What Performance Differences Separate Zirconium Silicate from Zirconia in Technical Applications? This question guides material selection decisions across numerous industries. From electronics to medical implants, engineers must understand how these two zirconium-based materials differ in performance. This article examines the critical differences in chemical structure, thermal behavior, mechanical properties, and other key characteristics that determine which material best suits specific technical needs.
What Chemical Composition and Structure Differences Impact Performance?
The fundamental differences between these materials start with their basic makeup. Zirconium silicate (ZrSiO₄) contains silicon as a key component, while zirconia (ZrO₂) consists only of zirconium and oxygen atoms. You might wonder how this seemingly small difference creates such varied performance profiles.
Basic Chemical Structure and Properties
Zirconium silicate forms a tetragonal crystal system with isolated SiO₄ tetrahedra connected by ZrO₈ dodecahedra. This arrangement creates exceptional stability that resists phase changes even at high temperatures. The silicon-oxygen bonds provide structural rigidity that pure zirconia lacks.
In contrast, zirconia shows polymorphism, existing in three forms: monoclinic at room temperature, tetragonal at intermediate temperatures (1170°C to 2370°C), and cubic at high temperatures (above 2370°C). These phase transformations significantly impact volume stability and mechanical properties.
Key Structural Differences
Feature | Zirconium Silicate (ZrSiO₄) | Zirconia (ZrO₂) | Performance Impact |
---|---|---|---|
Chemical Composition | Contains silicon | Only Zr and O | Affects chemical stability and thermal behavior |
Crystal Structure | Stable tetragonal phase | Multiple phases (monoclinic, tetragonal, cubic) | Impacts phase stability and mechanical properties |
Phase Transformation | Decomposes at ~1650°C | Transforms at 1170°C and 2370°C | Determines high-temperature stability |
Microstructure | Higher porosity, larger grains | Can achieve near-theoretical density, finer grains | Influences mechanical strength and toughness |
What truly sets these materials apart is how their structures respond to environmental stresses. Zirconium silicate maintains consistent properties across wide temperature ranges, while zirconia’s properties change dramatically with phase transformations.
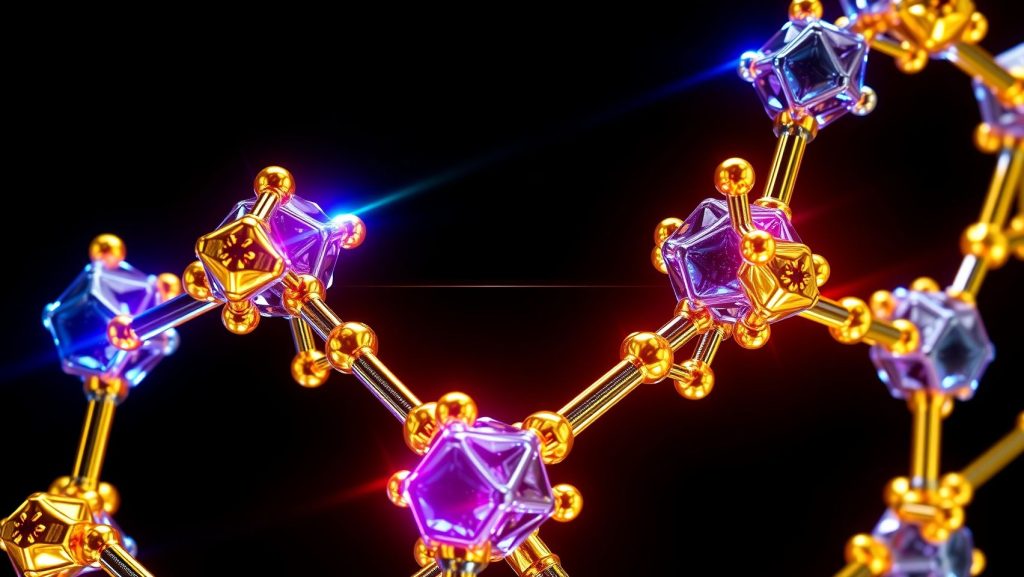
This image shows the tetragonal crystal structure of zirconium silicate, highlighting the SiO₄ tetrahedra and ZrO₈ polyhedra arrangement that creates its stable lattice configuration.
