In modern industrial settings, extreme environments pose unprecedented challenges to materials. High temperatures, corrosion, wear, and mechanical stress continuously test the limits of traditional materials. Against this backdrop, zirconia materials have emerged as the preferred solution for extreme industrial environments due to their exceptional performance characteristics. This article explores the unique properties of these materials and how they effectively address various challenges in extreme industrial settings.
What Material Challenges Exist in Extreme Industrial Environments?
Extreme industrial conditions typically manifest as combinations of severe factors that collectively challenge material performance. In these harsh settings, zirconia demonstrate remarkable resilience where conventional options fail.
High-temperature environments represent one of the most common extreme conditions. Many industrial processes, such as metal smelting, glass manufacturing, and ceramic sintering, operate at temperatures exceeding 1000°C. At these temperatures, most metallic materials soften, deform, or even melt, while polymer materials are completely unusable. Zirconia materials, however, maintain their structural integrity and performance even under these extreme thermal conditions.
Industrial Sector | Typical Temperature Range | Challenges for Traditional Materials | Zirconia Materials Advantage |
---|---|---|---|
Metal Smelting | 1200-1600°C | Metal component softening, refractory erosion | Retain strength and resist erosion |
Glass Manufacturing | 1400-1600°C | Mold thermal fatigue, melt erosion | Resist thermal shock and glass attack |
Ceramic Sintering | 1200-1800°C | Kiln furniture deformation, thermal shock cracking | Maintain dimensional stability |
Corrosive chemical environments pose equally severe challenges. Strong acids, strong bases, and oxidizing media common in chemical, petrochemical, and metallurgical industries rapidly degrade traditional materials. For example, sulfuric acid environments corrode most metals; hydrofluoric acid attacks glass and many ceramic materials. The chemical stability of zirconia materials makes them exceptionally resistant to these aggressive environments.
High-wear conditions represent another common extreme environment. In mining, cement production, and powder handling industries, material surfaces continuously experience impact and friction from hard particles, resulting in severe wear losses. Traditional wear-resistant steels often exhibit rapid material loss in these environments. Zirconia materials, with their superior hardness and toughness combination, significantly outperform conventional options in these applications.
The coexistence of multiple extreme conditions makes material selection particularly challenging. For instance, high-temperature corrosive environments accelerate material degradation rates; under high-temperature wear conditions, material hardness and strength typically decrease, further exacerbating wear rates. Zirconia excel in these compound extreme environments due to their multifunctional performance characteristics.
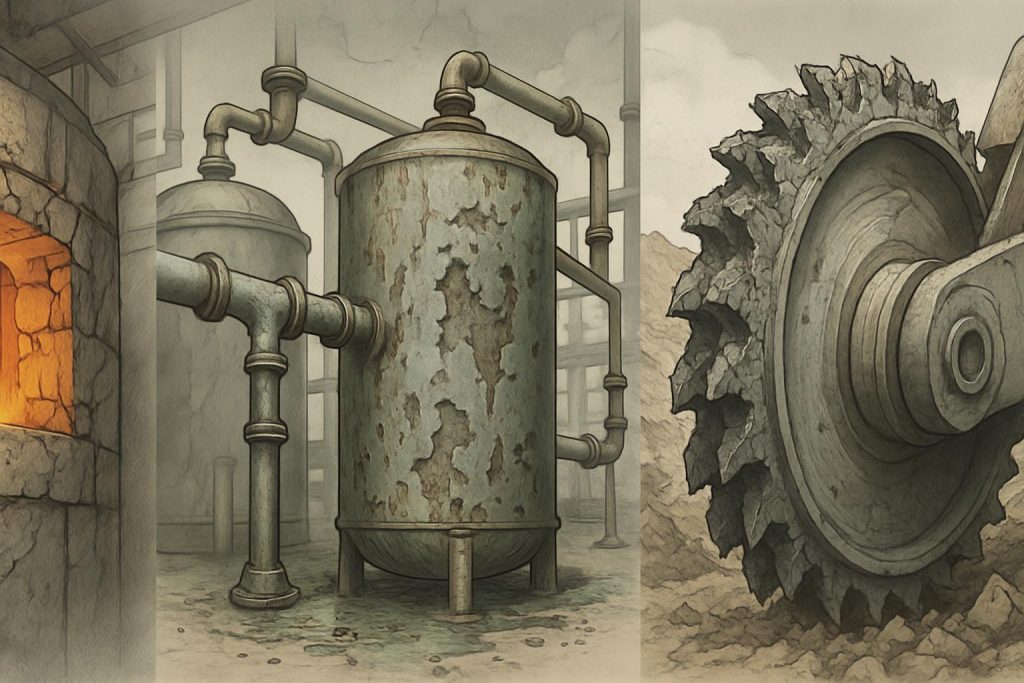
What Key Properties Make Zirconia Materials Exceptional?
