In the competitive arena of global manufacturing, the relentless pursuit of superior materials dictates the pace of innovation and market leadership. You might be wondering, what truly elevates a material from a mere commodity to a strategic asset?
This article aims to unravel the compelling case for zirconium, a remarkable element rapidly ascending to this pivotal status. We will delve into its distinctive array of properties and explore its diverse applications across multiple industries.
Our primary objective is to provide a comprehensive understanding of why zirconium is not simply another element on the periodic table. Rather, it’s a foundational cornerstone for future technological breakthroughs and a key enabler in advancing global manufacturing capabilities, solidifying its role as an indispensable strategic material.
Understanding Zirconium: From Element to Essential Strategic Manufacturing Material
Zirconium, bearing the atomic number 40, is a lustrous, greyish-white transition metal that has transitioned from a relatively obscure element into a vital strategic manufacturing material in modern high-technology sectors. First identified in 1789 by Martin Heinrich Klaproth and later isolated in 1824 by Jöns Jacob Berzelius, its initial applications were sparse, partly due to the difficulties in producing it in a pure, ductile form.
However, its unique combination of exceptional corrosion resistance against acids, alkalis, and seawater, a high melting point of 1855°C (3371°F), and a notably low absorption cross-section for thermal neutrons began to capture significant industrial attention.
But here’s the kicker… it was the dawn of the nuclear age in the mid-20th century that truly illuminated zirconium’s profound strategic value. Its inherent ability to withstand extreme temperatures and highly corrosive environments without significant degradation, coupled with its near transparency to thermal neutrons, rendered it indispensable for cladding nuclear fuel rods.
Zircaloy alloys, predominantly zirconium, are meticulously engineered for these demanding nuclear applications, serving as prime examples of how targeted material science has elevated zirconium’s industrial standing. Zirconium’s transformative journey from a chemical curiosity to an essential component in global manufacturing underscores a broader paradigm: material science advancements are the bedrock of new technological frontiers.
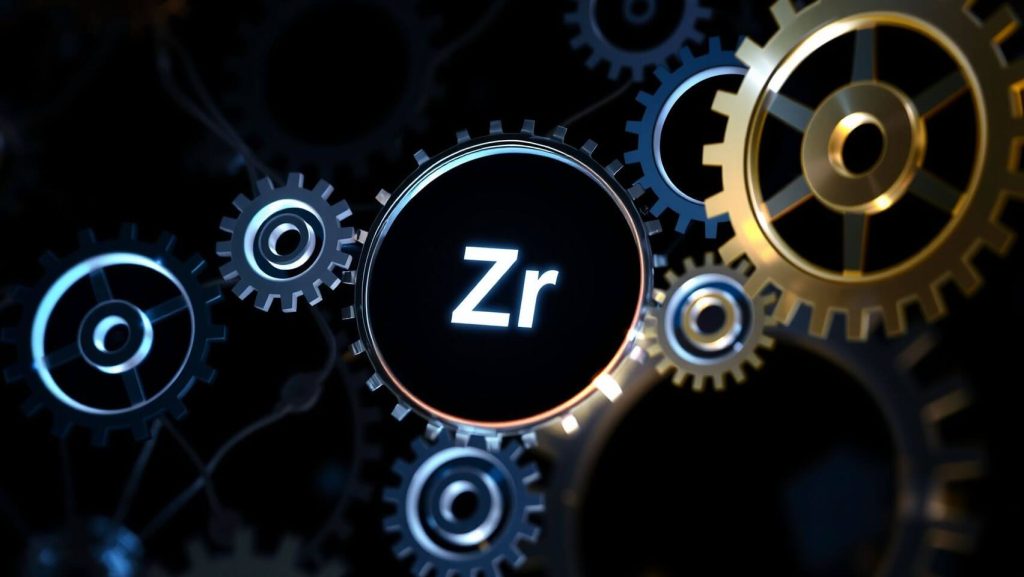
Superior Corrosion Resistance Makes Zirconium Irreplaceable
Zirconium’s status as a strategic manufacturing material stems primarily from its exceptional corrosion resistance. It forms a stable, self-healing oxide layer (ZrO₂) that protects the base metal from chemical attack.
