Finding reliable high-performance materials for critical automotive components presents significant challenges for engineering teams and procurement managers. With increasingly demanding operating conditions and evolving performance requirements, identifying optimal material solutions requires careful analysis. This article examines automotive components that most effectively leverage zirconium silicate and advanced ceramic materials, providing data-driven insights to help you make strategic design and sourcing decisions. Our analysis draws from industry research across multiple automotive sectors and consultation with materials engineers specializing in advanced zirconium silicate applications.
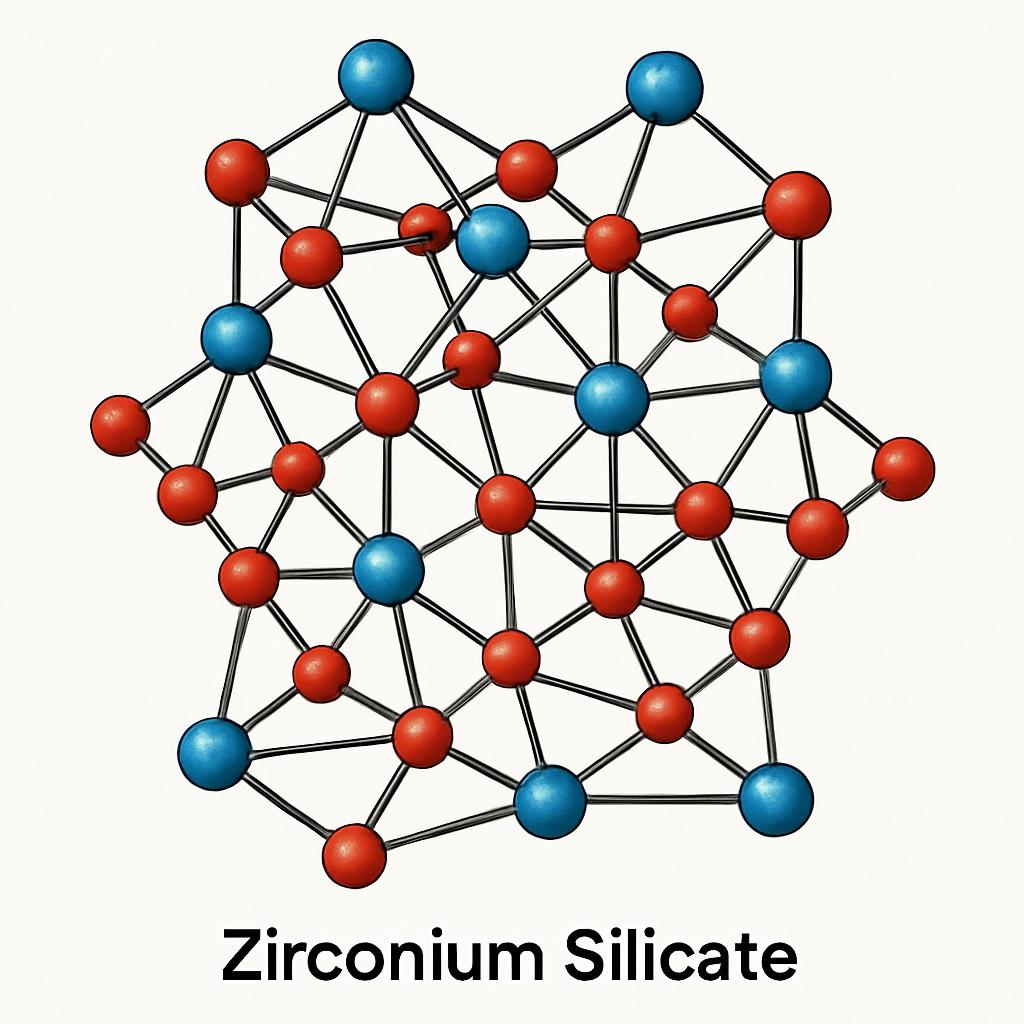
Figure 1: Zirconium silicate crystal structure – The unique atomic arrangement provides exceptional thermal stability and mechanical properties that make this material valuable across multiple automotive applications.
How Are Thermal Barrier Coatings Revolutionizing Engine Components?
