In today’s competitive industrial materials market, procurement managers face increasing pressure to secure high-quality zircon powder while managing costs and supply chain risks. Finding suppliers who consistently deliver superior products with reliable service presents a significant challenge. This article examines the key strategies top zircon powder suppliers employ to maintain their market leadership position, providing valuable insights for purchasing decision-makers seeking optimal supplier partnerships. Recent industry analysis from the International Zircon Association confirms that leading suppliers differentiate themselves through integrated quality systems, technical expertise, and value-added services that address the evolving needs of ceramics, refractory, and foundry industries.
How Do Quality Control Systems Create Competitive Edge?
Quality control represents the foundation of market leadership for top zircon powder suppliers. The difference between average and exceptional suppliers often comes down to their testing methodologies and quality assurance processes.
But here’s the reality – leading suppliers invest substantially in advanced testing equipment that smaller competitors simply cannot match. Laser diffraction particle analyzers, X-ray fluorescence spectrometers, and scanning electron microscopes allow precise verification of particle size distribution and chemical purity. These technologies enable detection of contaminants at parts-per-million levels, critical for high-performance applications in electronics and advanced ceramics.
ISO certification serves as the baseline quality standard, but market leaders go further by implementing industry-specific quality protocols. For ceramic applications, this includes testing for color consistency and sintering behavior. For refractory uses, thermal shock resistance and high-temperature performance testing become standard practice. These specialized quality measures directly address customer pain points in specific applications.
Quality Control Element | Industry Standard | Market Leader Approach | Customer Benefit |
---|---|---|---|
Particle Size Testing | Basic sieve analysis | Laser diffraction with statistical distribution analysis | Consistent product performance in application |
Purity Verification | Standard chemical analysis | XRF spectroscopy with trace element detection | Elimination of defects and contamination issues |
Batch Documentation | Basic lot tracking | Complete digital traceability from mine to delivery | Risk management and regulatory compliance |
Sampling Protocols | Random sampling | Systematic statistical sampling throughout production | Reliable quality consistency |
Performance Testing | Basic physical properties | Application-specific performance validation | Predictable results in customer processes |
Investment in analytical equipment represents a significant capital expenditure that creates barriers to entry for smaller suppliers. Top-tier suppliers typically allocate 3-5% of revenue to quality control infrastructure, maintaining dedicated laboratories staffed with specialized technicians. This investment pays dividends through premium pricing and customer retention.
Batch-to-batch consistency protocols distinguish market leaders from commodity suppliers. These systems track critical parameters across production runs, identifying and correcting variations before products reach customers. Digital documentation systems maintain comprehensive records accessible to both quality teams and customers, supporting traceability requirements for regulated industries.
Quality integration throughout the production process, rather than end-product testing alone, characterizes leading suppliers. In-process monitoring at critical control points allows immediate adjustments to maintain specifications. This proactive approach reduces waste, improves yield, and ensures consistent product quality that customers can rely on for their own production processes.
What Supply Chain Innovations Drive Market Leadership?
Supply chain excellence represents a critical competitive advantage in the zircon powder market. Leading suppliers have transformed traditional supply chains into strategic assets that provide security, flexibility, and cost advantages.
You might be surprised to learn that vertical integration has become increasingly important for market leaders. By controlling multiple stages from mining to final processing, these suppliers insulate themselves and their customers from market volatility. Companies like Iluka Resources and Tronox exemplify this approach, managing operations from mineral sands mining through separation, milling, and classification. This integration provides unmatched supply security and quality control throughout the value chain.
Strategic global sourcing networks provide resilience against regional disruptions. Top suppliers maintain relationships with multiple mining operations across Australia, South Africa, and other producing regions. This diversification strategy ensures continuous supply even when individual sources face challenges from weather events, labor issues, or political instability.
