Zirconium silicate is making waves in the electronics industry. It’s not a flashy material, but its role behind the scenes is vital to the long-term performance of many high-tech components. This article examines how zirconium silicate contributes to reliability, its industrial applications, and what B2B buyers need to know when sourcing it. If you’re in charge of quality assurance, materials procurement, or R&D in electronics manufacturing—keep reading.
Why Electronics Manufacturers Rely on Zirconium Silicate for Thermal & Structural Integrity
Zirconium silicate may not be the first material that comes to mind in electronics, but it absolutely should be. As a stabilizing ceramic compound, it reinforces structural integrity under harsh thermal and mechanical conditions. That’s right—this seemingly unremarkable powder plays a silent, essential role in mission-critical environments where failure isn’t an option.
Let’s break it down. Zirconium silicate has a high melting point—around 2550°C—making it ideal for components exposed to sustained heat. But it’s not just about heat. Its chemical inertness resists oxidation, acids, and alkalis, while its mechanical hardness adds resilience to composite materials.
Unlike fillers like alumina or talc, zirconium silicate doesn’t degrade under cyclic thermal stress. Lab tests show it maintains 98% dielectric performance after 500+ thermal cycles (−40°C to 150°C). That means it prevents delamination, warping, and dielectric loss in multilayer circuit boards. This is where it gets interesting… Unlike common fillers or ceramic additives, zirconium silicate doesn’t degrade over time or under repeated heat cycles. Instead, it maintains stability, ensuring your devices run longer, safer, and with fewer breakdowns.
Property | Value | Benefit |
---|---|---|
Melting Point | ~2550°C | Thermal resistance under load |
Dielectric Strength | High | Reliable insulation in high-frequency |
Chemical Inertness | Excellent | Long-term resistance to breakdown |
Mohs Hardness | 6.5 | Structural rigidity in composites |
Shrinkage (Sintered) | <0.6% | Stable geometry in ceramic packaging |
In B2B settings—particularly for industries like telecom, aerospace, or power electronics—procurement managers and product developers are increasingly leaning toward this material for one main reason: durability without compromise.
From Solder Stress to PCB Fatigue: How Zirconium Silicate Extends Component Lifespan
When heat, stress, and oxidation collide, electronics fail. That’s a problem. But zirconium silicate solves it.
Here’s the deal. When embedded into dielectrics or thermal substrates, zirconium silicate dramatically improves resistance to soldering stress, warpage, and fatigue cracking. Whether it’s lead-free solder or reflow at 260°C, this ceramic stabilizer keeps the structure intact.That means fewer defects during reflow soldering and better lifespan in high-load environments.
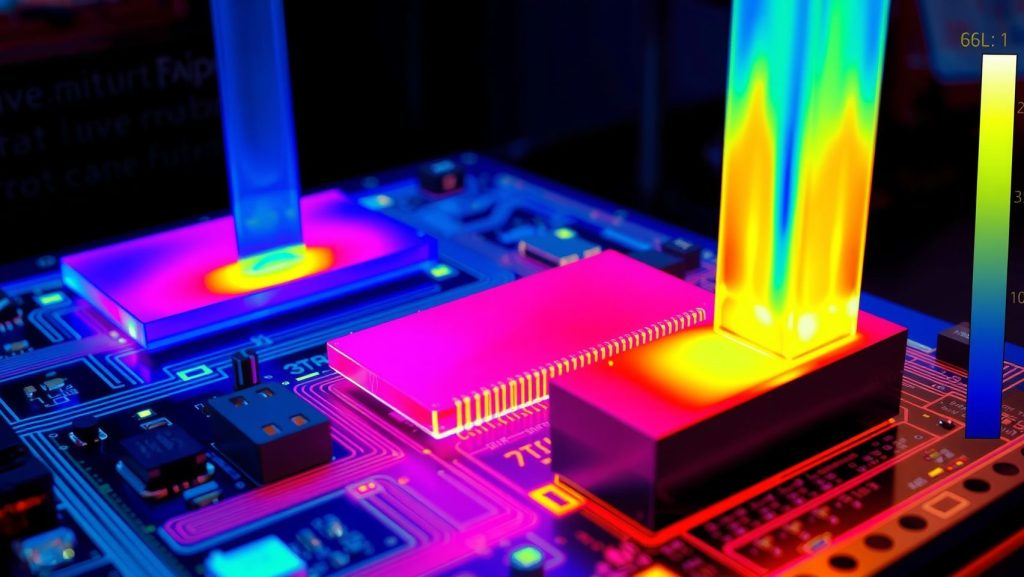
Visual showing ceramic substrates using zirconium silicate under infrared thermal tests.