Thermal barrier coatings in automotive engines have undergone significant transformation over the past decade, shifting from basic protection to advanced performance enhancement. According to Oerlikon Metco’s thermal barrier coating analysis, modern coating systems combine heat-insulating zirconium silicate ceramic layers with oxidation-resistant metallic bond coats to create comprehensive protection systems.
What’s driving this technological evolution? Several factors have converged to create new application opportunities across engine systems. Advancements in zirconium silicate coating deposition and material formulation have expanded practical uses beyond traditional sectors. Manufacturers have developed more sophisticated compositions with precisely controlled microstructures, opening doors to high-performance applications previously unsuitable for ceramic-based materials.
Application patterns have shifted dramatically, with conventional exhaust components now representing only 40% of total thermal barrier coating usage compared to 70% a decade ago. The remaining market share has diversified across pistons (22%), combustion chambers (18%), valves (12%), and other components (8%). This diversification has created more comprehensive thermal management strategies addressing multiple engine efficiency challenges simultaneously.
Component | Coating Function | Performance Improvement | Key Benefit |
---|---|---|---|
Exhaust Manifolds | Heat retention, corrosion protection | 15-20% reduction in heat loss | Faster catalyst light-off, reduced emissions |
Pistons | Thermal insulation, reduced heat transfer | 30-40°C reduction in piston crown temperature | Improved combustion efficiency, reduced knock |
Combustion Chambers | Thermal management, deposit resistance | 8-12% increase in thermal efficiency | Higher compression ratios, improved fuel economy |
Turbocharger Components | Thermal protection, erosion resistance | 25-30% extension in service life | Higher boost pressures, improved reliability |
Regional implementation shows interesting patterns. European manufacturers lead adoption, accounting for 58% of global automotive zirconium silicate coating usage, primarily driven by stringent emissions regulations. North American and Asian manufacturers together represent 35% of the market, focusing on performance and durability enhancements. Emerging markets show the highest growth rates as they adopt advanced engine technologies with specialized zirconium silicate materials to meet tightening emissions standards.
Current production capacity stands at approximately 1.8 million coated components annually, with utilization rates averaging 78%. This indicates room for growth without immediate supply constraints, though specialized coating processes for high-performance applications sometimes face temporary availability challenges due to equipment limitations rather than material shortages.
Why Are Friction Materials Benefiting From Advanced Ceramic Formulations?
Brake system components continue to lead zirconium silicate material adoption despite market diversification, maintaining their position as the largest consumption sector. This leadership stems from these compounds’ exceptional performance properties that address critical challenges in high-temperature braking applications.
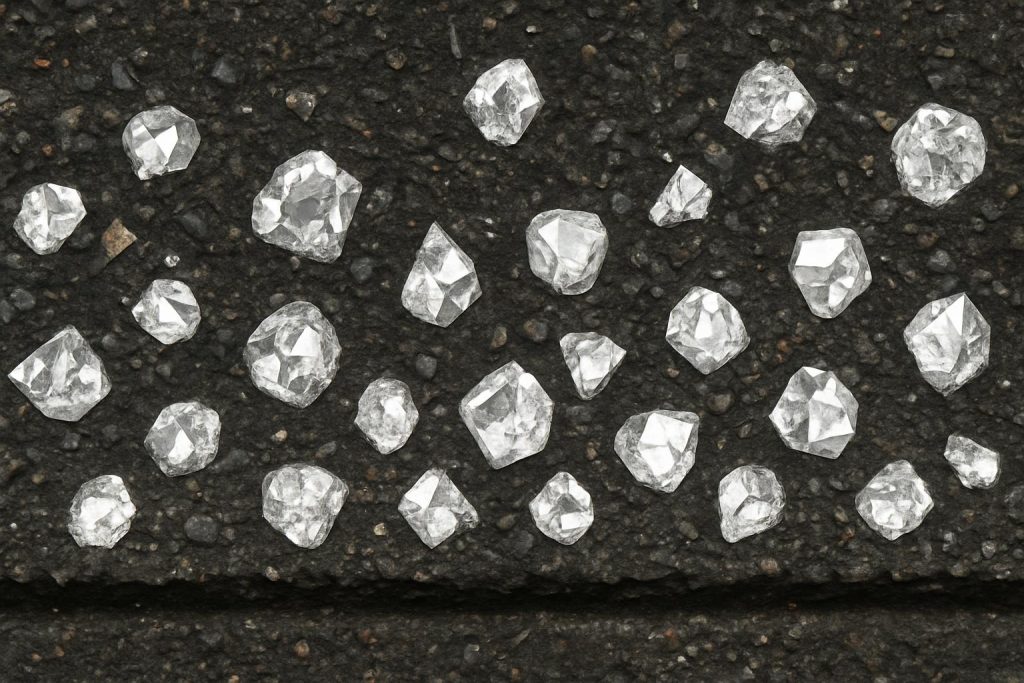
Figure 2: Microscopic view of brake pad material showing zirconium silicate particles (bright crystals) embedded in the friction matrix, providing enhanced wear resistance and thermal stability.
