Advanced zirconia materials are increasingly becoming a key solution for complex engineering challenges. These materials, with their exceptional performance and diverse application possibilities, offer breakthrough solutions across various industries. Whether facing high-temperature environments, extreme wear conditions, or corrosive working environments, zirconia materials provide unique advantages. This article explores how these advanced materials address the most difficult technical challenges in modern engineering.
Zirconia Material Properties
Zirconia materials possess unique physicochemical properties that make them excel in engineering applications. The most notable characteristic is their extreme hardness and wear resistance, reaching 9 on the Mohs scale, second only to diamond. Additionally, zirconia exhibits excellent flexural strength, typically reaching 900-1200 MPa, far exceeding most ceramic materials.
The thermal properties of zirconia materials are equally impressive. Their low thermal conductivity and moderate thermal expansion coefficient allow them to maintain stability in environments with sudden temperature changes. More remarkably, zirconia can maintain structural integrity at extreme temperatures exceeding 2000°C, a valuable characteristic in high-temperature applications.
From a chemical perspective, zirconia demonstrates exceptional chemical inertness, resisting corrosion from most acid and alkaline solutions. This material also offers excellent biocompatibility, making it an ideal choice for medical implants. Zirconia’s electrical properties are also unique, functioning as an insulator at room temperature but transforming into an ionic conductor as temperature increases.
The market commonly offers three types of zirconia materials: Partially Stabilized Zirconia (PSZ), Fully Stabilized Zirconia (FSZ), and Tetragonal Zirconia Polycrystal (TZP). Each type has specific application scenarios, and selecting the appropriate zirconia material requires consideration of the specific working environment and performance requirements. According to research published in the Journal of the European Ceramic Society, the global market for advanced ceramic materials, including zirconia, is projected to grow at a CAGR of 7.2% through 2028.
