Refractory materials form the backbone of high-temperature industrial processes. From steel production to glass manufacturing, these materials must withstand extreme conditions while maintaining structural integrity. The choice of raw materials directly impacts performance outcomes.
Zircon powder has emerged as a game-changing additive in refractory formulations. This naturally occurring mineral offers unique properties that address common challenges in high-temperature applications. Understanding these benefits helps procurement teams make informed decisions.
Modern industrial demands require refractories that perform longer, resist thermal shock better, and reduce maintenance costs. Zircon powder delivers on all these fronts through its exceptional thermal and chemical properties. The right material selection can transform operational efficiency.
This comprehensive guide examines how zircon powder enhances refractory performance across multiple dimensions. We’ll cover technical properties, cost implications, and practical implementation strategies. Every purchasing decision should be backed by solid technical understanding.
What Superior Properties Make Zircon Powder Ideal for Refractories?
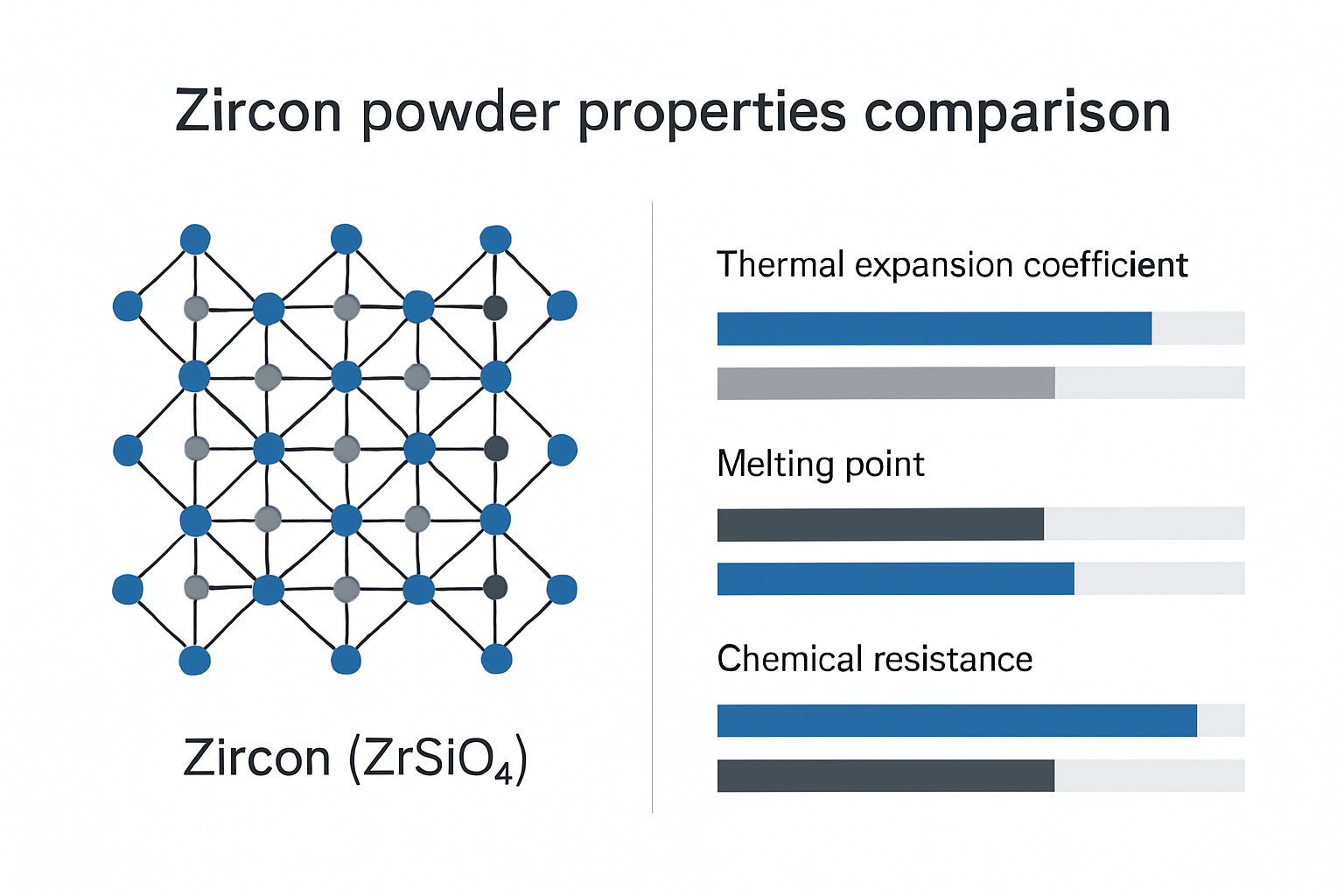
Zircon powder brings a unique combination of physical and chemical properties that make it exceptionally suited for refractory applications. These properties work together to create superior performance outcomes.