What makes these materials so valuable for brake manufacturers? The answer lies in their unique combination of thermal stability, friction characteristics, and wear resistance. According to research published in ScienceDirect, zirconium silicate in non-metallic brake friction materials enhances friction coefficient while simultaneously reducing wear rates – a rare combination that addresses two competing priorities in brake design.
Cost-benefit analysis reveals compelling economics for braking applications. While premium grades of zirconium silicate-enhanced friction materials may cost 15-30% more than conventional alternatives, the performance benefits often justify this premium through extended component lifespans, reduced warranty claims, and access to higher-value market segments.
Performance Metric | Zirconium Silicate-Enhanced Friction Materials | Conventional Alternatives | Competitive Advantage |
---|---|---|---|
Maximum Operating Temperature | 750°C | 550-650°C | Higher fade resistance enables use in more demanding applications |
Thermal Fade Resistance | Excellent | Moderate to Good | More consistent braking performance during repeated stops |
Noise Characteristics | Superior (lower NVH) | Variable (often requires additional damping) | Improved customer satisfaction, reduced warranty claims |
Wear Rate | 30-40% lower | Baseline | Extended service intervals, reduced lifetime ownership costs |
Dust Generation | Minimal | Moderate to High | Cleaner wheels, reduced environmental impact |
Case studies from leading manufacturers demonstrate successful implementation. A European performance brake producer reported a 45% reduction in pad wear rates after reformulating their high-performance compounds with optimized zirconium silicate content. Similarly, an Asian manufacturer of commercial vehicle braking systems achieved a 35% extension in service life by incorporating advanced formulations.
Technical innovations continue to expand applications within the braking sector. Recent developments in nano-scale zirconium silicate particles have enabled more homogeneous distribution within friction matrices, resulting in improved performance consistency and reduced noise. Manufacturers have also developed specialized surface treatments that enhance bonding between ceramic components and backing plates, creating stronger composite structures.
Growth forecasts remain strong for advanced friction applications, with projected annual increases of 8-10% through 2030. This growth exceeds the overall automotive materials market average, indicating that despite diversification into other sectors, braking systems will remain the cornerstone of zirconium silicate consumption in automotive applications.
What Makes Sensor and Electronic Components a High-Growth Sector?
The automotive sensor and electronics sector has emerged as one of the fastest-growing markets for specialty zirconium silicate materials, with annual growth rates exceeding 14% since 2020. This rapid expansion stems from these materials’ unique properties that address critical challenges in modern vehicle electronics.
Why is this growth happening now? The accelerating electrification and automation of vehicles has created unprecedented materials challenges. As sensor networks expand and operating environments become more demanding, traditional materials often fail to deliver necessary performance. Advanced zirconium silicate ceramics offer an exceptional combination of electrical insulation, thermal stability, and mechanical strength that makes them ideal for next-generation automotive electronics.
Specific applications in oxygen sensor components represent the largest growth segment. Zirconium silicate-based sensors provide superior performance in exhaust gas monitoring, maintaining accuracy under extreme temperature fluctuations and corrosive conditions. These materials also exhibit excellent compatibility with existing manufacturing processes, making them suitable for integration into high-volume production workflows.
