Electronic manufacturing faces increasing demands for materials that can withstand extreme conditions while maintaining precision and reliability. Zircon powder has emerged as a game-changing material in this sector, offering unique properties that address critical challenges in component production. The right material choice can transform manufacturing outcomes. This comprehensive guide examines how zircon powder solves common electronic manufacturing problems, from thermal management to dimensional stability. Industry leaders rely on zircon powder to achieve superior product quality, reduce defect rates, and meet stringent performance standards that modern electronics demand.
What Makes Zircon Powder Suitable for Electronics?
Zircon powder brings exceptional properties that make it ideal for electronic applications. These characteristics solve real manufacturing challenges. The material’s high dielectric strength provides excellent electrical insulation, preventing unwanted current flow between components. This property becomes critical in high-density electronic assemblies where space constraints require materials with superior insulating capabilities.
Thermal stability represents another key advantage. Zircon powder maintains its properties at temperatures exceeding 1,500°C, allowing manufacturers to use aggressive processing conditions without material degradation. This thermal resilience opens new processing possibilities. The material’s chemical inertness prevents contamination of sensitive electronic components during manufacturing, a concern that can cause costly failures in finished products.
The low thermal expansion coefficient of zircon powder helps maintain dimensional stability during temperature cycling. Electronic components experience repeated heating and cooling during operation, and materials with high thermal expansion can cause stress fractures or connection failures. Dimensional stability directly impacts product reliability.
Property | Zircon Powder | Alumina | Silica | Benefit |
---|---|---|---|---|
Dielectric Strength (kV/mm) | 15-20 | 10-15 | 8-12 | Superior insulation |
Thermal Expansion (×10⁻⁶/°C) | 4.2 | 8.8 | 14.0 | Better stability |
Melting Point (°C) | 2,550 | 2,054 | 1,713 | Higher processing temps |
Chemical Resistance | Excellent | Very Good | Good | Reduced contamination |
Purity levels in electronic-grade zircon powder typically exceed 99.5%, with strict controls on metallic impurities. Iron content must remain below 0.05% to prevent magnetic interference, while titanium levels stay under 0.1% to avoid unwanted optical properties. Purity specifications ensure consistent performance.
The particle size distribution can be precisely controlled during processing, allowing manufacturers to optimize packing density and surface finish quality. Typical electronic applications use particle sizes ranging from 0.5 to 10 micrometers, depending on the specific manufacturing process requirements.
Which Electronic Components Benefit from Zircon Powder?