Ready for the good part? This protective mechanism works effectively against acids, alkalis, and saline solutions. In many cases, zirconium significantly outlasts stainless steels when exposed to hot sulfuric or hydrochloric acid environments.
This remarkable durability translates directly to extended equipment life and ensures product purity in critical applications. The natural oxide layer makes zirconium ideal for applications requiring long-term reliability under harsh conditions.
Comparing Zirconium with Other Strategic Materials
Performance Metric | Zirconium | Titanium | Stainless Steel |
---|---|---|---|
Density (g/cm³) | 6.5 | 4.5 | 7.9 |
Melting Point (°C) | 1855 | 1668 | 1400-1450 |
Corrosion Resistance | Excellent | Good | Moderate |
Neutron Absorption | Very Low | Moderate | High |
Strength-to-Weight | High | Very High | Moderate |
Biocompatibility | Excellent | Excellent | Good |
Relative Cost | High | High | Moderate |
Extreme Performance Under Challenging Conditions
Zirconium maintains integrity under extreme conditions, solidifying its role as a strategic manufacturing material. This includes high temperatures, radiation, and mechanical stress.
This is where it gets interesting… In nuclear reactors, zirconium alloys (Zircaloy) endure harsh conditions while retaining strength. Low thermal neutron absorption aids reactor efficiency. In aerospace, zirconium ceramics (ZrB₂) withstand over 2000°C in rocket nozzles. This performance enables new technological efficiency and safety.
According to the World Nuclear Association, zirconium alloys are essential in nuclear reactors due to their exceptional neutron transparency and corrosion resistance.
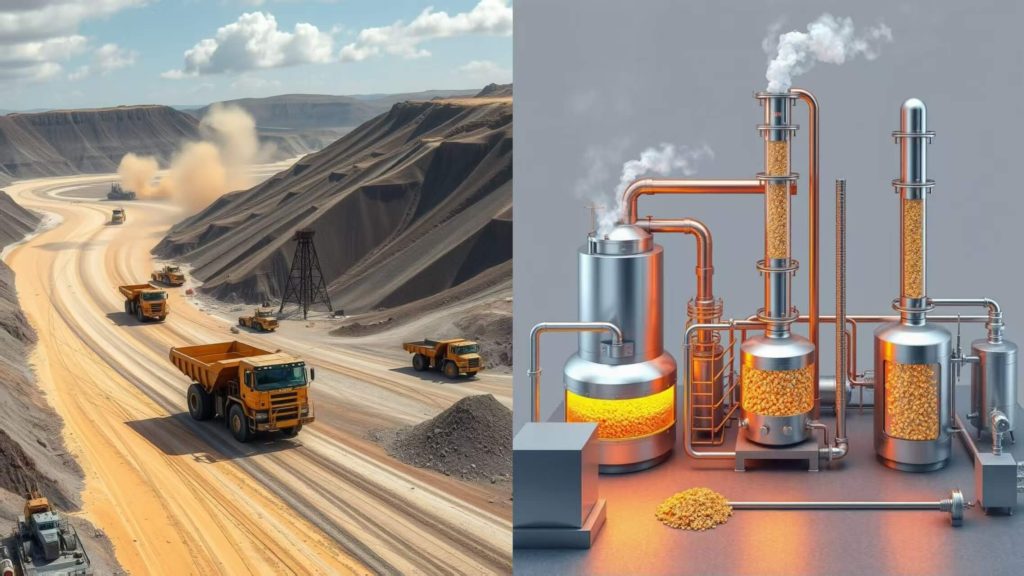
Versatile Applications Across Critical Industries
Several converging factors are currently amplifying zirconium’s role as a strategic manufacturing material. Firstly, the resurgent global interest in clean and sustainable energy sources has placed nuclear power, and by extension zirconium, back into a prominent position.
