Something’s not right with your zirconium silicate process? You’re seeing clogs, uneven batches, wasted energy—and the lab keeps flagging zirconium silicate purity issues.
This guide walks you through proven steps to get your zirconium silicate production line back on track. With firsthand insights and industry-backed fixes, we’ll help you hit zirconium silicate purity specs, reduce downtime, and maintain batch consistency—all while saving on costs.
What Are The Fundamentals of Zirconium Silicate Processing?
Zirconium silicate (ZrSiO₄) isn’t just another raw material—it’s the foundation of high-performance ceramics and coatings used across construction, aerospace, and consumer tile manufacturing. You might wonder why this particular material causes so many processing challenges.
When something goes wrong in zirconium silicate processing, the effects ripple across every department—QA sees rising rejections, operators start tweaking settings blindly, and clients start returning inconsistent batches. Understanding the science behind how zircon behaves when ground, suspended, dried, and fired is key to achieving process mastery.
Small changes in source material—such as an increase in rutile or baddeleyite—can drastically shift how zirconium silicate behaves in thermal environments. These shifts aren’t obvious until performance drops. That’s why understanding phase diagrams, impurity reactions, and sintering behavior is necessary to build reliable, cost-efficient operations with zirconium silicate.
The processing path begins with careful material selection and characterization of zirconium silicate. Manufacturers who invest in advanced testing methods like XRD and SEM analysis can identify potential issues before they enter production. This proactive approach reduces troubleshooting time by up to 40% compared to reactive quality control methods.
Processing Stage | Critical Parameters | Common Issues | Monitoring Methods |
---|---|---|---|
Milling | Particle size, Distribution curve | Overgrinding, Contamination | Laser diffraction, SEM |
Slurry Preparation | Viscosity, pH, Solids content | Settling, Foaming, Thickening | Rheometer, pH meter, Density cup |
Drying | Temperature profile, Moisture content | Case hardening, Cracking | Thermocouples, Moisture analyzer |
Firing | Ramp rate, Peak temperature, Soak time | Discoloration, Shrinkage variation | Thermal profiling, XRD analysis |
How Do You Identify Common Processing Challenges?
Most problems in zirconium silicate production don’t start in the dryer or press—they start quietly, upstream, and go unnoticed until the consequences pile up. But here’s the kicker – recognizing these early warning signs can prevent costly production failures.
Take, for instance, the classic “slurry becomes sludge” overnight issue. This points to instability in particle suspension caused by inconsistent milling of zirconium silicate, poor pH control, or binder mismatch. Or consider unexpected foaming in sprayers—often traced back to unaccounted-for surfactant buildup or microbial contamination in binders.
Another challenge is overgrinding of zirconium silicate, which leads to excessive surface area. This encourages particle agglomeration and disrupts settling behavior. Miscalibrated classifiers might allow fines to recirculate endlessly, creating inefficiencies and heat buildup that degrade both equipment and product.
Don’t overlook the water itself. Many factories rely on tap or borewell water, which changes composition seasonally. Hardness, TDS, and pH shifts can all subtly influence slurry rheology and binder activity in zirconium silicate processing. If your production is sensitive to environmental changes, this is likely the culprit.
Each of these issues, when handled in isolation, seems solvable. But collectively, they paint a picture of systems without robust monitoring and feedback. That’s why a holistic troubleshooting approach—one that spans raw inputs, the zirconium silicate process design, and QC—is what separates reactive operators from resilient manufacturers.
Case studies from leading ceramic manufacturers show that implementing comprehensive monitoring systems can reduce troubleshooting time by up to 65%. For example, one tile producer in Spain installed inline viscosity meters and particle size analyzers, allowing them to detect and correct zirconium silicate slurry issues within 30 minutes—compared to their previous 8-hour delay waiting for lab results.