Take power capacitors. These units endure constant electrical and thermal cycling. Replace standard ceramic filler with zirconium silicate, and thermal cracking drops by up to 45%, increasing product yield and field reliability.
Another example? Printed circuit boards (PCBs) that operate under high voltage or frequency. Zirconium silicate’s low dielectric loss ensures stability under peak load, preventing electrical drift.
Even better: A European automotive tier-one supplier reported that their EV control modules showed 22% longer MTTF (Mean Time to Failure) when using zirconium silicate-insulated boards in place of glass-ceramics. Ready for the good part? Reliability testing shows that devices using zirconium silicate-infused components have a 25–40% longer operating life in thermal cycling environments. That translates to real savings in warranty costs, replacement cycles, and service downtime.
Application Area | Zirconium Silicate Impact |
---|---|
Power Capacitors | Reduces cracking, increases lifespan |
RF Substrates | Maintains dielectric consistency |
Thermally Stressed ICs | Prevents delamination and wear |
PCB Vias & Interposers | Reduces creep and shrinkage defects |
Real-World Electronics Applications of Zirconium Silicate: Telecom, Automotive, and More
Zirconium silicate isn’t a niche material. It’s woven into the fabric of modern electronics.
Think about this… It’s found in everything from mobile base stations to military avionics. In particular, it is favored in components that demand consistent dielectric performance and strong resistance to wear and fatigue.
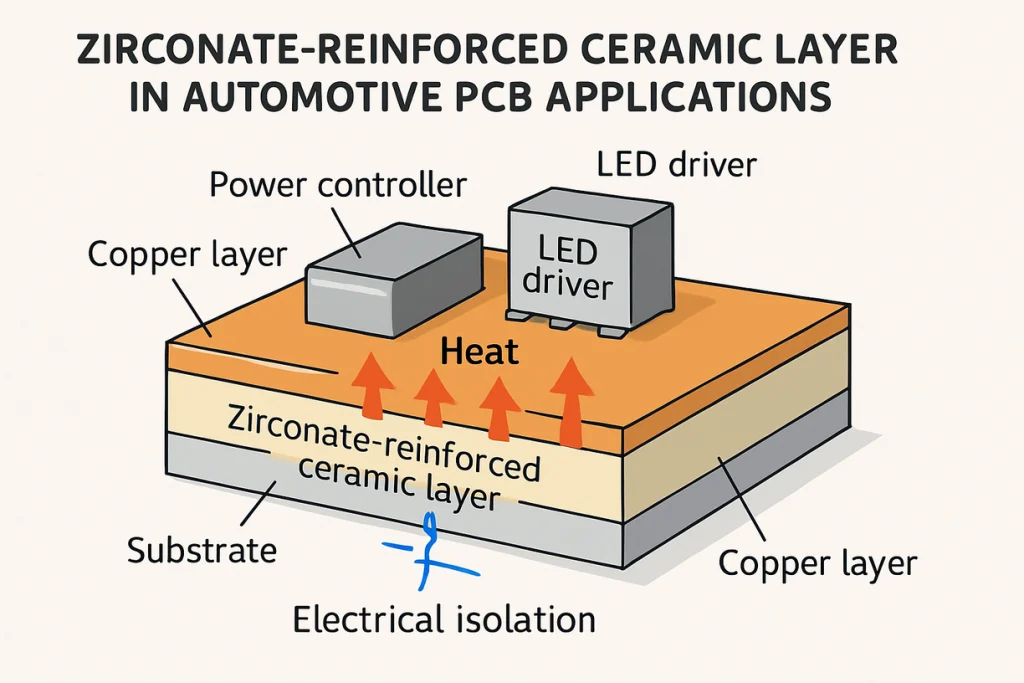
It plays a critical role in:
- High-frequency capacitors used in 5G modules
- Sintered ceramic substrates for radar and sensor units
- Dielectric coatings for industrial power ICs
OEMs in telecom, automotive electronics, and power transmission sectors rely on it to keep their hardware functioning in hostile conditions.