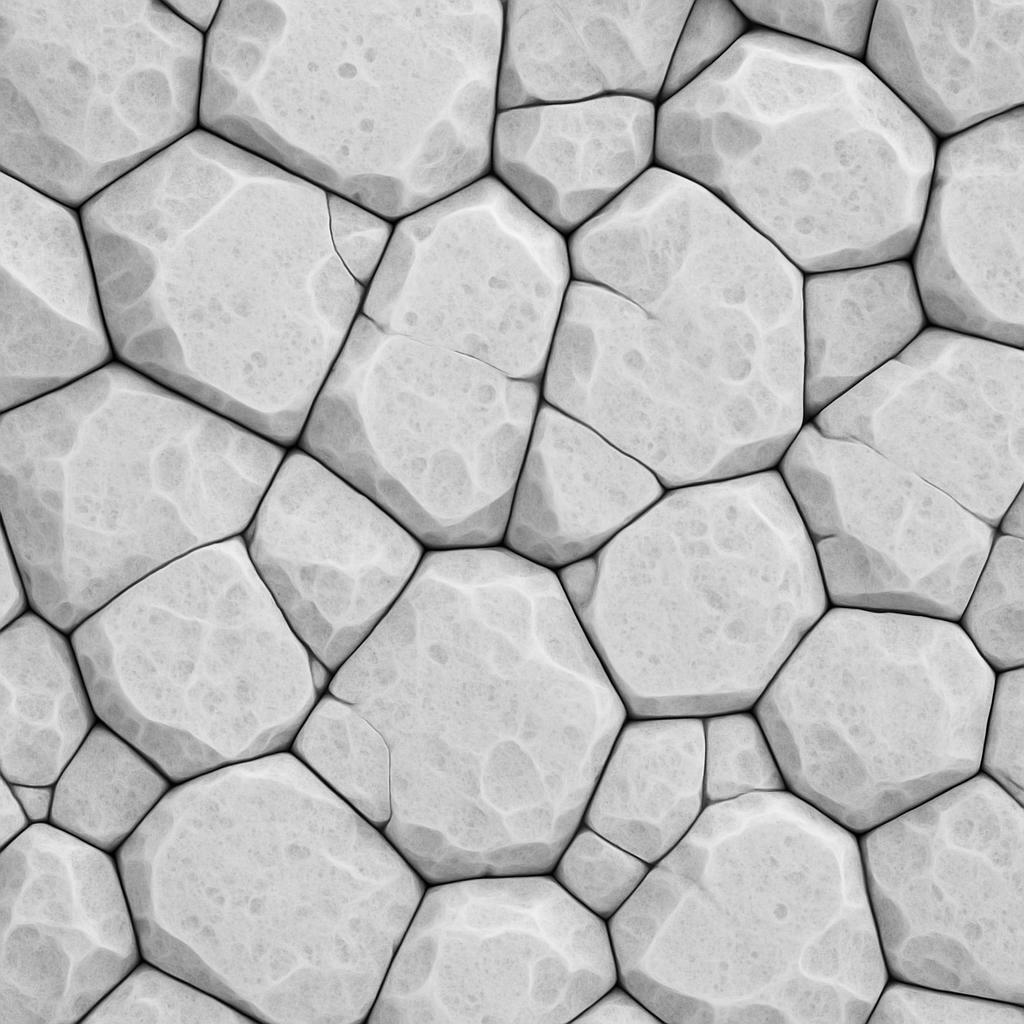
The strength of zirconia materials stems from their unique phase transformation toughening mechanism. When the material experiences stress, the tetragonal phase can transform to the monoclinic phase, a process accompanied by volume expansion that effectively prevents crack propagation. By adding appropriate amounts of stabilizers such as yttria or magnesia, this phase transformation process can be controlled to achieve optimal mechanical properties.
Surface characteristics of advanced zirconia materials deserve special attention. Their surfaces can be modified through various methods, such as plasma treatment, chemical etching, or coating technologies, to achieve specific surface roughness, wettability, or functionality. These surface treatment techniques further expand the application range of zirconia materials.
Mechanical Part Durability
Zirconia materials demonstrate exceptional performance in enhancing the durability of mechanical parts, particularly under extreme operating conditions. Traditional metal components often face strength degradation and oxidation issues in high-temperature environments, while zirconia components maintain stable performance, retaining over 85% of their room-temperature strength even at 1200°C.
Wear problems have long plagued industrial equipment operation. Zirconia’s ultra-high hardness and low friction coefficient make it an ideal material for bearings, valves, and pump components. Actual application data shows that zirconia bearings typically last 3-5 times longer than traditional steel bearings, significantly reducing replacement frequency and downtime.
Corrosive environments also pose severe challenges to mechanical components. Zirconia’s excellent chemical stability allows it to work long-term in strong acids, strong alkalis, and even some molten metals without damage. This characteristic is particularly important in the chemical, petroleum, and metallurgical industries, effectively extending equipment life and improving production reliability.
