Are you tasked with sourcing advanced ceramic components for demanding sectors like 5G infrastructure or medical devices? You need to understand the unique material requirements manufacturing complexities and critical supplier evaluation criteria. I can help you chart this course.
Sourcing advanced ceramic components for 2025 especially for 5G and medical applications requires a deep dive into material properties like dielectric performance biocompatibility and precision manufacturing capabilities from highly specialized suppliers.
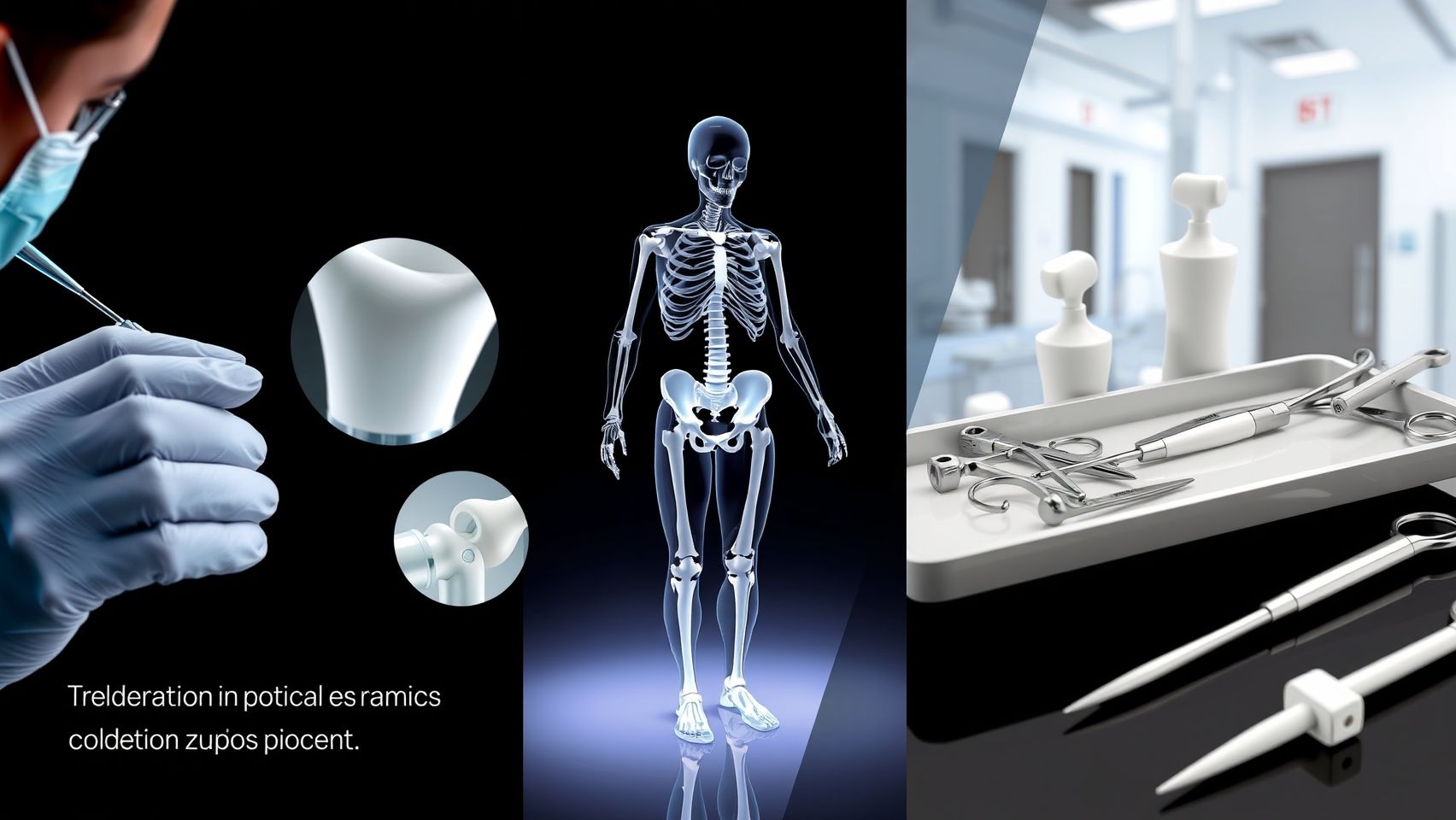
This image showcases sophisticated ceramic parts used in 5G technology and complex medical device applications.
Sourcing finished or semi-finished ceramic components made from zirconia or other advanced ceramics is a significantly different challenge compared to buying the raw powder. Here you are not just buying a material you are buying a precisely engineered part that often has to meet incredibly tight dimensio
nal tolerances and stringent performance criteria. This is especially true for cutting-edge applications in sectors like 5G telecommunications and medical devices. I have worked with companies developing components for both these fields and the level of precision and reliability required is immense. In 5G infrastructure for example ceramic materials like zirconia or alumina are used for components such as resonators filters and substrates due to their excellent dielectric properties at high frequencies low signal loss and good thermal stability. These components are critical for the performance of 5G base stations and user equipment. The material must have a precisely controlled dielectric constant and loss tangent and the manufactured component must adhere to sub-micron dimensional accuracy to function correctly at millimeter-wave frequencies. Any deviation can lead to signal degradation and system failure. Similarly in the medical field biocompatible zirconia ceramics are widely used for dental implants orthopedic joint replacements (like hip and knee components) and parts for surgical instruments. Here the primary requirements are biocompatibility (the material must not cause adverse reactions in the human body) high strength and fracture toughness excellent wear resistance and long-term stability in physiological environments. Again the manufacturing precision is critical to ensure proper fit and function of the implant or device. Sourcing these types of advanced ceramic components requires a very different approach to supplier selection and management. You are looking for a manufacturing partner not just a material vendor. The following sub-sections will explore the specific considerations for sourcing ceramic components for 5G and medical applications the criteria for evaluating manufacturers and an illustrative case study. My experience in these demanding sectors has shown that success hinges on finding suppliers with deep technical expertise proven manufacturing capabilities and an unwavering commitment to quality. This is a realm where cutting corners is simply not an option. The performance of your end product and potentially even human health can depend on the quality of these ceramic components. Therefore a rigorous and well-informed sourcing strategy is absolutely essential. This often involves a much longer supplier qualification timeline compared to raw materials as you are evaluating not just their material science knowledge but also their precision machining capabilities their cleanroom environments (if applicable) and their overall quality management systems tailored for these critical applications.
