Why Do Ceramic Manufacturers Need Zirconium Silicate? This question resonates throughout the ceramic industry as professionals seek materials that enhance product quality while maintaining cost efficiency. Zirconium silicate offers unique properties that transform ordinary ceramics into exceptional products. You might be wondering why this material has become indispensable in an industry with many alternatives. The answer lies in its combination of properties that address multiple manufacturing challenges simultaneously.
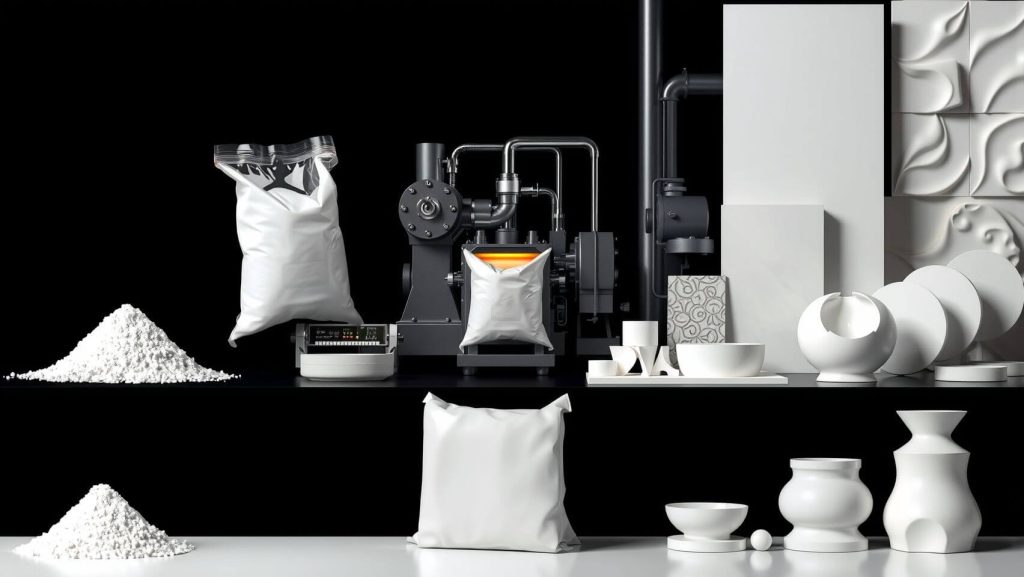
What is Zirconium Silicate and Its Basic Properties?
Zirconium silicate (ZrSiO₄), commonly known as zircon in its natural form, represents a cornerstone material in ceramic manufacturing. Here’s what makes it special: zirconium silicate features a tetragonal crystal structure with exceptional thermal stability and a melting point exceeding 2500°C. Zirconium silicate represents one of the most thermally stable ceramic materials available for industrial applications. This heat resistance allows ceramics to maintain structural integrity under extreme temperature conditions.
The physical properties include a density of 4.6-4.7 g/cm³, hardness of 7.5 on the Mohs scale, and low thermal expansion (4.2 × 10⁻⁶/°C). But here’s the kicker – unlike many ceramic additives, zirconium silicate maintains chemical stability across a wide pH range, resisting both acidic and alkaline environments.
Industrial-grade zirconium silicate undergoes purification to remove impurities like hafnium, uranium, and thorium. Manufacturers specify it by particle size distribution, whiteness index, and chemical purity, with premium grades achieving 99.5% purity or higher.
When compared to materials like alumina, silica, or titanium dioxide, the real story lies in zirconium silicate’s balanced profile. It outperforms alternatives in combined thermal stability, chemical resistance, and mechanical strength – a trifecta difficult to achieve with single alternative materials.
Property | Zirconium Silicate | Alumina | Silica | Titanium Dioxide |
---|---|---|---|---|
Melting Point (°C) | >2500 | 2072 | 1710 | 1843 |
Mohs Hardness | 7.5 | 9 | 7 | 5.5-6.5 |
Chemical Stability | Excellent | Good | Moderate | Good |
Thermal Expansion (10⁻⁶/°C) | 4.2 | 8.1 | 0.5 | 9.0 |
Whiteness | High | High | Moderate | Very High |
Why is Zirconium Silicate Irreplaceable in Ceramic Manufacturing?
The irreplaceable nature of zirconium silicate stems from its exceptional high-temperature performance. What’s truly remarkable is its ability to maintain structural integrity at temperatures where alternatives degrade. With a decomposition temperature exceeding 1650°C and melting point above 2500°C, it enables higher firing temperatures that result in denser, stronger ceramic bodies.