As nations worldwide strive to curtail carbon emissions, the operational reliability of nuclear reactors, which rely heavily on zirconium components, becomes paramount. Advanced reactor designs often require materials capable of withstanding extreme conditions, driving innovation in zirconium alloy development.
Secondly, aerospace and defense industries continuously seek materials offering superior strength-to-weight ratios that perform reliably under severe thermal and mechanical stresses. Zirconium alloys and ceramics increasingly find utility in rocket nozzles, jet engine parts, and thermal protection systems due to their exceptional stability.
Consider the demanding environment of a jet engine turbine; materials must endure extreme temperatures and corrosive combustion gases—a challenge for which zirconium-based materials are exceptionally well-suited.
Industry Applications Overview
Industry | Primary Applications | Key Advantages | Market Trends |
---|---|---|---|
Nuclear | Fuel rod cladding, reactor components | Low neutron absorption, corrosion resistance | Stable growth, increasing demand for new reactor designs |
Chemical | Pipes, valves, heat exchangers | Corrosion resistance, longevity | Continued growth, increasing specialty chemicals demand |
Aerospace | Engine components, thermal protection | High-temperature stability, strength | Rapid growth, new aircraft demand |
Medical | Implants, dental prosthetics | Biocompatibility, strength | Strong growth, aging population driving demand |
Electronics | Thin-film capacitors, sensors | Electrical properties, stability | Continuous innovation in applications |
Revolutionary Impact on Nuclear Energy
Zirconium has revolutionized nuclear energy, establishing itself as a critical strategic manufacturing material in this sector. Its main application is in fuel rod cladding, where it serves an essential safety and performance function.
Want to know the secret behind its success? Zirconium cladding performs exceptionally well under intense radiation, high temperatures, extreme pressure, and corrosive environments. Specialized Zircaloy alloys were specifically developed to meet these demanding requirements.
The material’s low neutron capture cross-section significantly boosts reactor efficiency, while its outstanding corrosion resistance prevents fuel rod degradation during operation. Today, Zircaloy remains the reliable industry standard, with advanced zirconium alloys continuously being developed to improve accident tolerance.
Global Zirconium Resources and Production
Country/Region | Reserve Share (%) | Annual Production (thousand tons) | Major Mining Areas |
---|---|---|---|
Australia | 32 | 500 | Murray Basin, Perth Basin |
South Africa | 21 | 400 | Richards Bay, Namakwa |
China | 9 | 140 | Guangdong, Hainan, Jiangxi |
India | 8 | 35 | Kerala, Tamil Nadu |
Ukraine | 6 | 65 | Vilnohirsk |
Other Countries | 24 | 160 | Brazil, Indonesia, Kenya, etc. |
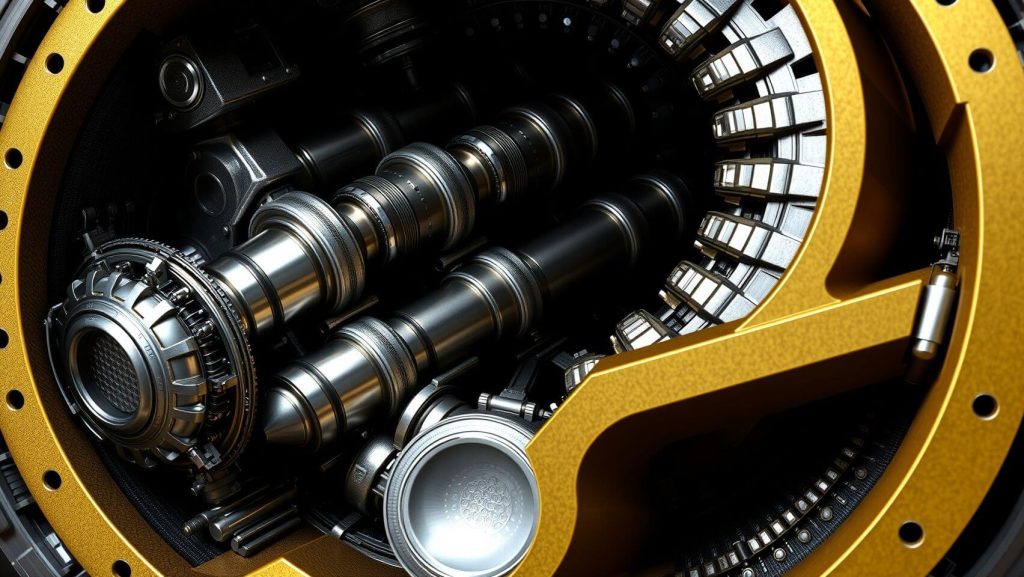
Customized Zirconium Alloys for Specialized Applications
Alloying enhances zirconium’s versatility as a strategic manufacturing material. Alloying fine-tunes properties to meet specific application requirements.
