Manufacturing reliable zirconia components remains a critical challenge for industries ranging from medical devices to aerospace applications. Companies struggle with inconsistent quality and premature failures that impact both reputation and bottom line. This article examines the manufacturing techniques that produce the most dependable zirconia components, providing evidence-based insights from industry research and practical manufacturing experience. Our analysis covers the entire production chain from powder processing to final quality control, helping you make informed decisions about zirconia component manufacturing.
What Factors Determine Zirconia Component Reliability?
The reliability of zirconia components depends on multiple interconnected factors that must be carefully controlled throughout the manufacturing process. The reality is that even minor variations in material properties can significantly impact final performance.
Material purity stands as perhaps the most fundamental determinant of zirconia reliability. Research shows that impurity levels as low as 0.1% can dramatically alter mechanical properties and aging resistance. High-purity zirconia powders (99.9%+) consistently produce components with superior strength and stability compared to lower-grade alternatives.
Purity Level | Typical Impurities | Impact on Reliability | Recommended Applications |
---|---|---|---|
Ultra-high (99.99%+) | <0.01% SiO₂, Al₂O₃ | Exceptional stability, highest strength | Medical implants, precision components |
High (99.9-99.99%) | 0.01-0.1% SiO₂, Al₂O₃, Fe₂O₃ | Very good stability, high strength | Industrial wear parts, cutting tools |
Medium (99.5-99.9%) | 0.1-0.5% mixed oxides | Moderate stability, good strength | General industrial components |
Standard (<99.5%) | >0.5% mixed oxides | Variable properties, lower reliability | Non-critical applications |
Microstructure control represents another critical factor. The grain size distribution directly influences mechanical properties, with finer grains (0.3-0.5 μm) typically providing higher strength and better aging resistance. However, extremely fine grains (<0.2 μm) can sometimes reduce fracture toughness. The optimal grain size depends on the specific application requirements.
Density and porosity levels dramatically affect mechanical performance. Components with relative density below 99% show exponentially decreasing strength and reliability. Modern manufacturing techniques aim for >99.5% relative density to maximize component performance and consistency.
Surface treatment and defect control play crucial roles in reliability. Surface flaws act as stress concentrators that can initiate cracks under load. Advanced manufacturing protocols incorporate careful surface finishing steps that can improve component strength by 30-50% compared to as-sintered surfaces.