The fundamental advantage lies in zircon’s crystal structure. Zircon (ZrSiO₄) forms a stable tetragonal crystal system that maintains its integrity at extreme temperatures. This structural stability translates directly into enhanced refractory performance. Crystal structure determines thermal behavior under stress.
Thermal expansion characteristics set zircon apart from conventional refractory materials. With a coefficient of thermal expansion around 4.2 × 10⁻⁶/°C, zircon powder helps create refractories with minimal dimensional changes during heating and cooling cycles. Controlled expansion prevents cracking and extends service life.
Chemical inertness represents another critical advantage. Zircon powder resists attack from most acids, alkalis, and molten metals. This resistance stems from the strong covalent bonds within the zircon crystal lattice. Chemical stability ensures consistent performance in aggressive environments.
Property | Zircon Powder | Silica Sand | Alumina | Magnesia |
---|---|---|---|---|
Melting Point (°C) | 2,550 | 1,713 | 2,054 | 2,852 |
Thermal Expansion (×10⁻⁶/°C) | 4.2 | 14.0 | 8.8 | 13.5 |
Thermal Conductivity (W/m·K) | 5.8 | 1.4 | 35.0 | 38.0 |
Chemical Resistance | Excellent | Good | Very Good | Poor |
Thermal Shock Resistance | Excellent | Poor | Good | Fair |
Density plays a crucial role in refractory performance. Zircon powder has a high bulk density of approximately 4.7 g/cm³, which contributes to the formation of dense, low-porosity refractories. Dense structures resist penetration by molten materials and corrosive gases.
The particle size distribution of zircon powder can be precisely controlled during processing. This control allows manufacturers to optimize packing density and minimize porosity in the final refractory product. Proper particle sizing maximizes performance benefits.
Thermal shock resistance emerges from zircon’s low thermal expansion and high thermal conductivity. When refractories experience rapid temperature changes, zircon-containing formulations show superior resistance to cracking and spalling. Thermal shock resistance directly impacts maintenance schedules.
Mechanical strength at elevated temperatures distinguishes zircon-based refractories from alternatives. The material maintains significant strength even at temperatures approaching 1,500°C. High-temperature strength prevents structural failure during operation.
Zircon powder also exhibits excellent compatibility with various binder systems. Whether using clay bonds, chemical bonds, or ceramic bonds, zircon integrates well to form cohesive refractory structures. Binder compatibility ensures reliable manufacturing processes.
The low iron content in high-grade zircon powder prevents unwanted reactions that could compromise refractory performance. Iron impurities can form low-melting phases that reduce refractoriness. Purity levels directly affect high-temperature performance.
How Does Zircon Powder Enhance Temperature Resistance and Thermal Performance?