Innovations in Ceramic Components: Zircon’s Contribution to Cleaner and Greener Steel
Term “green steelmaking” encompasses a range of new technologies and process modifications aimed at decarbonization. This includes using hydrogen as a reductant instead of coal (Direct Reduced Iron – DRI with hydrogen) or implementing carbon capture utilization and storage (CCUS) technologies. In these evolving processes the operating conditions for refractory materials can be even more demanding. For example in hydrogen-based steelmaking the atmosphere can be highly reducing and may contain significant amounts of water vapor at high temperatures which can affect the stability and performance of traditional refractories. Zircon-containing refractories due to their excellent chemical inertness and stability at high temperatures are being investigated and in some cases adopted for critical areas in these new green steelmaking routes. Their ability to withstand corrosive slags and aggressive atmospheres makes them suitable for lining certain types of reactors or furnaces used in these novel processes. I have had discussions with refractory engineers who are actively testing zircon-fortified materials for components in pilot-scale hydrogen DRI plants. Their initial feedback suggests that zircon’s non-wetting characteristics and resistance to chemical attack are beneficial in these environments. Furthermore the push for cleaner steel also means a greater focus on reducing inclusions in the final steel product. High-quality zircon-based refractories can contribute to cleaner steel by minimizing refractory erosion and contamination of the melt. This is particularly important for producing high-grade steels used in demanding applications like automotive aerospace and energy. The use of zircon sand or milled zircon as a component in specialized refractory mixes for green steel applications is therefore an area of active development. Buyers in the steel or refractory industries should keep an eye on these trends. While the volumes may initially be smaller compared to traditional refractory applications the technical requirements will be high and the value-in-use significant. Sourcing zircon for these applications will require close collaboration with refractory manufacturers and steel producers to understand the specific performance requirements and to ensure the zircon quality meets these demanding conditions. The table below outlines some potential roles of zircon in green steelmaking.
Green Steelmaking Aspect | Potential Role of Zircon-based Materials | Benefit / Reason |
---|---|---|
Hydrogen-based DRI | Refractory linings in reactors; components exposed to H₂/H₂O atmospheres | Resistance to reducing atmospheres high temperature stability |
Advanced Smelting Technologies | Linings for novel furnace designs with aggressive slag chemistries | Excellent corrosion resistance to various slags |
Carbon Capture Systems | Components in high-temperature CO₂ capture units | Thermal stability chemical inertness |
Cleaner Steel Production | High-purity refractories to minimize steel contamination | Reduces inclusions improves steel quality for high-grade applications |
Specialized Casting Components | Nozzles shrouds for casting advanced steel grades produced via green routes | Enhanced wear resistance thermal shock resistance |
My take is that this emerging application area while still in its relatively early stages represents a potentially significant long-term growth driver for high-quality zircon. It aligns with the global sustainability agenda and the increasing demand for materials that can perform under extreme conditions. As these green steelmaking technologies mature and scale up the demand for suitable refractory solutions including those incorporating zircon will likely increase. For procurement professionals this means staying informed about the technological developments in the steel industry and engaging with suppliers who are innovating in the refractory space. It also underscores the importance of sourcing zircon with consistent chemical purity and physical properties as these will be critical for performance in such demanding new uses. The journey of steel towards a greener future is a complex one and materials like zircon have a part to play in enabling this transition. This is not just about finding a new market for an existing material it is about contributing to a more sustainable industrial future. The rigorous testing and qualification processes for refractories in these new steelmaking routes mean that entry barriers for suppliers will be high ensuring that only high-quality consistent zircon products will be considered. This focus on quality and performance will likely support premium pricing for zircon grades suitable for these applications. The long-term implications for the zircon market could be substantial if even a fraction of global steel production transitions to these new greener methods requiring specialized zircon-containing refractories. Therefore this is a trend that warrants close attention from anyone involved in the zircon supply chain from miners to end-users. The collaborative effort between material scientists refractory engineers and steel plant operators will be key to unlocking the full potential of zircon in this evolving landscape. This synergy is something I have always championed in my own work fostering communication and joint development to solve complex material challenges. The green steel revolution is underway and zircon is poised to be a part of it.
Zircon for Ceramics: Balancing Cost, Quality, and Sourcing Alternatives
In any procurement role the pressure to manage costs is ever-present. When it comes to zircon sand which can be a significant cost component in ceramics and foundries exploring cost-saving alternatives is a natural part of due diligence. However this exploration must be done with extreme caution as compromising on quality can lead to much higher costs downstream due to production issues product failures or customer dissatisfaction. I have seen instances where a switch to a seemingly cheaper raw material ended up costing a company far more in the long run. That said there are legitimate avenues to explore for cost optimization. One approach is to evaluate whether the highest grade of zircon is always necessary for every application. Some applications might be less sensitive to certain impurities or variations in particle size. For example a less critical refractory application might tolerate a slightly higher iron oxide content than a prime white ceramic glaze. Working closely with your technical team to precisely define the minimum acceptable specifications for each specific use case can sometimes open the door to using standard or even second-grade zircon products from reputable suppliers which can offer cost savings without unduly compromising performance. However this requires thorough testing and qualification. Another area to consider is the use of reclaimed zircon from foundry operations. Zircon sand used in foundry molds can sometimes be mechanically reclaimed cleaned and reused. While the quality of reclaimed zircon can vary and it may not be suitable for all applications it can be a cost-effective option for certain foundry uses or even as a partial substitute in some ceramic bodies if properly processed and characterized. The viability of this depends heavily on the quality of the reclamation process and the consistency of the reclaimed material. I have worked with foundries that have successfully implemented zircon reclamation systems significantly reducing their new zircon purchase volumes and disposal costs. However they invested heavily in the reclamation equipment and rigorous quality control of the reclaimed sand. Blending different grades or sources of zircon can also be a strategy but this requires sophisticated quality control and a deep understanding of how the blend will perform. It is not a simple undertaking and carries risks if not managed properly. Beyond zircon itself sometimes alternative minerals can be considered as partial substitutes in certain applications although true one-to-one replacements for zircon are rare due to its unique combination of properties (opacity refractoriness density). For example in some ceramic applications other opacifiers like calcined alumina or even certain titania products might be used to partially reduce zircon consumption but this often involves a trade-off in performance or requires reformulation of the ceramic body or glaze. The key is to evaluate the total impact on product quality and manufacturing efficiency not just the raw material price. The table below lists some potential areas for cost-saving considerations but emphasizes the need for careful evaluation.
Cost-Saving Approach | Potential Benefit | Key Risks / Considerations |
---|---|---|
Using Lower Grade Zircon | Lower purchase price | Must be suitable for the specific application; requires thorough testing & qualification |
Reclaimed Foundry Zircon | Reduced new material cost; waste reduction | Quality consistency varies; may not suit all applications; requires good reclamation process |
Blending Zircon Grades/Sources | Potential for optimized cost/performance ratio | Complex QC needed; risk of inconsistency if not managed well |
Partial Substitution (Non-Zircon) | Reduced zircon consumption | Often involves performance trade-offs; requires reformulation & extensive testing |
Optimizing Zircon Usage | Reduced waste improved efficiency in application | Requires process optimization & technical expertise |
Strategic Sourcing & Negotiation | Better pricing terms through volume contracts logistics | Requires market knowledge strong supplier relationships |
My philosophy on cost-saving is that it should never come at the expense of unacceptable quality or increased operational risk. True cost optimization in zircon procurement often comes from a deep understanding of your application needs efficient use of the material strong supplier relationships and smart logistics rather than simply chasing the lowest headline price. For instance optimizing the particle size distribution of the zircon you buy to better suit your milling process can lead to energy savings and improved product quality which are indirect cost savings. Similarly working with suppliers to optimize shipping and inventory management can reduce overall landed costs. I always encourage clients to have open discussions with their key zircon suppliers about cost-saving opportunities. Sometimes suppliers can offer valuable insights or alternative grades that you might not be aware of. A collaborative approach is often more fruitful than an adversarial one. Remember that the cheapest option is not always the best value. A holistic view of cost incorporating quality performance risk and supplier reliability is essential for making truly smart purchasing decisions for zircon sand in 2025. This also involves regularly benchmarking your zircon costs against market prices and exploring different sourcing channels but always with a primary focus on securing consistent quality that meets your specific application requirements. The pursuit of cost savings should be a continuous improvement process not a one-time exercise and it must be balanced with the strategic importance of zircon to your products.