Ceramic capacitors represent one of the largest applications for zircon powder in electronics. These components form the backbone of modern circuits. The material serves as a key ingredient in dielectric layers, where its high dielectric constant and low loss factor improve capacitor performance. Manufacturers can achieve higher capacitance values in smaller packages, meeting the miniaturization demands of modern electronics.
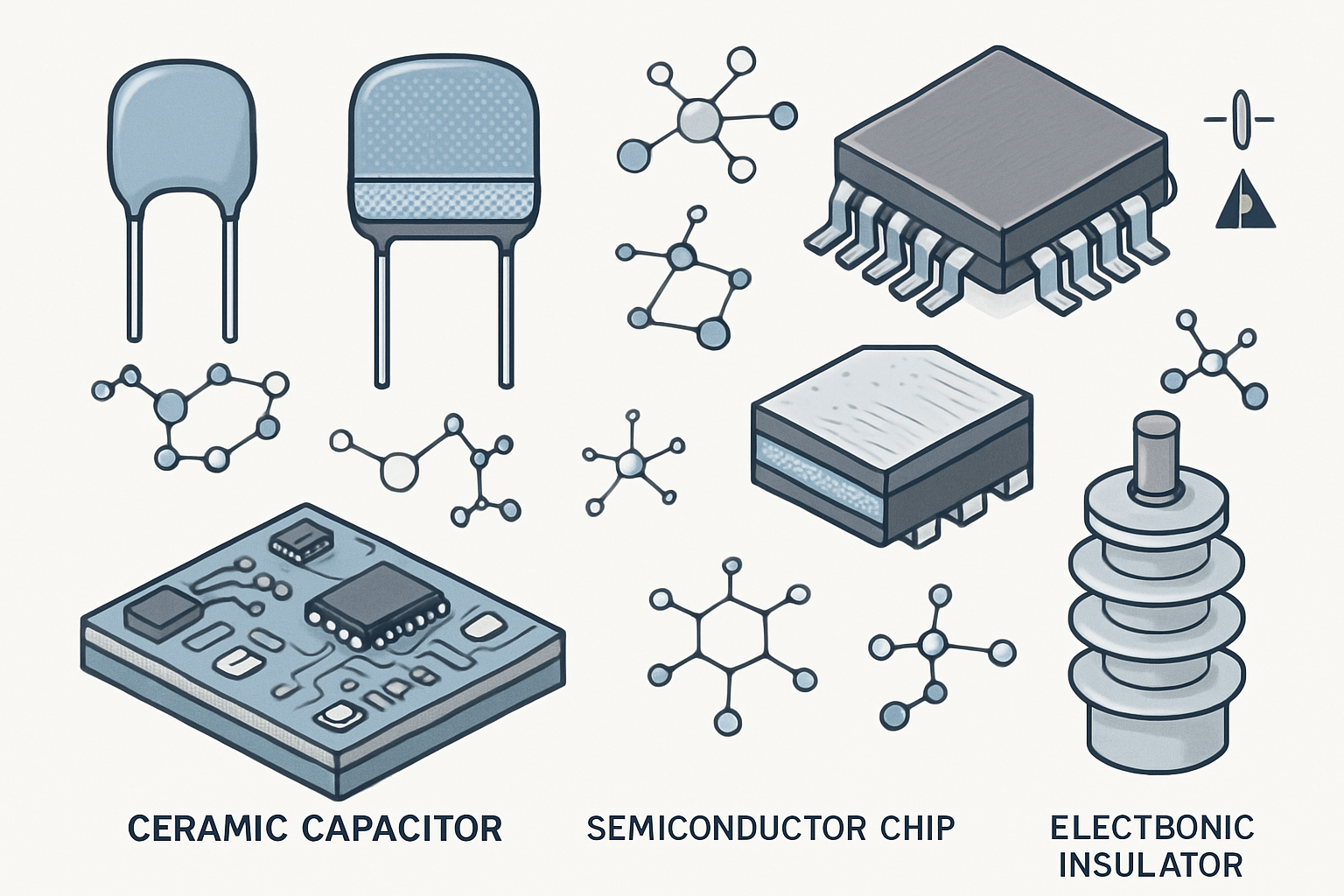
Semiconductor substrates benefit significantly from zircon powder additions. The material’s thermal conductivity helps dissipate heat generated during device operation, while its electrical insulation properties prevent unwanted current paths. Thermal management becomes critical in high-power applications. Advanced packaging materials incorporate zircon powder to achieve better thermal interface performance between chips and heat sinks.
Printed circuit board manufacturing uses zircon powder in specialized applications where standard materials cannot meet performance requirements. High-frequency applications require materials with stable dielectric properties across wide frequency ranges, and zircon powder delivers this consistency. Frequency stability enables next-generation communications.
Component Type | Application | Key Benefit | Market Size |
---|---|---|---|
Ceramic Capacitors | Dielectric layers | High capacitance density | $12.8 billion |
Semiconductor Substrates | Thermal management | Heat dissipation | $8.4 billion |
PCB Materials | High-frequency circuits | Frequency stability | $6.2 billion |
Electronic Insulators | Isolation barriers | Electrical safety | $3.1 billion |
Piezoelectric devices and sensors incorporate zircon powder to achieve precise mechanical-to-electrical energy conversion. The material’s stable crystal structure maintains consistent piezoelectric properties over wide temperature ranges, making it suitable for automotive and aerospace applications where reliability is paramount.
High-frequency communication components, including filters and resonators, use zircon powder to achieve stable performance across temperature variations. The material’s low temperature coefficient ensures that device characteristics remain consistent during operation, reducing the need for complex compensation circuits.
Electronic insulators in power applications rely on zircon powder’s high breakdown voltage and thermal stability. These components must withstand both electrical stress and thermal cycling without degradation, requirements that zircon powder meets effectively.
How Does Zircon Powder Improve Manufacturing Processes?
Manufacturing process improvements with zircon powder begin with thermal management during component fabrication. Better heat control leads to higher yields. The material’s thermal conductivity helps distribute heat evenly during sintering and firing operations, reducing temperature gradients that can cause cracking or warping in finished components.