Zirconia materials (ZrO₂), as advanced ceramic materials, possess a unique set of physical and chemical properties that enable their outstanding performance in extreme industrial environments.
From a chemical composition and crystal structure perspective, pure zirconia exists in three crystalline forms: monoclinic phase at room temperature, tetragonal phase above 1170°C, and cubic phase above 2370°C. These phase transformations are accompanied by volume changes. To control these phase transformations and stabilize the material structure, stabilizers such as yttria (Y₂O₃), magnesia (MgO), or calcia (CaO) are typically added.
Based on the type and content of stabilizers, zirconia can be classified into several main types:
Type | Stabilizer Content | Key Characteristics | Typical Applications |
---|---|---|---|
Partially Stabilized Zirconia (PSZ) | 3-8% | High toughness, good thermal shock resistance | Valves, pump components, thermal barrier coatings |
Fully Stabilized Zirconia (FSZ) | >8% | Excellent high-temperature stability, ionic conductivity | Oxygen sensors, solid oxide fuel cells |
Tetragonal Zirconia Polycrystal (TZP) | 2-3% | Extremely high strength and toughness | Precision mechanical parts, cutting tools |
The mechanical properties of zirconia are impressive. Their hardness typically ranges between 1200-1400 HV, with flexural strength reaching 900-1200 MPa and fracture toughness of 6-15 MPa·m½, far exceeding most ceramic materials. These excellent mechanical properties allow zirconia to maintain structural integrity in high-load and high-stress environments.
In terms of thermal properties, zirconia materials also perform exceptionally well. They have a melting point of 2715°C and maintain structural stability at extreme temperatures above 2000°C. Its low thermal conductivity makes them excellent thermal barrier materials, protecting underlying components from extreme heat.
Chemical stability is another major advantage. They resist corrosion from most acidic and alkaline solutions, exhibiting high stability in the pH range of 2-12. Even at high temperatures, it can resist corrosion from oxidizing and reducing atmospheres, making them ideal for aggressive chemical environments.
How Do Zirconia Materials Address High-Temperature Industrial Environments?
High-temperature industrial environments pose extreme challenges to materials, and zirconia materials have become an ideal choice in these settings due to their exceptional high-temperature performance.
These materials exhibit unique phase transformation behavior at different temperature ranges. By adding appropriate amounts of stabilizers, these transformations can be controlled, allowing the material to remain stable at high temperatures. For example, adding 8mol% yttria can fully stabilize the cubic phase structure of zirconia materials, maintaining phase stability across a wide temperature range from room temperature to 2200°C.
In ultra-high temperature applications above 2000°C, zirconia perform excellently. For instance, in glass furnaces, blocks can directly contact molten glass at 1600°C and work stably in this environment for several years. In metal casting industries, pouring systems can withstand molten metals above 1500°C without significant thermal erosion or thermal shock cracking.
High-Temperature Application | Operating Temperature | Solution | Performance Advantage |
---|---|---|---|
Glass Furnaces | 1400-1600°C | FSZ blocks and melting pool components | 3× longer lifespan than traditional materials |
Metal Casting | 1200-1700°C | PSZ pouring systems | 50% reduction in heat loss, improved casting quality |
Heat Treatment Furnaces | 1000-1400°C | TZP furnace components and supports | Reduced deformation, extended service life |
Thermal cycling conditions present another major challenge in high-temperature applications. Frequent heating and cooling generate internal thermal stresses in materials, eventually leading to thermal fatigue and cracking. Zirconia materials, especially magnesia-stabilized PSZ, exhibit excellent thermal shock resistance. These specialized materials can withstand hundreds or even thousands of rapid temperature changes without failure.