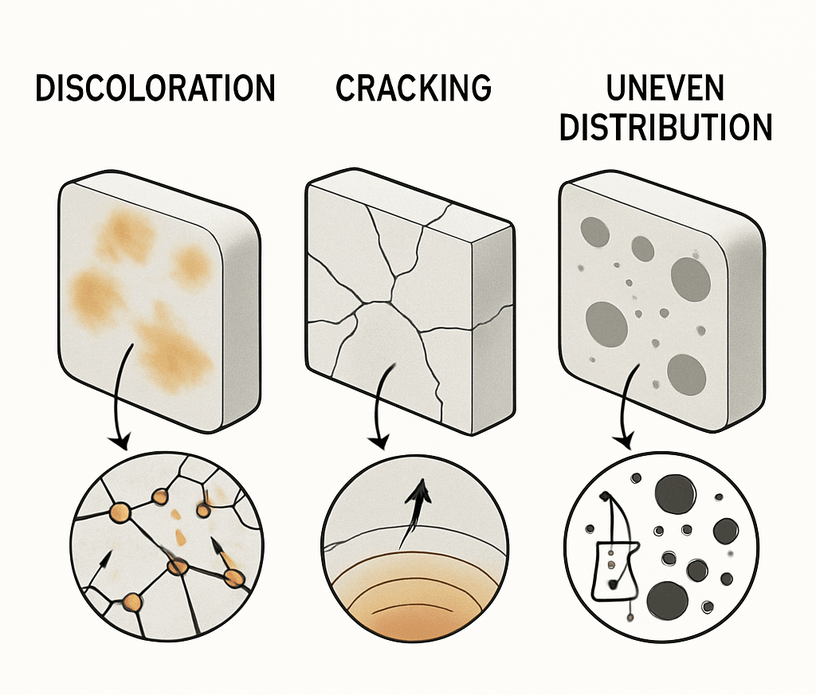
Why Is Raw Material Selection Critical?
Your zirconium silicate process is only as stable as your feedstock. What many processors fail to realize is that zircon concentrate from different mines—whether from Australia, South Africa, or India—varies significantly in Fe₂O₃, TiO₂, and SiO₂ content. And even within the same mine, seasonal variation affects everything from grindability to final brightness.
Instead of relying solely on certificates of analysis (COAs), forward-thinking buyers request impurity trends over 12 months. These insights, combined with in-house phase analysis and calcination trials, offer far more predictive power than a single zirconium silicate purity percentage ever could.
Zirconium silicate also behaves differently depending on its crystal structure and residual heavy mineral content. What looks pure under XRF may still cause sintering issues or unexpected discoloration during firing. This is where XRD (X-ray diffraction) and TGA (thermogravimetric analysis) become indispensable tools—not optional lab toys.
The financial impact of proper material selection cannot be overstated. A major European sanitaryware manufacturer reported that switching to a more consistent zircon source reduced their glaze defect rate by 37%, despite paying a 5% premium on raw material costs. The net savings in reduced rework and customer returns exceeded €175,000 annually for a medium-sized plant.
Source Region | Typical Impurities | Processing Implications | Recommended Testing |
---|---|---|---|
Australia | Lower Fe₂O₃, Higher TiO₂ | Better whiteness, Harder grinding | XRF, Grindability index |
South Africa | Moderate Fe₂O₃, Variable U/Th | Consistent sintering, Radiation monitoring | XRF, Radioactivity test |
India | Higher Fe₂O₃, Lower SiO₂ | Color management, Different flux needs | XRF, Colorimetry |
Southeast Asia | Variable heavy minerals | Inconsistent melt behavior | XRD, Melting point test |
One simple way to prevent feedstock-related surprises in zirconium silicate processing is to develop long-term partnerships with suppliers. Instead of spot-buying, negotiate consistent lot allocation and require representative samples for each incoming shipment. Over time, this practice alone can eliminate 30% of troubleshooting cycles in midstream production.
Advanced processors are now implementing AI-driven systems that correlate raw material characteristics with processing parameters and final product quality. These systems can automatically suggest adjustments to grinding time, dispersant levels, or firing profiles based on incoming material properties, creating a truly adaptive production system.
How Can You Resolve Equipment-Related Issues?
