In the competitive landscape of advanced ceramics, zirconia stands out as a material of exceptional versatility and performance. For procurement managers, engineers, and technical decision-makers, understanding the mechanical properties that differentiate premium zirconia grades from standard offerings is crucial for making informed material selection decisions.
The global zirconia market continues to expand, with premium grades commanding significant price premiums based on their superior mechanical characteristics. This article examines the critical mechanical properties that define top-tier zirconia materials, how they’re measured, and most importantly, how they impact real-world applications across industries.
What Makes Zirconia A Critical Engineering Material?
Zirconia has established itself as an indispensable material across numerous high-performance applications, from aerospace components to medical implants. Its unique combination of mechanical properties sets it apart from other engineering ceramics and even some metals.
Here’s what you need to know: Zirconia’s exceptional combination of strength, toughness, and hardness—properties that are typically mutually exclusive in most materials—makes it uniquely valuable for demanding applications where failure is not an option.
Commercial zirconia grades are categorized primarily by their stabilization method and resulting microstructure: Fully Stabilized Zirconia (FSZ), Partially Stabilized Zirconia (PSZ), and Tetragonal Zirconia Polycrystal (TZP). Each category offers distinct mechanical property profiles suited to different applications.
Unlike other engineering ceramics such as alumina or silicon carbide, zirconia exhibits a transformation toughening mechanism that dramatically enhances its fracture resistance. This unique characteristic allows zirconia components to withstand mechanical stresses that would cause catastrophic failure in other ceramic materials.
Zirconia Type | Primary Stabilizer | Key Mechanical Advantage | Typical Applications |
---|---|---|---|
TZP (3Y-TZP) | 3 mol% Yttria | Highest flexural strength (>1000 MPa) | Dental implants, cutting tools |
PSZ (Mg-PSZ) | 8-10 mol% Magnesia | Excellent thermal shock resistance | Pump components, valve seats |
Ce-TZP | 12 mol% Ceria | Superior fracture toughness | Automotive oxygen sensors |
FSZ | >8 mol% Yttria | High-temperature stability | Thermal barrier coatings |
ATZ | Alumina-toughened | Enhanced hardness with good toughness | Bearing components, wear parts |
How Does Hardness Define Commercial Zirconia Grades?
Hardness represents one of the fundamental mechanical properties that differentiate zirconia grades and directly impacts their performance in wear-critical applications. Understanding hardness variations and their implications is essential for proper material selection.
The key insight: While zirconia’s hardness (typically 1200-1300 HV) is lower than some other engineering ceramics, premium grades achieve an optimal balance between hardness and fracture toughness that standard grades cannot match.
Commercial zirconia grades exhibit hardness values ranging from 1100 to 1400 HV (Vickers Hardness), with variations primarily determined by stabilizer type and content, sintering conditions, and grain size. Measurement standards such as ASTM C1327 provide consistent evaluation methods.