Heat treatment protocols significantly impact phase stability. Properly executed thermal processing ensures optimal tetragonal-to-monoclinic phase ratios, which directly determine the component’s mechanical properties and aging resistance. Inadequate heat treatment can leave components vulnerable to premature degradation, particularly in humid environments.
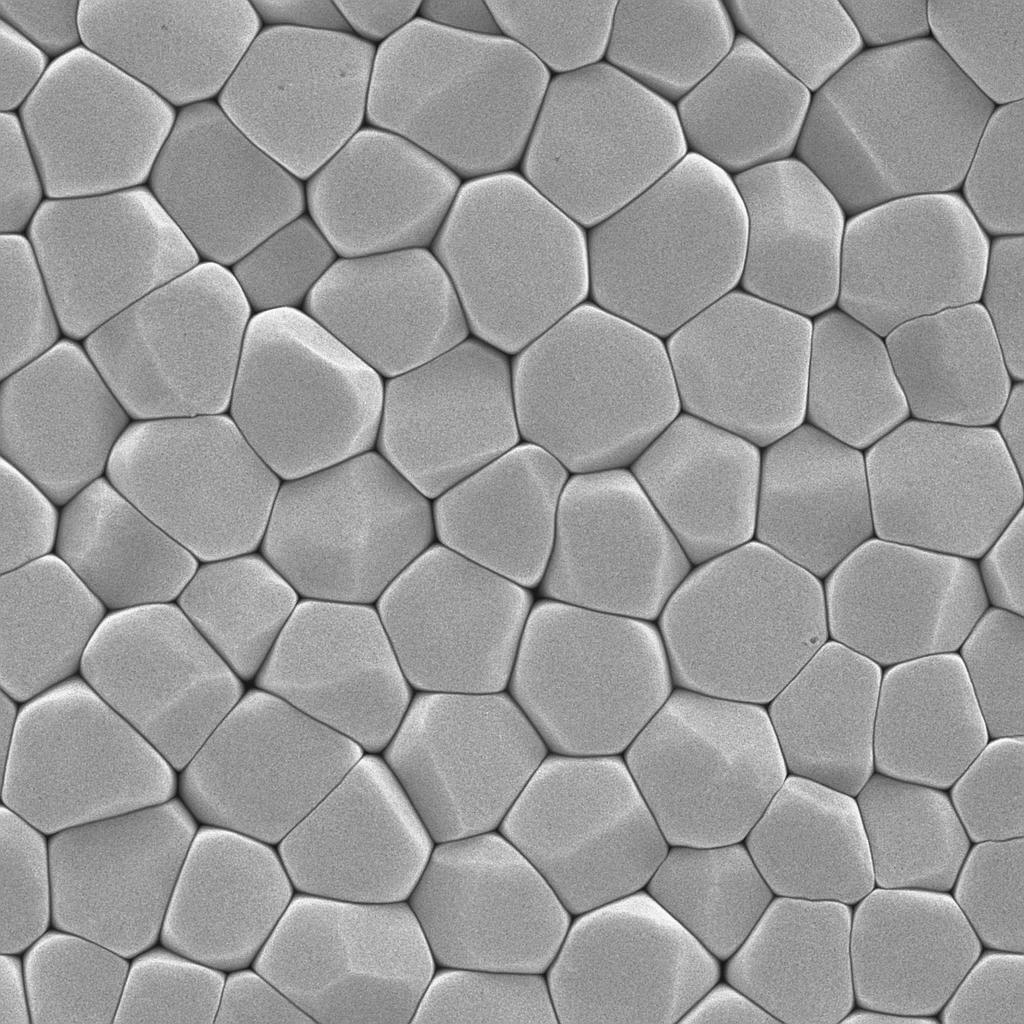
How Does Powder Processing Impact Final Product Quality?
The journey to reliable zirconia components begins with powder processing, which establishes the foundation for all subsequent manufacturing steps. You might be surprised to learn that up to 70% of final component quality is determined at this early stage.
Different powder preparation methods yield varying results. The co-precipitation method produces highly homogeneous powders with excellent sinterability but at higher cost. Hydrothermal synthesis creates powders with controlled morphology and narrow size distribution, beneficial for complex shapes. Sol-gel methods offer exceptional chemical homogeneity but typically involve more complex processing.
Powder Preparation Method | Particle Size Control | Homogeneity | Cost | Best For |
---|---|---|---|---|
Co-precipitation | Excellent | Very high | High | Medical components, precision parts |
Hydrothermal synthesis | Good | High | Medium-high | Complex geometries, thin-walled parts |
Sol-gel | Very good | Excellent | High | Multi-component systems, specialized applications |
Solid-state reaction | Fair | Moderate | Low | Standard industrial components |
Spray pyrolysis | Good | High | Medium | High-volume production |
Particle size distribution control proves essential for consistent results. Narrow distributions (typically with span values <1.0) promote uniform sintering behavior and minimize differential shrinkage that can cause warping or cracking. Modern manufacturing facilities employ sophisticated particle sizing equipment to maintain tight control over this critical parameter.
Additives selection and optimization significantly influence both processing behavior and final properties. Stabilizers like yttria (Y₂O₃) determine phase composition and mechanical characteristics, with 3 mol% being standard for structural applications. Sintering aids such as alumina or silica can reduce sintering temperature but must be precisely controlled to avoid compromising mechanical properties.
Mixing uniformity directly impacts component homogeneity. Inadequate mixing creates composition gradients that lead to differential sintering, internal stresses, and potential failure points. Advanced manufacturers employ high-energy mixing techniques followed by spray drying to ensure consistent powder characteristics throughout the batch.
Advanced powder characterization techniques play a vital role in quality control. Beyond basic particle size analysis, leading manufacturers employ techniques such as X-ray diffraction (XRD), specific surface area measurement (BET), and thermal analysis (DSC/TGA) to comprehensively evaluate powder properties before proceeding to forming operations.
Which Forming Techniques Yield Superior Zirconia Components?
