In today’s volatile manufacturing landscape, securing reliable zirconia supply chains has become a critical challenge for B2B buyers. The increasing demand for high-performance zirconia supply chains across industries, coupled with global supply chain disruptions, has created significant procurement hurdles. Companies that rely on consistent zirconia quality face production delays, quality variations, and unpredictable costs when zirconia supply chains falter. This article provides practical strategies for establishing resilient zirconia supply networks, implementing robust quality control measures, and leveraging technology to minimize disruptions. Drawing from industry best practices, these approaches help procurement teams maintain production continuity while ensuring the consistent material quality essential for high-performance applications.
Why Is Supply Chain Reliability Critical for Zirconia Materials?
The reliability of zirconia supply chains directly impacts manufacturing success across multiple industries. Unlike commodity materials, zirconia requires precise quality consistency to perform in demanding applications like medical implants, aerospace components, and advanced electronics.
But here’s the reality: even minor variations in zirconia properties can cause catastrophic product failures. When zirconia supply chains become unstable, these quality variations increase dramatically, creating ripple effects throughout production processes.
Manufacturing operations dependent on zirconia face several critical challenges when zirconia supply chains reliability falters:
● Production disruptions: Inconsistent zirconia deliveries force production slowdowns or complete stoppages, with each day of downtime potentially costing manufacturers tens of thousands of dollars. One automotive components manufacturer reported $175,000 in lost production per day when zirconia supplies failed to meet specifications.
● Quality inconsistencies: Variations in material properties between batches require constant process adjustments, increasing scrap rates and quality control costs. These inconsistencies often remain undetected until final product testing, multiplying the financial impact.
● Engineering complications: Design teams must build in wider tolerance margins when material properties cannot be guaranteed, potentially compromising product performance or requiring more expensive manufacturing processes.
● Competitive disadvantages: Companies with unreliable zirconia supply chains lose market share to competitors who can deliver consistent quality and meet delivery schedules.
Impact Area | Consequences of Unreliable Zirconia Supply | Financial Implications |
---|---|---|
Production | Line stoppages, reduced throughput | $10,000-$200,000/day depending on industry |
Quality | Increased rejection rates, rework requirements | 15-30% higher production costs |
Engineering | Conservative designs, performance limitations | Reduced market competitiveness |
Customer Satisfaction | Missed delivery dates, inconsistent performance | Lost contracts, reputation damage |
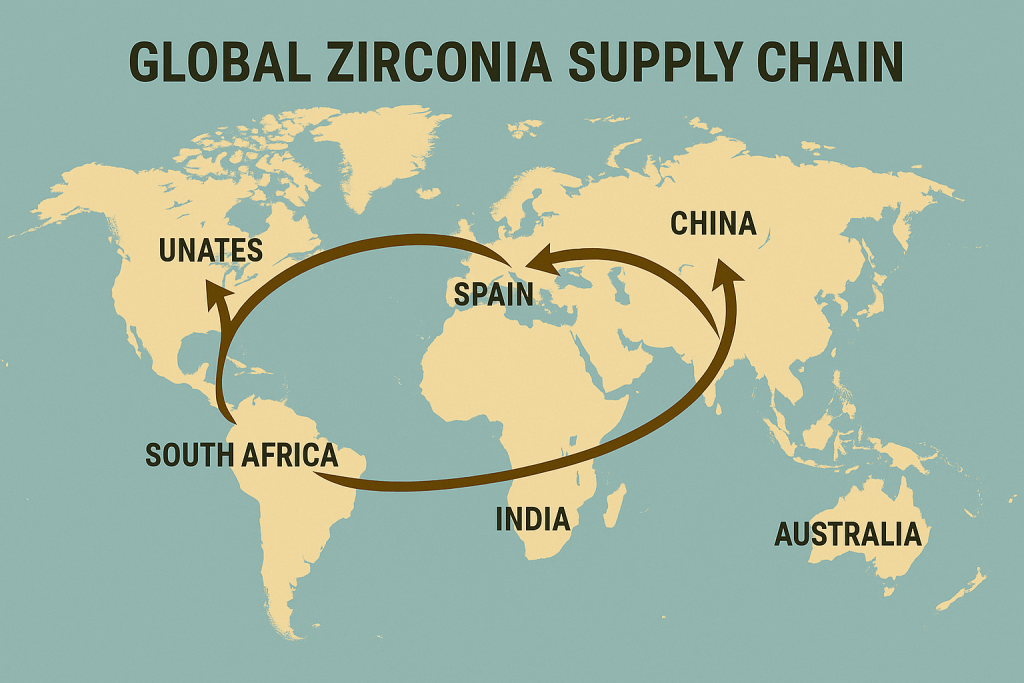
What Are the Core Components of a Resilient Zirconia Supply Chain?