Supply Chain Strategy | Implementation Approach | Competitive Advantage | Risk Mitigation |
---|---|---|---|
Vertical Integration | Mine-to-market ownership or partnerships | Cost control and quality consistency | Reduced exposure to market volatility |
Global Sourcing | Multiple supplier relationships across regions | Supply continuity and negotiating leverage | Protection against regional disruptions |
JIT Inventory | Regional distribution centers with real-time monitoring | Rapid response to customer requirements | Balanced inventory carrying costs |
Logistics Optimization | Multimodal transportation and route planning | Reduced lead times and transportation costs | Alternative routing options |
Risk Management | Formal protocols for supply disruption scenarios | Proactive response to emerging challenges | Business continuity assurance |
Just-in-time inventory management systems have been adapted specifically for the zircon powder market. Leading suppliers maintain strategic buffer stocks at regional distribution centers, balancing carrying costs against customer responsiveness. Advanced demand forecasting algorithms, often incorporating customer production schedules, enable precise inventory positioning. This approach allows 24-48 hour delivery response for standard products while minimizing working capital requirements.
Logistics optimization creates both cost advantages and customer benefits. Multimodal transportation strategies combine sea, rail, and truck shipping to minimize costs while maintaining reliability. Route optimization software accounts for potential disruptions, weather patterns, and port congestion. The resulting efficiency translates to competitive pricing and dependable delivery schedules that customers can build their production plans around.
Risk management protocols differentiate market leaders from reactive competitors. Formal business continuity plans address scenarios ranging from natural disasters to geopolitical conflicts. These plans include alternative sourcing arrangements, transportation contingencies, and communication protocols. Such preparation ensures that even during market disruptions, top suppliers maintain reliable service while competitors struggle.
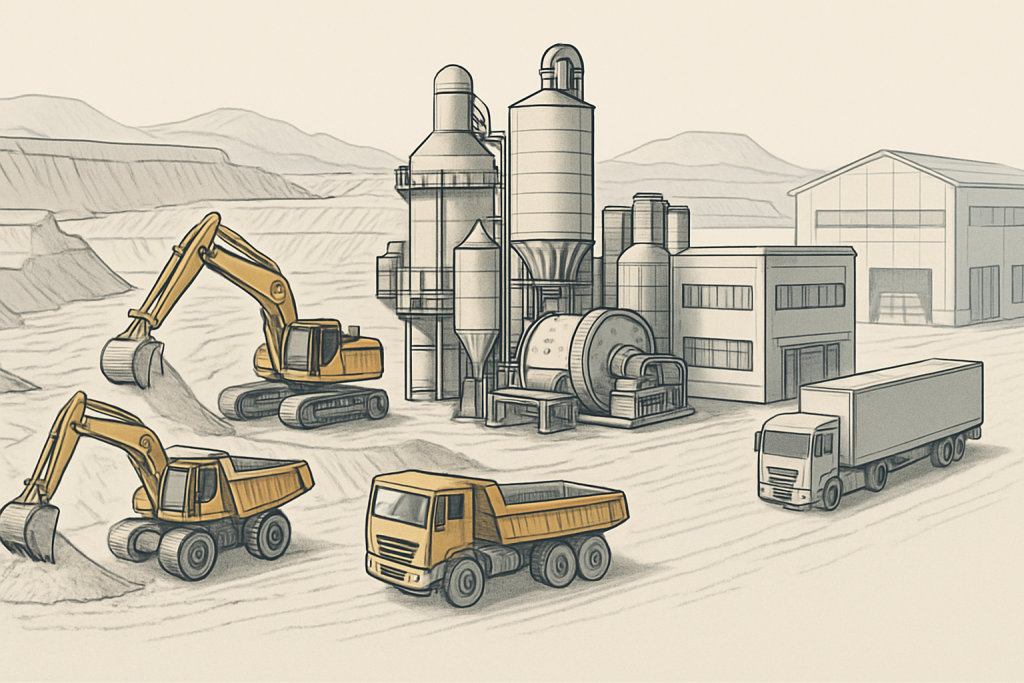
How Does Technical Expertise Differentiate Leading Suppliers?