Effective Zircon Procurement for Ceramics: A Dual Focus on Quality and Logistics
Buying zircon sand effectively in 2025 hinges on two critical pillars: ensuring consistent quality and managing logistics efficiently. These two aspects are deeply intertwined and getting them right can significantly impact your production costs product quality and overall supply chain reliability. I have learned over the years that a proactive and detailed approach to both is non-negotiable. Let’s start with Quality. The first step is to have a very clear and detailed specification for the zircon sand you require. This should go beyond just the headline ZrO₂ content and include maximum permissible levels for key impurities like Fe₂O₃ TiO₂ Al₂O₃ and others as well as the required particle size distribution (PSD). Different applications have different sensitivities to these parameters. For example in high-quality ceramics low iron and titania are crucial for whiteness while a specific PSD is needed for optimal glaze application and firing. Once you have your specification the next step is rigorous supplier qualification. This involves requesting samples from potential suppliers for thorough in-house testing. Do not rely solely on the supplier’s Certificate of Analysis (CoA) especially for new suppliers. Perform your own chemical analysis and PSD tests. I always recommend establishing a clear quality agreement with your chosen suppliers that outlines the agreed specifications testing methods and procedures for handling any out-of-specification material. This agreement should also cover batch traceability. Regular auditing of your key suppliers’ production facilities and quality control laboratories is also good practice. This helps build confidence in their processes and allows you to identify any potential issues early on. For ongoing shipments implement a system for incoming material inspection and testing. This could range from a simple visual inspection and PSD check for every batch to more comprehensive chemical analysis on a periodic basis or if any concerns arise. The frequency and intensity of testing can be adjusted based on the supplier’s historical performance and the criticality of the zircon to your process. Now let’s turn to Logistics. Zircon sand is a bulk commodity and efficient logistics are key to managing costs and ensuring timely delivery. The main modes of transport are bulk vessel shipments containerized shipments (in 1-2 ton bulk bags or smaller 25-50kg bags within containers) and sometimes truck or rail for shorter distances. The choice of transport mode will depend on your purchase volume your receiving capabilities and the supplier’s location. When sourcing internationally be sure to understand the Incoterms (e.g. FOB CIF DDP) being used as these define responsibilities for shipping insurance and other costs. Work closely with experienced freight forwarders or your supplier’s logistics team to optimize shipping routes and negotiate competitive freight rates. Shipping costs can be a significant portion of the landed cost of zircon so this is an area where savings can often be found. Consider your inventory management strategy. Holding too much inventory ties up working capital and incurs storage costs while holding too little risks production stoppages if there are supply delays. Finding the right balance requires careful demand forecasting and an understanding of supplier lead times and shipping transit times. For critical supplies it might be prudent to hold some safety stock. Packaging is another important logistical consideration. Ensure the zircon is packaged appropriately to prevent contamination and moisture absorption during transit and storage. Bulk bags should be of good quality and properly sealed. If you are receiving bulk shipments ensure your unloading and storage facilities are adequate to handle the material efficiently and safely. The table below summarizes some key buying tips for quality and logistics.
Aspect | Quality Tip | Logistics Tip |
---|---|---|
Specification | Define detailed specs for purity PSD etc. for your specific application | Understand impact of volume/packaging on shipping options & costs |
Supplier Qual. | Rigorous testing of samples; audit facilities; establish quality agreements | Evaluate supplier’s shipping experience & capabilities; clarify Incoterms |
Incoming QC | Implement inspection & testing for incoming shipments; verify CoAs | Optimize shipping routes & freight rates; work with experienced forwarders |
Traceability | Ensure batch traceability from supplier to your production | Plan inventory levels carefully considering lead times & transit times |
Contamination | Ensure proper handling & storage to prevent contamination | Choose appropriate packaging to protect material during transit & storage |
Documentation | Maintain clear records of specifications CoAs test results & shipments | Ensure all shipping & customs documentation is accurate & timely |
I recall a situation where a client was experiencing inconsistent firing results in their ceramic production. After a thorough investigation we traced the issue back to variations in the PSD of their zircon sand shipments from a particular supplier despite the CoAs looking acceptable. We implemented a stricter incoming PSD testing protocol and worked with the supplier to tighten their production controls. This resolved the issue but it highlighted the importance of not taking quality for granted. On the logistics front I once helped a client reduce their landed cost of zircon by consolidating their smaller orders into larger container shipments and negotiating an annual volume contract with a freight forwarder which gave them preferential rates and space allocation during peak shipping seasons. These kinds of optimizations require a proactive approach and a good understanding of the logistics market. In summary buying zircon sand effectively in 2025 is about meticulous attention to detail in both quality assurance and logistics management. Building strong transparent relationships with reliable suppliers who share your commitment to quality is fundamental. And continuously looking for ways to optimize your processes and supply chain will help you stay competitive in a dynamic global market. This holistic approach ensures you get the right material at the right time in the right condition and at a fair total cost.
Advanced Zirconia Ceramics: Meeting Demands of 5G and Medical Applications
Let’s delve deeper into the specific demands of 5G and medical applications for advanced ceramic components. For 5G telecommunications the push towards higher frequencies (millimeter-wave bands) to achieve greater bandwidth and faster data rates places extreme demands on the materials used in RF (radio frequency) components. Zirconia along with other ceramics like alumina and aluminum nitride is used for manufacturing parts such as dielectric resonators filters waveguides and substrates for integrated circuits. Key material properties for 5G applications include: a low and stable dielectric constant (εr) to minimize signal delay and enable component miniaturization; a low dielectric loss tangent (tanδ) to reduce signal attenuation and improve energy efficiency; high thermal conductivity to dissipate heat generated by active electronic devices; and excellent dimensional stability over a wide range of temperatures and humidity. The manufacturing of these components often involves precision green machining of the ceramic powder compacts followed by controlled sintering to achieve the desired density and microstructure and then potentially post-sintering machining (grinding lapping polishing) to meet the final dimensional tolerances which can be in the order of microns or even sub-microns. I recall a project for a 5G filter where the client required a specific grade of zirconia with a very tightly controlled dielectric constant. We worked with a specialized ceramic manufacturer who had developed proprietary doping techniques to fine-tune this property. The challenge was not just achieving the target value but ensuring its consistency across large production volumes. This required meticulous control over raw material purity powder processing forming sintering and final testing. For medical applications the primary driver is biocompatibility coupled with excellent mechanical properties and long-term stability. Zirconia ceramics particularly Yttria-Stabilized Zirconia (YSZ) have gained widespread acceptance for dental applications (crowns bridges implants) and orthopedic implants (femoral heads for hip replacements). The key advantages of YSZ in these uses are its high strength and fracture toughness (which helps prevent implant failure) its good wear resistance (important for articulating surfaces in joints) its chemical inertness (resistance to degradation by body fluids) and its aesthetic appeal (tooth-like color for dental restorations). However the success of medical ceramics also depends critically on avoiding a phenomenon called Low-Temperature Degradation (LTD) or aging where the zirconia can slowly transform from its strong tetragonal phase to a weaker monoclinic phase in the presence of moisture over time potentially leading to implant roughening and failure. Manufacturers of medical-grade zirconia have developed specific compositions (e.g. by adding small amounts of alumina or by carefully controlling the yttria content and grain size) and processing techniques to minimize LTD. When sourcing zirconia components for medical devices buyers must ensure that the supplier can provide extensive documentation and test data demonstrating biocompatibility (e.g. ISO 10993 compliance) mechanical properties and resistance to LTD. Full traceability of raw materials and manufacturing processes is also mandatory. The table below contrasts some key requirements for 5G and medical ceramic components.
