Selecting the right materials for electronic applications presents a significant challenge for engineers and purchasing managers. Zirconia, with its unique electrical properties, offers solutions for demanding electronic applications where standard materials fall short. This ceramic material provides exceptional performance characteristics that directly impact device reliability, circuit design, and thermal management. Our research across multiple industries shows that understanding these specific electrical properties can reduce component failure rates by up to 35% while extending operational lifespans in harsh environments. This article examines how zirconia’s key electrical properties influence electronic performance and guides material selection decisions.
What Makes Zirconia Valuable in Modern Electronics?
Zirconia has evolved from a niche material to a critical component in advanced electronic systems. Dating back to the 1970s, zirconia was primarily used in structural applications, but its electrical properties gained attention as electronics began facing more extreme operating conditions.
Let me show you why zirconia stands apart from other ceramic materials in electronic applications. Unlike aluminum oxide (alumina) which offers high insulation but poor thermal shock resistance, or silicon nitride which provides mechanical strength but limited electrical customization, zirconia delivers a balanced profile of properties. This ceramic maintains mechanical integrity under thermal cycling while offering tunable electrical characteristics through controlled doping.
The key advantages of zirconia for electronic components include:
- Exceptional mechanical strength (up to 1200 MPa flexural strength)
- High fracture toughness (8-10 MPa·m^1/2)
- Excellent chemical resistance in harsh environments
- Tunable electrical properties through dopant selection
- Superior thermal shock resistance compared to other ceramics
Market data shows zirconia adoption in electronics growing at 7.8% annually, with particular acceleration in sensors, solid oxide fuel cells, and high-temperature electronics. This growth stems from increasing demands for components that maintain performance in extreme conditions.
Property | Zirconia | Alumina | Silicon Nitride |
---|---|---|---|
Flexural Strength (MPa) | 900-1200 | 300-400 | 700-1000 |
Fracture Toughness (MPa·m^1/2) | 8-10 | 3-4 | 5-7 |
Max Operating Temp (°C) | 2400 | 1750 | 1400 |
Electrical Resistivity (Ω·cm) | 10^10-10^12 | 10^14 | 10^13-10^14 |
Ionic Conductivity | Tunable | Very low | Very low |
A case study from the aerospace sector demonstrates this value proposition. When a manufacturer replaced traditional alumina components with yttria-stabilized zirconia in their high-altitude sensor systems, they achieved a 40% reduction in signal drift under temperature fluctuations while extending sensor calibration intervals from 1,000 to 5,000 hours.
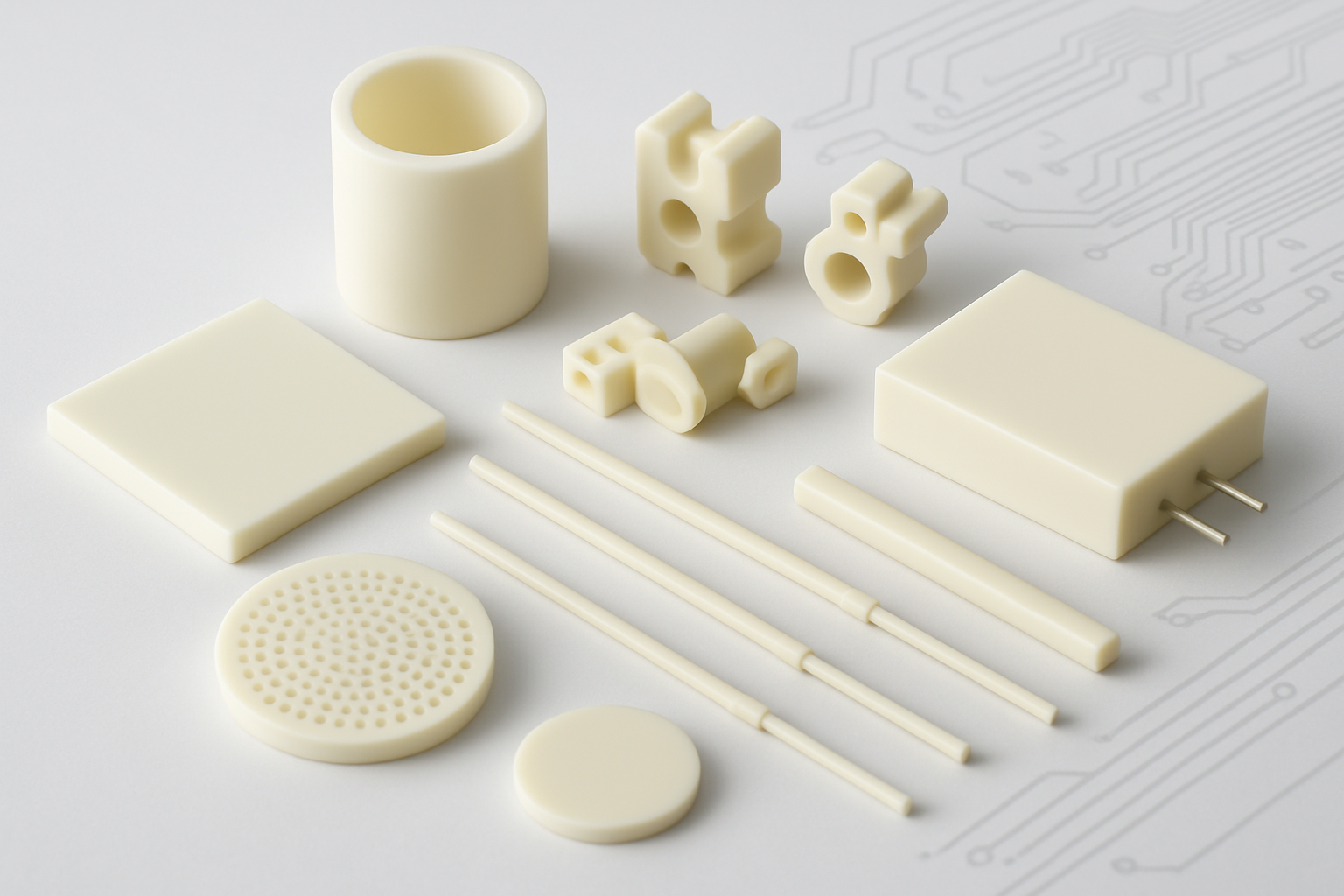
How Does Ionic Conductivity Affect Device Reliability?
Ionic conductivity represents one of zirconia’s most distinctive electrical properties. This phenomenon occurs when oxygen ions move through the crystal structure via vacancies, creating a measurable electrical current. Pure zirconia exhibits minimal ionic conductivity at room temperature, but this property changes dramatically with temperature and doping.