Zirconium silicate processing puts equipment through punishing conditions. Mills, separators, kilns, and classifiers each face abrasive forces, heat stress, and chemical exposure on a daily basis. This might surprise you, but equipment degradation often happens so gradually that operators don’t notice until quality has already suffered.
One of the most overlooked sources of variation is mill liner wear. As liners degrade, grinding becomes uneven. This not only affects particle size distribution but can also increase iron contamination due to contact with exposed metallic surfaces. The result? Discoloration in ceramics or functional failure in refractory uses. That’s why vibration monitoring and visual inspections should be routine, not reactive.
Separators and classifiers deserve special attention. These components are vital for ensuring particle size uniformity. When the internal blades or screens begin to warp—or worse, clog—the classification process becomes inconsistent. You might be sending coarse zirconium silicate particles into the next stage or retaining fines longer than needed, which messes with drying times and viscosity in downstream slurry preparation.
Modern facilities are implementing digital twin technology to monitor equipment health in real-time. By creating virtual models of physical assets, these systems can predict maintenance needs before failures occur. One refractory manufacturer in Germany reduced unplanned downtime by 43% after implementing vibration sensors and power consumption monitoring on their grinding circuit.
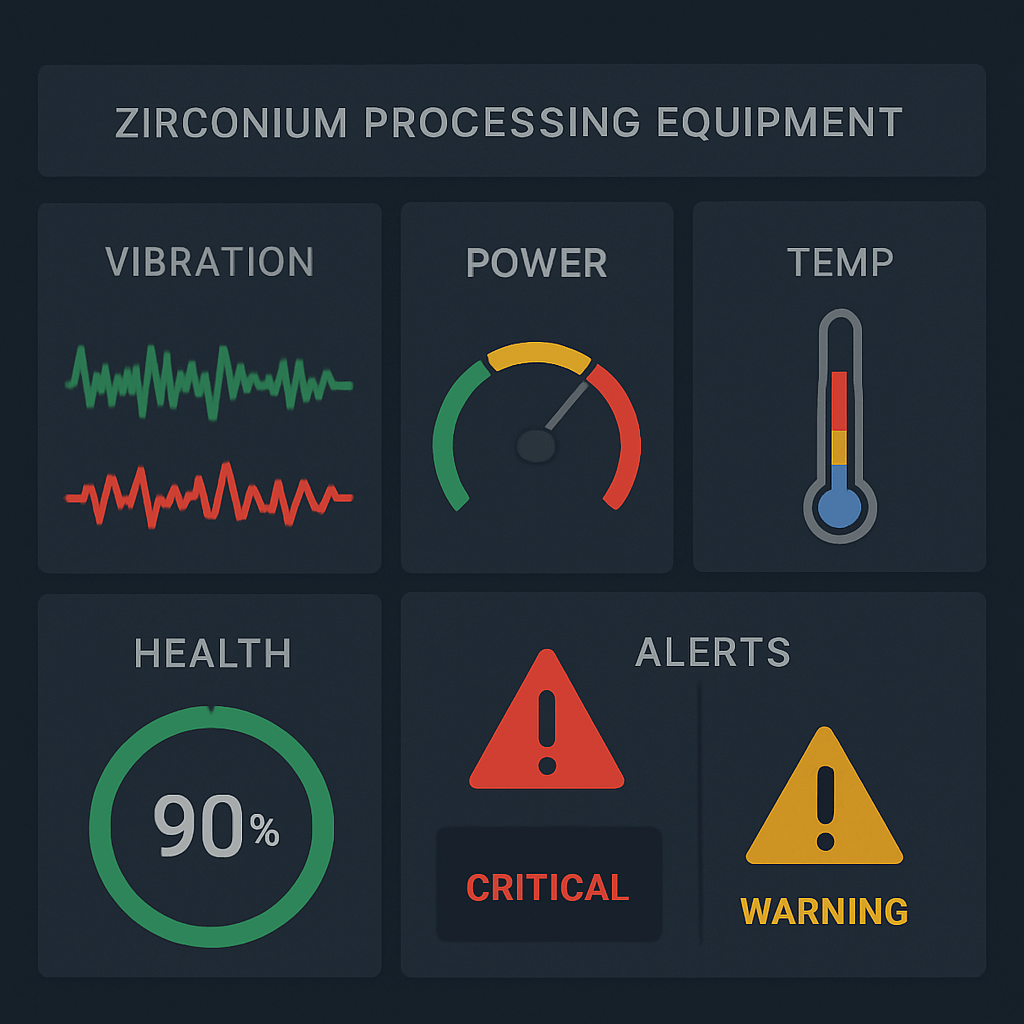
A smart approach involves integrating inline particle sizers and pressure gauges. A rise in pressure within separators often indicates internal blockages or a mechanical fault. Scheduled maintenance windows can prevent sudden failures, and stocking replacement parts minimizes downtime when issues do arise.