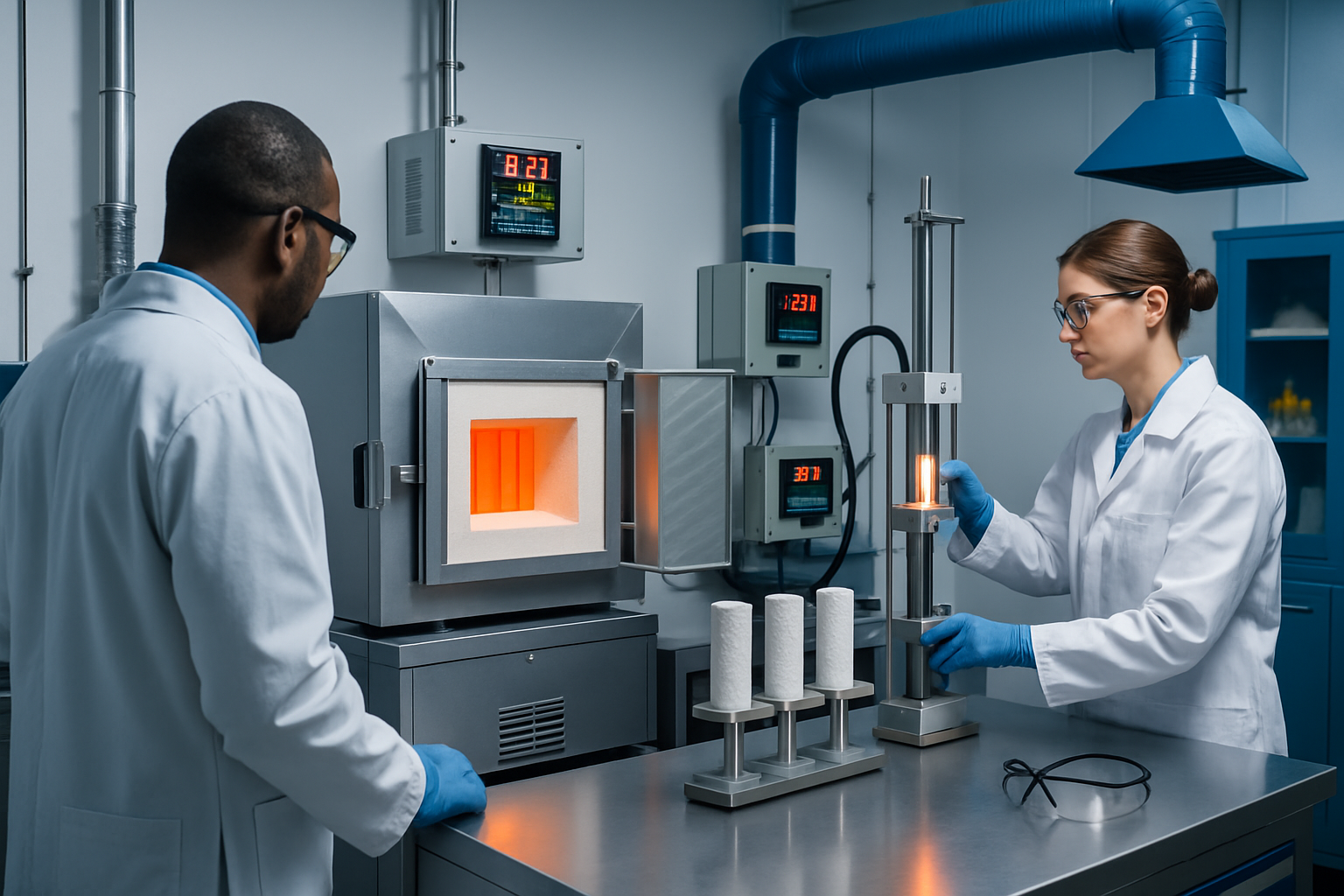
Temperature resistance forms the cornerstone of refractory performance, and zircon powder delivers exceptional benefits in this critical area. Superior temperature resistance translates to longer service life and reduced downtime.
The high melting point of zircon at 2,550°C provides substantial safety margins in most industrial applications. This temperature resistance allows refractories to operate safely at temperatures up to 1,800°C without approaching the material’s limits. Safety margins prevent catastrophic failures.
Thermal conductivity characteristics of zircon powder create unique advantages in refractory design. With moderate thermal conductivity of 5.8 W/m·K, zircon-based refractories provide controlled heat transfer. Controlled heat transfer optimizes energy efficiency.
The thermal diffusivity of zircon helps refractories respond appropriately to temperature changes. This property enables rapid heat distribution while preventing localized hot spots that could cause damage. Even heat distribution prevents stress concentrations.
Temperature Range (°C) | Zircon Performance | Typical Applications | Key Benefits |
---|---|---|---|
1,200-1,400 | Excellent | Glass furnaces | Low thermal expansion |
1,400-1,600 | Very Good | Steel ladles | Chemical resistance |
1,600-1,800 | Good | Blast furnaces | Thermal shock resistance |
1,800-2,000 | Fair | Special applications | High melting point |
Thermal cycling performance represents a critical test for refractory materials. Zircon powder helps refractories maintain integrity through repeated heating and cooling cycles. Thermal cycling resistance reduces replacement frequency.
The coefficient of thermal expansion remains remarkably stable across temperature ranges. This stability prevents the development of thermal stresses that could lead to cracking or spalling. Stable expansion characteristics ensure dimensional stability.
Heat capacity properties of zircon contribute to thermal management in refractory applications. The material’s ability to absorb and release heat helps moderate temperature fluctuations in industrial processes. Heat capacity provides thermal buffering effects.