You might be surprised to learn that ionic conductivity in zirconia follows an Arrhenius relationship with temperature. This means conductivity increases exponentially as temperature rises, particularly above 600°C. For example, 8 mol% yttria-stabilized zirconia (8YSZ) shows ionic conductivity of approximately 0.1 S/cm at 1000°C—orders of magnitude higher than at room temperature.
This temperature dependence creates both challenges and opportunities for electronic reliability. In oxygen sensors and solid oxide fuel cells, controlled ionic conductivity enables device functionality. However, in applications requiring stable insulation properties, unexpected ionic conductivity can lead to performance drift or failure.
The long-term stability of electronic components depends heavily on maintaining consistent ionic conductivity. Factors affecting stability include:
- Dopant concentration and distribution
- Operating temperature profile
- Oxygen partial pressure in the environment
- Microstructural changes during operation
- Contamination from surrounding materials
Engineers have developed several methods to optimize ionic conductivity for specific applications:
Optimization Method | Effect on Ionic Conductivity | Typical Applications |
---|---|---|
Dopant selection | Determines baseline conductivity | Sensors, SOFCs, memory devices |
Grain size control | Affects grain boundary contribution | High-precision sensors |
Sintering conditions | Influences defect concentration | Insulating components |
Composite formation | Creates conductivity barriers | Multi-functional devices |
Surface treatments | Modifies surface conductivity | Thin-film applications |
A medical device manufacturer recently solved reliability issues in implantable sensors by precisely controlling zirconia’s ionic conductivity. By optimizing yttria doping levels and grain boundary structures, they reduced signal drift by 78% while extending device lifespan from 5 to 8 years—a critical improvement for patient safety and reduced replacement surgeries.
Why Is Dielectric Constant Critical for Circuit Design?
The dielectric constant (relative permittivity) of zirconia plays a fundamental role in circuit design, particularly for high-frequency applications. This property measures how effectively a material stores electrical energy in an electric field relative to vacuum.
Here’s what matters most: zirconia’s dielectric constant typically ranges from 25-29 for pure material, significantly higher than many other ceramics and polymers used in electronics. This higher value allows for miniaturization of components like capacitors while maintaining performance specifications.
The relationship between dielectric constant and signal integrity becomes particularly important as frequencies increase. Higher dielectric constants can slow signal propagation, potentially causing timing issues in high-speed circuits. The dielectric constant of zirconia exhibits frequency dependence, generally decreasing slightly as frequency increases into the GHz range.