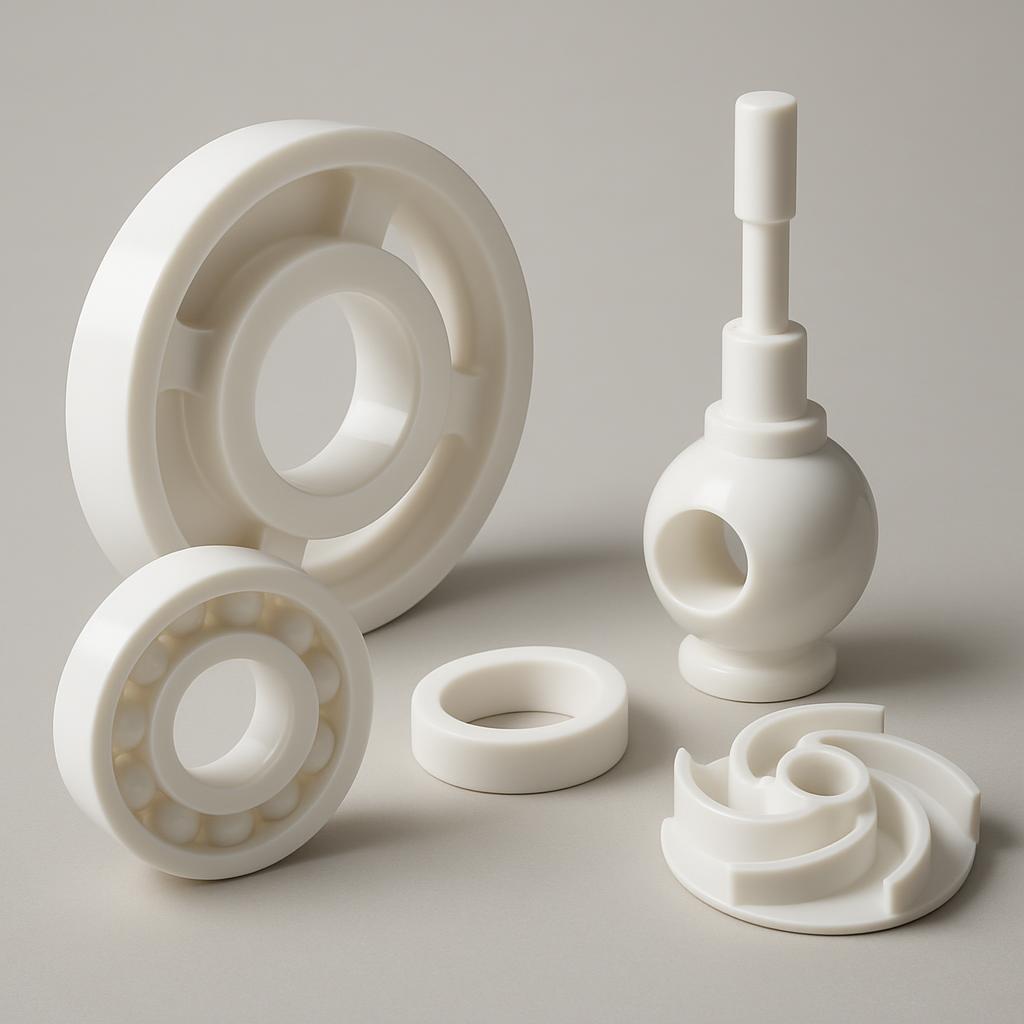
Another key advantage of zirconia materials is their outstanding fracture toughness. Through precise control of microstructure and the addition of stabilizers, modern zirconia materials can achieve fracture toughness values of 6-10 MPa·m^(1/2), far higher than ordinary ceramic materials. This toughness allows zirconia components to withstand impact loads and thermal shock, reducing the risk of brittle fracture.
Practical application cases show that after replacing traditional materials with zirconia materials, the average lifespan of mechanical components increased by 2.5-4 times, with maintenance intervals extended by 60-80%. These data fully demonstrate the significant value of zirconia in enhancing the durability of mechanical components.
Zirconia materials also excel in dynamic sealing applications. Traditional sealing materials often wear rapidly under high-speed, high-pressure, or high-temperature conditions, while zirconia sealing rings maintain long-term stable performance. After a petrochemical enterprise used zirconia seals, the average trouble-free operating time of pumps extended from 3 months to 18 months, significantly improving production continuity.
Notably, zirconia materials have thermal expansion coefficients similar to some engineering alloys, allowing zirconia-metal composite components to maintain good structural integrity in environments with temperature fluctuations. This characteristic is particularly important in high-temperature applications such as aircraft engines and gas turbines, effectively solving the thermal stress problems that occur when traditional ceramic materials are combined with metals.