Building resilience into zirconia supply chains requires a systematic approach addressing multiple interconnected elements. The foundation of zirconia supply chain resilience rests on four core components that work together to maintain material flow despite disruptions.
Here’s what matters most: zirconia supply chain visibility provides the foundation for all other resilience measures. Without clear visibility across the entire zirconia supply network, even the most sophisticated risk management strategies will fail.
● Multi-tier supplier mapping: Effective resilience strategies extend beyond direct suppliers to include second and third-tier providers. Comprehensive supplier mapping identifies all entities involved in your zirconia supply chains, including raw material producers, processors, and logistics providers. This visibility allows procurement teams to identify potential bottlenecks and single points of failure before they cause disruptions.
● Geographic diversification strategies: Concentrating zirconia sourcing in a single region creates significant vulnerability to localized disruptions like natural disasters, political instability, or transportation bottlenecks. Strategic geographic diversification balances risk reduction against the complexity of managing multiple supply sources. The optimal approach typically involves primary suppliers in stable regions supplemented by backup sources in different geographic areas.
● Inventory optimization techniques: Balancing inventory carrying costs against stockout risks requires sophisticated modeling that accounts for lead time variability, demand fluctuations, and criticality of different zirconia grades. Advanced inventory optimization moves beyond simple safety stock calculations to implement segmented strategies based on material criticality, supply risk, and usage patterns.
● Digital tracking systems: End-to-end zirconia supply chain visibility depends on integrated digital systems that provide real-time status information across the entire network. Modern tracking platforms combine IoT sensors, cloud-based data integration, and analytics to monitor material movement, quality parameters, and potential disruptions.
Resilience Component | Traditional Approach | Advanced Approach | Implementation Complexity | Resilience Impact |
---|---|---|---|---|
Supplier Network | Single-tier focus | Multi-tier mapping and management | High | Very High |
Geographic Strategy | Cost-optimized concentration | Strategic diversification | Medium | High |
Inventory Management | Fixed safety stock levels | Dynamic, risk-based segmentation | Medium | Medium-High |
Visibility Systems | Periodic manual reporting | Real-time digital tracking | High | Very High |
How Can Quality Control Be Integrated Throughout the Supply Chain?
Maintaining consistent zirconia quality requires a coordinated quality control approach spanning the entire zirconia supply chain. Traditional quality management focused primarily on incoming material inspection fails to address upstream factors that influence material properties.
Think about this: quality issues detected at your facility began much earlier in the zirconia supply chain. By implementing upstream quality controls, you can prevent problems before materials ever reach your receiving dock.
● Establishing standardized quality metrics: Effective quality control begins with clearly defined, measurable parameters that all zirconia supply chain participants understand and monitor. These metrics should include both material-specific properties (chemical composition, particle size distribution, phase stability) and process-related factors (contamination controls, temperature consistency, batch homogeneity).
● Implementing batch testing protocols: Strategic testing at critical zirconia supply chain nodes provides early detection of quality deviations before they impact downstream processes. Rather than relying solely on final inspection, advanced quality systems incorporate testing at raw material sourcing, after major processing steps, and before shipment.
● Leveraging third-party certification: Independent verification provides objective quality assurance that complements internal testing programs. Third-party laboratories offer specialized testing capabilities, reference standards, and impartial documentation that strengthens quality control systems.
● Real-time quality monitoring technologies: Advanced sensor systems enable continuous monitoring of critical process parameters that influence zirconia quality. These technologies range from in-line particle size analyzers and chemical composition sensors to environmental monitoring systems that track temperature, humidity, and potential contamination sources.