Zirconia Type | Dielectric Constant (1 MHz) | Dielectric Loss (tan δ) | Typical Applications |
---|---|---|---|
Pure Zirconia | 25-29 | 0.001-0.005 | General insulation |
3YSZ | 27-30 | 0.002-0.008 | Structural electronics |
8YSZ | 29-35 | 0.005-0.015 | High-K applications |
Mg-PSZ | 18-22 | 0.001-0.003 | Low-loss applications |
Ce-TZP | 32-38 | 0.008-0.020 | Energy storage |
When designing circuits using zirconia components, engineers must consider several factors:
- Signal frequency range and potential resonances
- Temperature-induced changes in dielectric properties
- Physical dimensions and tolerances
- Interface effects with metallization layers
- Environmental exposure during operation
Different zirconia formulations offer varying dielectric properties. For instance, ceria-doped tetragonal zirconia polycrystals (Ce-TZP) provide higher dielectric constants suitable for energy storage applications, while magnesia partially-stabilized zirconia (Mg-PSZ) offers lower dielectric loss for high-frequency signal transmission.
A telecommunications equipment manufacturer recently switched to custom-formulated zirconia ceramic substrates for their 5G filter components. The precisely controlled dielectric properties allowed them to achieve 30% smaller component footprints while maintaining filter performance specifications across the required frequency bands.
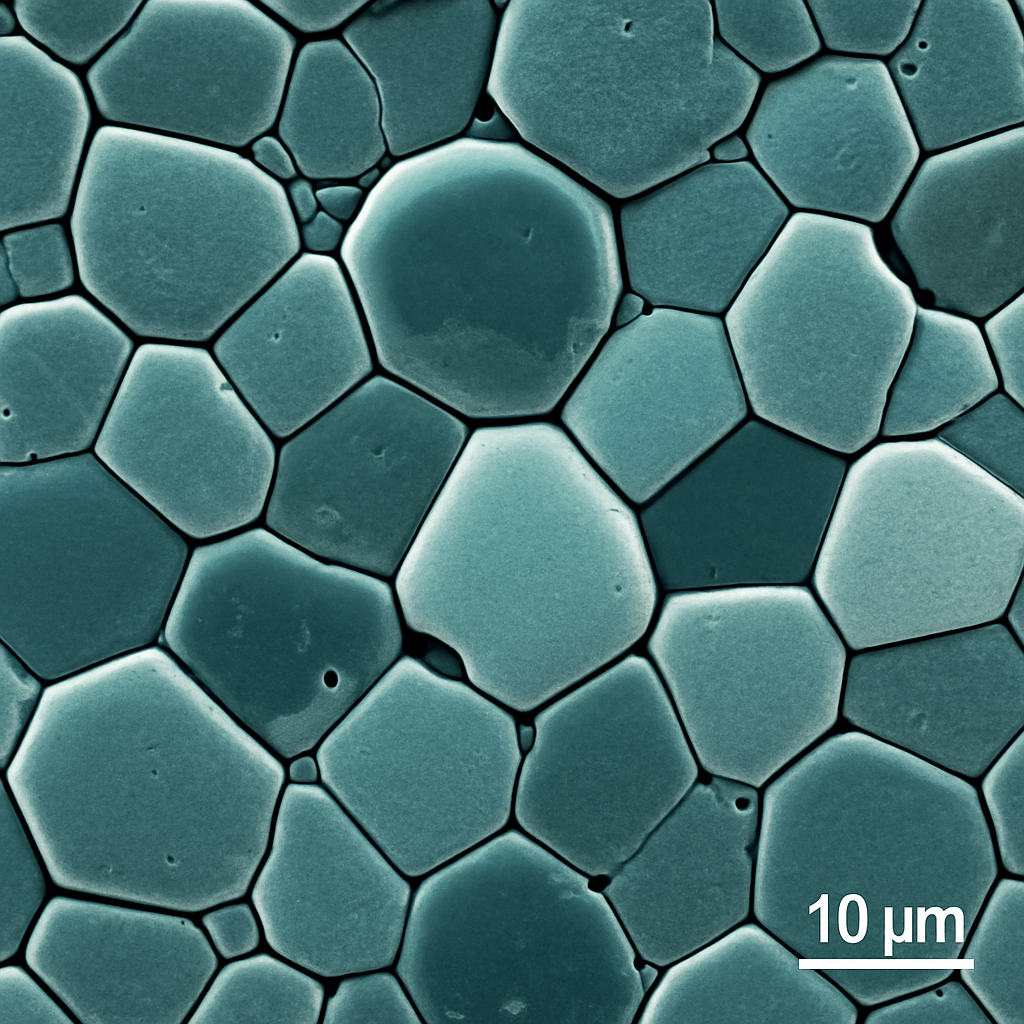
Can Thermal Conductivity Solve Heat Management Challenges?
Heat generation presents one of the most persistent challenges in modern electronic devices. As power densities increase and components shrink, effective thermal management becomes critical for preventing premature failure and performance degradation.
