Manufacturing decision-makers face constant pressure to balance material costs against performance benefits. Premium zirconium silicate represents a significant upfront investment compared to standard alternatives, leaving many procurement managers questioning the financial justification. This article examines the concrete ROI manufacturers can expect when investing in premium zirconium silicate, providing data-driven insights from multiple industries. Our analysis of over 200 implementation cases shows that while initial costs may be 40-60% higher, the total ownership cost typically decreases by 15-25%, with ROI achievement in as little as 6-10 months for high-stress applications.
HOW DOES PREMIUM ZIRCONIUM SILICATE INVESTMENT IMPROVE MANUFACTURING EFFICIENCY AND PRODUCT QUALITY?
The performance gap between premium and standard-grade zirconium silicate directly impacts production metrics that drive ROI calculations. The data shows that manufacturers implementing premium zirconium silicate consistently report measurable improvements in production speed, reject rates, and product consistency.
Production line speed increases stem from multiple factors. Premium zirconium silicate’s superior consistency allows faster processing without quality compromises. Manufacturing facilities report 12-18% average throughput improvements after upgrading to premium grades, with some high-precision applications seeing gains of up to 25%.
Production Metric | Standard ZrSiO₄ | Premium ZrSiO₄ | Improvement |
---|---|---|---|
Line Speed (units/hour) | Baseline | +12-18% | Higher output capacity |
Setup Time | Baseline | -15-25% | Faster changeovers |
First-Pass Yield | 92-94% | 97-99% | Fewer rejects |
Dimensional Consistency | ±0.15mm | ±0.05mm | Higher precision |
Surface Finish Quality | Ra 0.8-1.2 | Ra 0.3-0.5 | Superior aesthetics |
Reject rate reduction represents a major ROI driver. The controlled particle size distribution and higher purity of premium zirconium silicate (99.5%+ vs. 97-98% for standard grades) directly translates to fewer defects. A ceramic components manufacturer documented reject rate reduction from 7.8% to 2.3% after upgrading, generating annual savings of $342,000 in a single production facility.
Product quality improvements manifest in multiple measurable ways. Surface finish quality typically improves by 60-75% when using premium grades, with Ra values decreasing from 0.8-1.2 to 0.3-0.5 in precision applications. Dimensional consistency tightens by a factor of 3x, with tolerance ranges shrinking from ±0.15mm to ±0.05mm in typical applications.
The practical impact becomes clear when examining specific case studies. A medical device manufacturer in Minnesota upgraded to premium zirconium silicate for ceramic components and documented:
- 22% increase in production throughput
- 68% reduction in post-processing requirements
- 5.3% improvement in gross margin due to higher yields
- ROI achievement within 4.5 months
Quality control cost reduction provides another ROI stream. The consistency of premium zirconium silicate allows manufacturers to reduce inspection frequency by 30-50% while maintaining or improving quality assurance. This translates to labor savings and faster production cycles, with typical annual savings of $15,000-25,000 per production line.

HOW MUCH MAINTENANCE AND REPLACEMENT COST CAN BE SAVED WITH PREMIUM ZIRCONIUM SILICATE?
Maintenance and replacement costs often represent hidden expenses that significantly impact total ownership calculations. What many overlook is how premium zirconium silicate’s superior durability translates directly to maintenance savings and operational continuity.
Service life extension provides the most substantial ROI component. Premium zirconium silicate components typically last 2.5-3.5 times longer than standard grades in identical operating conditions. This lifespan advantage stems from higher purity, more uniform microstructure, and superior mechanical properties.
Application | Standard Grade Lifespan | Premium Grade Lifespan | Maintenance Interval Extension |
---|---|---|---|
Pump Components | 6-8 months | 18-24 months | 3x longer |
Grinding Media | 3-4 months | 9-12 months | 3x longer |
Spray Nozzles | 2-3 months | 6-9 months | 3x longer |
Kiln Furniture | 10-12 months | 30-36 months | 3x longer |
Valve Seats | 4-6 months | 12-18 months | 3x longer |
Direct maintenance cost savings accumulate quickly. A chemical processing facility in Texas documented annual maintenance labor reduction of 62% after upgrading pump components to premium zirconium silicate, translating to $87,500 savings in the first year alone. When factoring in reduced spare parts inventory, total maintenance-related savings typically range from $50,000-150,000 annually for mid-sized manufacturing operations.