Feature | 5G Telecom Applications | Medical Device Applications | Common Challenge |
---|---|---|---|
Key Material Property 1 | Low & stable Dielectric Constant (εr) | Biocompatibility (e.g. ISO 10993) | Achieving consistent material properties |
Key Material Property 2 | Low Dielectric Loss Tangent (tanδ) | High Strength & Fracture Toughness | Stringent quality control needed |
Key Material Property 3 | High Thermal Conductivity (for some parts) | Excellent Wear Resistance | Manufacturing to tight dimensional tolerances |
Critical Performance Factor | Signal integrity at high frequencies | Long-term in-vivo stability; resistance to Low-Temperature Degradation | Traceability of materials & processes |
Manufacturing Complexity | Precision machining; control of dielectric properties | Complex shaping; surface finishing; sterilization compatibility | High cost of specialized manufacturing |
Regulatory Oversight | Industry standards (e.g. for RF performance) | Stringent medical device regulations (e.g. FDA CE Mark) | Long supplier qualification & validation times |
I was involved in sourcing a complex zirconia component for a novel surgical tool. The design had very intricate features and required a highly polished surface finish to minimize tissue trauma. Finding a ceramic manufacturer who had both the advanced 5-axis CNC machining capabilities for hard ceramics and the expertise in polishing zirconia to the required optical-grade finish was a significant challenge. It took months of searching and auditing potential suppliers before we found a suitable partner. This experience underscored that for such critical applications you are not just buying a part you are buying the supplier’s entire ecosystem of expertise equipment and quality systems. The level of collaboration required between the buyer’s design team and the ceramic manufacturer’s engineering team is also much higher than for standard components. Early supplier involvement in the design phase (Design for Manufacturability – DFM) can often lead to more robust and cost-effective component designs. This proactive engagement is something I always advocate for when dealing with advanced ceramic components for these demanding high-stakes applications. The reliability of a 5G network or the success of a medical implant can hinge on the flawless performance of these often unseen ceramic parts.
Selecting Manufacturers for Advanced Zirconia Ceramic Components: A Comprehensive Evaluation Guide
Evaluating and selecting a manufacturer for advanced ceramic components especially for critical applications like 5G or medical devices is a multi-faceted process that requires a deep dive into their capabilities well beyond a simple price quote. My approach to this involves a systematic assessment across several key areas. Firstly Technical Expertise and R&D Capabilities. Does the manufacturer possess a strong understanding of ceramic science and engineering relevant to your application? Do they have in-house materials scientists and engineers who can work with you to select or even develop the optimal ceramic material and component design? Look for evidence of R&D activity patents publications or a history of solving complex ceramic manufacturing challenges. A manufacturer who is merely a “job shop” without deep material expertise might struggle with the nuances of advanced ceramics. I always try to gauge their problem-solving skills during initial discussions by presenting them with some hypothetical technical challenges. Secondly Manufacturing Capabilities and Equipment. You need to assess their entire manufacturing chain from powder preparation and forming (e.g. pressing injection molding slip casting 3D printing) to green machining sintering and final hard machining/finishing. Do they have state-of-the-art equipment appropriate for your component’s complexity and required tolerances? Are their processes well-controlled and documented? An on-site audit is usually essential to verify these aspects. Pay attention to the condition and maintenance of their equipment and the skill level of their operators. I remember visiting a potential supplier whose equipment looked impressive on paper but during the audit it became clear that their process control and metrology were lacking which was a major red flag. Thirdly Quality Management Systems (QMS) and Certifications. A robust QMS is non-negotiable. Look for certifications relevant to your industry such as ISO 9001 for general quality ISO 13485 for medical devices or IATF 16949 for automotive (if applicable to other product lines they make which can indicate a culture of quality). However a certificate alone is not enough. You need to understand how effectively their QMS is implemented. Review their procedures for raw material control in-process quality checks final inspection calibration and handling of non-conformances. For medical components ensure they comply with Good Manufacturing Practices (GMP). Fourthly Metrology and Inspection Capabilities. How do they measure and verify that the components meet your specifications? Do they have advanced metrology equipment such as Coordinate Measuring Machines (CMMs) optical profilometers surface roughness testers and equipment for microstructural analysis (e.g. SEM)? What is their calibration schedule for this equipment? The ability to accurately measure critical dimensions and material properties is fundamental. Fifthly Track Record and Customer References. What is their history of supplying similar components to other customers in demanding industries? Ask for references (while respecting confidentiality) and try to gauge their reputation for quality on-time delivery and customer service. A proven track record provides a degree of confidence. Sixthly Financial Stability and Scalability. Is the manufacturer financially stable and capable of investing in new equipment or capacity if your demand grows? Assess their financial health and their plans for future expansion. A supplier who is struggling financially may cut corners on quality or be unable to support your long-term needs. The table below provides a checklist for key evaluation areas.
Evaluation Area | Key Aspects to Assess | Red Flags to Watch For |
---|---|---|
1. Technical Expertise & R&D | Material science knowledge; problem-solving skills; R&D investment | Lack of in-house expertise; inability to discuss technical details meaningfully |
2. Manufacturing Capabilities | Equipment for forming sintering machining; process control; automation level | Outdated or poorly maintained equipment; inconsistent process documentation |
3. Quality Management Systems | Relevant certifications (ISO 9001/13485 etc.); effective implementation; traceability | Missing key certifications; poorly implemented QMS; lack of clear traceability |
4. Metrology & Inspection | Advanced measurement equipment; calibration procedures; skilled metrology staff | Inadequate metrology tools; infrequent calibration; inability to measure critical features |
5. Track Record & References | Experience in your industry/application; customer testimonials (if available) | No relevant experience; poor customer feedback or unwillingness to provide references |
6. Financial Stability & Scalability | Profitability; investment capacity; plans for growth | Signs of financial distress; no clear plans for scaling production |
7. Communication & Collaboration | Responsiveness; willingness to collaborate on design/problem-solving; transparency | Poor communication; unwillingness to share information or collaborate |
My personal experience has shown that the most successful supplier relationships for advanced ceramic components are built on a foundation of mutual trust transparency and strong technical collaboration. It is often a long-term partnership. The initial evaluation process might seem time-consuming and resource-intensive but investing this effort upfront can save you from much larger problems and costs down the line. I always advise clients to develop a detailed supplier questionnaire and an audit checklist tailored to their specific needs. And importantly involve a cross-functional team (engineering quality procurement) in the evaluation process to get a holistic perspective. Choosing the right manufacturing partner is arguably the most critical step in successfully bringing an advanced ceramic component to market. This decision should be based on a comprehensive assessment of their capabilities and their fit with your company’s long-term strategic objectives.