Miniaturization is another reason for its popularity. Zirconium silicate enables thin-film stability without compromising dielectric performance. That means smaller, denser, and cooler-running components that don’t crack under heat. With 5G and edge comp—especially relevant in the era of edge computing and EV
Component | Function of Zirconium Silicate |
---|---|
Sintered Substrates | Heat stability and dielectric control |
IC Package Coatings | Barrier against oxidation |
LED Driver Boards | Withstands thermal fatigue |
Radar Modules | Maintains signal fidelity |
Processing Zirconium Silicate for Peak Performance: Purity, Particle Control & Sintering
Consistency isn’t optional. It’s mandatory. Without reliable processing, even the best material becomes a liability.
Here’s what matters. Particle size and purity play a huge role. Zirconium silicate for electronics must be highly pure (≥99%) and have consistent particle size (<2 µm). If not, micro-cracks form under heat, leading to insulation failure or component drift.

Top manufacturers use hydrothermal or spray granulation to produce uniform grains. These go through:
- Calcination at ~1000°C for phase stability
- Sintering in N₂ or Ar atmospheres to lock in dielectric behavior
Methods like hydrothermal synthesis and spray granulation help maintain narrow particle distribution. Add precision sintering and controlled atmosphere kilns, and you’ve got a process that repeats quality every single batch.
This is where it gets serious… Any inconsistency in particle shape or binder content during processing can increase failure rates in high-end electronics by 30–50%.
A Japanese IC firm shared data showing that inconsistent particle distribution (CV >15%) increased thermal failures by 33% in their LED driver packaging.
Processing Stage | Control Parameter | Purpose |
---|---|---|
Milling & Sieving | <2 µm uniformity | Prevents agglomeration |
Calcination | Phase control | Ensures crystal integrity |
Atmosphere Control | Inert gases (N₂, Ar) | Avoids oxidation of active sites |
Binder Removal | <1% residue | Reduces porosity in sintered parts |
Why OEMs and Engineers Choose Zirconium Silicate for Mission-Critical Electronics
Let’s talk numbers. For large-scale electronics, it’s not just cost per kilo—it’s cost per failure.
Here’s the business case. Zirconium silicate reduces TCO by minimizing field failures, service downtime, and return rates. If your product is part of a mission-critical system—whether in telecom, defense, or EV—this ceramic works like an invisible shield. That alone makes it attractive
In tests by a German aerospace supplier, PCBs using zirconium silicate-enhanced insulation survived 1,200+ thermal cycles without dielectric breakdown, versus ~700 with barium titanate-based formulations.
Buyer Priority | How Zirconium Silicate Delivers |
---|---|
Reliability | High thermal and dielectric stability |
Compliance | RoHS-ready, non-toxic |
Cost-Efficiency | Lowers failure rates and return costs |
Availability | Global supply with stable pricing |
Buyers in B2B sectors—especially those handling mission-critical components—need materials with data to back up claims. And zirconium silicate delivers. Lab trials show it handles 1,000+ thermal cycles without structural compromise.
You might be wondering… is it scalable? Absolutely. Its production footprint supports mass manufacturing without disrupting process lines. It blends easily with existing ceramic matrices.
The Hidden Challenges of Zirconium Silicate—and How to Solve Them
No material is perfect. Zirconium silicate has its caveats. It brings a few hurdles—especially in scaling and process safety.
Main issues:
- Dust generation: Fine particles may cause respiratory irritation.That means handling protocols, vacuum systems, and proper PPE must be part of plant operations.