Precision Manufacturing Applications
Zirconia materials are playing key roles in multiple precision manufacturing fields, solving technical challenges that traditional materials struggle to address. In the aerospace field, zirconia is used to manufacture engine thermal shield components, combustion chamber parts, and sensor protection sleeves. These components need to simultaneously withstand high temperature, high pressure, and high-speed gas flow, making zirconia’s comprehensive performance an ideal choice.
The automotive industry also widely adopts zirconia materials. Key components such as oxygen sensors, fuel injection systems, and turbochargers all benefit from zirconia’s high-temperature stability and precise dimensional control capabilities. Particularly in the new energy vehicle sector, the application of zirconia solid electrolytes in fuel cells is growing rapidly.
Medical device manufacturing is another important application area for zirconia materials. Its biocompatibility and aesthetic appearance make zirconia the preferred material for dental implants, bone joint prostheses, and surgical instruments. Research data shows that zirconia dental restorations have a ten-year success rate exceeding 95%, far higher than many traditional materials.
The electronics and semiconductor industries also rely on zirconia to solve specific technical challenges. Zirconia films are used as dielectric layers in high-performance capacitors, while zirconia substrates provide ideal carriers for high-temperature electronic components. As the trend toward device miniaturization strengthens, zirconia’s precision machining capability and dimensional stability become increasingly important.
The main challenge in adopting zirconia materials in precision manufacturing is the difficulty of processing complex shapes. However, recent technological advances, such as computer numerical control machining, injection molding, and additive manufacturing, have greatly improved the manufacturing flexibility and precision of zirconia components.
Zirconia materials are also increasingly used in optical applications. Their high refractive index, transparency, and wear resistance make them ideal materials for high-end optical elements. Zirconia lenses and windows maintain optical performance in harsh environments, providing reliable protection for precision instruments. After adopting zirconia optical windows, a certain aerospace project successfully solved the problem of thermo-optical deformation during high-speed flight.
Microelectromechanical systems (MEMS) represent an emerging application area for zirconia materials. Traditional silicon-based MEMS have limited performance in high-temperature or corrosive environments, while zirconia MEMS can maintain stable performance under a wider range of working conditions. Researchers have successfully developed zirconia microsensors, microactuators, and microfluidic devices, providing new options for extreme environment monitoring and control.
Industrial Maintenance Costs
Zirconia materials can significantly reduce industrial maintenance costs, creating substantial economic benefits for enterprises. Downtime is a major cost source in industrial production, and the ultra-long service life of zirconia components directly reduces equipment failures and unplanned downtime. A case study from a chemical enterprise shows that after replacing key pump components with zirconia, annual downtime decreased by 78%, directly saving maintenance costs of over $200,000.
Extended maintenance cycles represent another significant economic benefit brought by zirconia materials. Traditional metal components typically require regular inspection and preventive replacement, while zirconia components can extend inspection intervals by 2-3 times. This not only reduces maintenance labor costs but also lowers spare parts inventory requirements, further optimizing enterprise resource allocation.