Now, let’s dive deeper… Zircaloys (with tin, iron, chromium) are key in nuclear fuel cladding, providing strength and corrosion resistance. Zr-Nb alloys (Zr-1Nb, Zr-2.5Nb) are suited for reactor pressure tubes and chemical processing applications. This customization allows zirconium to meet diverse industrial needs.
Research published by ASM International demonstrates that zirconium’s unique combination of properties makes it irreplaceable in several critical applications.
Zirconium Alloy Types and Characteristics
Alloy Type | Main Components | Characteristics | Typical Applications |
---|---|---|---|
Zr 702 | Pure Zr (>99.2%) | Excellent corrosion resistance | Chemical equipment, heat exchangers |
Zr 705 | Zr + 2.5% Nb | High strength, creep resistance | Pressure vessels, fasteners |
Zircaloy-2 | Zr + Sn, Fe, Cr, Ni | Radiation resistance, corrosion resistance | BWR fuel rod cladding |
Zircaloy-4 | Zr + Sn, Fe, Cr | Low hydrogen absorption, corrosion resistance | PWR fuel rod cladding |
ZIRLO | Zr + Nb, Sn, Fe | High burnup performance | Advanced nuclear fuel cladding |
Economic Value and Return on Investment
Thirdly, the chemical processing industry depends heavily on zirconium for constructing durable equipment designed to handle highly corrosive agents. The extended longevity of zirconium in aggressive environments translates directly into reduced maintenance costs and enhanced operational safety.
Furthermore, advanced manufacturing techniques, notably 3D printing, are creating new pathways for utilizing zirconium powders to create intricate, high-performance parts. These developments further cement its strategic importance across an expanding spectrum of industries.
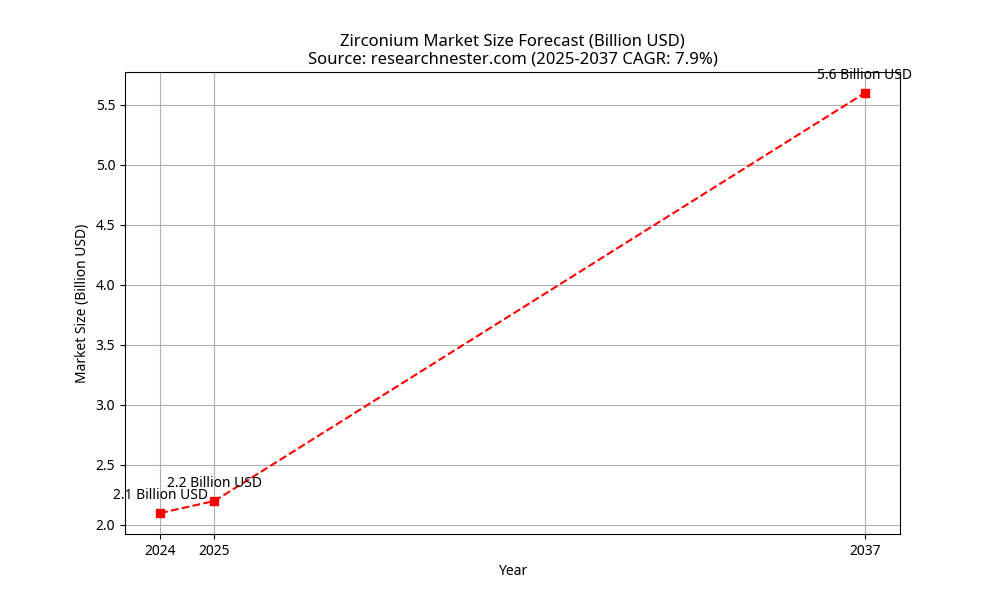
Cost-Benefit Analysis of Zirconium Materials
Evaluation Metric | Initial Cost | Service Life | Maintenance Cost | Total Cost of Ownership |
---|---|---|---|---|