Zircon Use in Ceramics:Automotive case study
While the primary focus of this section has been on 5G and medical applications the automotive industry also presents a fascinating and rapidly growing area for advanced ceramic components particularly those made from zirconia. Let me share a generalized case study that illustrates the kind of applications and sourcing considerations involved. Case Study: Zirconia Oxygen Sensors in Automotive Exhaust Systems. Oxygen sensors (often called lambda sensors) are critical components in modern automotive exhaust systems. They measure the oxygen content in the exhaust gases and provide feedback to the engine control unit (ECU) to optimize the air-fuel mixture for efficient combustion and to control emissions. The heart of many of these sensors is a thimble or planar element made from Yttria-Stabilized Zirconia (YSZ). YSZ is an oxygen ion conductor at high temperatures. By exposing one side of the YSZ element to exhaust gas and the other side to a reference air source a voltage is generated across the zirconia that is proportional to the difference in oxygen partial pressure. This voltage signal is what the ECU uses. The Challenge: The zirconia element in an oxygen sensor operates in an extremely harsh environment. It is exposed to temperatures ranging from ambient up to 800-900°C or even higher during engine operation. It must withstand severe thermal shocks (e.g. when a cold engine starts) and constant vibration. It is also exposed to corrosive gases in the exhaust stream. Despite these conditions the sensor must provide accurate and reliable readings for many tens of thousands of miles to meet emissions regulations and ensure optimal engine performance. Material and Manufacturing Requirements: Sourcing the YSZ components for oxygen sensors requires a manufacturer with very specific capabilities: 1. Material Purity and Composition: The YSZ material must have a precisely controlled yttria content (typically 3 to 8 mol%) to optimize ionic conductivity and phase stability. Impurities must be strictly controlled as they can affect sensor performance and longevity. 2. Microstructure Control: The grain size and porosity of the sintered YSZ ceramic are critical. A dense fine-grained microstructure is generally preferred for mechanical strength and to prevent gas leakage. 3. Precision Forming: The zirconia thimbles or planar substrates are often complex shapes with thin walls and precise dimensions. Manufacturing processes like injection molding or tape casting followed by precision machining are common. 4. Electrode Application: Conductive platinum electrodes are applied to both sides of the zirconia element. The adhesion and porosity of these electrodes are crucial for sensor performance and durability. Specialized screen printing or sputtering techniques are used. 5. High-Volume Consistent Production: The automotive industry demands millions of these sensors annually. Manufacturers must be capable of high-volume production with extremely tight process control to ensure batch-to-batch consistency and very low defect rates (often measured in parts per million – PPM). Sourcing Considerations (Learnings from such cases): When I have been involved in or observed sourcing for such automotive ceramic components several key learnings emerge: Tiered Supply Chain: Automotive sourcing often involves a tiered supply chain. The ceramic component manufacturer might be a Tier 2 supplier selling to a Tier 1 sensor assembler who then sells to the automotive OEM. Understanding the dynamics and quality requirements throughout this chain is crucial. Rigorous Qualification (PPAP): Automotive suppliers must typically go through a very rigorous Production Part Approval Process (PPAP) which involves extensive testing documentation and process validation before mass production can begin. This can be a lengthy and demanding process. Long-Term Contracts and Cost Pressures: The automotive industry often works on long-term contracts but there is also constant pressure for cost reduction. Ceramic component suppliers need to be highly efficient and continuously look for process improvements. Zero-Defect Mentality: Given the safety and regulatory implications the expectation is for near-zero defects. This requires robust quality systems statistical process control (SPC) and a culture of continuous improvement. * Global Platform Consistency: Automotive OEMs often use global platforms meaning the same sensor might be used in vehicles manufactured in different parts ofthe world. The ceramic component supplier must be able to ensure consistent quality and supply to multiple locations globally. The table below summarizes the key aspects of this type of automotive ceramic component sourcing.
Aspect | Requirement for Zirconia Oxygen Sensor Component | Implication for Supplier Evaluation |
---|---|---|
Operating Environment | High temp thermal shock corrosive gases vibration | Supplier must demonstrate material & component durability under harsh conditions |
Material Properties | Controlled YSZ composition ionic conductivity phase stability | Deep material science expertise; tight control over raw materials & processing |
Manufacturing Process | Precision forming (e.g. injection molding) electrode application high volume | Advanced manufacturing technology; automation; robust process controls (SPC) |
Quality System | Automotive standards (e.g. IATF 16949); PPAP; zero-defect target | Proven QMS; experience with automotive qualification; strong statistical capabilities |
Supply Chain Integration | Ability to work within tiered automotive supply chain; global supply capability | Experience as an automotive supplier; global footprint or strong logistics partners |
Cost Management | Continuous cost reduction pressure while maintaining quality | High operational efficiency; commitment to continuous improvement; value engineering capabilities |
This automotive case study although specific illustrates the extreme demands placed on advanced ceramic components in high-volume critical applications. The lessons learned in terms of rigorous supplier qualification process control and the need for a zero-defect mentality are applicable to sourcing advanced ceramics for many other demanding industries as well. It highlights that successful sourcing in this space is about finding a true manufacturing partner who can meet not just the technical specifications but also the demanding quality cost and delivery expectations of a global industry. The investment in developing such partnerships is substantial but essential for long-term success. The precision required in every step from powder formulation to final component assembly is a testament to the advanced state of ceramic manufacturing today.
Buying Guide: How Can You Effectively Navigate Price Volatility and Secure Quality Zirconium?
Are you finding it challenging to manage fluctuating zirconium prices while ensuring consistent quality and navigating certification demands? You need a practical buying guide that covers price management quality assurance and how to access samples and quotes. I will provide actionable strategies.
An effective 2025 zirconium buying guide involves proactive strategies for managing price volatility stringent quality verification processes understanding certification requirements and efficiently obtaining samples and quotes from reliable suppliers.