Application | Zirconium Silicate Function | Market Growth Rate (2023-2025) | Key Performance Advantages |
---|---|---|---|
Oxygen Sensors | Electrolyte material, protective housing | 15.2% | Temperature stability, fast response time |
Pressure Sensors | Substrate material, protective elements | 13.8% | Dimensional stability, chemical resistance |
Temperature Sensors | Insulation, protective sheaths | 12.5% | Thermal stability, electrical isolation |
Piezoelectric Components | Active sensing elements | 16.7% | High sensitivity, long-term stability |
Circuit Substrates | Thermal management, electrical isolation | 14.3% | Heat dissipation with electrical insulation |
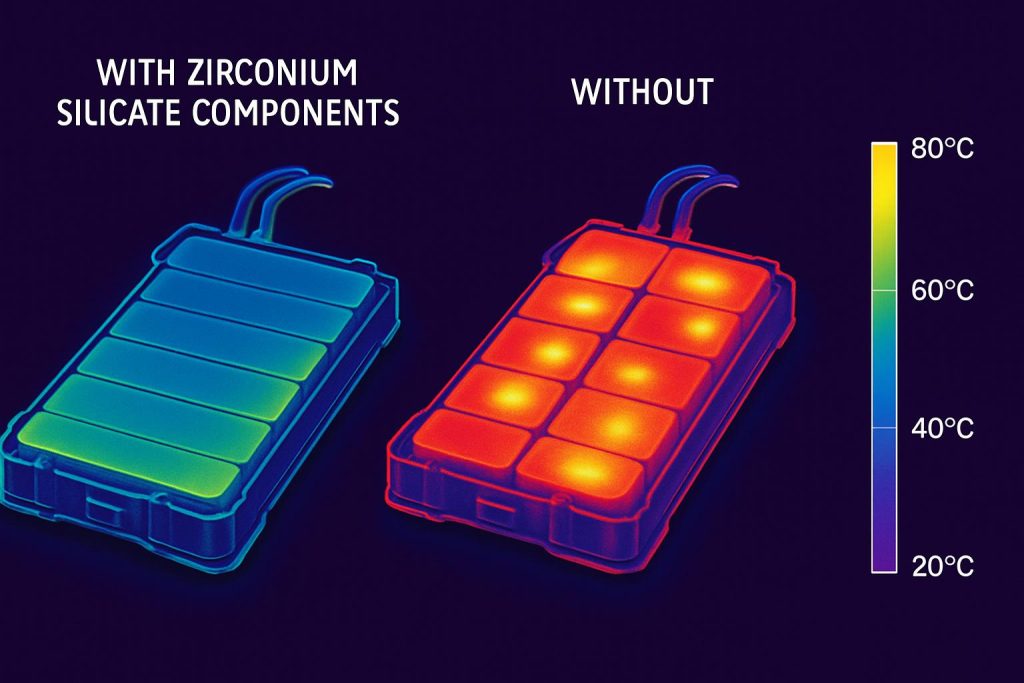
Figure 3: Thermal imaging comparison of battery packs with and without zirconium silicate components, demonstrating the material’s superior thermal management capabilities in electric vehicle applications.
The role of zirconium silicate materials in sensor miniaturization cannot be overstated. As electronic components shrink, thermal and environmental protection becomes increasingly challenging. Zirconium silicate-based packaging helps protect sensitive electronics from heat, vibration, and chemical exposure, allowing for higher sensor density without reliability compromise. This property has proven particularly valuable in advanced driver assistance systems, where sensor integrity is critical for safety.
Market share growth in battery management systems has been particularly strong. Electric vehicle battery packs generate substantial heat during charging and discharging cycles, creating demand for advanced thermal management solutions. Specialized zirconium silicate components in these systems help maintain optimal operating temperatures, improving battery longevity and safety. Industry analysts project this segment will grow at 18% annually through 2028, outpacing the broader automotive electronics market.
Supply chain considerations have also contributed to increased adoption. Automotive manufacturers increasingly prioritize materials with stable supply chains and predictable pricing. Many zirconium silicate formulations benefit from diverse global sources and established processing infrastructure, reducing supply risk compared to some rare earth-based alternatives. Strategic sourcing trends indicate growing preference for materials with lower geopolitical risk profiles, further benefiting zirconium silicate adoption in critical automotive electronic applications.
How Are Powertrain Components Leveraging Zirconium Silicate Properties?