Zirconium Equipment | High | 15-25 years | Very Low | Medium |
Stainless Steel Equipment | Medium | 5-10 years | Medium | Medium |
Carbon Steel Equipment | Low | 2-5 years | High | High |
Titanium Equipment | High | 10-20 years | Low | Medium |
Advancing Healthcare Through Biocompatible Applications
Zirconium’s biocompatibility, strength, and corrosion resistance make it a favored strategic manufacturing material in healthcare, particularly for implants. Zirconia (ZrO₂), its ceramic form, is non-toxic, non-allergenic, and integrates well with tissues.
It might surprise you, but zirconia’s strength makes it particularly suitable for orthopedic implants like hips and knees. Zirconium’s radiopacity aids in device visualization during medical imaging. Its chemical inertness ensures long-term safety. Zirconium coatings can also enhance the performance of metallic implants.
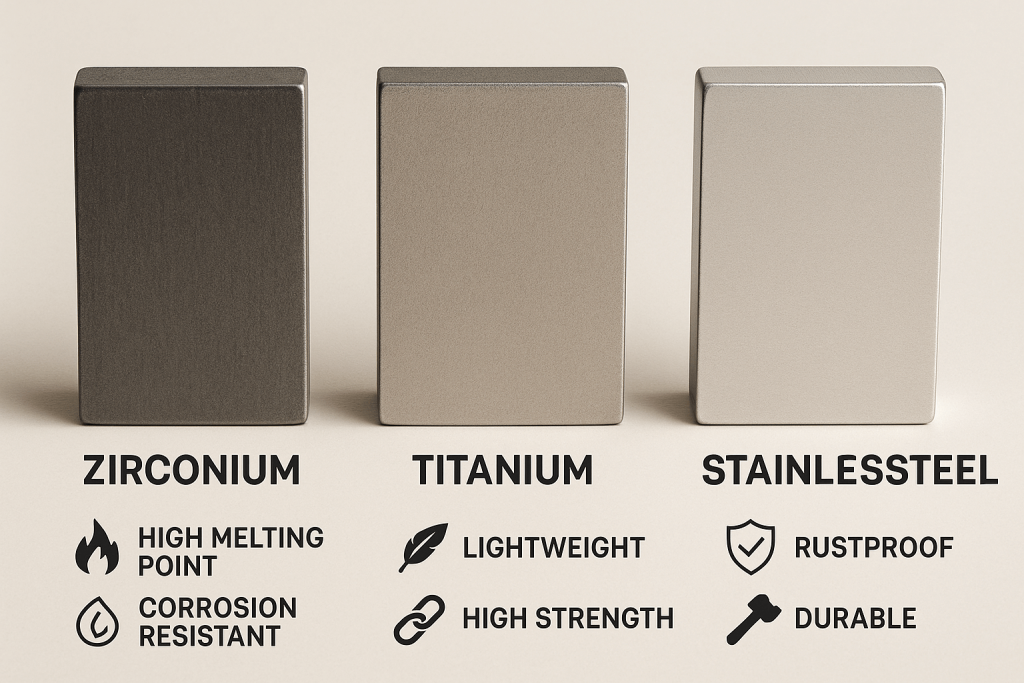
Medical Applications of Zirconium
Application Type | Zirconium Material Used | Advantages | Market Status |
---|---|---|---|
Dental Implants | Zirconia ceramic | Biocompatibility, aesthetics | Mature market, steady growth |
Orthopedic Implants | Zirconium alloys, zirconia | Strength, durability | Rapid growth, active innovation |
Surgical Instruments | Zirconium alloys | Hardness, edge retention | Stable growth |
Diagnostic Equipment | Zirconium compounds | Radiopacity | Emerging applications |
In dentistry, zirconia is a revolutionary strategic material. Think about this for a moment… It avoids PFM crown issues like metallic taste. Its natural color allows for aesthetic crowns and bridges. Zirconia’s strength means thinner restorations are possible. Monolithic zirconia crowns offer exceptional durability. Zirconia implants provide alternatives to titanium. CAD/CAM technology enables precise restorations. Zirconia has truly transformed modern dentistry.