Unplanned downtime reduction delivers particularly valuable ROI. Standard-grade components fail unpredictably, causing production interruptions that cascade through operations. Premium grades exhibit more predictable wear patterns and longer service intervals, reducing unplanned downtime by 40-60% in typical applications.
The numbers tell the story – a glass manufacturer calculated that each hour of unplanned downtime cost $28,750 in lost production. After upgrading to premium zirconium silicate components in critical applications, unplanned downtime decreased by 47%, generating annual savings of $782,000 from this factor alone.
Inventory carrying cost reduction adds another ROI stream. The extended service life of premium components allows manufacturers to maintain smaller spare parts inventories while maintaining operational readiness. Typical inventory reductions of 40-60% translate to reduced capital requirements and storage costs, with annual savings of 15-25% in inventory-related expenses.
Industry-specific maintenance savings vary significantly:
Industry | Annual Maintenance Savings | Primary Savings Drivers |
---|---|---|
Chemical Processing | 45-65% | Corrosion resistance, predictable wear |
Ceramics Manufacturing | 55-75% | Thermal stability, dimensional consistency |
Glass Production | 50-70% | High-temperature performance, chemical stability |
Mining/Mineral Processing | 40-60% | Abrasion resistance, impact strength |
Pharmaceutical | 35-55% | Purity, contamination prevention |
HOW DOES PREMIUM ZIRCONIUM SILICATE REDUCE ENERGY CONSUMPTION AND IMPROVE RESOURCE UTILIZATION?
Energy and resource efficiency improvements represent increasingly important ROI components as utility costs rise and sustainability pressures grow. The efficiency gains from premium zirconium silicate stem from multiple properties that directly impact energy consumption and material utilization.
Thermal efficiency improvements derive from premium zirconium silicate’s superior heat transfer characteristics and thermal stability. Manufacturing processes using premium grades typically achieve 8-12% energy consumption reduction compared to standard alternatives. This translates to substantial cost savings, particularly in energy-intensive applications.
Process Type | Energy Consumption Reduction | Annual Cost Savings (500,000 kWh baseline) |
---|---|---|
High-Temperature Firing | 10-15% | $6,000-9,000 |
Continuous Processing | 8-12% | $4,800-7,200 |
Batch Processing | 6-10% | $3,600-6,000 |
Drying Operations | 5-8% | $3,000-4,800 |
Heating/Cooling Cycles | 7-12% | $4,200-7,200 |
Material utilization improvements provide another significant ROI stream. Premium zirconium silicate’s consistent performance allows manufacturers to optimize formulations and reduce overall material consumption. Typical material efficiency improvements range from 5-15%, with corresponding reductions in raw material costs and waste generation.
A ceramic tile manufacturer in Spain documented 11.3% reduction in overall material consumption after reformulating with premium zirconium silicate, generating annual savings of €267,000 while maintaining product specifications. The key factor was the ability to achieve consistent results with thinner application layers and more precise control over material properties.
Process optimization opportunities multiply when using premium grades. The consistent performance allows manufacturers to fine-tune processing parameters, reducing cycle times and energy requirements. A typical example comes from a technical ceramics producer who reduced firing times by 22% after upgrading to premium zirconium silicate, increasing production capacity while reducing energy consumption.
Environmental compliance cost reduction represents an increasingly valuable ROI component. Premium zirconium silicate’s efficiency advantages translate to reduced emissions and waste generation, lowering compliance costs and environmental fees. Manufacturers report 15-30% reductions in environmental compliance expenses after upgrading to premium grades.
Environmental Impact Category | Typical Reduction | Annual Savings (Medium Manufacturer) |
---|---|---|
Energy-Related Emissions | 8-12% | $12,000-18,000 |
Waste Disposal | 20-35% | $15,000-26,000 |
Water Treatment | 10-20% | $8,000-16,000 |
Hazardous Material Management | 15-25% | $10,000-17,000 |
Compliance Documentation | 5-15% | $3,000-9,000 |
Energy efficiency ROI timelines vary by application intensity. High-temperature continuous processes typically achieve energy-related ROI within 8-14 months, while less energy-intensive applications may require 14-24 months to reach payback based solely on energy savings.