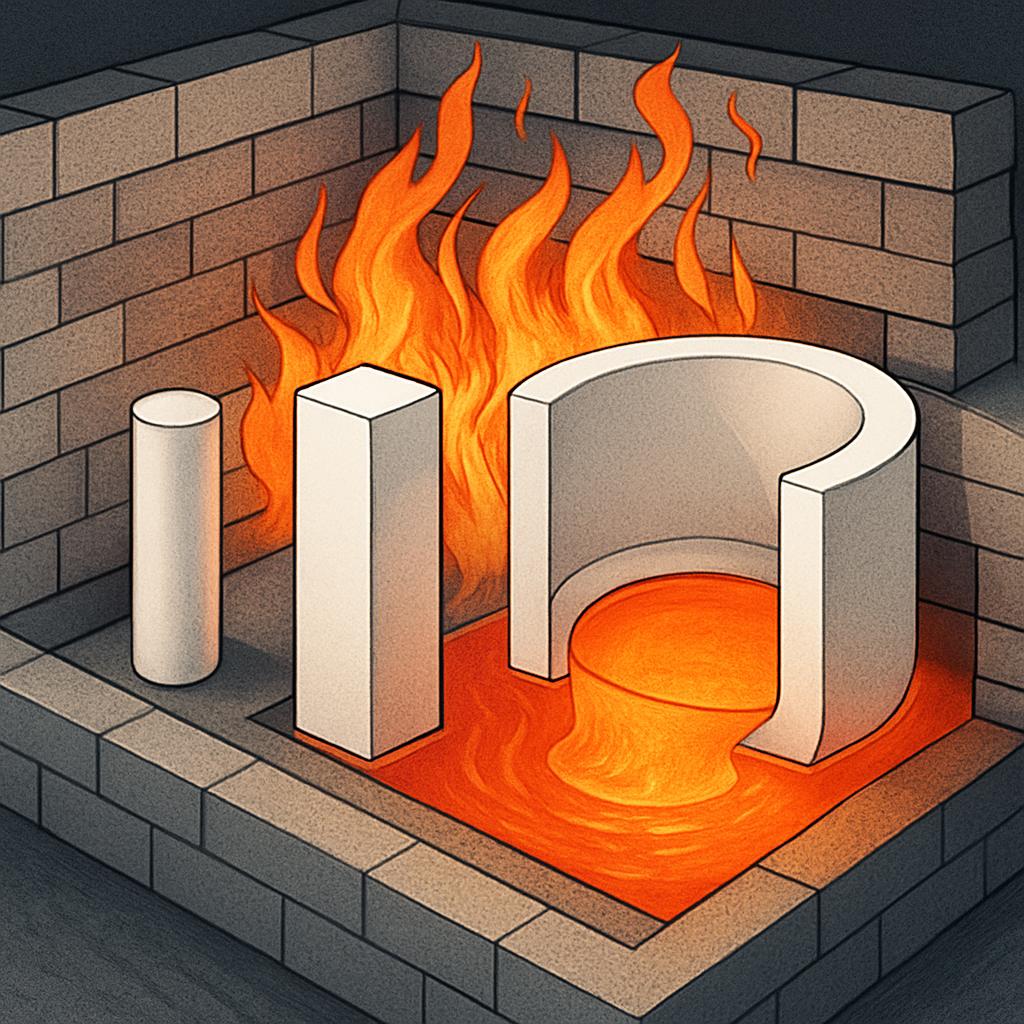
Compared to other high-temperature materials, zirconia offers distinct overall performance benefits. While materials like silicon carbide may outperform in specific properties, zirconia’s balanced performance and relatively lower cost make it practical for many applications.
How Do Zirconia Materials Perform in Corrosive Environments?
Corrosive environments present another major challenge in industrial applications, and zirconia materials excel in this area as well.