Tracking power consumption of each major unit provides early warning signs. A gradual increase in power usage often correlates with wear or misalignment. When paired with real-time temperature tracking, it forms a predictive maintenance matrix that safeguards production and extends equipment life by up to 30%.
What Solutions Exist for Slurry Handling Problems?
Slurry is often treated like an afterthought. It shouldn’t be. This phase of zirconium silicate processing is one of the most dynamic—and the easiest to disrupt. Here’s what works in maintaining homogeneity, preventing settling, and controlling viscosity in real-world conditions.
Inconsistent mixing of zirconium silicate leads to stratification. Poorly designed tanks without proper baffles or impeller placement create dead zones where heavier particles settle. Once this happens, any dosing or pumping based on volume assumptions becomes unreliable.
Temperature fluctuations can drastically alter zirconium silicate slurry behavior. Warmer slurries may lose viscosity and increase sedimentation, while colder ones may thicken unpredictably. That’s why smart operators install temperature-controlled holding tanks and insulated pipelines—especially in colder climates or variable-shift factories.
A case study from a major porcelain manufacturer demonstrates the impact of proper slurry management. After installing a combination of temperature control systems and redesigned mixing tanks with computational fluid dynamics-optimized baffles, they reduced batch-to-batch viscosity variation by 68%. This translated directly to more consistent spray drying and a 22% reduction in fired defects.
Slurry Issue | Root Causes | Solution Approaches | Monitoring Methods |
---|---|---|---|
Settling/Stratification | Inadequate mixing, Poor dispersant | Redesign tank, Optimize dispersant | Visual inspection, Density gradient |
Viscosity Fluctuation | Temperature changes, Water quality | Temperature control, Water treatment | Inline viscometer, Temperature logging |
Foaming | Excess surfactants, Microbial growth | Defoamer addition, Biocide treatment | Visual monitoring, Foam height sensor |
pH Drift | Water quality, Microbial activity | Buffer addition, Regular calibration | Continuous pH monitoring |
Agglomeration | Overgrinding, Binder incompatibility | Particle size control, Compatibility testing | Microscopy, Particle size analysis |
Foaming is another frequent complaint. Often caused by excessive dispersants or contaminated recycled water, foam not only ruins appearance but affects volume and dosing accuracy. The solution? Inline defoamers and accurate chemical control systems.
Viscosity needs constant monitoring. One method involves torque-based mixing sensors combined with real-time rheometers. This ensures that deviations are spotted before they impact casting or spraying operations. The earlier the intervention, the lower the risk of lost batches.
Also consider biological growth in tanks. Warm, stagnant zirconium silicate slurry is a breeding ground for bacteria that interfere with binders and stability. Scheduled sanitization, UV sterilizers, or biocide dosing—when applied properly—eliminates this risk and prevents the mysterious weekend viscosity shifts that plague many operations.
How Should You Approach Temperature and Drying Control?
Drying zirconium silicate slurry isn’t about “removing water.” It’s about doing it consistently, evenly, and without altering particle chemistry. What makes this particularly challenging is balancing speed with quality—too fast creates defects, too slow wastes energy and reduces throughput.