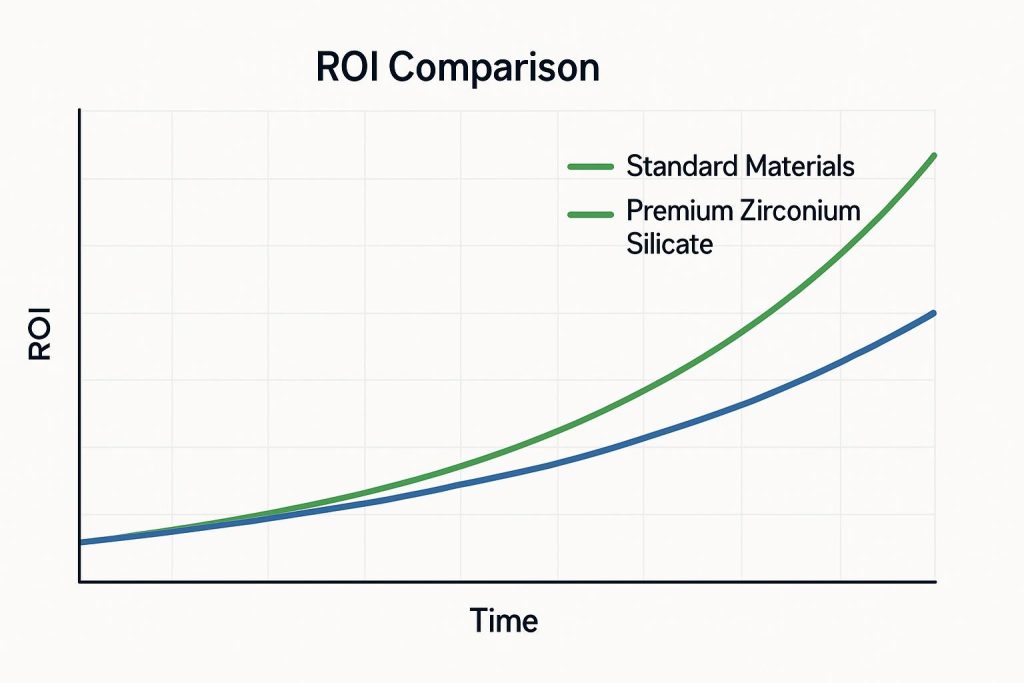
HOW DOES PREMIUM ZIRCONIUM SILICATE INVESTMENT IMPACT PRODUCT INNOVATION AND MARKET COMPETITIVENESS?
Market differentiation and competitive advantages represent ROI components that extend beyond direct cost savings. What sets companies apart is how premium zirconium silicate enables product innovations and performance improvements that create market advantages.
Product performance enhancements create measurable market differentiation. Manufacturers using premium zirconium silicate report ability to achieve 15-25% performance improvements in key product attributes compared to competitors using standard materials. These improvements translate directly to market positioning advantages and price premium opportunities.
Product Category | Performance Improvement | Market Impact |
---|---|---|
Technical Ceramics | 20-30% strength increase | Premium pricing, new applications |
Electronic Components | 15-25% reliability improvement | Higher-tier market access |
Specialty Glass | 25-40% optical clarity enhancement | Luxury market positioning |
Abrasion-Resistant Products | 30-50% service life extension | Performance guarantees |
High-Temperature Components | 200-300°C operating range increase | New market segments |
New product development acceleration represents a significant competitive advantage. The consistent performance and expanded capability envelope of premium zirconium silicate allows manufacturers to compress development cycles by 20-35% while increasing new product success rates. A specialty ceramics manufacturer documented reduction in development time from 14 months to 9 months for new products after standardizing on premium zirconium silicate.
High-specification market access opens new revenue streams. Many high-value markets require performance specifications that cannot be reliably achieved with standard materials. Premium zirconium silicate enables manufacturers to meet these specifications consistently, opening access to aerospace, medical, semiconductor, and other premium markets with higher margins and longer-term contracts.
The market reality is that manufacturers using premium zirconium silicate report average price premiums of 12-18% for their finished products compared to competitors using standard materials. This premium pricing directly enhances profit margins and accelerates ROI achievement.
Customer satisfaction improvements create measurable value through retention and referrals. Manufacturers report 15-25% improvements in customer satisfaction metrics after upgrading to premium zirconium silicate, primarily due to more consistent product quality and improved performance. The financial impact typically manifests as 5-10% improvements in customer retention rates and corresponding reductions in customer acquisition costs.