The forming stage transforms zirconia powder into the desired component shape, establishing critical structural characteristics. What’s particularly interesting is that the choice of forming technique can dramatically influence reliability, even when using identical powder.
Dry pressing represents the most common forming method for simple geometries. This technique offers high production rates and good dimensional control but can create density gradients in complex shapes. Modern presses with advanced control systems minimize these issues through precise pressure distribution and multi-directional compaction.
Forming Technique | Complexity Capability | Density Uniformity | Production Rate | Typical Applications |
---|---|---|---|---|
Dry pressing | Low to medium | Good for simple shapes | Very high | Discs, rings, simple bushings |
Cold isostatic pressing | Medium | Excellent | Medium | Rods, tubes, symmetrical parts |
Injection molding | High | Very good | Medium-high | Complex shapes, thin-walled parts |
Extrusion | Low (prismatic) | Very good | High | Tubes, rods, honeycomb structures |
3D printing/additive | Very high | Moderate to good | Low | Prototypes, custom designs, complex geometries |
Cold isostatic pressing (CIP) significantly improves density uniformity. By applying pressure from all directions through a fluid medium, CIP eliminates the density gradients common in uniaxial pressing. Components formed via CIP typically show 15-25% higher strength and better reliability, particularly for larger or more complex geometries.
Injection molding excels for complex-shaped components. This technique combines zirconia powder with polymer binders to create a feedstock that can be molded into intricate shapes. While requiring additional processing steps for binder removal, injection molding enables the production of complex geometries impossible with other methods. The key challenge lies in maintaining dimensional control during binder removal and sintering.
Extrusion and 3D printing represent emerging alternatives with specific advantages. Extrusion works well for components with constant cross-sections, while 3D printing offers unparalleled geometric freedom. However, both techniques currently face challenges in achieving the same reliability as traditional methods, primarily due to density variations and potential defect introduction.
Different forming methods create distinct defect patterns that influence reliability. Dry pressing can introduce lamination defects at powder flow boundaries. Injection molding may create voids during binder removal. Understanding these characteristic defects allows manufacturers to implement specific quality control measures for each forming technique.
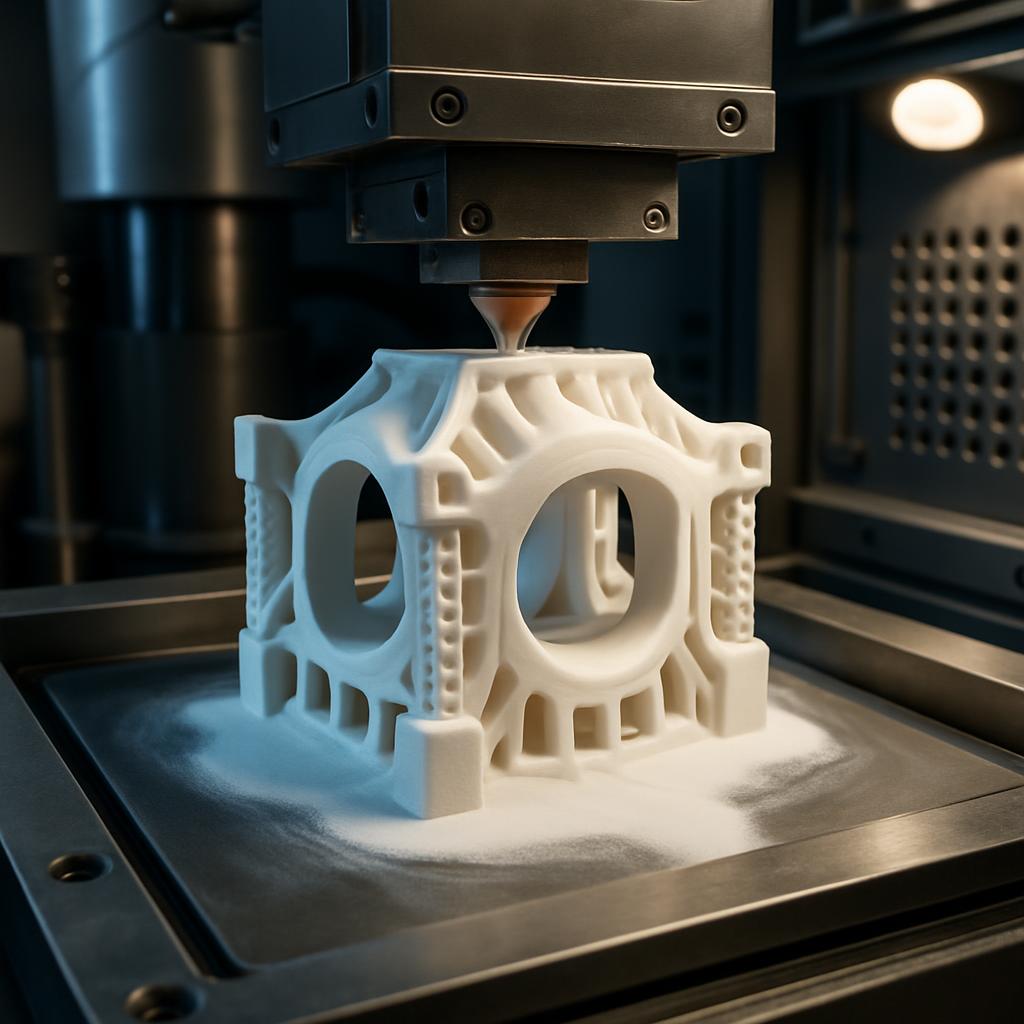
Why Is Sintering The Critical Stage For Reliability?
Sintering transforms the formed “green” component into a dense, strong ceramic, making it perhaps the most crucial stage in determining reliability. The truth is that even perfectly formed components can be ruined by improper sintering.