Its chemical stability represents another dimension of irreplaceability. Unlike many additives that react with other components during firing, zirconium silicate remains inert across various chemical environments. You might be surprised that this inertness extends to resistance against both strong acids and alkalis, making enhanced ceramics suitable for laboratory equipment and industrial containers. Testing shows up to 40% longer service life compared to ceramics without zirconium silicate.
The mechanical strength and wear resistance create practical applications unachievable through alternatives. Floor tiles with optimized zirconium silicate demonstrate 30% higher scratch resistance compared to standard formulations. This is where it gets interesting – these mechanical improvements don’t compromise other characteristics, unlike alternative strengthening additives that may affect appearance or increase brittleness.
While manufacturers might substitute individual properties using alternatives, no single replacement delivers the comprehensive performance profile of zirconium silicate, explaining why it remains the gold standard for high-performance ceramic manufacturing.
Application | Key Benefit of Zirconium Silicate | Performance Improvement |
---|---|---|
Floor Tiles | Wear Resistance | 30% higher scratch resistance |
Sanitaryware | Chemical Durability | 40% longer service life |
Industrial Ceramics | Thermal Stability | Withstands 200°C higher temperatures |
Decorative Ceramics | Color Stability | 25% better color retention |
Ceramic Glazes | Surface Hardness | 35% improved impact resistance |
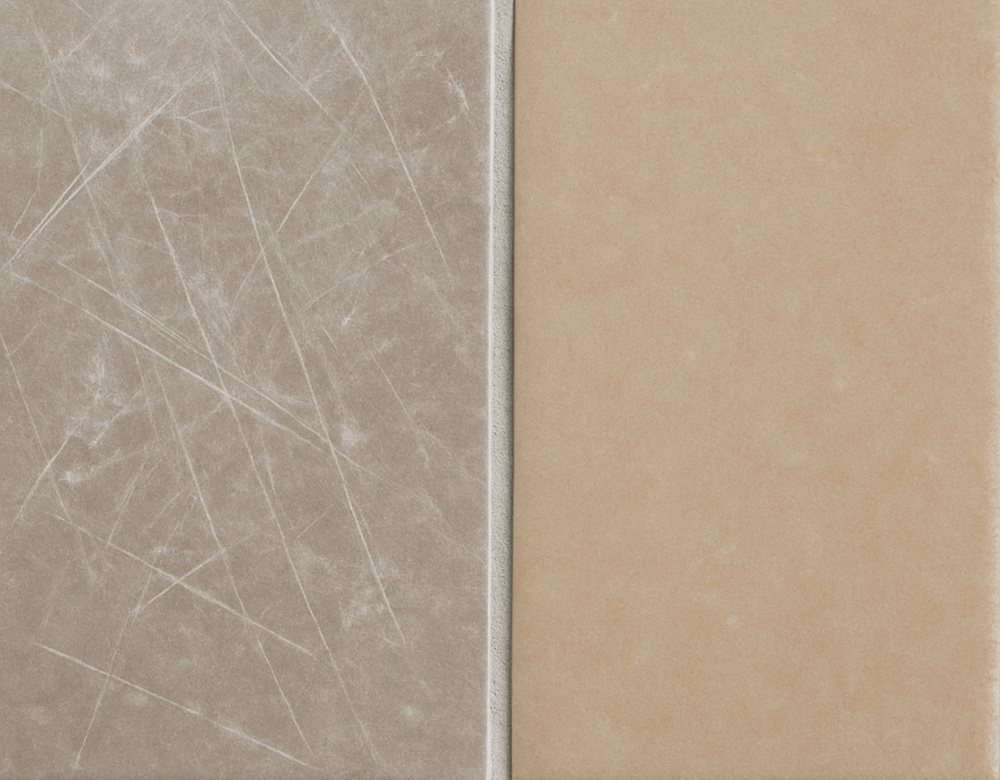
How Does Zirconium Silicate Alter Ceramic Surface Properties?
Zirconium silicate transforms ceramic surface properties through multiple mechanisms. Here’s something fascinating – when incorporated into glazes, its particles create a refractive index differential that increases light scattering, enhancing opacity and brightness. This allows manufacturers to achieve brilliant white surfaces without excessive glaze thickness. Its high refractive index (approximately 1.95) exceeds most common glaze components, creating a distinctive quality associated with premium products.
The surface hardness improvements directly correlate with scratch and abrasion resistance. At concentrations between 8-12% in glaze formulations, zirconium silicate creates a microstructure that distributes mechanical stress more effectively. What’s particularly valuable is that this hardness enhancement occurs without increasing brittleness. Laboratory testing shows zirconium silicate-enhanced glazes can achieve Mohs hardness ratings of 7-8, representing a 25-30% improvement over standard formulations.