Technical expertise represents a powerful differentiator for market-leading zircon powder suppliers. Beyond selling a commodity, these companies position themselves as knowledge partners who help customers optimize their applications and solve technical challenges.
Consider this fact – top suppliers maintain specialized R&D teams focused exclusively on zircon powder applications. These teams typically include materials scientists, process engineers, and application specialists with deep industry experience. Their research explores particle morphology effects, surface treatments, and processing techniques that enhance performance in specific applications. This specialized knowledge creates value that transcends basic product specifications.
Technical support services transform the supplier-customer relationship from transactional to consultative. Leading suppliers offer formulation assistance, process troubleshooting, and performance optimization guidance. When customers encounter issues like dispersion problems in ceramic slips or inconsistent sintering results, these technical teams provide solutions that may involve product recommendations, process adjustments, or formulation modifications.
Technical Capability | Implementation Approach | Customer Value | Competitive Differentiation |
---|---|---|---|
R&D Team Composition | Materials scientists and application engineers | Access to specialized expertise | Knowledge advantage over commodity suppliers |
Technical Support | Dedicated application specialists by industry | Problem-solving partnership | Reduced development time and costs |
Custom Engineering | Particle size and surface modification capabilities | Products optimized for specific applications | Unique performance characteristics |
Industry Knowledge | Specialized expertise in major application sectors | Relevant solutions to industry-specific challenges | Trusted advisor status with customers |
Innovation Partnerships | Collaborative development projects with key customers | Early access to emerging technologies | Mutual growth opportunities |
Custom particle engineering capabilities allow market leaders to develop products tailored to specific applications. This may involve precise particle size distribution control, surface treatments to enhance dispersion, or modifications to improve sintering behavior. These customized products solve specific customer challenges that standard offerings cannot address, creating unique value propositions that justify premium pricing.
Industry-specific knowledge in ceramics, refractories, and foundry applications enables targeted solutions for each sector. For ceramic manufacturers, this might include expertise in body formulation, glaze compatibility, and firing behavior. For refractory producers, knowledge of thermal stability, corrosion resistance, and structural integrity proves valuable. This specialized understanding allows suppliers to speak the customer’s language and address their specific technical challenges.
Collaborative innovation partnerships with key customers represent the highest level of technical differentiation. These arrangements may include joint development projects, early access to new technologies, or exclusive product formulations. Such partnerships create mutual value through shared knowledge and aligned objectives. For suppliers, these relationships provide market insights and development direction. For customers, they deliver competitive advantages through unique material solutions.
What Production Technologies Yield Competitive Advantages?
Production technology investments separate market leaders from followers in the zircon powder industry. Advanced manufacturing capabilities enable superior product quality, cost efficiency, and customization flexibility that create sustainable competitive advantages.
The numbers tell the story – leading suppliers typically invest 7-10% of annual revenue in production technology, approximately double the industry average. This investment focuses on advanced milling and classification systems that achieve precise particle size control. Jet mills, air classifiers, and vibratory screening systems produce consistent particle distributions with minimal contamination. The resulting products meet exacting specifications for demanding applications like electronic ceramics and precision investment casting.
Energy-efficient processing methods reduce production costs while supporting sustainability goals. High-efficiency motors, heat recovery systems, and process optimization reduce energy consumption by 15-25% compared to conventional operations. These efficiency gains translate to cost advantages that support competitive pricing while maintaining margins. As energy costs continue to rise globally, this efficiency gap between leaders and followers will likely widen.