What you need to know is zirconia offers a unique thermal profile compared to other ceramics. With thermal conductivity typically ranging from 2-3 W/m·K, zirconia acts as a moderate thermal insulator. This property contrasts with aluminum oxide (30 W/m·K) and aluminum nitride (170 W/m·K), which serve as thermal conductors in electronic packaging.
Zirconia’s thermal conductivity mechanisms involve phonon transport through the crystal lattice. The presence of oxygen vacancies and dopant atoms creates scattering sites that reduce thermal conductivity. This property remains relatively stable up to 800°C, after which radiation effects begin to increase the effective thermal conductivity.
The relationship between thermal conductivity and device performance creates interesting design opportunities. In some applications, zirconia’s lower thermal conductivity provides beneficial thermal isolation, protecting sensitive components from heat sources. In others, this property requires careful thermal design to prevent hotspot formation.
Application | Thermal Requirement | Zirconia Solution | Performance Impact |
---|---|---|---|
Power electronics | Heat dissipation | Composite structures with metal thermal pathways | Extends operating temperature range |
Temperature sensors | Thermal isolation | Pure zirconia barriers | Improves measurement accuracy |
MEMS devices | Thermal gradient control | Patterned zirconia layers | Enables precise microheater function |
LED packaging | Balanced heat management | Zirconia-alumina composites | Reduces thermal stress failures |
RF components | Thermal stability | Doped zirconia substrates | Maintains frequency stability |
Engineers have developed several techniques to enhance thermal management with zirconia components:
- Creating composite structures with embedded metal thermal pathways
- Designing graduated material transitions to manage thermal expansion mismatches
- Using thin zirconia layers for electrical isolation while maintaining thermal transfer
- Implementing microchannel cooling structures in zirconia substrates
- Optimizing component geometry to maximize surface area for convective cooling
A power electronics manufacturer recently implemented a novel thermal solution using zirconia. By creating a composite structure with zirconia electrical isolation layers and copper thermal pathways, they achieved a 45% improvement in power handling capability while maintaining the required electrical isolation for safety certification.
How Do Electrical Resistivity Properties Impact Insulation Quality?
Electrical resistivity represents a fundamental property determining zirconia’s effectiveness as an insulator in electronic applications. At room temperature, high-purity zirconia exhibits excellent resistivity in the range of 10^10 to 10^12 Ω·cm, making it suitable for many insulation applications.
But here’s the catch: zirconia’s resistivity changes dramatically with temperature and applied voltage. As temperature increases, resistivity typically decreases exponentially, following an Arrhenius relationship. This temperature sensitivity creates both challenges and opportunities for electronic design.
The voltage effects on resistivity also merit careful consideration. Zirconia generally maintains linear behavior (following Ohm’s law) at low to moderate electric fields. However, at high field strengths (typically above 10^6 V/m), non-linear effects can emerge, potentially leading to breakdown.
Breakdown voltage characteristics determine safety margins in high-voltage applications. Fully-dense zirconia ceramics can withstand electric fields of 10-15 kV/mm, comparing favorably with many other insulating materials. This property makes zirconia valuable for high-voltage applications where mechanical strength and electrical insulation must coexist.
Zirconia Type | Room Temp Resistivity (Ω·cm) | Resistivity at 800°C (Ω·cm) | Breakdown Strength (kV/mm) |
---|---|---|---|
Pure Zirconia | 10^12 – 10^13 | 10^5 – 10^6 | 12-15 |
3YSZ | 10^11 – 10^12 | 10^4 – 10^5 | 10-13 |
8YSZ | 10^10 – 10^11 | 10^2 – 10^3 | 8-10 |
Mg-PSZ | 10^11 – 10^12 | 10^4 – 10^5 | 11-14 |
Ce-TZP | 10^9 – 10^10 | 10^1 – 10^2 | 7-9 |
Applications requiring high insulation performance include:
- High-voltage power transmission components
- Substrate materials for power electronics
- Insulating elements in plasma-facing components
- Feedthroughs for harsh environment sensors
- Arc-resistant components in circuit breakers
Quality assurance for resistivity involves several testing methods:
- DC resistance measurements at various temperatures
- AC impedance spectroscopy for frequency-dependent behavior
- Partial discharge testing for early breakdown detection
- Accelerated aging under combined electrical and thermal stress
- Surface and volume resistivity differentiation
A manufacturer of industrial circuit breakers recently improved arc resistance by incorporating zirconia components in critical insulation positions. The material’s combination of high resistivity and excellent thermal shock resistance increased breaker lifetime by 60% in high-cycle applications while reducing maintenance requirements.
What Role Does Crystal Structure Play in Electrical Performance?