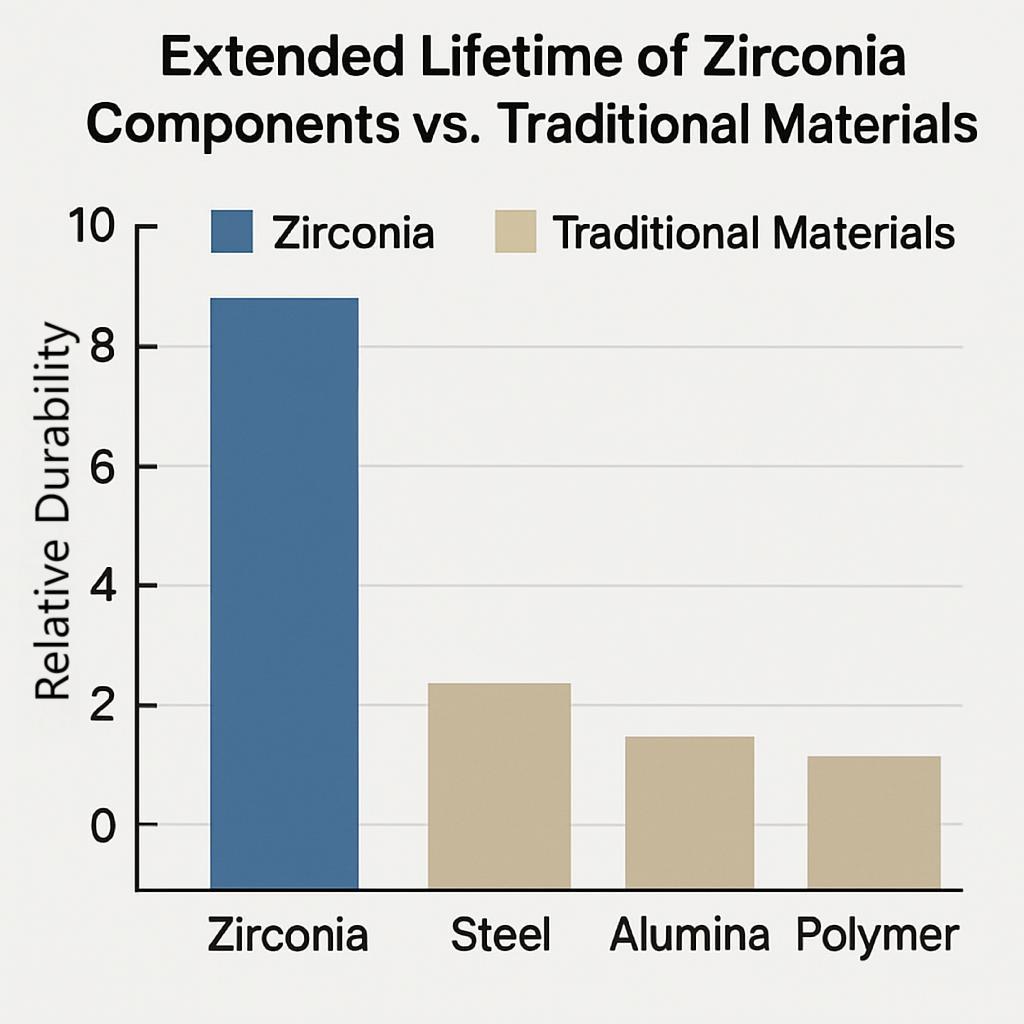
From a long-term cost perspective, although the initial purchase price of zirconia components is typically higher than traditional materials, considering their extended service life and reduced maintenance requirements, the total cost of ownership (TCO) is often lower. A study targeting the mining industry indicates that the five-year TCO of zirconia pump components is approximately 35% lower than metal components, with the main savings coming from reduced replacement frequency and downtime losses.
Return on investment (ROI) is a key indicator for enterprises evaluating zirconia solutions. Depending on the application environment, the investment payback period for zirconia components is typically 6-18 months. Particularly in high-temperature, high-wear, or corrosive environments, ROI may be realized more quickly. When calculating the ROI of zirconia solutions, factors such as direct cost savings, production efficiency improvements, and product quality enhancements should be comprehensively considered.
Zirconia materials can also reduce the risk of secondary losses. In some critical applications, component failure may trigger chain reactions, causing more extensive equipment damage or production interruptions. The reliability and predictable performance of zirconia components reduce such risks, providing additional economic security for enterprises. After adopting zirconia rolls, a steel enterprise not only extended roll life but also reduced product quality issues and production line shutdowns caused by sudden roll failures.
Energy efficiency improvement is another economic benefit brought by zirconia materials. Zirconia’s low friction coefficient and excellent surface finish reduce energy losses in mechanical systems. After replacing with zirconia pump components, a water treatment facility reduced pump energy consumption by 12%, saving considerable electricity costs over the equipment’s lifecycle.