Thermal shock resistance testing demonstrates zircon’s superiority over conventional materials. Standard test methods show that zircon-containing refractories can withstand temperature differentials of 1,000°C or more without failure. Thermal shock resistance prevents sudden failures.
The thermal gradient tolerance of zircon-based refractories allows for steep temperature profiles without structural damage. This tolerance is particularly valuable in applications where one face experiences extreme heat while the other remains relatively cool. Gradient tolerance enables versatile applications.
Creep resistance at high temperatures ensures that zircon-based refractories maintain their shape under load. This property prevents sagging or deformation that could compromise furnace geometry. Creep resistance maintains structural integrity.
Thermal aging characteristics show that zircon powder maintains its properties over extended exposure to high temperatures. Unlike some materials that degrade over time, zircon remains stable throughout its service life. Thermal stability ensures consistent performance.
What Durability Improvements and Service Life Extensions Can Be Expected?
Durability improvements represent one of the most compelling reasons to specify zircon powder in refractory applications. Extended service life directly impacts operational costs and productivity.
Corrosion resistance stands as a primary durability advantage. Zircon powder creates refractories that resist attack from molten metals, slags, and aggressive atmospheres. Corrosion resistance prevents premature deterioration.
The mechanism of corrosion resistance involves zircon’s stable crystal structure and low reactivity. When exposed to corrosive environments, zircon forms protective surface layers that prevent further attack. Protective layers maintain material integrity.
Erosion resistance benefits from zircon’s hardness and toughness. In applications where refractories face mechanical wear from moving materials or gas flows, zircon-based formulations show superior resistance to erosion. Erosion resistance maintains dimensional stability.
Durability Factor | Improvement with Zircon | Typical Service Life Extension | Cost Impact |
---|---|---|---|
Corrosion Resistance | 40-60% | 25-40% longer | 15-25% cost reduction |
Erosion Resistance | 30-50% | 20-35% longer | 10-20% cost reduction |
Thermal Shock | 50-70% | 30-50% longer | 20-30% cost reduction |
Chemical Attack | 35-55% | 25-45% longer | 15-25% cost reduction |
Spalling resistance improves significantly with zircon powder additions. Spalling occurs when surface layers separate from the main refractory body due to thermal or mechanical stresses. Spalling resistance prevents surface deterioration.
The microstructure of zircon-containing refractories contributes to enhanced durability. Dense, fine-grained structures resist penetration by corrosive agents and maintain structural integrity under stress. Microstructure optimization enhances all durability aspects.
Penetration resistance prevents molten materials from infiltrating the refractory structure. Zircon’s low porosity and chemical inertness create effective barriers against penetration. Penetration resistance preserves core material properties.
Oxidation resistance becomes important in applications involving oxygen-rich atmospheres. Zircon powder helps create refractories that resist oxidation-induced degradation. Oxidation resistance maintains performance in air-fired applications.
Alkali resistance addresses a common failure mode in many industrial processes. Alkali vapors can cause rapid deterioration of conventional refractories, but zircon-based formulations show excellent resistance. Alkali resistance prevents vapor-phase attack.
The fatigue resistance of zircon-containing refractories enables them to withstand cyclic loading without developing cracks. This property is particularly important in applications with frequent thermal cycling. Fatigue resistance prevents crack propagation.
Dimensional stability over time ensures that refractory linings maintain their intended geometry throughout their service life. Zircon powder helps prevent shrinkage, expansion, or warping that could compromise performance. Dimensional stability maintains system efficiency.
Long-term performance data from industrial installations demonstrates the durability benefits of zircon powder. Case studies show service life extensions of 25-50% compared to conventional refractory formulations. Field data validates laboratory predictions.
How Do Cost Savings and Economic Benefits Justify Zircon Powder Investment?
Economic considerations drive most refractory selection decisions, and zircon powder delivers compelling cost benefits despite higher initial material costs. Total cost of ownership analysis reveals significant savings.
Initial material costs for zircon powder typically run 2-3 times higher than conventional refractory raw materials. However, this premium is offset by performance improvements that reduce total system costs. Performance benefits justify premium pricing.
Labor cost reductions emerge from extended service life and reduced maintenance requirements. Fewer refractory replacements mean less downtime and lower labor costs for installation and removal. Reduced maintenance frequency cuts labor expenses.