Traditional versus advanced sintering technologies offer different advantages. Conventional sintering in air atmospheres at 1400-1500°C remains the industry standard for most applications. However, advanced techniques like hot isostatic pressing (HIP) can further increase density and eliminate closed porosity, improving reliability for critical applications despite higher costs.
Sintering Method | Maximum Achievable Density | Process Temperature | Cycle Time | Relative Cost | Key Advantages |
---|---|---|---|---|---|
Conventional | 99.5% | 1400-1500°C | 8-15 hours | Low | Simple, well-established |
Two-step | 99.7% | 1250-1450°C | 10-20 hours | Low-medium | Better grain size control |
Hot isostatic pressing | >99.9% | 1200-1400°C | 4-8 hours | High | Highest density, closed pore elimination |
Microwave | 99.5% | 1300-1450°C | 2-4 hours | Medium | Rapid heating, energy efficient |
Spark plasma | >99.8% | 1000-1300°C | 0.5-2 hours | High | Rapid processing, fine grain size |
Temperature profile design proves critical for optimal results. The heating rate, maximum temperature, hold time, and cooling rate all significantly impact the final microstructure. Too rapid heating can create thermal gradients and cracking, while excessive hold times or temperatures cause unwanted grain growth. Modern sintering operations employ computer-controlled furnaces with precise temperature management to optimize these parameters.
Atmosphere control significantly influences phase stability. Sintering in reducing atmospheres can create oxygen vacancies that affect mechanical properties, while excessive oxygen can promote certain phase transformations. For most zirconia components, carefully controlled air atmospheres provide the best balance of properties.
Thermal gradients and size effects require careful management. Larger components face greater challenges in maintaining uniform temperature throughout the volume during sintering. Manufacturers address this through slower heating rates, optimized component positioning, and sometimes custom furnace configurations for particularly large or complex parts.
Innovative sintering methods offer specific advantages for certain applications. Microwave sintering provides more uniform heating from the inside out, reducing thermal gradients. Spark plasma sintering (SPS) enables extremely rapid densification with minimal grain growth, preserving nanoscale features. These techniques continue to evolve, offering new possibilities for enhanced reliability in specialized applications.
What Role Do Post-Processing Treatments Play?
Post-processing treatments can significantly enhance zirconia component reliability, addressing manufacturing imperfections and optimizing surface properties. You’ll find it valuable to know that properly executed post-processing can improve component lifespan by 30-50%.