Quality Control Element | Implementation Level | Benefits | Challenges | ROI Timeframe |
---|---|---|---|---|
Standardized Metrics | Foundation | Common language, consistent evaluation | Initial supplier alignment | Short-term |
Multi-point Testing | Intermediate | Early detection, root cause identification | Coordination, cost | Medium-term |
Third-party Certification | Intermediate | Objectivity, specialized capabilities | Additional expense | Medium-term |
Real-time Monitoring | Advanced | Immediate intervention, trend analysis | Technology investment | Long-term |
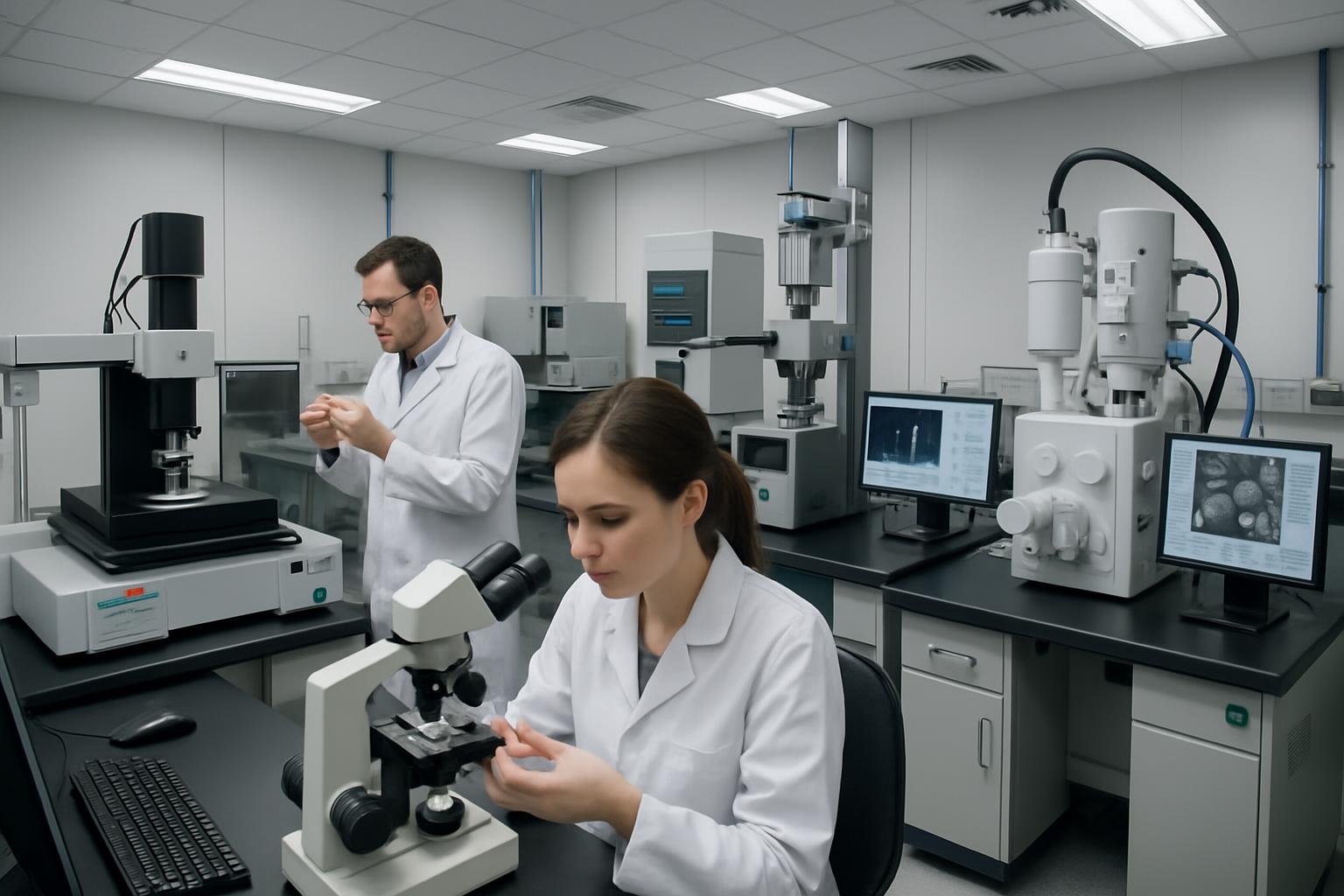
What Risk Management Strategies Protect Against Supply Disruptions?
Effective risk management for zirconia supply chains combines proactive identification of potential disruptions with prepared response strategies. This systematic approach transforms zirconia supply chain vulnerabilities from unexpected crises into manageable challenges.
Consider this critical point: most zirconia supply chain disruptions follow predictable patterns that can be identified and mitigated before they impact operations. The difference between companies that weather supply challenges and those that suffer significant impacts often comes down to preparation rather than reaction.