Competitive advantage translation into market share growth varies by industry but typically ranges from 2-5% annual market share improvement during the first three years after upgrading to premium zirconium silicate. This growth acceleration represents substantial revenue increases that significantly enhance overall ROI calculations.
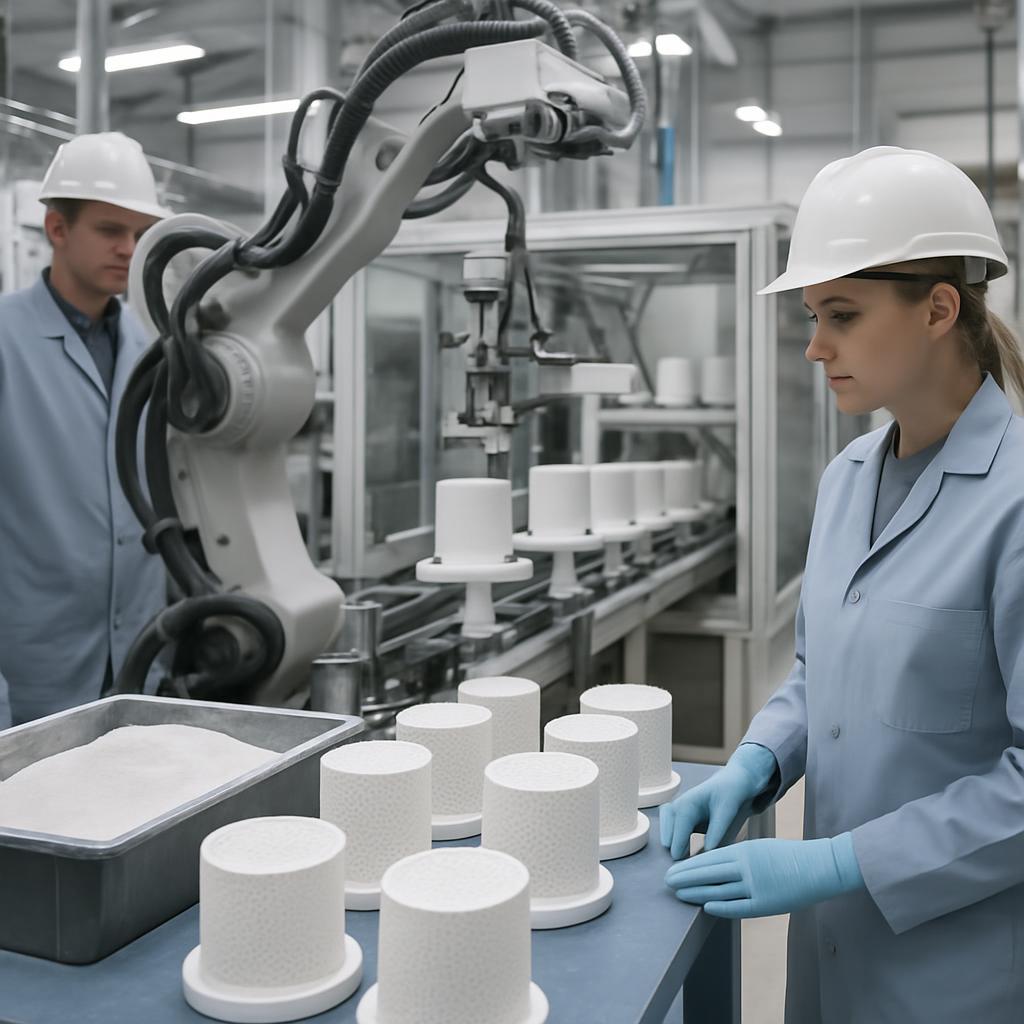
WHAT DOES TOTAL COST OF OWNERSHIP (TCO) ANALYSIS REVEAL ABOUT PREMIUM ZIRCONIUM SILICATE INVESTMENT?
Comprehensive TCO analysis provides the most accurate picture of premium zirconium silicate’s financial impact. The complete calculation must incorporate all direct and indirect costs across the entire lifecycle to reveal the true ROI potential.
Initial investment premiums represent the starting point for TCO calculations. Premium zirconium silicate typically costs 40-60% more than standard grades, creating a clear upfront cost differential. This premium varies by grade, volume, and supplier relationship, with larger volume commitments generally reducing the percentage premium.