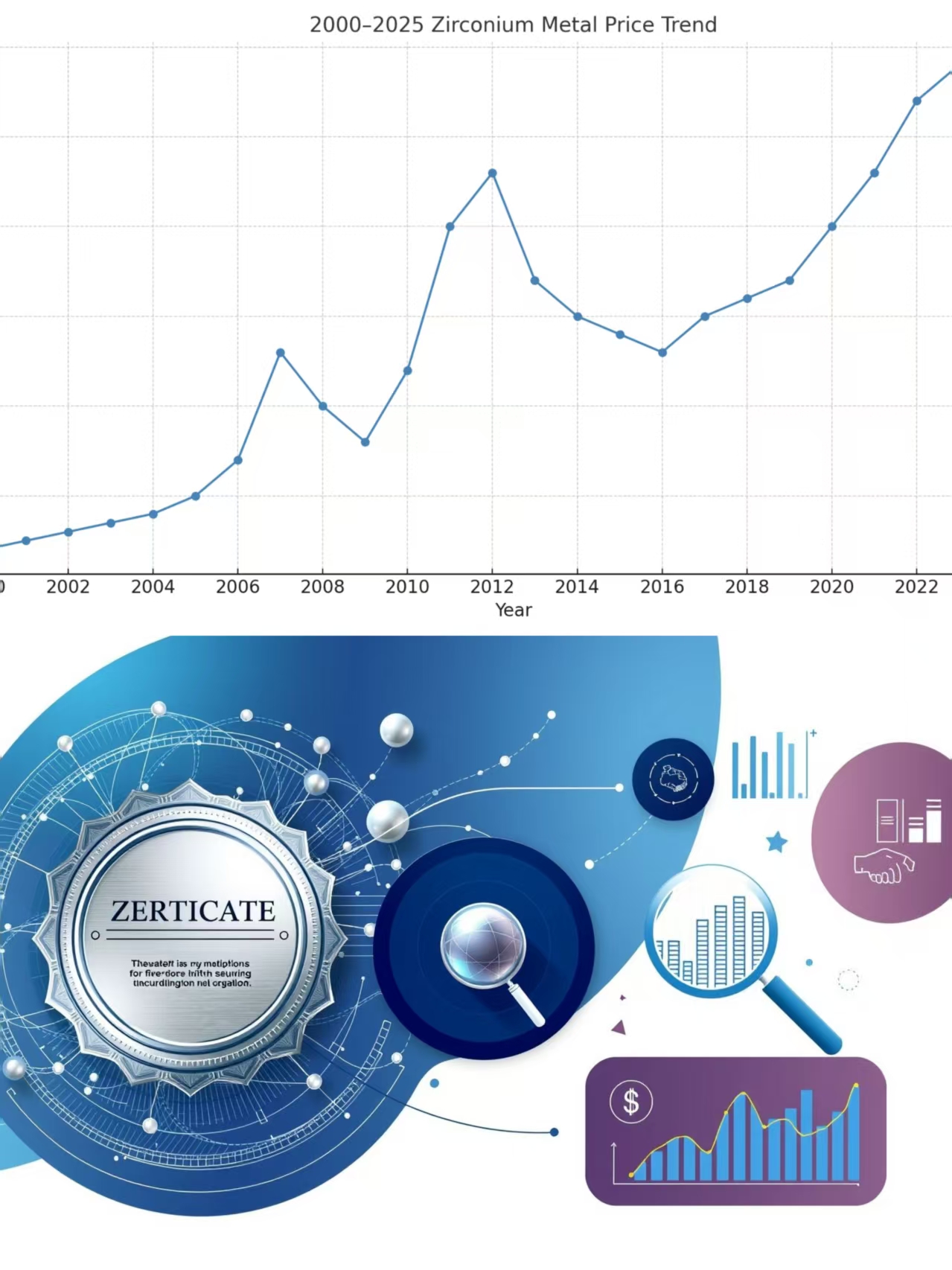
This image visually represents a strategic approach to buying zirconium incorporating price analysis quality assurance and supplier engagement.
Navigating the complexities of the zirconium market requires more than just finding a supplier and placing an order. It demands a strategic approach to buying that balances cost quality and security of supply. I have spent years refining my own buying strategies and helping clients develop theirs. This guide aims to consolidate some of the most effective practices for 2025. The zirconium market like many industrial commodities can experience periods of price volatility driven by shifts in supply and demand macroeconomic factors energy costs and geopolitical events. At the same time the technical requirements for zirconium materials especially for advanced applications are becoming increasingly stringent. This means buyers are often caught between the pressure to control costs and the imperative to secure high-quality consistent materials. Successfully managing this balancing act is the hallmark of effective procurement. This involves not only understanding the market dynamics we discussed earlier but also implementing practical strategies for price management quality assurance and supplier engagement. It is about making informed decisions based on good data and strong supplier relationships. In my experience a reactive approach to buying – simply responding to price changes or quality issues as they arise – is rarely successful in the long run. A proactive approach where you anticipate market shifts build robust quality systems and cultivate strategic supplier partnerships is far more effective. This section will provide actionable tips and insights into managing price fluctuations ensuring you get the quality you pay for understanding certification requirements and efficiently engaging with suppliers to obtain samples and quotes. Think of this as your practical toolkit for optimizing your zirconium procurement in the year ahead. The goal is to empower you to make smarter more confident buying decisions that support your company’s operational needs and strategic objectives. Let us explore these key aspects of a comprehensive zirconium buying guide. This involves a continuous cycle of market analysis supplier evaluation negotiation and performance monitoring. It is an ongoing process not a one-time task. The more informed and prepared you are the better you will be able to navigate the inevitable challenges and opportunities that the market presents.
Zircon for Ceramics: Managing price fluctuations
Price fluctuations are a reality in most commodity markets and zirconium is no exception. Several factors can influence zirconium prices including changes in mining output downstream processing capacity energy costs global demand from key industries (ceramics foundries chemicals high-tech) inventory levels and even currency exchange rates. As a buyer managing the impact of these fluctuations on your procurement costs is a key challenge. I have found that a multi-pronged approach is generally most effective. Firstly Market Intelligence is Key. Stay informed about the factors driving zirconium prices. Subscribe to industry publications market reports and news services that cover the zirconium and related mineral markets. Track price indices for zircon sand and different grades of zirconia if available. Understanding the underlying market fundamentals can help you anticipate potential price trends and make more informed buying decisions. For example if you see reports of major production disruptions at key mines or a surge in demand from a large consuming sector you might anticipate upward price pressure. Secondly Strategic Sourcing and Supplier Relationships. Develop relationships with a portfolio of reliable suppliers. While it is tempting to always chase the lowest price a more strategic approach involves building long-term partnerships with key suppliers. These suppliers are often more willing to work with you on price stability perhaps through longer-term contracts or by providing early warnings of potential price changes. Having multiple qualified suppliers also gives you some leverage and alternative options if one supplier implements an unacceptably large price increase. However constantly switching suppliers based purely on small price differences can be counterproductive as it can damage relationships and potentially compromise quality consistency. Thirdly Contractual Agreements. Where possible explore different types of contractual agreements. For larger consistent volumes you might be able to negotiate fixed-price contracts for a certain period (e.g. 6-12 months) which can provide budget certainty. Alternatively some contracts might include price adjustment clauses linked to specific market indices or input costs (e.g. energy) which can offer transparency. Understand the terms and conditions of any contract carefully especially regarding price review mechanisms and volume commitments. I once helped a client negotiate a contract that included a cap and collar on price escalation providing them with a defined range of price certainty for a year. Fourthly Inventory Management. Your inventory strategy can also help buffer against short-term price volatility. Holding some strategic safety stock (if financially viable and practical for the material’s shelf life) can allow you to delay purchases during periods of peak prices or supply tightness. However this needs to be balanced against the costs of holding inventory (storage capital tied up risk of obsolescence). Fifthly Hedging (Limited Applicability). For some very large volume commodities financial hedging instruments are available to manage price risk. However for most zirconium products especially specialized grades formal hedging markets are generally not well-developed or accessible to most buyers. This option is therefore usually limited. The table below summarizes these price management strategies.