How Do Thermal Properties Differ Between These Materials?
Thermal performance represents a critical differentiator between these materials. But here’s the kicker – understanding these differences helps engineers predict exactly how components will perform under specific thermal conditions.
Temperature Stability Comparison
Zirconium silicate boasts an impressive melting point of approximately 2550°C but decomposes into zirconia and silica at about 1650°C. This decomposition temperature effectively serves as its practical upper limit for most applications.
Zirconia offers a slightly higher melting point of 2715°C but undergoes phase transformations at 1170°C and 2370°C. These transformations cause volume changes that can create internal stresses and potential failure points unless stabilizing oxides are added.
The thermal expansion coefficient of zirconium silicate (4.0-4.5 × 10⁻⁶/°C) measures significantly lower than zirconia’s (10-11 × 10⁻⁶/°C). This lower expansion rate provides superior dimensional stability during thermal cycling, making zirconium silicate valuable in precision applications where maintaining tight tolerances under varying temperatures matters.
Thermal Performance Data
Thermal Property | Zirconium Silicate | Zirconia | Application Impact |
---|---|---|---|
Melting Point | ~2550°C | ~2715°C | Determines maximum operating temperature |
Phase Change Temperature | Decomposes at ~1650°C | Transforms at 1170°C and 2370°C | Affects structural stability at high temperatures |
Thermal Expansion | 4.0-4.5 × 10⁻⁶/°C | 10-11 × 10⁻⁶/°C | Impacts dimensional stability during thermal cycling |
Thermal Conductivity | ~5.1 W/m·K | 2-3 W/m·K | Influences thermal shock resistance |
In cyclic temperature applications, zirconium silicate typically outperforms unstabilized zirconia in maintaining dimensional stability. The absence of phase transformations during heating and cooling cycles eliminates the volume changes that can lead to microcracking in unstabilized zirconia components.
Why Do Mechanical Properties Matter in Material Selection?
The mechanical properties of these materials represent perhaps their most striking performance differences. Engineers must carefully weigh these distinctions when selecting materials for mechanically demanding environments.
Strength and Toughness Analysis
Zirconia stands out for its exceptional mechanical strength and toughness, particularly in its partially stabilized form. With flexural strength values typically ranging from 800-1500 MPa and fracture toughness between 6-15 MPa·m½, zirconia significantly outperforms zirconium silicate in these critical parameters.
This might surprise you – zirconia’s remarkable toughness stems from its unique transformation toughening mechanism. When stress is applied, the tetragonal phase transforms to monoclinic, creating compressive stresses that inhibit crack propagation. This mechanism gives zirconia its exceptional damage resistance.
Zirconium silicate exhibits more modest mechanical properties, with flexural strength typically between 150-300 MPa and fracture toughness around 1-3 MPa·m½. The absence of transformation toughening mechanisms makes zirconium silicate inherently more brittle, limiting its applications in high-stress environments.
Mechanical Performance Comparison
Mechanical Property | Zirconium Silicate | Zirconia (Partially Stabilized) | Application Impact |
---|---|---|---|
Flexural Strength | 150-300 MPa | 800-1500 MPa | Affects load-bearing capacity |
Fracture Toughness | 1-3 MPa·m½ | 6-15 MPa·m½ | Determines resistance to crack propagation |
Vickers Hardness | 800-1100 HV | 1200-1400 HV | Influences wear resistance |
Elastic Modulus | 150-170 GPa | 200-210 GPa | Impacts stiffness and strain response |
Under cyclic loading conditions, zirconia typically demonstrates better fatigue resistance, particularly in humid environments where zirconium silicate may experience accelerated crack growth due to stress corrosion mechanisms.