Many manufacturers use flash dryers or rotary kilns, but if your feed rate isn’t steady or your exhaust isn’t calibrated properly, you’ll develop hot spots and cold zones. These invisible inconsistencies degrade uniformity batch after batch. That’s why thermal mapping is critical—don’t rely on one temperature probe near the exit port.
Install multiple thermocouples throughout the dryer length and use thermal imaging cameras periodically. These tools highlight surface vs core drying differentials—needed for eliminating partially dried product that later causes pinholes in glaze or inconsistent hardness.
A technical ceramics producer in Japan revolutionized their approach by implementing a multi-zone drying system with independent temperature and humidity controls. By creating a carefully engineered drying profile that gradually removed moisture while preventing case hardening, they reduced cracking defects by 76% while simultaneously decreasing energy consumption by 14%.
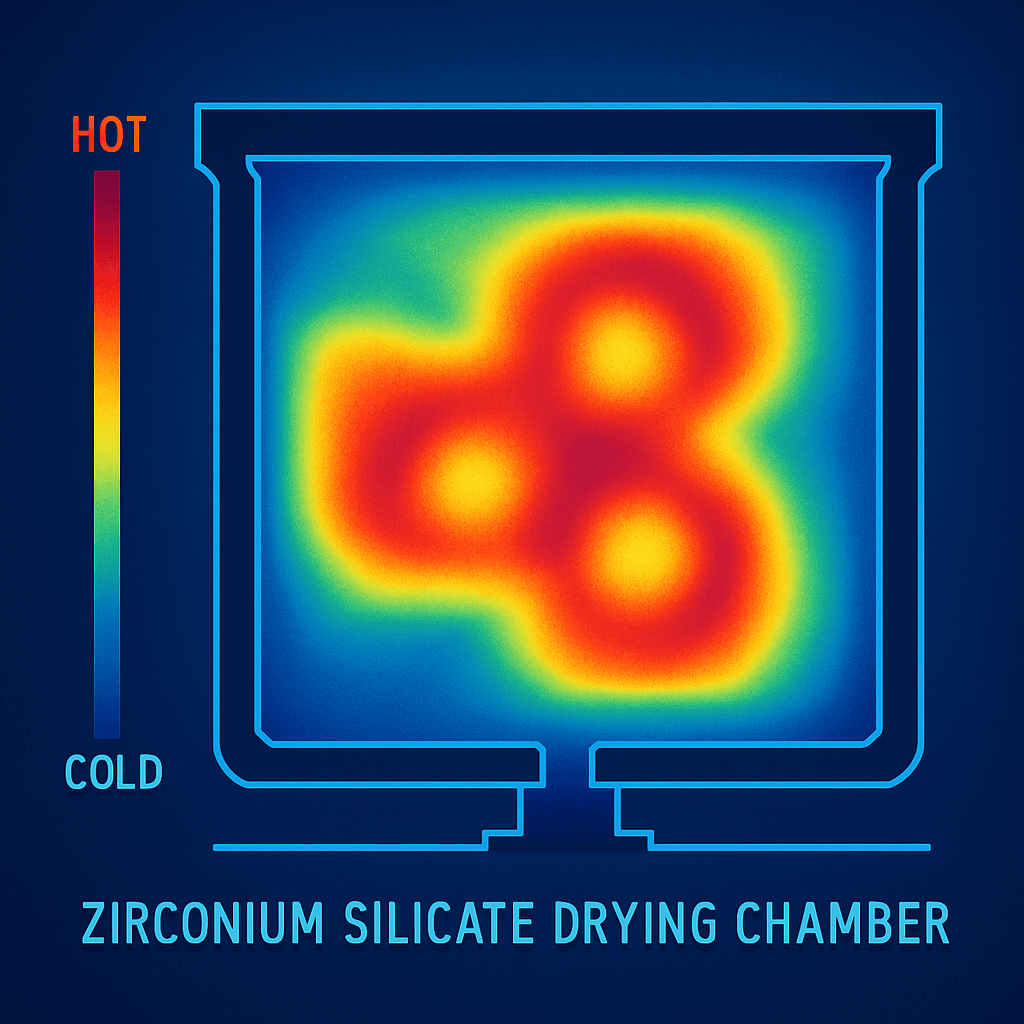
Don’t ignore humidity control. Most factories monitor temperature only, but residual humidity has just as much impact. Low exhaust airflow or poor moisture venting in thick batches can result in case hardening—the outside dries while the inside remains soft, leading to crumble or mold during storage.