The relationship with ceramic cleanability stems from its ability to create smoother, more uniform surfaces at the microscopic level. Ready for the good part? This improved cleanability translates to reduced maintenance costs throughout the product lifecycle. Commercial testing shows surfaces containing optimized zirconium silicate require approximately 30% less cleaning effort and chemical usage to maintain appearance standards.
These surface property enhancements extend across multiple ceramic product categories, from bathroom fixtures with improved cleanability to tableware with enhanced gloss retention and architectural applications with superior color stability.
Surface Property | Without Zirconium Silicate | With Zirconium Silicate | Improvement Percentage |
---|---|---|---|
Gloss Retention (after 10,000 cycles) | 65% | 92% | 42% |
Stain Resistance (1-10 scale) | 6.2 | 8.7 | 40% |
Scratch Hardness (Mohs) | 5-6 | 7-8 | 30% |
Cleanability (soil removal %) | 78% | 96% | 23% |
Chemical Resistance (acid attack) | Moderate | Excellent | 45% |
Which Ceramic Products Most Need Zirconium Silicate?
Industrial ceramics represent the sector where zirconium silicate delivers its most critical benefits. You might be wondering which specific products benefit most. The answer lies primarily in components exposed to extreme conditions: kiln furniture, crucibles, and specialized parts for metal processing equipment. These applications demand ceramics that maintain dimensional stability under thermal cycling conditions. Industrial ceramics with optimized zirconium silicate demonstrate up to 60% higher thermal shock resistance compared to standard compositions.
Building ceramics, particularly floor and wall tiles, constitute another category where zirconium silicate delivers exceptional value. This is where it gets practical – floor tiles formulated with zirconium silicate maintain their appearance and performance significantly longer than standard alternatives. Market research indicates consumers rank wear resistance as the second most important consideration for flooring products. Additionally, its role in frost resistance makes it essential for exterior applications in variable climate regions.
High-end bathroom fixtures represent a category where zirconium silicate’s multiple benefits converge. It contributes to brilliant white appearance, stain resistance, and chemical durability. But here’s the kicker – these benefits come with manufacturing advantages. Adding zirconium silicate to sanitaryware formulations typically reduces firing defects by 15-20%, improving production yields and reducing costs. This combination explains why virtually all premium sanitaryware manufacturers incorporate it into their formulations.