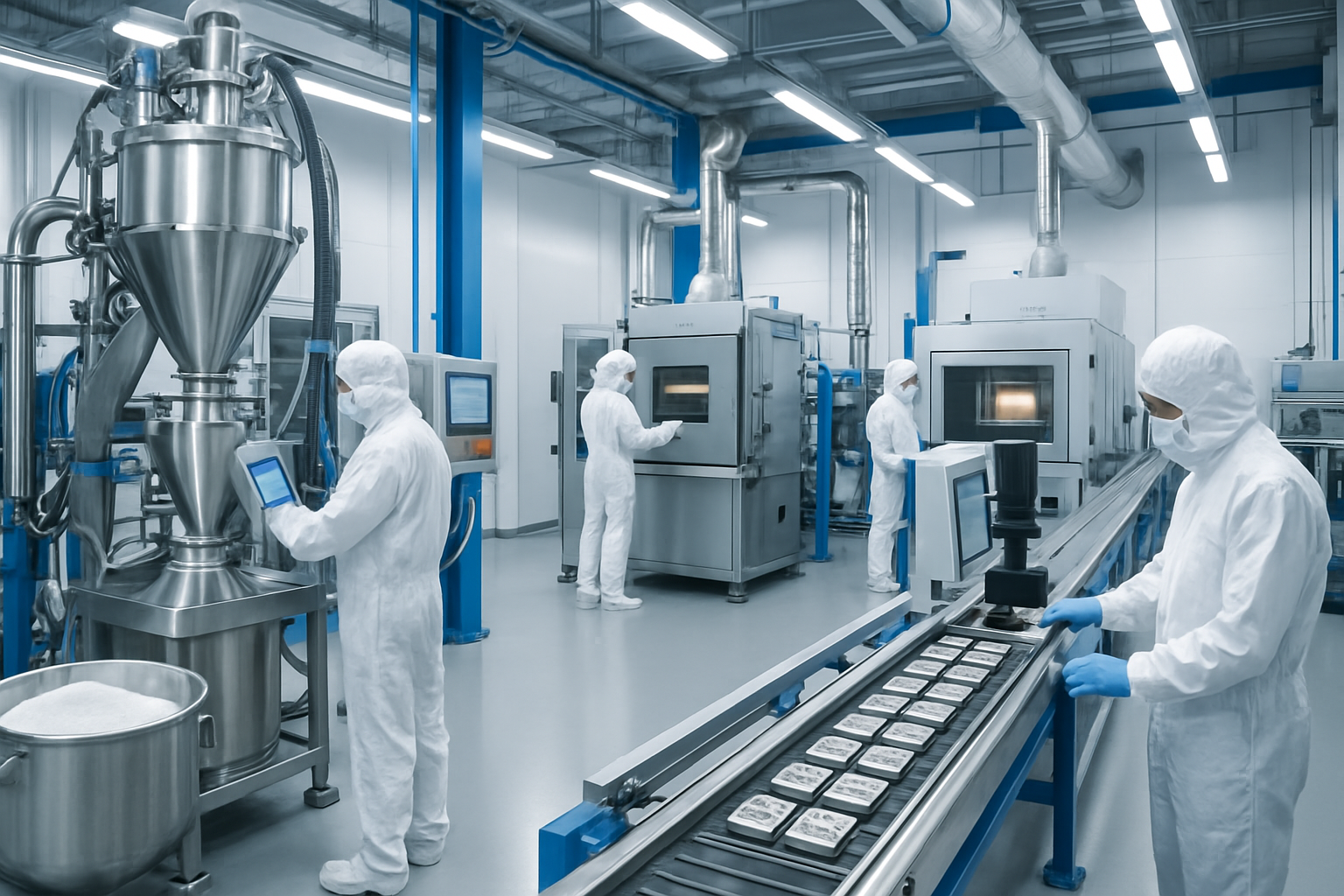
Dimensional stability improvements reduce defect rates significantly. Components made with zircon powder maintain their intended geometry throughout processing and operation, eliminating failures caused by dimensional changes. Consistent dimensions mean reliable performance. This stability becomes particularly important in multi-layer assemblies where layer-to-layer alignment must remain precise.
Electrical insulation improvements prevent short circuits and current leakage that can cause component failures. Zircon powder’s high resistivity ensures that electrical isolation remains effective even under challenging operating conditions. The material maintains its insulating properties across wide temperature ranges, providing consistent protection.
Thermal stress reduction occurs because zircon powder’s low thermal expansion minimizes stress development during temperature cycling. Components experience less mechanical stress, leading to longer service life and improved reliability. Reduced stress extends component lifetime.