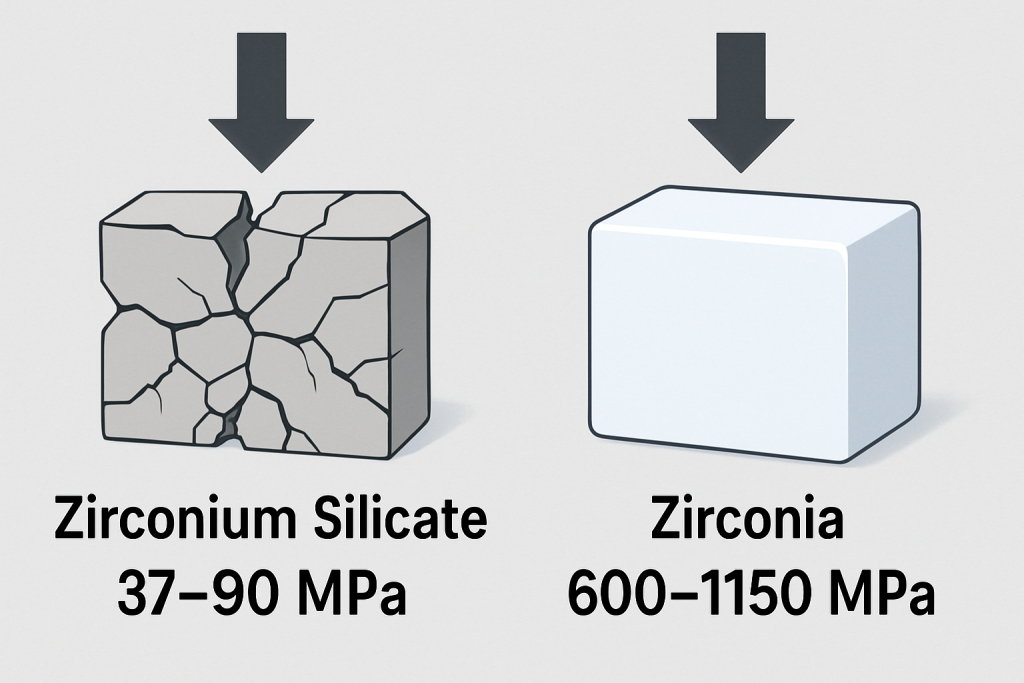
This chart compares the mechanical strength properties of zirconium silicate and zirconia, clearly showing the significant advantages zirconia offers in strength and toughness for structural applications.
How Do Electrical Properties Influence Application Choices?
When evaluating these materials for electrical and insulation applications, their distinct electrical properties create significant performance differences that engineers must consider.
Insulation and Dielectric Performance
Zirconium silicate typically exhibits higher electrical resistivity compared to zirconia, with values often exceeding 10¹⁴ Ω·cm at room temperature. What makes this particularly valuable is how it maintains its insulating properties across a broader temperature range than many alternatives, with minimal conductivity increases even at elevated temperatures.
The dielectric constant of zirconium silicate generally falls between 8-12, significantly lower than zirconia’s typical range of 25-29 for fully stabilized material. This lower dielectric constant translates to reduced capacitive effects, making zirconium silicate preferable in high-frequency applications where signal integrity matters.
Electrical Property Comparison
Electrical Property | Zirconium Silicate | Zirconia | Application Impact |
---|---|---|---|
Electrical Resistivity | >10¹⁴ Ω·cm | 10¹⁰-10¹² Ω·cm | Affects insulation performance |
Dielectric Constant | 8-12 | 25-29 | Influences capacitive effects |
Dielectric Strength | 10-15 kV/mm | 9-12 kV/mm | Determines breakdown voltage |
Temperature Dependence | Lower | Higher | Impacts performance stability during temperature fluctuations |
In terms of temperature-dependent electrical properties, zirconia exhibits more pronounced changes in resistivity with increasing temperature compared to zirconium silicate. This characteristic makes zirconium silicate more reliable in applications experiencing thermal fluctuations.