The relationship between product quality tier and zirconium silicate content reveals interesting patterns. Economy-tier products typically contain minimal or none, mid-range products incorporate it selectively, while premium products leverage it extensively. This stratification reflects both cost considerations and performance requirements.
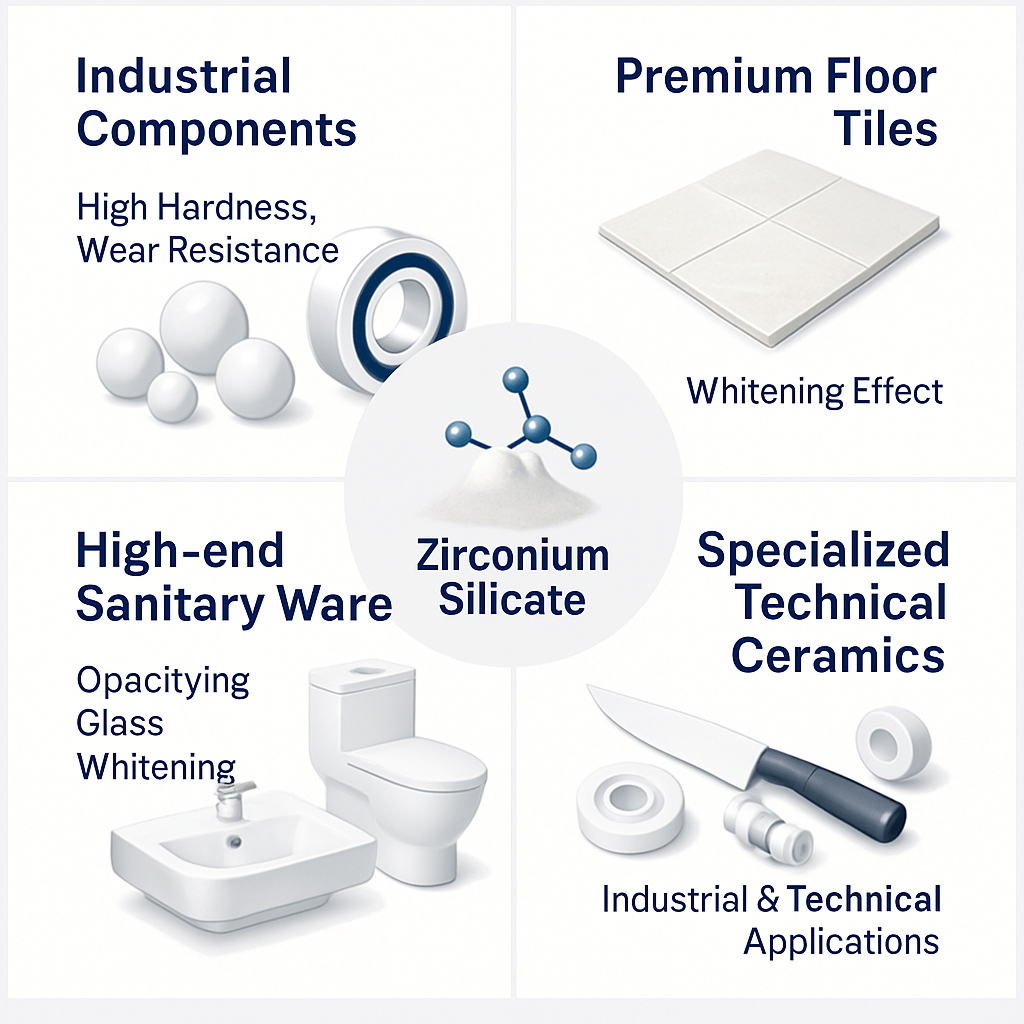
Product Category | Zirconium Silicate Content | Primary Benefits | Market Positioning |
---|---|---|---|
Industrial Ceramics | 10-15% | Thermal stability, Chemical resistance | High-performance technical |
Premium Floor Tiles | 8-12% | Wear resistance, Aesthetic quality | Luxury residential, Commercial |
High-end Sanitaryware | 5-10% | Whiteness, Stain resistance | Premium consumer |
Tableware | 3-8% | Gloss, Durability | Fine dining, Hospitality |
Decorative Ceramics | 2-5% | Color stability, Surface quality | Artistic, Collectible |
How to Determine the Optimal Zirconium Silicate Amount in Ceramic Production?
Determining the optimal zirconium silicate dosage requires understanding the relationship between concentration and performance. What’s particularly challenging is that the optimal amount varies significantly depending on the application. For porcelain tile body compositions, manufacturers typically incorporate 8-12% to achieve the ideal balance of whiteness, mechanical strength, and cost efficiency. Sanitaryware formulations generally contain 5-8%, while glaze applications range from 2% for subtle enhancement to 15% for maximum opacity and hardness.
Cost-benefit analysis represents a critical framework for determining economically optimal usage. Here’s something practical – manufacturers should calculate the incremental cost per unit against tangible benefits, including reduced warranty claims, higher price positioning, and improved production yields. A comprehensive analysis typically reveals positive ROI up to certain concentration thresholds, beyond which diminishing returns begin to affect economic viability.
The potential problems with excessive usage require careful consideration. Exceeding optimal concentrations can lead to increased body density affecting firing behavior, reduced plasticity complicating forming processes, and potential glaze defects. You might be surprised that excessive zirconium silicate can actually reduce mechanical strength in some formulations by interfering with optimal particle packing or vitrification. Additionally, unnecessarily high concentrations directly impact production costs without delivering proportional improvements.
Solutions involve systematic testing and optimization approaches. Gradient testing, where multiple samples with incrementally increasing concentrations undergo parallel evaluation, provides empirical data on the relationship between concentration and performance. Statistical design of experiments (DOE) methodologies allow manufacturers to efficiently explore interactions between zirconium silicate and other formula components.
