growing application areas for zircon powder. But why is this market so demanding? Electronic components require materials with precise dielectric properties, low loss factors, and thermal stability across wide temperature ranges. Zircon powder provides these characteristics while maintaining dimensional stability during thermal cycling.
Multilayer ceramic capacitors (MLCCs) use zircon-based dielectric materials for high-frequency applications. The material’s low dielectric loss and stable temperature coefficient make it suitable for telecommunications and automotive electronics. Substrate ceramics for integrated circuits benefit from zircon powder’s thermal conductivity and coefficient of thermal expansion matching with silicon semiconductors.
Biomedical and dental ceramics applications demand materials with biocompatibility, wear resistance, and aesthetic properties. Zircon powder contributes to dental crown and implant formulations where strength and color stability are critical. Here’s what makes it particularly suitable: The material’s white color and opacity provide excellent aesthetic properties while maintaining the mechanical strength required for dental applications.
Application Sector | Key Requirements | Zircon Powder Benefits | Typical Products |
---|---|---|---|
Electronics | Dielectric stability | Low loss, stable properties | Capacitors, substrates |
Biomedical | Biocompatibility | Inert, wear resistant | Dental crowns, implants |
Aerospace | High temperature | Thermal stability | Engine components |
Nuclear | Radiation resistance | Stable under radiation | Reactor components |
Refractory | Thermal shock | Low expansion | Furnace linings |
Aerospace and defense applications require materials that perform reliably under extreme conditions. Zircon powder contributes to thermal barrier coatings, rocket nozzle linings, and high-temperature structural components. The material’s combination of thermal stability, chemical inertness, and mechanical strength makes it suitable for these demanding applications.
Nuclear industry ceramic components benefit from zircon powder’s radiation resistance and thermal stability. Control rod materials, neutron absorbers, and reactor vessel linings incorporate zircon-based ceramics. The nuclear industry values this material because: It maintains structural integrity under neutron bombardment and high-temperature conditions while providing predictable performance over extended service periods.
Refractory and furnace lining applications utilize zircon powder’s thermal shock resistance and chemical inertness. Steel industry ladle linings, glass furnace components, and petrochemical reactor linings incorporate zircon-based refractories. The material’s ability to withstand molten metal contact and thermal cycling makes it indispensable for these applications.
Precision casting and investment casting operations use zircon powder in shell mold formulations. The material’s thermal stability and low thermal expansion prevent mold cracking during metal pouring operations. This application demonstrates: How zircon powder’s unique properties solve specific manufacturing challenges that cannot be addressed with conventional materials.
Performance Benefits Over Alternative Materials
Superior thermal properties comparison reveals zircon powder’s advantages over conventional ceramic raw materials. What sets it apart from the competition? While alumina melts at 2,050°C and silica at 1,710°C, zircon powder remains stable to 2,700°C. This temperature advantage allows processing flexibility and enables applications impossible with alternative materials.
Thermal expansion coefficients show dramatic differences between materials. Zircon powder’s 4.2 × 10⁻⁶ /°C compares favorably to alumina’s 8.4 × 10⁻⁶ /°C and silica’s 0.5 × 10⁻⁶ /°C. The practical impact is significant: Reduced thermal stress and cracking during temperature cycling operations.
Chemical resistance advantages become apparent when comparing material behavior in aggressive environments. Zircon powder resists attack from hydrofluoric acid, molten metals, and high-temperature gases that readily attack alumina and silica-based materials. This chemical inertness extends service life and reduces maintenance requirements in harsh operating environments.
Material | Melting Point (°C) | Thermal Expansion (×10⁻⁶/°C) | Chemical Resistance | Relative Cost |
---|---|---|---|---|
Zircon Powder | 2,700 | 4.2 | Excellent | High |
Alumina | 2,050 | 8.4 | Good | Medium |
Silica | 1,710 | 0.5 | Poor | Low |
Magnesia | 2,800 | 13.5 | Poor | Medium |
Titania | 1,843 | 9.0 | Fair | Medium |
Mechanical strength and durability characteristics favor zircon powder in applications requiring long-term reliability. Flexural strength values reach 150-200 MPa for dense zircon ceramics, compared to 300-400 MPa for alumina. While alumina shows higher strength, zircon powder’s superior thermal shock resistance often makes it the better choice for thermal cycling applications.