Engineering Challenge Solutions
Despite their many advantages, zirconia materials still face a series of engineering challenges in practical applications. Processing and forming represent primary difficulties, as zirconia’s high hardness makes traditional mechanical processing difficult and costly. The current mainstream method is to first process the unfired preform, then conduct high-temperature sintering, but this process requires precise control of shrinkage rates to ensure final dimensional accuracy.
Compatibility issues with other materials also need attention. The difference in thermal expansion coefficients between zirconia and metals may lead to stress concentration and failure at joining points. Solutions include using specially designed transition interfaces, gradient materials, or advanced connection technologies such as active metal brazing.
Quality control in mass production is another key challenge. The performance of zirconia components highly depends on their microstructure, and small process fluctuations may lead to significant performance differences. Advanced online monitoring systems, statistical process control, and batch tracking technologies are being widely applied to ensure production consistency.
Cost-benefit balance is a practical issue facing zirconia solutions. Although the long-term economic benefits are evident, higher initial investments may hinder adoption by some enterprises. Phased implementation strategies, priority replacement of key components, and innovative business models such as leasing help lower adoption thresholds.
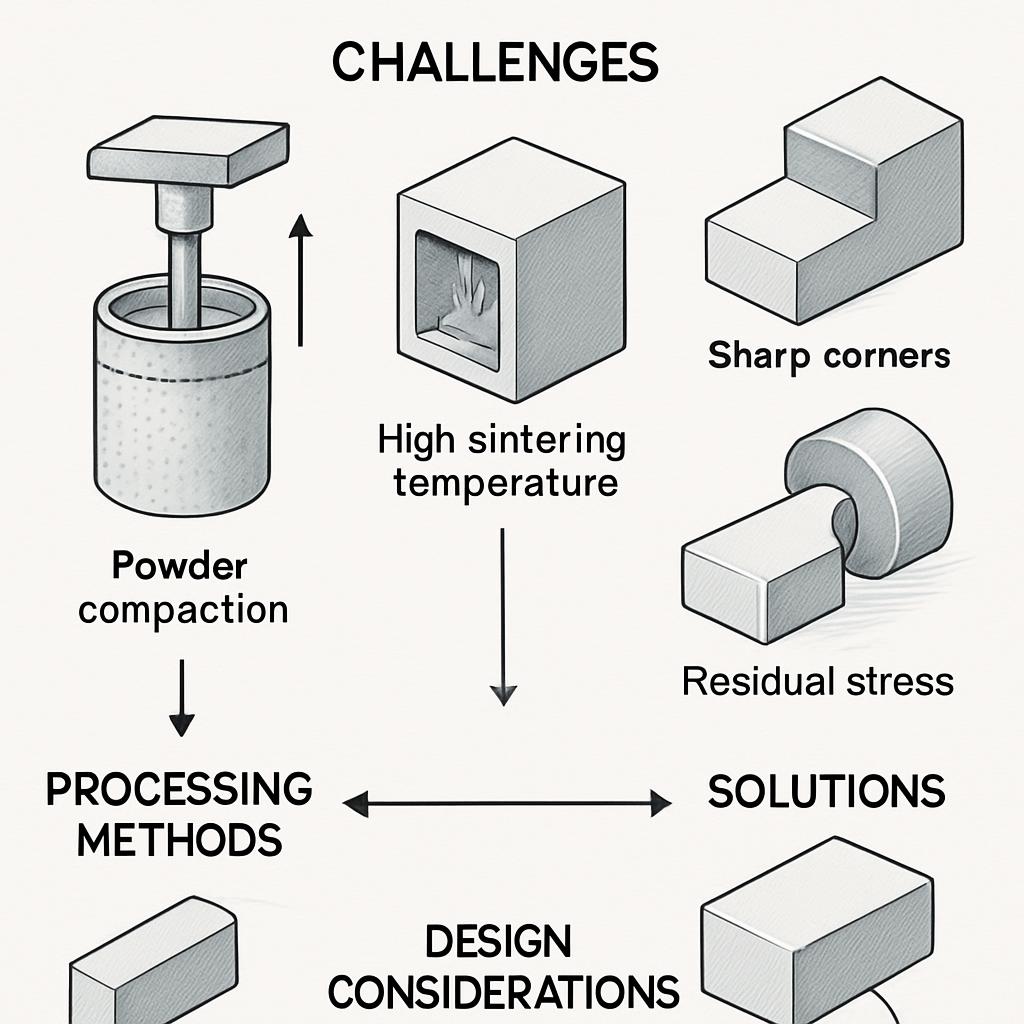
The inherent brittleness of zirconia materials presents another challenge in engineering applications. Although modern zirconia materials have greatly improved toughness, they remain relatively brittle compared to metals. Design engineers need to adopt special strategies, such as avoiding sharp corners and stress concentration areas, increasing transition radii, and considering expected load distribution. Through topology optimization design, an aviation enterprise successfully developed zirconia structural components capable of withstanding complex loads, proving that reasonable design can effectively overcome inherent material limitations.