● Early warning systems: Sophisticated risk monitoring combines technology and human intelligence to identify potential disruptions before they impact material flow. These systems track multiple risk indicators including supplier financial health, geopolitical developments, transportation bottlenecks, and natural disaster potential.
● Contingency planning: Detailed response plans for different disruption scenarios enable rapid, effective action when zirconia supply chain challenges emerge. Comprehensive contingency planning addresses alternative sourcing options, transportation route changes, production schedule adjustments, and customer communication protocols for various disruption types.
● Strategic buffer stocks: Targeted inventory strategies for critical zirconia materials provide time to implement contingency plans during supply disruptions. Rather than applying uniform safety stock policies across all materials, advanced approaches segment inventory strategies based on criticality, supply risk, and lead time variability.
● Supplier financial monitoring: Proactive assessment of supplier financial stability helps identify potential disruption risks before they manifest as delivery or quality problems. Regular financial health checks, including liquidity ratios, debt levels, and profitability trends, provide early warning of suppliers that may struggle to maintain operations.
Risk Management Strategy | Application Level | Implementation Approach | Resource Requirements | Disruption Protection Level |
---|---|---|---|---|
Early Warning Systems | Enterprise | Integrated risk monitoring platform | High | Very High |
Contingency Planning | Material Category | Scenario-based response protocols | Medium | High |
Buffer Stock Strategy | Individual Material | Risk-based inventory segmentation | Medium | Medium-High |
Financial Monitoring | Key Suppliers | Regular financial health assessment | Low-Medium | Medium |
How Do Collaborative Supplier Relationships Enhance Quality Consistency?
Traditional transactional supplier relationships focused primarily on price negotiation fail to deliver the quality consistency required for high-performance zirconia applications. Leading organizations have shifted toward collaborative partnerships that align incentives and capabilities across the zirconia supply chain.
Here’s the truth: the lowest-price supplier rarely delivers the lowest total cost when quality inconsistency impacts your production. Collaborative relationships that prioritize quality consistency typically provide better value despite potentially higher unit prices.
● Joint quality improvement initiatives: Collaborative programs that combine buyer and supplier expertise address root causes of quality variations more effectively than compliance-focused approaches. These initiatives typically begin with joint analysis of historical quality data to identify priority improvement areas, followed by cross-functional teams developing and implementing solutions.
● Knowledge sharing platforms: Systematic information exchange between buyers and suppliers creates a foundation for continuous quality improvement. Digital collaboration platforms enable secure sharing of technical specifications, process data, testing results, and improvement ideas.
● Performance-based incentive structures: Aligning financial incentives with quality performance strengthens supplier commitment to consistency. Advanced procurement organizations move beyond penalty clauses for non-conformance to implement positive incentives for superior quality performance.
● Long-term partnership agreements: Strategic zirconia supply chain relationships governed by multi-year agreements provide the stability needed for significant quality investments. These agreements typically include volume commitments, pricing mechanisms, quality expectations, and continuous improvement targets.
Collaboration Element | Traditional Approach | Collaborative Approach | Quality Impact | Implementation Complexity |
---|---|---|---|---|
Quality Initiatives | Buyer-directed compliance | Joint problem-solving | High | Medium |
Information Sharing | Limited, transaction-focused | Comprehensive, transparent | Very High | High |
Incentive Structure | Penalty-based | Balanced rewards and consequences | Medium-High | Medium |
Relationship Timeframe | Short-term, transactional | Long-term, strategic | High | Medium-High |
What Technologies Are Transforming Zirconia Supply Chain Management?
Digital technologies are revolutionizing how organizations manage zirconia supply chains, enabling unprecedented visibility, predictive capabilities, and process control. These technologies transform traditional reactive supply management into proactive, data-driven approaches.
This is important: technology alone doesn’t create zirconia supply chain resilience. The most successful implementations combine advanced technology with redesigned processes and skilled personnel who can translate data into effective decisions.
● Blockchain applications for material traceability: Distributed ledger technology creates immutable records of zirconia materials as they move through the supply chain, enabling complete traceability from raw material to finished component. Blockchain systems record critical information including material properties, processing parameters, test results, and chain of custody at each supply chain stage.
● AI-powered demand forecasting: Machine learning algorithms analyzing multiple data streams generate more accurate demand predictions than traditional forecasting methods. These systems incorporate historical usage patterns, customer order trends, market indicators, and even social media sentiment to predict future zirconia requirements.