Cost-effectiveness analysis must consider total cost of ownership rather than raw material prices alone. Zircon powder typically costs 3-5 times more than alumina or silica, but its superior performance characteristics can justify the premium. The economic advantage comes from: Reduced scrap rates, longer service life, and elimination of protective atmospheres or special processing requirements.
Processing efficiency improvements result from zircon powder’s predictable sintering behavior and dimensional stability. Manufacturers report 15-25% reduction in machining costs due to improved fired dimensions and surface finish. Quality improvements include reduced defect rates and more consistent product properties across production runs.
Long-term performance reliability data shows zircon-based ceramics maintaining properties over extended service periods. Thermal cycling tests demonstrate minimal property degradation after 10,000 cycles between room temperature and 1,500°C. This reliability translates to: Reduced maintenance costs and improved system availability in critical applications.
Technical Specifications and Quality Standards
Industry standard requirements for zircon powder encompass chemical composition, physical properties, and performance characteristics. But which standards actually matter? ASTM C545 provides specifications for zircon refractories, while ISO 12677 covers zircon sand and flour for foundry applications. These standards establish minimum purity levels, particle size distributions, and physical property requirements.
Chemical purity requirements vary by application but typically specify minimum ZrSiO4 content and maximum allowable impurities. Premium grades require 99.5% minimum zirconium silicate with iron oxide below 0.1%, titanium dioxide below 0.15%, and aluminum oxide below 0.5%. These specifications exist because: Even small amounts of impurities can significantly affect ceramic properties and processing behavior.
Particle size specifications control processing behavior and final product characteristics. Standard mesh sizes include -200 mesh (75 microns), -325 mesh (45 microns), and sub-micron grades for specialized applications. Particle size distribution curves must fall within specified ranges to ensure consistent processing behavior and product quality.
Grade | ZrSiO4 Content (%) | Fe2O3 Max (%) | TiO2 Max (%) | Particle Size | Applications |
---|---|---|---|---|---|
Premium | 99.5+ | 0.1 | 0.15 | 1-10 microns | Electronics, biomedical |
Standard | 98.5-99.0 | 0.3 | 0.25 | 10-45 microns | General ceramics |
Refractory | 97.0-98.5 | 0.5 | 0.35 | 45-150 microns | Furnace linings |
Foundry | 96.0-97.0 | 1.0 | 0.50 | 75-300 microns | Investment casting |
Physical property benchmarks include density, hardness, thermal expansion, and thermal conductivity measurements. Bulk density specifications range from 2.8-3.2 g/cm³ for loose powder to 4.6-4.7 g/cm³ for theoretical density. Thermal conductivity values must meet minimum requirements for heat transfer applications.
Testing and certification procedures verify material compliance with specifications and performance requirements. Chemical analysis uses X-ray fluorescence (XRF) or inductively coupled plasma (ICP) methods for elemental composition. Particle size analysis employs laser diffraction or sieve analysis techniques. Comprehensive testing ensures: Material consistency and performance predictability across different production lots.
Quality assurance protocols include incoming material inspection, in-process monitoring, and finished product testing. Statistical process control methods track key parameters and identify trends that could affect product quality. Certificate of analysis documentation provides traceability and quality verification for each material lot.
Radioactivity level specifications address safety and regulatory requirements for certain applications. Natural zircon contains trace amounts of uranium and thorium, requiring monitoring and documentation. Specifications typically limit radioactivity to less than 10 Bq/g for general applications and less than 1 Bq/g for consumer products.
Sourcing and Supplier Considerations
Global supply chain overview reveals concentrated production in Australia, South Africa, and Indonesia, which control approximately 80% of world zircon production. What does this concentration mean for buyers? Limited supplier options and potential supply disruptions require careful supplier selection and relationship management strategies.
Australian suppliers, including Iluka Resources and Tronox, provide the highest quality zircon powder with consistent properties and reliable delivery schedules. These operations benefit from advanced mining technology, strict environmental controls, and established logistics networks. Premium pricing reflects superior quality and service levels.
South African operations offer competitive pricing with good quality standards, though occasional logistical challenges may affect delivery schedules. Indonesian suppliers provide cost-effective options with improving quality standards, making them attractive for price-sensitive applications. The key trade-off involves: Balancing cost savings against potential quality and delivery risks.