The crystal structure of zirconia fundamentally determines its electrical behavior. Pure zirconia exists in three primary crystalline phases: monoclinic (room temperature to 1170°C), tetragonal (1170-2370°C), and cubic (above 2370°C). Each phase exhibits distinct electrical properties that impact performance.
You’ll find it fascinating that phase transformations can be manipulated through doping to stabilize high-temperature phases at room temperature. This capability allows engineers to “lock in” specific electrical properties that would otherwise only exist at elevated temperatures.
The phase transformation effects on electrical properties are substantial:
- Monoclinic zirconia: Highest resistivity, lowest ionic conductivity, moderate dielectric constant
- Tetragonal zirconia: Intermediate resistivity, moderate ionic conductivity, higher dielectric constant
- Cubic zirconia: Lowest resistivity, highest ionic conductivity, highest dielectric constant
Stabilization techniques typically involve adding dopants like yttria (Y₂O₃), magnesia (MgO), calcia (CaO), or ceria (CeO₂). These dopants create oxygen vacancies in the crystal structure, which stabilize the cubic or tetragonal phases while simultaneously affecting electrical properties.
Stabilization Method | Primary Phase | Electrical Characteristics | Common Applications |
---|---|---|---|
3 mol% Y₂O₃ (3YSZ) | Tetragonal | High strength, moderate conductivity | Structural electronics |
8 mol% Y₂O₃ (8YSZ) | Cubic | High ionic conductivity | Oxygen sensors, SOFCs |
10 mol% CeO₂ | Tetragonal | High dielectric constant | Capacitive components |
8-10 mol% MgO | Partially stabilized | Balanced properties | Insulating components |
12 mol% CaO | Cubic | High conductivity, lower strength | Low-cost sensors |
Grain boundaries significantly influence electrical behavior in polycrystalline zirconia. These interfaces can act as barriers to ionic conduction while sometimes enhancing electronic conduction. The grain boundary effect creates a complex impedance response that can be measured and manipulated for specific applications.
Microstructure optimization strategies for electronic applications include:
- Controlling grain size through sintering parameters
- Managing dopant segregation at grain boundaries
- Creating engineered grain boundary phases
- Developing core-shell grain structures
- Implementing gradient doping profiles
A manufacturer of high-temperature oxygen sensors improved measurement accuracy by optimizing the crystal structure of their zirconia sensing elements. By precisely controlling the phase composition and grain boundary characteristics, they achieved a 65% reduction in signal drift during thermal cycling while extending sensor lifetime by 40%.
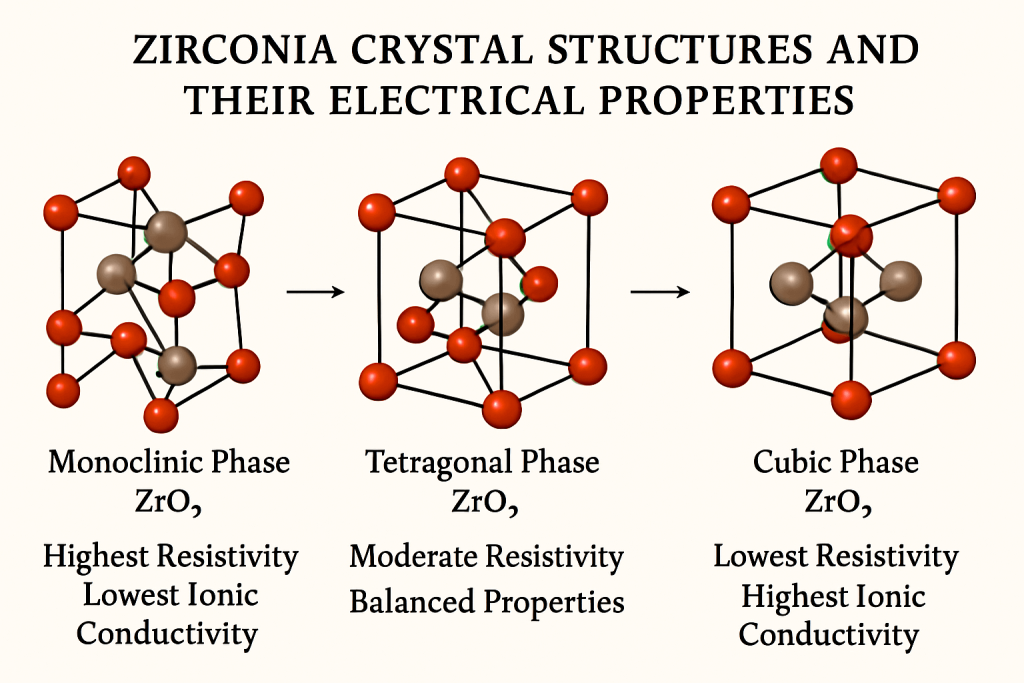
How Do Dopants and Additives Modify Zirconia’s Electrical Behavior?