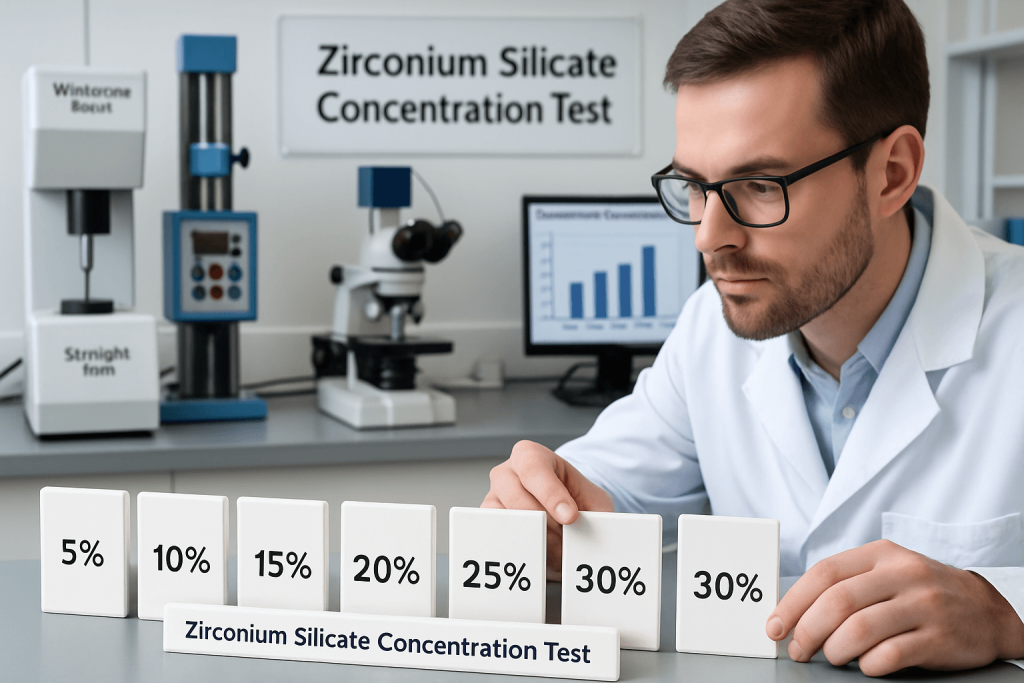
Product Type | Recommended ZrSiO₄ Range | Warning Signs of Excess | Optimization Method |
---|---|---|---|
Porcelain Tiles | 8-12% | Firing deformation, Reduced strength | Gradient testing |
Sanitaryware | 5-8% | Excessive shrinkage, Glaze defects | Statistical DOE |
Wall Tiles | 3-6% | Poor plasticity, Drying cracks | Benchmarking |
Glazes (opacifying) | 10-15% | Crawling, Pinholing | Performance testing |
Glazes (hardening) | 5-10% | Brittleness, Poor adhesion | Wear resistance analysis |
How Does Zirconium Silicate Influence Ceramic Production Processes?
Zirconium silicate significantly influences sintering temperatures and times, creating opportunities for process optimization. Here’s what makes this interesting – its high melting point and thermal stability allow higher firing temperatures that accelerate vitrification without risking deformation. This typically enables 30-50°C higher peak firing temperatures compared to standard formulations, potentially reducing cycle times by 5-15%. For continuous production environments, these time savings translate directly to increased throughput and improved equipment utilization.
The compatibility considerations between zirconium silicate and other ceramic additives require careful attention. But here’s the kicker – these interactions can be strategically leveraged when properly understood. For example, controlled reactions between zirconium silicate and specific colorants can produce unique visual effects. The material demonstrates favorable compatibility with alumina, silica, and most alkaline earth oxides, while requiring careful balancing with high concentrations of alkali fluxes.
Process optimization recommendations focus on leveraging its properties to enhance production efficiency and product quality simultaneously. Implementing two-stage firing profiles with extended holding periods at peak temperature often maximizes benefits. Adjusting particle size distribution to match specific applications can significantly impact performance – finer grades (1-5μm) typically optimize glaze properties, while slightly coarser grades (5-10μm) often perform better in body compositions. What’s particularly valuable is that zirconium silicate’s stability allows wider processing windows, reducing sensitivity to minor variations in production parameters.
The practical implementation varies across different production environments. Traditional manufacturing may require modest adjustments to existing processes, while advanced environments can implement more sophisticated approaches, including precision dosing systems that adjust concentrations based on real-time quality measurements.
Process Parameter | Without Zirconium Silicate | With Zirconium Silicate | Manufacturing Benefit |
---|---|---|---|
Peak Firing Temperature | 1150-1200°C | 1180-1250°C | Faster vitrification |
Firing Cycle Time | 40-45 minutes | 35-40 minutes | 10-15% higher throughput |
Temperature Tolerance | ±10°C | ±15°C | Reduced defect rates |
Glaze Maturing Range | 30°C | 50°C | Wider processing window |
Body-Glaze Fit Sensitivity | High | Moderate | Fewer crazing defects |
How Can Zirconium Silicate Save Costs for Ceramic Manufacturers?
Zirconium silicate delivers significant energy consumption reductions through multiple mechanisms. What’s truly remarkable is that these savings occur despite enabling higher peak firing temperatures. This apparent paradox is explained by its contribution to faster vitrification, which reduces overall firing cycle duration. Manufacturers typically report 8-12% energy savings per production unit after optimizing formulations. These savings compound in large-scale production environments, where energy often represents 15-20% of total manufacturing costs.