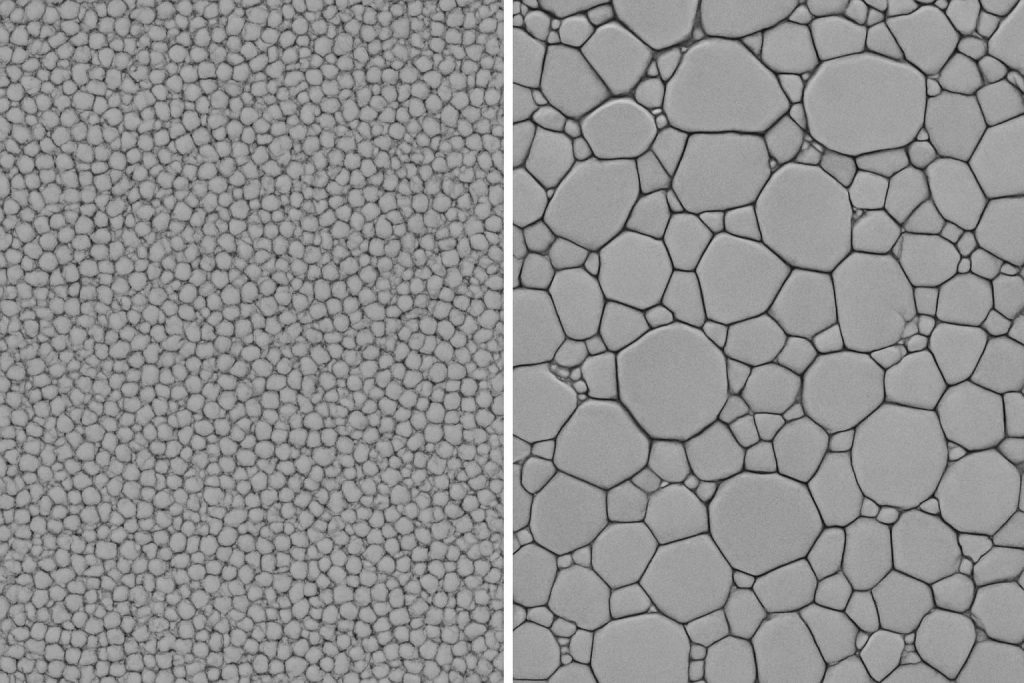
Recent research has established clear correlations between microstructure and hardness in zirconia ceramics. Premium grades feature precisely controlled grain size distributions (typically 0.3-0.5 μm) that optimize hardness without compromising other mechanical properties.
The relationship between hardness and wear resistance is not always linear in zirconia materials. While hardness contributes significantly to abrasion resistance, premium grades incorporate additional microstructural features that enhance wear performance beyond what hardness alone would predict.
Zirconia Grade | Typical Hardness (HV) | Grain Size (μm) | Relative Wear Resistance | Price Premium (%) |
---|---|---|---|---|
Standard 3Y-TZP | 1200-1250 | 0.5-1.0 | Baseline | – |
Premium 3Y-TZP | 1250-1300 | 0.3-0.5 | 1.5-2× better | 30-40% |
Standard Mg-PSZ | 1100-1150 | 15-30 | 0.7-0.8× baseline | -10% |
Premium Mg-PSZ | 1150-1200 | 10-15 | 1.2-1.5× better | 20-25% |
ATZ Composite | 1300-1400 | <0.5 (ZrO₂), <1.0 (Al₂O₃) | 2-3× better | 50-70% |
Why Is Fracture Toughness The Game-Changer?
Fracture toughness represents perhaps the most distinctive mechanical property of premium zirconia grades and fundamentally differentiates them from both standard zirconia and other engineering ceramics. This property determines a material’s resistance to crack propagation—a critical factor in applications subject to impact, stress concentration, or cyclic loading.
What matters most: Premium zirconia grades achieve fracture toughness values of 6-10 MPa·m^(1/2)—up to three times higher than other engineering ceramics—enabling applications that would otherwise require metals or composites.
The transformation toughening mechanism unique to zirconia creates its exceptional fracture resistance. When stress concentrates at a crack tip, metastable tetragonal zirconia transforms to the monoclinic phase, creating a localized volume expansion that compresses the crack and inhibits its propagation.
Different stabilizers dramatically influence fracture toughness. Yttria-stabilized grades (3Y-TZP) offer an excellent balance of properties with toughness values of 5-6 MPa·m^(1/2), while ceria-stabilized grades can reach 8-10 MPa·m^(1/2) but with some reduction in hardness and strength.
Property Relationship | Standard Grades | Premium Grades | Engineering Significance |
---|---|---|---|
Toughness vs. Hardness | Strong inverse correlation | Optimized balance | Better wear resistance without brittleness |
Toughness vs. Strength | Moderate positive correlation | Enhanced synergy | Higher design stress limits with safety margin |
Toughness vs. Aging Resistance | Often compromised | Maintained balance | Better long-term reliability |
Toughness vs. Temperature Stability | Limited range | Extended capability | Wider application temperature range |
What Role Does Flexural Strength Play?