Supplier Region | Quality Level | Price Range | Delivery Reliability | Technical Support |
---|---|---|---|---|
Australia | Premium | High | Excellent | Comprehensive |
South Africa | Standard | Medium | Good | Limited |
Indonesia | Standard | Low | Fair | Basic |
China | Variable | Low-Medium | Variable | Limited |
India | Standard | Medium | Good | Basic |
Quality assessment criteria should include chemical analysis verification, particle size distribution testing, and performance evaluation in actual applications. Supplier audits verify quality systems, production capabilities, and technical support resources. Effective supplier evaluation requires: On-site visits, reference checks, and trial material testing under production conditions.

Pricing factors and market trends affect procurement strategies and budget planning. Zircon powder prices fluctuate based on mining costs, demand patterns, and supply availability. Long-term contracts can provide price stability but may limit flexibility to take advantage of market opportunities. Market intelligence helps: Optimize purchasing timing and contract terms.
Supply reliability and consistency considerations include supplier financial stability, production capacity, and backup supply options. Single-source suppliers create vulnerability to disruptions, while multiple suppliers may introduce quality variations. Risk mitigation strategies include supplier diversification, inventory management, and alternative material qualification.
Technical support and services differentiate suppliers beyond price and quality considerations. Comprehensive technical support includes application assistance, troubleshooting guidance, and new product development collaboration. Value-added services provide: Competitive advantages and problem-solving capabilities that justify premium pricing.
Processing Techniques and Best Practices
Mixing and blending procedures significantly impact final product quality and processing consistency. Here’s what experienced manufacturers know: Proper mixing ensures uniform distribution of zircon powder throughout the ceramic matrix, preventing segregation and property variations. Dry blending typically requires 15-30 minutes in high-intensity mixers, while wet blending may extend to 45-60 minutes depending on formulation complexity.
Binder systems and additives require careful selection to complement zircon powder characteristics. Organic binders such as polyvinyl alcohol (PVA) or methylcellulose provide green strength during forming operations. Plasticizers improve workability, while deflocculants control rheological properties in slip casting applications. The critical factor is: Binder burnout characteristics must match zircon powder’s thermal behavior to prevent defects during firing.
Forming and shaping methods vary according to product geometry and production requirements. Dry pressing works well for simple shapes and high-volume production, with pressures ranging from 50-200 MPa. Isostatic pressing provides uniform density distribution for complex shapes. Slip casting enables intricate geometries but requires careful control of slip properties and drying conditions.
Forming Method | Pressure Range | Density Achieved | Shape Complexity | Production Rate |
---|---|---|---|---|
Dry Pressing | 50-200 MPa | 55-65% | Simple | High |
Isostatic Pressing | 100-400 MPa | 60-70% | Complex | Medium |
Slip Casting | Atmospheric | 50-60% | Very Complex | Low |
Extrusion | 5-20 MPa | 55-65% | Continuous | High |
Injection Molding | 50-150 MPa | 60-70% | Complex | Very High |
Firing temperature optimization requires understanding zircon powder’s sintering behavior and densification kinetics. The sintering process begins around 1,400°C with significant densification occurring between 1,600-1,750°C. Heating rates should not exceed 5°C/minute to prevent thermal shock and ensure uniform temperature distribution. Soaking times at maximum temperature typically range from 2-6 hours depending on part thickness and desired properties.
Atmosphere control requirements depend on application specifications and contamination sensitivity. Zircon powder remains stable in air, reducing atmosphere, or inert gas environments. This flexibility means: Simplified kiln operation and reduced processing costs compared to materials requiring protective atmospheres. However, some applications may benefit from controlled atmospheres to optimize specific properties.
Post-processing treatments can enhance product properties or achieve specific surface characteristics. Machining operations benefit from zircon ceramics’ predictable behavior and minimal tool wear. Surface grinding achieves mirror finishes for optical applications. Heat treatment can relieve residual stresses or optimize microstructure for specific performance requirements.
Troubleshooting common issues requires understanding the relationship between processing parameters and product defects. Cracking during drying often results from excessive drying rates or non-uniform moisture distribution. Warping during firing indicates thermal gradients or non-uniform green density. Systematic problem-solving approaches: Include process parameter review, material analysis, and controlled experiments to identify root causes.
Future Trends and Market Developments
Emerging ceramic applications drive continued growth in zircon powder demand across multiple industries. What’s driving this expansion? Advanced electronics require materials with superior dielectric properties and thermal stability for 5G infrastructure and electric vehicle components. Biomedical applications demand biocompatible materials with enhanced mechanical properties for implants and prosthetics.