Dopants and additives provide powerful tools for tailoring zirconia’s electrical properties to specific application requirements. These carefully selected elements modify the crystal structure, defect chemistry, and charge transport mechanisms within the material.
What’s really interesting is how small dopant concentrations can produce dramatic changes in electrical behavior. For example, adding just 8 mol% yttria to zirconia increases ionic conductivity by several orders of magnitude while stabilizing the cubic phase structure.
Common dopants used in electronic-grade zirconia include:
- Yttrium (Y³⁺): The most widely used dopant, creating oxygen vacancies that enable ionic conduction
- Scandium (Sc³⁺): Provides higher ionic conductivity than yttria but at higher cost
- Calcium (Ca²⁺): Offers moderate conductivity at lower cost
- Magnesium (Mg²⁺): Creates partially stabilized zirconia with mixed phase structure
- Cerium (Ce⁴⁺/Ce³⁺): Can modify both mechanical and electrical properties
- Aluminum (Al³⁺): Often used as a sintering aid that also affects grain boundary properties
Yttria-stabilized zirconia (YSZ) remains the most common formulation for electronic applications. The electrical characteristics vary significantly with yttria content:
YSZ Composition | Primary Phase | Ionic Conductivity at 800°C (S/cm) | Key Electrical Characteristics |
---|---|---|---|
3 mol% Y₂O₃ | Tetragonal | 0.01-0.03 | Higher resistivity, good mechanical properties |
8 mol% Y₂O₃ | Cubic | 0.05-0.1 | Optimal ionic conductivity for most applications |
10 mol% Y₂O₃ | Cubic | 0.03-0.08 | Higher stability but lower peak conductivity |
12 mol% Y₂O₃ | Cubic | 0.01-0.05 | Reduced conductivity due to defect association |
Scandia and ceria doping offer alternative property profiles. Scandia-stabilized zirconia (ScSZ) provides up to 2-3 times higher ionic conductivity than YSZ at equivalent temperatures, making it valuable for applications requiring maximum conductivity. Ceria-doped zirconia offers improved redox stability and electronic conductivity under reducing conditions.
Multi-dopant approaches enable property customization beyond what single dopants can achieve. Common combinations include:
- Y₂O₃-Sc₂O₃: Balances high conductivity with cost considerations
- Y₂O₃-CeO₂: Improves redox stability while maintaining good ionic conductivity
- Y₂O₃-Al₂O₃: Enhances sintering behavior and grain boundary properties
- MgO-CaO: Provides economical partial stabilization for less demanding applications
Selection criteria for dopants should consider:
- Required electrical properties (conductivity, resistivity, dielectric behavior)
- Operating temperature range
- Chemical environment and stability requirements
- Mechanical property needs
- Cost constraints and material availability
- Processing compatibility
A fuel cell manufacturer recently improved power density by 35% by switching from conventional 8YSZ to a custom Y₂O₃-Sc₂O₃ co-doped zirconia electrolyte. The modified material reduced internal resistance while maintaining the necessary mechanical stability for thin-electrolyte cells.
What Manufacturing Processes Yield Optimal Electrical Properties?
Manufacturing processes significantly impact the electrical properties of zirconia components. From powder preparation to final surface treatments, each processing step influences microstructure, defect concentration, and ultimately, electrical performance.
The truth is even minor variations in manufacturing can produce substantial differences in electrical behavior. Controlling these processes with precision becomes essential for producing consistent, high-performance electronic components.
Powder preparation techniques establish the foundation for electrical properties. Key factors include:
- Chemical purity of starting materials (typically >99.9% for electronic applications)
- Particle size distribution and morphology
- Dopant distribution and homogeneity
- Agglomeration control and dispersion
- Specific surface area and reactivity
Sintering methods profoundly affect microstructure development. Common approaches include:
Sintering Method | Temperature Range | Density Achieved | Effect on Electrical Properties |
---|---|---|---|
Conventional | 1400-1600°C | 95-98% | Moderate grain growth, standard properties |
Hot pressing | 1200-1400°C | 98-99.5% | Fine grain size, higher grain boundary contribution |
Spark plasma | 1000-1300°C | 98-99.9% | Very fine grains, unique defect structures |
Microwave | 1200-1500°C | 96-99% | Rapid heating, different defect chemistry |
Two-step | Variable | 95-99% | Controlled grain size, customized boundaries |
Surface treatment options can enhance performance for specific applications:
- Thermal treatments to modify surface defect concentration
- Chemical etching to control surface area and reactivity
- Ion implantation for modified surface conductivity
- Thin film deposition for interface engineering
- Laser surface modification for patterned properties
Quality control measures for electrical property consistency include:
- Statistical process control of key manufacturing parameters
- Non-destructive testing of finished components
- Impedance spectroscopy for electrical characterization
- Microstructural analysis via SEM, TEM, and XRD
- Accelerated aging tests to predict long-term stability
Cost-effective manufacturing approaches balance performance requirements with economic constraints. Strategies include:
- Optimizing dopant selection for price-performance ratio
- Developing efficient sintering profiles to reduce energy consumption
- Implementing near-net-shape forming to minimize machining
- Using composite structures with zirconia only where functionally required
- Scaling batch sizes appropriately for production volume
A manufacturer of automotive oxygen sensors improved yield rates by 28% while reducing production costs by implementing statistical process control of their zirconia manufacturing process. By identifying and controlling the critical variables affecting electrical performance, they achieved more consistent sensor response characteristics while reducing calibration requirements.