Flexural strength (also called bend strength or modulus of rupture) represents a critical mechanical property for zirconia components subject to bending loads or tensile stresses. This property often determines design limits and safety factors in structural applications.
The reality is: Premium zirconia grades achieve flexural strengths exceeding 1200 MPa—approaching the strength of some high-performance metal alloys while maintaining ceramic advantages in hardness, wear resistance, and chemical stability.
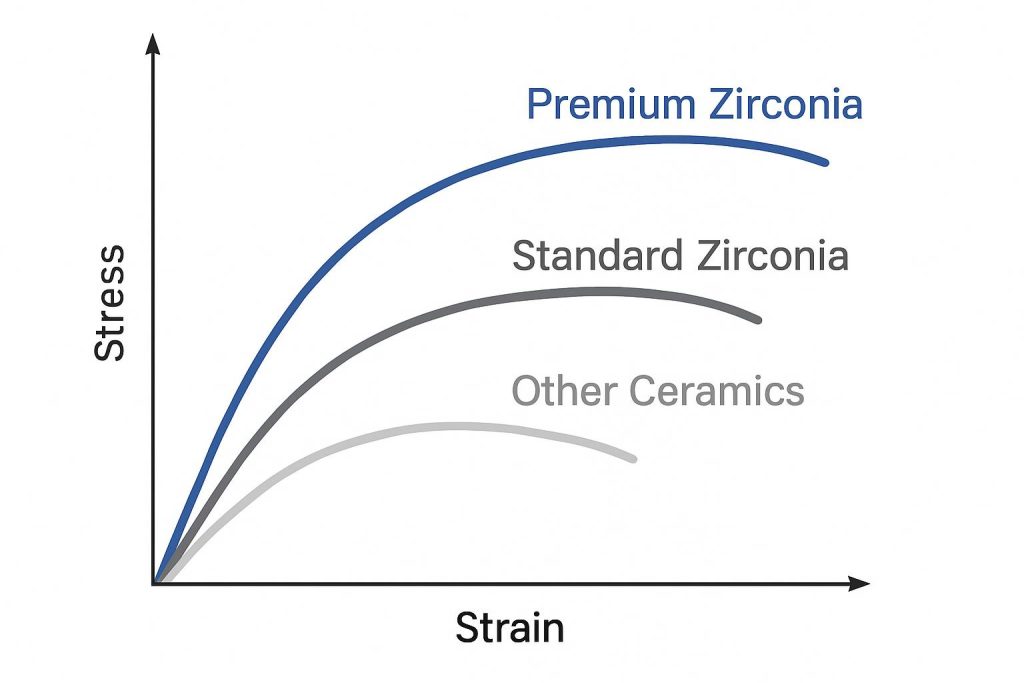
Commercial zirconia grades exhibit a wide range of flexural strength values, from 500 MPa for some partially stabilized variants to over 1200 MPa for advanced tetragonal zirconia polycrystals (TZP). Testing methodology significantly impacts measured values, with standards such as ASTM C1161 and ISO 14704 specifying precise specimen preparation.
Environmental factors can significantly impact flexural strength. Temperature, humidity, and chemical exposure all influence zirconia’s mechanical performance. Premium grades incorporate specific stabilizer combinations and microstructural features that enhance environmental stability.
Application | Minimum Required Flexural Strength | Critical Performance Factors | Premium Grade Advantage |
---|---|---|---|
Dental Implants | >900 MPa | Biocompatibility, aging resistance | 30-40% higher strength, enhanced reliability |
Cutting Tools | >1200 MPa | Edge stability, thermal shock resistance | 25% longer tool life, higher cutting speeds |
Pump Components | >700 MPa | Corrosion resistance, wear performance | 3-5× longer service life in abrasive media |
Oxygen Sensors | >600 MPa | Thermal cycling resistance, gas tightness | Improved thermal shock resistance, better sealing |
How Do Thermal Properties Complement Mechanical Performance?