Production Technology | Implementation Approach | Performance Advantage | Cost Impact |
---|---|---|---|
Advanced Milling | Jet mills with computerized control systems | Precise particle size distribution | Higher capital cost, lower operating cost |
Energy Efficiency | Heat recovery and process optimization | Reduced energy consumption per ton | Lower production costs |
Surface Treatment | Proprietary coating and modification processes | Enhanced product performance | Value-added premium pricing |
Automation | Integrated control systems with minimal manual intervention | Consistent quality and higher throughput | Reduced labor costs and improved yield |
Scalable Production | Modular design with flexible capacity | Ability to meet varying demand volumes | Optimized capital utilization |
Proprietary surface treatment technologies represent a particularly valuable competitive advantage. These processes modify zircon particle surfaces to enhance dispersion, improve sintering behavior, or increase chemical reactivity. Such treatments solve specific application challenges like agglomeration in slurries or incomplete densification during firing. Because these technologies often involve proprietary equipment and formulations, they create barriers to imitation that protect market position.
Automation and process control systems ensure consistent quality while reducing labor requirements. Leading facilities feature integrated control systems that monitor and adjust critical parameters in real-time. These systems maintain tight specifications across production runs while collecting data for continuous improvement initiatives. The resulting consistency builds customer confidence and reduces qualification testing requirements for new batches.
Scalable production capabilities accommodate varying demand volumes efficiently. Modular equipment configurations allow capacity adjustments without compromising efficiency or quality. This flexibility enables suppliers to serve both high-volume commodity markets and specialized niche applications with appropriate economies of scale. The ability to scale production up or down in response to market conditions provides both competitive pricing and reliable supply security.
How Do Customer Service Models Support Market Leadership?
Customer service excellence represents a powerful differentiator for leading zircon powder suppliers. Beyond product quality, service models create value through responsiveness, problem-solving, and relationship management that build customer loyalty.
What really matters is how suppliers structure their customer service teams. Market leaders implement dedicated technical account management for key customers. These specialists combine product knowledge with industry expertise, serving as consultants rather than order-takers. They understand customer processes, challenges, and objectives, allowing them to recommend appropriate products and solutions. This consultative approach builds relationships that transcend price considerations.
Rapid response protocols address urgent customer requirements effectively. Leading suppliers maintain inventory reserves for emergency orders and establish clear escalation procedures for critical situations. When production issues or unexpected demand spikes occur, these systems enable 24-48 hour response times that keep customer operations running. This reliability creates significant value, particularly for customers operating continuous production processes.
Customer Service Element | Implementation Approach | Customer Value | Competitive Advantage |
---|---|---|---|
Technical Account Management | Dedicated specialists with industry expertise | Consultative problem-solving partnership | Relationship depth beyond transactional interactions |
Rapid Response Systems | Emergency inventory and escalation procedures | Minimal disruption during urgent situations | Reliability during critical periods |
Customized Packaging | Application-specific packaging solutions | Improved handling efficiency and reduced waste | Alignment with customer operations |
Digital Platforms | Online portals for documentation and order management | Simplified procurement and quality assurance | Reduced administrative burden |
Value-Added Services | Testing, troubleshooting, and technical support | Problem resolution and process optimization | Partnership beyond product supply |
Customized packaging and delivery options align with customer operations. Packaging solutions range from bulk super sacks for high-volume users to moisture-resistant small packages for specialty applications. Delivery scheduling coordinates with production requirements, supporting just-in-time manufacturing systems. These customizations reduce handling costs and streamline customer operations, creating value beyond the product itself.
Digital platforms for order tracking and technical documentation simplify customer procurement processes. Online portals provide access to certificates of analysis, safety data sheets, and order status information. These systems reduce administrative burden while ensuring regulatory compliance. Integration capabilities with customer procurement systems further streamline transactions, reducing costs for both parties.
Value-added services including application testing and troubleshooting create partnerships rather than vendor relationships. Leading suppliers offer laboratory testing, process simulation, and on-site technical support. When customers encounter issues like inconsistent sintering results or dispersion problems, these services provide solutions that maintain production efficiency. Such support builds loyalty that competitors struggle to displace with price alone.