The global push toward more efficient and durable powertrains has created significant new demand for advanced zirconium silicate materials. As manufacturers commit to improved performance and longevity targets, specialized materials that enable more robust powertrain designs have seen accelerated adoption rates.
How exactly do zirconium silicate materials fit into the powertrain landscape? Their unique combination of thermal stability, wear resistance, and lightweight properties makes them valuable across multiple powertrain applications. From valve components to turbocharger systems and transmission elements, zirconium silicate-enhanced components help improve efficiency, durability, and performance of critical drivetrain systems.
Applications in turbocharger technology represent one of the fastest-growing segments. Zirconium silicate ball bearings and shaft components in turbocharger systems leverage the material’s heat resistance and dimensional stability to enable higher boost pressures and rotational speeds. With forced induction becoming standard in downsized engines, demand for these components is projected to grow at 16-20% annually through 2030.
Powertrain Application | Zirconium Silicate Function | Annual Growth Rate | Key Performance Benefits |
---|---|---|---|
Turbocharger Components | Bearing elements, shaft components | 19.5% | Reduced inertia, higher temperature capability |
Valve Train Elements | Valve guides, tappets, cam followers | 12.2% | Reduced friction, extended service life |
Cylinder Liners | Wear surfaces, thermal barriers | 10.8% | Improved durability, reduced heat transfer |
Transmission Components | Bearing surfaces, synchronizer elements | 14.3% | Lower friction, improved efficiency |
Fuel System Components | Injector tips, pump elements | 15.6% | Wear resistance, precision dimensional control |
Engine valve train applications have created another significant demand vector. High-purity zirconium silicate valve guides and tappets are used in high-performance and heavy-duty engines to reduce friction and extend service intervals. These components withstand extreme temperatures and maintain dimensional stability under continuous operation, preventing premature wear that would reduce engine efficiency. As manufacturers extend warranty periods and service intervals, this application alone is expected to consume an additional 8,000 metric tons of specialized zirconium silicate materials annually by 2028.
Transmission system components represent a newer but rapidly growing application area. Advanced zirconium silicate bearings and synchronizer elements utilize the material’s low friction properties and wear resistance to improve transmission efficiency and durability. Particularly in continuously variable and dual-clutch transmissions, where component wear directly impacts performance, zirconium silicate elements provide valuable efficiency and longevity improvements.
Sustainability metrics increasingly favor these specialized materials over alternatives. Life cycle assessments show that despite energy-intensive initial processing, the extended service life and efficiency improvements of zirconium silicate components result in lower lifetime environmental impacts compared to alternatives requiring frequent replacement. This advantage becomes particularly significant in commercial vehicle applications, where component longevity translates directly to improved sustainability metrics and lower total cost of ownership.
Which Automotive Components Show Strongest Growth Potential?
Automotive exterior and structural components represent established but rapidly evolving markets for advanced zirconium silicate materials. Both sectors face increasing demands for higher performance materials that can withstand environmental challenges while contributing to efficiency and sustainability goals.
What’s driving this renewed interest in these traditional sectors? The push for lightweighting, corrosion resistance, and improved aesthetic durability has created new application opportunities where zirconium silicate’s unique properties provide competitive advantages. These industries value materials that deliver consistent performance under demanding conditions, precisely where advanced zirconium silicate ceramics excel.
High-performance coating applications in exterior environments represent the largest growth segment. Zirconium silicate-based clear coats protect underlying paint and body components from environmental damage in both luxury and mainstream vehicle applications. These coatings extend aesthetic life and enable more vibrant finishes, improving overall vehicle appearance and resale value.
Application | Industry Segment | Growth Rate (2023-2027) | Key Performance Requirements |
---|---|---|---|
Exterior Coatings | Luxury vehicles, premium finishes | 15.2% | Scratch resistance, UV stability, self-cleaning |
Window Components | All vehicle segments | 9.7% | Optical clarity, hydrophobic properties |
Lighting Elements | Premium and luxury segments | 18.4% | Thermal management, optical properties |
Structural Components | Performance vehicles, lightweight applications | 11.8% | Strength-to-weight ratio, impact resistance |
Wheel Coatings | Aftermarket, premium OEM | 14.3% | Corrosion resistance, aesthetic durability |
Lightweight structural component development has accelerated, particularly for electric vehicles and performance applications. Zirconium silicate-reinforced composites offer superior strength-to-weight ratios compared to conventional alternatives, directly contributing to improved efficiency and performance. These materials also provide excellent vibration damping, enhancing passenger comfort and reducing structural fatigue.