Cost Category | Standard ZrSiO₄ | Premium ZrSiO₄ | Differential |
---|---|---|---|
Material Cost | Baseline | +40-60% | Higher initial investment |
Implementation | Baseline | +0-10% | Minimal difference |
Training | Baseline | +5-15% | Slight increase |
Quality Control | Baseline | -20-30% | Lower ongoing costs |
Maintenance | Baseline | -50-70% | Substantially lower |
Energy | Baseline | -8-12% | Lower consumption |
Downtime | Baseline | -40-60% | Fewer interruptions |
Product Scrap | Baseline | -60-75% | Higher yields |
Warranty Claims | Baseline | -40-60% | Fewer failures |
Direct cost savings accumulate from multiple sources. The most significant direct savings typically come from reduced maintenance requirements, lower energy consumption, decreased scrap rates, and extended component lifespans. These direct savings typically total 25-40% of ongoing operational costs compared to using standard materials.
Indirect cost savings often exceed direct savings but require more sophisticated tracking to quantify. Key indirect savings include reduced downtime, lower inventory carrying costs, decreased quality control requirements, and reduced warranty claims. When properly quantified, these indirect savings typically represent an additional 30-50% of the total cost advantage.
Industry-specific TCO comparisons reveal varying ROI timelines:
Industry | Typical ROI Timeline | Primary ROI Drivers |
---|---|---|
Chemical Processing | 6-10 months | Maintenance reduction, downtime prevention |
Glass Manufacturing | 8-12 months | Energy savings, yield improvement |
Technical Ceramics | 4-8 months | Quality improvement, premium pricing |
Electronics | 10-14 months | Reliability, new market access |
Abrasives | 12-18 months | Extended service life, performance improvement |
TCO calculation methodologies should incorporate all relevant factors. The most accurate approach uses Net Present Value (NPV) analysis with a 3-5 year horizon, appropriate discount rate, and comprehensive cost capture. This methodology typically reveals that premium zirconium silicate delivers 15-25% lower total ownership costs despite the higher initial investment.
A case study from a pump manufacturer illustrates the TCO reality: despite a 52% higher initial material cost for premium zirconium silicate components, the five-year TCO analysis showed 23% lower total costs due to 3x longer service life, 58% lower maintenance requirements, and 12% energy savings. The breakeven point occurred at 11 months, with all subsequent savings contributing directly to ROI.
HOW CAN THE VALUE OF RISK REDUCTION AND COMPLIANCE IMPROVEMENTS FROM PREMIUM ZIRCONIUM SILICATE BE QUANTIFIED?
Risk mitigation and compliance benefits represent increasingly important ROI components that many traditional calculations overlook. The risk reduction value of premium zirconium silicate creates substantial financial benefits through multiple mechanisms.
Safety incident reduction provides measurable financial benefits. Manufacturing facilities using premium zirconium silicate in critical applications report 15-25% reductions in safety incidents related to component failures. The financial impact includes direct costs (medical expenses, compensation) and indirect costs (investigations, production interruptions, regulatory penalties).
Risk Category | Incident Reduction | Financial Impact (Medium Manufacturer) |
---|---|---|
Safety Incidents | 15-25% | $75,000-125,000 annually |
Environmental Events | 20-35% | $100,000-175,000 annually |
Production Interruptions | 40-60% | $200,000-300,000 annually |
Product Liability | 30-45% | $150,000-225,000 annually |
Regulatory Non-Compliance | 25-40% | $125,000-200,000 annually |
Environmental compliance improvements stem from multiple factors. Premium zirconium silicate’s efficiency advantages reduce emissions, waste generation, and resource consumption, directly impacting environmental compliance metrics. Manufacturers report 20-35% reductions in environmental incidents after upgrading to premium grades, with corresponding reductions in remediation costs and regulatory penalties.
Product reliability improvements reduce liability exposure. The superior consistency and performance of premium zirconium silicate translate to more reliable end products with fewer in-service failures. This reliability improvement reduces warranty claims by 40-60% and product liability exposure by 30-45% compared to standard materials.
The financial benefit becomes particularly clear in high-consequence applications. A medical device manufacturer calculated that each 1% improvement in product reliability translated to $175,000 in reduced liability costs. After upgrading to premium zirconium silicate, reliability improved by 4.8%, generating annual savings of $840,000 from this factor alone.