These materials demonstrate exceptional stability in strong acid and strong base environments. Experimental data show that at room temperature, zirconia can resist corrosion from most concentrations of sulfuric acid, hydrochloric acid, nitric acid, and phosphoric acid, with corrosion rates typically below 0.1mm/year. In alkaline environments, zirconia materials also exhibit extremely high corrosion resistance to sodium hydroxide and potassium hydroxide solutions.
Corrosive Medium | Concentration | Temperature | Zirconia Materials Corrosion Rate | Stainless Steel Corrosion Rate |
---|---|---|---|---|
Sulfuric Acid | 98% | 80°C | <0.1mm/year | >10mm/year |
Hydrochloric Acid | 37% | 25°C | <0.05mm/year | 5-8mm/year |
Sodium Hydroxide | 50% | 60°C | <0.01mm/year | 0.5-2mm/year |
The chemical and petrochemical industries have widely adopted zirconia materials to solve corrosion problems. For example, in sulfuric acid production equipment, valves and pump components can work stably in 98% concentrated sulfuric acid environments for many years, while traditional alloy materials typically need replacement every 6-12 months.
Long-term stability under oxidizing and reducing atmospheres is another major advantage. In high-temperature oxidizing environments, zirconia are already fully oxidized and therefore will not undergo further oxidation. In reducing atmospheres, zirconia materials typically remain stable below 1500°C and only experience partial reduction at higher temperatures.
High-temperature corrosive environments are among the most challenging operating conditions because high temperatures accelerate chemical reaction rates, making corrosion processes more intense. In such environments, zirconia’ chemical stability and high-temperature performance combine to provide comprehensive advantages that other materials can hardly match.
Why Do Zirconia Materials Excel in High-Wear Applications?
High-wear environments represent another major challenge in industrial applications, and zirconia materials’ excellent tribological properties make them ideal wear-resistant materials.
Zirconia’ tribological characteristics stem from their high hardness and unique microstructure. Their hardness typically ranges between 1200-1400 HV, approaching traditional hard materials like corundum and silicon carbide. However, unlike these materials, zirconia also possess relatively high toughness, allowing them to resist crack propagation under high-stress conditions.
The wear mechanisms include abrasive wear, adhesive wear, and fatigue wear. Under abrasive wear conditions, zirconia materials’ high hardness enables them to effectively resist cutting and plowing actions from hard particles; under adhesive wear conditions, its chemical stability reduces chemical reactions and material transfer with counterpart materials.
Mining, cement, and ceramic processing industries have widely adopted zirconia to solve wear problems. For example, in ore crushing and grinding equipment, zirconia materials liners typically last 3-5 times longer than high-chromium cast iron. In cement plant conveying systems, zirconia materials-lined pipes can work in highly abrasive powder environments for 2-3 years, while traditional wear-resistant steel liners typically only last 6-8 months.
High-Wear Application | Traditional Material Lifespan | Zirconia Materials Lifespan | Performance Improvement |
---|---|---|---|
Ore Crusher Liners | 6-8 months | 2-3 years | 3-4× |
Cement Conveying Pipes | 8-10 months | 2.5-3 years | 3-4× |
Ceramic Extrusion Dies | 3-4 months | 1-1.5 years | 3-4× |
Compared to traditional wear-resistant materials, zirconia offers significant lifespan and cost-effectiveness advantages. While components often cost 30-50% more initially, considering extended service life and reduced downtime, zirconia typically results in 20-40% lower total ownership costs.