While purely mechanical properties often dominate material selection discussions, thermal properties play a crucial role in determining zirconia’s performance in real-world applications. The interaction between thermal characteristics and mechanical properties defines the operational limits of different zirconia grades.
Here’s what you need to know: Premium zirconia grades maintain their mechanical integrity across wider temperature ranges and under more severe thermal cycling conditions than standard grades—a critical advantage in many high-value applications.
Thermal expansion behavior significantly impacts mechanical performance in multi-material assemblies or thermally cycled components. Zirconia’s coefficient of thermal expansion (CTE) ranges from 9-11 × 10^(-6)/K, depending on grade and temperature.
Thermal shock resistance—the ability to withstand sudden temperature changes without failure—represents a critical performance parameter in many applications. This property depends on a complex interplay between thermal conductivity, expansion coefficient, elastic modulus, and strength.
Thermal Property | Standard Grades | Premium Grades | Application Impact |
---|---|---|---|
Thermal Shock Resistance (ΔT) | 150-200°C | 250-350°C | Wider process temperature windows, faster heating/cooling cycles |
Strength Retention at 800°C | 60-70% | 80-90% | Higher operating temperatures, improved safety margins |
Thermal Cycling Durability | 500-1000 cycles | 2000-5000 cycles | Extended service life in cyclic temperature applications |
Thermal Conductivity | 2-2.5 W/m·K | 2.5-3.5 W/m·K | Better thermal management, reduced thermal gradients |
Which Microstructural Features Determine Mechanical Properties?
The microstructure of zirconia ceramics fundamentally controls their mechanical properties. Understanding these relationships is essential for evaluating different grades and selecting the optimal material for specific applications.
The key insight: Premium zirconia grades achieve their superior mechanical properties through precisely engineered microstructures that standard grades cannot match—differences that aren’t always apparent in basic material specifications.
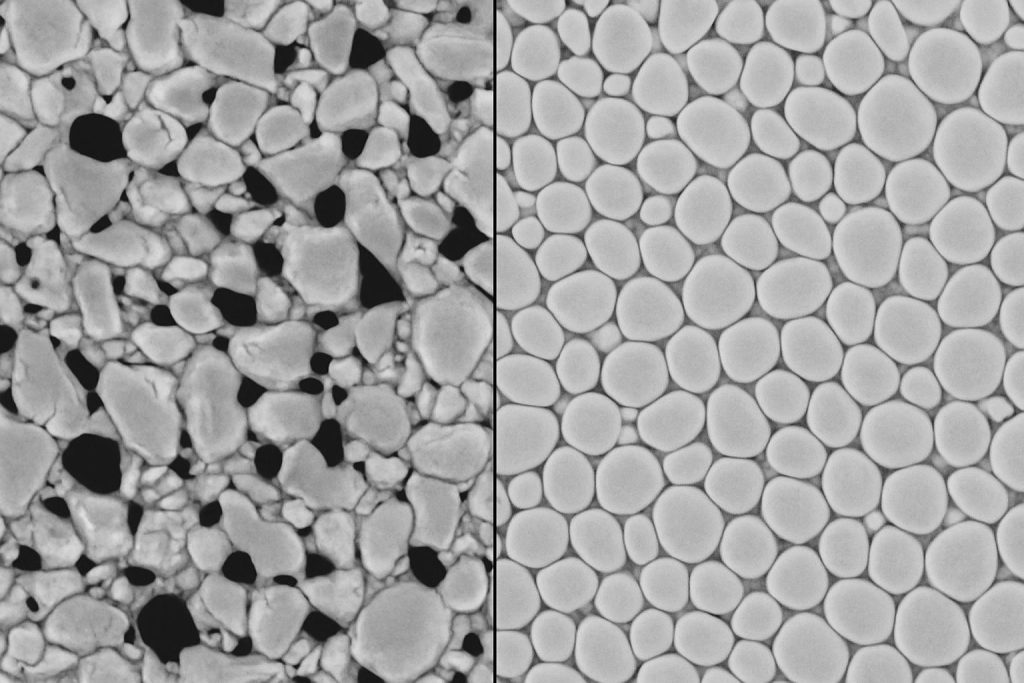
Grain size and distribution represent perhaps the most critical microstructural parameters affecting mechanical performance. Premium grades typically feature finer average grain sizes (0.3-0.5 μm for TZP grades) with narrower size distributions than standard grades.