Mechanical processing techniques must be carefully selected to avoid introducing new defects. Diamond grinding and polishing remain standard approaches but require proper cooling and controlled pressure to prevent surface damage. Advanced techniques like ultrasonic machining offer advantages for complex geometries but at higher cost.
Post-Processing Method | Surface Finish Capability | Risk of Damage | Processing Time | Cost | Best Applications |
---|---|---|---|---|---|
Diamond grinding | Very good | Medium | Moderate | Medium | Flat surfaces, simple contours |
Diamond polishing | Excellent | Low | Long | High | Optical components, wear surfaces |
Ultrasonic machining | Good | Low | Long | High | Complex internal features |
Laser machining | Good | Medium-high | Short | High | Precision features, micro-texturing |
Abrasive water jet | Fair | Low | Moderate | Medium | Thick sections, rough cutting |
Heat treatments effectively eliminate residual stresses. Components often develop internal stresses during manufacturing that can reduce strength and reliability. Annealing treatments at 1000-1200°C relieve these stresses while maintaining the desired phase composition. The specific temperature profile depends on component size and geometry.
Surface modification techniques can dramatically improve wear resistance. Processes like ion implantation create hardened surface layers that can increase wear resistance by 200-300% in demanding applications. These treatments prove particularly valuable for components subject to sliding contact or particulate erosion.
Coating applications provide protection in harsh environments. While zirconia offers excellent inherent corrosion resistance, specialized coatings can further enhance performance in extreme conditions. Environmental barrier coatings protect against high-temperature water vapor, while biocompatible coatings improve integration in medical applications.
Quality inspection and non-destructive evaluation methods ensure final component integrity. X-ray computed tomography can detect internal defects as small as 10-20 μm. Ultrasonic testing identifies subsurface flaws, while dye penetrant inspection reveals surface cracks. Leading manufacturers employ multiple complementary techniques to comprehensively evaluate critical components.
How Do Manufacturing Parameters Affect Specific Applications?
Manufacturing parameters must be tailored to specific applications to achieve optimal reliability. The key point to remember is that parameters that work perfectly for one application may produce substandard results in another.
Medical implant manufacturing demands exceptional precision and purity. The biomedical industry requires zirconia with >99.9% purity and precisely controlled yttria content (typically 3-5 mol%) to ensure biocompatibility and long-term stability. Manufacturing protocols must prevent all contamination and achieve 100% traceability for regulatory compliance.
Application | Critical Parameters | Key Challenges | Reliability Requirements | Typical Manufacturing Approach |
---|---|---|---|---|
Medical implants | Purity, phase stability | Biocompatibility, aging resistance | >15 years in vivo | Clean room processing, 100% inspection |
High-temperature industrial | Thermal shock resistance | Thermal cycling, chemical attack | 3-5 years continuous operation | Specialized compositions, protective coatings |
Electronic components | Dimensional precision | Electrical properties, hermeticity | <0.1% failure rate | Precision forming, controlled atmosphere sintering |
Cutting tools | Wear resistance, edge stability | Mechanical shock, thermal cycling | Predictable tool life | HIP processing, specialized edge treatments |
Aerospace components | Reliability, weight | Extreme environments, certification | Zero-failure tolerance | Advanced NDE, statistical process control |
High-temperature industrial applications focus on thermal stability. Components for furnace fixtures, molten metal handling, and thermal barriers require specialized compositions (often with magnesia or ceria stabilizers) and manufacturing protocols optimized for thermal shock resistance. Post-processing typically includes thermal cycling tests to verify performance under operating conditions.
Electronic and sensor component production prioritizes dimensional precision. Zirconia substrates and packages for electronic applications require exceptionally tight tolerances (often ±0.1% or better) and carefully controlled surface finish. Manufacturing typically involves precision forming followed by controlled-atmosphere sintering to maintain dimensional stability.
Cutting tool and abrasive production emphasizes edge stability and wear resistance. These applications benefit from higher hardness achieved through specific sintering profiles and sometimes post-sintering treatments. Quality control focuses on edge geometry consistency and microstructural uniformity to ensure predictable tool life.
Aerospace-grade components require specialized certification protocols. Beyond standard manufacturing controls, aerospace applications typically involve statistical process control, comprehensive documentation, and extensive testing. Manufacturing facilities must maintain specific certifications and demonstrate consistent process capability.