Which Material Offers Better Chemical Resistance?
The chemical stability and corrosion resistance of these materials represent critical performance differentiators in aggressive chemical environments.
Acid and Alkali Resistance
Zirconium silicate demonstrates exceptional resistance to acids, maintaining structural and chemical integrity even in concentrated sulfuric, hydrochloric, and nitric acid environments. But here’s what many engineers overlook – its resistance to hydrofluoric acid significantly surpasses that of zirconia, making it the preferred choice for applications involving this particularly aggressive chemical.
In alkaline environments, the performance comparison shifts notably. Zirconia typically exhibits better resistance to strong bases, particularly at elevated temperatures where zirconium silicate may experience accelerated degradation through attack of the silicate component.
Chemical Resistance Profile
Chemical Environment | Zirconium Silicate | Zirconia | Application Impact |
---|---|---|---|
Strong Acids | Excellent | Good | Influences chemical processing equipment selection |
Hydrofluoric Acid | Good | Poor | Critical for semiconductor and glass processing |
Strong Bases | Moderate | Excellent | Important for alkaline processing applications |
Oxidizing Conditions | Excellent | Good | Affects high-temperature oxidation applications |
Reducing Conditions | Good | Excellent | Impacts metallurgical applications |
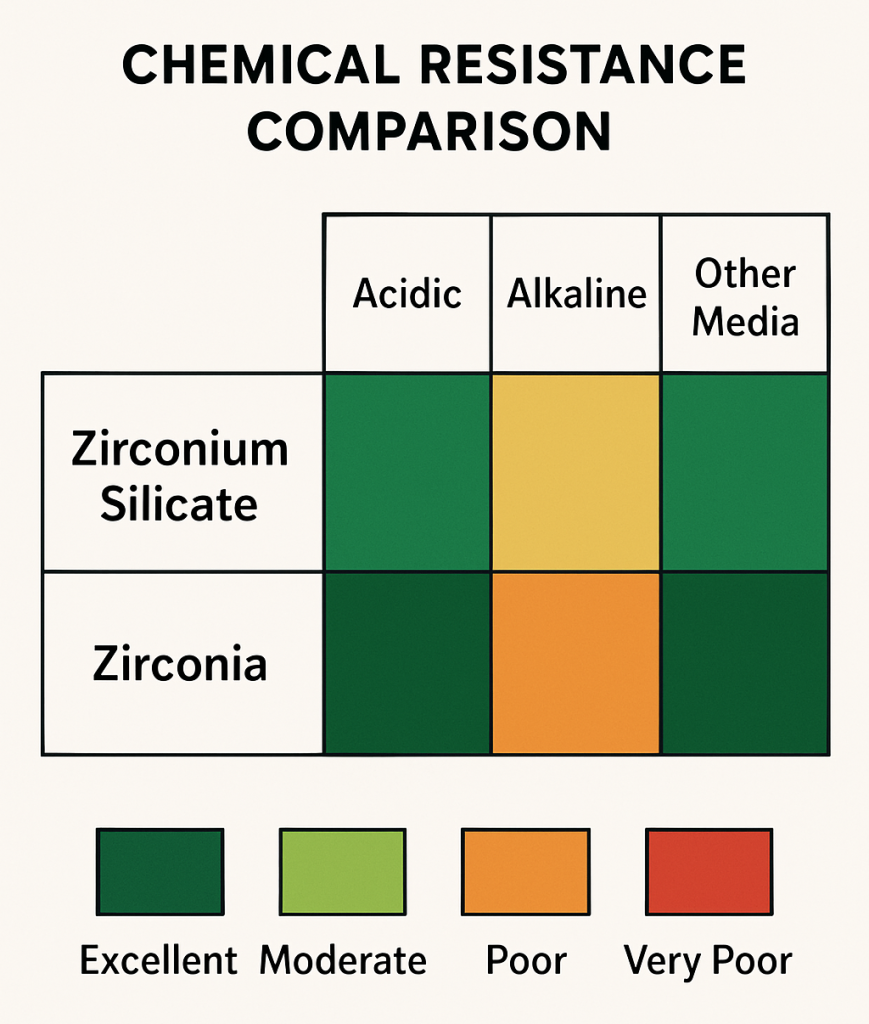
This chart illustrates the relative chemical resistance of both materials across various corrosive environments, using color coding to show performance differences in acids, bases, and other chemical media.