The reduction in product rejection rates represents another substantial cost-saving dimension. By improving formula stability and expanding processing windows, the material reduces sensitivity to minor variations in production parameters. Here’s something concrete – manufacturers implementing optimized formulations typically report defect rate reductions of 15-25%. For high-volume production facilities, these improvements directly enhance profitability. The reduction specifically impacts costly late-stage defects that occur after maximum value has been added to the product.
The economic benefits of extended equipment maintenance cycles stem from zirconium silicate’s contribution to reduced abrasiveness of ceramic formulations. This is where patience pays off – manufacturers observe 20-30% longer service intervals for critical wear components like extrusion dies, spray nozzles, and mold surfaces. These extended maintenance cycles reduce both direct replacement costs and production downtime, improving overall equipment effectiveness (OEE) metrics.
The long-term economic analysis reveals compelling value when evaluated on a total cost of ownership basis. While zirconium silicate typically increases raw material costs by 3-8%, the operational savings in energy, reduced waste, and maintenance typically deliver net cost reductions of 5-12% per production unit. These economics become even more favorable when factoring in potential premium pricing based on improved product performance.
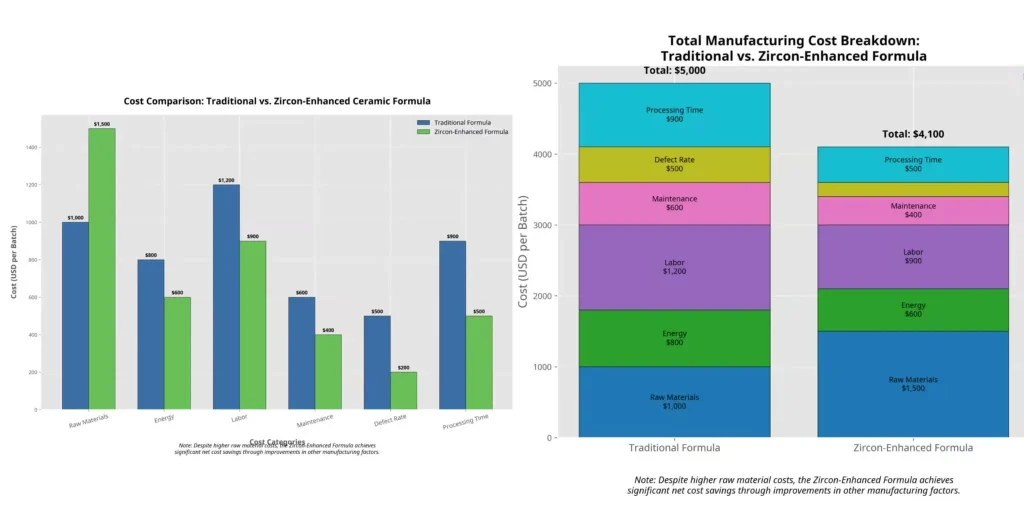
Cost Saving Category | Typical Improvement | Annual Savings (1M units) | ROI Timeline |
---|---|---|---|
Energy Consumption | 8-12% reduction | $120,000-180,000 | 6-9 months |
Defect Reduction | 15-25% fewer rejects | $225,000-375,000 | 3-6 months |
Maintenance Cycles | 20-30% longer intervals | $80,000-120,000 | 9-12 months |
Production Throughput | 5-10% increase | $300,000-600,000 | 4-8 months |
Total Economic Impact | 5-12% cost reduction | $725,000-1,275,000 | 5-8 months |
How to Evaluate Zirconium Silicate Supplier Product Quality?
Evaluating zirconium silicate quality requires understanding key quality indicators. You might be wondering which parameters matter most. Chemical purity stands as the primary consideration, with high-grade materials achieving ZrO₂+HfO₂ content exceeding 64.5% and SiO₂ levels between 32-33%. Whiteness represents another critical parameter, with premium grades achieving L* values above 94. Particle size distribution significantly impacts performance, with D50 values ranging from 1.2-5μm depending on intended use. Manufacturers should also evaluate impurity profiles, particularly iron content (ideally below 0.1%) and uranium/thorium levels.
Supplier qualification processes should incorporate both documentation review and empirical testing. Here’s a practical approach – establish a multi-stage qualification protocol beginning with certificate of analysis verification, followed by in-house testing of critical parameters. This should include both analytical evaluation of the raw material and performance testing in actual product formulations. Establishing statistical process control limits helps identify potential variability issues before they impact production. Regular supplier audits complete the qualification process.