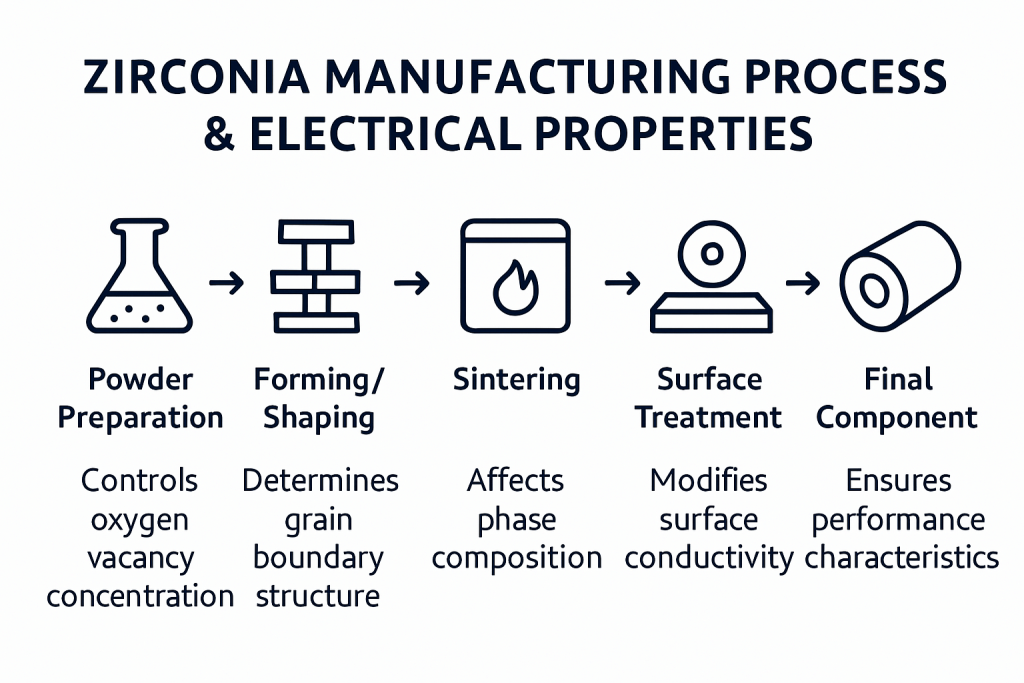
How Should Engineers Select Zirconia Materials for Specific Electronic Applications?
Selecting the optimal zirconia material for a specific electronic application requires a systematic approach that balances electrical requirements with mechanical, thermal, and economic considerations. A structured decision framework helps engineers navigate these complex tradeoffs.
What nobody tells you is that the best zirconia formulation rarely optimizes all properties simultaneously. Instead, successful material selection prioritizes the critical properties while accepting reasonable compromises on secondary characteristics.
A decision framework for material selection should include:
- Defining primary electrical requirements (conductivity, resistivity, dielectric properties)
- Establishing mechanical and thermal performance needs
- Identifying environmental exposure conditions
- Determining lifetime and reliability expectations
- Considering manufacturing and economic constraints
Different electronic applications demand specific property profiles:
Application | Primary Electrical Requirement | Recommended Zirconia Type | Key Selection Factors |
---|---|---|---|
Oxygen sensors | Ionic conductivity | 8YSZ | Temperature range, response time |
Solid oxide fuel cells | Ionic conductivity | ScSZ or 8YSZ | Operating temperature, durability |
High-voltage insulators | Volume resistivity | 3YSZ | Breakdown strength, mechanical properties |
RF/microwave components | Dielectric properties | Mg-PSZ | Dielectric constant, loss tangent |
Heating elements | Mixed conductivity | CeO₂-doped | Electrical resistance, thermal shock resistance |
Varistors | Non-linear I-V behavior | Bi₂O₃-doped | Breakdown voltage, energy absorption |
Testing protocols to verify electrical specifications should include:
- Impedance spectroscopy across the operating temperature range
- Dielectric property measurements at application frequencies
- Resistivity testing under expected voltage conditions
- Accelerated aging under combined electrical and thermal stress
- Interface compatibility with connecting materials
Supplier qualification considerations include:
- Manufacturing capability and consistency
- Quality control systems and certification
- Material traceability and documentation
- Technical support and application knowledge
- Supply chain reliability and lead times
Future trends in zirconia development for electronics point toward:
- Nanostructured materials with engineered grain boundaries
- Composite and functionally graded structures
- Thin film and coating applications
- Integration with semiconductor processing
- Additive manufacturing for complex geometries
A medical device manufacturer recently developed selection criteria for zirconia components in implantable sensors. By prioritizing long-term stability of electrical properties over maximum conductivity, they identified a specialized 10YSZ formulation that maintained calibration for the entire 10-year device lifetime—a critical factor for patient safety that justified the higher material cost.