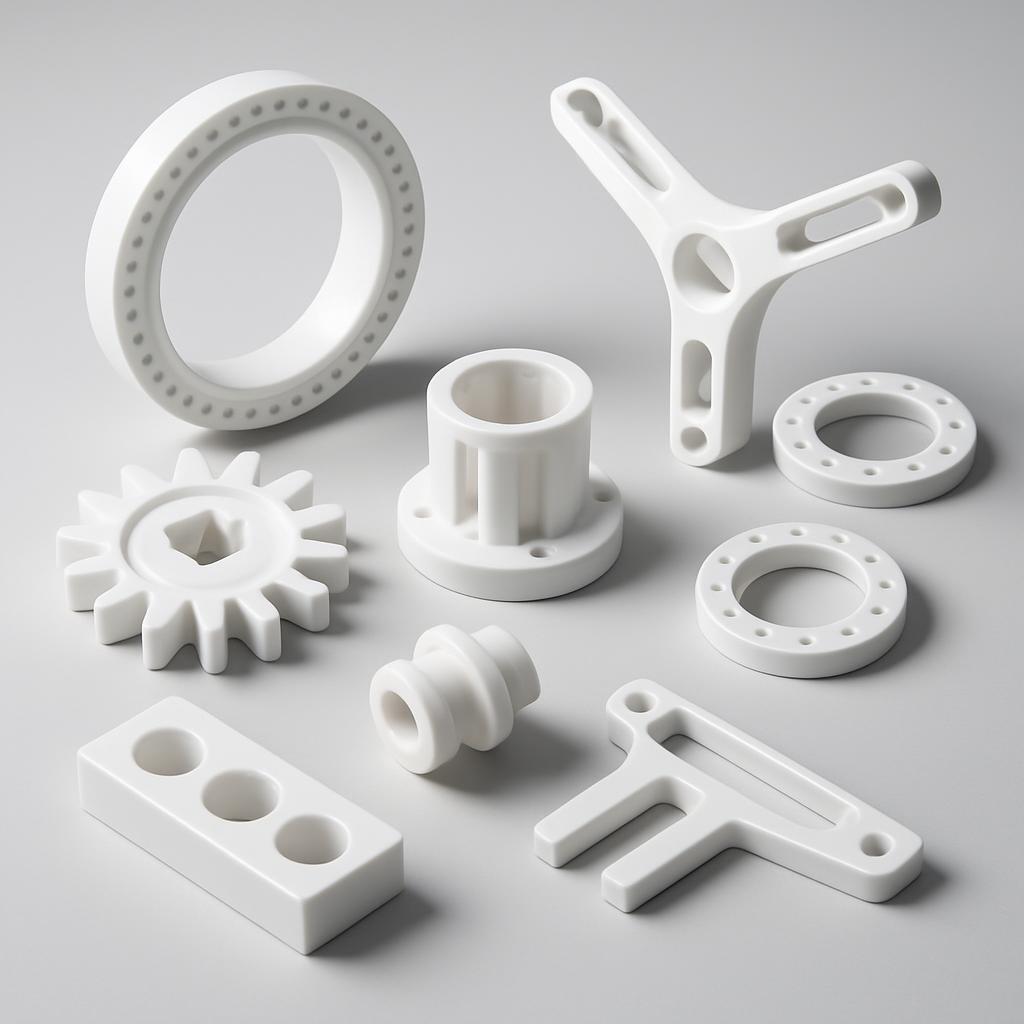
What Are The Latest Innovations In Zirconia Manufacturing?
Manufacturing technology for zirconia components continues to evolve rapidly, with several innovations promising significant reliability improvements. What makes this particularly exciting is that these advances are making previously impossible designs and applications feasible.
Smart manufacturing and digital twin technology represent major advances. By creating virtual models that simulate the entire manufacturing process, manufacturers can predict and prevent quality issues before they occur. These systems continuously monitor critical parameters and automatically adjust processing conditions to maintain optimal results.