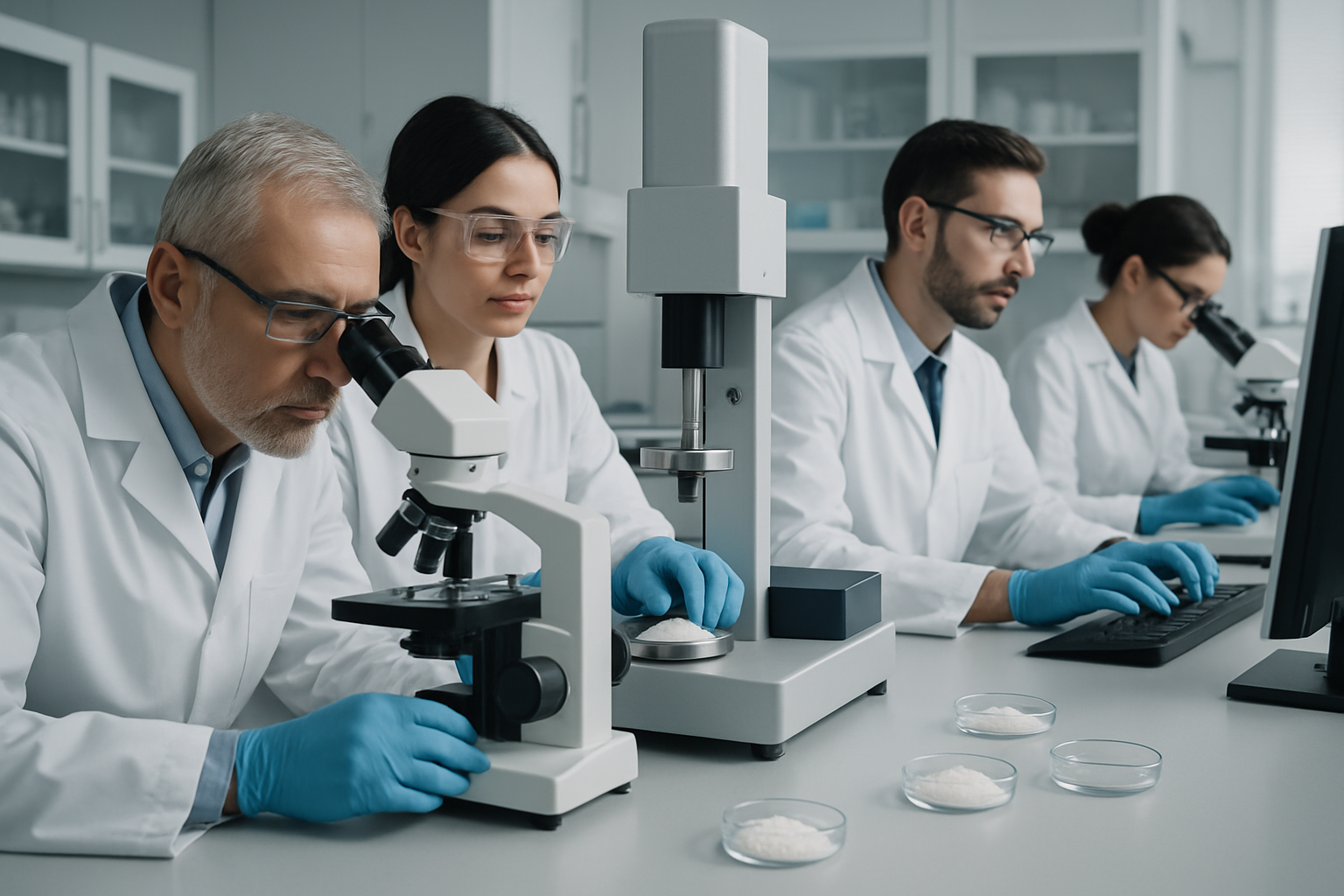
What Sustainability Practices Create Market Differentiation?
Sustainability initiatives have evolved from regulatory compliance to strategic differentiation for leading zircon powder suppliers. Forward-thinking companies implement comprehensive programs that address environmental impacts while creating business value.