Cost Category | Conventional Refractory | Zircon-Enhanced | Savings |
---|---|---|---|
Material Cost ($/ton) | 800-1,200 | 1,800-2,400 | -100% to -150% |
Installation Cost ($/m²) | 150-250 | 150-250 | 0% |
Service Life (months) | 12-18 | 18-27 | +50% to +75% |
Maintenance Cost ($/year) | 50,000-80,000 | 30,000-50,000 | 25% to 40% |
Total Annual Cost | 180,000-280,000 | 140,000-220,000 | 15% to 25% |
Energy efficiency improvements contribute to operational cost savings. Better thermal properties of zircon-based refractories can reduce energy consumption in heating applications. Energy savings accumulate over time.
Downtime reduction represents a major economic benefit. Extended service life means fewer planned shutdowns for refractory replacement. Reduced downtime maintains production schedules.
The productivity impact of improved refractory performance extends beyond direct cost savings. More reliable operation enables higher production rates and better product quality. Productivity improvements enhance competitiveness.
Inventory cost reductions result from longer service intervals. Facilities can reduce refractory inventory levels when replacement frequency decreases. Lower inventory requirements free up working capital.
Quality improvements in end products can result from better refractory performance. More stable thermal conditions and reduced contamination lead to higher product quality. Quality improvements increase product value.
Risk mitigation provides intangible but valuable economic benefits. More reliable refractories reduce the risk of unplanned shutdowns and emergency repairs. Risk reduction improves operational predictability.
Life cycle cost analysis demonstrates the economic advantages of zircon powder over 5-10 year periods. While initial costs are higher, total costs are typically 15-25% lower. Life cycle analysis reveals true economic benefits.
Return on investment calculations show payback periods of 12-24 months for zircon powder upgrades. The combination of extended service life and reduced maintenance costs drives rapid payback. Quick payback justifies investment decisions.
What Application-Specific Performance Gains Does Zircon Powder Provide?
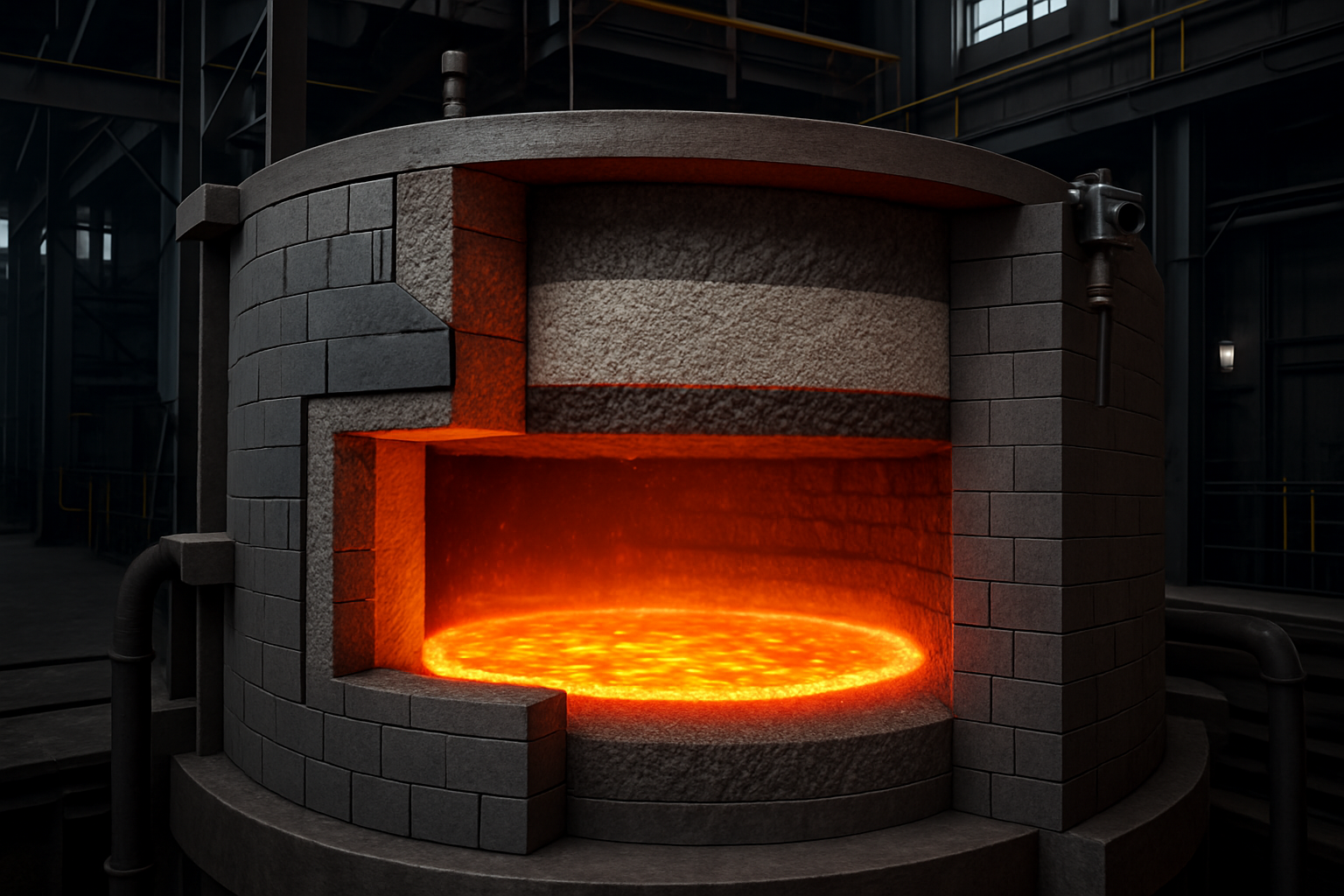
Different industrial applications present unique challenges that zircon powder addresses through specific performance improvements. Application-specific benefits maximize value in targeted uses.