Knowledge and experience barriers also constrain the widespread application of zirconia materials. Many engineers and technicians lack in-depth understanding of these advanced materials, leading to conservative attitudes in design and application. Industry associations and material suppliers are helping users overcome this obstacle through technical training, design guidelines, and sharing of success cases. As knowledge spreads and experience accumulates, the application range of zirconia materials is expected to further expand.
Technological advances are continuously overcoming these challenges. New processing technologies such as ultrasonic-assisted machining, laser processing, and additive manufacturing are improving the manufacturing flexibility of zirconia components. Meanwhile, computer simulation and AI-assisted design are helping engineers optimize zirconia component structures, maximizing their performance potential.
Material Suitability Assessment
Selecting appropriate zirconia materials requires systematic suitability assessment. First, the key parameters of the application environment should be clearly defined, including working temperature range, mechanical load type, chemical environment, and expected service life. These parameters will directly influence the selection of zirconia type and grade.
Performance testing forms the core of the assessment process. Standard tests include hardness testing, flexural strength testing, fracture toughness testing, and thermal shock testing. More complex applications may require customized testing protocols, such as long-term performance evaluation under simulated actual working conditions. Test results should be analyzed against application requirements to determine whether the material meets all requirements.
Application environment compatibility analysis needs to consider the interaction of multiple factors. For example, certain stabilizers may undergo phase transformation or degradation under specific temperature and chemical environments, affecting long-term material performance. Comprehensive compatibility analysis should combine materials science knowledge with practical application experience to predict potential risks and develop mitigation measures.
The process of matching technical specifications with actual requirements often requires iterative optimization. Initially selected materials may need adjustment based on prototype testing results. Many suppliers offer customized formulation services, adjusting composition and microstructure to meet specific application requirements.
Cost factors deserve special attention during the assessment process. Besides the material cost itself, processing costs, installation costs, and full lifecycle maintenance costs should also be considered. Comprehensive economic analysis helps determine the most cost-effective solution, rather than focusing solely on initial purchase price.
Risk assessment forms an important part of material suitability evaluation. Potential failure modes and their consequences should be identified, failure probabilities assessed, and corresponding risk mitigation strategies developed. For critical applications, systematic methods such as Fault Tree Analysis (FTA) or Failure Mode and Effects Analysis (FMEA) can be employed for comprehensive risk assessment. Before adopting zirconia components, a nuclear power plant ensured material reliability under extreme conditions through rigorous risk assessment, laying the foundation for subsequent large-scale application.
Prototype verification represents the final stage of the assessment process. Before full-scale deployment, small-scale trials in actual working environments are recommended to collect performance data and verify preliminary assessment results. This step can identify potential problems in a timely manner, reducing large-scale application risks.