Another overlooked element is ramp rate—how quickly you increase temperature. A steep ramp may shock the slurry structure, especially when using organic binders. A gradual thermal profile allows better binder burnout and smoother shrinkage later in the firing stage.
Document everything. Logging air inlet/outlet temperatures, humidity, airflow rate, and feed rate helps detect deviation trends early. Pair this with sample collection after drying to test bulk density and water retention. Drying isn’t a black box—it’s a data-driven checkpoint that can make or break your final zirconium silicate product quality.
What Process Flow Optimization Strategies Work Best?
A process line is only as good as its weakest transfer point. You might be surprised to learn that in many zirconium silicate facilities, inefficiencies emerge not from raw material or equipment—but from poorly mapped flows and inconsistent transition steps. That’s where process optimization plays a critical role.
Start with a visual: map out every step, from raw input to final drying. Where does material pause unnecessarily? Where do two shifts perform the same task differently? These “grey zones” create variation. And variation breeds error.
Use value-stream mapping (VSM) to analyze the flow of materials and information. Include physical movement, buffer storage, manual inspections, and downtime between operations. In most cases, there’s up to 20–25% idle time in the average zircon line. That’s hidden cost.
A leading abrasives manufacturer implemented lean manufacturing principles specifically adapted for zirconium silicate processing. By eliminating non-value-adding steps and standardizing work procedures across shifts, they reduced lead time by 37% and decreased work-in-process inventory by 42%. Most impressively, these improvements required minimal capital investment—just smarter process design and operator training.
Process Stage | Common Inefficiencies | Optimization Approach | Expected Improvement |
---|---|---|---|
Material Receiving | Inconsistent sampling, Delayed testing | Standardized protocols, Rapid testing | 15% faster material approval |
Grinding/Milling | Batch-to-batch variation, Excessive recirculation | Parameter standardization, Inline monitoring | 20% reduction in energy consumption |
Slurry Preparation | Long holding times, Manual adjustments | Automated dosing, Just-in-time mixing | 30% reduction in variation |
Drying/Calcining | Uneven loading, Variable moisture | Automated loading, Moisture feedback loop | 25% improvement in consistency |
Quality Testing | Delayed feedback, Limited sampling | Real-time testing, Statistical sampling | 40% faster problem identification |
Add timestamps at every step. This isn’t just for tracking output but to identify process dwell time. For example, if slurry sits in the holding tank for two hours instead of one, it may start sedimenting or flocculating. Long waits between pressing and drying also introduce humidity inconsistency.
Automation helps—but standardization matters more. Ensure every operator follows the same parameters, logging the same data points, and reacting to the same indicators. This limits human-induced variability.