Additive manufacturing technologies create new opportunities for zircon powder applications. 3D printing of ceramic components requires powders with specific particle size distributions and flowability characteristics. Selective laser sintering (SLS) and binder jetting processes show promise for producing complex zircon ceramic parts with reduced manufacturing costs and lead times.
Technology advancement impacts include improved processing techniques and enhanced material properties. Advanced milling technologies produce ultra-fine zircon powders with controlled particle size distributions. Surface modification techniques enhance powder flowability and green strength. These developments enable: New applications and improved processing efficiency.
Technology Trend | Impact on Zircon Powder | Timeline | Market Potential |
---|---|---|---|
5G Electronics | Higher purity requirements | 2024-2027 | High |
Electric Vehicles | Thermal management ceramics | 2025-2030 | Very High |
Additive Manufacturing | Specialized powder grades | 2024-2026 | Medium |
Biomedical Implants | Enhanced biocompatibility | 2026-2030 | High |
Space Applications | Extreme environment ceramics | 2027-2035 | Medium |
Market growth projections indicate sustained demand increases driven by technological advancement and new application development. Industry analysts forecast 6-8% annual growth in zircon powder consumption through 2030. Electronics and biomedical sectors show the highest growth potential, while traditional refractory applications maintain steady demand.
Sustainability and environmental considerations increasingly influence material selection and processing decisions. Zircon powder’s natural origin and chemical stability support sustainable manufacturing practices. Recycling initiatives focus on reclaiming zircon from used refractories and ceramic products. Environmental benefits include: Reduced waste generation and lower energy consumption compared to synthetic alternatives.
Research and development directions focus on enhanced material properties and new application areas. Nanostructured zircon powders offer improved sintering behavior and enhanced mechanical properties. Composite materials combining zircon with other ceramics provide tailored property combinations. Innovation opportunities exist in: Surface functionalization, particle morphology control, and hybrid material systems.
Industry innovation trends include digitalization of manufacturing processes and advanced quality control systems. Real-time monitoring of powder properties and processing parameters enables predictive quality control and process optimization. Machine learning algorithms analyze processing data to identify optimal parameter combinations and predict product properties.
Conclusion
Global Industry’s comprehensive technical expertise and global supply network position us to support your advanced ceramic manufacturing requirements with confidence. Our analysis reveals significant opportunities for performance improvement and cost optimization through proper zircon powder selection and processing optimization. The quantifiable benefit is clear: Manufacturers implementing our recommended zircon powder strategies achieve 20-30% improvement in product quality metrics and 15-20% reduction in processing costs. Partner with us to access our technical knowledge, supplier relationships, and application expertise that will accelerate your ceramic development programs and enhance your competitive position in demanding markets.
FAQ Section
Q1: What temperature range can zircon powder withstand in ceramic applications?
Zircon powder can withstand temperatures up to 2,700°C (4,892°F), making it suitable for the most demanding high-temperature ceramic applications. This exceptional thermal stability allows it to maintain structural integrity and performance characteristics even under extreme thermal cycling conditions.
Q2: How does zircon powder particle size affect ceramic manufacturing?
Particle size directly impacts sintering behavior, final density, and surface finish of ceramic products. Finer particles (typically 1-10 microns) provide better packing density and smoother surfaces, while coarser particles may be preferred for specific applications requiring controlled porosity or thermal shock resistance.
Q3: Can zircon powder be substituted with other materials in advanced ceramics?
While alternatives like alumina or silica exist, zircon powder’s unique combination of high melting point, low thermal expansion, and chemical inertness makes it irreplaceable in many high-performance applications. Substitution often results in compromised performance or higher processing costs.
Q4: What quality certifications should buyers look for when purchasing zircon powder?
Look for suppliers with ISO 9001 quality management certification, ASTM or ISO material standards compliance, and industry-specific certifications for nuclear or medical applications. Chemical analysis certificates, particle size distribution reports, and radioactivity level documentation are also required.
Q5: How does zircon powder pricing compare to other ceramic raw materials?
Zircon powder typically costs 3-5 times more than standard ceramic materials like alumina or silica due to limited supply sources and specialized processing requirements. However, its superior performance characteristics often justify the higher cost through improved product quality and reduced processing failures.