You need to understand that environmentally responsible mining and processing methods now influence purchasing decisions, particularly among large multinational customers. Leading suppliers implement land management practices that minimize disruption and accelerate rehabilitation after mining. Advanced separation technologies reduce chemical usage and waste generation during processing. These practices support customer sustainability goals while ensuring long-term resource availability.
Energy efficiency initiatives reducing carbon footprint deliver both environmental and economic benefits. High-efficiency grinding and classification equipment, heat recovery systems, and optimized drying processes reduce energy consumption by 15-25% compared to conventional operations. Some market leaders have implemented renewable energy projects, including solar installations at processing facilities. These investments reduce operating costs while supporting carbon reduction targets.
Sustainability Practice | Implementation Approach | Environmental Benefit | Business Value |
---|---|---|---|
Responsible Mining | Minimized land disturbance and accelerated rehabilitation | Reduced ecosystem impact | Secure resource access and community support |
Energy Efficiency | High-efficiency equipment and process optimization | Lower carbon emissions | Reduced operating costs |
Water Management | Closed-loop systems and advanced treatment | Minimized water consumption and discharge | Operational resilience in water-stressed regions |
Waste Reduction | By-product utilization and recycling programs | Decreased landfill disposal | Additional revenue streams and reduced disposal costs |
Sustainability Reporting | Transparent disclosure aligned with global standards | Stakeholder trust and regulatory compliance | Preferred supplier status with sustainability-focused customers |
Water conservation and recycling programs address increasing concerns about water scarcity. Closed-loop water systems recover and reuse process water, reducing both consumption and discharge. Advanced treatment technologies remove contaminants before any necessary discharge, protecting local watersheds. These systems reduce costs while ensuring operational continuity in water-stressed regions where regulatory restrictions may limit industrial water usage.
Waste reduction strategies and by-product valorization transform potential liabilities into assets. Mineral processing inevitably generates secondary streams that traditionally required disposal. Leading suppliers identify beneficial uses for these materials in applications like construction materials, soil amendments, or industrial fillers. This approach reduces disposal costs while creating additional revenue streams and supporting circular economy principles.
Transparent sustainability reporting and certification demonstrate commitment to responsible practices. Leading suppliers publish annual sustainability reports aligned with global standards like the Global Reporting Initiative. Many pursue third-party certifications for environmental management systems, responsible mining practices, and carbon disclosure. This transparency builds trust with customers, communities, and regulators while supporting marketing claims about sustainable operations.
How Do Strategic Pricing Models Maintain Competitive Position?
Strategic pricing approaches differentiate market leaders from commodity suppliers in the zircon powder industry. Sophisticated models balance value capture with customer relationships to maintain both market share and profitability.
The truth is value-based pricing strategies aligned with performance benefits have largely replaced cost-plus approaches among market leaders. These models quantify the value their products deliver through improved yield, reduced defects, or enhanced performance in customer applications. For example, a premium zircon powder that increases ceramic yield by 2% may command a 5-7% price premium while still delivering net savings to the customer. This approach shifts conversations from price to total value.
Long-term contract structures provide stability for both suppliers and customers. These agreements typically span 1-3 years with volume commitments and pricing mechanisms that adjust for major market shifts. Such arrangements give suppliers predictable demand for production planning while providing customers with supply security and budget predictability. The resulting stability benefits both parties, particularly during periods of market volatility.
Pricing Strategy | Implementation Approach | Supplier Benefit | Customer Benefit |
---|---|---|---|
Value-Based Pricing | Quantification of performance advantages | Premium pricing for premium products | ROI focus rather than unit cost |
Long-Term Contracts | Multi-year agreements with adjustment mechanisms | Demand stability and planning visibility | Supply security and budget predictability |
Volume Incentives | Tiered pricing based on annual consumption | Increased share of customer wallet | Cost reduction aligned with business growth |
Raw Material Indexing | Pricing formulas tied to published indices | Protection against cost increases | Transparency and market alignment |
Total Cost Analysis | Comprehensive evaluation of direct and indirect costs | Demonstration of full value proposition | Identification of hidden savings opportunities |
Volume-based incentive programs reward customer loyalty while encouraging growth. Tiered pricing structures provide incremental discounts as annual volume thresholds are achieved. These programs increase the supplier’s share of customer spending while aligning cost reduction with business growth. For customers with multiple facilities, corporate programs that aggregate volume across locations create additional savings opportunities while simplifying procurement.