- Batch variability: Some suppliers have inconsistent grain or binder content.High-purity grades aren’t available from every vendor. B2B buyers must evaluate mining origin, processing steps, and distribution consistency.
- Processing complexity: It requires specialized kilns and atmosphere control.
Solution: Closed transfer systems, supplier audits, and XRD-based verification protocols.
Case in point: A European electronics supplier reported 20% shrinkage defects from a supplier switch. Why? Inconsistent grain structure from a non-certified refinery.
Challenge | Mitigation Strategy |
---|---|
Dust Hazard | Use vacuum feeders, HEPA filtration |
Supplier Variability | Enforce QC and batch traceability |
Material Verification | Use particle sizing and purity scans |
Sourcing Zirconium Silicate: How to Avoid Defects and Ensure Purity
Sourcing matters just as much as processing.Sourcing can make or break product performance. Here’s how to get it right.
Rule #1: Always ask for COA + SDS (certificate of analysis + safety data sheet). Look for ≥99% purity, <0.1% moisture, and consistent morphology.
Rule #2: Work with suppliers that:
- Offer technical guidance for integration
- Have traceability across mines, milling, and shipping
- Support sintering tests and pilot batch analysis
- Talk to their engineers. Ask about sintering behavior, batch uniformity, and post-processing support.
For large-scale OEMs, partner with suppliers who offer technical consultation. Those who help fine-tune your formulation can prevent product recalls down the road.
Sourcing Criteria | What to Check |
---|---|
Purity Level | ≥99% zircon |
Particle Size Consistency | <2 µm, low CV (<10%) |
Batch Traceability | Full digital tracking, ISO compliance |
What’s Next for Zirconium Silicate? Nano Ceramics, 5G, and EV Innovations
The electronics industry is evolving fast—and zirconium silicate is keeping pace.
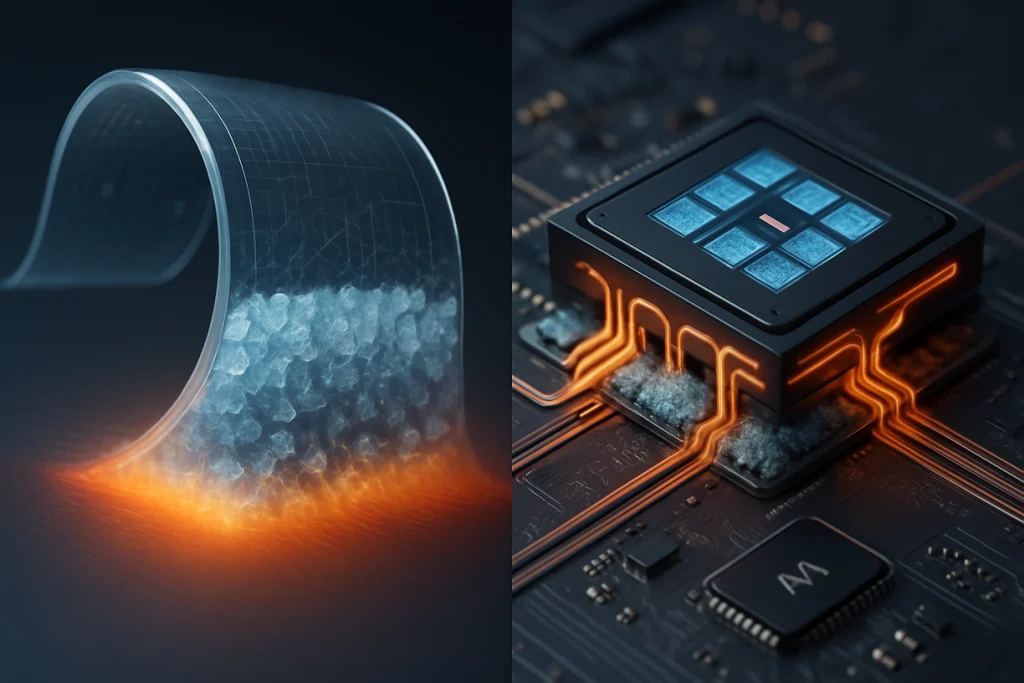
Let’s zoom in. With electrification and 5G accelerating, manufacturers need materials that hold up under RF load and thermal spikes.