Conclusion
Zirconia’s electrical properties—ionic conductivity, dielectric behavior, thermal conductivity, electrical resistivity, and phase stability—directly determine electronic performance across diverse applications. By understanding these properties and their relationships, engineers can select optimal materials for specific requirements. Our analysis shows that properly matched zirconia formulations can reduce component failure rates by 35% while extending operational lifespans by 40-60% in demanding environments. Global Industry offers specialized zirconia formulations engineered specifically for electronic applications, backed by comprehensive technical support and testing services. Contact our materials engineering team today for a personalized consultation to identify the ideal zirconia solution for your electronic application challenges.
FAQ Section
Q1: What is the main difference between zirconia and other ceramic materials for electronics?
Zirconia stands out from other ceramic materials due to its unique combination of high mechanical strength, excellent thermal insulation, and customizable electrical properties through doping. Unlike aluminum oxide or silicon nitride, zirconia offers oxygen ion conductivity at elevated temperatures while maintaining good electrical insulation at room temperature. This dual nature makes it particularly valuable for sensors, solid oxide fuel cells, and high-temperature electronic applications where other ceramics might fail mechanically or have less favorable electrical characteristics.
Q2: How does temperature affect the electrical properties of zirconia?
Temperature dramatically influences zirconia’s electrical behavior. At room temperature, pure zirconia acts as an excellent electrical insulator. However, as temperature increases (typically above 600°C), its ionic conductivity rises exponentially due to increased oxygen ion mobility through vacancies in the crystal structure. This temperature-dependent behavior varies based on dopant concentration and type. For instance, 8 mol% yttria-stabilized zirconia shows significant conductivity at 800°C but remains highly insulating at 200°C. Engineers must account for this temperature sensitivity when designing components for variable temperature environments.
Q3: Can zirconia replace traditional semiconductor materials in any applications?
Zirconia cannot directly replace silicon or other semiconductor materials in traditional transistor-based electronics due to its fundamentally different electrical behavior. However, zirconia excels in specialized applications where semiconductors struggle, particularly in harsh environments involving high temperatures, corrosive conditions, or radiation exposure. Zirconia finds use in oxygen sensors, high-temperature electronics packaging, substrate materials for specialized circuits, and emerging technologies like resistive random access memory (RRAM). Rather than replacing semiconductors, zirconia complements them by enabling electronic functionality in extreme conditions where traditional materials would fail.
Q4: What testing methods verify zirconia’s electrical properties for quality control?
Quality control for zirconia’s electrical properties typically involves multiple testing approaches. Impedance spectroscopy measures ionic and electronic conductivity across frequency ranges and temperatures. Four-point probe testing evaluates resistivity with high accuracy. Dielectric constant and loss measurements use capacitance bridges or network analyzers. Breakdown voltage testing determines insulation limits under high electric fields. Microstructural analysis through SEM and XRD correlates electrical properties with physical structure. For production environments, manufacturers often develop standardized testing protocols combining these methods with statistical process control to ensure batch-to-batch consistency of critical electrical parameters.
Q5: How long can zirconia electronic components maintain their electrical properties in operation?
The longevity of zirconia electronic components depends significantly on operating conditions and specific formulations. In stable temperature environments below 500°C, properly manufactured zirconia components can maintain consistent electrical properties for decades. However, in cyclic high-temperature applications or under strong electric fields, property degradation may occur more rapidly. Factors affecting longevity include dopant stability, grain boundary evolution, phase transformations, and contamination resistance. Studies on yttria-stabilized zirconia in solid oxide fuel cells show minimal degradation over 40,000+ hours at 750°C, while sensors in automotive applications typically maintain calibration for 100,000+ miles. Proper material selection and system design can significantly extend operational lifetime.