● IoT solutions for real-time monitoring: Connected sensor networks throughout the zirconia supply chain provide continuous visibility into material location, condition, and surrounding environment. These systems monitor critical parameters like temperature, humidity, shock exposure, and processing conditions that might affect zirconia quality.
● Digital twin technology: Virtual zirconia supply chain models that mirror physical operations enable scenario planning, risk assessment, and process optimization without disrupting actual material flow. These digital twins combine real-time data from physical operations with simulation capabilities to predict how changes or disruptions would impact the entire supply network.
Technology | Primary Benefits | Implementation Challenges | Adoption Stage | ROI Timeframe |
---|---|---|---|---|
Blockchain Traceability | Complete provenance verification | Integration complexity | Early | Medium-term |
AI Forecasting | Improved accuracy, reduced inventory | Data quality, algorithm training | Growth | Short-medium term |
IoT Monitoring | Real-time visibility, preventive intervention | Sensor deployment, data management | Growth | Short-medium term |
Digital Twin | Risk simulation, optimization capabilities | Model development, data integration | Early | Long-term |
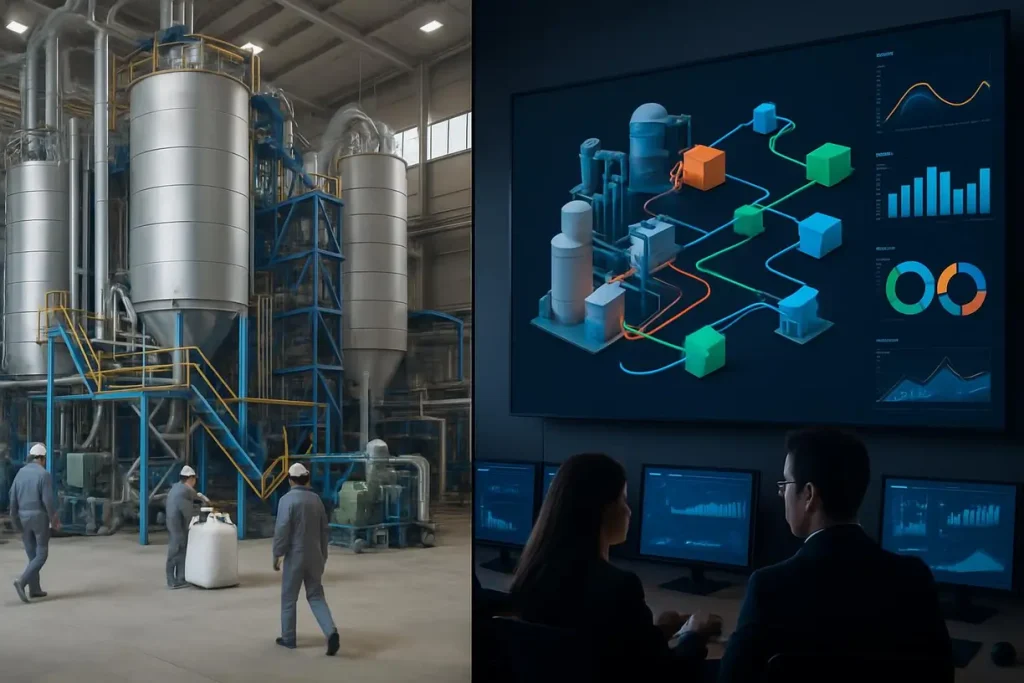
How Can Organizations Measure Supply Chain Performance for Zirconia?
Effective performance measurement provides the foundation for continuous zirconia supply chain improvement. Organizations that excel in zirconia supply management implement comprehensive metrics systems that balance multiple performance dimensions.
Remember this fundamental principle: what gets measured gets managed. The metrics you choose directly influence which aspects of zirconia supply chain performance receive attention and resources.
● Key performance indicators: A balanced scorecard approach measuring multiple zirconia supply chain dimensions provides more actionable insights than isolated metrics. Comprehensive measurement frameworks typically include quality consistency, delivery reliability, risk management effectiveness, cost performance, and innovation capabilities.
● Benchmarking methodologies: Comparing performance against industry standards and best practices identifies improvement opportunities that might not be apparent from internal data alone. Effective benchmarking combines quantitative metrics comparison with qualitative assessment of processes and practices.