Strategy | Action | Benefit |
---|---|---|
1. Market Intelligence | Track prices drivers news; subscribe to reports | Better anticipation of trends; more informed buying decisions |
2. Strategic Sourcing | Build relationships with key suppliers; have multiple qualified sources | Potential for price stability; leverage; alternative options |
3. Contractual Agreements | Explore fixed-price or indexed contracts; understand terms | Budget certainty; transparency in price adjustments |
4. Inventory Management | Maintain appropriate safety stock levels | Buffer against short-term price spikes & supply delays |
5. Value Analysis / Engineering | Work with R&D to see if less costly (but suitable) grades can be used | Potential for direct material cost reduction if performance is maintained |
6. Consolidated Purchasing | Consolidate volumes across business units or over time for better leverage | Increased bargaining power; potential for volume discounts |
One often overlooked aspect of managing price fluctuations is Value Analysis/Value Engineering (VA/VE). Continuously review your material specifications with your technical team. Is it possible to use a slightly different or less expensive grade of zirconia without compromising the performance of your end product? Sometimes a material is over-specified for an application. A successful VA/VE exercise can lead to significant cost savings. However this requires careful testing and validation. I have also found that Consolidated Purchasing can be effective. If your company has multiple sites or business units using similar zirconium materials consolidating the purchasing volume can give you greater leverage with suppliers and potentially lead to better pricing. Finally do not underestimate the power of Good Negotiation Skills based on solid market knowledge and a clear understanding of your own requirements and alternatives. Being well-prepared for negotiations can make a significant difference. Managing price fluctuations is an ongoing process that requires vigilance adaptability and a strategic mindset. There is no single magic bullet but by employing a combination of these strategies you can better navigate the inherent volatility of the zirconium market and protect your company’s bottom line. This also means being prepared to walk away from a deal if the price or terms are not acceptable and you have viable alternatives.
Ensuring Quality: Key Certifications for Zirconium Used in Ceramic Components
In today’s global marketplace certifications play a crucial role in demonstrating product quality safety and compliance with various industry and regulatory standards. When sourcing zirconium materials especially for applications with stringent requirements understanding and verifying relevant certifications is a key part of the buyer’s due diligence. The specific certifications required will vary greatly depending on the zirconium product (e.g. zircon sand zirconia powder finished ceramic component) and its intended end-use (e.g. industrial ceramics electronics medical devices). For Quality Management Systems the most common certification is ISO 9001. This indicates that the supplier has a documented QMS in place to ensure consistent product quality and customer satisfaction. While ISO 9001 is a good baseline for more critical applications you might look for industry-specific QMS certifications. For example ISO 13485 is the standard for QMS for medical device manufacturers. If you are sourcing ceramic components for medical implants ensuring your supplier is ISO 13485 certified is usually a fundamental requirement. For automotive components IATF 16949 is the relevant QMS standard. For Product-Specific Certifications or Compliance there are numerous possibilities. For example: RoHS (Restriction of Hazardous Substances) and REACH (Registration Evaluation Authorisation and Restriction of Chemicals): If you are sourcing zirconium materials or components for use in electronic equipment sold in the European Union (and many other regions that have adopted similar regulations) you will need to ensure they comply with RoHS (which restricts the use of specific hazardous materials like lead mercury cadmium etc.) and that the substances are appropriately managed under REACH. Suppliers should be able to provide declarations of conformity. Biocompatibility Testing (e.g. ISO 10993): For medical-grade zirconia used in implants or devices extensive biocompatibility testing according to standards like ISO 10993 is required to ensure the material is safe for use in the human body. You will need to see test reports from accredited laboratories. Food Contact Compliance (e.g. FDA FDA (EC) 1935/2004): If zirconia is used in ceramic tableware or food processing equipment that comes into contact with food it must comply with relevant food contact material regulations in the target markets. Conflict Minerals Compliance: While zirconium itself is not typically classified as a “conflict mineral” (like tin tantalum tungsten gold sourced from certain regions) it is good practice to understand your supplier’s sourcing policies and due diligence regarding ethical sourcing of all raw materials. Some customers particularly in the electronics industry may require declarations regarding conflict minerals. * Certificates of Analysis (CoA): While not a “certification” in the same way as ISO a CoA provided by the supplier for each batch of material is a critical document. It should detail the key chemical and physical properties of the batch and confirm that it meets the agreed specifications. You need to ensure the CoA is comprehensive accurate and from a reputable source (ideally the manufacturer). The table below lists some common certification areas.
Certification / Compliance Area | Relevance for Zirconium Sourcing | What to Look For / Request from Supplier |
---|---|---|
ISO 9001 (QMS) | General quality management for most suppliers | Valid certificate from an accredited certification body |
ISO 13485 (Medical QMS) | Essential for suppliers of medical-grade zirconia or components | Valid certificate; evidence of compliance with all relevant clauses |
IATF 16949 (Automotive QMS) | For suppliers of automotive components | Valid certificate; evidence of PPAP capability etc. |
RoHS / REACH Compliance | For materials/components used in electronics | Declarations of Conformity; test reports if necessary |
Biocompatibility (ISO 10993) | For medical implants/devices | Full test reports from accredited labs for the specific material grade |
Food Contact Compliance | For ceramics used in food applications | Declarations of Conformity with relevant FDA EU or other regulations |
Certificate of Analysis (CoA) | For every batch of material to verify specifications | Detailed accurate CoA from manufacturer; compare against your specs |
Environmental Certs (e.g. ISO 14001) | Demonstrates environmental management | May be important for corporate sustainability goals |
My advice is to always Verify Certifications. Do not just accept a copy of a certificate at face value. You can often check the validity of ISO certificates with the issuing certification body. For product compliance declarations ask for supporting test reports where appropriate. Understand the Scope. Ensure the certification covers the specific products processes or sites relevant to your purchase. A company might be ISO 9001 certified but that certification might not cover the specific production line making your material. Integrate into Supplier Qualification. Make certification requirements a clear part of your supplier qualification process and your purchase agreements. Specify which certifications are mandatory and what documentation you require. I remember a case where a client was sourcing zirconia powder for a food contact application. The supplier claimed compliance but could not provide the specific migration test reports required by EU regulations. This led to a delay in product launch while a new supplier was qualified. This highlights the importance of clarifying and verifying certification requirements early in the sourcing process. Keeping up-to-date with evolving regulations and standards in your industry and target markets is also crucial as requirements can change. This due diligence on certifications is an essential step in mitigating risks ensuring product safety and quality and maintaining market access for your own products.