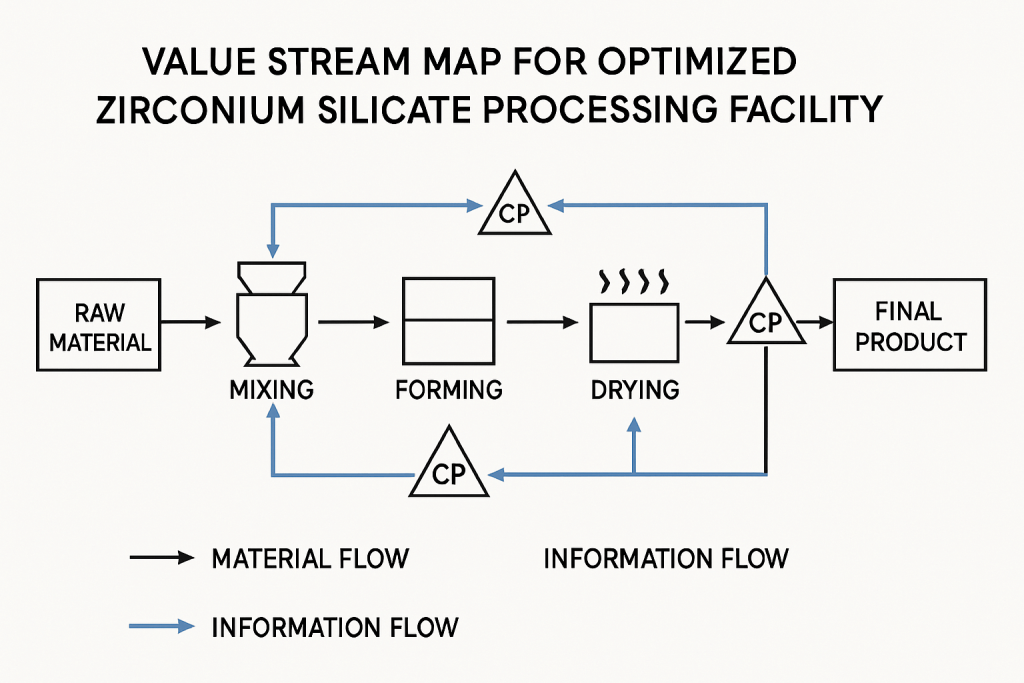
To wrap up, minimize rework loops. Every batch sent back to re-mix or re-dry burns energy and increases risk of contamination. Build checkpoints early in the line to catch issues before they escalate. The most successful facilities implement “quality gates” at critical transition points, where material cannot proceed until it meets specific criteria—preventing downstream issues before they begin.
FAQ Section
Q1: What is zirconium silicate used for?
Zirconium silicate is primarily used in ceramics, refractories, and tile glazing. Its whiteness, thermal resistance, and chemical inertness make it ideal for high-temperature and aesthetic applications. The material’s exceptional hardness (7.5 on the Mohs scale) also makes it valuable in abrasives and precision casting applications where dimensional stability at high temperatures is critical.
Q2: How can particle size affect performance?
Smaller particles improve smoothness and suspension but may agglomerate or require more binder. Larger particles reduce viscosity but can cause uneven glaze or texture. The optimal particle size distribution depends on the specific application—for example, fine zirconium silicate particles (D50 < 5μm) are preferred for high-gloss glazes, while coarser distributions (D50 > 10μm) may be better for refractory applications where thermal shock resistance is more valuable than surface finish.
Q3: Why does my slurry thicken overnight?
Common causes include temperature drop, binder instability, microbial growth, or water source changes. Check all variables related to zirconium silicate, not just solids content. Temperature fluctuations of even 5-10°C can significantly impact viscosity, especially with certain dispersants. Implementing temperature-controlled storage and regular pH monitoring can prevent most overnight thickening issues. For persistent problems, consider adding small amounts (0.05-0.1%) of biocide to prevent microbial growth.
Q4: How often should equipment be serviced?
It depends on usage, but weekly inspections and monthly calibration are standard. Always log changes and correlate with production data. High-wear components like zirconium silicate mill liners should be inspected according to manufacturer guidelines, typically every 500-1000 operating hours. Implementing a predictive maintenance program based on vibration analysis and power consumption monitoring can extend equipment life by 15-30% compared to fixed-interval maintenance schedules.
Q5: Is automation worth the investment in small plants?
Yes—if implemented wisely. Start with critical control points (like dryer temp or slurry pH), then expand. ROI often comes from fewer rejects, faster diagnosis, and better consistency. Even small facilities can benefit from targeted automation investments for zirconium silicate processing. For example, automated pH and viscosity control systems typically pay for themselves within 12-18 months through reduced waste and improved product consistency. The key is prioritizing automation that addresses your specific pain points rather than implementing comprehensive systems all at once.