How Do These Materials Perform in Medical Applications?
In biomedical applications, the performance differences between these materials become particularly significant, with direct implications for patient outcomes and device longevity.
Biocompatibility and Clinical Performance
Zirconia has established itself as the gold standard for many biomedical applications, particularly in dental fields. What’s the real story behind its dominance? The material’s exceptional biocompatibility stems from its chemical inertness, minimal ion release, and ability to integrate with surrounding tissues without triggering significant inflammatory responses.
Cytotoxicity studies consistently demonstrate that both materials exhibit minimal adverse effects on cellular viability. However, zirconia typically shows superior performance in direct cell attachment and proliferation tests, with osteoblasts and fibroblasts demonstrating enhanced adhesion and growth on zirconia surfaces compared to zirconium silicate.
In dental applications, zirconia’s combination of aesthetic qualities, mechanical strength, and biocompatibility has made it the material of choice for crowns, bridges, and abutments. Its white color and translucency provide natural-looking restorations that closely mimic natural teeth.
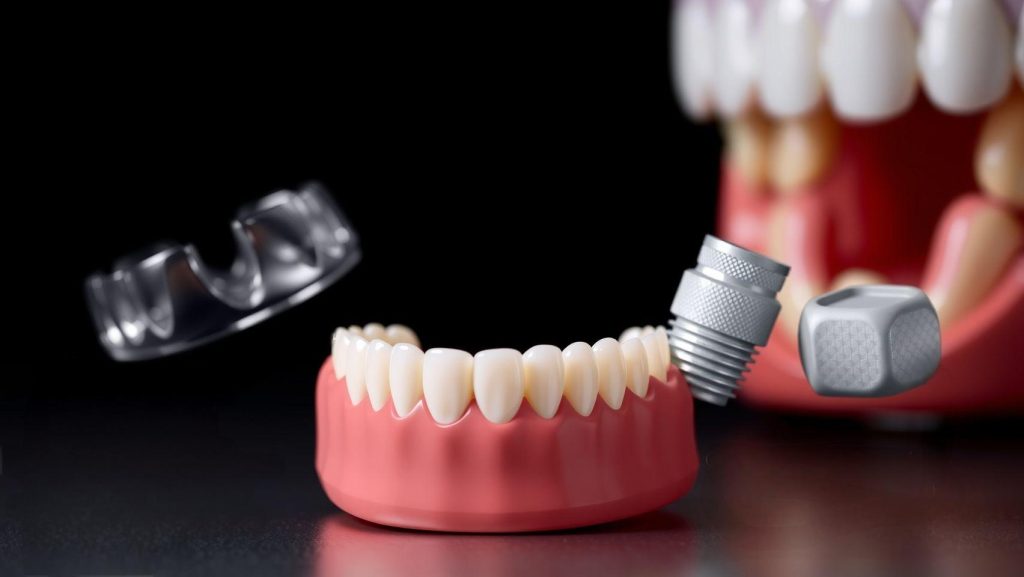
This image shows various dental applications of zirconia, including crowns, bridges, and implant components, highlighting its aesthetic qualities and structural performance in oral environments.