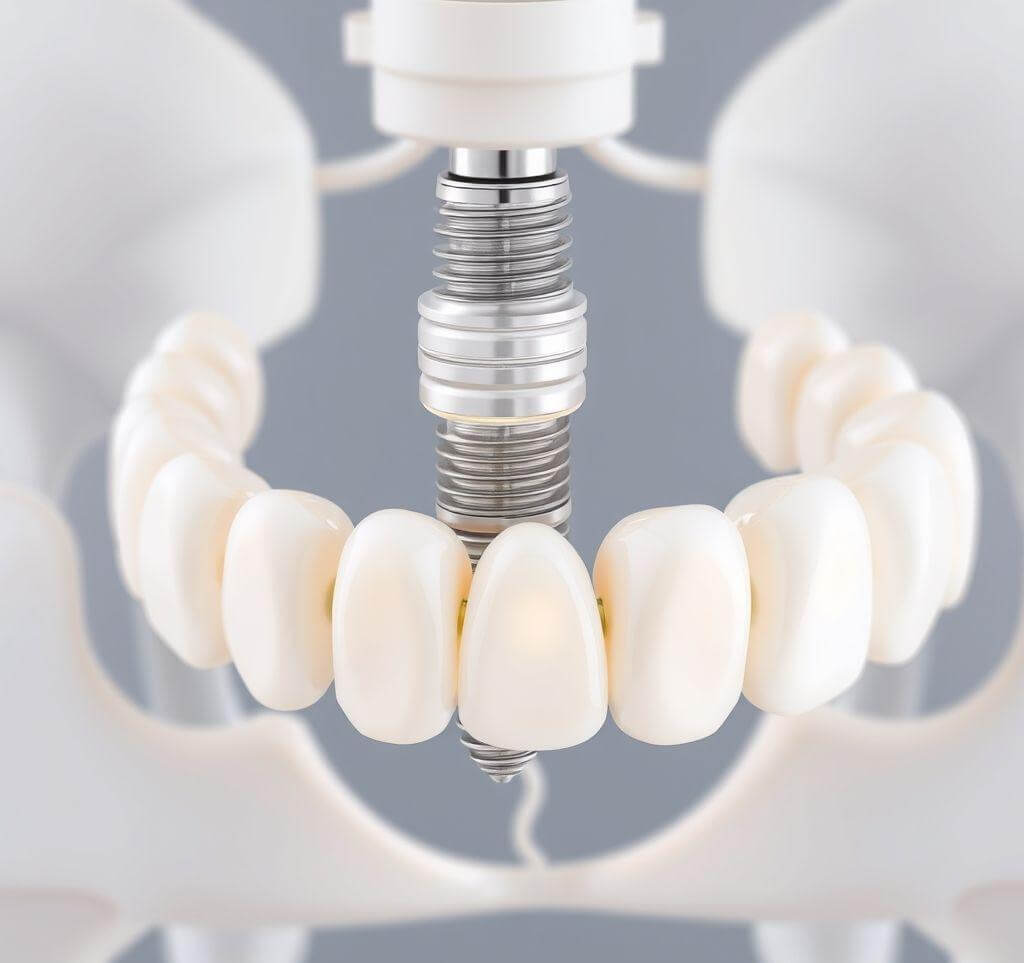
Future Development Trends in Zirconium Materials
Research Direction | Technology Readiness | Potential Impact | Expected Commercialization |
---|---|---|---|
Nanostructured Zirconium | Laboratory Stage | High | 5-10 years |
Advanced Zirconium Alloys | Pilot Stage | Medium | 3-5 years |
Zirconium-Based Composites | Early Application | High | 2-4 years |
Additive Manufactured Zirconium | Early Commercial | Very High | 1-3 years |
Zirconium Catalysts | Laboratory Stage | Medium | 5-8 years |
The Future of Zirconium in Manufacturing
Recent studies featured in the Materials Research Society Bulletin highlight emerging applications of zirconium-based nanomaterials in energy storage and catalysis.