Process Parameter | Without Zircon | With Zircon | Improvement |
---|---|---|---|
Defect Rate (%) | 3.2-4.8 | 1.1-1.8 | 65-70% reduction |
Dimensional Tolerance (μm) | ±15-25 | ±5-10 | 60-75% improvement |
Thermal Cycling Life (cycles) | 5,000-8,000 | 12,000-18,000 | 140-225% increase |
Processing Temperature (°C) | 1,200-1,400 | 1,400-1,600 | Higher capability |
Surface finish quality improves when zircon powder is incorporated into coating formulations. The material’s hardness and chemical inertness create smooth, durable surfaces that resist wear and contamination. This improvement becomes particularly valuable in applications where surface quality affects electrical performance.
Adhesion properties between different materials improve with zircon powder additions. The material acts as a bonding agent that creates strong interfaces between dissimilar materials, reducing delamination failures in multi-layer structures. Strong bonds prevent assembly failures.
Processing temperature capabilities expand with zircon powder, allowing manufacturers to use higher temperatures for better material consolidation and improved properties. This capability enables the production of components with superior mechanical and electrical characteristics.
What Quality Standards Apply to Electronic-Grade Zircon?
Electronic-grade zircon powder must meet stringent purity requirements that exceed those for other industrial applications. Quality standards ensure consistent performance. Total impurity levels typically cannot exceed 0.5%, with individual metallic impurities limited to even lower concentrations. Iron content must remain below 0.05% to prevent magnetic interference in sensitive electronic circuits.
Particle size distribution specifications require tight control to ensure consistent processing characteristics. The distribution typically follows a normal curve with specific limits on both fine and coarse particles. Particles larger than 20 micrometers can cause surface defects, while excessive fine particles may create processing difficulties.
Quality Parameter | Specification | Test Method | Acceptance Criteria |
---|---|---|---|
ZrO₂ Content | ≥66.0% | XRF Analysis | Pass/Fail |
Fe₂O₃ Content | ≤0.05% | ICP-MS | Quantitative limit |
Particle Size D50 | 2-8 μm | Laser Diffraction | Statistical control |
Surface Area | 3-8 m²/g | BET Method | Range specification |
Moisture Content | ≤0.1% | Karl Fischer | Maximum limit |
Electrical resistivity measurements verify the material’s insulating properties. Electronic-grade zircon powder must demonstrate resistivity values exceeding 10¹² ohm-cm at room temperature, with minimal variation across different production batches. Consistent electrical properties ensure reliable performance.
Dielectric constant specifications ensure that the material provides predictable electrical behavior in capacitor and insulator applications. The dielectric constant must remain stable across frequency ranges from DC to several gigahertz, with loss factors below specified limits.
Thermal property verification includes measurements of thermal expansion coefficient, thermal conductivity, and specific heat capacity. These properties must fall within narrow ranges to ensure consistent thermal behavior during processing and operation.
Industry certifications from organizations like ISO, IEC, and JEDEC provide additional quality assurance. These certifications verify that manufacturing processes and quality control systems meet international standards for electronic materials.
Chemical composition analysis using techniques like X-ray fluorescence (XRF) and inductively coupled plasma mass spectrometry (ICP-MS) provides detailed verification of elemental composition. These analyses detect trace impurities that could affect electronic performance.