Innovation | Technology Readiness | Reliability Impact | Implementation Cost | Primary Benefits |
---|---|---|---|---|
Digital twin technology | Commercial | High | High | Process optimization, predictive quality |
AI parameter optimization | Early commercial | Medium-high | Medium | Reduced defects, optimized properties |
In-situ monitoring | Commercial | High | Medium-high | Real-time quality control |
Nanoscale zirconia | Commercial for select applications | Very high | High | Superior mechanical properties |
Hybrid/composite zirconia | Commercial for select applications | High | Medium-high | Application-specific property optimization |
Artificial intelligence plays an increasing role in parameter optimization. Machine learning algorithms analyze historical production data to identify complex relationships between manufacturing parameters and final properties. These systems have demonstrated 15-30% reductions in defect rates while simultaneously improving mechanical properties through non-obvious parameter combinations.
In-situ monitoring and closed-loop control systems transform quality assurance. Rather than relying solely on post-production inspection, advanced manufacturers implement sensors throughout the production process. These systems detect anomalies in real-time and either adjust parameters automatically or alert operators before defects occur.
Nanoscale zirconia materials offer exceptional properties. By controlling grain size at the nanometer scale (typically <100 nm), manufacturers can achieve combinations of strength, toughness, and transparency impossible with conventional materials. While processing challenges remain, these materials show promise for next-generation applications.
Hybrid and composite zirconia materials provide application-specific solutions. By combining zirconia with other ceramics, metals, or polymers in carefully designed structures, manufacturers can create components with tailored property combinations. Examples include zirconia-alumina composites for improved toughness and zirconia-metal functionally graded materials for joining applications.
How To Implement Quality Control Throughout Production?
Comprehensive quality control throughout the production chain proves essential for reliable zirconia components. The bottom line is that even the best manufacturing methods fail without rigorous quality systems.
Raw material verification and batch management systems form the foundation. Leading manufacturers implement detailed specifications for all incoming materials and conduct comprehensive testing before production use. Each material batch receives a unique identifier that follows it through production, enabling complete traceability.
Quality Control Stage | Key Parameters | Testing Methods | Sampling Frequency | Critical Limits |
---|---|---|---|---|
Raw material verification | Purity, particle size, surface area | XRD, BET, ICP-MS | Each batch | Application-specific |
In-process monitoring | Density, dimensions, visual defects | Various physical measurements | Statistical sampling | Process-specific |
Statistical process control | Critical process parameters | Control charts, capability indices | Continuous | Cp, Cpk >1.33 |
Non-destructive testing | Internal defects, cracks | X-ray CT, ultrasonic | 100% for critical parts | Application-specific |
Traceability system | Documentation completeness | Audit | Continuous | Zero missing records |
In-process control points and parameter monitoring prevent quality drift. Rather than relying solely on final inspection, effective quality systems establish control points throughout production. Each critical parameter has defined limits with specific actions required when variations occur. This approach catches issues early when corrections remain possible.
Statistical process control provides early warning of potential issues. By tracking key parameters over time and analyzing trends, manufacturers can identify and address process shifts before they create defects. Effective systems maintain process capability indices (Cp, Cpk) above 1.33 for critical parameters, ensuring consistent quality.
Non-destructive testing technologies verify internal quality. X-ray computed tomography can detect internal voids or inclusions without damaging components. Ultrasonic testing identifies subsurface cracks or delaminations. For critical applications, 100% inspection using these technologies ensures that only flawless components reach customers.
Traceability systems enable rapid problem resolution. Complete documentation linking raw materials, processing parameters, inspection results, and final properties allows manufacturers to quickly identify root causes when issues arise. This capability proves particularly valuable for critical applications where failure analysis may be required.