Steel industry applications benefit from zircon’s resistance to iron oxide and slag attack. In ladle linings, zircon-based refractories show 30-50% longer service life compared to conventional materials. Steel industry benefits include extended campaign life.
Glass industry applications leverage zircon’s low thermal expansion and chemical inertness. Glass tank refractories containing zircon powder resist glass corrosion and maintain dimensional stability. Glass industry benefits focus on product quality.
Application | Primary Benefit | Performance Improvement | Typical Service Life |
---|---|---|---|
Steel Ladles | Slag resistance | 40-60% longer life | 150-200 heats |
Glass Tanks | Corrosion resistance | 30-50% longer life | 8-12 years |
Blast Furnaces | Thermal shock resistance | 25-40% longer life | 10-15 years |
Incinerators | Chemical resistance | 35-55% longer life | 3-5 years |
Petrochemical | High temperature stability | 30-45% longer life | 2-4 years |
Petrochemical applications require resistance to hydrocarbon cracking and sulfur compounds. Zircon powder helps create refractories that maintain integrity in these challenging environments. Petrochemical benefits include chemical stability.
Cement industry applications benefit from zircon’s resistance to alkali attack and thermal cycling. Kiln linings with zircon powder show improved resistance to alkali-induced deterioration. Cement industry benefits include alkali resistance.
Aluminum industry applications leverage zircon’s resistance to molten aluminum and fluoride-containing fluxes. Furnace linings show significantly extended service life with zircon additions. Aluminum industry benefits include flux resistance.
Power generation applications require refractories that withstand coal ash corrosion and thermal cycling. Zircon-based formulations show superior performance in these demanding conditions. Power generation benefits include ash resistance.
Incineration applications present extreme chemical challenges from waste combustion products. Zircon powder helps create refractories that resist acid gas attack and heavy metal corrosion. Incineration benefits include multi-chemical resistance.
Foundry applications benefit from zircon’s resistance to metal penetration and thermal shock. Furnace linings show improved performance and longer service life. Foundry benefits include metal resistance.
Non-ferrous metal applications require resistance to specific metal oxides and fluxes. Zircon powder provides tailored solutions for copper, lead, zinc, and other non-ferrous operations. Non-ferrous benefits include specialized resistance.
The customization potential of zircon powder allows optimization for specific application requirements. Different grades and particle sizes can be selected to maximize performance in targeted uses. Customization maximizes application-specific benefits.
How Do Different Zircon Powder Grades Compare for Refractory Selection?
Grade selection significantly impacts refractory performance, and understanding the differences between zircon powder grades enables optimal material specification. Grade selection determines performance outcomes.
Premium grade zircon powder contains 66-67% ZrO₂ with minimal impurities. This grade provides maximum performance benefits but commands premium pricing. Premium grades deliver maximum performance.
Standard grade zircon powder contains 65-66% ZrO₂ with slightly higher impurity levels. This grade offers excellent performance at moderate cost for most applications. Standard grades balance performance and cost.