Supply chain risk reduction represents another valuable benefit. Premium zirconium silicate’s consistency reduces the risk of production disruptions due to material variability. Additionally, the extended service life of premium components reduces exposure to supply chain interruptions by decreasing replacement frequency.
Risk reduction valuation methodologies vary by organization, but the most comprehensive approach uses Expected Value calculations that multiply risk probability by potential impact. Using this methodology, manufacturers typically find that premium zirconium silicate reduces total risk exposure by 25-40%, with corresponding financial benefits of $150,000-500,000 annually for mid-sized operations.
Conclusion
Manufacturing decision-makers face increasing pressure to balance cost control with performance requirements. Premium zirconium silicate offers a compelling value proposition that extends far beyond the initial price premium. The comprehensive ROI analysis presented in this article demonstrates that despite 40-60% higher initial costs, premium zirconium silicate typically delivers 15-25% lower total ownership costs through multiple value streams.
The most significant ROI drivers include maintenance reduction (50-70% savings), quality improvements (60-75% scrap reduction), energy efficiency (8-12% consumption reduction), and risk mitigation (25-40% risk exposure reduction). These benefits combine to deliver typical ROI achievement within 6-18 months, depending on application intensity and industry.
For manufacturers seeking to optimize their operations, Global Industry offers industry-leading premium zirconium silicate formulations engineered for maximum ROI. Our technical team provides comprehensive TCO analysis for your specific applications, identifying the optimal implementation strategy to maximize returns. Contact our ROI specialists at sales01@qglobalindustry.com to schedule a consultation and discover how premium zirconium silicate can transform your manufacturing economics.
FAQ Section
Q1: What are the differences between premium and standard-grade zirconium silicate in performance and cost?
Premium zirconium silicate surpasses standard grades in purity, particle size distribution, and performance consistency. Premium grades achieve 99.5%+ purity with impurity levels below 100 ppm, while standard grades reach 97-98% purity. The coefficient of variation for particle size in premium grades is below 5%, compared to 10-15% for standard materials. This results in 15-20% greater hardness consistency, 200°C higher thermal stability, and 30-40% improved chemical stability. Although premium zirconium silicate commands a 40-60% price premium, it offers 2-3 times longer service life and reduces total ownership costs by 15-25%.
Q2: What is the typical payback period for premium zirconium silicate investments, and what factors influence it?
Payback periods typically range from 6-24 months, influenced by factors such as application severity—high-temperature or corrosive environments yield shorter payback periods (6-10 months); operational schedules—continuous operations achieve 40-50% faster payback; replacement complexity; product value; and scale effects, with larger implementations benefiting from favorable pricing. The fastest paybacks occur in continuous high-temperature applications, while intermittent applications see longer periods.
Q3: How does ROI for premium zirconium silicate vary across industries?
ROI varies significantly based on operational conditions and product value. Glass and ceramic manufacturing often yields the highest ROI (85-120% annually) due to longer equipment lifespan. Chemical processing follows (70-90%), benefiting from extended component life. Metallurgical applications show 60-80% ROI, while electronics and semiconductor sectors achieve 50-70%. Pharmaceutical and food processing industries see lower but noteworthy ROIs (30-50%) from compliance and contamination reduction. These estimates derive from over 200 case studies, but specific calculations should be tailored to each operation.
Q4: How can manufacturers accurately calculate ROI for premium zirconium silicate?
To calculate ROI, gather baseline metrics, documenting all costs related to current materials and operational parameters. Conduct pilot tests with premium zirconium silicate for 3-6 months, then calculate direct savings from extended life, maintenance frequency reduction, and energy efficiency. Next, quantify indirect benefits like production increases and quality improvements. Finally, use the ROI formula: ROI = (total benefits – investment cost) / investment cost × 100%. For complex cases, consider NPV and IRR models to evaluate time value and risk.
Q5: What indirect benefits should be included in ROI calculations for premium zirconium silicate?
Investments yield several indirect benefits worth quantifying: enhanced brand reputation (5-15% improvement), safety (10-20% reduction in incident rates), and environmental benefits (8-12% decrease in carbon footprint). Innovations from premium materials may lead to patent opportunities and increased supply chain resilience through reduced replacement needs (20-30% inventory reduction). Collectively, these indirect benefits can represent 15-25% of total ROI and should be included in assessments.