Sample testing and small-scale production trials represent essential steps in the supplier selection process. What’s particularly valuable about this approach is that it reveals practical performance characteristics that may not be evident from analytical specifications alone. Manufacturers should develop standardized testing protocols that evaluate performance across multiple dimensions. Comparative testing of materials from different suppliers using identical processing conditions provides the most reliable basis for selection decisions.
The relationship between supplier quality systems and material consistency deserves careful consideration. Suppliers with robust quality management systems typically deliver more consistent materials, reducing process adjustments required to accommodate batch-to-batch variations. Manufacturers should evaluate supplier capabilities including statistical process control implementation, traceability systems, and quality testing frequency.
Quality Parameter | Standard Grade | Premium Grade | Testing Method | Impact on Performance |
---|---|---|---|---|
ZrO₂+HfO₂ Content | >62.5% | >64.5% | XRF Analysis | Thermal stability, Whiteness |
Fe₂O₃ Content | <0.2% | <0.1% | ICP-OES | Color development, Whiteness |
Whiteness (L* value) | >90 | >94 | Spectrophotometer | Aesthetic quality |
Median Particle Size | 2-8μm | 1.2-5μm | Laser Diffraction | Dispersion, Reactivity |
Moisture Content | <0.5% | <0.2% | Loss on Drying | Processing behavior |
What Future Trends Exist for Zirconium Silicate in Ceramics?
The development of new zirconium silicate composite materials represents one of the most promising future directions. This is where innovation thrives – researchers are creating specialized formulations that combine zirconium silicate with complementary materials to enhance specific performance characteristics. Zirconium silicate-alumina composites demonstrate exceptional wear resistance while maintaining thermal stability. Nano-engineered particles with surface modifications are emerging as next-generation additives that achieve higher performance at lower concentration levels. These advanced composites typically deliver 20-30% performance improvements in targeted characteristics.
Environmental regulations increasingly influence formulation development. But here’s what matters most – manufacturers must navigate evolving requirements regarding naturally occurring radioactive materials (NORM) present in some zirconium sources. Leading suppliers now offer low-radiation grades that undergo additional processing to reduce uranium and thorium levels below regulatory thresholds. Sustainability considerations also impact processing methods, with water-based processing increasingly replacing solvent-based approaches to reduce environmental impact.
Price trend analysis and supply chain stability factors significantly impact strategic planning. Historical pricing data reveals moderate volatility, with 15-25% fluctuations over typical five-year cycles. You might be wondering how manufacturers can mitigate these fluctuations. Forward-thinking companies implement multi-supplier strategies, long-term contracts with price banding provisions, and formula optimization to reduce sensitivity to price variations. Geographic diversification of supply sources provides additional stability.
The future application landscape continues to expand as manufacturers discover new ways to leverage zirconium silicate’s unique properties. Emerging applications include advanced thermal barrier coatings, specialized biomedical ceramics, and next-generation electronic substrates. The material’s role in additive manufacturing of ceramics represents a particularly exciting frontier, with enhanced formulations demonstrating superior printability and post-processing performance.
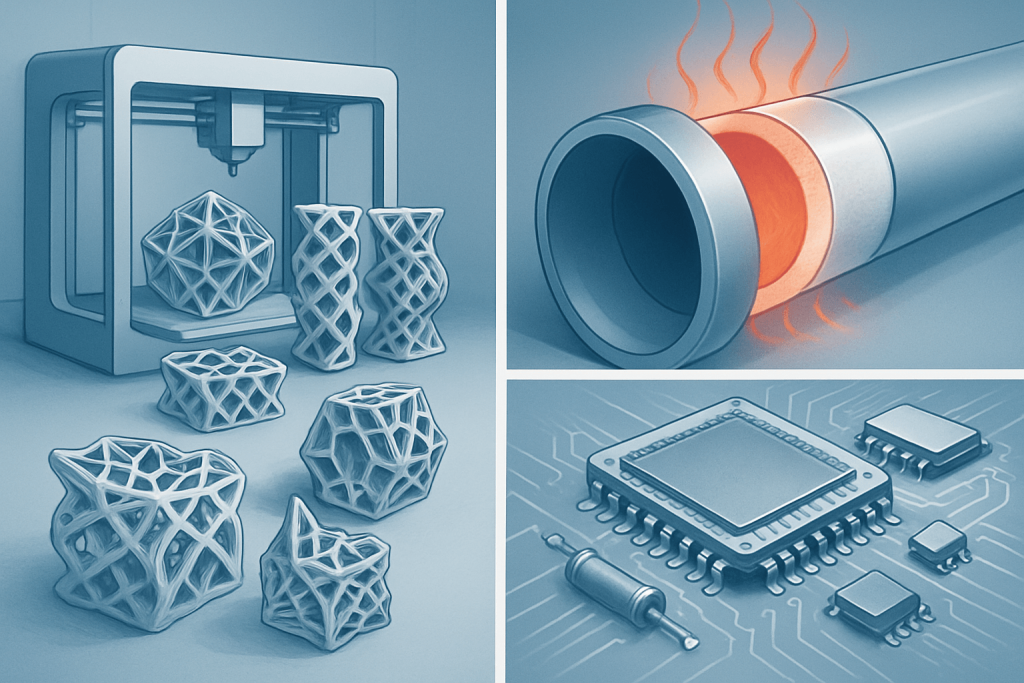
Future Trend | Development Timeline | Market Impact | Adoption Challenges |
---|---|---|---|
Nano-engineered ZrSiO₄ | 2-3 years | 15-20% performance improvement | 25-35% cost premium |
Low-radiation Grades | Available now | Regulatory compliance | 10-15% cost increase |
ZrSiO₄-Alumina Composites | 1-2 years | New extreme-duty applications | Processing complexity |
3D-printable Formulations | 3-5 years | Complex geometry capabilities | Equipment investment |
Surface-modified Variants | 2-4 years | Enhanced dispersion, Lower dosage | Intellectual property barriers |