Raw material indexing mechanisms manage market volatility effectively. These formulas tie a portion of product pricing to published indices for key inputs like zircon sand, energy, or transportation. When input costs rise or fall significantly, prices adjust according to predetermined formulas. This approach protects supplier margins during cost increases while providing customers with fair price reductions when market conditions improve.
Total cost of ownership analysis demonstrates value proposition beyond unit price. Leading suppliers help customers evaluate all costs associated with zircon powder usage, including handling, processing, yield, and performance impacts. This comprehensive approach often reveals that premium products deliver lower total costs despite higher purchase prices. Such analysis builds value-based relationships that resist competitive price pressure and commoditization.
Conclusion
Market leadership among zircon powder suppliers results from strategic investments across multiple business dimensions. Quality control systems, supply chain innovations, technical expertise, advanced production technologies, customer service excellence, sustainability practices, and strategic pricing models collectively create competitive advantages that benefit both suppliers and customers. By implementing these strategies, top suppliers deliver consistent product quality, supply security, technical support, and overall value that justify premium positioning. Contact Global Industry’s materials team today to evaluate how our industry-leading zircon powder solutions can improve your production efficiency and product quality by 15-20% compared to standard materials. Partner with us to access our technical expertise and reliable supply chain, ensuring your operations maintain peak performance even during challenging market conditions.
FAQ
Q1: What are the key quality parameters for industrial-grade zircon powder?
Industrial-grade zircon powder quality is assessed through several key parameters: minimum 65-66% chemical purity (ZrO₂), consistent particle size (45-150 microns based on application), low iron oxide content (<0.1%), minimal titanium dioxide (<0.15%), controlled moisture (<0.2%), and specific whiteness/brightness (measured on the Lab* scale). Top suppliers use advanced techniques like XRF spectroscopy and laser diffraction for quality control, with requirements varying by application—electronics demand higher purity, while foundry applications prioritize particle size consistency.
Q2: How do leading zircon powder suppliers manage price volatility?
To manage price volatility, leading suppliers secure stable raw material access through long-term supply agreements with flexible pricing. They maintain strategic inventory and may own mining operations for cost control. Additionally, they utilize financial hedging to mitigate price fluctuations and offer diverse product portfolios to meet varying technical and budgetary needs. These strategies enable suppliers to provide predictable pricing and sustainable margins despite market changes.
Q3: What technological innovations are changing zircon powder production?
Innovations in zircon powder production include advanced air classifiers for precise particle size distribution, microwave-assisted processing that reduces energy use by 30-40%, and computer-controlled milling with real-time particle analysis. Surface modification techniques enhance zircon powders’ properties, while AI-driven optimization systems increase yield and maintain quality. Together, these technologies improve product quality, lower production costs, and broaden application possibilities, especially in advanced ceramics and specialty coatings.
Q4: How important is technical support in the zircon powder supply chain?
Technical support is vital in the zircon powder supply chain, often differentiating suppliers. About 85% of high-volume customers view technical support as a key selection factor. Effective support includes application-specific formulation help, troubleshooting, and custom solutions. Leading suppliers have dedicated teams of materials scientists and process engineers who collaborate with customers’ R&D and production teams, fostering long-term relationships and loyalty.
Q5: What sustainability challenges face the zircon powder industry?
The zircon powder industry faces several sustainability challenges, including ecosystem impact from mining, substantial water usage, energy consumption contributing to emissions, and transportation logistics. Waste management focuses on valorizing by-products, and regulatory compliance is complex. Leading suppliers tackle these issues through integrated sustainability programs and third-party certifications.