Effective Zirconium Sourcing for Ceramics: From Sample Request to Quotation Analysis
Obtaining samples for testing and detailed quotations are fundamental steps in the process of qualifying new zirconium suppliers or new material grades. Effectively managing this process can save time resources and help you make better sourcing decisions. Here is my approach to getting the most out of sample requests and quotation processes. 1. Be Specific and Clear in Your Sample Request. Before requesting a sample ensure you have a clear preliminary specification for the material you need. Provide the potential supplier with as much detail as possible about your application the required grade (e.g. purity particle size phase composition for powders; or dimensional drawings and material specs for components) and the specific properties you will be testing. This helps the supplier provide you with the most relevant sample. Specify the quantity of sample needed for your evaluation. For powders this might range from a few hundred grams to a few kilograms. For components it might be a small number of pieces. Also clarify if there are any specific packaging or labeling requirements for the sample. While many suppliers offer small evaluation samples free of charge (especially for standard products) some may charge for larger quantities or for highly specialized custom-made samples. It is always best to clarify the cost (if any) and shipping terms for the sample upfront. I usually prepare a formal Sample Request Form that details all this information to ensure clarity. 2. Plan Your Sample Evaluation Thoroughly. Once you receive a sample have a clear plan for how you will test and evaluate it. This plan should be based on your critical-to-quality parameters. For powders this might include chemical analysis (purity impurities) particle size distribution specific surface area phase analysis (e.g. using XRD) and processing trials (e.g. making a small batch of your product). For components this would involve dimensional checks material property verification (e.g. density hardness strength) and functional testing in your application. Document all your test results meticulously. This data will be crucial for comparing different suppliers and for discussions with the supplier if any issues arise. 3. Provide Constructive Feedback on Samples. After evaluating a sample provide timely and constructive feedback to the supplier regardless of whether the sample met your requirements or not. If the sample was good this reinforces their understanding of your needs. If there were issues specific feedback can help the supplier understand what went wrong and potentially offer an improved sample or a different solution. This collaborative approach can be very beneficial. 4. Requesting Quotations (RFQ/RFP). When you are ready to request a formal quotation (Request for Quotation – RFQ or Request for Proposal – RFP for more complex requirements) be as comprehensive as possible. Your RFQ should include: Detailed material specifications or component drawings. Required annual or batch volumes. Desired delivery schedules and locations. Packaging requirements. Quality requirements (including any specific certifications or CoAs needed). Quoting currency and Incoterms. Validity period for the quotation. Any other relevant commercial terms and conditions. Providing all this information upfront allows suppliers to give you an accurate and complete quotation which makes comparison easier. I often use a standardized RFQ template. 5. Evaluate Quotations Holistically. When you receive quotations do not just compare the unit price. Evaluate the total landed cost which includes the material price shipping insurance duties and any other associated costs. Also consider other factors such as: Supplier’s lead time and delivery reliability. Payment terms. Warranty and quality guarantees. Technical support offered. * Supplier’s overall capability and reputation (based on your earlier qualification work). A slightly higher unit price from a more reliable supplier with better quality and shorter lead times might represent better overall value. The table below summarizes tips for samples and quotes.
Process Step | Key Action | Benefit |
---|---|---|
1. Sample Request | Be specific on grade quantity application; clarify costs & shipping | Supplier provides relevant sample; avoids misunderstandings |
2. Sample Evaluation | Have a clear test plan; document results meticulously | Objective comparison of suppliers; data for technical discussions |
3. Sample Feedback | Provide timely constructive feedback to supplier | Improves supplier understanding; facilitates problem-solving |
4. RFQ Preparation | Be comprehensive: specs volumes delivery quality terms etc. | Suppliers provide accurate complete quotes; easier comparison |
5. Quote Evaluation | Consider total landed cost lead time payment terms quality support etc. | Holistic decision-making; best overall value not just lowest price |
6. Negotiation | Negotiate based on market knowledge your volumes & total value proposition | Achieve fair terms and conditions; build a sustainable supplier relationship |
I always recommend treating the sample and quotation process as an opportunity to further assess a potential supplier’s professionalism responsiveness and attention to detail. How quickly and accurately do they respond to your requests? Are they willing to provide detailed technical information? Their behavior during this pre-commercial phase can often be indicative of how they will perform as an ongoing supplier. For critical materials it is often worthwhile to request samples from multiple qualified suppliers to have a basis for comparison. And when you move to commercial orders ensure that the quality of the production material consistently matches the quality of the approved sample. This can be specified in your purchase agreement. Efficiently managing the process of obtaining and evaluating free samples and detailed quotes is a cornerstone of effective zirconium procurement. It lays the groundwork for successful long-term supplier partnerships and ensures you are sourcing the best possible materials for your needs under fair commercial terms. This diligence upfront pays dividends in supply chain stability and product quality.
Conclusion
Navigating the 2025 global zirconium market requires informed strategies for sourcing ZrO₂ zircon sand and ceramic components. Understanding supply dynamics price forecasts geopolitical impacts and stringent quality certifications alongside smart buying practices is absolutely key for your procurement success.
FAQ
Q1: What are the primary drivers for high-purity zirconia (HPZ) demand in 2025?
A1: The primary drivers for HPZ demand in 2025 are advanced technology sectors. These include the rapidly growing market for solid-state batteries where HPZ is used for electrolytes or coatings. The semiconductor industry also requires HPZ for components in manufacturing equipment due to its plasma resistance and thermal stability. Additionally medical applications like dental and orthopedic implants and specialized industrial uses such as advanced sensors and 3D printing of intricate ceramic parts contribute significantly to the increasing demand for zirconia with purity levels often exceeding 99.9%.
Q2: How can I mitigate risks associated with zircon sand price volatility?
A2: Mitigating zircon sand price volatility involves several strategies. Firstly maintain strong market intelligence to anticipate trends. Secondly cultivate relationships with multiple reliable suppliers to ensure options and some leverage. Thirdly explore longer-term contracts with fixed or indexed pricing where feasible. Fourthly implement an optimized inventory management strategy to buffer against short-term spikes without overstocking. Lastly continuously conduct value analysis to ensure you are using the most cost-effective grade suitable for your application and consolidate purchasing volumes for better negotiation power.
Q3: What are the critical supplier evaluation criteria for advanced ceramic components used in medical devices?
A3: For medical device ceramic components critical evaluation criteria include: ISO 13485 certification for their Quality Management System. Proven technical expertise in medical-grade ceramics and precision manufacturing. Documented evidence of biocompatibility (e.g. ISO 10993 test reports for the specific material). Stringent raw material control and full manufacturing process traceability. Advanced metrology and inspection capabilities to ensure tight dimensional tolerances and material integrity. A strong track record of supplying to the medical industry and robust procedures for managing Low-Temperature Degradation (LTD) in zirconia.
Q4: Are there any significant new applications for zircon sand I should be aware of for 2025?
A4: Yes one notable emerging application for zircon sand is in certain aspects of green steelmaking. Zircon-containing refractories are being explored and used for critical components in new decarbonized steel production routes such as hydrogen-based Direct Reduced Iron (DRI) plants. Zircon’s excellent high-temperature stability corrosion resistance and chemical inertness make it suitable for the demanding conditions in these novel processes contributing to cleaner and more sustainable steel production.
Q5: What is the first step I should take when requesting a sample of specialized zirconia powder?
A5: The first step when requesting a sample of specialized zirconia powder is to clearly define and communicate your requirements to the potential supplier. This includes providing a detailed preliminary specification (target purity key impurity limits desired particle size distribution phase composition etc.) explaining your intended application and the specific properties you will be evaluating. Also specify the sample quantity needed and clarify any costs or shipping terms upfront to ensure the supplier can provide the most relevant material for your testing.