The future trajectory for zirconium as a strategic manufacturing material looks promising. Clean energy initiatives continue to drive nuclear demand, with small modular reactors (SMRs) potentially increasing zirconium usage. Aerospace and defense sectors maintain strong growth trajectories. The chemical industry provides steady demand, while medical and dental applications continue to expand.
Investment opportunities in zirconium span from mining operations to end-product manufacturing. Direct investment in mining offers exposure but carries resource-specific risks. Companies developing advanced alloys and ceramics present growth potential. Research and development into new applications could yield significant returns. Investors should consider market cycles, production costs, and technical expertise requirements.
Conclusion
Zirconium has firmly established itself as a critical strategic manufacturing material across multiple industries. Its exceptional combination of properties—corrosion resistance, performance under extreme conditions, and versatility—makes it irreplaceable in applications ranging from nuclear energy to healthcare.
As global manufacturing continues to advance toward more demanding applications and environments, zirconium’s importance will only increase. The material’s ability to enable technological breakthroughs while providing reliability and longevity positions it as a cornerstone of future industrial innovation.
For manufacturers, engineers, and investors alike, understanding zirconium’s strategic value provides insight into emerging technologies and market opportunities. As we’ve explored throughout this article, zirconium isn’t just another industrial material—it’s a key enabler of progress across the manufacturing landscape.
FAQ Section
Q1: What makes Zirconium a strategic manufacturing material?
A1: Zirconium is a Zirconium strategic manufacturing material for its corrosion resistance, high-temp stability, low neutron absorption (nuclear), and biocompatibility. Indispensable in nuclear, chemical, aerospace, medical/dental sectors. Its role in advanced tech elevates its strategic importance.
Q2: How does Zirconium compare to Titanium for industrial applications?
A2: Both resist corrosion. Zirconium strategic manufacturing material often better in aggressive reducing acids. Titanium excels in oxidizing environments. Zirconium\s low neutron absorption is key for nuclear, where Titanium isn\t used. Choice depends on media, temp, needs; Zirconium superior in niches.
Q3: What are the main challenges when working with Zirconium?
A3: Zirconium strategic manufacturing material challenges: machining difficulty (galls, work-hardens), complex welding (reacts with air, needs inert gas), pyrophoric dust. Needs specialized knowledge, equipment, safety (Class D extinguishers).
Q4: What are Zircaloys and why are they important?
A4: Zircaloys (Zr alloys with tin, iron, chromium, nickel) are crucial Zirconium strategic manufacturing material in nuclear for fuel rod cladding. Important for low neutron absorption, corrosion resistance in high-temp water/steam, mechanical strength, ensuring nuclear safety.
Q5: Is Zirconium environmentally friendly?
A5: Zirconium strategic manufacturing material production has impacts (mining land use). Industry focuses on sustainability (rehab, efficiency). Zirconium is durable, recyclable, conserving resources. Efforts minimize ecological footprint.