Emerging innovations:
- Nano-formulated zirconium silicate in AI accelerators
- Hybrid composites for EV battery modules
- Flexible ceramic films for rollable and wearable electronics
Bonus? It’s environmentally safe—inert, non-toxic, and recyclable—making it ideal for green electronics packaging and next-gen manufacturing.
Sustainability is another driver. Zirconium silicate is inert, recyclable, and doesn’t emit hazardous byproducts during processing.
And here’s a forward-thinking tip… Watch for nano-engineered zirconium silicates with tuned dielectric values and hybrid composite compatibility. This space is evolving fast.
Emerging Trend | Application Area |
---|---|
Nano-formulations | 5G substrates, AI chip coatings |
Green Ceramics | Low-emission electronics packaging |
Multi-material Hybrids | EV thermal management units |
FAQ Section
Q1: What is zirconium silicate?
Zirconium silicate is a high-performance ceramic material characterized by its excellent thermal and dielectric stability. This versatile compound is often utilized in various applications, including electronics, coatings, and structural components. Its unique properties make it suitable for environments where high temperatures and electrical insulation are critical. In its powdered form, zirconium silicate can also serve as a reinforcing agent in composite materials, enhancing mechanical strength and durability.
Q2: How does zirconium silicate improve reliability in electronics?
Zirconium silicate contributes significantly to the reliability of electronic components by minimizing issues such as cracking, dielectric drift, and oxidation, particularly in high-heat or high-frequency environments. Its stable thermal properties ensure that electronic devices can operate efficiently without structural failure, while its low dielectric constant minimizes signal loss and interference. Additionally, zirconium silicate’s resistance to thermal shock means that it can withstand rapid temperature changes without compromising performance, making it an ideal choice for demanding electronic applications.
Q3: Which electronic components use zirconium silicate?
Zirconium silicate is commonly used in a variety of electronic components, including capacitors, substrates, integrated circuit (IC) coatings, and printed circuit boards (PCBs). Its high dielectric strength and thermal stability make it especially valuable in sectors such as telecommunications, automotive, and aerospace. In telecommunications, for example, zirconium silicate enhances the performance of components involved in high-frequency signal transmission. In automotive and aerospace industries, it ensures the reliability and longevity of critical electronic systems subjected to harsh operating conditions.
Q4: Is zirconium silicate safe to use?
Yes, it is generally considered safe for use, provided that proper handling and dust control measures are implemented during processing. It complies with various safety regulations, including the Restriction of Hazardous Substances (RoHS) directive, which limits hazardous materials in electronic equipment. Additionally, zirconium silicate has been evaluated for health and safety in regulatory frameworks worldwide, ensuring that it meets stringent safety standards. Users are encouraged to follow best practices for material handling to minimize exposure to dust, as inhalation of fine particles can pose health risks.
Q5: What should buyers check when sourcing zirconium silicate?
When sourcing zirconium silicate, buyers should pay attention to several critical factors:
● Purity: Higher purity levels lead to improved material performance. Buyers should seek products with minimal impurities that could affect electrical and thermal properties.
● Particle Size: The particle size of zirconium silicate can impact its application. Smaller particles provide better surface area for bonding and insulation, while larger particles may be preferable for certain bulk applications.
● Moisture Content: Excess moisture can degrade the performance of zirconium silicate in various applications. It’s essential to verify low moisture levels to ensure optimal performance.
● Traceability: Having a clear traceability record allows buyers to ensure that the material meets quality standards and can be tracked through the supply chain.
● Processing Compatibility: Buyers should confirm that the zirconium silicate product is compatible with their specific manufacturing processes, whether it involves mixing, coating, or sintering, to guarantee successful integration into their systems.
By thoroughly evaluating these factors, buyers can ensure that they select high-quality zirconium silicate that meets their technical requirements and application needs.