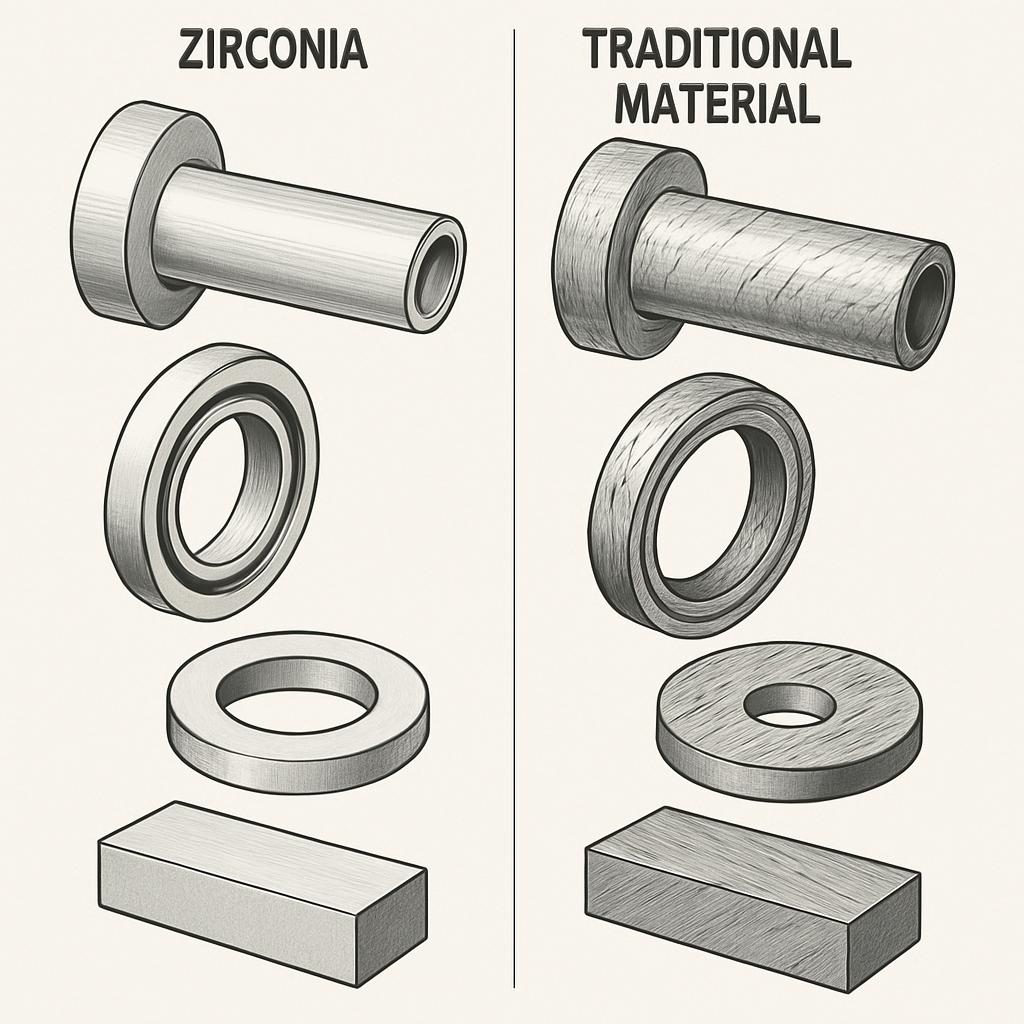
Wear-corrosion synergistic effect environments are among the most challenging operating conditions. In such environments, corrosion accelerates the wear process, while wear continuously exposes new surfaces to corrosion. Zirconia’ chemical stability and wear resistance combine to effectively address these compound extreme conditions.
What Economic Benefits Do Zirconia Materials Offer?
While zirconia materials require higher initial investment, from a long-term economic perspective, they often represent the best choice for extreme industrial environments.
Comparing initial investment with long-term total ownership cost is key to assessing economic viability. Components typically cost 30-100% more than traditional materials. However, when considering extended service life and reduced maintenance needs, zirconia generally saves 25-40% in total costs over 3-5 years.
Extended equipment life and reduced downtime offer significant economic value. In continuous production industries, each hour of downtime can result in thousands or even tens of thousands of dollars in losses. By extending maintenance intervals with zirconia components, businesses can significantly reduce unplanned downtime and improve production efficiency.
Cost Factor | Traditional Materials | Zirconia Materials | Difference |
---|---|---|---|
Initial Component Cost | Low | 30-100% higher | Higher initial investment |
Service Life | Short | 3-5× longer | More economical |
Maintenance Frequency | High | Low | More economical |
5-Year Total Ownership Cost | High | 25-40% lower | More economical |
Return on investment case studies across different industries further demonstrate zirconia’ economic value. In the petrochemical industry, one company invested $100,000 to replace critical valve components with zirconia materials parts and achieved approximately $350,000 in savings through reduced maintenance and downtime within two years, representing an ROI exceeding 250%.