● Continuous improvement frameworks: Structured approaches for identifying, prioritizing, and implementing zirconia supply chain enhancements transform measurement insights into tangible improvements. These frameworks typically include regular performance reviews, root cause analysis of deviations, and formal project management for implementation initiatives.
● ROI calculation models: Quantifying the financial impact of zirconia supply chain investments enables more informed decision-making and resource allocation. Comprehensive ROI models consider multiple value dimensions including direct cost savings, quality improvement benefits, risk reduction value, and productivity enhancements.
Performance Dimension | Leading Indicators | Lagging Indicators | Measurement Frequency | Primary Stakeholders |
---|---|---|---|---|
Quality Consistency | Process capability indices | Defect rates, customer complaints | Daily/Weekly | Quality, Operations |
Delivery Reliability | Supplier capacity utilization | On-time delivery, lead time adherence | Weekly | Operations, Procurement |
Risk Management | Risk assessment completion | Disruption frequency, recovery time | Monthly | Procurement, Finance |
Cost Performance | Price trend analysis | Total cost of ownership | Monthly/Quarterly | Finance, Procurement |
Innovation | Improvement suggestions | New material implementations | Quarterly | R&D, Procurement |
Conclusion
Securing reliable zirconia supply chains requires a comprehensive approach combining strategic supplier relationships, integrated quality control, proactive risk management, and enabling technologies. Organizations that implement these strategies consistently outperform competitors during zirconia supply chain disruptions while maintaining the material quality consistency essential for high-performance applications. Companies adopting these approaches have reported up to 85% fewer quality-related production disruptions and 40% faster recovery from supply chain disturbances. To strengthen your zirconia supply chain resilience, partner with Global Industry for access to industry-leading expertise in ceramic material sourcing, quality assurance programs, and supply chain optimization. Contact our technical team today to schedule a supply chain vulnerability assessment and develop a customized resilience strategy tailored to your specific manufacturing requirements.
FAQ Section
Q1: How does zirconia quality variation impact end-product performance?
Quality variations in zirconia materials can significantly affect end-product performance through inconsistent mechanical properties, dimensional stability issues, and unpredictable wear resistance. For precision applications, even minor variations in chemical composition or microstructure can lead to premature component failure, reduced service life, or compromised functionality. Manufacturing processes may require constant adjustment to compensate for these variations, increasing production costs and reducing efficiency. In critical applications like medical implants or aerospace components, quality inconsistencies can create serious safety risks and potential liability issues.
Q2: What are the most effective supplier qualification processes for zirconia materials?
The most effective supplier qualification processes for zirconia materials combine rigorous technical assessment with comprehensive business evaluation. Technical qualification should include detailed material specification reviews, production capability audits, quality management system verification, and extensive sample testing across multiple batches. Business qualification should assess financial stability, capacity planning, ethical practices, and environmental compliance. Progressive qualification programs typically involve a multi-stage approach: initial screening, documentation review, site audits, trial orders, and continuous performance monitoring.
Q3: How can companies balance cost efficiency with quality assurance in zirconia supply chains?
Companies can balance cost efficiency with quality assurance by adopting a total cost of ownership (TCO) approach rather than focusing solely on purchase price. This involves quantifying the financial impact of quality issues, including rework costs, customer returns, warranty claims, and brand damage. Strategic approaches include tiered supplier programs that match zirconia quality levels to application requirements, collaborative cost reduction initiatives that preserve quality standards, and value engineering that optimizes material specifications without compromising performance.
Q4: What emerging risks should procurement teams monitor in global zirconia supply chains?
Procurement teams should monitor several emerging risks in global zirconia supply chains: geopolitical tensions affecting access to raw material sources, particularly in regions with concentrated zirconium deposits; increasing environmental regulations impacting mining and processing operations; energy price volatility affecting production costs; counterfeit materials entering supply chains through unauthorized distributors; intellectual property concerns when sharing specifications with international suppliers; cybersecurity vulnerabilities in connected supply chain systems; and climate change impacts on transportation infrastructure and mining operations.
Q5: How are sustainability requirements changing zirconia supply chain management?
Sustainability requirements are fundamentally transforming zirconia supply chain management through increased demands for environmental impact transparency, ethical sourcing verification, and circular economy practices. Companies now face pressure to document carbon footprints across the entire supply chain, implement water conservation measures in processing operations, and ensure fair labor practices at mining sites. Advanced organizations are developing closed-loop systems for zirconia recycling, investing in energy-efficient production technologies, and collaborating with suppliers on sustainability innovation.