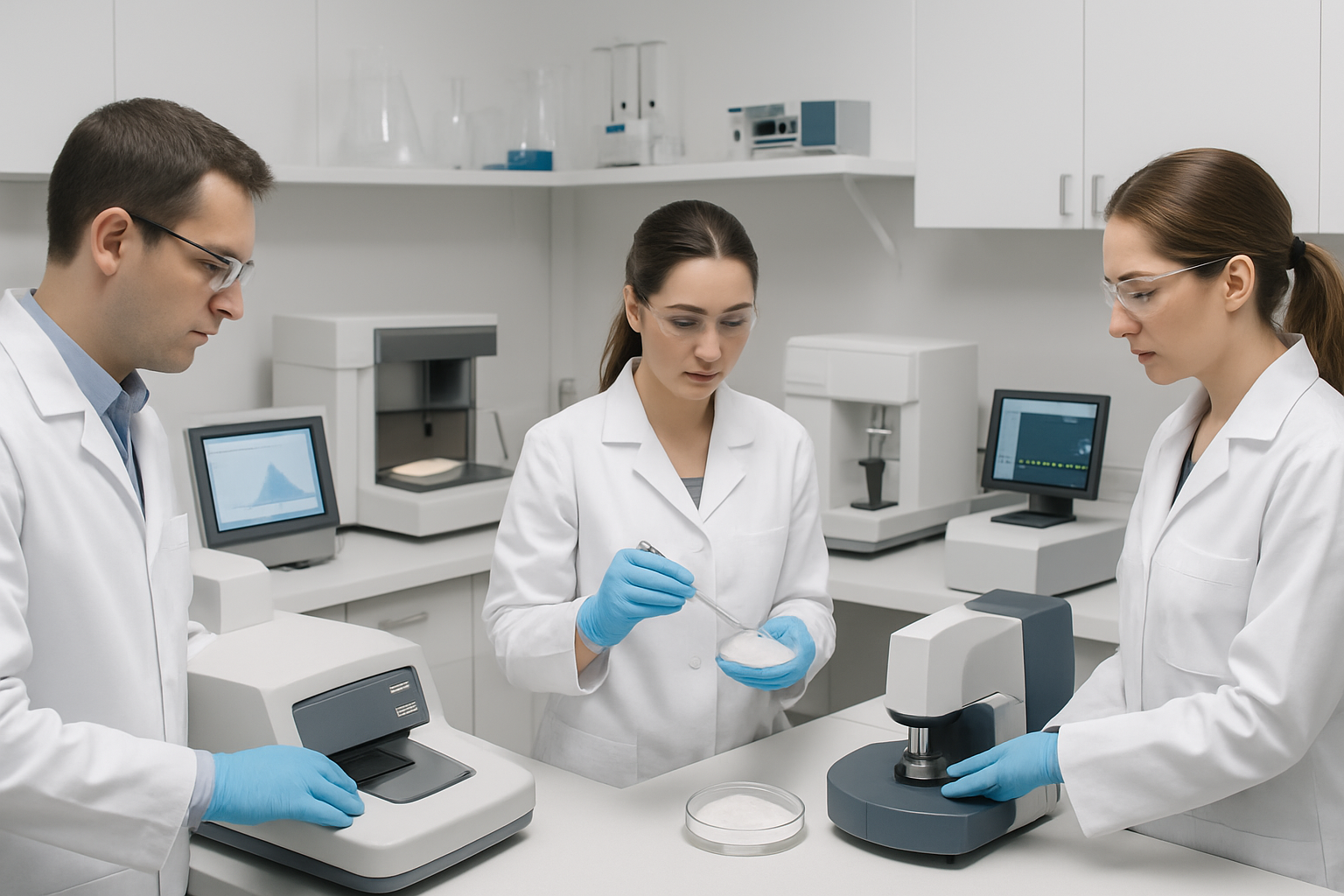
How Do Costs Compare with Alternative Materials?
Initial material costs for electronic-grade zircon powder typically run 40-60% higher than conventional alternatives like alumina or silica. Higher upfront costs deliver long-term value. However, this premium is often offset by performance improvements that reduce total manufacturing costs and improve product reliability.
Processing cost implications vary depending on the specific application. Zircon powder’s higher processing temperature capability can reduce cycle times in some applications, offsetting material cost increases. The material’s stability also reduces waste from defective parts, providing additional cost savings.
Cost Factor | Alumina | Zircon Powder | Difference |
---|---|---|---|
Material Cost ($/kg) | 8-12 | 15-22 | +75-85% |
Processing Cost ($/kg) | 25-35 | 20-30 | -15-20% |
Defect Rate Cost ($/kg) | 15-25 | 5-10 | -60-65% |
Total Manufacturing Cost | 48-72 | 40-62 | -15-20% |
Long-term reliability benefits provide significant value through reduced warranty costs and improved customer satisfaction. Components made with zircon powder typically demonstrate 2-3 times longer service life compared to conventional materials, reducing replacement costs and downtime.
Total cost of ownership calculations must include factors beyond initial material costs. Energy savings from improved thermal management, reduced maintenance requirements, and extended component life often justify the higher material costs. Total cost analysis reveals true value.
Supply chain considerations include availability and price stability. Zircon powder supply is generally stable, with multiple global suppliers ensuring competitive pricing and reliable delivery. Long-term contracts can provide price protection against market fluctuations.