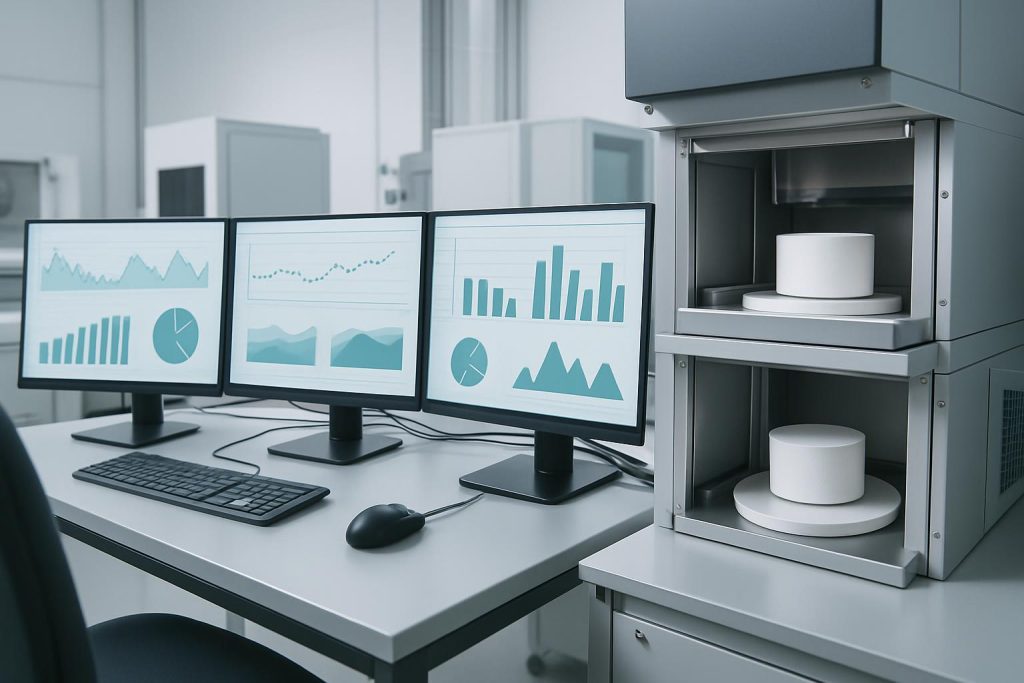
Conclusion
Manufacturing reliable zirconia components requires careful attention throughout the entire production process. From powder selection and processing through forming, sintering, and post-processing, each step significantly impacts final reliability. By implementing the manufacturing methods discussed in this article and maintaining rigorous quality control, manufacturers can consistently produce zirconia components that meet or exceed performance requirements.
For critical applications, advanced techniques like isostatic pressing, optimized sintering protocols, and comprehensive non-destructive testing provide the highest reliability levels. Emerging technologies including AI-optimized processing, in-situ monitoring, and novel material formulations continue to push performance boundaries even further.
By selecting manufacturing partners with demonstrated expertise in these advanced techniques and quality systems, companies can secure the reliable zirconia components essential for their most demanding applications. Contact our technical team today to discuss how these manufacturing approaches can be optimized for your specific requirements.
FAQ Section
Q1: How do different stabilizers affect zirconia components?
Different stabilizers (Y₂O₃, CeO₂, MgO) impact phase stability and mechanical properties of zirconia. Y₂O₃ stabilizes with optimal strength but a narrow processing range. CeO₂ offers better stability and a broader window but slightly lower strength. MgO excels in high-temperature settings. Stabilizer type influences sintering, phase behavior, and final reliability.
Q2: What testing methods predict the long-term reliability of zirconia components?
Key testing methods for long-term reliability include accelerated aging in humid conditions, cyclic fatigue testing, fracture toughness assessments, microstructural analysis, and simulation testing. Combining these with Weibull statistics enhances reliability predictions.
Q3: How does batch-to-batch consistency affect zirconia reliability?
Batch consistency is crucial for zirconia reliability, as small variations in materials can lead to significant performance differences. Strict material specifications, standardized processes, real-time monitoring, and traceability help maintain consistency and quickly identify issues.
Q4: What environmental factors are considered in zirconia manufacturing?
Environmental factors include energy use during sintering, water consumption, handling of harmful materials, dust control, and worker safety. Efficient manufacturing incorporates energy-saving technologies, closed-loop water systems, non-toxic additives, and dust collection to minimize impact.
Q5: What is the most cost-effective method for manufacturing reliable zirconia components?
Optimized dry pressing with isothermal sintering offers the best cost-benefit for most applications. For complex shapes, injection molding can lower unit costs at higher initial tooling expenses. Choosing the right combination methods is essential based on application requirements and production volume.