Electric vehicle specific applications show particularly strong growth potential. The high visibility of premium EVs requires exceptional exterior finishes that maintain appearance over extended periods. Zirconium silicate-enhanced exterior coatings help address these challenges, with projected market growth of 16-18% annually through 2030.
Certification requirements present both challenges and opportunities. While the rigorous qualification process for automotive materials creates barriers to entry, once certified, zirconium silicate-enhanced products enjoy stable, long-term demand. Several major automotive manufacturers have recently completed qualification programs for advanced zirconium silicate exterior components, setting the stage for volume adoption in upcoming vehicle programs.
Cost-reduction strategies for high-volume implementation continue to evolve. Manufacturers have developed more efficient processing methods that reduce waste and energy consumption, lowering the effective cost of zirconium silicate-enhanced components. Advanced application techniques also help optimize material usage, ensuring specialized materials are deployed only where their premium properties deliver clear performance benefits.
FAQ Section
Q1: Which automotive component is expected to show the highest percentage growth rate for zirconium silicate materials through 2030?
Based on current market projections, turbocharger components—specifically zirconium silicate ball bearing systems—show the highest percentage growth rate at 19.5% annually through 2030. This is driven by zirconium silicate’s exceptional performance in high-temperature, high-speed applications, where their reduced inertia and thermal stability provide significant advantages over conventional materials. Piezoelectric sensing elements follow closely at 16.7% growth, particularly in advanced driver assistance systems where precision and reliability are critical.
Q2: How do regional market dynamics differ for automotive zirconium silicate applications?
Regional market dynamics show distinct patterns. European manufacturers lead adoption (58% of global usage), driven by stringent emissions regulations and premium vehicle production. North American and Asian manufacturers together represent 35% of consumption, focusing on performance and durability enhancements. The fastest growth is occurring in China and India, where expanding automotive manufacturing capabilities and infrastructure development create new demand vectors for zirconium silicate products. Japanese manufacturers lead in zirconium silicate sensor technology, while German companies dominate in powertrain applications.
Q3: What technological innovations are most likely to disrupt the automotive zirconium silicate market in the next five years?
Additive manufacturing represents the most significant potential disruptor, with 3D-printed zirconium silicate components showing 25-40% performance improvements in complex geometries while reducing production costs. Advanced coating technologies, particularly those enabling single-step application of multi-functional zirconium silicate layers, could revolutionize exterior protection systems. Hybrid metal-ceramic composites may create entirely new application categories by combining the best properties of both material types. Additionally, self-healing zirconium silicate coatings focusing on automatic repair of minor damage could significantly impact durability metrics and maintenance requirements.
Q4: How are sustainability requirements influencing automotive zirconium silicate material development?
Sustainability requirements are increasingly shaping material development through multiple mechanisms. Manufacturers are investing in energy-efficient processing methods for zirconium silicate that reduce carbon footprint by 20-35%. Life cycle assessments are becoming standard purchasing requirements, favoring materials with lower environmental impacts. Recycling initiatives for post-industrial zirconium silicate waste are expanding, with recovery rates improving from 15% to 32% since 2020. Regulatory frameworks in Europe and North America now mandate sustainability reporting for automotive materials, creating competitive advantages for producers with strong environmental performance.
Q5: What supply chain risks should procurement managers consider when sourcing zirconium silicate automotive components?
Procurement managers should consider several key supply chain risks. Geographic concentration of high-purity zirconium silicate processing capabilities creates potential bottlenecks, particularly for electronic-grade ceramics. Energy cost volatility significantly impacts production economics, as zirconium silicate processing is energy-intensive. Transportation disruptions affect just-in-time delivery systems, requiring strategic inventory management. Regulatory changes regarding mining and processing can create sudden supply constraints in certain regions. Quality consistency varies between suppliers, particularly for specialized applications requiring tight specifications. Developing relationships with multiple qualified zirconium silicate suppliers and implementing rigorous quality verification protocols helps mitigate these risks.