Grade | ZrO₂ Content | TiO₂ Content | Fe₂O₃ Content | Al₂O₃ Content | Price Premium |
---|---|---|---|---|---|
Premium | 66-67% | <0.1% | <0.05% | <0.5% | 100% |
Standard | 65-66% | <0.2% | <0.1% | <1.0% | 85% |
Commercial | 64-65% | <0.3% | <0.15% | <1.5% | 70% |
Industrial | 63-64% | <0.5% | <0.2% | <2.0% | 55% |
Commercial grade zircon powder provides good performance for less demanding applications. With 64-65% ZrO₂ content, this grade offers cost-effective solutions for many industrial uses. Commercial grades suit moderate-duty applications.
Industrial grade zircon powder serves applications where cost is the primary consideration. While performance is reduced compared to higher grades, significant benefits remain versus conventional materials. Industrial grades provide entry-level benefits.
Particle size distribution varies among grades and affects refractory properties. Finer grades provide better packing density but may require different processing approaches. Particle size affects processing requirements.
Impurity levels determine high-temperature performance characteristics. Iron content particularly affects refractoriness and should be minimized for demanding applications. Impurity control ensures performance reliability.
The selection criteria for zircon powder grades depend on application requirements, performance expectations, and cost constraints. Grade selection requires application-specific analysis.
Processing requirements may vary among grades due to differences in particle size and surface characteristics. Higher grades often require less processing to achieve desired properties. Processing requirements affect total costs.
Quality consistency varies among suppliers and grades. Premium grades typically offer tighter specifications and more consistent quality. Quality consistency affects performance predictability.
Availability and supply chain considerations may influence grade selection. Some grades may have limited availability or longer lead times. Supply chain factors affect procurement decisions.
The performance-to-cost ratio varies among grades and applications. Detailed analysis helps identify the optimal grade for specific requirements. Performance-to-cost analysis guides selection.
What Installation and Handling Best Practices Optimize Zircon Powder Performance?
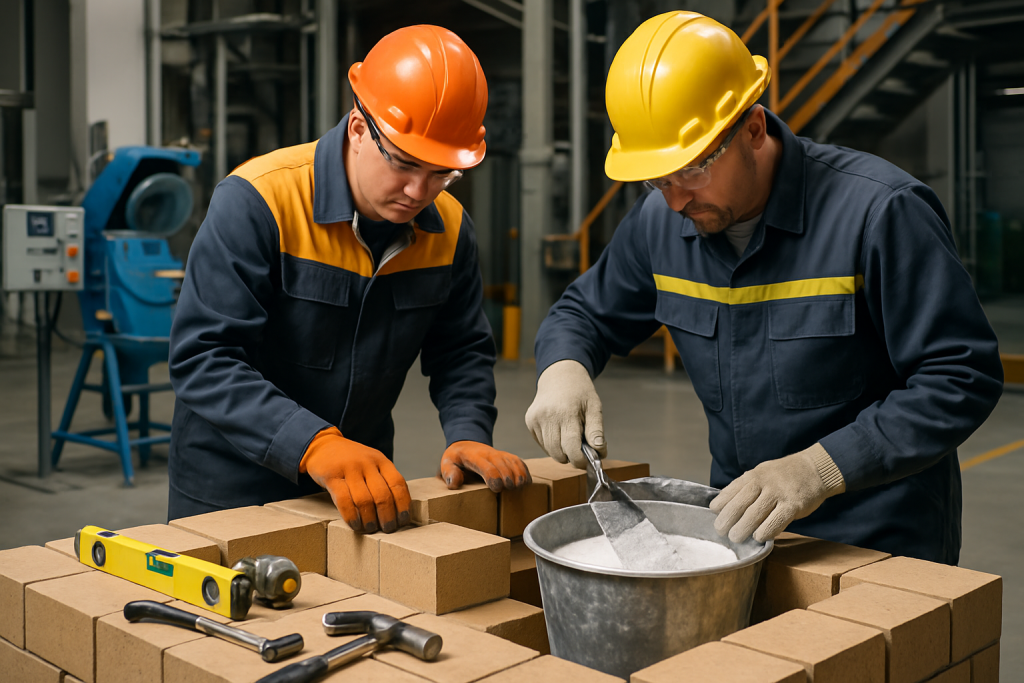
Proper installation and handling practices are essential to realize the full performance potential of zircon powder in refractory applications. Installation quality determines performance outcomes.
Storage requirements for zircon powder focus on moisture control and contamination prevention. The material should be stored in dry conditions with relative humidity below 60%. Proper storage maintains material quality.