With advances in production technology, zirconia costs have decreased by approximately 20-30% over the past decade. This trend is expected to continue, making zirconia solutions economically viable for more applications.
How Should You Select and Apply Zirconia Materials?
Selecting and applying zirconia materials requires a systematic approach and expertise to ensure optimal performance and economic benefits.
Application environment analysis is the first step. This includes identifying key parameters such as operating temperature range, temperature fluctuation frequency, chemical environment, mechanical load type, and wear mechanisms. For example, if the application involves frequent temperature fluctuations, magnesia-stabilized PSZ might be the best choice; if maximum mechanical strength is required, Y-TZP might be more suitable.
Component design must consider the material’s characteristics and limitations. As ceramic materials, zirconia materials have high hardness and rigidity but relatively low tensile strength and notch sensitivity. Therefore, designs should avoid sharp internal corners, thin-walled structures, and pure tensile loads. Best practices include using large radii, uniform wall thickness, and designs that primarily bear compressive loads.
Manufacturing process selection significantly impacts performance. Common forming methods include dry pressing and injection molding. Each method has advantages and limitations suitable for different geometries. Sintering conditions, such as temperature and time, also affect the final microstructure.
Quality control and performance verification are crucial for ensuring zirconia materials component reliability. Common testing methods include density measurement, hardness testing, flexural strength testing, X-ray diffraction analysis, and microstructure observation. For critical applications, small-scale field trials are recommended to evaluate zirconia materials performance in actual operating environments before full implementation.
FAQ Section
Q1: What is the typical service life of zirconia materials?
In extreme industrial environments, components typically last 3-5 times longer than traditional materials. For example, in high-temperature wear environments, zirconia materials valve seats can last 2-3 years, while metal valve seats typically only last 6-8 months. Specific lifespan depends on the severity of the application environment, component design, material grade, and quality control. In some special applications, such as high-purity chemical processing equipment, zirconia materials components can even last over 10 years without replacement.
Q2: What are the temperature limitations of zirconia materials?
Different types of zirconia materials have different temperature limitations. Partially Stabilized Zirconia (PSZ) can typically operate stably below 1000°C, while Fully Stabilized Zirconia (FSZ) can withstand temperatures up to 2200°C. However, long-term operating temperatures are typically recommended to be 200-300°C lower than maximum tolerance to ensure zirconia materials stability and extend service life. Under thermal cycling conditions, magnesia-stabilized PSZ zirconia materials exhibits the best thermal shock resistance and can withstand more frequent temperature fluctuations.
Q3: How do zirconia materials component costs compare to traditional materials?
Zirconia materials components typically cost 30-100% more initially than traditional metal or polymer materials, depending on complexity, size, and precision requirements. However, from a total cost of ownership (TCO) perspective, considering extended service life, reduced maintenance requirements, and downtime, zirconia materials solutions usually save 25-40% in total costs over a 3-5 year period. For example, after a petrochemical company replaced metal components with zirconia materials pump parts, although initial investment increased by 60%, the five-year total cost decreased by 32%.
Q4: In which extreme environments are zirconia materials not suitable?
Despite zirconia materials’ excellent performance in various extreme environments, they are not universal. These materials are unsuitable for: strong fluorination environments containing hydrofluoric acid (HF), as HF attacks zirconia materials to form soluble fluorides; high-temperature alkali metal environments (such as molten sodium), which cause materials degradation; certain reducing atmospheres at ultra-high temperatures (>1500°C) that may cause partial reduction of zirconia materials; and applications requiring high thermal conductivity, as zirconia materials are inherently thermal insulators.
Q5: How can you verify the quality and performance of zirconia materials components?
Methods for verifying zirconia materials component quality and performance include: material certificate review to confirm chemical composition, density, and mechanical properties meet specifications; non-destructive testing techniques such as ultrasonic testing, X-ray inspection, and microscopic observation to detect microcracks and internal defects; laboratory tests including hardness testing, flexural strength testing, and fracture toughness testing; small-scale field trials to evaluate performance in actual operating environments; and accelerated aging tests such as high-temperature aging, pressure cycling tests, and corrosion immersion tests.