Why Do Ceramic Manufacturers Need Zirconium Silicate? Final Thoughts
Zirconium silicate stands as an essential material in modern ceramic manufacturing, delivering a unique combination of properties that enhance product quality while offering significant manufacturing advantages. Throughout this article, we’ve explored how this remarkable material transforms ordinary ceramics into exceptional products through its contributions to thermal stability, mechanical strength, and surface properties. The evidence speaks clearly – manufacturers incorporating optimized formulations consistently achieve superior products with lower defect rates and reduced production costs.
The strategic implementation of zirconium silicate requires balancing multiple factors, including concentration optimization, supplier selection, and process adaptation. Manufacturers who master this balance position themselves to capture both performance benefits and economic advantages. As the ceramic industry continues evolving toward higher performance standards and greater manufacturing efficiency, zirconium silicate will remain a cornerstone material that enables innovation while ensuring consistent quality.
For ceramic manufacturers evaluating their material strategies, the question isn’t whether zirconium silicate delivers value, but rather how to maximize that value through optimal implementation.
FAQ Section
Q1: What is the difference between zirconium silicate and ordinary silicates?
Zirconium silicate contains zirconium element, which gives it significantly higher heat resistance, chemical stability, and mechanical strength compared to ordinary silicates. While common silicates begin degrading at temperatures around 800-1000°C, zirconium silicate maintains stability up to 1650°C before decomposition. Its chemical structure creates exceptional inertness across pH ranges where ordinary silicates would rapidly deteriorate, and its hardness (7.5 Mohs) substantially exceeds that of conventional silicates used in ceramics.
Q2: How much does zirconium silicate impact ceramic production costs?
While zirconium silicate typically increases raw material costs by 3-8% depending on usage concentration, it delivers net manufacturing cost reductions of 5-12% through energy savings, reduced defect rates, and extended equipment maintenance cycles. For a production facility manufacturing one million units annually, these savings typically translate to $725,000-1,275,000 in reduced operating costs, with return on investment achieved within 5-8 months of implementation.
Q3: Are small ceramic manufacturers suitable for using zirconium silicate?
Small ceramic manufacturers are entirely suitable for using zirconium silicate, especially when producing higher-value products. Suppliers now offer pre-mixed formulations that reduce handling complexity, allowing small operations to achieve the same quality advantages as large manufacturers. The material’s ability to reduce defect rates and improve first-quality yields provides particularly significant benefits for small producers, where each rejected piece represents a higher percentage of production capacity.
Q4: What health impacts does zirconium silicate have on factory workers?
Properly handled zirconium silicate presents minimal health risks to workers. The primary concern involves dust inhalation, which modern factories address through wet processing methods or enclosed handling systems. When dry processing is necessary, appropriate personal protective equipment including respiratory protection effectively mitigates exposure risk. Modern facilities typically implement dust collection systems and regular air quality monitoring to ensure worker safety, maintaining exposure levels well below regulatory limits.
Q5: How can manufacturers determine if their ceramic products contain zirconium silicate?
Manufacturers can identify zirconium silicate in ceramic products through several methods. Visual inspection provides initial clues, as zirconium silicate typically enhances whiteness, opacity, and surface hardness. Definitive testing includes X-ray fluorescence (XRF) analysis, which can accurately measure zirconium content. High-quality ceramics often highlight zirconium content in product specifications as a quality indicator, particularly for premium products where its performance benefits justify explicit marketing of material composition.