Porosity and density significantly impact all mechanical properties. Premium grades achieve densities exceeding 99.9% of theoretical, with carefully controlled pore size distributions that minimize stress concentration effects.
Microstructural Feature | Measurement Technique | Impact on Mechanical Properties | Premium Grade Differentiation |
---|---|---|---|
Grain Size | FE-SEM, EBSD | Controls strength, toughness, aging resistance | 30-50% finer, narrower distribution |
Porosity | Archimedes method, 3D tomography | Affects all mechanical properties | <0.1% vs 0.5-1% in standard grades |
Phase Distribution | XRD, Raman spectroscopy | Determines transformation toughening effectiveness | More uniform stabilizer distribution |
Grain Boundary Chemistry | TEM-EDS, Atom Probe | Influences high-temperature properties, aging resistance | Engineered segregation profiles |
How To Select The Right Zirconia Grade For Specific Applications?
Selecting the optimal zirconia grade requires a systematic approach that balances mechanical property requirements, operating conditions, and economic considerations. This process is critical for maximizing performance while managing costs effectively.
What matters most: The highest-priced zirconia isn’t always the best choice for every application—optimal selection requires matching specific grade characteristics to application requirements and prioritizing the properties that most directly impact performance.
Systematic selection methodologies begin with comprehensive requirements analysis. Critical parameters include maximum operating stress, temperature range, chemical environment, wear conditions, and expected service life.
Industry-specific performance priorities vary significantly. Medical implant applications prioritize biocompatibility, aging resistance, and reliability above all else. Cutting tool applications demand optimal combinations of hardness, toughness, and thermal shock resistance.
Application Category | Critical Properties | Recommended Grade Type | Selection Considerations |
---|---|---|---|
Structural Components | Strength, toughness, reliability | Premium 3Y-TZP, ATZ | Safety factors, fatigue resistance, inspection capabilities |
Wear Applications | Hardness, toughness, friction coefficient | ATZ, Premium 3Y-TZP | Lubrication conditions, counterface material, surface finish |
Thermal Applications | Thermal shock resistance, high-temperature strength | Mg-PSZ, Ce-TZP | Temperature range, cycling frequency, thermal gradients |
Corrosion Resistance | Chemical stability, density, mechanical integrity | FSZ, Premium 3Y-TZP | Specific chemical environment, temperature, pressure |
What Testing Methods Validate Mechanical Properties?
Reliable testing methodologies are essential for validating the mechanical properties of zirconia grades and ensuring they meet application requirements. Understanding these methods helps technical buyers evaluate supplier claims and select appropriate materials.
The reality is: Standard testing methods don’t always predict real-world performance—premium grade suppliers typically offer more comprehensive testing data and application-specific performance validation than suppliers of commodity grades.
Standardized mechanical testing protocols provide the foundation for material comparison. Key standards include ASTM C1161 for flexural strength, ASTM C1421 for fracture toughness, and ASTM C1327 for hardness.
Advanced characterization techniques increasingly complement standard tests. High-resolution microscopy, spectroscopic methods, and 3D tomography provide insights into microstructural features that directly correlate with mechanical performance.