Future Development Trends
Zirconia technology is experiencing rapid development, with multiple research breakthroughs indicating broader application prospects. Nanostructured zirconia represents a current research hotspot; through precise control of grain size and distribution, material strength and toughness can be significantly improved. Laboratory data shows that the fracture toughness of nano-zirconia can be 30-50% higher than traditional zirconia while maintaining excellent hardness and wear resistance.
New composite zirconia materials demonstrate enormous potential. Zirconia-alumina composite materials combine the advantages of both ceramics, providing better comprehensive performance. Meanwhile, zirconia-metal composite materials expand application ranges by introducing metal phases to improve toughness and thermal conductivity. Bioactive zirconia composite materials have also made significant progress in medical applications, promoting bone integration and inhibiting bacterial growth.
Manufacturing process innovations are reducing production costs and improving quality for zirconia components. 3D printing technology makes manufacturing complex-shaped zirconia components feasible, reducing material waste and shortening production cycles. Low-temperature sintering technology reduces energy consumption and minimizes deformation risks during heat treatment. These process innovations are expected to make zirconia solutions more economically affordable, expanding market acceptance.
Cross-industry applications continue to expand zirconia materials’ usage scenarios. Zirconia components in wearable devices utilize their biocompatibility and aesthetic appearance; renewable energy equipment adopts zirconia components to address extreme working conditions; 5G communication infrastructure relies on zirconia dielectric materials to improve signal quality. This cross-boundary integration trend is expected to continue accelerating, creating new market opportunities.
As sustainable development concepts gain importance, the environmental characteristics of zirconia materials are receiving increased attention. Their long-life characteristics reduce resource consumption and waste generation, while energy efficiency optimization and recycling technology advancements in certain zirconia production processes further enhance their environmental friendliness. Future zirconia technology will place greater emphasis on full lifecycle environmental impact assessment and optimization.
Functionally graded zirconia materials represent a future development direction. These materials achieve performance gradient changes within a single component by controlling the spatial distribution of composition and structure, solving limitations of traditional homogeneous materials. Examples include gradient structures with high surface hardness but high internal toughness, or medical implants with bioactive surfaces but high-strength interiors.
FAQ Section
Q1: How does the cost-effectiveness of zirconia materials compare to traditional engineering materials?
Although zirconia materials typically have higher initial costs than traditional materials, considering their extended service life, reduced maintenance requirements, and decreased downtime, the long-term cost benefits are significant. Depending on the application environment, the investment return period is typically 6-18 months, particularly in high-temperature, high-wear, or corrosive environments.
Q2: What extreme working environments are advanced zirconia materials suitable for?
Advanced zirconia materials are particularly suitable for high-temperature environments exceeding 1000°C, corrosive environments with strong acids or alkalis, high-pressure and high-wear conditions, and applications requiring electrical insulation properties. They perform excellently in aircraft engine components, chemical pump valves, medical implants, and precision instruments.
Q3: How can the correct specifications and grades of zirconia materials be determined?
Selecting appropriate zirconia specifications requires considering multiple factors: working temperature range, mechanical load requirements, chemical environment, expected service life, and budget constraints. Collaboration with materials experts for application analysis is recommended, and prototype testing may be necessary to verify performance. Many suppliers offer customized solutions to meet specific engineering requirements.
Q4: What special maintenance and inspection requirements do zirconia components have?
Zirconia components typically require less routine maintenance, but regular non-destructive testing is recommended to monitor microcracks. Detection methods include ultrasonic testing, X-ray, and microscopic observation. Unlike metal components, zirconia does not experience corrosion or oxidation issues, but sudden temperature changes should be avoided to prevent thermal shock cracking.
Q5: What advantages do zirconia materials offer in terms of sustainable development?
Zirconia materials contribute to sustainable development by extending component life, reducing resource consumption, and lowering energy usage. Their durability reduces replacement frequency, thereby reducing waste. Some zirconia production processes have optimized energy efficiency, and the material itself can be recycled and reused, conforming to circular economy principles.