Mixing procedures require careful attention to achieve uniform distribution throughout the refractory mix. Dry blending for 5-10 minutes followed by wet mixing ensures proper dispersion. Uniform mixing ensures consistent performance.
Installation Parameter | Recommended Value | Critical Factor | Impact on Performance |
---|---|---|---|
Moisture Content | <1.0% | Water control | Prevents steam damage |
Mixing Time | 8-12 minutes | Uniformity | Ensures consistent properties |
Placement Temperature | 15-25°C | Workability | Affects installation quality |
Curing Time | 24-48 hours | Strength development | Determines initial strength |
Drying Rate | 25-50°C/hour | Crack prevention | Prevents thermal shock |
Water content control during mixing prevents steam-related damage during initial heating. Excess moisture can cause explosive spalling when converted to steam. Moisture control prevents installation failures.
Placement techniques should ensure proper compaction without segregation. Vibration or tamping helps achieve target density while maintaining uniform composition. Proper placement optimizes density.
Curing procedures allow proper strength development before exposure to high temperatures. Adequate curing time ensures that binder systems develop full strength. Proper curing ensures structural integrity.
Drying schedules must be carefully controlled to prevent thermal shock during initial heating. Gradual temperature increases allow moisture removal without damage. Controlled drying prevents cracking.
Quality control testing during installation verifies that specifications are met. Density measurements, strength tests, and composition analysis ensure proper installation. Quality control validates installation success.
Joint design considerations account for thermal expansion and contraction. Proper joint spacing and sealing prevent stress concentrations. Joint design accommodates thermal movement.
Surface preparation requirements ensure good bonding between new and existing refractories. Clean, sound surfaces provide optimal adhesion. Surface preparation ensures bonding.
Tool requirements for installation may differ from conventional refractories due to zircon’s hardness. Appropriate cutting and shaping tools prevent damage during installation. Proper tools ensure installation quality.
Safety considerations include dust control and personal protective equipment. Zircon powder can create respirable dust that requires appropriate controls. Safety measures protect installation personnel.
Inspection procedures verify installation quality and identify potential issues before startup. Visual inspection, dimensional checks, and non-destructive testing ensure proper installation. Inspection prevents startup problems.
Conclusion
Zircon powder delivers substantial performance improvements in refractory applications through its unique combination of thermal, chemical, and mechanical properties. The evidence clearly supports zircon powder’s value proposition.
The superior temperature resistance, enhanced durability, and extended service life justify the premium cost of zircon powder. Economic analysis consistently shows positive returns on investment through reduced maintenance costs and improved operational reliability. Economic benefits validate the investment decision.
Application-specific performance gains demonstrate zircon powder’s versatility across diverse industrial sectors. From steel production to glass manufacturing, the material provides tailored solutions for challenging high-temperature environments. Versatility enables broad application.
Grade selection and proper installation practices are critical to realizing full performance potential. Understanding the differences among grades and following best practices ensures optimal results. Proper implementation maximizes benefits.
The future of refractory technology increasingly points toward advanced materials like zircon powder that deliver superior performance and economic value. Advanced materials drive industry progress.
For procurement professionals evaluating refractory options, zircon powder represents a proven solution that balances performance, durability, and cost-effectiveness. Zircon powder offers compelling value for informed buyers.
FAQ Section
Q1: What is the typical cost premium for zircon powder compared to conventional refractory materials?
Zircon powder typically costs 2-3 times more than conventional refractory raw materials. However, the extended service life and reduced maintenance requirements often result in 15-25% lower total cost of ownership over the refractory’s lifetime.
Q2: How much longer do zircon-based refractories last compared to standard formulations?
Service life extensions of 25-50% are typical for zircon-based refractories compared to conventional formulations. In some applications, such as steel ladles, improvements of 40-60% have been documented.
Q3: What applications benefit most from zircon powder additions?
Steel industry ladles, glass tank refractories, and blast furnace linings show the greatest benefits from zircon powder. These applications involve severe thermal cycling, chemical attack, and mechanical stress that highlight zircon’s advantages.
Q4: Are there any special handling requirements for zircon powder?
Zircon powder requires standard industrial hygiene practices including dust control and personal protective equipment. Storage should maintain moisture content below 1% to prevent processing issues and ensure optimal performance.
Q5: How do I select the right grade of zircon powder for my application?
Grade selection depends on temperature requirements, chemical environment, and cost constraints. Premium grades (66-67% ZrO₂) suit the most demanding applications, while standard grades (65-66% ZrO₂) provide excellent performance for most industrial uses.