Testing Category | Standard Methods | Advanced Methods | Value of Premium Grade Data |
---|---|---|---|
Strength Testing | 3-point bend (ASTM C1161) | 4-point bend, biaxial flexure | Larger sample sizes, Weibull statistics |
Fracture Toughness | SEVNB (ASTM C1421) | Double torsion, R-curve analysis | More complete fracture behavior characterization |
Hardness | Vickers (ASTM C1327) | Nanoindentation mapping | Spatial distribution data, depth-dependent properties |
Aging Resistance | Autoclave (ISO 13356) | Low-temperature long-term studies | Correlation with actual application environments |
Conclusion
The mechanical properties that define premium zirconia grades represent more than just impressive numbers on a specification sheet—they translate directly to performance advantages in demanding applications. From the exceptional fracture toughness that prevents catastrophic failure to the optimal hardness-strength combinations that extend component life, these properties enable designs and applications that would be impossible with standard ceramic materials.
For technical decision-makers, understanding these properties and their interrelationships is essential for making informed material selections. The price premium commanded by high-performance zirconia grades is justified by tangible benefits: longer service life, enhanced reliability, improved efficiency, and access to operating conditions beyond the capabilities of standard materials.
FAQ Section
Q1: How does the cost of premium zirconia grades compare to standard grades?
Premium zirconia grades typically command price premiums of 30-100% over standard grades, depending on specific properties and manufacturing complexity. This price difference reflects several factors: more sophisticated powder processing to achieve finer, more uniform particle sizes; more complex stabilizer packages requiring precise chemical control; additional processing steps such as hot isostatic pressing (HIP); more rigorous quality control including 100% inspection and comprehensive testing; and often, more extensive application support. However, lifecycle cost analysis frequently justifies this premium through 3-5× longer service life, reduced maintenance requirements, and performance capabilities that standard grades cannot match.
Q2: What are the most effective supplier qualification processes for premium zirconia materials?
Effective supplier qualification for premium zirconia should include comprehensive technical assessment and business evaluation. Technical qualification should examine material property documentation, statistical process control data, and quality management systems. Request sample components for independent testing, focusing on properties critical to your application. Consider conducting site visits to evaluate manufacturing capabilities and quality systems firsthand. Business qualification should assess production capacity, financial stability, and technical support capabilities. The most successful relationships typically involve collaborative development rather than transactional purchasing.
Q3: How do stabilizers affect the mechanical properties of zirconia?
Stabilizers (such as yttria, magnesia, ceria, or calcia) fundamentally control zirconia’s mechanical properties by influencing its crystal structure and transformation behavior. These additives prevent the catastrophic volume change associated with the tetragonal-to-monoclinic transformation during cooling, while still allowing beneficial transformation toughening under stress. Different stabilizers produce distinct property profiles: yttria (3 mol%) creates TZP with excellent strength and good toughness; magnesia (8-10 mol%) produces PSZ with superior thermal shock resistance; ceria (12 mol%) maximizes toughness but reduces hardness.
Q4: What mechanical property changes occur at elevated temperatures?
Zirconia’s mechanical properties change significantly with temperature, with the specific behavior depending on grade and stabilizer type. Flexural strength typically decreases gradually up to about 800°C, with premium grades retaining 80-90% of room-temperature values compared to 60-70% for standard grades. Above 800-1000°C (depending on grade), strength decreases more rapidly as grain boundary sliding and creep mechanisms activate. Fracture toughness behavior is more complex—some grades (particularly ceria-stabilized) actually show increased toughness at moderate temperatures due to enhanced transformation toughening, before declining at higher temperatures.
Q5: How do processing methods affect the mechanical properties of commercial zirconia?
Manufacturing processes dramatically impact zirconia’s mechanical properties through their effects on microstructure. Powder synthesis methods (co-precipitation, sol-gel, or hydrothermal) influence powder purity, particle size distribution, and agglomeration state, which directly affect final density and grain size. Forming techniques (dry pressing, isostatic pressing, injection molding, or additive manufacturing) impact green density distribution and internal stresses, which influence sintering behavior and final mechanical properties. Sintering conditions (temperature, time, atmosphere) are perhaps the most critical processing parameters—temperature too high leads to excessive grain growth and toughness reduction, while insufficient temperature results in residual porosity and strength reduction.