Return on investment for manufacturing upgrades typically occurs within 12-18 months when switching to zircon powder. The combination of reduced defect rates, improved yields, and enhanced product performance drives rapid payback of any additional material costs.
Market demand for high-performance electronic materials continues growing, driven by applications in 5G communications, electric vehicles, and renewable energy systems. This demand supports continued investment in zircon powder technology and manufacturing capacity.
What Processing Techniques Optimize Zircon Powder Performance?
Mixing and dispersion methods play a critical role in achieving uniform zircon powder distribution throughout electronic materials. Proper mixing ensures consistent properties. High-energy ball milling for 4-8 hours typically provides adequate dispersion, while ultrasonic treatment can improve particle separation and reduce agglomeration.
Sintering temperature profiles must be carefully controlled to achieve optimal densification without grain growth. Typical sintering temperatures range from 1,400-1,600°C, with heating rates of 2-5°C per minute to prevent thermal shock. Controlled heating prevents defects. Atmosphere control during sintering prevents oxidation and maintains material purity.
Processing Parameter | Recommended Range | Control Method | Impact on Quality |
---|---|---|---|
Mixing Time | 4-8 hours | Timer control | Uniformity |
Sintering Temperature | 1,400-1,600°C | PID controller | Density |
Heating Rate | 2-5°C/min | Programmed ramp | Crack prevention |
Atmosphere | Inert or reducing | Gas flow control | Purity maintenance |
Cooling Rate | 1-3°C/min | Controlled cooling | Stress relief |
Coating application techniques for zircon powder suspensions require careful control of viscosity and particle loading. Spray coating, dip coating, and screen printing each offer advantages for different applications. Viscosity control through binder selection and solvent ratios ensures uniform coating thickness.
Quality control testing during processing includes real-time monitoring of temperature, atmosphere composition, and dimensional changes. Statistical process control methods help identify trends that could affect product quality before defects occur. Continuous monitoring prevents quality issues.
Equipment requirements for zircon powder processing include high-temperature furnaces, controlled atmosphere systems, and precision mixing equipment. Furnace design must provide uniform temperature distribution and precise atmosphere control to achieve consistent results.
Safety protocols for zircon powder handling include dust control measures, personal protective equipment, and proper ventilation systems. While zircon powder is generally safe, proper handling procedures prevent inhalation and skin contact that could cause irritation.
Material handling systems must prevent contamination and maintain powder characteristics during storage and transport. Sealed containers, moisture control, and first-in-first-out inventory management ensure material quality throughout the supply chain.
What Future Trends Shape Zircon Powder Electronics Applications?
Miniaturization demands continue driving requirements for materials with superior performance in smaller packages. Smaller components need better materials. Zircon powder’s high dielectric constant and thermal stability enable the production of compact components that maintain performance despite reduced size. This trend particularly affects mobile devices and wearable electronics where space constraints are severe.
5G technology requirements create new challenges for electronic materials. High-frequency applications demand materials with stable dielectric properties across wide frequency ranges and minimal signal loss. Zircon powder’s consistent electrical properties make it well-suited for 5G infrastructure components and devices.
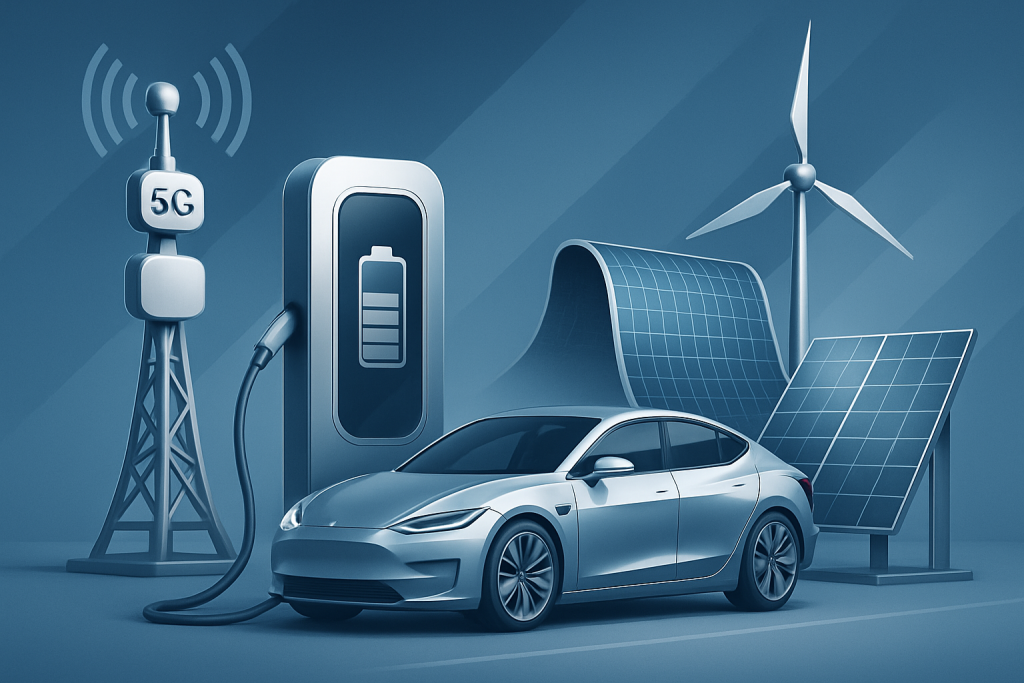
Electric vehicle electronics present opportunities for zircon powder in power management systems. The harsh operating environment in electric vehicles, including high temperatures and electrical stress, requires materials that can maintain performance under challenging conditions. Automotive applications demand reliability. Zircon powder’s thermal stability and electrical insulation properties address these requirements effectively.