What Cost and Manufacturing Considerations Should Guide Selection?
The manufacturing processes and cost considerations for these materials represent crucial factors that often determine material selection beyond pure performance metrics.
Production Economics and Processing Requirements
Zirconium silicate typically offers significant cost advantages over zirconia, with raw material expenses often 30-50% lower depending on grade and purity requirements. You might be surprised to learn that the economic advantage extends beyond raw material costs to include processing considerations.
Zirconium silicate generally requires lower sintering temperatures (typically 1450-1550°C) compared to zirconia (1500-1700°C for fully dense components), resulting in reduced energy consumption and potentially lower equipment investment for manufacturing facilities.
The forming processes for these materials also differ substantially. Zirconia demonstrates superior plasticity in ceramic forming operations, allowing for more complex shapes through techniques like injection molding and extrusion. This formability advantage must be weighed against the higher material costs.
What Future Innovations Will Expand Applications?
The evolving landscape of advanced materials continues to expand the application possibilities for both materials, with emerging technologies creating new opportunities.
Emerging Technologies and Applications
Additive manufacturing represents perhaps the most transformative development for these materials in recent years. What makes this particularly exciting is how their different properties create distinct advantages in this emerging field. Zirconia has gained significant traction in stereolithography applications, particularly for dental components where its superior mechanical properties provide clear benefits.
Nanostructured variants of both materials are opening new application frontiers. Nano-zirconia has demonstrated enhanced catalytic activity and improved low-temperature sinterability. Similarly, nano-zirconium silicate shows promise in environmental applications, particularly for nuclear waste remediation and heavy metal adsorption.
FAQ Section
Q1: What are the primary chemical differences between zirconium silicate and zirconia?
Zirconium silicate (ZrSiO₄) contains silicon as an integral component, forming a stable tetragonal structure with SiO₄ tetrahedra and ZrO₈ polyhedra. Zirconia (ZrO₂) consists only of zirconium and oxygen, exhibiting polymorphism with three crystal phases depending on temperature. This fundamental chemical difference creates distinct performance characteristics across thermal, mechanical, and chemical applications.
Q2: How do the thermal expansion properties compare between these materials?
Zirconium silicate has a significantly lower thermal expansion coefficient (4.0-4.5 × 10⁻⁶/°C) compared to zirconia (10-11 × 10⁻⁶/°C). This lower expansion rate gives zirconium silicate superior dimensional stability during thermal cycling, making it preferable for precision applications where maintaining tight tolerances under varying temperatures is critical.
Q3: Why does zirconia offer superior mechanical properties compared to zirconium silicate?
Zirconia’s exceptional mechanical strength and toughness stem from its unique transformation toughening mechanism, where stress-induced phase transformation from tetragonal to monoclinic creates compressive stresses that inhibit crack propagation. This mechanism gives partially stabilized zirconia flexural strength values of 800-1500 MPa and fracture toughness between 6-15 MPa·m½, significantly outperforming zirconium silicate’s 150-300 MPa and 1-3 MPa·m½ respectively.
Q4: Which material performs better in aggressive chemical environments?
Performance depends on the specific chemical environment. Zirconium silicate demonstrates superior resistance to most acids, particularly hydrofluoric acid, making it preferable for semiconductor processing and glass manufacturing. Zirconia exhibits better resistance to strong bases and alkaline environments, especially at elevated temperatures, making it more suitable for applications involving molten alkali metals or concentrated sodium hydroxide solutions.
Q5: What cost factors should be considered when choosing between these materials?
Zirconium silicate typically offers 30-50% lower raw material costs compared to zirconia, depending on grade and purity. Processing costs also differ, with zirconium silicate requiring lower sintering temperatures (1450-1550°C vs. 1500-1700°C for zirconia), reducing energy consumption. However, zirconia’s superior formability allows for more complex shapes with fewer machining steps, potentially offsetting its higher material cost in certain applications.