Application Trend | Market Growth | Zircon Powder Opportunity | Timeline |
---|---|---|---|
5G Infrastructure | 25% annually | RF components | 2024-2027 |
Electric Vehicles | 30% annually | Power electronics | 2024-2030 |
Renewable Energy | 15% annually | Inverter components | 2024-2028 |
Flexible Electronics | 20% annually | Substrate materials | 2025-2030 |
Renewable energy component manufacturing requires materials that can withstand outdoor environmental conditions while maintaining electrical performance. Solar inverters and wind turbine electronics use zircon powder in components that must operate reliably for 20-25 years without maintenance.
Advanced packaging technologies for semiconductors increasingly rely on materials like zircon powder to achieve better thermal management and electrical isolation. Three-dimensional packaging architectures require materials that can handle complex thermal and electrical environments while maintaining dimensional stability.
Flexible electronics represent an emerging application area where zircon powder’s properties could provide advantages. The material’s ability to maintain electrical properties during mechanical stress makes it suitable for flexible circuit applications, though processing techniques must be adapted for flexible substrates.
Artificial intelligence and machine learning applications drive demand for high-performance computing components that generate significant heat. Zircon powder’s thermal management properties become increasingly valuable as processor power densities continue increasing.
Conclusion
Zircon powder delivers transformative benefits for electronic manufacturing through its unique combination of thermal, electrical, and mechanical properties. The material addresses critical challenges including thermal management, dimensional stability, and electrical insulation while enabling manufacturers to achieve higher performance standards. Companies implementing zircon powder typically see 60-70% reductions in defect rates and 140-225% improvements in component lifetime. Global Industry’s technical team provides comprehensive support for zircon powder implementation, from material selection through process optimization. Contact our electronic materials specialists today to evaluate how zircon powder can improve your manufacturing outcomes and product reliability.
FAQ Section
Q1: What purity level of zircon powder is required for electronic applications?
Electronic-grade zircon powder typically requires 99.5% or higher purity with strict limits on iron, titanium, and other metallic impurities. The exact specifications depend on the specific application, with semiconductor applications requiring the highest purity levels.
Q2: How does zircon powder compare to alumina in electronic applications?
Zircon powder offers superior thermal shock resistance and lower thermal expansion compared to alumina, making it ideal for applications with thermal cycling. However, alumina provides higher thermal conductivity, so the choice depends on specific performance requirements.
Q3: What are the typical particle size requirements for electronic manufacturing?
Electronic applications typically require zircon powder with particle sizes ranging from 0.5 to 10 micrometers, depending on the specific process. Finer particles provide better surface finish but may require different processing parameters.
Q4: Are there any environmental or safety concerns with zircon powder in electronics?
Zircon powder is generally considered safe for electronic applications when proper handling procedures are followed. It contains naturally occurring radioactive elements at very low levels, but these are well below regulatory limits for electronic use.
Q5: What is the typical shelf life and storage requirements for electronic-grade zircon powder?
Electronic-grade zircon powder has an indefinite shelf life when stored properly in dry conditions below 60% relative humidity. Moisture control is critical to prevent agglomeration and maintain processing characteristics.